
17 minute read
Advanced Energy Property Deployment
Butler-Justice offers the X-VOCS™ system, which is designed to eradicate invisible, odor-causing emissions at the hot asphalt storage tanks by incorporating a five-stage filtration system. In the first three stages, a series of filters remove more than 95% of targeted particulates down to 0.3 microns; in the final two stages, carbon filtration beds remove remaining odors and volatiles, according to the manufacturer. Photo courtesy of Butler-Justice
ADVANCED ENERGY ADVANCED ENERGY PROPERTY DEPLOYMENT PROPERTY DEPLOYMENT
PART 2:
Despite lack of clarity, DOE encourages innovative GHG reduction
ABY SANDY LENDER As discussed in last month’s installment of this series, owners of hotmix asphalt (HMA) sites and quarries can not only upgrade existing facilities for their best environmental performance, but they can also receive government funding—eventually—for a portion of the cost. This was shared in detail during a National Asphalt Pavement Association (NAPA) member briefing held Sept. 8, 2022. During that briefing, Jay Hansen, executive vice president—advocacy for NAPA, shared information about the $5.8 billion available through the Advanced Industrial Facilities Deployment Program, through which facilities owners can receive rebates of up to 50% of the cost to design and install advanced technology at their plants. The goal, Hansen explained, is to drive down greenhouse gas (GHG) emissions throughout many industries and the program is run through the Department of Energy (DOE). As discussed in both our November and December editions, one way to take advantage of available funding is through applying to the DOE for a grant to identify and install appropriate technology for achieving a more efficient operation. At press time, industry awaited guidance on grant funding.
In fact, during testimony at the U.S. Senate on Environment & Public Works’ “Putting the Bipartisan Infrastructure Law to Work: The Private Sector Perspective” hearing held Nov. 30, 2022, Gary W. Johnson, the vice president of Granite Construction Company, told the committee that his company is ready to apply for grants to subsidize the GHG-reducing measures it has put into practice. “Grant opportunities need to come online as soon as possible,” Johnson told the EPW.
You can view the entirety of the Nov. 30 hearing at this permalink, where you will also find links to the five individual witnesses’ testimonies: https://www.epw. senate.gov/public/index.cfm/2022/11/putting-thebipartisan-infrastructure-law-to-work-the-privatesector-perspective
COMPONENTRY
As members of the asphalt industry are aware, producer members have been upgrading plant componentry to become more environmentally friendly and sustainable for decades. Gone are the days when a facility might emit dark clouds of smoke from questionable liquid asphalt cement (AC) purities, extreme production temperatures, lack of ductwork or baghouse, and so on; that’s something seen in old blackand-white photos from historical documents.
Instead, we have technologies such as pulsejet and reverse-flow baghouses, counterflow drums that capture gases and redirect them to a combustion zone for incineration, and blue smoke capture systems around loadout, transfer conveyors, and elsewhere, essentially negating blue smoke emissions. We have electric heating for tanks and Lo-NOx burners capable of burning any number of environmentally friendly fuels.
We have solutions to any problem.
Of course, the examples I list above represent merely a handful of the technologies asphalt industry innovators and entrepreneurs have brought to market over the years. And that’s what this article intends to share: ideas to encourage thought leaders to bring more examples to the readers who are interested in lowering emissions further.
Take a look at capturing fume specifically. • Mike Butler of Butler-Justice Inc., Anaheim, California, spoke of his company’s patented Blue Smoke Control system, which is designed to capture and filter blue smoke from various potential emission points at the HMA plant. The company’s newest system for eradicating odor-causing emissions is the X-VOCS™, and it’s designed to filter and remove up to 99% of odors and volatile organic compounds such as hydrogen sulfide (H2S) from hot asphalt storage tanks. “These systems can be installed together or separately,” Butler said. “We can incorporate them into new plants or retrofit an existing plant with minimal modification.”
That flexibility comes in handy for producers looking to upgrade for grant-filing purposes. • The researchers at Astec Industries, Chattanooga, designed a blue smoke capture system called the fiberbed mist collector that removes hydrocarbons from the incoming gas stream. This system captures minute particles from a gas stream and allows them to coalesce into droplets, which are heavy enough to fall through filters. Check out the Here’s How it Works feature from December 2021 for a detailed explanation.
Take a look at burner technology next. While some permits specify plants must have a Lo-NOx or Ultra Lo-NOx burner to begin operation, there are ways to increase the efficiency of these already advanced technologies. Mike Mauzy of Reliable Asphalt Products, Shelbyville, Kentucky, shared how one of his clients uses the Vulcan burner at his plant.
“Asphalt Supply Company (ASCO) in Sellersburg, Indiana, conducted a plant upgrade in April 2022, which included a new Vulcan 120 million BTU burner firing on natural gas,” Mauzy shared. He reported that ASCO immediately experienced noticeable fuel savings.
Brandon Watson, ASCO’s general manager, told Mauzy, “Over the next few months, we realized a 20% average reduction in natural gas usage.”
This improvement remained consistent since the April installation into late October 2022, when Reliable Asphalt Products, the North American supplier and manufacturer of the Vulcan burner, conducted a water injection test on the ASCO Vulcan burner. By introducing water mist at the fuel injection point, it has been proven that NOx emissions can be reduced even further. This test resulted in a NOx reduc-
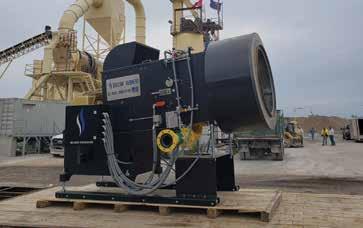
The Vulcan burner from Reliable Asphalt Products features a direct drive, VFD-controlled blower and is designed to provide flame stability over a wide operating range. Photo courtesy of Reliable Asphalt Products
tion while simultaneously increasing mix temperature and reducing natural gas usage even further.
“Further tests are forthcoming, but we were very encouraged with the threefold improvements by simply adding a small amount of water to our burner,” stated Dennis Mauzy, the Vulcan burner sales and service general manager.
As discussed in last month’s article, electric heat can be employed to reduce emissions all around the tank farm and yard. Ron Herman, business development manager of Enerquip Thermal Solutions, Medford, Wisconsin, listed a number of basic “hot spots” he recommends customers look at for energy and money savings. Among those is the use of LoNOx or Ultra Lo-NOx on burners, as mentioned above.
Herman also discussed replacing tank fire tubes with bottom-mounted tank coils, which can remove an emissions source at each tank on the site. When sitting down with customers to make a list of least expensive to more high dollar investments in energy efficient changes or upgrades, one of the first things Enerquip looks at is replacing inefficient tank coils or adding coils in those tanks without them. For example, if a customer is using older technology such as direct-fire heat at the tank, that customer is working with a small emissions source at each and every tank. That can be eliminated by switching to coils that are fed by a hot oil heater or electric heat, Herman said.
“For customers that already have tank coils, we’re looking at the type and efficiency of the coils they have in there,” Herman said. Depending on the technology of the coil, it could encourage coking, increased energy demands and higher maintenance activities. “We provide tank coils with helical-wound coils, which stand vertically so they’re like little discs around the pipe. Any sediment that tries to settle will fall between them and settle to the bottom to be cleaned out during their preventive maintenance programs.”
With this type of system, the producer can experience more heat transfer per foot than with other systems because there are so many more “fins” per foot. “There’s more heat transfer per foot; they’re more efficient so it takes less energy to heat the tank; and they’re not insulating themselves with sediment,” Herman said. In summary, a producer “can gain 10 or 15% efficiency just by switching out tank coils.”
BIG PICTURES
Another resource that shared a list of steps with producers was Intrame, a plant manufacturer in Spain. The spokesperson recommended a host of best practices when seeking to lower one’s carbon footprint and emissions output.
“We suggest, to reduce carbon footprint and emissions, the following actions: • Increasing the RAP in the mix designs • Reducing the temperature of the mix, by: o Using foaming systems o Using additives as waxes o Using emulsions, etc. • Using gas instead of other fuels such as heavy fuel, diesel, RFO, etc. • Using electrical heating for the tanks and lines • Using adequate venting systems in the tanks • Covering bins and stockpiles to reduce the increase of moisture with the rain • Reducing wastes during plant start up and stop • And of course, try to design the plant with as much energy efficiency as possible.”
When designing the whole plant, the team at Gencor Industries, Orlando, has taken its Gencor Ultraplant seriously. Dennis Hunt of Gencor, spoke of the Ultraplant’s design. He stated the individual components are optimized in design “with the intention of maximizing thermal, mechanical and heating efficiencies—all contributing to the reduction of greenhouse gas emissions throughout the United States. Gencor hot-mix asphalt plant design has reduced conventional energy usage to the lowest level attainable to produce hot-mix asphalt for roadbuilding and infrastructure development.”
What readers should keep in mind is this is a goal of any original equipment manufacturer (OEM) now. The OEMs are working hand in hand with customers to find ways to reduce energy use while keeping up with production demands. Herman at Enerquip spoke to this concept, explaining he runs equations for customers to show how they can save energy—and money—by insulating their tanks. We spelled it out in the first article for you, but the point is insulating tanks—and maintaining insulation—will make an enormous difference in thwarting energy loss and reducing heating costs.
“That’s one way that they can save without really investing in any new infrastructure or equipment,” Herman said. “It’s instant energy savings just by insulating their tanks. That doesn’t make us any money; we don’t sell insulation. But that’s one thing I preach to my clients because it’s such a big impact that often goes unnoticed.”
Hunt also pointed to the importance of insulation going into 2023. “The Gencor Ultradrum rotary dryer is fully insulated,” Hunt shared. “Insulating the rotary dryer not only helps maintain a uniform operating shell temperature throughout the length of the dryer but is part of an ongoing Gencor effort to increase overall thermal efficiency of the drying system. A system designed to produce 400 TPH of hot-mix asphalt with full Ultradrum dryer insulation will see a reduction of 887,328 pounds per year in GHG emissions.”
Modern plants require more than insulation to keep energy use down. The spokesperson for Intrame suggested a list of tasks, which many producers already implement, but which serves as a good reminder of best practices. • Increase the RAP capacity of the plants. (Of course, authorities must permit these mix designs.) • Retrofit the plants with modern foaming systems • Retrofit the plants with additive systems • Retrofit the plants with covers for the bins and for the stockpiles • Retrofit the plants with cold mix production system • Change or adapt burner to be able to work with natural gas • Consider electric heat for new plants • Modernize plant automation and controls to reduce wastes during plant start up and stop
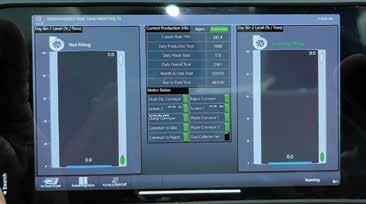
A plant manager or other member of management can see and react to plant operational data in real time these days, which makes any inefficiency that might be creeping into production easier to notice and resolve before it becomes a problem. Photo courtesy of Tarmac International
Looking at controls, as the Intrame team suggests in its final bullet point, is something Ron Heap at Tarmac International Inc., Lee’s Summit, Missouri, reminded producers to consider as helpful new tech in the New Year. “PLC controls for asphalt plants have been available for years and can be diagnosed and updated over the internet,” Heap shared. “New PLC systems not only replace obsolete electrical components but can now collect plant operating data and present this to management on daily, weekly, or monthly reports and give real time plant operating variables over “dashboard” data to management phone or tablet. Data acquisition and distribution gives management operational data wherever you are.”
Heap offered advice to keep the supply chain from hampering your upgrading plans: “Order your equipment early as burners, burner controls, larger motor control panels/motor control centers, baghouse ID fans, and dryer trunnion bearings have long lead times. Also, before you order a burner, find out if new lower NOx and CO levels will be needed. If so, then adjust your burner purchase to match the emissions required.”
CLARITY
Looking at that first bullet point the Intrame team suggests regarding the implementation of higher RAP percentages in mix designs takes us back to the Nov. 30 hearing mentioned at the outset of this article. Multiple witnesses at the EPW hearing stressed the need for clear, consistent regulatory guidance. And they weren’t limiting their desire for guidance to grant applications.
Dave Bauer, the president and CEO of the American Road and Transportation Builders Association (ARTBA), used the waffling legislation of the Waters of the United States (WOTUS) as an example when asking for “regulatory clarity” and “regulatory certainty.” But Granite’s Johnson made it clear in his testimony that our industry could indeed increase higher RAP percentages in mix designs if our industry had the regulatory certainty to do so. Johnson shared that in 2021, 16% of the material in Granite’s asphalt was recycled. That percentage increased to 21% in 2022. He said, “We could do more,” if the state agencies were more consistent.
In other words, clear, consistent regulation that allows for innovation will result in an industry that pushes for excellence. Turning on the switch that allows the industry to apply for grants to innovate, install and implement advanced technologies for the reduction of emissions will result in an industry that increases its innovations and deploys advanced energy property technology.
Whether producers are looking at upgrades to take advantage of grant monies, to apply for tax credits, to placate encroaching neighbors or to find new ways of lowering already low emissions, they don’t have
to go it alone. OEMs and consultants are willing to help when regulatory agencies come knocking at the door, whether you’re applying for grants or not. Butler shared: “For instance, the New York State DEC has proposed new air regulations on blue smoke control at asphalt plants that affect liquid asphalt storage tanks, hot-mix asphalt storage silos, pugmills, truck loadout, and drag conveyors.”
Producers doing business in that area might not be ready to apply for a grant from the DOE but would need to be ready to prove their environmental compliance under this proposal.
“Similarly, The Utah Division of Air Quality is considering regulation of VOC emissions from hot-mix asphalt plants as part of its Northern Wasatch Front (NWF) Ozone State Implementation Plan (SIP),” Butler continued. “This proposed rule would require HMA plant operators to control both VOCs and blue smoke emissions in the production and loading of HMA and at asphalt storage tanks. With minimal modification to their plants, producers can install our Blue Smoke Control system, which captures blue smoke from emission points in the asphalt production process.”
A white paper from the BlueGreen Alliance® titled “Buy Clean, A Tool to Create Good Jobs, Cut Pollution, and Renew American Manufacturing” purports U.S. manufacturing is contributing 23% of GHGs to climate change while it completely ignores volcanic activity around the globe. Be that as it may, the white paper suggests “any strategy to reduce industrial sector emissions must also boost the important economic benefits of domestic manufacturing and enhance international competitiveness. One such policy tool is Buy Clean, which would use the government’s vast purchasing power to create a large and stable market for the manufacture of low-carbon construction materials like steel, concrete, cement, and aluminum, which are among the biggest sources of industrial climate pollution.”
Other government documents lump asphalt into the list of materials that the government purchases and which can be used to lower carbon footprint.
Also from the white paper’s executive summary, “The Biden administration has recently taken major action to advance Buy Clean federally with Executive Order 14057, and a Buy Clean Task Force established in February 2022. The Inflation Reduction Act, which President Biden signed into law in August 2022, will complement Buy Clean by investing billions of dollars to directly help manufacturers reduce emissions and use environmental product declarations, while devoting billions to government purchases of low-emissions construction materials for public buildings and highways. The billions the federal government spends on public infrastructure could hold the key to reforming the status quo and creating markets for firms that innovate to reduce emissions and create good jobs.”
What this tells us is the Buy Clean policies instituted in a handful of states are now mandated at the federal level and it’s up to producers to fall in line if they want to continue doing business across state lines. The ideas suggested in this article are steppingstones to compliance, whether or not a grant program is up and running by the time this article hits the streets.
WEB EXTRA
Learn about the grant-application portion of the IRA’s program in AsphaltPro’s product gallery department article “Learn How to Write a Grant,” from the November 2022 issue at TheAsphaltPro.com.
IRS Doesn’t Clarify IRA
The Internal Revenue Service (IRS) offers incentives to participate in environmental sustainability. Its incentives have not proven entirely clear as of press time. Oct. 7, the Department of the Treasury (Treasury Department) issued a “Request for Comments on Energy Security Tax Credits for Manufacturing Under Sections 48C and 45X” to be filed by Nov. 4.
Notice 2022-47's purpose, as explained in Section 1 of the official document, was to receive general and specific comments of questions the Treasury Department had prior to developing guidance for implementing and administering the two codes, which are part of the IRA. The Associated Builders and Contractors (ABC), a national construction industry trade association established in 1950, which represents more than 22,000 members in 68 chapters, reported Nov. 29, 2022, that the Treasury Department and IRS’s guidance released that day provided almost no clarity “regarding tax credits for private clean energy projects funded by the IRA conditioned on compliance with prevailing wage and government-registered apprenticeship requirements.”
Ben Brubeck, ABC vice president of regulatory, labor and state affairs, said it appeared several of the questions ABC had raised in its comments to the IRS in its Nov. 4 comments weren’t addressed. “IRS says it will issue additional proposed regulations with respect to these requirements in the coming months and there are more questions that need to be answered between now and when this rule goes into effect in roughly 60 days.”
In other words, shortly after this issue hits the streets, the IRS should release more guidance. It appears ABC would like to see that guidance sooner rather than later because it could adversely affect contractors in all construction trades. Not only can contractors receive incentives for upgrading to advanced technology componentry, but they could also be in danger of being penalized for failing to upgrade.
“Developers, taxpayers, contractors and subcontractors need clear and specific guidance on how these new provisions will be implemented so developers can decide whether the tax credits are worth the significant risks and penalties, and large and small business contractors and subcontractors can decide whether to bid on and perform such work,” Brubeck said. “Today, this administration did not provide that clear guidance, which is likely to prevent stakeholders from taking full advantage of the tax credits and slow down clean energy infrastructure development.
“Regardless, the IRA’s unprecedented expansion of anti-competitive prevailing wage and apprenticeship requirements through the federal tax code onto private clean energy projects is likely to disrupt the marketplace of contractors who successfully and safely build solar, wind, electric vehicle charging stations and other clean energy projects across America,” Brubeck continued. “These new policies may result in fewer clean energy construction projects and less private investment, which would undermine President Biden’s goals of creating well-paying, middle-class jobs across America while reducing carbon emissions.”