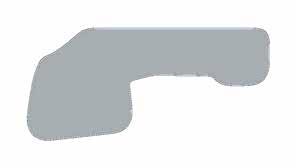
2 minute read
Road Widener’s Offset Vibratory Roller Attachment
Step 1
The host machine connects to the universal mounting pad. Step 2
The operator uses the remote control to swing the arm into the desired offset position, left or right.
Step 4
The host machine drives safely on the roadway while compacting sloping shoulders.
Step 3
The operator continues making remote controlled adjustments for the compaction drumʼs pivot angle and height.
TThe offset vibratory roller attachment from Road Widener LLC, a road construction equipment manufacturer headquartered in Delafield, Wisconsin, is designed to increase safety and eliminate rollover accidents on sloped shoulders. The offset positioning of the attachment makes this possible. Here’s how it works:
Due to its compact design, the offset vibratory roller is typically transported to jobsites on the same common-width trailer as the host machine.
Once on site, the offset vibratory roller can be attached to most skid steers, compact track loaders, road graders or wheel loaders by inserting the host machine’s lift arm pads into the offset vibratory roller’s universal mounting pad. The offset vibratory roller is then connected to the host machine’s standard or high flow hydraulics and paired to a handheld remote control.
After connection and pairing, the operator uses the remote control to swing the arm into the desired offset position and set the pivot angle (up to 30 degrees) and height (as low as 30 inches below the mounting point) of the compaction drum.
With the compaction drum in an offset position, the operator can drive safely on flat ground while compacting sloping shoulders, ditches and other hard-to-reach areas alongside the road.
The hydraulic connection and remote control allow the operator to adjust the compaction drum from the safety of the cab. Additionally, the compaction roller accepts 2, 3 and 4-foot-wide interchangeable drums.
Operating off the host machines engine and hydraulics reduces maintenance by 90%, leaving only five grease fittings to look after.
For more information, call (844) 494-3363 or visit roadwidenerllc.com.
SHOW US HOW IT WORKS
If you’re an original equipment manufacturer with a complex product, let us help you explain its inner workings to asphalt professionals. There’s no charge for this news department, but our editorial staff reserves the right to decide what equipment fits the parameters of a HHIW feature. Contact our editor at sandy@ theasphaltpro.com.
CRUSH RAP COSTS
with the HONEY BADGER
From replaceable abrasion-resistant steel wear liners to a 1/2" steel pulverizing hopper, this machine is ready for wear and tear. And by reducing material handling and minimizing moisture, the Honey Badger increases production and saves on fuel costs. Average return on investment is 1/8 the cost of other crushing operations. Fully-equipped with max power, reliable operation, and easy maintenance, the Honey Badger is ready to crush your costs!
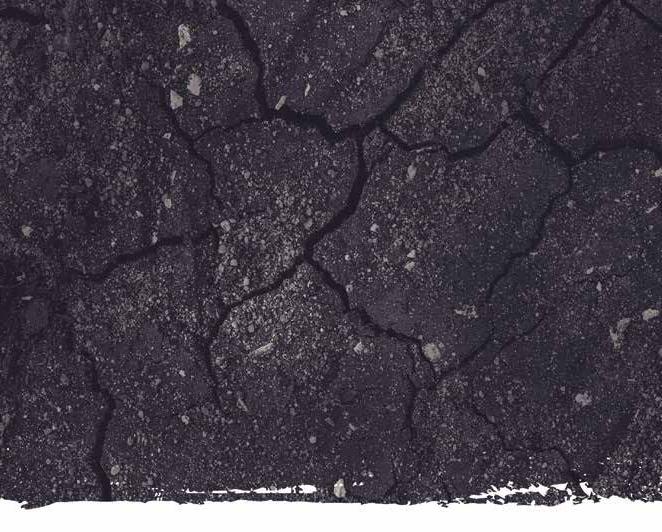
Reduced RAP moisture = lower fuel consumptions
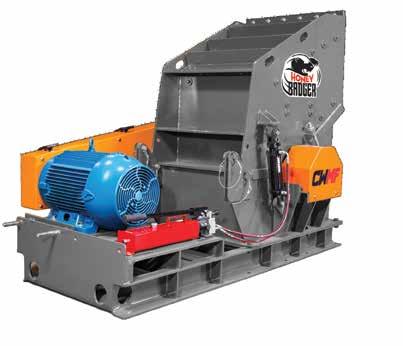
Reduce or eliminate crushing costs
Typical 6 month ROI
(300,000 ton/season plant)
Minimize material handling
STATIONARY PORTABLE
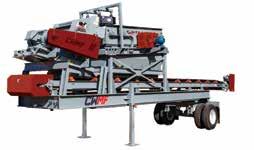
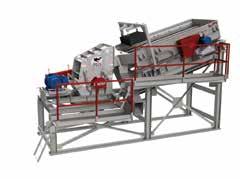