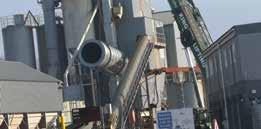
11 minute read
Change Out a Drum
Steam evacuation pipework was removed on the first day. The old drum was removed by crane on the second day.
FROM AMMANN GROUP
Ammann Group, Langenthal, Switzerland, reported on a dryer upgrade to extend the life of a plant for customer Breedon Group in the United Kingdom. The Ammann ABP Universal Asphalt-Mixing Plant began operation in 2004.
The Longwater plant, located near Norwich, England, was well maintained and had much more operating potential. Yet the dryer had surpassed its life expectancy. It was time for a replacement.
“We allowed for five days,” said Richard Coles, parts sales manager at Ammann UK Ltd. “On the first day, the steam evacuation pipework—from mixer and screen to raw gas ducting—was removed by crane, as was the suction hood. The slinger conveyor was disconnected and moved out of the dryer. “
The old dryer then was removed by crane. This was completed by the second day.
“On the third day, the new drum was positioned, and the disconnected items were reinstalled on the plant,” Coles said. Mechanical installation was finished the next day. On the fifth day, tracking was completed, marking the end of the project.
Mark Wood, area operations manager for Breedon Group, spoke of the process.
“When it was decided that the dryer drum on our Longwater asphalt plant was due for renewal, we went out for quotes for the replacement,” he said. They decided to use Ammann as the preferred supplier. There was good communication from Ammann as to lead times and delivery dates, which were all on time and as quoted, Wood said.
“The contractors (Dixon Engineering Ltd.) that Ammann used to install the drum were exemplary in providing all relevant safe systems of work and risk assessments,” Wood said. “We didn’t find any fault with their work during the entire operation. The job was completed on schedule and with no incidents.”
Coles was pleased with the smooth project as well. He counts on Dixon Engineering to handle such work. The experienced firm based in Derbyshire is committed to quality and timeliness.
“Over a period of time, Dixon Engineering has formed a strong business relationship with Ammann UK—working together to deliver time-critical projects within the asphalt industry,” said Marcus Jinks, director of Dixon Engineering. “These projects range from like-for-like replacements, retrofits and adaptations requiring various skill sets for heavy plants and equipment.”
The replacement drum on Breedon Group’s asphalt plant has a skin thickness of 15 mm and should last at least another 15 years, Coles said. “Further benefits include improved overall plant efficiency due to heat retention,” he concluded.
For more information, visit www.ammann.com.
ASTEC
The Astec M-Pack from Astec Industries, Chattanooga, is designed for quick setup. The plant has the capacity and size of a permanent facility with reduced setup costs. It is engineered as a set of modules that are transported by truck. Each Astec M-Pack plant ships in ready to set up loads when it leaves the manufacturing facility. Level and pave your site, then lift the pre-piped, pre-wired modules off the trailer and bolt them up. If you ever have to move to another site, most loads fit on lowboy type trailers and the built-in foundations go with them. The Astec M-Pack features high-production, large capacity, full-size control rooms, high-quality components, and excellent maintenance access, according to the manufacturer.
For more information, visit www.astecindustries.com
CATERPILLAR
Caterpillar announced its new compact wheel loaders May 4 with an expected arrival date in the United States and Canada in fourth quarter 2022. The 906, 907 and 908 are the updated machines built in Lester, England, and featuring new amenities for operators as well as enhancements to hydraulics. All three machines offer air conditioning as an option and a spokesperson explained this “has been upgraded versus the previous HVAC system by +60% increase in performance.”
Also check out the LED roading and working lights, some of which can be rotated 90 degrees and feature light guarding for extra safety.
The 906 has an 18.5-gallon fuel tank, which represents a 30% increase over the earlier model. The 907 and 908 models have 24-gallon fuel tanks. None of these require DEF fluid.

The Astec M-Pack asphalt plant is engineered as a set of modules and can incorporate one of four exclusive mixing systems: Double Barrel, Double Barrel X, Double Bareel XHR or UniDrum.
CRUSH RAP COSTS
with the HONEY BADGER
From replaceable abrasion-resistant steel wear liners to a 1/2" steel pulverizing hopper, this machine is ready for wear and tear. And by reducing material handling and minimizing moisture, the Honey Badger increases production and saves on fuel costs. Average return on investment is 1/8 the cost of other crushing operations. Fully-equipped with max power, reliable operation, and easy maintenance, the Honey Badger is ready to crush your costs!
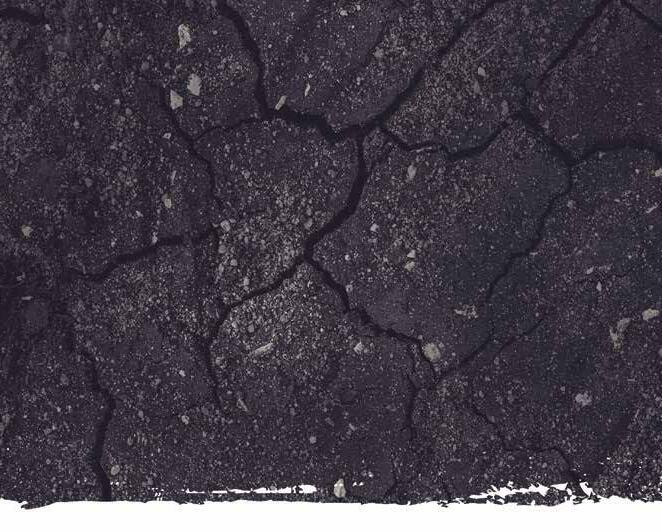
Reduced RAP moisture = lower fuel consumptions
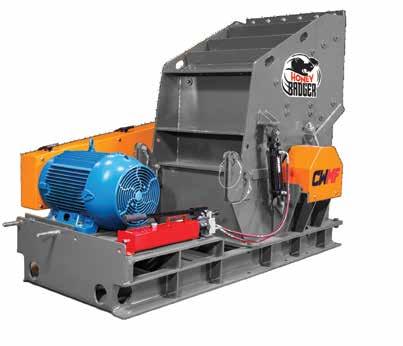
Reduce or eliminate crushing costs
Typical 6 month ROI
(300,000 ton/season plant)
Minimize material handling
STATIONARY PORTABLE
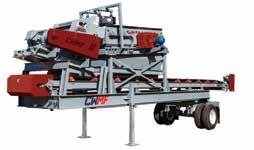
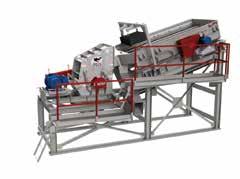
All three models offer touch screens in the cab and touch-screen controls for operators. If the owner wishes to assist new operators, he can “lock the system” into a simplified mode. A representative explained, “This can be done in the field via a service menu, which has a separate password that an administrative fleet manager could know. Dealers aren’t required in this instance.”
For more information, contact your local Cat dealer.
CWMF
CWMF, Waite Park, Minnesota, now offers a fines metering system for its portable Dust-Eater® baghouses, allowing producers better control of fines and reducing set-up time. As mix designs evolve, controlling dust is imperative to producing a quality product that will meet specifications. This device is designed to consolidate a remotely located dust pod and additional augers. It works when baghouse fines are first conveyed to the discharge auger on the baghouse. The discharge auger has a drop-out point where the dust will be stored in a small pod. This pod will have a rotary vane feeder attached, which will meter the amount of fines returned to the drum. If you are producing more fines that you are returning, the auger will bypass the dust pod, discharging them to a wet auger. At this point, water will blend with the fines, and it can be rejected.
For more information, contact sales@cwmfcorp.com.
EVOQUIP
EvoQuip, a Terex Company, launched its “Think Green, Think EvoQuip” campaign in April 2022 and with it demonstrates continued growth by creating equipment that is increasingly sustainable, according to the manufacturer. The compact crushing and screening brand have also posted a sustainability responsibility statement on their website stating 4 key commitments.
For more information, visit the EvoQuip website.
HONEYWELL
Honeywell, headquartered in Houston, has introduced the Honeywell Safety Watch, its real-time location solution (RTLS), to help drive safety and security and boost workforce efficiency. Supporting continuous operational improvement, the Safety Watch gives organizations actionable information on their workers and assets to help meet the demands of modern industrial operations.
Leveraging Honeywell OneWireless™ infrastructure, the solution is designed to work with all major industrial wireless standards; the Safety Watch uses active wireless tags integrated into employee badges and Honeywell’s OneWireless multi-protocol infrastructure. The infrastructure also supports other applications such as instrumentation, control and mobile devices.
“Our new Safety Watch RTLS helps organizations improve compliance, productivity, security and the safety, reducing the risk of incidents, and if one should occur, enabling a quick and effective response,” said Nisha Lathif, safety solutions business director, Honeywell Process Solutions. “Providing relevant information and real-time data processing, Safety Watch is purpose-built for industrial settings.”
Real-time location data is an integral part of the Industry 4.0 ecosystem, which combines the latest technologies and digital capabilities to tap into data anywhere and everywhere. RTLS meets this need

The Honeywell Safety Watch technology is designed to give organizations actionable information on workers and assets, leveraging the OneWireless infrastructure.
to help organizations achieve digital transformation through the industrial Internet of things.
For more information visit https://bit.ly/3afGayN.
INGEVITY
Ingevity, North Charleston, South Carolina, announced May 12 an environmental product declaration (EPD) was published for its Evotherm® M1 Warm Mix Asphalt (WMA) technology. The Evotherm M1 EPD distinguishes Ingevity as the first chemical additive supplier to be included in the National Asphalt Pavement Association’s (NAPA) Emerald Eco-Label tool that provides supply chain-specific upstream environmental data for asphalt mixes. The EPD for Evotherm M1 denotes Ingevity’s compliance with environmental impact assessment standards for manufacture of the warm mix additive by measuring and reporting the cradle-to-gate impacts of manufacturing and packaging, and assessing the material, energy, waste and emissions impacts of processing and transporting the raw additive materials.
“Ingevity’s decision to publish the EPD for Evotherm M1 demonstrates the industry’s commitment to transparency and sustainability,” said Richard Willis, NAPA’s vice president for Engineering, Research, and Technology. “Additionally, it aligns with NAPA’s The Road Forward initiative, which launched this year and challenges the asphalt pavement community to achieve net zero carbon emissions during asphalt production and construction by 2050.”
Another company committed to The Road Forward is Kokosing Materials Inc., headquartered in Westerville, Ohio. A spokesperson for Ingevity shared that Kokosing Materials recently decided to use exclusively Evotherm WMA technology at all 18 of the company’s asphalt plants for complete warm-mix production in an effort to reduce their carbon footprint and move towards a more sustainable mix design. Watch for that full story in the August edition of AsphaltPro.
For more information, visit https://www.ingevity.com/featuredproducts/evotherm/
PHCO
Process Heating Company (PHCo), headquartered in Seattle, offers Lo-Density® Drop-in Tank Heaters for 100%-efficient heating of asphalt and emulsions in both underground tanks and distributor trucks. The Drop-in Heater is designed to be installed by simply dropping it through the tank’s manway and attaching it horizontally to the tank bottom. If needed, multiple heaters can be laid end-to-end using flexible high-temperature power leads.

PUGMILL SYSTEMS
We’ve been designing and manufacturing custom mixing solutions in Tennessee for nearly 40 years.
RCC • CTB • Pugmix • Stabilized Sand
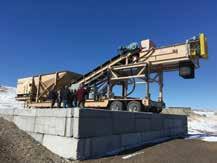
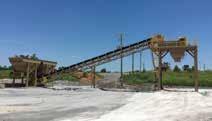
Coldmix • Fly Ash • Salt Treatment

Rental Plants Available
Check out additional projects at: PUGMILLSYSTEMS.COM or give us a call at: 931-388-0626

The Lo-Density Drop-in Tank Heaters from PHCo offer electric, drywell-style heat for underground as well as above-ground tanks and distributor trucks.
Producers know of the numerous benefits underground asphalt storage tanks can provide. Lo-Density, electric, drywell-style heat requires no permits or stacks, requires little maintenance, and is always 100% efficient, according to the manufacturer, but the Lo-Density Drop-in Heaters are also appropriate for above-ground applications, including static installations up to 50,000 gallons, as well as distributor trucks. The heaters install the same way as in underground tanks. Above-ground tanks must have a minimum of 3 inches of fiberglass (or similar) insulation and weatherproofing.
Drop-in Heaters from PHCo are available for tank capacities ranging from 1,000 gallons to 50,000 gallons, and they will maintain temperatures from 125° F to 325° F. The heaters’ recommended capacities include sufficient heat to maintain the temperature shown, plus a reserve capacity for heat-up requirements. The Drop-in Tank Heater kit includes a UL-Listed control panel with digital thermostats for tank content temperature control. The complete kit includes heaters, controls, temperature sensors, wiring boxes, and transition fittings for the tank top. As with all of its heaters, PHCo stands behind its equipment, offering a one-year element replacement guarantee.
For more information, call 866-682-1582 or visit www. processheating.com.
RUBBLEMASTER
Rubble Master, Ennis, Texas, announced it is elevating the service and operating experience for users through its digitalization, electrification and automation efforts with the launch of the RM XSMART telemetry & fleet management product, which is designed to help contractors get more clarity about their operation, to identify blind spots and improve processes. It also assists operators with more information about the condition of their machines to become more proactive and accelerate service processes. RM XSMART is available as an app on your phone or your desktop computer to access machine data anywhere, at any time. Operators can monitor fuel levels, reset belt scales, and track tonnages with an optional belt scale from their cab. RM XSMART documents machine use such as run time, operating hours and tonnages, which can be shared with your client or back-office. The operator can choose between a job report that documents the progress of a specific job or a daily report that summarizes the day’s achievements.
For more information, visit the Rubble Master website.
GTB-5543E
Hauck® StarJet 580 Burner with TBA-36-100 Blower
GTB-5542
Dillman® 400 TPH Highly Portable Parallel Flow Drum Plant
GTB-5540I Cedarapids®/Standard Havens® Nominal 60,000 CFM Portable Baghouse
GTB-5516D Astec® 200 TPH Double Barrel Stationary Counterflow Drum