
4 minute read
GPR Offers Safeguard
W.W. Clyde Shares ARTBA Safety Award Tips
AAt the annual convention for American Road and Transportation Builders Association (ARTBA) in October 2020, the organization called for attendees to go above and beyond on safety. In fact, they called for attendees to go “beyond zero.”
“Instead of everyone aiming for zero safety incidents as their goal, ARTBA called for us to go beyond zero,” said Nate Neal, safety director at W.W. Clyde, Orem, Utah. “Going beyond zero means changing your company culture so everyone chooses to do what’s safe even if no one is looking.”
Neal knows all about safety culture. W.W. Clyde was recognized at ARTBA’s 2020 convention with a Safety Award for its employee safety program. When asked what makes W.W. Clyde’s program stand out, Neal listed three initiatives that have had a major impact:
1. WEEKLY INSPECTIONS
Every week, W.W. Clyde’s safety department conducts inspections where deficiencies are noted and fixed by the end of the shift.
For example, the area was really tight on a recent trenching operation. As a result of the inspection, the company opted for open cutting despite added expense and time. “If that situation were left to play out, there would have been an elevated risk that we could have prevented,” Neal said.
Travis Wentz, the senior area manager over road and highway for W.W. Clyde, said most of the hazards identified are small things, but that’s how the plan is meant to operate. “If you point out hazards when they’re small, you can fix them before they have a chance of putting someone’s life in danger.”
The safety department conducts the inspections with a PDF checklist on an iPad that they can add pictures and comments to and share as needed after the inspection. However, in 2021, the company is switching to a platform called SiteDocs. SiteDocs allows the company to more easily track its forms, which can be a challenge with numerous forms, hundreds of employees and multiple locations.
“Once you build the forms in SiteDocs and they’ve been filled out, they are automatically sent to everyone who needs to see them,” Neal said. For example, W.W. Clyde’s president and vice president receive all safety inspection reports. The system also keeps the forms organized by type and by project.
SiteDocs also tracks employee training. “I could query the whole company to see who has forklift training, or see what training [Wentz] has taken within the company,” Neal said. “This helps us make sure people don’t miss training they need to work safely.”
“When it comes to safety, if it’s not documented, it often doesn’t happen,” Neal said.
2. GOAL OF THE DAY
Another proactive tool Neal recommends is the company’s “Goal of the Day” program, begun in 2017, which is a pre-planning process performed every day by crews covering pre-shift start up, obstacles of the day and strategies to overcome those obstacles.
The pre-shift start-up checklist includes items such as work area inspection, review of personal protective equipment, and ensuring tools and equipment are in working order. The obstacle of the day section requests the crew mark all obstacles that apply from a large list, including work at heights, inclement weather, falling objects and more. And, lastly, the crew reviews protections and strategies to overcome the day’s obstacles.
All of the Goal of the Day checklists will also be completed and saved within SiteDocs.
3. MICRO-LEARNING
In 2019, the company began using Tyfoom, an online micro-learning platform. Employees receive push notifications to their phones each morning to watch two two-minute videos of training information, most of which relate to safety. After completing the videos, the employees take a quick quiz. Meanwhile, Tyfoom tracks views, scores and progress throughout the company.
The videos can be from the large library of videos Tyfoom has created on topics from electrical hazards and first aid to ergonomics and eye strain, or the company can create its own videos. For example, Neal made a video about the importance of using the correct chains after a link broke on a company project. He also prepared fire extinguisher training specific to their facilities.
“[Tyfoom] lets us be timely and get very specific with safety messages that are important to our company,” Neal said. This has also enabled Neal to share safety messages during the COVID-19 pandemic. “Right after an update from the governor, we could create and push a video out on Tyfoom.”
The platform also lets W.W. Clyde organize employees into groups by job so each group receives videos relevant to their job. For example, Wentz receives modules that help him in a more administrative role. “The modules are quick and to the point, but you really learn something,” Wentz said.
SUMMING UP SAFETY
“These tools help us keep our safety relevant, current and effective,” Neal said. But, of course, the above list is nowhere near comprehensive.
And of course, the foundation of W.W. Clyde’s safety culture is commitment from management. The company’s president and vice president are part of every safety decision the company makes, Neal said. His last bit of advice? “Be persistent. Don’t ever quit on safety. Changes don’t happen fast, but things that are worth doing take time.
– BY SARAH REDOHL
THE LEGEND IS BACK
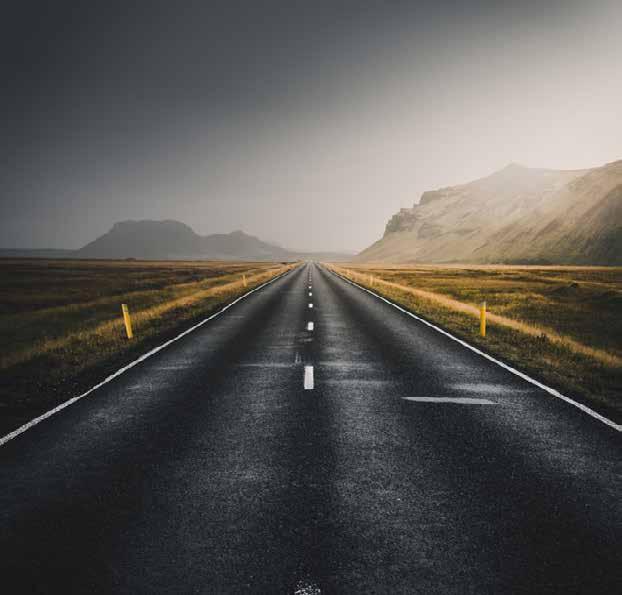
With over a century of innovation to its credit, Blaw-Knox pavers have earned a reputation for quality, durability and performance unmatched in the industry. Today, with its new and improved highway-class designs, Blaw-Knox continues to deliver on its promise with all the performance features you’ve come to expect from an industry leader.
BLAW-KNOX, THE LEGACY LIVES ON.
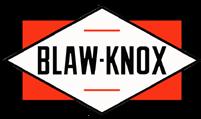