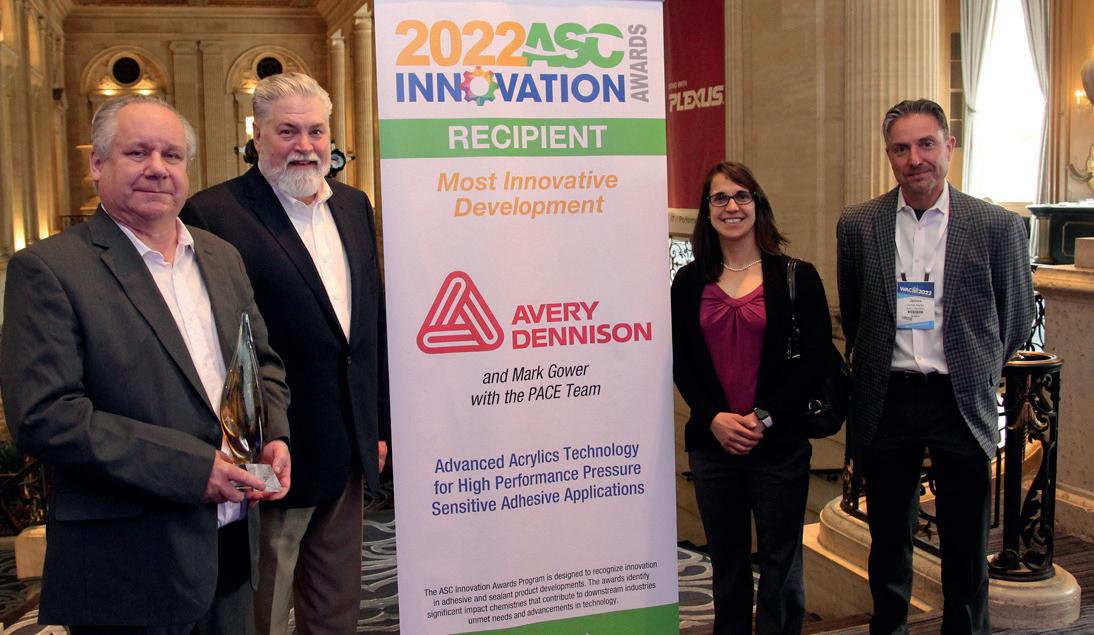
3 minute read
Awards A rewarding experience
In advance of ASC announcing who will receive the 2023 Innovation Award, Avery Dennison discusses its winning entry last year
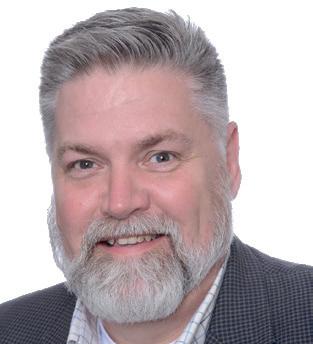
Innovation drives progress in the adhesive and sealant industry and ASC recognizes the importance that companies put on keeping their competitive edges sharp with its annual Innovation Awards.
Inaugurated in 2017, the awards will next be presented at ASC’s Annual Convention & EXPO in New Orleans from April 17-19, 2023.
Last year, Avery Dennison was selected from a record number of entries and received the accolade for its ground-breaking, solventfree acrylic pressure sensitive adhesive.
Mark Gower, Technical Principal, who led the development team, says it was “a really big deal to win a global award” and it had a hugely positive impact on the product, technology, and team behind the development.
The winning submission was centered around Avery Dennison’s Advanced
Acrylics Technology, which delivers high performance pressure sensitive adhesives. It was developed at the company’s Polymers, Adhesives and Coatings Center of Excellence (PACE) research facilities at Mill Hall, PA.
As well as providing Avery Dennison with a strong external marketing opportunity, winning the award helped the team “to market our department internally. It helped to get the word out about the technology outside and inside the company,” says Gower.
Chuck Williams Senior Director, R&D, Global Platform at Avery Dennison adds that the award “validates the last seven years’ work and it is important that the ASC recognizes this development for the sake of the industry. It is a fledgling product, but the award recognizes that it is a game-changing technology.”
A year on from winning and the technology is being commercialized. “The award is helping,” he says. “More people are approaching us with more confidence about using the product and we are extracting value from the technology.”
Water-based adhesives evaporate water
Mark Gower Technical Principal, Avery Dennison
during the manufacture of self-adhesive articles whereas solvent-based systems evaporate large quantities of flammable and toxic solvents. The Advanced Acrylics technology can match, and often exceed, the performance requirements placed on traditional solvent-based systems.
Solvents-based systems (whether water or hydrocarbon-based) have solvents removed during self-adhesive article manufacture to provide a tape or label with a dried PSA layer ready for application/end-use. For legacy emulsions, surfactant accumulates at the adhesive/air interface during the adhesive drying step, lowering the overall performance of the ready-to-use self-adhesive article.
Williams explains that the technology was developed because of demand pull from the market and technology push from within Avery Dennison. “There is a need to get away from solvent-based systems. Solvents are hazardous and are only used as a carrier,” he says.
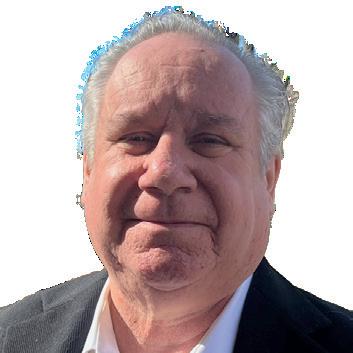
Moving away from solvents has a number of benefits. The water-based systems are typically 65% solids, and solvent-based adhesive systems are around 35-40% solids.
Watch the video...
Avery
Watch the video by visiting https://www.averydennison. com/en/home/newsroom/ avery-dennison-blog/ Graphics-Solutions-Blog/ avery-dennison-recognizedfor-another-industry-first.html
This means that much less carrier is shipped with each delivery, so the amount of carbon generated for each pound of useful adhesive is reduced.
Water is also much less expensive than solvent. Moving to these systems in 2022 resulted in Avery Dennison reducing fossil fuel use by 67% and energy use by 49% compared to solvent-based products.
There are also benefits from water being non-flammable. Water-based systems are easier and safer to process than a flammable solvent mixture and, as water-based emulsions contain no solvents, empty drums of emulsion are also much less hazardous in terms of waste disposal than empty containers of solvent-based systems.
But emulsion-based systems are complex. Emulsions are designed to keep two incompatible liquids as a mixture, by adding a third: a surfactant.
Surfactants have two different properties in their molecular design. One part of the molecule is attracted to one liquid, the other end is attracted to the other. Soap is a good example. One end of soap molecules is attracted to greasy hydrocarbons, the other is attracted to more polar water. That is why washing works — dirt in the grease is floated off into water by the soap.
With adhesives, however, emulsions can pose a challenge. The surfactant can get between the active adhesive and the substrate, which can reduce the strength of adhesive bonds or prevent bonds forming at all. Avery Dennison’s PACE team found a way around this.
“We had some history with controlled polymerization in solvent-based systems and decided it would be interesting to try something similar with our adhesives based on emulsion coatings,” says Gower. “We had some initial success, but it was complex.”
He says work published by the University of Minnesota gave his team encouragement. This suggested that if it were possible to keep the surfactant away from the interface between the substrate and the adhesive there would be a good chance of forming a strong bond.
The PACE team designed molecules to gain adhesion, which Gower says “is bridging the gap between polymer chemistry and fine chemistry”.
“A unique outcome of our work is that there is no surfactant at the bond,” he notes. The solution is to polymerize the surfactant as part of the bonding process.
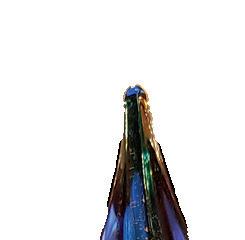
For Williams, ASC’s Innovation Award helps to highlight the benefits of designing molecules to gain adhesion as well as the molecular architecture which drives adhesion. It also demonstrates the strength of the Avery Dennison team — and shows that it is possible to produce high-performance, sustainable adhesives that are not solvent based.
To find out more about the Innovation Awards, visit ASC’s website at https://www. ascouncil.org/innovation-awards
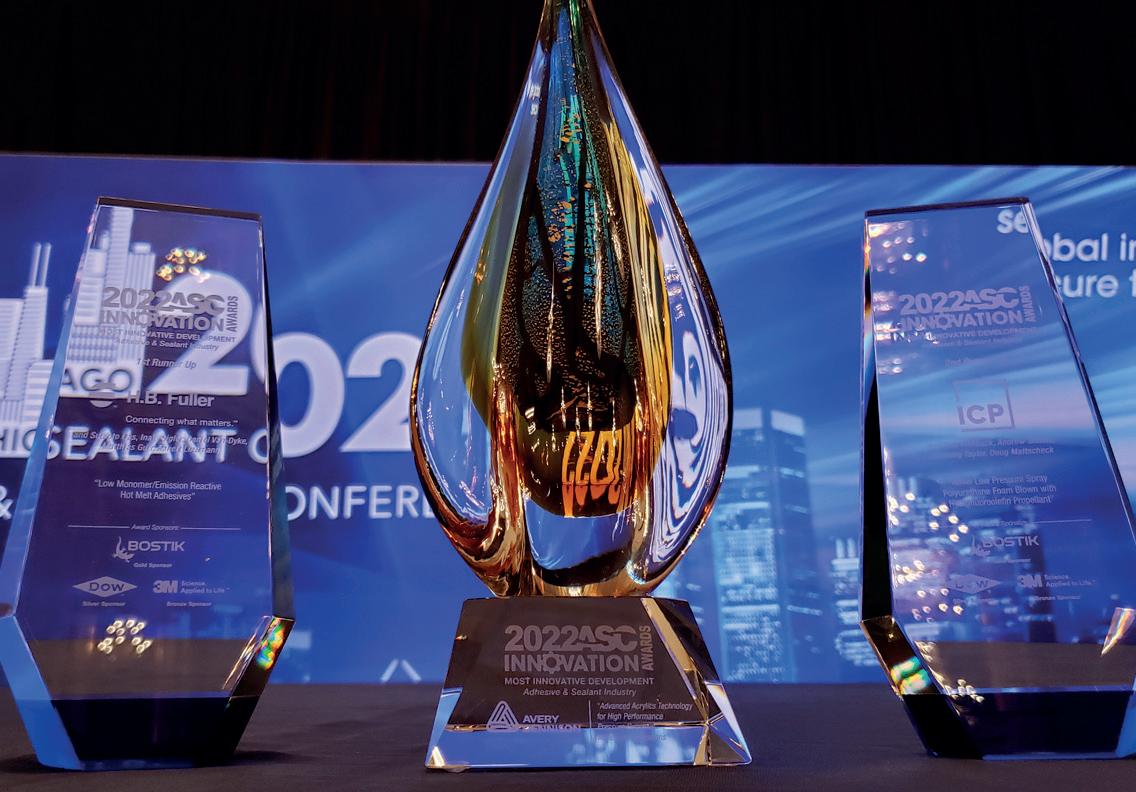
Simon Robinson
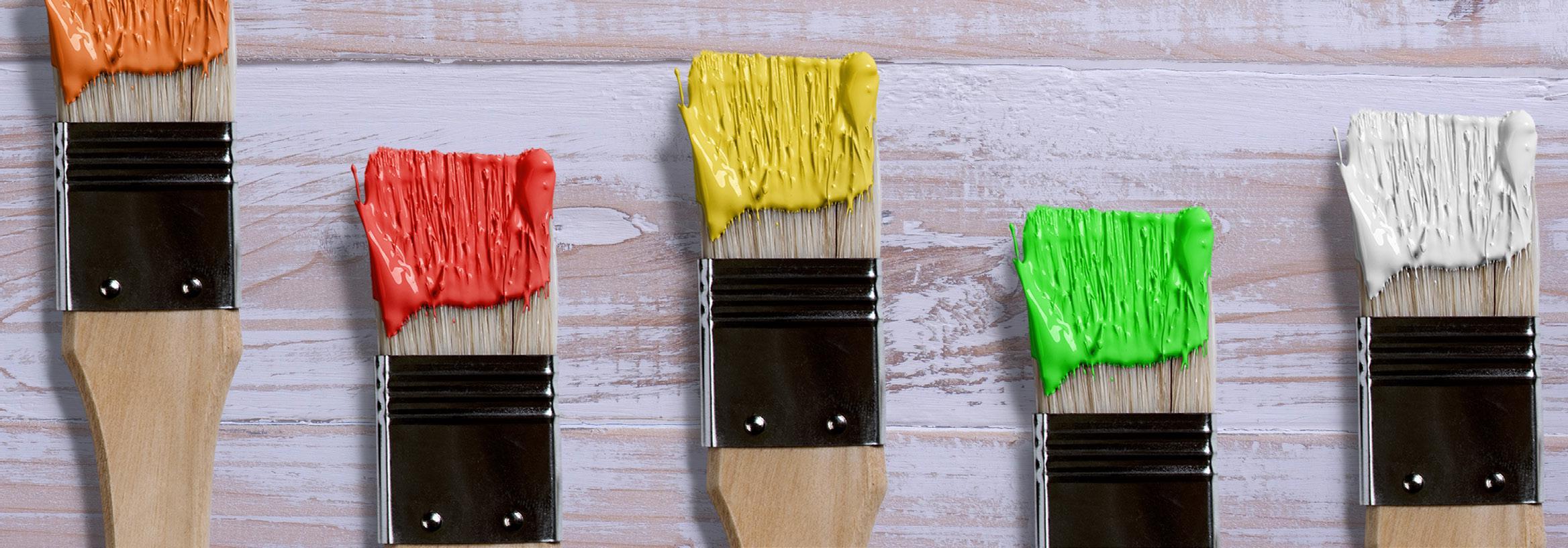