
14 minute read
City Asphalt Celebrates Staten Island Plant
CITY ASPHALT CELEBRATES CITY ASPHALT CELEBRATES STATEN ISLAND PLANT STATEN ISLAND PLANT
BY SARAH REDOHL
City Asphalt's new plant was delivered in August 2019 and erected that fall.
FFrom the first day City Asphalt began to lease Vanbro Corporation’s asphalt plant property on Staten Island in 2018, company officials knew it was only a matter of time before they’d replace the 70-year-old batch plant on the property.
City Asphalt LLC, owned by the Cruz family and a leader in the New York City construction market, saw a shining opportunity beneath the rust of the old plant. Located along the west shore of Staten Island, the facility has barge and rail access and is also located just off the
West Shore Expressway, making it an attractive supplier for paving contractors in Staten
Island, Brooklyn and Manhattan. Despite being rebuilt three times during its 70 years in operation, the batch plant had sat unused since around 2010 and was in need of major repairs when the Cruz family took over.
Bringing the old plant back to life was no easy task. “It was much more expensive over the long term than buying a new plant,” said City
Asphalt General Manager Matthew Cruz. The Vanderbilt family, under the name of VANBRO Corporation, operated an asphalt plant on this 42-acre property as far back as 1947.
All of the wiring had to be replaced, much of the equipment was rusted out, the control room needed to be repaired and the computers replaced. “It was like playing Whac-AMole,” Cruz said. “When we fixed one thing, another thing would break. We ended up virtually rebuilding the entire plant from scratch.”
It was a necessary, albeit temporary, hardship.
“The plan was always to build a new plant once we could get through the arduous permitting process in New York City,” Cruz said. They immediately began working toward obtaining the necessary permits in 2015.
In the meantime, they had to rely on the old batch plant in order to serve their customers, including an annual supply contract to provide 150,000 to 200,000 tons of asphalt for the New York City Department of Transportation’s operations in Staten Island. That was in addition to another 50,000 to 100,000 tons for City Asphalt’s private customers.
The NYC DOT owns and operates two of its own asphalt plants, one in Brooklyn and one in Queens, contracting out mix supply for the other three boroughs of Manhattan, the Bronx, and Staten Island.
Despite their numerous improvements, the old batch plant was often a source of frustration and expense. For example, when the old batch plant’s gearbox broke down, they needed to immediately source a suitable replacement. Ultimately, they found a 40-year-old gearbox on eBay that had been sitting in a ga-
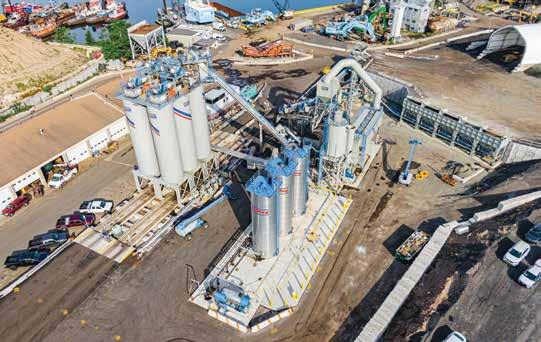
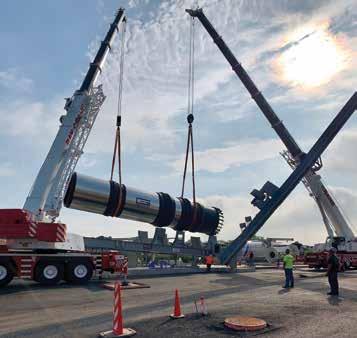
ABOVE: When City Asphalt began leasing the Vanbro Corporation’s asphalt plant property, they knew they’d have to replace the 70-yearold batch plant. LEFT: The Cruz Family was able to self-perform the construction of their new plant, which expedited the construction schedule. They were able to advance the schedule to get the construction completed in 11 months.
rage in Oregon. The gearbox itself cost only $800, but overnight shipping it to New York City cost more than $4,000. To add insult to injury, it was too heavy for a single shipment overnight so it had to be disassembled and sent as four separate packages then reassembled upon delivery.
“All of these breakdowns were transpiring under a penalty with our NYC DOT contract,” said City Asphalt’s Director of Business Development Tom Dooley. “If we couldn’t provide them with the material they needed, we’d get a violation that came with a significant penalty.”
Naturally, City Asphalt was eager to get its new 400 tph Gencor Drum Mix Ultraplant up and running, and so was the NYC DOT.
And construction never stops in the city that never sleeps. In total, New York City resurfaces more than 6,000 miles of streets
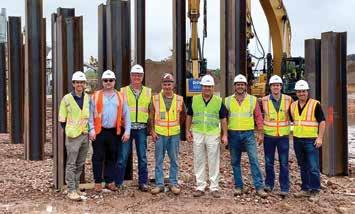
LEFT: City Asphalt decided to purchase their plant from Gencor, Orlando. RIGHT: The Cruz family’s construction team breaks ground on the construction of the new plant. Due to the poor soil conditions, extensive piling was required to be driven to bedrock to support the weight of the new equipment. Pictured from left to right: Chris Lada, Peter Lauro, Chuck Lada, Grahame Turnbull, Evarett Cruz, David Cruz, Matthew Cruz and Carlos Catao
LEFT: The plant has six heated 300-ton capacity silos, organized into two lanes. One lane is dedicated to their biggest customer, NYC DOT, and the other for private contractors. RIGHT: City Asphalt’s crew regularly had to repair the old batch plant.

and highways, resulting in resurfacing that requires over 1,000,000 tons of asphalt annually, according to the NYC DOT. Not only does the city have high traffic density and allow for heavier truck tonnages than many other states, Dooley said, but its roads are often dug up to access water and gas lines, or, as is increasingly the case, to install technology infrastructure such as 5G.
“The NYC DOT saw the issues we were facing with our old plant in order to meet their demand,” Dooley said, adding that they were supportive throughout the process of permitting and building City Asphalt’s new plant. “They wanted to see our new plant operating on Staten Island because it’s easier for them and their crews to access asphalt in the local market, without having to traverse toll bridges to New Jersey or Brooklyn.”
PREPARE TO PERMIT
Despite NYC DOT’s support, there was a long road ahead. “It took about two years to obtain the required construction permits. We were going back and forth with engineers, design consultants, various NYC and New York State (NYS) agencies, and even simply choosing a location on the 42-acre property to build the new asphalt plant before we could break ground,” Cruz said.
At first, the design consultants identified that the location the company chose for the new plant would have required a modification to the tidal wetlands permit, which would have added three years to the permitting process. “Therefore, we took drone photos which we imported into AutoCAD to overlay the new plant in various locations of the property,” Cruz said. “This allowed us to perform feasibility studies to determine the most efficient use of space on the property.”
“We were able to determine the most effective traffic flow pattern, the widest turning radius for large dump trailers and stay away from various property limits and protected wetland areas,” Cruz said. After the feasibility study, it turned out that the best location to construct the new plant required City Asphalt to tear
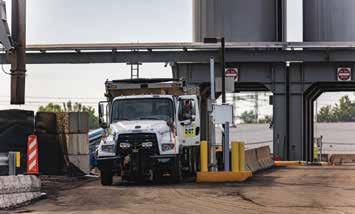
LEFT: City Asphalt has an annual supply contract to provide 150,000 to 200,000 tons of asphalt for the New York City Department of Transportation’s operations in Staten Island. RIGHT: City Asphalt’s new 400 tph Gencor Drum Mix Ultraplant became operational in March 2020.
down the existing 5,000-square-foot office building. This involved yet another building permit. “In the interest of making the process as streamlined as possible we were forced to compromise on things.”
The property was low-lying, so City Asphalt needed to perform extensive work in order to comply with modern day regulations. One of the permits required the company to elevate its facility by four feet. After Hurricane Sandy in 2012, the Federal Emergency Management Agency (FEMA) required all new construction to be above an elevation of 12 feet above sea level, and City Asphalt’s old facility was only eight feet above sea level.
City Asphalt also had to install 280 piles in the foundation, requiring more than 1,000 cubic yards of concrete, and develop a plan to seismically engineer their plant in case of earthquakes. The company hired a structural engineer to work with Gencor to develop a plan in compliance with NYC Department of Buildings (NYC DOB) requirements.
Utilities presented another obstacle. City Asphalt had to run new natural gas lines to the plant, which required approval from the Fire Department of New York (FDNY). They also needed a stormwater pollution permit from the New York State Department of Environmental Conservation (DEC) and an air pollution permit from New York City Department of Environmental Protection (NYC DEP). Once everything was said and done, City Asphalt had worked with almost a dozen agencies, including the NYC DEP, FDNY, NYS DEC, NYC DOT, NYC Small Business Services (NYC SBS) and NYC DOB, among others.
Thankfully, the permitting process for the plant itself wasn’t as difficult. “Because we were able to shut down the old plant when we started using the new plant, that wasn’t too big of an issue,” Cruz said. All they needed was a permit modification from the old plant to the new. Plus, the new plant was more environmentally friendly to begin with and required less energy with its variable frequency drives (VFDs). “Our old plant required a 2000-kw generator, but the new one only needs 800 kw.”
The plant itself was delivered in August 2019 and was erected throughout the fall. However, New York City’s crane permits presented an unexpected last-minute challenge. City Asphalt had to get multiple permits and get their cranes signed off by a master crane rigger before they could lift the silos and drag slats.
After the wiring was completed in early 2020, a Gencor representative was on site programming all the computers (the plant uses Gencor’s Ultralogic control system). By February, they could power up the plant, but they still had no gas.
“The city doesn’t allow gas valves to be opened during the cold winter months, so we had to wait until March 1,” Cruz said. “We could spin the drum and turn the drag slats, but we couldn’t produce mix until March.”
Then, they hit another snag. The day before they were to open up the plant, the Gencor rep they’d had on site for months was called back to Gencor’s home offices because of the COVID-19 pandemic. “We basically opened up the plant by phone and FaceTime,” Cruz said. “Literally, we were FaceTiming our Gencor rep as he told us what buttons to press, what settings to change. We even calibrated our burner remotely via FaceTime.”
“When we constructed this plant, we spared no expense,” Cruz said. City Asphalt’s decision to purchase their plant from Gencor, Orlando, came down to word of mouth. “We’d been hearing their service and reliability was the best in the industry.”
Another benefit of the Gencor plant is its capacity to manufacture asphalt with a high recycled asphalt product (RAP) content of up to 60 or 70 percent. The NYC DOT requires a minimum of 40 percent RAP in its mixes.
“RAP utilization is a huge issue in New York City because as part of our asphalt supply contract with the city, we are responsible for taking in the millings they produce before putting down fresh asphalt,” Dooley said. “That’s an expensive proposition because every acre of land we lease comes with a very high price tag.”
City Asphalt chose to invest in Gencor’s Advanced Rap Entry system, which allows the company to fractionate its RAP. The drum is equipped with two RAP collars, one for 1/4inch minus fine RAP and one for 5/8-inch minus coarse RAP. “We can make a much higher quality mix by using the correct percentage of those two separate products,” Cruz said. “This is particularly useful since using fractionated RAP allows for a more consistent product.”
City Asphalt followed National Asphalt Pavement Association’s best practices by providing a tent to cover the RAP and
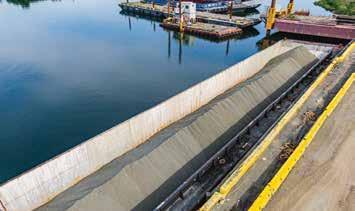
Located along the west shore of Staten Island, the facility has barge and rail access.
additionally paved the entire RAP and virgin aggregate storage bins with 8 inches of asphalt with a significant back pitch slope so rainwater could easily drain through the aggregate. Using these methods, they were able to maximize the efficiency of their operation and significantly lower energy costs in heating aggregate. The plant is also equipped with a flue gas system, blue smoke recovery system, and VFDs in the drum, drag slat and baghouse.
The plant has six heated 300-ton capacity silos, organized into two lanes. One lane is dedicated to their biggest customer, NYC DOT, and the other is for private contractors.
“We can make 5,000 tons per day without any issues,” Cruz said. Dooley added that another asphalt plant in the city that can only accommodate one lane through the plant often sees trucks backed up onto city streets. “We have plenty of room on our 1,500-foot driveway for trucks to queue, if needed.”
TURN ON THE HEAT: REALIZE THE REWARDS
Lower Your Operating Costs Improve Your Product Quality Reduce Your Maintenance Needs Enjoy Decades of Trouble-Free Efficiency Improve Your Sustainability

Lo-Density® Is Better!

Our 100%-efficient Lo-Density® drywell-style electric heaters provide safe, clean, reliable, and cost-effective heat — making them the best choice for heating your asphalt tanks, hot oil circulating systems, fuel oil preheaters, distributor trucks, and more.
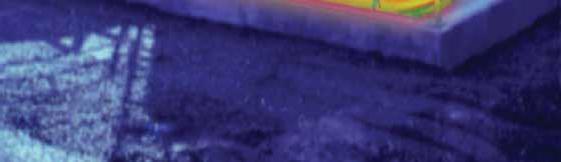
866-682-1582 info@processheating.com
PROCESS HEATING COMPANY www.processheating.com
TOP: City Asphalt paved the entire RAP and virgin aggregate storage bins with 8 inches of asphalt with a significant slope for rainwater to easily drain away from the aggregate. BOTTOM: City asphalt followed best practices by providing a tent to cover the RAP.
Additionally, the ability to store 1,800 tons of asphalt in the air has helped the company minimize its labor cost.
Its NYC DOT contract requires availability for day and night jobs. The old batch plant could only produce 120 tph and store a maximum of 500 tons, so City Asphalt required both a day and night crew. With the six silos at the new plant, they can produce product during the day and store whatever might be needed to serve those night contracts, which means they no longer need to staff a full second-shift crew.
To further improve loadout, City Asphalt invested in a Silo Safety System, which ensures that silos can only be opened once the truck below is in the proper position, and the Generation 3 Silo Loadout from Libra Systems, a subsidiary of Command Alkon, Harleysville, Pennsylvania.
“This modern day technology really helps speed up traffic through our facility,” Cruz said, “especially with COVID-19, since trucks can drive in and out without physical contact with plant staff.”
City Asphalt also designed its operations with redundancy in mind. They have a spare electrical motor and gearbox for every single component of the plant. “It’s like having a spare asphalt plant sitting on the ground just in case something breaks down on the new plant,” Cruz said.
Although the plant primarily runs on natural gas, the company invested in a diesel-powered generator as a backup. They also have two wheel loaders at the plant, alternating between the two each month with one in use and one parked as a spare.
City Asphalt’s new plant relies on the same lab that served the old batch plant, with some improvements to accommodate for increased production. In the future, they plan to build a new state-of-the-art lab and expand into different mixes, including Port Authority and Federal Aviation Administration (FAA) mixes.
Other future plans include the addition of two to four additional silos, two cold feed systems and a fourth AC tank. “This will allow us to increase our production to meet demand, or to expand into other work like FAA or Port Authority paving,” Cruz said.
Despite plans for future growth, the team at City Asphalt is proud of what they’ve accomplished in the plant’s first season. “And that’s despite COVID-19,” Dooley said.
Connect With Us!
Stay in touch with AsphaltPro between issues where you can find how-to content, trends and technology, and industry insight.
The Recycling Issue
The Production Issue
E.T. Simonds Shares Plant Moves PRODUCTION – PROFESSIONALS – PRODUCTS IR-Dry RAP asphaltPROasphaltPRO Experts Share Their Secrets For Equipment Staging Success PRODUCTION – PROFESSIONALS – PRODUCTSasphaltPROasphaltPRO
Seal the Southeast
• How to Protect Feed Sensors • Overlay Ultimate Maintenance • Here’s Your Next Best Investment • How to Incorporate Asphalt in Freight
JANUARY 2017 WWW.THEASPHALTPRO.COM • How to Build an ADA Ramp• How to Rejuvenate Your Recycling• C.W. Matthews Crushes Pavement Maintenance
FEBRUARY 2017 WWW.THEASPHALTPRO.COM
facebook.com/ AsphaltPro
bit.ly/AsphaltPro LinkedIn
theasphaltpro.com
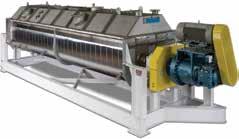