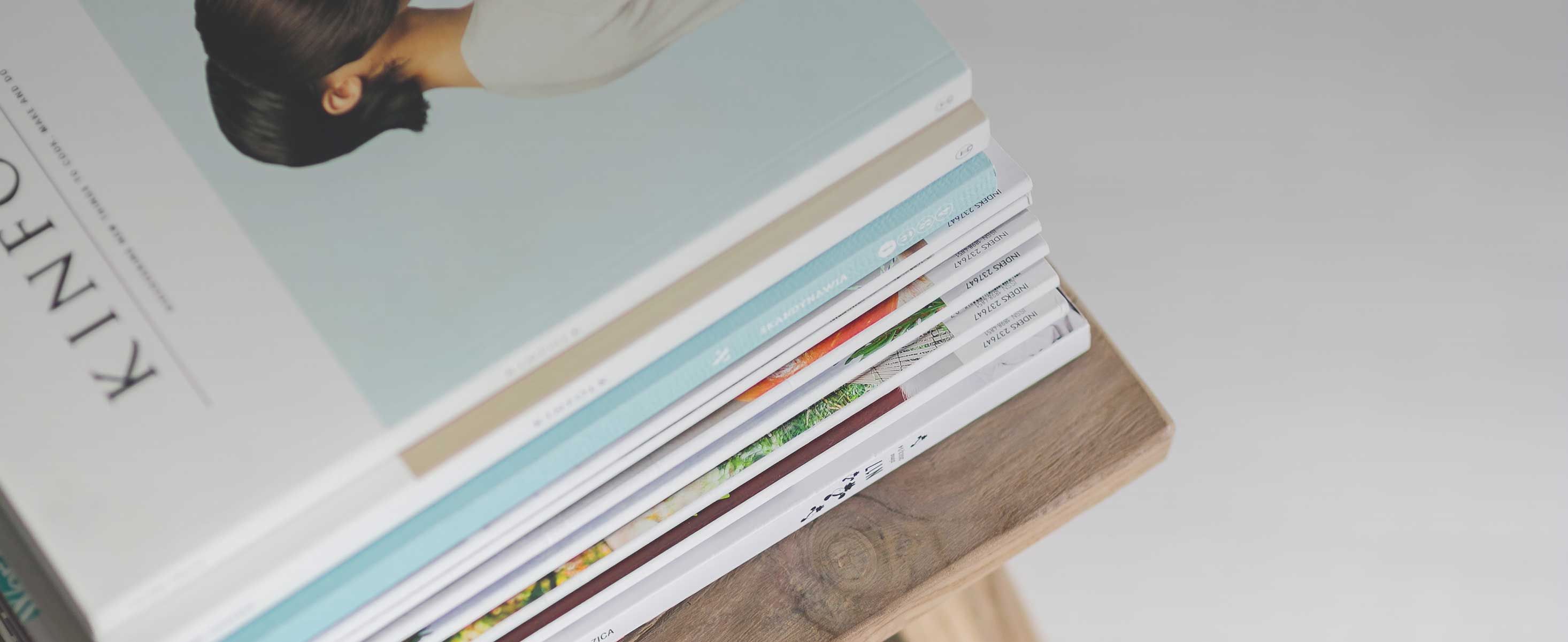
3 minute read
Soybean Solution
Biomag soybean-derived polymer proves its worth at NCAT
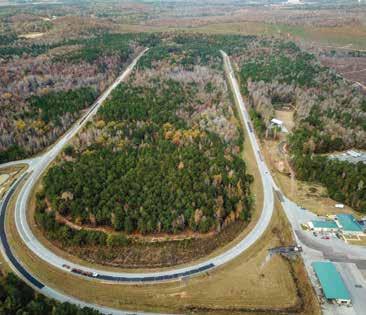
BY ALEXANDRA ZAHN
Producers and asphalt contractors looking to reduce their carbon footprint and meet Environmental Social and Governance (ESG) targets have another proven option at their disposal. The makers of Invigorate, a soybean-based rejuvenator that delivers improvements to the molecular makeup of reclaimed asphalt pavement (RAP), have successfully completed the first three-year test cycle of their soybean-derived polymer at the National Center for Asphalt Technology’s (NCAT) Test Track at Auburn University.
Biomag™ Hot Mix is a new generation of polymer asphalt additive, designed for high-traffic and heavy-load applications such as interstates and highways. “It consists of one part of our soybean rejuvenator (Invigorate) and one part soybean-derived polymer,” explained Austin Hohmann, product manager for Colorbiotics, Ames, Iowa. “It is a hyperbranched polymer that helps to interconnect and extend the SBS (styrene butadiene styrene) domains within asphalt.”
According to Nam Tran, associate director at NCAT, this is the first biobased polymer of its kind undergoing lab and track testing at NCAT. “We have tested some rubber-based polymers, but polymers are typically derived from petroleum. The purpose of the polymer is to improve the rutting and cracking resistance of the binder.”
By their nature, soybean plants help to reduce carbon dioxide (CO2) levels in the atmosphere because plants absorb it. “Polymers made from plants and trees can be considered carbon negative, possibly offering carbon credits,” added Tran.
Further environmental benefits are reaped along the production chain of bio-based polymers. “On average, it takes two pounds of [petroleum] oil to make one pound of polymer,” offered Hohmann. “By contrast, it takes just under one pound of soybean oil to make one pound of polymer.” Test results so far also indicate that the mix design may be optimized to increase the amount of RAP used to make the asphalt mix.
Sustainability is only half of the equation. Regardless of the potential environmental benefits, the soybean-based polymer must perform as well as petroleum-based binders in the lab and field to offer true benefits for the industry. For that, Colorbiotics worked with NCAT to test the bio-based performance-graded binder against a standard control mix to analyze and compare performance. More than a third of the way through its second three-year cycle, “both sections are performing well at this point,” commented Jason Nelson, NCAT Test Track manager.
Passing Grade
NCAT designed the experiment to evaluate the impact of the new biopolymer on asphalt binder, plant-produced mix and field performance on the NCAT Test Track. Biomag includes soybean oil to improve the resistance of asphalt binders to oxidative aging. It was blended at an asphalt terminal and delivered to East Alabama Paving, who produced the mix paved at the test track.
The difference between the two new surface mixes tested by NCAT showed only in the type of virgin asphalt binders. Test Track Section
W10 was paved with mix using the asphalt binder modified with the Biomag biopolymer, while the control section E5A included the binder modified with the traditional petroleum based SBS polymer.
“We produced a mix with the biopolymer that matched the SBS polymer control mix to get an apples-to-apples comparison,” offered Buzz Powell, associate director at NCAT and research professor at Auburn University.
Aggregate gradation for the surface mix included a 12.5-millimeter (0.50-inch) nominal aggregate size, and 20% RAP was introduced at a 12.5-millimeter (0.50-inch) size with 5.5% binder and granite aggregate plus a local sand. Volumetric design parameters for both included 4% air voids, 5.3% total combined binder content with a 4.9% effective binder, and a 2.5% maximum specific gravity.
Binder analysis was based on test results of both the virgin binders and the extracted plant-produced asphalt mixtures that included RAP. A PG76-22 SBS modified binder was used for the control for E5A, while the supplied W10 experimental binder mixed at the terminal offered a performance grade of PG70-16. Reviewing the binder test results, researchers noticed differences in the biopolymer when comparing the test results of the virgin and extracted binders.
The asphalt samples at the plant were mixed at a higher temperature than in the lab, and as a result, the extracted W10 biopolymer binder offered a high-temperature performance grade of 88°C, like the E5A control mix. Additionally, the low-temperature performance of the extracted E5A binder increased from –22°C to –16°C, whereas the extracted W10 binder maintained its low-temperature performance of –16°C. Therefore, both extracted mixes showed the same performance grading.
Hohmann explained the W10 performance improvement of the extracted binder. “There is a reaction that occurs when mixing plant temperatures that we didn’t anticipate happening. Between tank to pavement, the increase in heat catalyzed a reaction not seen in the