
3 minute read
Five Manufacturing
FIVE MANUFACTURING TRENDS TO WATCH IN 2021
FROM AEM
AAs original equipment manufacturers (OEMs) adapt to trends, their adjustments influence your bottom line. Here are five trends poised to have an impact in 2021—and beyond—on not only the manufacturing industry, but also on you—the customer.
COVID-19, EMPLOYEE SAFETY
Workplace safety and compliance with CDC guidelines, OSHA regulations and local safety measures will remain front of mind for manufacturers into 2021. Organizations will need to remain vigilant in their efforts to protect employees. Doing so, however, requires a significant investment of time, effort and resources on the part of company leaders.
Organizations will need to continue practicing social distancing in the workplace, restricting visitors to facilities, encouraging the practice of good hygiene, and ensuring employees are healthy and fit for work before allowing them on the job.
It’s been about a year since the COVID-19 pandemic took hold in the United States, and it remains a challenge for manufacturers across the country and around the world. While companies do have plans and protocols in place to combat the virus, adhering to them and ensuring the health and well-being of employees continues to be no small task.
CONNECTED WORKFORCE
Equipping workers with technology to keep them connected to collaborate from a distance has long been on a trend on the rise within the manufacturing industry. As older generations continue to leave the workforce and are replaced by younger employees, and the rise of the big data era in manufacturing takes shape, finding tools and technologies to make an increasingly spread-out and remote workforce as productive as possible is a top priority for companies today.
It remains critical for manufacturers to provide training and resources to employees as they try to maximize productivity from afar. Those who do it first—and do it well—will achieve a significant competitive advantage.
INTERNET OF THINGS
The Internet of Things (IoT) has long been a trend to watch in manufacturing, and this year is no different. As it continues to grow in prominence and becomes more widespread over time, IoT technology will drive value for the industry by allowing organizations to make measured, informed decisions using real-time data to increase efficiency and positively impact their bottom lines.
According to a recent study conducted by the MPI Group, approximately 31 percent of manufacturing production processes now incorporate smart devices and embedded intelligence. Furthermore, more than one-third of manufacturers have established plans to implement IoT technology into their processes, while 32 percent plan to embed IoT technology into their products.
IoT technology offers both remote monitoring and predictive maintenance capabilities, making it even more valuable for organizations looking to maintain visibility of equipment performance from afar. With the COVID-19 pandemic continuing to impact the industry in 2021, IoT technology will continue to be a go-to for manufacturers looking to maintain efficiency and productivity.
LOCALIZED PRODUCTION
The rise of customization and personalization has given way to opportunities for manufacturers to succeed in a localized economy. By rethinking the way products get out to the public, organizations can craft an ecosystem of smaller, flexible factories located near existing and prospective customers.
Manufacturers are used to thinking on a global level. However, shifting their focus to a local level, they may be better able to meet the ever-changing needs, wants and preferences of the markets they serve. Consumers are making it abundantly clear that authenticity matters, and a localized approach to manufacturing is proving to be among the most effective ways to for organizations to respond accordingly.
PREDICTIVE MAINTENANCE
The ability for manufacturers to predict impending equipment failures and prevent equipment downtime is incredibly impactful to the bottom line. Advancements in technology now allow organizations to do just that.
The benefits, according to a recent blog post from EAM-Mosca Corporation, showcase why predictive maintenance is so valuable to organizations today. Predictive maintenance helps companies: • Reduce costs; • See fewer failures; • Minimize scheduled downtime; and • Optimize parts delivery.
Effectively conducting predictive maintenance is no easy task, however. Adopting a successful predictive maintenance model requires manufacturers to gain insights into the variables they are collecting and how often those variables present themselves on factory floors. Therefore, it’s imperative for manufacturers to possess accurate and relevant knowledge about their equipment. They must know what previous failures have taken place, and they need to make decisions around lead time. Because, as the closer to failure a machine is allowed to go, the more accurate the prediction will be.
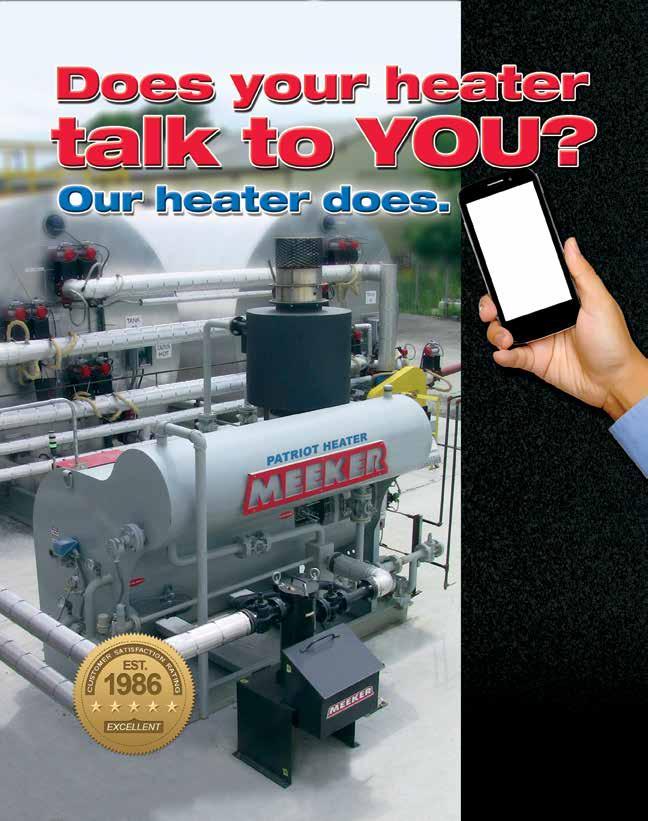