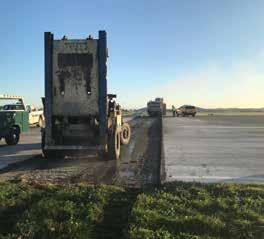
13 minute read
Asphalt Creativity Solves Concrete Instability
BY SARAH REDOHL
Maine’s Bangor International Airport boards around half a million passengers each year on up to 20 daily departures. When the concrete beneath its runway began to buckle, making the repairs in a timely manner was of the utmost importance. Northeast Paving, a civil contractor headquartered in Bangor, Maine, was up to the task.
“Throughout the years we have done a majority of the paving at BIA,” said Northeast Paving Engineer Devon White. In 2021, Northeast Paving won the bid to repair BIA’s Runway 15/33.
Northeast Paving Chief Estimator Greg Schaub said that, prior to the start of the contract, there were two areas of the existing runway that had heaved as a result of an Alkali-Silica Reaction (ASR) in the concrete. Also known as “concrete cancer,” ASR is a swelling reaction that occurs in concrete over time. Given sufficient moisture, the concrete’s highly alkaline cement paste reacts with the amorphous silica found in many common aggregates.
BIA’s concrete runway was placed in the 1950s as part of Dow Air Force Base.
“This reaction caused the existing concrete to expand and with no place to go it started to buckle,” Schaub said.
To resolve the issue, Northeast Paving took a creative approach. During the course of a 48-hour shutdown, its crews demolished two 300-foot-long concrete strips running transversely across the runway where the heaving was most severe and replaced them with 14 inches of P-209 aggregate base and surface asphalt.
“The P-209 blend of stone and asphalt will work as a large-scale expansion joint of sorts to relieve pressure and heaving due to pressure,” White said. Ultimately, the asphalt strips aim to reduce swelling caused by ASR.
BREAK CONCRETE, FAST
Because the runway upon which Northeast Paving would be working is BIA’s only runway, the entire airport had to shut down for the work to be performed.
“Shutting down the entire airport isn’t an easy thing for BIA to do,” Schaub said, so having weekly meetings in the month leading up to the job provided an opportunity to discuss methods, timeframes and logistics. “They needed to feel comfortable that we could get the job done in a tight timeframe.”
Schaub thinks that Northeast Paving’s history of working at the airport not only helped give the client confidence that they could perform the work, but it also gave Northeast’s crews “an idea of what we were up against.”
The full airport shutdown did make traffic control a bit easier than it otherwise would have been, added Northeast Paving Engineer Marshal Deckers.
Northeast Paving hired Pavilion Drainage Supply Co. to use its Wirtgen CB 7000 Guillotine Drop Hammer on the underlying concrete.
“On a normal airport job, we’d have to block off every entrance point for aircrafts,” Deckers said. For this job, he added, it was more important to mark the runway as closed down in such a way that it was visible from the air, rather than setting up barriers on the ground. “If you have moving aircraft while you’re working, you need more barricades and better delineation.”
White said this includes Notice to Airmen or Notice to Air Missions (NOTAMs) issued stating that the runway will be closed, as well as flashing trailer mounted Xs as a visual indicator of a closed runway for potential approaching aircraft.
Not having to set up so many barriers on the ground ended up saving the crew a small amount of time, which was particularly precious given that the crew would have a mere 48-hour window to complete the project.
During the estimating phase of the contract, Schaub said Northeast Paving evaluated several different options to remove the existing concrete. “Breaking up the concrete with traditional hoe rams on excavators was evaluated but determined to be too time-consuming of a process,” Schaub said.
During a previous job Northeast performed at BIA in 2008 to rubblize the concrete Air National Guard’s heavy duty apron, the company tried to use a resonant breaker—particularly near the fuel tanks—with the hope that it would cause less impact to the subgrade. However, Schaub said, the resonant breaker was unable to break the concrete all the way through, so they ended up using a guillotine on that job anyway.
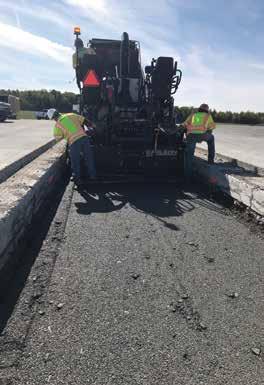
A paver was used in lieu of a typical grader or dozer to place the subbase because the trench was too narrow to accommodate Northeast Paving’s graders and dozers.
For the 2021 job, Northeast Paving hired the same subcontractor who helped them in 2008, Pavilion Drainage Supply Co., Pavilion, New York. “After conversations with Pavilion and having worked with them to rubblize that apron in 2008, we were confident that they could get the concrete broken up and ready for removal much faster than we could ourselves,” Schaub said.
During the week prior to the 48-hour shutdown, Northeast Paving was allowed to saw cut the perimeters of the troughs during short windows from midnight to 6 a.m. to minimize the amount of work they needed to complete during the runway shutdown.
“When the saw blade cut all the way through the concrete, the pressure gave and the saw cut pinched together on our 54-inch saw blade,” White said. “The water we were using to cool the saw blade shot up like a geyser! That shows just how much pressure was built up.”
Ultimately, it took two extra hours to remove the saw blade with jackhammers and patch the area, which was thankfully located along the runway’s shoulder.
When the 48-hour project window arrived, the saw cutting was complete and Northeast Paving’s crews were ready to hit the ground running Oct. 4, 2021, at 6 a.m.
The crews would need to create two troughs running transversely across the runway, located ¾ of a mile apart.
The troughs were 14 feet wide at the top and 10 feet wide at full depth, with the 24-inch depth varying from 15 to 18 inches of the existing concrete and 5 to 9 inches of existing HMA. This provided a 2-foot ‘shelf’ on either side along the runway’s surface at varying depths between 5 to 9 inches.
“We milled the shelf all the way down to the concrete,” White said. “The HMA on the runway is variable depth in regards to its transverse profile, with 5 to 9 inches on centerline and 2 to 4 inches on the shoulder.”
“Creating that shelf prevents having joints stacked straight over one another all the way through,” White said, “so it ties back into the existing runway a bit better.”
Once Northeast Paving’s Wirtgen 220 asphalt milling machine had finished milling the asphalt in the troughs, the Wirtgen CB 7000 guillotine drop hammer got to work on the concrete below. The roughly 250 cubic yards of concrete was then removed from the troughs using a Cat 349 Excavator.
In total, the concrete removal took just four hours, and that included a 90-minute breakdown of the guillotine. Even despite the breakdown, White said the speed of the demolition portion “set the tone for the rest of the project.”
The crews then placed between 5 and 9 inches of P-209 aggregate subbase in two lifts using its 8-foot Cat AP655F paver with Carlson screed.
“A paver was used in lieu of a typical grader or dozer because the trench was 10 feet wide at the depth at which the stone was being placed,” White said, “and we did not have access to a small enough grader or dozer to efficiently place and grade the material.”
They even tried removing the ends of the cutting edge on a dozer in an attempt at fitting it in the trench, but were unsuccessful. On the plus side, White said, placing the subbase with a paver turned out to be a much cleaner operation in regards to site cleanliness and spilled stone.
As a result of BIA’s experience with concrete, the airport has particularly stringent testing requirements for any concrete placed at the airport. “Thankfully, this job didn’t have concrete on it, so those didn’t apply to us,” Schaub said. For the time being, BIA is opting for asphalt.
ALL ABOUT ASPHALT
Then came the five lifts of asphalt, totaling 14 inches thick, loaded with a Weiler E2850 transfer machine.
The three lower lifts were between 3 and 4 inches, compacted. “These lifts were placed at varying depths due to the tapered construction of the runway going into the shoulder sections,” Deckers said.
The base course lifts, he added, were placed in large-depth increments to accelerate the construction process given the intense time constraints.
“The base course aggregate usually has density requirements, but given the time frame, we came to an agreement on density in the field by looking for any issues while ‘proof rolling,’” White said. However, Schaub added, “We were able to achieve compaction better on this job than on normal jobs because it was constrained on both sides.”
The surface lift was placed at a depth of 2 inches for a better-riding exposed layer.
One strip required 400 tons of asphalt, and the other, 310 tons. The mix was produced by Northeast Paving’s HMA plant and quarry in Hermon, Maine, only a few miles away from BIA. “The proximity and nighttime production capability of this plant makes supplying our Bangor Airport paving projects very convenient and efficient,” Deckers said.
Schaub said that the prevalence of granite ledge in the region, and the ability to operate its own quarry, helps Northeast Paving secure high quality weightbearing stone for its mixes.
The HMA used—a P-403 12.5 mm mix with PG76-28 called for in the specifications—was an airport-specific mix intended for heavy aircraft traffic. The mix design Northeast Paving used on the project was one that had been applied recently and effectively on previous BIA projects, another time-saving decision.
On standard airport paving projects, Deckers said, a small test strip is required immediately prior to paving. Using a mix design that had previously been used with success at BIA eliminated the need for that step.
It turned out that the most significant challenge, given the project’s time constraints, Deckers said, “was ensuring the HMA was properly cured and suitable for super-heavy aircraft, as there were multiple lifts placed within 24 hours.”
“Going into the project, we thought that the biggest variables in relation to time would be the demolition of concrete and the cooling of HMA lifts,” White said. “By gaining extra hours with the expedited demolition phase, that gave us extra time to let the four lifts of pavement cool between each placement.”

“When the saw blade cut all the way through the concrete, the pressure gave and the saw cut pinched together on our 54-inch saw blade,” White said.
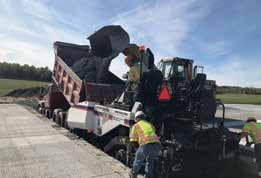
To load the paver as it laid the P-209 aggregate subbase layers, the crew loaded the paver in the trench with a haul truck in front of it, and a loader dumping into the haul truck from the side.
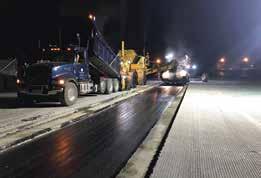
The five lifts of asphalt, totaling 14 inches thick, was loaded into the paver with a Weiler E2850 transfer machine.
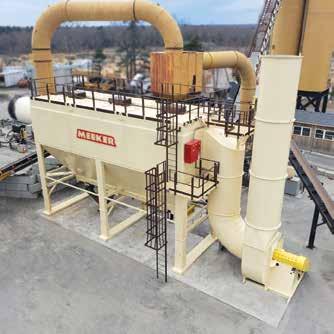
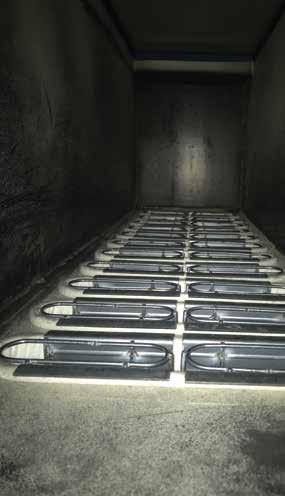
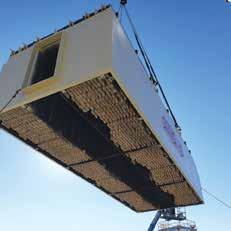
Your Preferred Asphalt Equipment Resource
The Meeker Family
The crew finished paving the final lift at 10 p.m., eight hours before the runway was set to reopen, so the surface would have enough time to cool.
After the paving was completed, the crew performed a shallow ⅜-inch deep, ½-inch wide sawcut along the joints on both sides of the troughs and sealed it with hot rubber to act as a minor expansion joint, with the goal of reducing transverse reflection cracking.
They also had a substantial amount of cleanup, including the removal of a bypass road they created in order to access the further trough. Electricity had to be restored to the lights on the taxiway, White said, and airport inspectors had to ensure all “foreign object debris” had been removed.
The sealing, which the airport requires for all asphalt, as well as the striping, were performed by the airport’s own maintenance crews, since it would be easier to coordinate with their own crews and expedited Northeast Paving’s portion of the project.
During the shutdown, the airport’s maintenance crews took the opportunity to make miscellaneous repairs and the airport’s engineering firm surveyed the runway for future projects, though everyone gave the paving crews ample room to get their work done safely.
Northeast Paving dedicated two crews to the project at all times, running two 12-hour shifts per day. “They worked around the clock to complete the project during the tight 48-hour window,” Schaub said, “making sure the airport operations would not be impacted more than absolutely necessary.”
Ultimately, Northeast Paving’s crews were able to clear the runway two hours early. White attributes this to proper planning, communication and execution by Northeast Paving’s team, its subcontractors, the engineering firm, and BIA staff.
“We finished at 4 a.m. on a Wednesday,” White recalled, “and already planes were taxiing up to get on the runway.”
SISTER CREW EARNS SHELDON G. HAYES FOR NORTHEAST PROJECT
Eurovia Atlantic Coast, dba Northeast Paving, and the Pennsylvania Department of Transportation District 12, were named the winner of the 2021 Sheldon G. Hayes Award for their work on I-70 in Washington, Pennsylvania. The National Asphalt Pavement Association (NAPA), Greenbelt, Maryland, announced Jan. 26, the winner and finalists of the 2021 Sheldon G. Hayes Award for excellence in construction of an asphalt pavement. The award, bestowed annually since 1971, recognizes the country’s highest quality highway pavements.
The winning project, performed by Northeast Paving teams in Pittsburgh, involved resurfacing 18 miles of I-70 with all mixes incorporating warm-mix asphalt (WMA) technology and the surface mix incorporating 15% reclaimed asphalt pavement (RAP). The team lost one month of production to COVID delays in the state but made up that time by the end of the project with teamwork and dedication to best practices, finishing on time and under budget. Management offered thanks to PennDOT for partnership in safety initiatives to ensure a safe work environment for all on this project. They also thanked the men and women of the safety, quality control, production, laydown, estimating and additional departments at Northeast Paving.
Finalists for the award were Seaboard Construction Co. and the Georgia Department of Transportation for I-95 in Camden County; and Shelly & Sands Inc. and the Ohio Department of Transportation District 5 for I-70 in Muskingum County.
The Sheldon G. Hayes Award winner and finalists are determined through a two-year evaluation process. All highway pavement projects using more than 50,000 tons of asphalt are eligible for consideration. Initially, the project must win a Quality in Construction (QIC) Award, which is determined by numerical scores given by an independent pavement engineer on the basis of how well the contractor met specifications and achieved density on the finished pavement. All pavements that meet a benchmark figure earn the QIC Award.
The year after a project wins a QIC Award, it is eligible for consideration for the Sheldon G. Hayes Award. The top-ranked projects from each year are tested for smoothness, and then visually inspected by an independent pavement consultant with many years of experience in the industry. This year, the evaluator praised all the candidates for their highquality construction practices, which resulted in smooth, safe and durable pavements.
At NAPA’s 67th annual meeting in Scottsdale, Arizona, the winner and each finalist were presented with an award for their achievement. “The asphalt pavement industry is committed to building quality pavements that deliver high performance and drivability to the public,” said James Winford, NAPA 2021 chairman.
LEARN MORE
Northeast Paving management accepts the Sheldon G. Hayes award from NAPA 2021 Chairman Jay Winford at the 67th annual meeting in Scottsdale. Photo courtesy of Northeast Paving