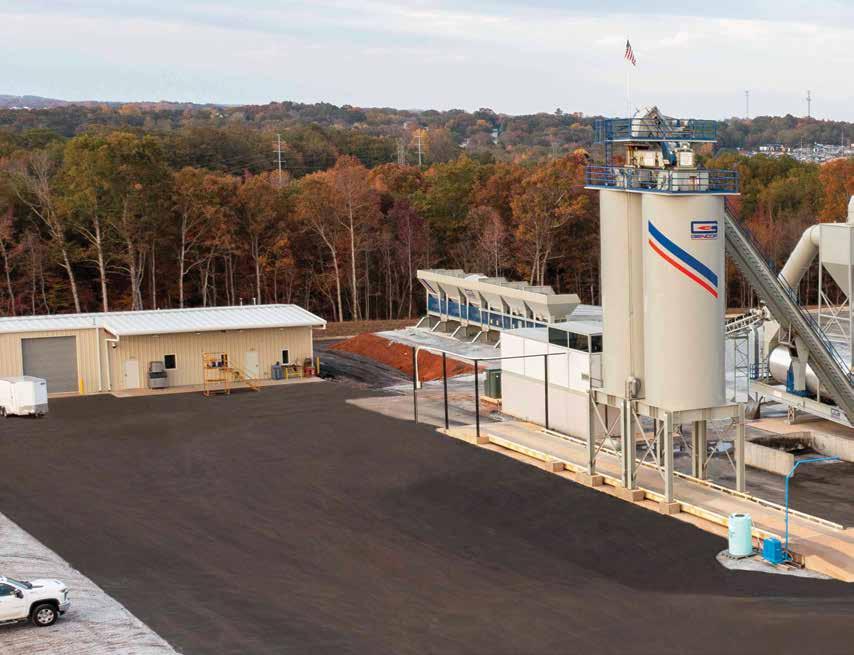
6 minute read
PALMETTO COMPLETES SUCCESSFUL BUILDS PALMETTO COMPLETES SUCCESSFUL BUILDS
BY SANDY LENDER
TThe team at Palmetto Corporation, headquartered in Conway, South Carolina, has managed steady growth over the years. When management saw opportunity in the market at the outset of the 2020s, they reached out to long-time partner Gencor Industries, Orlando, to get the ball rolling on updates and ideas. Among the results of that partnership is the new plant installation creating jobs and facilitating infrastructure development around the city of Greer, South Carolina.
Market Forces
Ray Mothershead is the manager for all the plants for Palmetto and he spoke of the leadership that brought the Greer plant to life. His words portrayed nothing but respect and admiration for Shawn Godwin, CEO and owner of Palmetto Corp., and the person he commended for finding the spot.
“We knew where we wanted to go,” Mothershead said. “We had that confidence. Shawn said this is the market we want to go to. He lays out the vision and we follow it. We have relationships with customers and the DOT around the area and he saw that in the market.”
Godwin spoke of the area as well. “South Carolina is a great place to live and do business. We have known this for years but now the rest of the world is starting to see the potential. This has led to remarkable economic growth, specifically in the Upstate market. Our new asphalt plant in Greer will allow us to service this area.”
Having relationships means taking care of the community, even before you arrive with the iron. “Do your community awareness before you buy,” Mothershead suggested. “Get out there in your community and do your due diligence. We just gotta be a good neighbor.”
Part of being a good neighbor is letting the community know you’re there for them. Mothershead said, “We hire their sons and daughters. Shawn gives to the local baseball teams.” Other examples he shared included having local elementary school kids come to the plant for field trips, which gives teachers, children and parents the chance to learn more about the positive job source in the community.
Updates And Capacity Increases
Other projects getting updates while the Greer plant was underway included the Orangeburg property for Palmetto. Gencor’s Mark Spicer, who is based in Ocala, Florida, visited the Orangeburg site with Mothershead to assess what the team required there.
Around December 2020, the teams rebuilt a used plant out of Michigan for the Orangeburg site, Spicer said. He listed the drum, baghouse, cold feeds, recycle bins and drag as used components that came from the existing Michigan plant; the liquid asphalt cement (AC) tanks, silos, control house and cables were components that were required to complete the plant that Gencor supplied. These were the remaining components that Palmetto ordered through one person in the Gencor parts department so everything would be under one code and not overwhelming for either party.
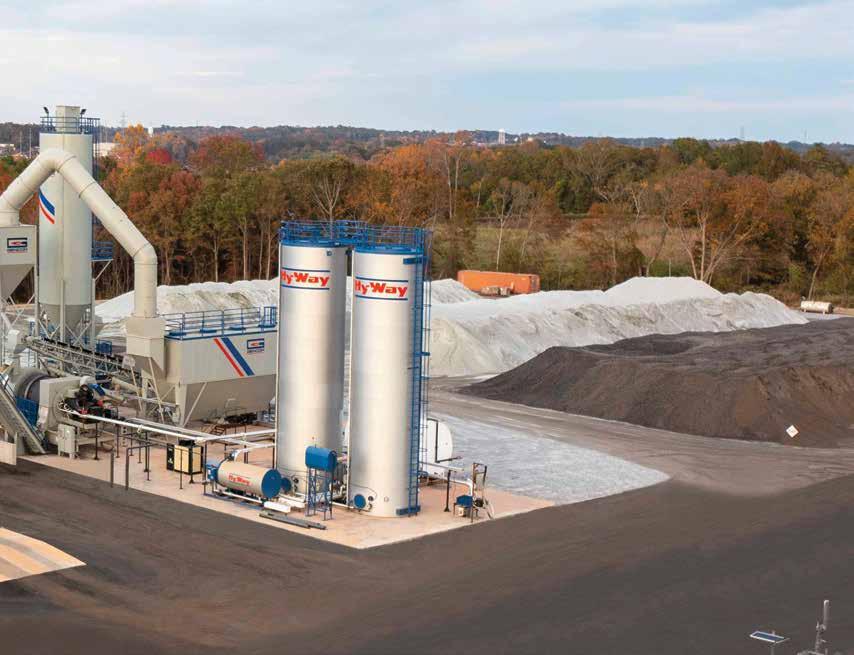
Spicer said they had everything evaluated and ready to order by April 2021. “All the manufacturers were way out on delivery by then,” Spicer said. “We needed about eight months for the new pieces.” By January 2022, the Orangeburg plant was ready to set up.
“We started to put the Orangeburg plant up in January [2022],” Mothershead said. “We ran it in March.” He stated that “getting the transformer was a problem,” and the team ran into the same delay with that component when working on the final elements of the Greer plant installation.

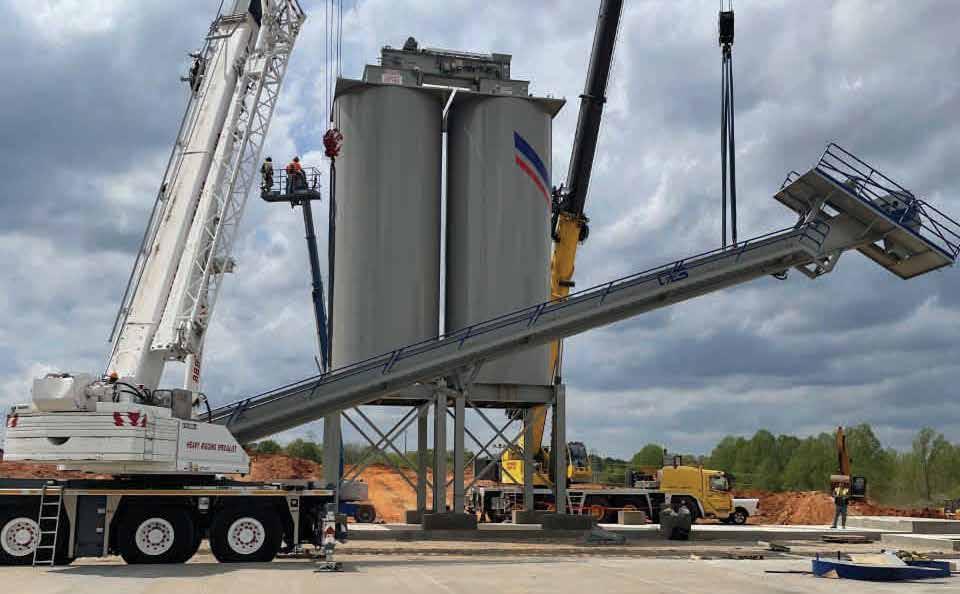
“They [transformers] take time to get in because of the current supply chain,” Mothershead warned. And that’s something to be mindful of these days.
NEW PLANS, NEW PLANT, NEW CREW
Something else to watch out for is extraneous permit requirements. While both Spicer and Mothershead explained the building permit was not in hand when Palmetto ordered the Greer plant in August of 2021, the process would be straight-forward. Mothershead spoke of the process as almost “easy if you do your due diligence,” but also said the process started “right after we bought the plant.” There was no waiting around to get the permitting process off the ground.
“The permitting process is no different than any other phase of the project,” Godwin shared. “It always takes a team effort to get to the finish line. Wade Kennard spearheaded the permit process and pulled in other resources as needed. The permit process took about nine months.”
Mothershead listed other team members who were integral to the process. “There were other people who didn’t go to the city council meetings but helped out, like Eric Faulk and Mark Nye.”
“Make sure that the land you’re buying really is heavy industrial,” Mothershead cautioned. “When you’re going to buy a piece of land, buy as much of it as you can and make yourself a buffer. Follow the policy to the letter. We’ve got a great team here with great relationships. As long as you meet the criteria, you can get the permit.”
With the building permit in hand, and the plant going up, the Palmetto team faced an interesting twist from the city. “You can buy the property and do the sitework and start erecting the plant, but you still need the operational permit,” Mothershead said. “The control tower has to have an engineer sign off on it. Gencor thinks ahead and already did that. We never encountered that because we put plants up in a county. This was scrutinized by the city of Greer. But the control tower? Gencor already knew about it.”
The plant will also need utilities to operate. As mentioned above, getting a physical transformer in place took a bit of time due to the supply chain challenges we’ve seen lately. “It sat waiting for utilities; just needed gas and power for getting it turned on,” Spicer said.
They achieved the operating permit from the city in July, ran test mix, and were making mix by August 2022. That bit of delay gave way to a stellar new installation for Palmetto—one that shows off the teamwork of a blended crew.
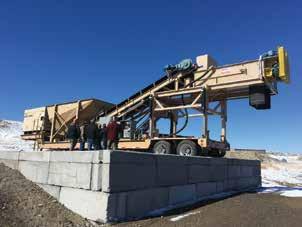
Sources spoke proudly of the team at Palmetto. “Their own inhouse maintenance crew did the install,” Spicer said. “Gencor was
We’ve been designing and manufacturing custom mixing solutions in Tennessee for nearly 40 there for putting the iron up and for setup, but their [Palmetto’s] people did the install.”
TOP: In this image, you can see the attention to detail that Gencor’s Mark Spicer commended the Palmetto team on. Piping around the plant included insulation that will keep fuel use down. Not only is this a nod to good long-term cost management, but it’s also another way to manage one’s overall carbon footprint. BOTTOM: The control center is a split-level design allowing the operator a 360-degree view of the entire plant. The motor control center is situated on the lower level of the unit. All control centers are pre-wired from the factory for fast setup and operation, and that proved handy for the Greer facility when it came time to grab the final operational permit.

He said they did it the right way, too, taking the time and spending the money “upfront” to handle details such as insulating all the piping. By insulating and jacketing piping around the tank farm and elsewhere, the Palmetto crew minimizes heat loss and keeps fuel consumption—thus costs—down for the future.
“One goal with the Greer build was to do it better than the one before,” Mothershead said. “We wanted to be more efficient...and we were. And we brought some new people on board and they did great. They help fulfil our company’s needs.”
Mothershead is a self-proclaimed asphalt fan who loves this industry. He looks for people who know how to work together for the good of the industry, the good of the company and the good of each other. “The guys we brought on worked great. They’re a great bunch of guys working it out. There’s gotta be a bridge between family and work. We hire great people with skills. Building strong relationships with team members. Bringing everyone’s skills to the project.
“I’m very proud of the men and women who work in the plants with me. They’re the ones who do the work these days.”
End Goals
At the end of the day, the Palmetto team overcame supply chain hiccups and a twist from the city with the help of their long-time partner and succeeded in a new plant installation. They have a new Ultradrum® plant from Gencor rated at 300 tons per hour with two silos with a storage capacity of 400 tons.
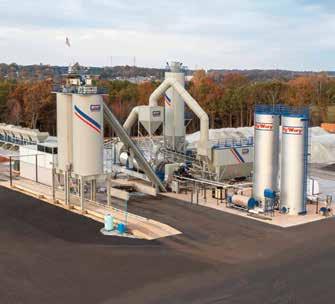
“We don’t put asphalt plants up to sell mix,” Mothershead said. “We put up asphalt plants to support our crews.” He shared the plants feed both customers and Palmetto crews with about 80% supplying all their work from their plants.
The end goal, he said: “Be efficient, get the mix out the door and get paid for every drop of it.”
After two years of testing the top asphalt rejuvenators in mixes with 40% RAP, Invigorate beat the competition by 300%.
For more information on the results, call us at 1-888-663-6980.
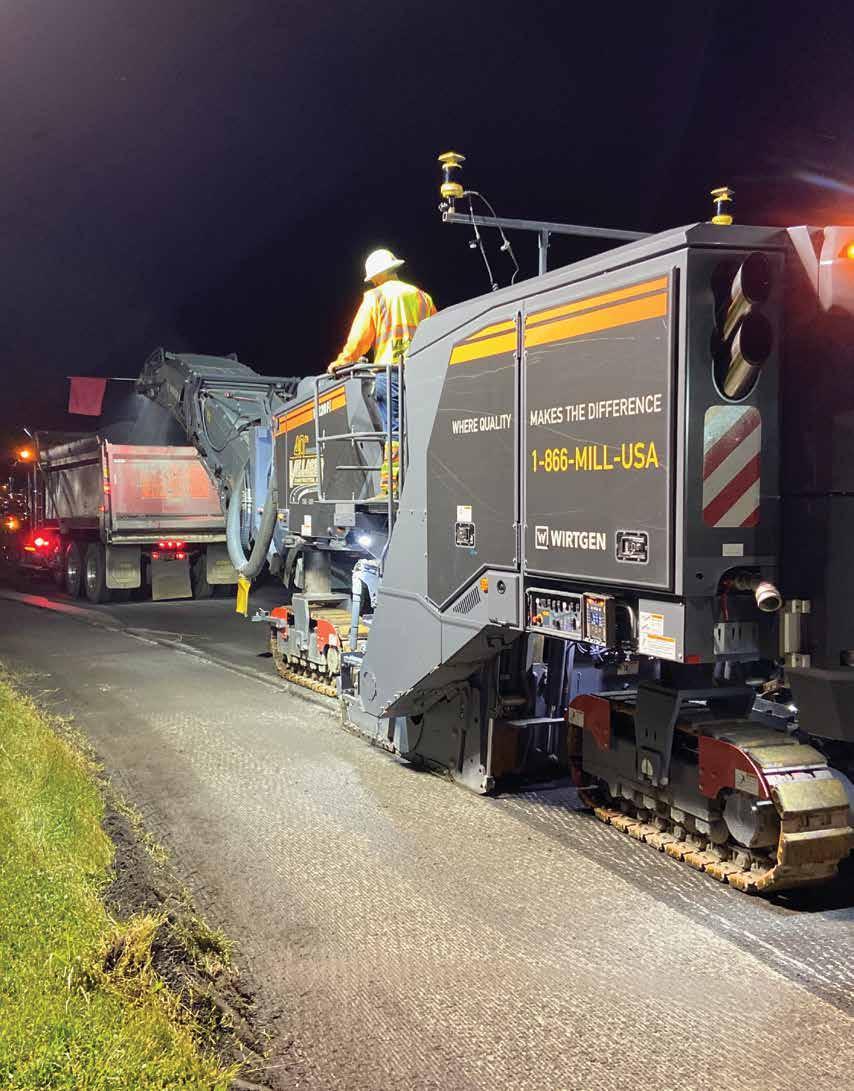