
12 minute read
SteelPhalt Gives Steel Slag a Second Life
SteelPhalt’s new Cardiff plant, a Parker StarMix 4000, can produce up to 300,000 tonnes (330,693 tons) per year. In its inaugural year, the plant produced more than 150,000 tonnes (165,347 tons).
BY SARAH REDOHL
For more than three centuries, the city of Sheffield in the United Kingdom has had an international reputation for steel making. According to the UK’s Government News Network, the Sheffield region currently produces more steel by value than at any point in the city’s history.
Although steel remains a primary industry in Sheffield, it’s also provided an opportunity for steel-related businesses to thrive.
SteelPhalt, a Harsco Environmental company, has built a successful business making use of steel slag, a byproduct of steel making. Since 1963, SteelPhalt has been using steel slag aggregate to produce asphalt at its plant 7 miles northeast of Sheffield in Rotherham.
Steel slag is a byproduct of steel making when molten steel is separated from impurities. Originally a molten liquid, the slag consists of a complex solution of silicates and oxides that solidifies upon cooling, according to the Federal Highway Administration (FHWA).
The FHWA estimates that between 7 and 7.5 million metric tons of steel slag is used within the U.S. each year, primarily as a granular base or an aggregate material in construction applications.
“From the beginning, our main purpose was to use the slag aggregate from the surrounding steel mills for asphalt projects in a 150-kilometer (93 miles) radius from our Rotherham plant,” said Julian Smith, SteelPhalt’s global strategic growth director. “That’s what we’ve been doing ever since.”
For more than five decades, SteelPhalt grew gradually, consistently and organically. Then, starting three years ago, the company began to grow exponentially as a result of increasing demand for more environmentally conscious products.
“Being net carbon zero is high on the UK government’s agenda,” Smith said. “Our products align with that goal because we are able to create a conventional product at a lower carbon footprint.” SteelPhalt estimates that its carbon footprint is 40 percent less by using steel slag in place of natural aggregate in the asphalt the company produces.
In the UK, agencies score contractors’ bids based on both cost and quality (which includes environmental impact). Although cost continues to be a major factor, Smith said agencies have increased focus on each bid’s environmental impact. “Our products provide an easy win for local authorities, since they are able to specify a greener product with no loss in quality and minimal impact on cost.”
This has been a significant driver in the company’s growth. To keep up with increasing demand, SteelPhalt has invested in two new asphalt plants since summer 2020.
NEW PLANTS, NEW MARKET, MORE CAPACITY
SteelPhalt’s existing Rotherham plant is the busiest independent asphalt plant in the UK.
With the opening of a second plant on the same site in July 2021—a Roadstar 1500 from Parker Plant Limited, Leicester, UK, capable of producing 500,000 tonnes (551,155 tons) per year—Smith estimates SteelPhalt will be able to produce 700,000 tonnes (771,618 tons) in Rotherham in 2022.
SteelPhalt’s other new plant, opened in June 2020, expanded the company into a new market in Cardiff, South Wales. The Cardiff plant, a Parker StarMix 4000, can produce up to 300,000 tonnes (330,693 tons) per year. In its inaugural year, the plant produced more than 150,000 tonnes (165,347 tons).
It’s the first permanent asphalt plant in Cardiff in over 70 years. Smith attributes this to the availability of aggregates from the region’s many quarries (limestone, granite and basalt) and the fact that the market has long been dominated by a couple large asphalt companies. Quite simply, there wasn’t a demand for steel slag as aggregate—until now.
In the past, Smith said, steel slag from Cardiff’s mills was primarily used in lower value applications, such as sub-base and general construction fill. When SteelPhalt was able to partner with Cardiff-based Celsa Steel, Smith said, “we were able to offer a solution that maximizes the value of this undervalued resource.”
Instead of getting rid of the slag, Celsa Steel can now demonstrate it is recycling the slag into asphalt mix designs. “This partnership solves a problem for them in the form of an opportunity for us,” Smith said.
As part of that partnership, SteelPhalt was able to locate its plant on Celsa’s land, “virtually in the city center,” Smith said. Historically, high land prices in Cardiff have made it more economical to haul asphalt into the city from asphalt plants located at the surrounding quarries. Now, SteelPhalt offers a more centrally-located option.
Being located in the city center, SteePhalt’s new Cardiff plant faced many strict environmental regulations, including strict control of emissions, noise, water discharge and also dust from stockpiles.
For example, the filter system is 25 percent bigger than what would usually be found on a plant this size to make sure the plant is as effective as possible at removing particulate, Smith said. They also planted trees and installed bunding around the perimeter of the plant to create a natural barrier for noise from other residents of the area.
“We also have controls over our vehicle movements and hours of operation in Cardiff,” Smith said. They have a set number of vehicles that can come in and out per day and can only operate Monday
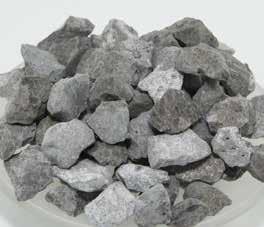
Smith said that in most of Europe, any mix that can be made with natural aggregate can be made with steel slag. This photo shows 14mm steel slag from a steel manufacturer in Port Talbot, Wales.
SteelPhalt’s mix was recently used on a resurfacing project near Cardiff Castle.
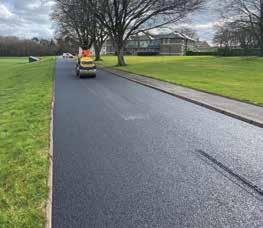
through Friday from 9 a.m. to 5 p.m. However, Smith said, they’re working with local authorities to expand their hours of operations. “We believe this constraint actually creates more pollution as a result of congestion. If we were able to extend our working window to nights and weekends, we could reduce the impact we have on commuters and day-to-day road users.”
Although Rotherham doesn’t face vehicle movement limitations, they limit running both plants at night to minimize impact on local communities. And SteelPhalt strives to make all of its plants more environmentally friendly.
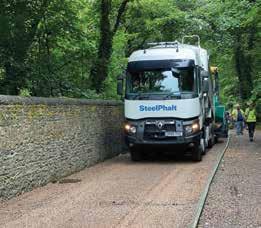
Historically, high land prices in Cardiff have made it more economical to haul asphalt into the city from asphalt plants located at the surrounding quarries. Now, SteelPhalt offers a more centrally-located option from its plant at Celsa Steel, close to the city center.
SteelPhalt’s Cardiff plant the first permanent asphalt plant in Cardiff in over 70 years.
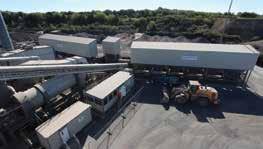
All three of SteelPhalt’s plants run on liquified petroleum gas (LPG) and are capable of producing warm mix. The temperature range to produce asphalt in the UK ranges from 160 to 190 degrees Celsius (320 to 374 degrees Fahrenheit). However, Smith said, it’s becoming more common to target the lower end of the conventional asphalt temperature range with the use of warm mix additives. SteelPhalt uses LowTherm 4G from SIMA Asphalt to produce at a lower temperature while achieving the same workability characteristics.
“Our very first ton at Cardiff was produced at a reduced temperature 20 degrees Celsius (68 degrees Fahrenheit) below traditional asphalt,” Smith said, “and every single ton produced since has been produced at that lower temperature.”
They’ve also begun to use recycled plastics to replace a small percentage of the binder at both locations. “By utilizing the properties of the selected plastics, that’s another way we can conserve natural resources in a way that is of higher value than, say, biomass usage.”
All three plants also use recycled asphalt products (RAP) in base and binder courses. “There aren’t specific limits to RAP usage as long as you can demonstrate performance, but generally we are limited to 20 percent at Cardiff and 30 percent at Rotherham,” Smith said.
“Generally, base and binder layers tend not to use steel slag because we see it as using a high value product for a lower value application,” Smith said. In Rotherham, SteelPhalt predominantly uses quarried aggregate and RAP for base and binder courses. “In Cardiff, we may use slag in base and binder courses because we have a surplus of steel slag in that market.”
MAKE THE MOST OF STEEL SLAG
Smith said steel slag is classified as a manufactured aggregate in the UK, rather than a recycled aggregate, which means there’s no limit on its use. “In Europe, any mix that can be made with natural aggregate can be made with steel slag,” he said. Most of SteelPhalt’s mixes exclusively use steel slag aggregate.
Smith regularly travels to educate industry professionals around the world on the use of steel slag in asphalt. This fall, he visited the U.S. to speak to departments of transportation in Iowa and Illinois where he highlighted how SteelPhalt uses steel slag.
The steel slag at its Cardiff plant is all produced on-site by Celsa Steel; the steel slag used at the Rotherham plants arrives from several steel mills located within 2 kilometers (1.2 miles).
“Being involved in processing our materials from start to finish sets us apart from traditional asphalt producers,” Smith said. Each batch of slag is analyzed for its chemistry, and every 15 tonnes (16.5 tons) of steel slag has a documented chemical footprint. “It’s basically a quality controlled aggregate.”
As such, SteelPhalt gives its specifications to steel mills with the specific chemical parameters it’s looking for in its slag. “If slag falls out of those parameters, they will divert that away from utilization within our processes,” Smith said. The rejected slag is still reused, only in lower value processes.
“We also have robust quality control processes to treat the slag before it comes to our plant,” Smith said, which dictate how the material is to be cooled, screened and crushed. “The beauty of slag is that, because it’s a manufactured aggregate, it’s very consistent and produces a very durable aggregate once it’s treated correctly.”
In Smith’s previous jobs in the asphalt industry, he’s seen companies accept all kinds of steel slag and use it like any other aggregate, which he cautions against. “Steel slag behaves differently from natural aggregate,” he said, “and if you can harness those differences, you’ll end up with a superior product.”

Being located in the city center, SteePhalt’s new Cardiff plant faced many strict environmental regulations, including strict control of emissions, noise, water discharge and also dust from stockpiles.
SteelPhalt claims that the shape of steel slag can improve asphalt’s resistance to rutting while maintaining a high level of skid resistance throughout the life of the pavement. “Because of the chemical makeup of steel slag, it has a high affinity to bitumen,” Smith said, adding that the alkali characteristic of the steel slag, along with an acidic bitumen, results in high adhesion. “So, it’s less prone to issues like striping.”
Smith said steel slag also tends to absorb less water, thus has a more consistent moisture content. This property reduces the energy consumption needed to dry the aggregate while resulting in a more consistent moisture content for the mix.
SteelPhalt’s technical team also produces several products using the unique properties of steel slag. One of these products, called Steel Flow, was developed when a local authority wanted a longer lasting alternative to chip seal. Steel Flow can be applied at 15 mm (0.6 inches) thick with a traditional paver while offering high skid resistance. Another custom SteelPhalt product is Ultragrip, applied at a thickness of around 25 mm (1 inch), which uses a specific type of bitumen to provide a flexible overlay on concrete.
Another difference between steel slag and natural aggregate is that steel slag is more dense. “When you’re dealing with slag aggregate, it’s naturally heavier so you need more of it to do the same area,” Smith said. “We use less bitumen per ton in a steel slag mix than in an equivalent natural aggregate mix of normal density, but that ton with steel slag doesn’t go as far, so overall we use the same amount of bitumen per square yard.”
Smith said that because steel slag is so dense and has a high polished stone value (PSV), it wears more heavily on certain parts of the plant. He estimates the mixer paddles and arms, as well as the screens, wear out 10 percent faster than with conventional aggregate. “Anywhere the aggregate is falling with velocity, weight and speed, you’ll see increased wear,” he said, adding that they reinforced several of these locations at the plant.
They also have to make modifications to their software to deal with slight differences with the aggregate density. “Other than that, there are no major differences,” Smith said. “Most of the differences relate to the science behind the aggregate itself versus at the plant.”
OVERCOME OBSTACLES
SteelPhalt faced a number of challenges getting its two new plants up and running. Opening the Cardiff plant in June 2020 was particularly difficult because it was an entirely new market for the company.
“In Rotherham, we already had a customer base and they were eagerly asking for more,” Smith said, “but in Cardiff, we were trying to bring in new customers during a pandemic when we couldn’t meet anyone face to face.” He thinks the early success of the Cardiff plant despite that challenge is a testament to SteelPhalt’s products and the plant’s convenient location in the city.
Availability of parts was a challenge for both plants as a result of pandemic-related logistical issues. Smith said patience was the key to overcoming logistical challenges. “Instead of waiting on certain parts, we looked at what we could do without those parts,” he said. For example, while they waited on a part for the RAP addition system for the Cardiff plant, they opted to retrofit the part at a later date rather than hold up the opening of the plant.
Staffing its new plants also proved challenging. Not only did they face the same workforce challenges our industry has long been experiencing in North America, but they were also facing a generous furlough scheme that Smith thinks might have kept more potential workers out of the labor force.
SteelPhalt employs 40 people across its two locations.
One solution is to attract employees from demographics who haven’t historically participated in the asphalt industry, including women. SteelPhalt is also engaging with local schools to promote job opportunities within the asphalt industry.
“The UK is facing the same issue our industry is facing around the world in attracting a younger generation,” Smith said. He said our industry tends to be branded as an old industry, so he strives in his presentations at local schools to illustrate its relevance. “I explain to them how their old cars and washing machines go to, say, Celsa Steel, where they are recycled into steel and that we use that slag to produce asphalt. So, they might be driving on their parents’ old cars. There’s a lot more interest when I start talking about how we are conserving the planet.”