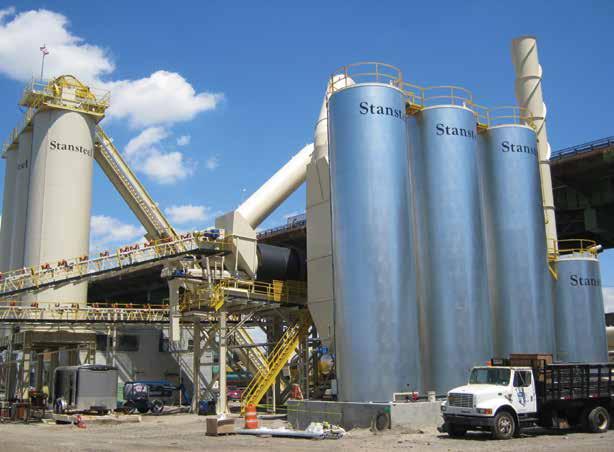
11 minute read
Granite Manages Multiple Tanks
Granite Mana es Multiple Tanks New system ensures safe, economical, provable practices at the tank farm
BY SANDY LENDER
TEditor’s Note: It’s worth noting that liquid asphalt cement (AC) “spills” cool quickly in ambient temperatures and solidify, rather than flow. The type of overflow referenced in this article is relegated to the containment areas that asphalt producers are required to build around tank farms, creating mounds of solid material on concrete platforms within concrete barriers. No liquid is entering the environment at large. To prevent overflow situations and accidental contamination of one liquid asphalt cement (AC) binder with another, management at Granite Construction Company Inc., Sacramento, is in the process of installing the Tank Manager™ System from Stansteel of Louisville, Kentucky, at six of its asphalt mix sites. Plant Equipment Manager Chris Herne discussed the problems and solutions of tank management, including removing human error for safety and efficiency purposes.
“If you spill a ton of AC onto the ground from your secondary containment while it’s hot, it goes under everything,” Herne explained. “It’ll cost between two and five thousand dollars a ton to clean that up. We had some plants that had continuous problems with spilled asphalt, whether that was from overfilling a tank that would ooze out The plant operator or a remote user can know the material level of the AC tanks, hot-mix silos, and dust or lime silo capacity, as this team in New York has learned. Photo courtesy of Stansteel
Chris Herne of Granite Construction Company Inc., Sacramento, (at left) and Chris Loher of Stansteel/Hotmix Parts & Service, Louisville, sat down to talk about the Tank Manager System during CONEXPO-CON/AGG 2020.
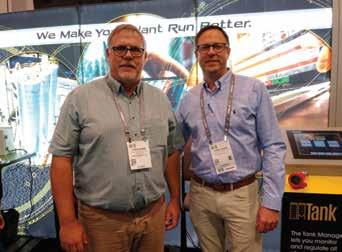
the top, spilling AC was the number one problem.
“The number two problem is that we could contaminate AC. If we paid high dollar for a polymer-modified mix and pumped regular grade AC on top of it, all of a sudden we wouldn’t have that polymer-modified to the standard it used to be.”
The Tank Manager System is designed to not only manipulate and control the valves on those tanks where it’s installed, but to also provide data on those tanks. It observes the tank—or silo—levels in real time and tracks temperatures. It will also monitor hot oil heater vitals and provides instant error alerts to team members. It also permits the tank and valve status to be monitored by authorized smart phones plus sends alerts to key personnel.
Stansteel’s Chris Loher explained: “Having the knowledge and information of what’s the precise level in AC tanks and silos can permit a much better running operation. As an example, if a paving superintendent called and asked, ‘Do you have enough mix in the silo to give me three more loads?’ most operators would not be sure unless they already had a full silo. By the same token, if a plant producer has multiple plants, and one of their other plants cannot accept the full tank truckload, it could be diverted to another plant if there was a known capacity level remaining in one of the tanks at the second plant. Without this knowledge and information the producer might incur demurrage [truck waiting charges].”
“The asphalt tank tracker takes the human side out of it,” Herne said. “It says, ‘okay, we’re going to move this asphalt out of a tank or pump this asphalt back from the batch tower.’ It’s always showing what we’re unloading and what’s in the tank already, and if those two don’t match, it stops us from making a mistake. It forces somebody to look.”
Herne explained that tanker-truck drivers, typically making deliveries at night when the plant isn’t at high production, have been known to cut corners if they aren’t being held accountable. He was quick to point out that not all truck drivers skirt safety measures, but Granite personnel have witnessed activities at unloading stations that needed to be curtailed.
“Truck drivers are paid to unload that truck,” he said. One unsafe practice that Granite management wanted to eliminate was drivers forcing an overflow situation to get their tanker trucks unloaded. They provided a system with a high-level alarm that warned when it was time to stop pumping material. The
Another benefit Granite Construction sees from the system is in overall planning. “One of the things we intend to do when all of the tank tracker systems are online, is to give certain people access to see all the plants. Our asphalt supply group wants access to the Tank Manager System so they know where they can put a block of material to store it. Winter fill rates are gone; they don’t exist anymore. We own tanks in various refineries and when they’re plumb full, and the refinery says we’re pumping into that tank, better unload it, we can send 16 trucks in and unload and put it where we know there’s room.”
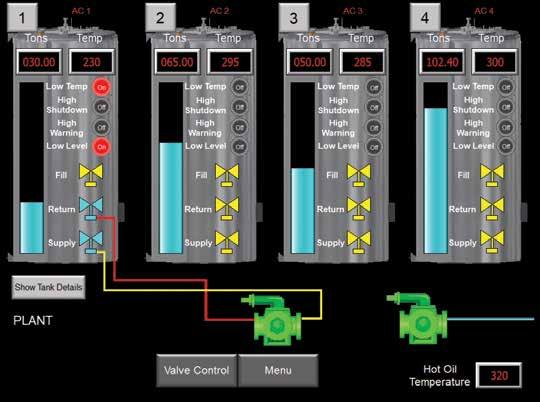
high-level alarm triggered a “stop.” Some drivers knew they could override the “stop” by holding in the starter.
“We have verified instances of when the truck driver has held the starter in so he can force the pump to override,” Herne shared. “Then he gets paid because he unloaded the whole truck, but the material went into the secondary containment and we paid dearly to clean that up.”
TANK SAFETY REMAINS TOP OF MIND
This is not only an expensive problem; it’s a safety issue Granite wished to solve.
“That’s 300 degree liquid AC,” Herne said. “I’ve never been in a burn unit myself, but I’ve met some of the guys who’ve been through that.”
The horror he described of having asphalt-soaked skin and muscle peeled with brushes from one’s body is both graph ic and frightening. About 25 years ago, a worker at the company’s Coalinga site was injured at an AC unloading station. “It was the worst accident in our histo ry,” Herne said. The worker had not worn personal protective equipment (PPE) and suffered severe burns to his face and body. A picture of that worker’s injuries now hangs at every unloading station with a reminder to all vendors and em ployees that Granite management takes safety seriously.
“On our sites, at the unload station, is a safety cabinet,” Herne explained. “And inside that safety cabinet is the full arms, full canvas, nonflammable materials for everybody, the face shields; and that’s required for everybody.”
Not only does Granite management provide the safety gear, Granite provides training for its use and for safe movement around the site.
“We do site-specific training for every person who does any work on our properties every year,” Herne said. “We bring the trucking companies into our facilities and anybody who works in that company that comes into our site has to have onsite training to be there.
“If they don’t have the right insurance, they’re not allowed on our properties. That’s set up in our purchasing contracts for the [material] and delivery.”
While Granite has cancelled trucking companies for safety violations, its team
VÖGELE ErgoPlus 3 is Paving Made Easy
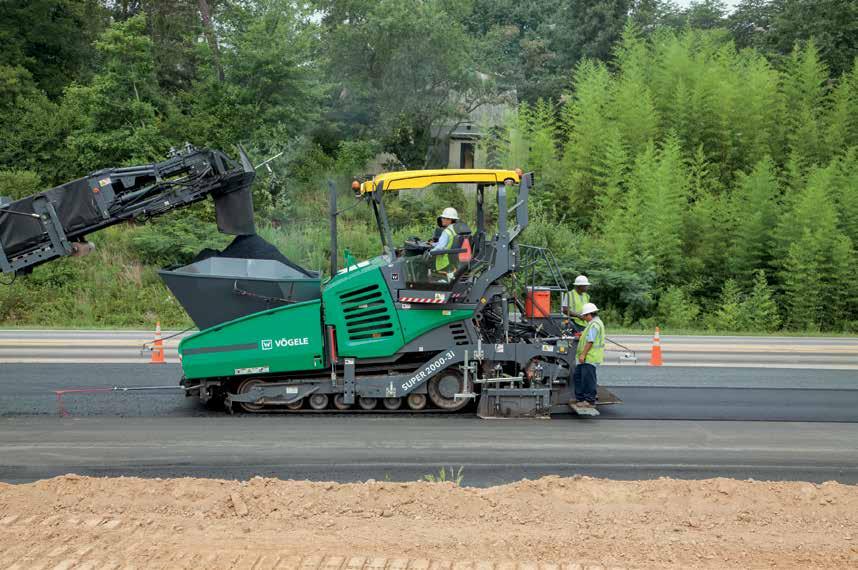
Training Made Easy Operating Made Easy Control Made Easy
Train, operate, control: do it all, effortlessly, with the world’s easiest paving operating system. VÖGELE ErgoPlus 3 offers clear and intuitive design for precise and flexible control. And there’s even an app to make learning the system a snap, available for free.
See more, do more, and get more done with ErgoPlus 3 at voegele.info/webspecial/ergoplus
will work with drivers and companies to help drivers comply with safety directives.
“If we see someone who has violated something, we’ll bring them back and ask them, ‘Why were you wearing a baseball cap instead of a hard hat? Why weren’t you wearing a face shield, because that attaches to the hard hat?’ So, we’ve retrained some [drivers]. We’ve also called trucking companies and told them which drivers are no longer allowed on our properties because they won’t comply.”
PROVING TANK TRACKING
Granite management installed the Tank Manager System at its Smith Island site in Everett, Washington, first.
“The reason we went to this plant first was because they had the truck drivers who would hold the starters in,” Herne said. “Smith Island has a concrete secondary containment that their tanks sit in. If we could get all the oil out of there and into tanks, it’s probably 20 tons worth. We’ve had spill after spill that they can’t get cleaned up and stay ahead of the truck drivers. Every time, they spill 500 or 1,000 pounds. It’s built up and solidified in the secondary containment now.”
With the Tank Manager System, the plant operator is able to monitor what’s taking place at the tank farm from the control house or from home. “The plant operator knows the night before he goes home that the drivers are coming in,” Herne said. “He sets the valves before he goes home. He can see everything from his smart phone to see that the driver’s sending material into the right tank and then into the backup tank. So the truck driver can get unloaded and get paid. The beauty of it is that the system oper ates the valves. The truck driver doesn’t have to go move the valves. The system will move to the second tank and keep going without any interaction of the truck driver.”
The ground personnel have an easier time of coordinating operation with the system in place, as well, minimizing errors and eliminating contamination.
“When our operators are running the plant from the control room…the ground man doesn’t have to climb over tanks to move valves…The operator ‘switches tanks’ off of control panels in the control room. Now the system is fully automatic. If the tank tells him he’s running out of AC,
The Accu-Level feeds into the Level Readout display. “The electric sensor is giving you the dead-on the open space in the tank,” Chris Herne shared.
The team at Granite noticed a tonnage error that occurred with one of its tanks when the material was at about mid-tank. “That’s because when we purchased the tank, it was round, but because it’s been overflowed so many times, it’s sort of bulged in the middle. The Accu-Level measures a vertical space of openness and does a calculation to tell you what volume is in there. The tank bulged from abuse and got a little wider. We re-calculated to get the real numbers dialed in. It was a problem we always had and just didn’t know it. If every tank was brand new and perfectly round, it would be easy to do the calculations, but they’ve been used and abused.”
Stansteel calibrated the system for each of Granite’s tanks. “In most cases, they can give us the dimensions and we can calibrate on site,” Stansteel’s Chris Loher said.
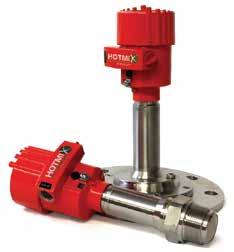
it switches automatically and the AC addition doesn’t have a gap. There’s no timeframe gap in the flow of asphalt.”
That gap in the flow matters for quality control reasons, of course. Herne explained that the ground man no longer has to remember which valve to close or open first or second. “An experienced ground man would know to open the valve and give the AC 30 seconds to flow down the pipe before he closes the other pipe so we don’t have a gap in our AC,” Herne said. This keeps the variable frequency drive (VFD) from misunderstanding the gap, ramping up the AC pump for a few seconds, and sending the new flow of AC into the mix at a very high rate for 10- or 30-seconds.
“You don’t want to see an air gap hit the pump, which is followed by a slug of AC that causes a rush resulting in 10 percent of AC instead of the 5 percent the mix design calls for,” Herne cautioned. “The Tank Manager System from Stansteel has all that built into it. And those are the kinds of efficiencies that you can’t measure. If that happens once a day, you save a couple hundred pounds of material every day. If you add that up over time, it’s a huge deal.”
Granite Construction is seeing a cost savings with the Tank Manager System in place, but Herne explained it’s difficult to put a number on. “There is a cost savings, but it’s like trying to prove a negative. Before, I could say, we had that spill and we lost x number of tons and it cost $20,000 to clean up. Now we have no spill.”
For more information, contact Chris Loher at (800) 826-0223 or visit www.stansteel.com.
Web Extra at https://youtu.be/SfZ9OOuCgLY: Watch a video from CONEXPO-CON/AGG 2020 explaining how the Tank Manager™ System parts and pieces work together.




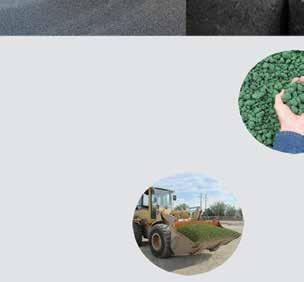


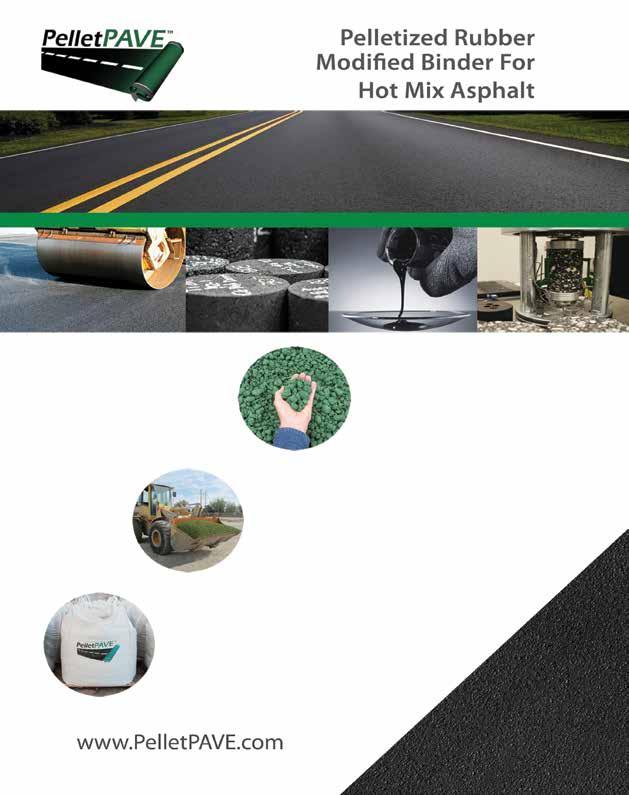