
7 minute read
ASCO INVESTS IN DECREASING DOWN DAYS B ASCO INVESTS IN DECREASING DOWN DAYS
According to Watson, ASCO is the largest asphalt supplier in its region on the west side of the Ohio River. The company has experienced steady growth since 2010, increasing tonnage from 150,000 to 370,000 tons a year. “They’ve been able to grow so much because of the amount of mix they’re laying at [sister company Libs Paving],” Watson said. “They’ve gained a couple hundred thousand tons worth of paving in the last several years, and ASCO supplies 99% of what they lay.”
“With just one plant, the growth has been purely as a result of increasing tonnage at this plant,” Watson said. That’s why, when Watson joined the family-owned company, the owners’ primary goal was to minimize down days. “If we have a down day at our only plant, the paving crews will keep paving but they’ll have to buy the mix from somewhere else. So, one down day is very expensive.”
Not to mention, Watson added, when the crews buy mix from other suppliers, the company has less control over the quality of the product. “The vast majority of the asphalt we lay is driveways and parking lots, which often require a lot of handwork,” Watson said. “So having quality mix is particularly important. It’s not just about quantity, it’s about producing the highest quality mix possible.”
Maintain To Maximize
Watson said the biggest challenge to reaching zero down days is staying on top of plant maintenance. “You have to anticipate what’s going to break next and develop a plan to get ahead of it,” he said. “I’ve seen many companies run a plant into the ground and wonder why it won’t run well, breaks down constantly or is inefficient.”
Good plant maintenance, he said, is step one.
When Watson first started at ASCO, there was no set preventive maintenance schedule and the company outsourced a lot of its plant maintenance. “They were running it until the plant was on its last legs and then bringing in a crew to fix it,” Watson said. “That was one thing we immediately changed.”
ASCO had planned to hire a ground man for the plant, but Watson recommended instead finding someone with more industry experience who could be a mechanic specifically for the plant. Watson also made a list of parts that needed to be replaced as soon as possible and implemented a preventive maintenance schedule.
“Now, our mechanic greases the plant, looks at problem areas and keeps an eye on the plant every day,” Watson said. “We might go a week without seeing any issues, or we might experience daily problems that we can correct overnight.”
“Despite doing our best with preventive maintenance, it’s something we’re still struggling with,” Watson said. For example, when a repair caught them off guard in December 2022, the staff spent 16.5 hours repairing the rigging on the drum and swapping out a trunnion so the plant was ready to make mix the following morning. “I think staying ahead of maintenance with high tonnage will always be a big challenge.”
One way to minimize that challenge, Watson said, is to invest in the plant whenever necessary. “Nothing on the plant is too expensive to repair or replace compared to the cost of downtime,” he said.
For example, when Watson was at a previous job, several plants had faced electrical problems for years. Ultimately, each plant was rewired and by doing so resolved a persistent problem. “If you're having problems in a certain area, rebuild it, replace it,” Watson said. “If you put on a Band-Aid, it better be temporary.”
Another change ASCO has implemented is more lab testing. “Because we run a whole lot of private mix and are often short-handed, the plant never did a lot of testing,” Watson said. But, testing can have a big impact on the plant’s bottom line. For example, he added, “Are we losing money because we’ve been running the last month with AC content that’s higher than it needs to be? Our best month in 2022 was 57,000 tons, so one little thing can make a big difference over the course of a month, either in terms of cost or in terms of the quality of the mix you’ve produced.” Now, the company tests its mix weekly.
Invest In Zero Down Days
Given that mindset, ASCO has been aggressively investing in equipment to minimize down days while maximizing efficiency. Just in the past year, the company has invested in a new baghouse, burner, hot oil heater control system, RAP crushing system and 300ton silos.
“The old baghouse was falling apart and limiting our production,” Watson said. “So that was the first major thing we replaced.” ASCO chose a CWMF Dust Eater baghouse due to its superior design, he added, and its ready availability during the plant’s planned downtime. ASCO replaced the bag house during seasonal shutdown in February 2022.
In April 2022, they installed a Vulcan Burner from Reliable Asphalt Products after facing efficiency issues and parts availability issues with their existing burner. “Going from an open air burner to a total air burner completely changed how the plant runs, too,” Watson said. “It increased our heat output while increasing our fuel efficiency.”
“The Vulcan Burner alone lowered our fuel usage by about 20% from 2021 to 2022,” Watson said, estimating that it saved them around 20 to 25 cents per ton. “Spread across 370,000 tons, it was definitely worth it.”
LEFT: Watson was impressed by ALmix’s quick and professional install. “They knew what they were doing and they knocked out the silo erection really quick over a long weekend.” MIDDLE: Watson said the biggest challenge related to ASCO’s recent investments was bringing together all the pieces within the company’s preferred timeline while minimizing downtime related to equipment installation. RIGHT: In June 2022, ASCO installed the Burke Heating Systems hot oil heaters and control panels from Reliable Asphalt Products. Watson chose this system because of his familiarity with Reliable and its parts, and for the system’s remote monitoring capabilities.
Watson also appreciated the availability of parts, given that Reliable is less than 45 minutes’ drive away. “My biggest concern with all this new equipment is parts availability,” he said. “Whatever parts the manufacturer keeps readily available is what I want on the silos, the chain, the slats, sensors, whatever it is. I don’t want to customize the equipment where I’ll have to track down special parts if we go down.”
Watson also applies this mentality to ASCO’s existing equipment. For example, the company changed out some of the parts on its 10-year-old Dillman drum and thrust rollers to ones that are more readily available.
The next investment ASCO made was in June 2022, when it installed the Burke Heating Systems hot oil heaters and control panels from Reliable Asphalt Products. Watson chose this system because of his familiarity with Reliable and its parts, and for the system’s remote monitoring capabilities.
“One of the worst downtime experiences is when you come in the morning and your hot oil heater is out,” Watson said, adding that he no longer needs to worry about that. “If it fails, I’m notified immediately and can remote in and reset it from home. Since then, we have never come in to a cold plant.”
Watson estimates that 40 dump trucks and 120 employees waiting several hours for the plant to get hot easily costs $15,000. “So, it was definitely worth it,” he said. “The system paid for itself in 2022 alone.”
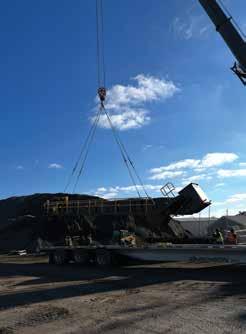
The last big addition in 2022 were two 300ton silos from ALmix, Fort Wayne, Indiana.
The primary reason for the investment was to load mix more quickly. Prior to the addition of the two new silos, ASCO had three silos that held less than 500 tons total (two 150ton silos and one 180-ton silo).
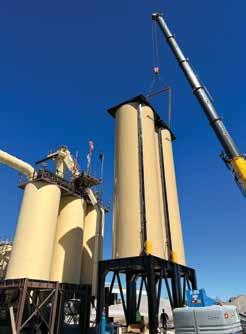
“We generally store mix every single night, unless it looks like rain,” Watson said, adding that some mornings, they might have 30 or 40 trucks to load. “I’ve always been big on storing mix rather than coming in at 4 a.m. or risking being broken down the next morning.”
The plant crew usually starts loading trucks around 6:30 a.m. and strives to be done by 4:30 p.m. on weekdays. “We never load trucks until 7, 8, 9 p.m. like some companies do and we don’t do night shifts,” Watson said. “When we work Saturdays, we work half-days.”
“You can't work until 8 or 9 p.m. every night and expect people to stick around nowadays,” Watson said. “The owner tries to make sure people have plenty of family time and he isn't breaking people down.”
With the new silos, ASCO will be able to store more than 1,000 tons of mix for the next morning to get the trucks to the crews as quickly as possible. “Before the new silos, the most we've been able to load from 6:30 a.m. to noon is 2,500 tons,” Watson said. “An extra 600 tons of storage will mean we'll easily be able to do more than 3,000 tons by noon.”
“When you look at man hours and trucking costs, getting out an extra 600 tons a day in the same amount of hours is huge for us,” Watson said. “It can be thousands of dollars a day, so that's where the silo system really pays for itself.”
The price quotes Watson received on silo options were competitive, but he chose ALmix because he was familiar with their parts inventory, knew it would be easy to get parts (especially with ALmix’s headquarters within driving distance), and he had positive previous experience with ALmix silos. “I like how heavy they’re built,” he said. He was also impressed by their quick and professional install. “They knew what they were doing and they knocked out the silo erection really quick over a long weekend.”
Trends Continue Into 2023
In January 2023 and over the course of its winter shutdown in February, ASCO made two additional upgrades at the plant. It installed the Honey Badger RAP Crusher from
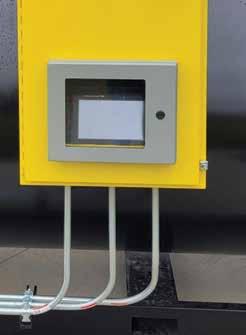