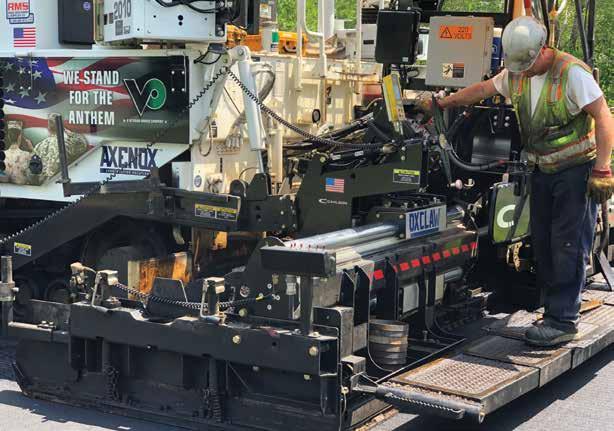
10 minute read
Patterned Screed
PATTERNED SCREED PLATE PATTERNED SCREED PLATE OFFERS SMOOTH MAT OFFERS SMOOTH MAT
BY ASPHALTPRO STAFF
BBrent Carron is the first to admit that if you want a smooth road, it makes sense to start with a smooth screed plate. After one season paving with a patterned screed plate from AXENOX Construction Solutions, Powell, Wyoming, he’s ready to reconsider that conventional wisdom.
Carron, vice president at Valley Paving Inc., Shakopee, Minnesota, ron puts it, his father thought he could make a better widget. “My father’s always been an early adopter,” Carron said. “He swears to me he was the first in Minnesota to adopt belly-dump paving with windrow elevators after seeing it out in California.” first learned about the unique screed in February 2020. He and his father,
Rich Carron, were attending a product demonstration when they struck up a conversation with the screed’s inventors, brothers Stuart and Michael Frost.
“Not 90 seconds into the conversation, Stuart took out his phone and showed us this patterned screed plate and asked if we’d like to try it,”
Carron said. “It was the craziest thing I ever saw.”
Crazy as it seemed, Valley Paving’s history of innovation encouraged them to give it a try. The company itself was born in 1979 when, as Car-
Valley Paving Inc., specializes in heavy highway work, but also performs municipal work, parking lots and the occasional driveway. In 2020, the company paved 500,000 tons of asphalt with its two crews.
He and his father knew the Minnesota Department of Transportation (MnDOT) was open to innovation, having been a leader in intelligent compaction and thermal profiling. They also knew their crews enjoyed a new challenge. And, they could tell the Frosts grew up in the industry.
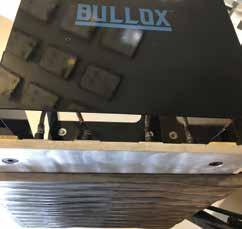
The OXCLAW attaches to another product from AXENOX, a conductor plate called BULLOX, via a silicon rope. “The beauty of this system is once the BULLOX is on there, it’s there for the life of the screed and you just have to change the plates,” Carron said.
“I could tell [the Frosts] were engineering-smart, but I could see that they also had the experience and the passion to improve our industry,” Carron said. “We decided to give it a whirl.”
Valley Paving received its OXCLAW screed in early June 2020 and has since used the screed on more than 30 projects, varying from city streets and county roads to state highways and airport runways.
According to Carron, the OXCLAW’s corrugated pattern not only doubles the surface area of a flat screed plate, but it also forces the mix to zig and zag its way under the screed. “By the time the mix moves from the front of the screed plate to the back, it’s moved about 3 inches laterally,” Carron said. “The screed plate sort of remixes the mix and the aggregates lock together a bit.”
The first day they took the screed on a project, the whole crew swore it wouldn’t work. “After reading density and riding the mat with the truck at the end of the day, they shook their heads and said ‘These guys might be onto something,’” Carron said. “Now they want to use the OXCLAW on every job.”
PLAIN VS. PATTERNED, SIDE BY SIDE
Over the summer of 2020, Valley Paving had a chance to directly compare the OXCLAW’s performance with a traditional screed. They were performing a 2-inch mill and overlay on I-94 between St. Paul and Minneapolis. They would be echelon paving 30,000 tons along three miles of the four-lane highway over the course of four weekends, using two Roadtec RP-195e pavers with Carlson EZ-R2 screeds.
One screed had a traditional screed plate and one had the OXCLAW. “It was the perfect test scenario,” Carron said. “We’re taking out all the variables that we can so we can really compare the performance of the screed plates.”
Carron, who is also the president of the Minnesota Asphalt Paving Association, decided to use the job as an opportunity to showcase the screed more widely. “We can talk theory all day long, but seeing is believing,” Carron said.
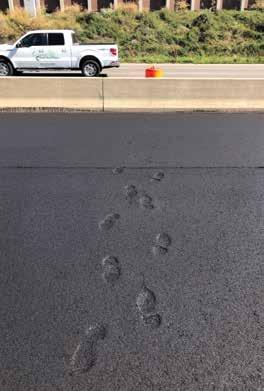
Carron said the OXCLAW results in better density right behind the screed. In fact, if a person walks across the mat, their footprints are barely visible. In this photo, the footprints closest to the camera are on a traditional mat, and the footprints on the far side of the picture are on the mat behind the OXCLAW.
Carron said that in his experience, it’s possible to eliminate a roller pass or even an entire roller, when paving with the OXCLAW.
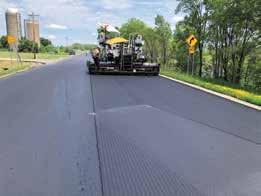
He invited agency staff, asphalt companies, even his competitors, to see the OXCLAW in action. In addition to various MnDOT personnel, visitors from as far as Florida, Georgia and Washington came to watch. After a video of the OXCLAW circulated widely on social media, many people were curious about this patterned screed.
The first thing people ask about, Carron said, are the shadows left behind the screed; the mat looks textured. This is a result of the aggregate being placed and interlocked in the mat. “The second thing they do is get down close to the mat and realize it’s actually smooth.”
The shadows created by the patterned screed depend on the mix design, with sandy mixes leaving less pronounced shadows and rocky mixes resulting in more defined shadows. Carron compares them to what you might see on the mat after a pass with a rubber tire roller. In fact, the shadows remain even after the road has been compacted. Carron considers it his company’s calling card. “Everyone knows everywhere Valley Paving goes,” he said. “Knowing everybody’s looking at their work has become a source of pride for the crew.”
After satisfying his audience about the shadows, Carron has newbies walk across the mat. “It feels like it’s already been knocked down by the first roller,” he said. “You can’t turn a blind eye to the fact that you can walk across the mat and barely see footprints. Even if you don’t believe the theory of it, you realize how much better density you’re getting right off the screed.”
And that extra density is nothing to turn a blind eye to. On the I-94 job, Valley Paving was able to eliminate a couple roller passes over the OXCLAW side of the mat and still achieve the same 93 and 94 percent density they achieved on the conventional side.
Carron also said the unconfined joint showed higher densities, as well. “You don’t see the typical roller squish out with the breakdown at the joint, as you would with a conventional screed,” Carron said. “The bituminous edge stays intact, resulting in higher densities at your joints.” In fact, Carron said they paved the Crystal Airport runway using the OXCLAW and were able to achieve 93.3 percent density on the joint.
Normally when they echelon pave interstate work, they have eight rollers behind their two pavers: four breakdown rollers, two intermediate rollers, and two finish rollers, working in tandem. The crew soon realized they were over-compacting the OXCLAW side with this rolling pattern. In addition to eliminating roller passes, they also turned off vibration during finish rolling on the OXCLAW side.
They also used the OXCLAW on an echelon paving job on State Trunk Highway 212 in November. Carron remembers it was cold enough that there was snow on the ground. The crew was only paving a 1.5-inch lift and the job was 40 minutes from the plant. Even with these challenges, they were able to achieve 93 and 94 percent density on the side with the OXCLAW. The side with the traditional screed plate was consistently at 92 percent.
“Working in those conditions shows the best place to get density is at the screed,” he said. “If this system helps us achieve density right at the screed, we could potentially not have deductions for density when we have to pave in November. That’s a huge benefit for us northern contractors who are often stuck paving early and late in the year when it’s really cold out.”
In addition to the improved density, Carron said the rideability is just as good as with a traditional screed. “We’ve achieved a ride bonus on every job we’ve done with this system,” he said.
On the I-94 job, Valley Paving also used a thermal profiler on both pavers. “It was the same mix, at the same temperature, paved by the same pavers and screeds paving side by side,” Carron said. However,
when they reviewed the results, they noticed a thin cold streak behind the flat screed, usually created by the auger drive chain assembly. “The OXCLAW side was a nice consistent temperature all the way through.”
Even though the overlay on I-94 was a Band-Aid™ job, Carron said, the results were very good. “The best part about it was a project engineer from MnDOT said we needed to put it up for an award because of how well it turned out,” he said. “That just goes to show that MnDOT sees the effects of it, too.”
SAME, BUT DIFFERENT
Carron said the only difference for his screed operator has been an adjustment of fluff factor. The standard is usually to add ¼ inch depth per inch of lift, so a 2-inch lift becomes a 2 ½-inch lift behind the screed. With the OXCLAW, he recommends reducing that fluff factor from 1/4 of an inch to 1/8 of an inch or 3/16 of an inch. “If you don’t make that adjustment with this screed system, you’ll blow your yield on every job,” he said.
Another difference is with the angle of attack. Unlike with a traditional screed, where the front is a bit higher so the tail compacts the mat, the OXCLAW runs flat. “The grooves at the front of the OXCLAW act as an angle of attack anyways,” Carron said. “The flatter you run, the more the screed touches the mix, the more vibrations from the screed are going into the mat, and the better density you’re going to get right off the screed.”
In fact, Carron has noticed less vibration on the screed’s catwalk compared to a traditional set up. “It seems like the vibrations are going into the mat and bouncing the screed back up less.”
Carron said the crew hasn’t had issues with mix sticking to the patterned plate, nor have they needed to change clean-up procedures at the end of the shift.
He’s also noticed that the OXCLAW seems to heat up quickly and evenly. The OXCLAW attaches to another product from AXENOX, a conductor plate called BULLOX. “The aircraft-grade aluminum on the BULLOX conducts heat really well, so the OXCLAW heats up faster even though it’s made of chromium carbide.”
Because the OXCLAW is made of chromium carbide instead of heavy-duty steel, Carron expects the OXCLAW to last a long while. Even wear from running flat could also extend the OXCLAW’s lifespan, he surmises. “We normally get through about ¾ of a season per screed plate,” Carron said. “I think we’ll get three seasons out of the OXCLAW.”
With the OXCLAW, the process of changing the screeds out took only five hours. Normally it takes 1 ½ days, Carron said. Instead of taking off 75 or so bolts, the OXCLAW attaches to the BULLOX conductor plate with a silicon rope. “The beauty of this system is once the BULLOX is on there, it’s there for the life of the screed and you just have to change the plates.”
With a seven-month paving window in Minnesota, shutting down for two days to swap out screeds is a hardship. “The OXCLAW would be worth it for the fast change-out alone,” Carron said. “Everything else is an added bonus.”
“A lot of people think that the way our dads and grandads did things is the way we’re always going to do it,” Carron said. “Stuart and Michael have proven that a patterned screed plate can leave behind a flat mat. They’ve shown there’s room to shake up the screed industry.”

PUGMILL SYSTEMS
We’ve been designing and manufacturing custom mixing solutions in Tennessee for nearly 40 years.
RCC • CTB • Pugmix • Stabilized Sand
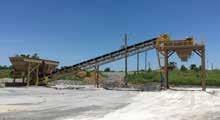
Coldmix • Fly Ash • Salt Treatment
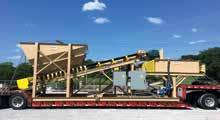
Rental Plants Available
Check out additional projects at: PUGMILLSYSTEMS.COM or give us a call at: 931-388-0626