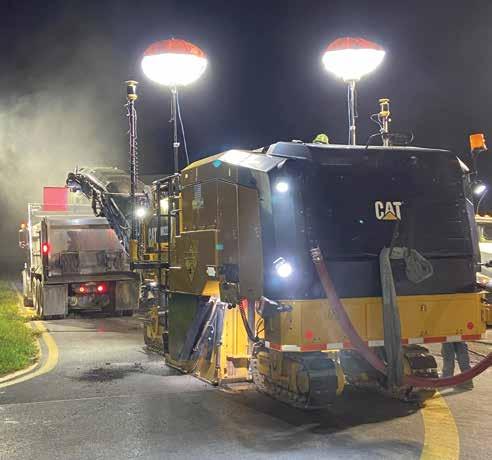
5 minute read
U
Urgency drives most any airport resurfacing effort. Even in cases when the facility has the luxury to totally shut down for the duration of the resurfacing, the pressure is on to reopen and restore flight traffic. For times when contractors don’t have that luxury, and work is done in a segmented fashion between temporary closings, steady production is key.
On a recent taxiway resurfacing project at Albany International Airport (ALB), general contractor Rifenburg Construction, Troy, New York, faced some of those daunting logistical challenges as it worked to mill and pave one of the facility’s main taxiways. Aided by the use of a 3D machine control system controlling both milling machines on the project—including the first Wirtgen 210 Fi in North America to be so outfitted—the company and its subcontractor easily handled the profile milling effort and completed the project on time with excellent results.
The Setup
Located just north of downtown, ALB serves as the major air center for New York State’s Capital Region, as well as the northeastern part of the state, and Western New England, handling roughly 1.5 million passengers annually. Built in 1908, ALB is the first (and still the oldest) municipal airport in the United States. While much has changed since then, the very numbers that confirm its success also dictate the difficulty of scheduling regular maintenance on its runways and taxiway surfaces.
“One of the real challenges after winning the bid for the Taxiway ‘A’ Rehab Project, as the job is known, was getting the necessary work done in a severely constricted time frame,” said Darin Cooper, Rifenburg’s superintendent. “We were limited to performing between 10:00 p.m. and 5:00 a.m. In that time, we had to get out to the area being resurfaced, set up, do all the required milling, clean out the area after milling, tack it, pave it, get it striped, and move off. That’s a whole lot of activity to complete in such a short period.”
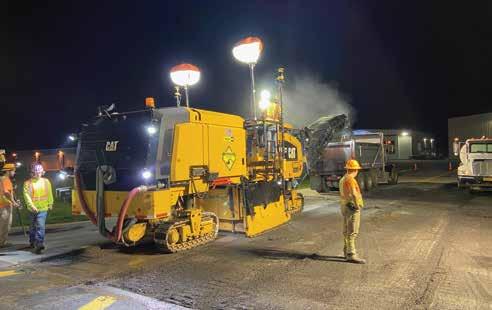
Considering it took 20 to 30 minutes each for setup and breakdown, he added, the crew was actually only left with about six hours to do everything mentioned above. “It was an exercise in efficiency, for sure,” Cooper said.
ABOVE: Here you can easily see the receivers atop the CAT PM822 as it prepares to mill with 3D milling precision. AT LEFT: The team said this was the first W 210 Fi to be outfitted with the Topcon 3D machine control system in the United States, showcasing the two OEMs’ compatibilities. They installed a valve switching unit to control the electronic automation on the CAT PM822.
It Takes A Villager
While Rifenburg counts milling as one of its core strengths, for the ALB airport job, because of equipment availability, it found it necessary to subcontract out a portion of the milling effort to Villager Construction, Fairport, New York. With nearly 30 machines at work throughout New York State and up and down the east coast, Villager is a milling force to be reckoned with. Under normal circumstances, using a sub of that caliber would have been a straightforward arrangement. At ALB, however, additional factors had to be considered, according to Mike Momrow, a Topcon professional services manager.
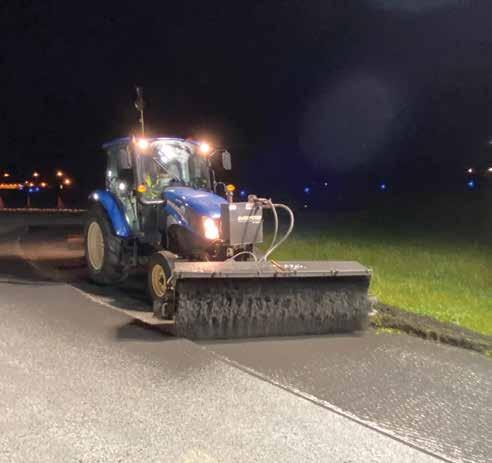
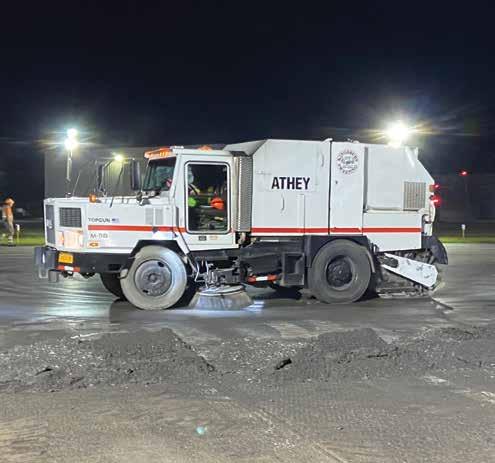
“Rifenburg decided early on that a profile milling approach would be best to correct a number of surface irregularities that had been identified in the initial survey design,” he said. “So, well before the project started, we met with representatives from Villager to discuss ways in which the Topcon Millimeter GPS solution could work with a new Wirtgen 210 Fi they’d just purchased. At the same time they were using that machine, however, Rifenburg would also be milling with a Cat unit, so there was a compatibility concern to address.”
For some, integration difference between the two machines could have presented problems. However, the combination of the Wirtgen unit’s CAN interface and the plug-andplay design of the Millimeter GPS solution resolved any concerns about “playing nice with others.” For Rifenburg’s Cat PM822 machine, Momrow said, a relatively old-school approach solved the compatibility concern.

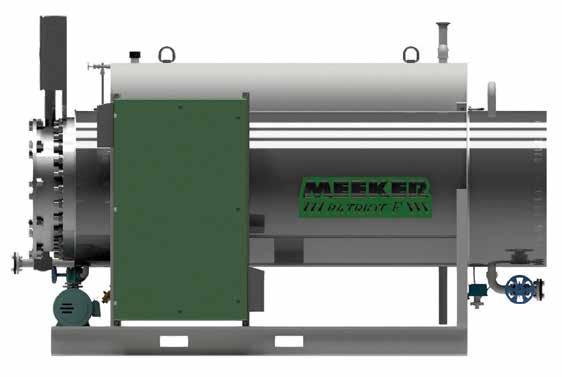
“For the Cat [machine], we installed a valve switching unit to control the machine’s electronic automation,” he said. “So, while the two platforms were completely different, they were both able to work off the same digital model and get equally impressive results. It worked like a charm and, despite being new to the technology, Villager’s crew really took to it after just a couple basic sessions on operation.”
Long Overdue
If the Albany Airport project had a theme, it might have been “It’s about time.” In addition to aptly describing the tight work window faced every night, it also summed up the taxiway’s overdue need for repair. While the 01/19 runway was resurfaced in 2015—a project Rifenburg also headed up—the adjacent taxiway was not. The need for improvement was showing in many areas, according to Brian McGrath, Rifenburg’s survey manager.
“There were many cracks in the taxiway surface, some of which had grass growing through them—that’s never a good thing,” he said. “And, based on some areas that had standing water after a heavy rain, there were also some grade issues that needed to be corrected. So, it wasn’t a typical ‘mill-and-fill’ where we could just track the existing surface, mill 2 inches and put back 2 inches. It needed a profile-based solution, which played perfectly to the strengths Millimeter GPS brings.”
Variable Depth
The solution the crews of both Rifenburg and Villager drew upon—Millimeter GPS—augments the benefits of GPS positioning technology with a zone laser reference to improve the vertical accuracy of the milling machine. Working off an initial survey design, Rifenburg simply ran a minus 2-inch offset from proposed grade and both units milled to that design grade.
“Running off that model made all the difference on the taxiway project,” McGrath said. “I’m sure there’d been some basic mill-andpave resurfacing in the past—without any changes for grade issues. Now, however, in order to get the necessary grade corrections, we were milling anywhere from less than an inch in some spots to as much as 5 inches in others, all while trying to maintain a 1:1.5 slope to the edges. Without the Millimeter GPS solution, it would have been extremely difficult.”
The benefits realized through use of Millimeter GPS were many. In addition to bringing the taxiway up to standard and correcting the long-standing drainage issues, the solu- tion both streamlined the milling process and resulted in material savings.
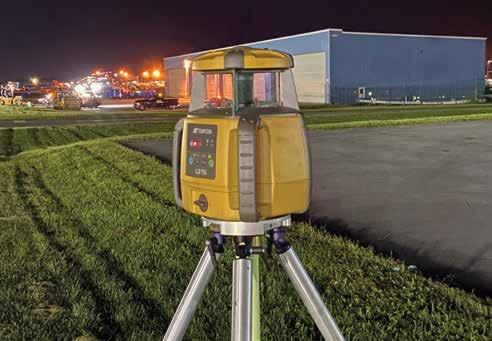
“Profile milling with Millimeter GPS results in a much higher degree of accuracy,” Cooper said. “Because the accuracies are so tight to the design, the amount of asphalt needed to get back to grade is reduced, saving the owners money. On a project in which we paved anywhere from 500-650 tons per night, material savings are welcome.”
Though Rifenburg Construction is a seasoned user of Topcon millimeter-grade mill- ing and paving solutions, this was Villager’s first foray into the 3D realm. According to Momrow, the company’s status as a major milling services provider added an element of interest to the Albany project.

“Villager owns and operates more than two dozen machines up and down the east coast,” Momrow said. “Until now, they’ve never made a commitment to adding 3D control to one of their machines. So, we wanted to make sure they realized the full benefits our solution can provide, and I know we did.”
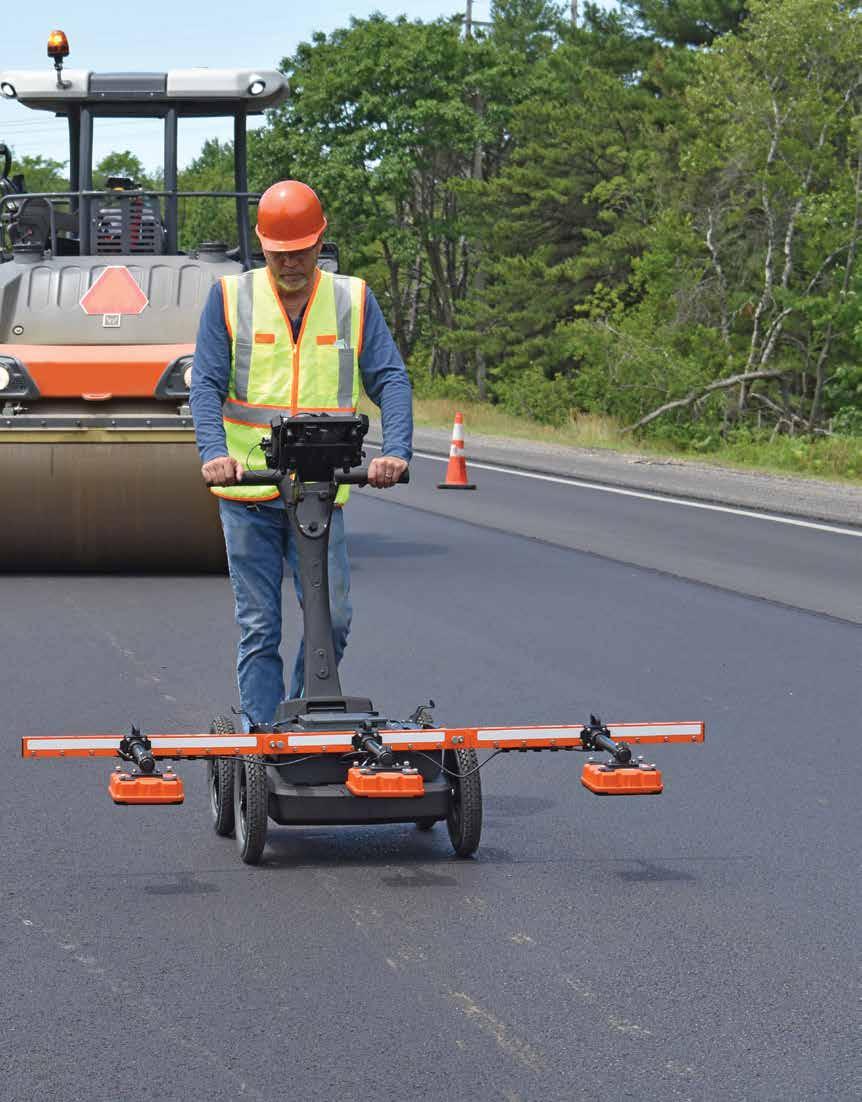