
8 minute read
Palmer Sand & Gravel Wins Safety Gold
BY SARAH REDOHL
Palmer Paving Corp.’s Sand & Gravel operation, a Peckham Industries Inc. family company, has been recognized as the gold winner of the National Stone, Sand & Gravel Association (NSSGA) Safety Excellence Awards for the second year in a row. The Safety Excellence Awards recognize operations that maintain a safe workplace, evidenced by safety performance over a consecutive period without an MSHA-reportable injury.
“Our reportable injuries have been steadily declining for years, but we are always trying to get to zero,” said Steve Benton, corporate safety director for Peckham. “We call it ‘Achieve Zero,’ but it’s not just words on paper. It’s our company motto. We believe it’s our obligation to our employees to Achieve Zero.”
And Peckham is getting close—85% of its operations in 2021 achieved zero reportable injuries. To do so, Benton said Peckham, and its subsidiaries, have employed most of the traditional techniques and approaches, while adding a plan of its own. “We track recordable incident rates, lost time, etc., but most of those best practices are a bit reactive,” Benton said. To take it to the next level, Peckham would need to become more proactive.
That’s why the company introduced its Peckham Engagement Plan (PEP) in 2020. “We believe those closest to the risk should
BENTON REITERATES THE IMPORTANCE OF ACTING ON EMPLOYEES’ SUGGESTIONS, ADDING THAT EACH TIME A SUGGESTION IS PUT INTO ACTION, “IT ENERGIZES OUR EMPLOYEES AND MAKES THEM FEEL MORE EMPOWERED.”
Peckham Industries introduced its Peckham Engagement Plan (PEP) in 2020. The plan aims to gather insight on ways to make Peckham’s operations safer from employees at every level of the organization.
have the most to say about it,” Benton said. “It’s a safety strategy that comes from the bottom up instead of the top down.”
“We started PEP to open up a conversation about safety and what we could be doing better,” Benton said. “We’re still following all the safety best practices after incidents take place, but PEP has been a powerful tool to be proactive about safety—and we’re seeing the program’s success in our numbers.”
The core component of the program is what Benton calls PEP observations. The company built a program in-house that allows managers throughout the company to report feedback they’ve collected from employees at all levels.
“We’ve trained more than 75 managers in our PEP process,” Benton said. This includes senior management, safety team, environmental team, QC team, sales team, superintendents and project managers, and some foremen. “We’ve been rolling it out incrementally, but we’d like to get to a point where each individual employee can file PEP observations. I think that’s when we will start to make serious inroads in our safety culture.”
Whenever someone files a PEP observation, Benton and other stakeholders receive email alerts in real time. Every two weeks, they receive a report tallying all observations by location/operation.
“When PEP observations are done well, they clearly outline the issues and conversations that have been had with employees to come up with a solution,” Benton said. Most of the solutions turn out to be quite simple. “Most of it are just things that have been overlooked for years because it’s the way things have always been done.”
For example, the site manager at Peckham’s quarry in Patterson, New York, facilitated a safety brainstorming session with the quarry’s employees. The company had
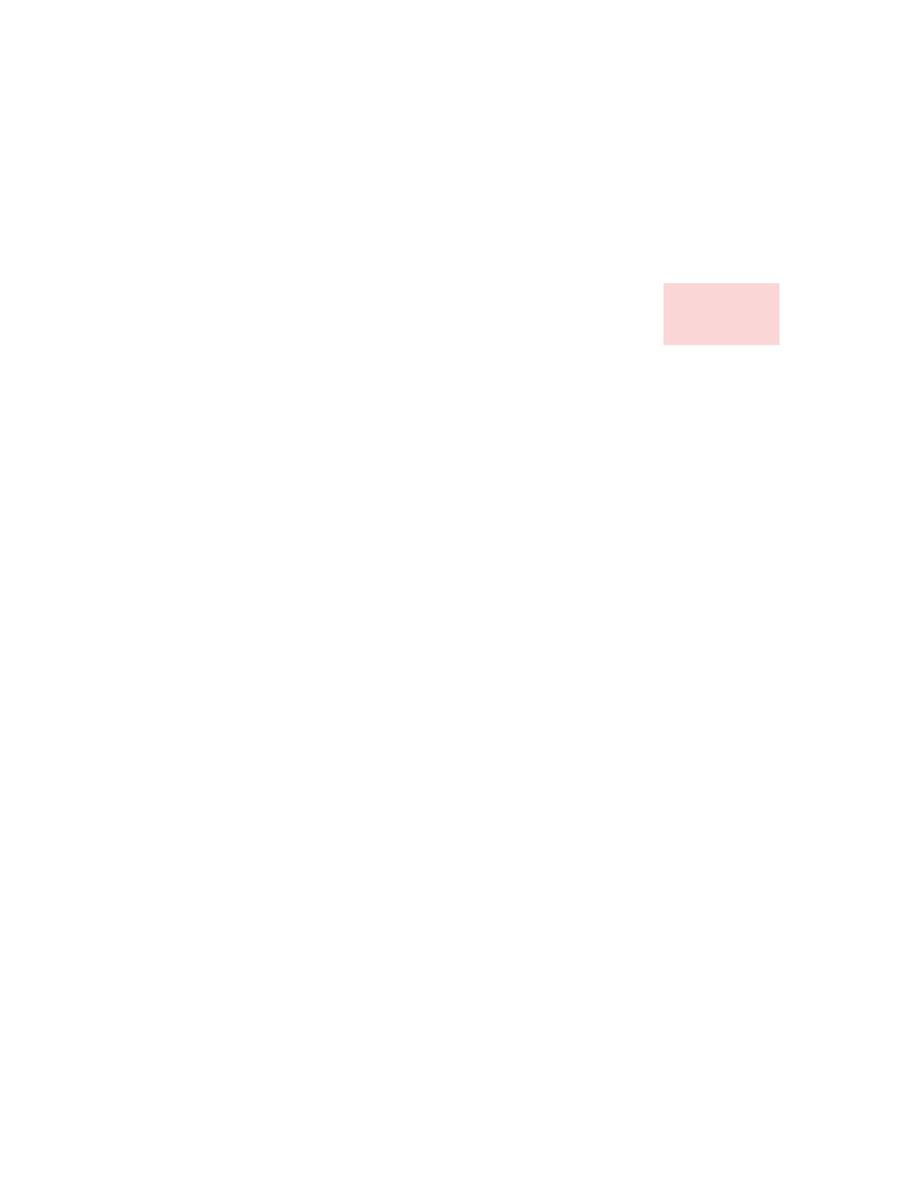
In Stock Now

recently experienced an influx of new hires to that location and during the course of that conversation realized there was room for improvement within the employee orientation process. “The employees were able to walk us through what should be included in a new employee orientation process centered around safety and specific to that quarry,” Benton said.
Peckham was then able to duplicate the process for its other quarry operations. “That’s the power of Peckham,” Benton said. “We’re able to share best practices across all our operations.”
Today, Peckham employs around 1,000 people in five states.
Other outcomes from PEP observations include the trimming of tree branches obstructing visibility along haul routes and signage improvements. “These aren’t expensive capital projects,” Benton said. “It seems like such a basic concept and such simple solutions, but we’re already realizing the benefits of it.”
Peckham also strives to recognize employees and operations both for their engagement and for their safety performance. This includes recognition on the flat screen TVs located across Peckham’s operations, most often in break rooms, shops, and other places where other employees will see them. “We add some photos and text to recognize employees in real time and change them every week,” Benton said. The screens are also used to share safety tips, HR information, or learning lessons from incidents and near misses. “It’s been a great tool for an additional level of communication with our employees.” Employees are also recognized in Peckham’s newsletters.
In 2021, Peckham launched several safety awards, recognizing Peckham operations overall and by region: Most Improved, Overall Safety Excellence and Safety Champion awards. “The Safety Champion Award is named after Joe Wildermuth, who recently retired and was the epitome of a safety champion during his time with Peckham,” Benton said. Winners are nominated by Peckham’s regional safety committees and were awarded trophies made in-house in Peckham’s precast division.
The construction division, which includes Palmer Paving Corporation and Peckham Road Construction, won the Overall Excellence award last year. “With no incidents whatsoever, it was an easy choice,” Benton said. The Most Improved Award went to the precast division, which cut its incident rates by 50% last year, and the Safety Champion Award went to Bill Perry at Dailey Precast.
“Not everyone is motivated in the same way,” Benton said, “but it seems somewhat generational. Employees today seem more motivated by recognition than they used to be. As a company, that means we need to change with the times.”
Plus, the recognition is well deserved. “This is a tough industry. At the end of the day, it’s hard work and we need to recognize our people for going above and beyond.”
In the future, Benton said Peckham plans to continue expanding its PEP process throughout all levels of its organization and will continue to work very hard to Achieve Zero.
“We are excited to be recognized on a national level,” Benton said. “The recognition is great, but the real satisfaction is witnessing the employee engagement, including the implementation of solutions to reduce and eliminate injuries and accidents. Ultimately, it’s about getting them home to their loved ones in the same or better shape than when they arrived.”
LEARN MORE

From left, Joe Sisto, Scott Pooters and Ahron Young
In June 2022, three Peckham Industries employees (Scott Pooters, Joe Sisto and Ahron Young) from its PARCO Terminal in Athens, New York, performed chest compressions and used an on-site AED on a truck driver who was experiencing a cardiac event.
“Within the past few years, our employees have had to use an AED two times, on both occasions, a life has been saved,” Benton said. “In the first instance, it was an employee, and in the second, it was an owner operator who was transporting our product. Both of these individuals made full recoveries and are alive today thanks to Peckham employees that were trained and acted, utilizing company owned AED devices.”
According to Benton, all Peckham employees are offered First Aid/CPR/ AED training annually. This has been the company’s policy for decades. “We have hundreds of employees trained and continue to add more,” he said. “At some point in everyone's life, they are likely to encounter an emergency, and having the right training can make the difference between life and death.”
The company also has AEDs on-site—approximately 60 units at all its facilities. “Many sites have multiple due to the sheer size of the operation,” Benton said.
STOP OVERFILLING TANKS!
The Tank Management System is comprised of three levels of functionality and is customizable for your plant.
This component makes it possible for you to never have to second-guess how much material is in your A.C. tanks or hotmix silos. The Accu-Level continuously monitors tank levels alerting the operator when an over ll is approaching.
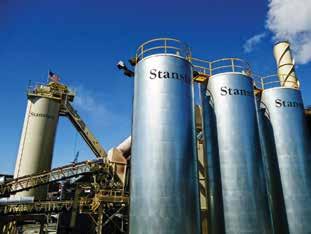
The app allows you to monitor speci c operations of your plant. While using it, you can: observe tank and silo levels in real-time, keep track of temperatures, monitor hot oil heater vitals, receive error alerts, allow team access, and more. Completely mobile-friendly, the app can be operated on a computer, tablet or any smart phone.
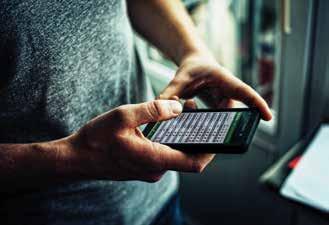
v.3.0.0 Profile Log Users Outputs Monitor
Name
Tank 1 AC-47
Tank 2 AC-40
Tank 3 AC-55
Tank 4 AC-30
Tank 5 AC-21
Tank 6 AC-20
Tank 7 AC-10
Tank 8 AC-10
Tank 9 AC-10 Silo 1 AC-1
Silo 2 AC-2 Silo 3 AC-3
Silo 4 AC-4
Silo 5 AC-5
Silo 6 AC-6
Silo 7 AC-7
Silo 8 AC-8
FireEye HoneyWell Electric
Level (Gallons)
26850
26842
5355
0
Temp oF
268
268
268
0
0 268
0 268
0
0 268
-124
53.6%
53.6% 53.6%
53.6% 53.6%
53.6% 53.6%
53.6%
268
268
-124
High Level Low Level High Temp Low Temp
Network Connected 12/13/2022 11:24:35
This system allows you to monitor and regulate all of your A.C. tanks. Users can set individual tank high/low parameters for level and temperature to initiate a pump shutdown and prevent tank over ows. In addition, you can operate A.C. tank supply, return, and ll valves with the push of a button from the control room, tank farm or any smart phone.
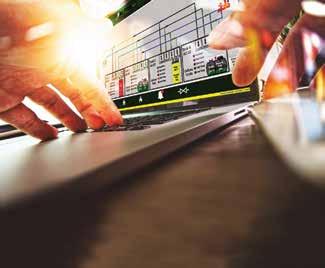