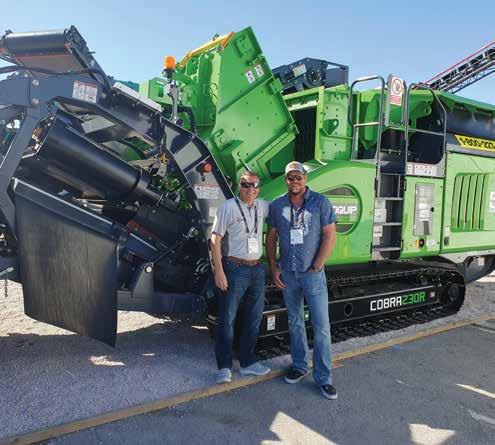
4 minute read
Asphalt Outlaws and Production Scoops
EEvoQuip, a Terex brand, has helped Outlaw Excavating, Tucson, Arizona, grow into its asphalt, concrete and rock applications. Outlaw Excavating was founded in 2005 by Cody White who, born and raised on a farm in Kansas, found himself operating machinery for many different agriculture applications. He relocated to Tucson to join an IT company with the goal of progressing toward a career in architecture. However, he was soon employed by a company specializing in pool construction. By 2004, White had the confidence to establish his own company, Outlaw Excavating, which specialized in pool construction.
Fast forward to early 2020, and White had a job contract that required over 5,000 yards of screened dirt and gravel, which saw him approach Gerald McCarthy of Powerscreen Western, a Terex distributor representing Powerscreen and EvoQuip equipment across Arizona and part of Nevada.
McCarthy recommended a Colt 600 for the job—a compact, forward-facing screen designed for aggregates, sand and gravel, top soil, construction demolition and recycling applications where site space is at a premium. While being the smallest scalping screen in the EvoQuip line up, its 308TPH output potential pleased White. He said, “It still impresses me today what that little screener can do, and it can even go on a tagged trailer.”
White began bringing materials back to his yard in Tucson, originally consisting of gravel and dirt but he soon recognized the need to recycle concrete, rock and asphalt from his job sites. By 2021, White was removing so much concrete, rock and asphalt from job sites, he needed to rent a crusher to process the material. From that, he began making spec materials that he could not only use on his own job sites, but could also market to other contractors in the construction industry.
“It was a game changer for us to be able to use our own materials,” White said. “Gerald provided a Powerscreen 320 Trackpactor for the rental and brought with him a lot of training and support for a customer who was new to the crushing industry.”
By the end of 2021, with the COVID-19 pandemic in the rearview mirror, Cody decided it was time to own a jaw crusher for the concrete, rock and asphalt applications he was dealing with. McCarthy supplied an EvoQuip Bison 280 jaw crusher—perfect for an entry level contractor that is looking for a jaw that can be closed in tighter to make reusable products.
The growth story of Outlaw Excavating continues in 2022, with the decision to purchase a compact impact crusher to make dense grade products from his concrete and asphalt. Their choice was an EvoQuip Cobra 230 with a 4-bar rotor and hydraulic controlled aprons. “Having both the jaw and impactor allows us to handle a bigger variety of inbound materials while making better spec’d products for our job sites and for our customers,” White said.
Andrew Lawrence, EvoQuip sales director for North America said, “EvoQuip offers a comprehensive portfolio of products to address the needs of the compact crushing and screening markets. The impressive growth story of Outlaw Excavating shows how our equipment is ideal for companies new to our industry who are keen to grow and diversify their portfolio of equipment to tap into new markets.”
A host of original equipment manufacturers (OEMs) specializing in best and most efficient production are featured on the next few pages. Check out their iron and services and let them know you saw them in the pages of AsphaltPro magazine.
Astec
Astec Industries showcased at CONEXPO-CON/AGG 2023 the new Heatec Portable Polymer Blending System, which the company described as “compact enough to fit in a shipping container or trailer so you can take polymer blending where you need it.” The system includes two 1,700-gallon heated tanks with two polymer mixers per tank. The Barracuda® mill, rated at 150 horsepower, is situated between the tanks with power and control panels situated behind it. This compact configuration ships in a standard, 40foot, open-top cargo container.
For more information, visit https://www. astecindustries.com/products/details/heatecpolymer-blending-systems
Brock
BROCK, a leading supplier of equipment, parts and on-site construction services for hot-mix asphalt plants, is pleased to an- nounce Lance Clark as its new regional sales manager—Southwest. He takes over the states previously covered by Sales Representative Phil Hoffman, who will be helping Clark as he transitions into the area. Clark’s territory includes the states of Texas, Oklahoma, Arkansas, Louisiana, Mississippi and Alabama.
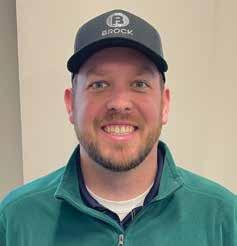
For more information, contact (423) 476-9900.
Conveyor Components
The Model RS pull cord, manufactured by Conveyor Components Company, Croswell, Michigan, is a safety stop control designed to provide a quick, positive shut off of dangerous equipment in emergencies. It is actuated by a cable pulled by endangered personnel. The outputs of the Model RS can control up to four separate circuits, depending on the model chosen. These alarms can include one for machinery shutdown and one for alarm. The Model RS control is designed to act as an emergency stop for conveyors and other moving machinery.
This standard housing construction is corrosion resistant cast aluminum, with an optional polyester or epoxy powder coating. The operating handle must be manually reset after the problem has been corrected.

For more information, contact (800) 233-3233.
Kenco
To extend the performance of components at the asphalt plant, Kenco Engineering offers tungsten carbide impregnated (TCI) wear strips in lengths up to 10 feet long. The TCI wear strips are welded in places of high wear on steel surfaces, using any low hydrogen rod or mig wire. In many asphalt plant applications, the strategic placement of just a couple TCI wear strips can break the channeled flow of materials that cause severe wear problems, according to the manufacturer. Wear strips are particularly effective on flop gates, elevator bottom areas, and all high wear areas where materials land after leaving a belt, bucket or chute.
For more information, visit www. kencoengineering.com/.
Surface Tech
Surface Tech, a provider of long life, low carbon asphalt solutions for the asphalt industry, is pleased to announce the adoption of the ASTM Standard D8395-23 for Aramid Fibers in Asphalt Mixtures. https:// www.astm.org/d8395-23.html This standardization sets a dosage of 2.1 ounces per US ton mix for aramid fibers, ensuring a consistent and uniform application of this low carbon performance additive.
The standardization of aramid fiber dosing is important for state department of transportation (DOT) projects, city