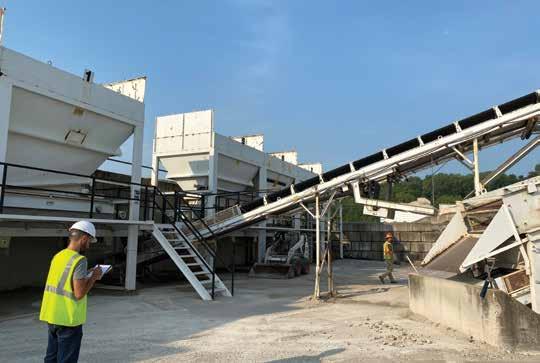
5 minute read
New Frontier Materials Updates Controls for Quality
Mike Raasch, the controls engineer and project manager at WEM Automation, double-checks the cold feed sensors. All photos courtesy of WEM
FROM WEM AUTOMATION
You’ll know when the time has come to update plant controls. For any number of reasons, you may have put it off as long as you could, but now it must be done.
The question becomes, how much of the system do you update? Do you update your entire operation with “full plant” controls, or do you update a portion of your plant and keep its overall existing architecture? This is a common query facing many asphalt producers, and one that deserves significant analysis and planning. After all, you will be working with and using this system for many years to come.
Moving to a modern plant control system will require a move from the manual style push button controls to a new paradigm. The on-screen, human machine interface (HMI)/graphical user interface (GUI), full plant type of automation control takes away the multiple panels of buttons and toggles. James Keene, the general manager of asphalt operations, and his crew at New Frontier Materials, Fort Belle, Missouri, started with that idea.
The New Frontier Materials team was operating with a plant control system that dated back to 2004. They were experiencing many technical issues and running the risk of product replacement availability and obsolescence.
Keene noted, “the lack of online and technical support to keep up with an older system was definitely a push to make the upgrade.”
Keene and his co-workers were looking for a new system that was not only suitable for their current needs, but one with the necessary support service and flexibility that would carry them for years to come.
The decision to shift from push-button to on-screen full plant automation seemed like a natural and wise progression for New Frontier Materials, especially since they already had familiarity with this style of controls at other plant sites. Regarding any fears or hesitations with making the move, Keene mentioned, “There was no hesitation
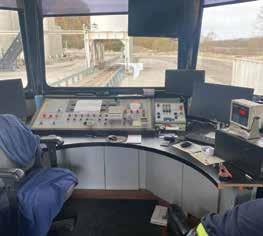
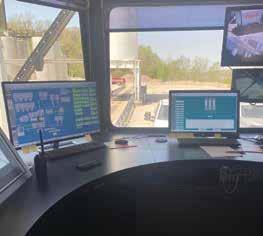
The control house before a controls upgrade may be chaotic with older, lower-grade wiring. Once the upgrade takes place, a neat and tidy setup not only carries signals and electric load more efficiently, but it also offers a safer, cleaner, more organized environment for business, setting the operator up for success.
with getting rid of buttons. No fears whatsoever. Our experience with WEM and success at other sites using this type of control has given us full confidence. We knew that this is what we wanted to do—an easy judgement call.”
Dave Kelling, plant superintendent at New Frontier Materials’ Fort Belle facility, also commented on the move to on-screen full plant automation. “The switch to get rid of buttons was natural—just have to be a computer-friendly user. Most operators coming in have those basic computer skills.”
After using their new system for a bit, Kelling declared the controls user-friendly. “I have a new guy that I am training, and he has caught on very quickly. WEM does a good job of breaking the plant down by use of tabs.” Kelling continued, “Anyone who can turn a computer on can run a WEM system.”
A key component in any successful controls replacement project is paying close attention to detail and doing the site-specific homework. Mike Raasch, controls engineer and project manager for WEM Automation, noted: “No two plants are exactly the same. Taking the time to learn each plant from electrical layout to component makeup and material flow is essential. There are no shortcuts here if you want a happy customer.”
To that end Keene added, “the whole WEM team, from sales, to engineering, to their service and technical staff were all extremely helpful...We have leaned on WEM’s expertise, and they have come through with questions we have had.”
“Another important opportunity when updating to new control systems is the ability to utilize many new sensors and IoT type technologies that, when designed in a new control system, can provide instantaneous, important feedback, and information to operators all in one easy to view location,” Raasch noted. “Things like material temperatures, bin levels, valve position, and on-screen ammeters are easily incorporated into today’s modern designs.”
We all know when it comes to plant controls, functionality and reliability are of course key. However, the professional image that these new systems offer can be a big bonus as well.
A modern looking plant not only communicates to your team that you are interested in investing in their work environment but can also be a statement piece when vendors and customers come calling. Many control rooms tend to be very cramped spaces filled with paperwork and all sorts of panels and gauges added over the years. The change to on-screen full plant automation can provide much needed room and give a clean, organized look to the workspace.
Some advice from the New Frontier Materials team for others who are considering how and what to upgrade or replace in their plant control system was, “don’t be scared about the switch, it’s not going to change how your plant operates. It will provide you with more information on what the plant is doing,” Keene noted.
LEARN MORE
3 Components to Controls Success Today
1 When you update your plant controls, consider both the hardware and software portions of a controls package. The risk of component obsolescence and operating system support is an important factor to consider. 2 The flexibility or ability to adapt and add to the system should also be explored. Will you be able to add features onto this system at a future date to meet your and our industry’s requirements? 3 Finally, does this controls vendor offer the level of service and support from its on-site and remote technical support teams you will require?