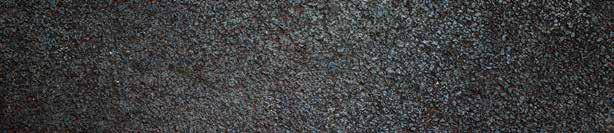
8 minute read
Sustainability Tips for Asphalt Plant Dryer Burners
BY MALCOLM SWANSON, P.E.
TThe most fun I ever had during my years with Astec was when participating in the development, building and testing of burners. In addition to having fun, we built some really fine burners, including some that established the definition of “world class.” That is a good thing, because a burner is a necessary part of every asphalt plant.
From time to time, I receive a request for guidance about purchasing a new burner. When I ask what the purpose of purchasing a new burner would be, the answer is usually “fuel efficiency.”
Here is the first truth. Fuel efficiency is seldom a valid reason for changing burners. Notice that I did not say that it is never a valid reason but changing burners to reduce the fuel bill is usually disappointing. All good burners are capable of burning all the fuel and getting all the heat release when properly adjusted and operating in their efficient operating range. The differences are in emissions, noise, electric power consumption and the size of the efficient range or “sweet spot.”
BURNER TYPES HIT THE SWEET SPOT
To do a useful job of covering this subject, I need to mention the different types of burners that are available to the asphalt plant market. Almost all burners for this market are either hybrid or total air burners. These two terms refer to how they handle combustion and excess air.
Hybrid burners, like the well-known Hauck StarJet, have an integrated blower that introduces part of the needed air and have provision for the rest of the air to be “induced” or sucked in around the burner body and heat shield by the exhaust fan.
Many people refer to this type of burner as an induced air burner, but that is incorrect. An induced air burner has no blower at all. As far as I know, there are no induced air burners in service in the U.S. market.
Total air burners, as the name suggests, bring in all of the combustion and excess air by an integrated burner blower.
Both of these two burner types can burn a wide range of fuels including recycled fuel oil (RFO), No. 2 oil, propane and natural gas.
Typically, total air burners have better control of fuel/air ratio than hybrid burners. A burner of either type can do a great job when it is on ratio but it is easier to keep the total air burner on ratio across more of its firing range.
Hybrid burners are generally less expensive than total air burners. The extra money goes into the more complete control of air. The ability to control air throughout the firing range makes it possible to have a large operating sweet spot. Hybrid burners have a relatively narrow portion of their firing range where they are on ratio and highly efficient, but within that sweet spot there is no measurable difference in fuel efficiency as compared to total air burners. Some hybrid burners have a bigger sweet spot than others. Those that provide a larger percentage of the air through the blower tend to have a larger sweet spot, making it a good thing to ask about before buying. The size of the sweet spot is very important, because any burner can be inefficient when operating off ratio.
Unfortunately, if you ask this question by using my “sweet spot” terminology, the burner manufacturer may not know what you are talking about. If you are considering a hybrid burner to control cost, just ask what percentage of the air is provided by the burner blower. A correct answer to that question will tell you which burner has the optimum sweet spot.
There are two major subtypes of total air burners—nozzle-mix and premix. These terms may not be familiar to some but they are easily explained.
In a nozzle-mix burner, the fuel and air are kept separate until the fuel exits the fuel atomizing nozzle at the nose of the burner. In a premix burner, they are brought together and mixed at some point upstream of the nose of the burner.
I believe the cleanest burning, quietest and most efficient burners available are of the premix type. You might think it makes sense then that everyone should go with premix, but there are several reasons to carefully consider that option.
The most important thing that premix burners can do that nozzle mix burners cannot do is operate with ultralow emissions. However, in most parts of the world, that level of performance is not yet required. Premix burners are expensive; so why pay the price if you don’t need the performance. The day is probably coming when it will be needed everywhere but we are not there yet. This means the right burner to buy depends on where the plant is located and how it will be operated.
In California, New Jersey and a few other places, a premix burner may be the only type that can meet the emissions limitations. On a portable plant operating on long stretches of highway in less populous areas, the plant may operate wide open all day. The burner is called upon to almost always operate pretty much in the same narrow part of its firing range. A hybrid burner will be a good choice. A plant in a city may be up and down a lot and operated at different rates. A total air burner will enable efficient operation over a wider range. If noise is a critical issue, total air burners are generally quieter and premix burners are quietest of all.
Some burner blowers are constant speed with air flow control by means of a damper while others use a variable speed drive (VFD) to control air flow by adjusting blower speed. VFD air flow control reduces electricity consumption and reduces noise. It also offers more precise control of air flow than is possible with damper control, and therefore, better control of fuel/air ratio.
Choosing the right type of burner does not ensure that you making the best choice. Some burners of any particular type are just better than others of the same type. If certain aspects of performance are critical, get the applicable data. If, for example, you need ultralow
NOx emissions capabilities, get data. Stack test reports are generally public information that can be accessed through state websites.
The performance of burners, like anything else, depends upon the quality of engineering and manufacturing invested in it. Some fuel nozzles atomize fuels better than others. Some premix burners mix the fuel and air better than others. Intimate mixing of fuel and air in the correct ratio is critical to performance.
As you can see, selecting the right burner is not a simple matter but it is an important one. Every manufacturer rightly wants to sell their own products and can provide good reasons why you should buy theirs. My somewhat self-serving advice is get independent expert help in making the right choice. I say “somewhat” because I am certainly not the only available expert.
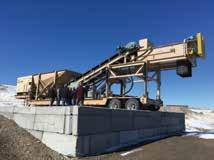
FACTOR IN EXHAUST GAS TEMPERATURE
Now, let’s go back to the beginning of this article where I mentioned that the reason most folks want to change burners is to improve fuel efficiency. If you want to make significant simultaneous impacts on your bottom line via fuel efficiency and on sustainability via carbon emission reduction, don’t look to the burner to do it. It is just a popular myth that seems to persist. You can mess it up with the burner; but the presumption at this point is that you have a decent burner and have it properly adjusted. What matters after that is that you make the best use of the heat provided to the process by the burner. Assuming complete combustion of fuel, fuel efficiency can be summed up in three words: exhaust gas temperature.
Having an exhaust gas temperature of 350oF is bad; 220oF is good; 180oF is better; 160oF is best. Before you write me off as being nuts at this point, because you know that my better and best numbers will make mud in the baghouse, hear the rest of the story.
The dew point temperature of asphalt plant dryer exhaust gases is usually about 165oF but may be much lower, depending upon the moisture contents of the virgin aggregates and recycled asphalt pavement (RAP). If you know where your dew point is, it is possible to operate safely at these “better and best” exhaust gas temperatures.
Some pretty big energy savings are available if you can get your exhaust gas temperatures down, and they aren’t just in burner fuel savings. Significant electricity savings are automatically included in this deal through reduced power needs at the exhaust fan motor and at the burner blower motor, if both are speed controlled by VFDs. You will also see production rate gains in many cases.
Reduced fuel bill, reduced power bill and selling more mix equal more money in your wallet. These reductions also mean less carbon released into the atmosphere at your plant and at the power plants providing your electricity. This might be another good place to be “somewhat” self-serving by offering expert help. Telling you what to do is easy. Telling you how to do it is more dependent on your situation.
Malcolm Swanson, P.E., is the proprietor of e5 Engineers, Chickamauga, Georgia. With at least 33 innovative patents and a career in asphalt plant engineering solutions, he can be reached at (423) 667-6781 or malcolm@e5engineers.com.
PUGMILL SYSTEMS
We’ve been designing and manufacturing custom mixing solutions in Tennessee for nearly 40 years.
RCC • CTB • Pugmix • Stabilized Sand
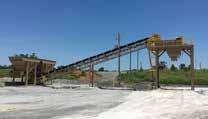
Coldmix • Fly Ash • Salt Treatment

Rental Plants Available
Check out additional projects at: PUGMILLSYSTEMS.COM or give us a call at: 931-388-0626