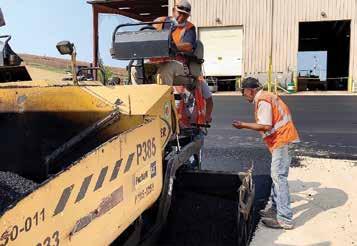
6 minute read
Gravel Lot Gets a Big Upgrade
By Sarah Redohl
WWaste Management, Houston, is North America’s largest environmental solutions provider and recycler, supplying waste disposal services to more than 21 million municipal, commercial and industrial customers, according to the Waste Management website.
The company’s hauling depot in Springdale, Arkansas, is its local base of operations for its administration, logistics, fleet maintenance and natural gas refueling for dozens of trucks that service a metropolitan area of approximately 500,000.
After several decades of struggling with a parking lot, service center and refueling station that operated 365 days a year on a gravel lot, the company submitted a public bid for base replacement and paving. The goal was to reduce tracking out of debris; the seasonally challenging Midwest weather conditions would frequently turn the area to mud and ice.
When the resulting quotes far exceeded the available budget for the project and were slated to take six or more weeks, the Waste Management team called on Pavecon, headquartered in Dallas, to find a solution.
Pavecon is a pavement maintenance and construction company with eight divisions across the southern United States, spanning from Phoenix to northern Florida. The company is a preferred vendor and contracted
Because the structure beneath was so stable, the engineer thought 2 inches of asphalt would be sufficient. However, Pavecon paved up to 5 inches thick in some areas that were at higher risk for failure.
maintenance provider for Walmart, Home Depot and many other national partnerships, including dozens of school systems and universities. Originally founded by David Walker in 1992, Pavecon has grown to over 1,500 employees across several companies.
Stabilize and Save Pavecon worked with its project design team and Waste Management’s engineer and facility manager at the Springdale depot to resolve the challenges other bids had faced, such as trying to replace the base. This started with learning more about the customer’s needs and how Pavecon could develop a solution that met those needs and the budget.
“The way landfills work is actually fascinating,” said James Eldridge, sales manager for Pavecon’s Arkansas division. When the landfill is full, he explained, Waste Management is contracted to maintain the landfill from a safety and environmental perspective for an additional 30 years. With this landfill expected to be full in less than 10 years, Waste Management faced a unique challenge. They needed a pavement that could handle heavy use in the near future, but one that also made financial sense, given limited traffic to the facility once the landfill reaches capacity.
Most of the bids that had come in had proposed base replacement, but Pavecon’s team recognized the strength of the existing base upon which they’d be paving. “They’ve been using that facility for decades,” Eldridge said. “It’s all really deep base and super compacted.”
Instead of reclaiming the existing gravel lot, Pavecon suggested stabilizing it with a mixture of Portland cement into the existing base, recompacting it and then paving a new asphalt surface course. By doing so, Pavecon was able to come in at Waste Management’s budget, around 27 percent less than the lowest bid received. Additionally, this would allow Pavecon to complete the project in less than half of the original project timeline.
The crew used its Wirtgen WR 200 XLi cold recycler and soil stabilizer to stabilize to a depth of 8 inches at 6 percent cement stabilization. Beneath the stabilized base, Eldgridge said, is an additional 4 to 6 inches of industrial-level compacted base. “We were essentially doing stabilization on top of already base stabilized material,” he said.
Because the structure beneath was so stable, the engineer thought 2 inches of asphalt would be sufficient. However, Pavecon paved up to 5 inches thick in some areas that were at higher risk for failure. For example, where the asphalt meets the concrete of the service area.
The job required 1,600 tons of asphalt, purchased from APAC’s Sharp’s Quarry asphalt plant.
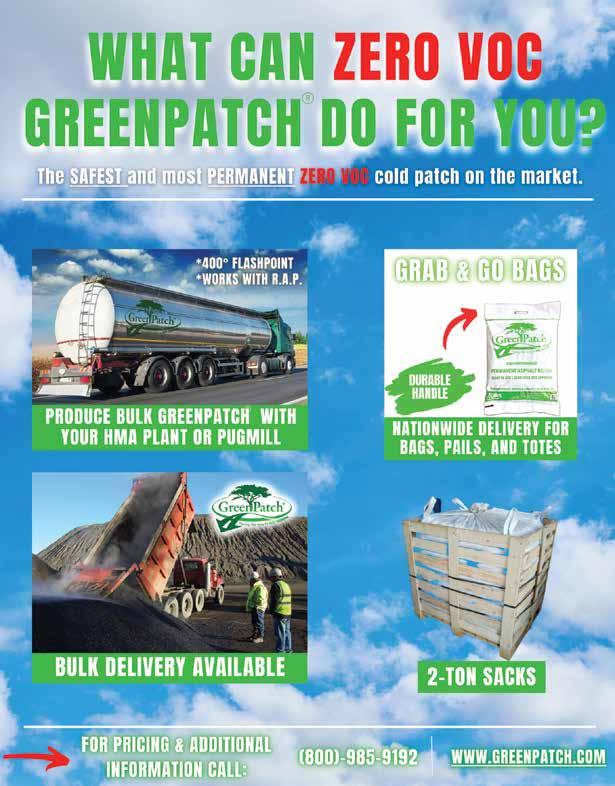
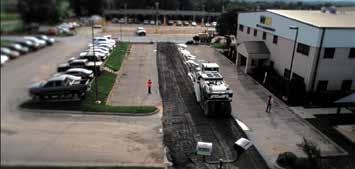
Instead of reclaiming the existing gravel lot, Pavecon suggested stabilizing it, recompacting it and then paving a new asphalt surface course.
After several decades of struggling with a parking lot, service center and refueling station that operated 365 days a year on a gravel lot, Waste Management submitted a public bid for base replacement and paving.
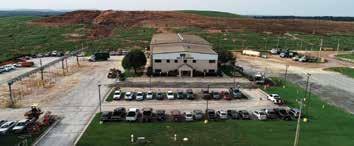

Schedule for Safety Most of the challenges Pavecon faced related to scheduling and project preparation. Due to heavy use of the facility six days a week, scheduling presented a challenge. Pavecon’s foreman on the project, Shannon Middleton, worked closely with Waste Management’s plant manager so the crew’s operations would minimally impact the facility’s operations.
“They were in constant communication,” Eldridge said. This allowed Waste Management to continue operating the facility at maximum capacity while Pavecon hit its own production goals.
Scheduling was made more challenging by a tight timeline and the need to work more slowly around many natural gas, power and fiber lines. There’s also a natural gas rail on-site that refuels more than a dozen trucks each night.
For the private facility, Pavecon called 811 and contracted a private locate company to identify the location and depth of all lines. “Without that, we’d be flying blind running a mill with 16-inch teeth,” Eldridge said. They marked out the locations of all lines and made a plan to work safely around these obstacles. “As we got close to where those lines were, we switched from production rate to a safety-oriented, risk mitigation mentality.”
Pavecon’s Northwest Arkansas division began work on the project Sept. 13, finishing Sept. 27 without a single safety incident.
Results Earn Respect The lot project was completed in two weeks, and an estimated 400 gallons of reduced fuel consumption also contributed to the cost savings to the client.
“By executing a solution aligned with Waste Management’s commitment to sustainability, Pavecon reduced the loads of base material hauled off by approximately 3,800 tons thus saving the client both time and money within the project,” Eldridge said. This was important to the customer, because Waste Management prides itself on its commitment to sustainability.
Pavecon’s performance on the job also resulted in Waste Management hiring them to perform three other jobs at the facility, including an access road where the company’s fully loaded trucks bring the waste to be processed.
“We helped them realize there are options out there that mean they can present us with their budget and we will not only respect that, but give them maximum value for whatever they have available,” Eldridge said.
Fiber Reinforced
For the half-mile access road, Pavecon was initially paving in two lifts for a total thickness of 5 inches. However, they ultimately decided to add Forta-Fi fibers to the mix at one pound per ton. Pavecon was able to pave the access road at a stronger structural coefficient and use 40 percent less asphalt material, which resulted in significant cost savings. The decision also halved production time, because the job could be paved in one lift, and minimized disruption to the facility.
