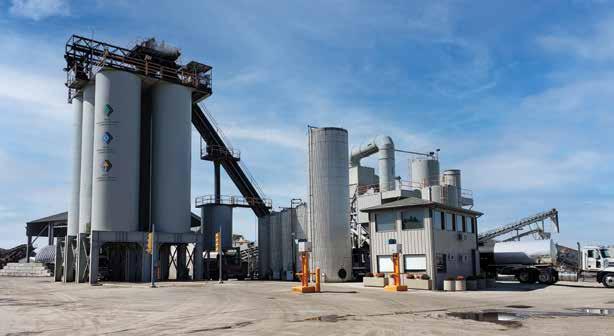
5 minute read
Three Tips for Successful Plant Calibration
After moving abrasive materials through the asphalt plant, you’ll see minute changes in equipment settings. To continue producing quality mixes on spec, you want to ensure all components stay in calibration. All photos courtesy of WEM Automation
BY JOE HIGGINS AND TED CHRISTIAN
OOur asphalt plants produce many thousands of tons of asphalt each year, with few breaks in the action available during the peak season. Moving hard, dusty, and abrasive materials like virgin aggregates and reclaimed asphalt pavement (RAP) through a plant takes its toll on your equipment. Things naturally will change and move over time. It’s inevitable. Therefore, it is important to ensure your plant is calibrated properly to produce the consistent, quality product you are after. A well-executed calibration process not only saves you time, but it can also draw your focus to areas of your plant that need attention or items that need to be replaced. Before you start up your plant for the season (or shut down for routine maintenance in warmer climates) here are a few calibration tips to help keep your plant operating efficiently and effectively.
It becomes an enormous, if not almost impossible task, to get a well calibrated and “dialed-in” plant if we aren’t certain our virgin aggregate and RAP weighbridges are in proper alignment. These weighbridges are the primary determining factor of a successful plant calibration and achieving your desired results.
Always start here and give this critical area an adequate amount of your time and focus.
Make sure to complete the work on your weighbridges before you start tackling your liquid asphalt cement (AC) flow calibration procedures. If you don’t, you may find yourself revisiting and reworking things on your plant and performing calibration procedures more times than you care to.
Always make sure of your weighbridge zero values and calibration accuracy before chasing AC variances in production. Remember, all other materials and setpoints rely upon aggregate weighbridge accuracy.
At times, verifying that your idler roller alignment is within acceptable tolerances on your weighbridges can seem a bit tedious, but it is essential. Even a variation of 1/16 of an inch beyond the recommended settings can have a significant impact on proper flow and the composition of aggregate material reaching the drum.
Check for significant belt movement or your belt tracking from side to side as material goes up the belt. If you see this, it can be an indication you have a weighbridge alignment issue. A belt that lacks proper alignment, or isn’t trained properly, will not allow for an accurate reading by your loadcell(s). As we all know, bad or inaccurate loadcell readings equate to mix that is not made to your desired specifications.
Without getting too far into the weeds or specifics here on alignment procedures, the original equipment manufacturer (OEM) for your equipment should be able to provide you detailed, step-by-step instructions on the process of proper idler alignment for the specific model you use. If you don’t already have it readily available, we strongly recommend you contact them and get a copy of these instructions sent your way. There are also some good videos and tutorials available online if you are up for a little search.
MAKE SURE YOUR CALIBRATION POINTS END UP IN A LINEAR FASHION ON YOUR GRAPH
Now it is time to get out your ruler and start to fine-tune those graph skills. When completing your calibration graph, it is recommended to use a minimum of three calibration points, although four is preferable (points 0 – 4).
All points on your graph should line up with your zero (initial) point. As long as your points on the line are within a pixel or two you are in good shape. Your midpoint reading should represent your typical running range (tons/hour) for the plant. Otherwise, your calibration could be off without you knowing it. We can’t stress enough that it is important to insure you have a linear line on your calibration graph. A non-linear line could indicate you have a loadcell or belt alignment issue, which we discussed above. Don’t settle for anything but a straight line.
CLEAR THE AIR AT YOUR ASPHALT PLANT
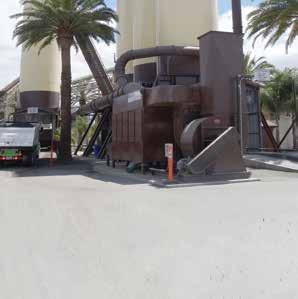
The Blue Smoke Control system from Butler-Justice, Inc., captures and filters blue smoke from emission points in your plant — with 99.9% overall efficiency.
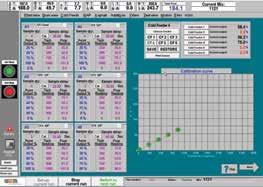
This image shows an example of four plot/test points on a calibration graph in the desired linear fashion.
CALIBRATE YOUR BINS
When starting with the calibration of your virgin aggregate and RAP bins, you must maintain a consistent material bed depth throughout the process. Why? Changes in the bed depth on your belt, of course, mean a different aggregate flow rate. Thus, achieving an accurate, consistent measurement during the bin calibration process will elude you if material bed depth varies.
As an example, when you move or adjust your bin gate opening, your flow rate changes, so you will need to recalibrate your bin at that new opening level.
As a side note, at times, during the season, you may find a need to open up a gate and clear out a large piece of material or obstruction in a bin. Even if you mark the gate opening setting and “put the gate back to where it was,” you will want to recalibrate that bin, generally at the end of your run. Why should you recalibrate? If your gate opening is off even by as little as 1/8 of an inch from its previous setting, (which is hard to see and can be the width of your reference mark), it can make a significant difference on the flow rate of a bin and your numbers will reflect that accordingly.
Another important point regarding this part of the process is to check and verify your material no-flow indicators are all in place and functioning properly. These indicators play a very important role in ensuring a proper matrix of aggregate (versus just the proper amount of aggregate) reaches the weighbridge and your drum mixer.
These three tips are just a few out of the many important pieces to a successful and essential plant calibration procedure. We hope you find them useful. This process has many variables involved and is time consuming for sure. But if you “plan your work, then work your plan,” make sure you are precise and methodical with your methods, the overall time spent will be less and the results well worth the effort.
Joe Higgins, senior controls technician, has been with WEM for over 13 years, helping asphalt customers with their technical controls questions and support. Ted Christian, strategic account manager, has actively been involved within the asphalt industry for over 25 years.
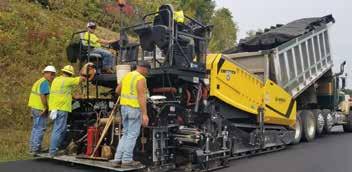
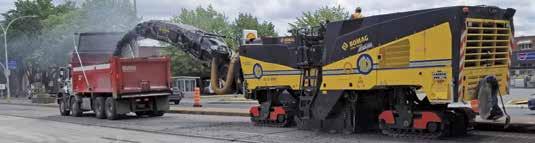