
40 minute read
More Money, More Tons, More
CONVEYOR COMPONENTS
The Model RS-27P cable support, manufactured by Conveyor Components Company, Croswell, Michigan, joins the ranks of the RS-23 and RS-27 and provides another way to properly support e-stop cable for the product line of engineered safety stop switches. The RS-27P “pig-tail” or “corkscrew” cable support allows the installer to quickly install the pull cable without having to thread the cable through a traditional eye.
E-stops or emergency cable pull controls are required in many parts of the world to protect personnel from dangerous situations, and are designed to act as an emergency stop for conveyors and other moving machinery.
The RS-27P cable support consists of zinc plated steel support with spiral eye and comes complete with two hex nuts and a lock washer. Installation involves a ½-inch diameter hole in the conveyor side-rail or frame.
For more information, contact Conveyor Components Company at (800) 233-3233.
CWMF
The Wedge-Lok™ Tire Suspension System from CWMF Inc., Waite Park, Minnesota, has been in use for over 25 years. The design allows the end user to secure the tire to the drum and eliminate tire slippage by simply adjusting setscrews. The inclined plane mechanism provides superb holding strength and there is no need to apply shim stock, according to the manufacturer. A secured and balance tire extends the life expectancy and reduces costly downtime. CWMF will be introducing a new featured
The Wedge-Lok™ from CWMF retrofits on this CMI drum.
video onto their website (summer 2021), which will demonstrate how to properly install the Wedge-Lok™ Tire Suspension System.
For more information, contact sales@cwmfcorp.com or visit www. cwmfcorp.com.
CURRY
Curry Supply Company, Martinsburg, Pennsylvania, has appointed Cory Wilson as the company’s vice president of operations. In this role, Wilson oversees all elements of the company’s supply chain, manufacturing, and engineering, ensuring that excellence in quality remains central to Curry’s customer value proposition and growth strategy. Wilson joins Curry after serving in various roles at JLG Industries in McConnellsburg, Pennsylvania, for the past 17 years.
DOOSAN
The front of the wheel loader has been considered a major safety issue due to blind spots. That's why Doosan Infracore, Seoul, South Korea, has introduced a “transparent bucket” function on a wheel loader. The system allows wheel loader drivers to see blind spots in front of the bucket via a monitor in the cab.
The system records images in front of the wheel loader with cameras installed at the top and bottom of the bucket and shows the combined images in real time using a curved projection method. According to the manufacturer, Doosan Infracore is the first company to develop and apply a front projection function like this for a construction machine.
EVOQUIP
EvoQuip®, a Terex brand, has launched the revamped Bison 120 jaw crusher with a new fuel efficient Deutz 2.2 L3 Engine Stage V engine, larger crusher drive motor and easily adjustable belt tensioner to aid tensioning and belt replacement. The new style panels offer access to the engine bay from all three sides, making maintenance and servicing easy, according to the manufacturer. The revamped model now has the addition of a programmable logic controller (PLC) with intuitive push button control panel as standard along with a remote control to enable the operator to adjust the jaw’s closed side setting (CSS) and to start or stop from the cab. The Bison 120 features a 680 mm by 400 mm single toggle jaw crusher. The jaw is driven hydraulically, allowing the customer the ability to reverse the crusher to clear a blockage as well as being able to run in reverse permanently for sticky applications such as asphalt. The ability to adjust the jaw setting and operate the plant from the remote control allows for a fast and simple set up for the customer.
For more information, contact your local Terex dealer.
H&B
Haver & Boecker Niagara, St. Catharines, Ontario, highlights the advantages of pairing eccentric screening technology with polyurethane screen media. The combination of the eccentric machines in its Niagara F-Class and Niagara N-Class with polyurethane media, such as Ty-Max and Ty-Deck, are designed to offer more uptime, fewer screening problems and higher screening efficiency. Here’s what they’ve learned:
“We pride ourselves on providing our customers technology that advances their operations’ productivity and profitability,” said Karen Thompson, president of Haver & Boecker Niagara’s North American and Australian operations. “Though each of these two technologies are highly beneficial on their own, their benefits dramatically increase when combined. The result for our customers is less downtime and better screening.”
Advanced eccentric screening technology implemented by Haver & Boecker Niagara, combined with the benefits of the manufacturer’s polyurethane media has been shown to reduce pegging and blinding; handle high impacts; improve screening action and increase screening efficiency; and lessen vibrations transmitted to the structure.
Eccentric screening optimizes vibrating screens for handling heavy-duty applications, such as classifying and scalping. The eccentric shaft design forces the screen body to follow the shaft movement. While it travels upward, the counterbalance weights move in the opposite direction and create an equal force to that generated by the body. As a result, the forces cancel each other out while generating a consistent positive stroke that minimizes structural vibration and handles material volume spikes without losing momentum. This leads to the machine transmitting fewer vibrations to the structure and allows for longer component life. Additionally, the design creates a self-cleaning action that reduces blinding and pegging while improving overall screening efficiency.
Haver & Boecker Niagara’s polyurethane media then offers a combination of open area and wear life for both wet and dry applications. It is poured open cast, resulting in 1.5 to 2 times longer wear life than injection-molded products sold at comparable prices, according to the manufacturer. In addition, open cast polyurethane permanently hardens when cured to maintain its chemical properties to improve wear life.
Operations can choose wear liners for improved screen media protection and even higher performance and longevity from their machines. Liners for vibrating screen cross beams are also available.
For more information, visit the H&B website.
JOHN DEERE
Deere & Company, Moline, Illinois, announced the four companies that will be part of the 2021 cohort of the Startup Collaborator program. This program was launched in 2019 to enhance and deepen its interaction with startup companies whose technology could add value for John Deere customers.
“The Startup Collaborator program continues to build tremendous interactions between startups and John Deere,” said Julian Sanchez, director, Emerging Technology for John Deere. “This year is no different as this diverse group of companies has great potential to transform our markets.”
Deere is pleased to welcome into the Startup Collaborator four leading startups that are working to transform their industries. These companies include:
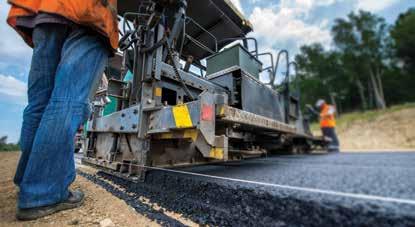
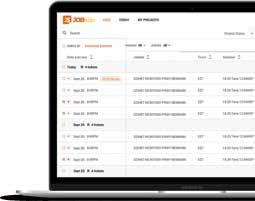
• Nori—A company working to reverse climate change by building a carbon market where all types of consumers can purchase carbon credits directly from farmers. • NVision Ag—A company working to help corn farmers make nitrogen management decisions based on data modeling and aerial imaging. • Scanit—A company that provides physical detection and classification of airborne plant pathogens before widespread disease onset. • Teleo—A company that is converting construction and mining equipment into tele-operated robots controlled by operators working remotely from a desk, thus unlocking productivity and operational gains for contractors.
The Startup Collaborator is a year-long program that provides flexibility for Deere and startup companies to test innovative technologies with customers and dealers without a more formal business relationship. Startups also gain affiliation with and mentoring from a world-class leader in technology for agricultural and construction equipment.
“Innovation is one of our company’s core values. The Startup Collaborator program is one way we can continue the innovative spirit that has helped define Deere for more than 180 years,” Sanchez said.
PLASTIQ
Plastiq, headquartered in San Francisco, announced its end-to-end Intuit QuickBooks online integration in the payments industry to offer businesses an up-to-date, accurate record of all outgoing payments, with no manual entry required. The new integration will import invoices directly from QuickBooks, quickly identifying and populating all essential information such as vendor, amount due, invoice due date and more. Once the invoice has been paid through Plastiq, the platform will then export the payment information back into QuickBooks, including differentiating the portion of the payment applied to the invoice from Plastiq’s transaction fee.
Plastiq has revolutionized how its more than 1.5 million customers optimize working capital by providing an all-in-one solution that enables them to pay or accept payment for anything with cash or a credit card, even where credit cards or digital payments are not accepted. Thanks to strategic partnerships with companies including US Bank, Visa, Mastercard, Silicon Valley Bank and more, any business can use Plastiq to pay or get paid.
PYRAMEX
Wearing your prescription eyewear is not enough on the job site. Pyramex® Safety has designed four impressive over-the-spectacle protective eyewear options that are so lightweight, you’ll barely know you have them on. Select from four models—OTS®, OTS XL, Cappture™ or Cappture™ Plus—all constructed of hard-wearing materials for durability and featuring lens technology that works to protect your eyes blocking high percentages of harmful UV rays. All are ANSI rated and impact tested.
Pyramex Safety has more than 2,000 distributors in over 60 countries and is committed to investing countless hours to research, design and testing to ensure Pyramex products meet the highest industry safety standards.
STANSTEEL
Asphalt plant safety is the No. 1 priority for every asphalt producer. It is vital to take steps to keep everyone on the asphalt plant safe from harm. The largest number of asphalt plant injuries comes from hot liquid asphalt cement. With the ever-changing governmental regulations of having to sample liquid AC more frequently, it is time to remove the person from the process. Stansteel and Hotmix Parts, Louisville, Kentucky, engineered the asphalt Safe-T Station to do just that. The Safe-T Station from Stansteel
The Safe-T Station is an in- and Hotmix Parts was designed with line liquid AC sample port plant personnel and safety in mind. that encloses the sample container, immediately removing any harm of burn or injury. The Safe-T Station is large enough to fit a one-gallon sample container but also provides the safety of taking a quart size sample. The door of the enclosed collection container includes a viewing glass so the person collecting the sample can get the amount needed. The Safe-T Station takes safety another step further by not allowing the plug valve to release AC unless the door is securely closed. There is also a safety latch for the plug valve handle when not in use. This ensures the plug valve is never accidently activated when no one is present.
The Safe-T Station is versatile to your plant setup. The Safe-T Station can be incorporated into all brands and manufactures of asphalt plants. The AC line is fully jacketed and comes in 3-inch or 4-inch lines and can also be horizontal or vertical. Many have even begun using the Safe-T Station after the unloading pump to ensure they are receiving the correct AC from the refinery for total quality assurance.
For more information, visit https://stansteel.com/asphalt-plantcomponents/.
TRUX
TRUX™, Waltham, Massachusetts, has launched a new widget within its Order Delivery Tracker tool for material producers. The debut of the delivery velocity visualization provides customers with greater insights into their scheduled deliveries and helps them monitor and improve their jobsite operations and efficiency.
With the addition of this widget to the Order Delivery Tracker, material producers can provide a more enhanced customer service experience to their customers. The new tool builds on the existing ability to track deliveries throughout the day and get an accurate estimated time of arrival for material en route to the jobsite. The widget displays the number of tons delivered per hour, the number of scheduled tons per hour and the average delivered tons per hour, all designed to measure delivery velocity on a broader order level.
“Since we launched the Order Delivery Tracker in October of 2019, we have been able to provide material producers with a detailed view of delivery progress for their customers,” said Bart Ronan, CEO of TRUX. “The introduction of this new widget takes our tool one step further and provides order-level insights to help material producers provide a differentiated service to their end-customers. Jobsite operations are significantly impacted by the number of tons delivered per hour and there was not an accurate way to capture this information in the field. Time-sensitive materials, like asphalt, or equipment that is rated for a particular velocity rely on accurate delivery velocity and now we are able to provide that through our Order Delivery Tracker.”
The delivery velocity widget is the first in a series of widgets TRUX plans to launch in the coming months aimed at helping material producers optimize delivery management and prepare contractors to receive material on-site. The additional visualizations, expected later this year, will allow material producers to provide even more value to their customers, with deeper insights into delivery status, jobsite efficiency, and overall material supply.
TSURUMI
Tsurumi America has launched a new content website for pumping specialists called Built For Work. Its site at TsurumiPump will continue to serve as Tsurumi’s main website for company and product information.
“Tsurumi’s new content website is an effort to consolidate our fantastic customer stories, engineering breakthroughs, maintenance tips, repair videos and other educational materials into one place,” said Glenn Wieczorek, managing director of Tsurumi America.
Visitors can find information on pump applications in the construction, wastewater, mining and industrial, and water feature sectors. A pump education section will help homeowners and professionals find pump maintenance tips, best practices and other technical and industry-related information.
WESTERN GLOBAL
Western Global, Troy, Michigan, which provides portable tanks and dispensing equipment for the storage and handling of fuels, lubricants and other fluids, announces the addition of Jayna Rodgers as its Central U.S. regional sales manager. Rodgers will be responsible for building the territory while bringing in new business and maintaining current clientele in Texas, New Mexico, Colorado, Wyoming, Montana, Oklahoma, Kansas, Nebraska, South Dakota and North Dakota. Rodgers’ 16 years of industry experience includes five years as a senior fuel consultant for 4Refuel, a refueling service company with U.S. locations centered in the Dallas-Fort Worth area. There she received the top sales award five years in a row and played a crucial role in building the company’s construction division. Prior to that, Rodgers owned a construction company in Houston where she managed the day-to-day fuel needs of the company.
IMAGINE YOUR DREAM
YOUR BUSINESS STARTED AS A DREAM, TO GROW AND PROFIT. To get the personalized attention you want to help you on your way. The customization you need to meet your business’s specific production goals. Consult with one of our specialists today to help configure just the right asphalt plant for you. Start your custom plant design today.
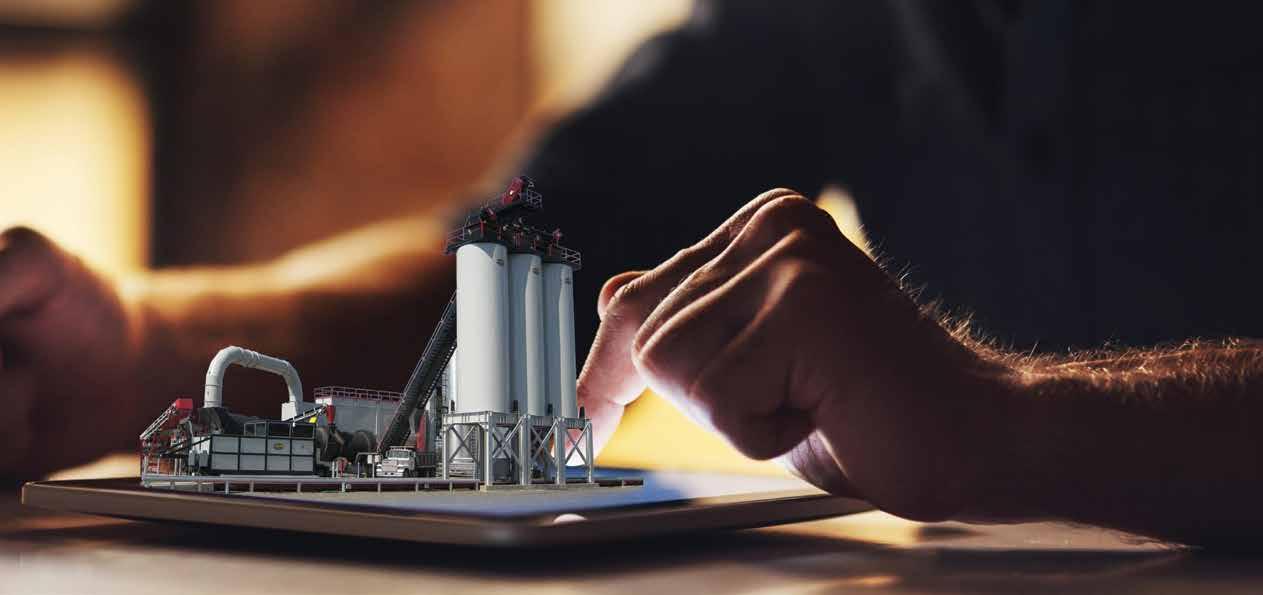

KLS exclusively uses Graco LineLazers and LineDrivers to perform its work. “They’re top of the line,” Keathley said. “We also enhance our stripers with the latest gadgets in order to help us perform our work in an efficient manner.”
By Sarah Redohl
WWhen Mike Keathley first opened Keathley Line Striping (KLS), LaVernia, Texas, three years ago, he used to mention to potential customers that everyone on his crew is deaf.
“We found that this kept losing us bids,” he said. “There is a stigma that comes with being deaf. People don’t understand what we can do and therefore become hesitant to allow us to submit a bid.”
KLS is a 100 percent deaf-owned and employed company. After facing this early discrimination, Keathley no longer mentions this to prospective clients.
“When customers call us, they are not asking us for a medical history,” he said. “They are asking us to perform a job so there is no reason to share that we are deaf. When we show up on a job site, whether we’re doing an estimate, a walk-through or performing the job requested, we find that people are blown away. They can see we are professionals and leaders in our industry.”
A Culturally Deaf Crew KLS has a crew of three and additional part-time staff as needed. Every member of the crew is culturally deaf, including Keathley. A person is culturally deaf if he or she has always been in a predominantly deaf environment. In Keathley’s case, he attended a deaf school, his children are deaf and most of his friends are deaf.
“I live in a world of sign language and closed captioning,” Keathley said. “The only time I interact with hearing people is when I go shopping or go to work.”
Although Keathley’s whole team is deaf, he doesn’t hire based on disability status. “I hire them because I know what they are capable of,” he said. “As a result, I am blessed to be able to provide an equal footing for a disenfranchised group of people.”
Having a deaf team also improves communication on the crew, which uses American Sign Language as its primary language. Furthermore, Keathley said he and his crew have a strong desire to prove its work ethic and overcome discrimination.
“We always bust our butts and want to make our customers happy with our work,” he said. “Nobody has anything to fear by hiring deaf employees.”
However, KLS still regularly faces discrimination as a deaf-owned and operated business.
Recently, the company was awarded some work by a major industry player. While performing the work, a store manager became upset when the crew asked him to either remove his mask, so the crew could read his lips, or to write down what he was saying.
“He got very agitated that we could not understand him and kept yelling at us,” Keathley said. “I kept telling him we are deaf and that we
Every member of KLS’s crew is culturally deaf, including Keathley. Not only does this provide jobs to a disenfranchised group of people, Keathley said, but it also improves communication on the crew, which uses American Sign Language as its primary language.
can’t tell what he’s saying, but he became so agitated by this that I could do nothing but walk away and continue to finish our work.”
Although the team finished the job and the customer was happy with the results, Keathley was shocked by their lack of understanding when it comes to communicating with deaf people. “What if another customer refuses to proactively communicate with me or my team?” he said. Although his company appreciated the work, it put Keathley in a difficult situation. “We cannot allow them to hold our disability against us as a condition of employment, so we chose to let them go as a customer.”
In another instance, a store manager insisted that Keathley’s team needed to have a hearing person on site while striping the facility. Keathley himself arrived on the job shortly after the manager’s request.
“When I introduced myself as the deaf owner of the company, the manager’s eyes got so big and he got so flustered,” Keathley recalls, but the manager remained adamant that they needed to have a hearing person on site. “He felt we needed to be supervised; he just didn’t know what deaf people can do.”
The crew packed up and left, but Keathley didn’t quit. He reached out to the property owner who hired his company for the job, who was furious at the manager’s behavior. “The property owner had us return to complete the job and happily paid us for the extra time.”
“We know most people don’t maliciously discriminate,” Keathley said, “but people do discriminate and that nonsense needs to stop.”
Although the company battles audism from time to time, Keathley is heartened that many of his customers find their story uplifting and inspiring. “We actually get a ton of work from it.”
Safety Without Sound Keathley reiterates that his company adheres to all OSHA rules and federal, state, county and city laws. He has generally modeled KLS to avoid work situations that would require him to obtain an exemption based on his crew’s disability. However, he knows how to handle these situations when they arise. For example, there is a hearing test required to obtain a Department of Transportation medical card, for which KLS was able to request an exemption from the Federal Motor Carrier Safety Administration (FMCSA) because they are protected by the Rehabilitation Act of 1973. The Rehabilitation Act prohibits discrimination on the basis of disability in programs conducted by federal agencies, in programs receiving federal financial assistance, in federal employment, and in the employment practices of federal contractors.
“Safety is paramount when working in active roadways and parking lots,” Keathley said, regardless of circumstances. KLS has invested in approximately 24 LED safety warning lights on its truck and enclosed trailer, and four on its line drivers, in addition to wearing bright colored reflective safety uniforms. However, Keathley recognizes that there are only so many safety products one can implement.
“We also run a crew that’s usually one man larger than the average striping crew so we have an extra set of eyes on our job sites,” he said. “We keep our heads on a swivel and we look out for each other.”
He’s also found this approach a bit easier because roughly 80 percent of KLS’s work is parking lots. Fifteen percent are unique jobs such as helipads, basketball courts, playgrounds, athletic fields, etc. Only 5 percent are roadways. “We’re not a long line striping company, so public roads aren’t a big part of what we do, but that could always change in the future as we grow,” Keathley said.
KLS exclusively uses Graco LineLazers and LineDrivers to perform its work. “They’re top of the line,” Keathley said. “We also enhance our stripers with the latest gadgets in order to help us perform our work in an efficient manner.” For example, its stripers are equipped with gun raisers to raise and lower the paint guns without getting off the machine. “I firmly believe we remain safer by keeping our butts in our seats, instead of getting off and fiddling around with our machines in an open parking lot,” Keathley said.
A Self-Taught Striper Before launching KLS, Keathley had been performing repair work for friends of his mother and sign language interpreters. When his mother passed away, Keathley struggled to find new work and began exploring the commercial market. However, he faced regular discrimination and rejection.
LEFT: KLS is a 100 percent deaf-owned and employed company. CENTER: Although the company battles audism from time to time, Keathley is heartened that many of his customers find their story uplifting and inspiring. “We actually get a ton of work from it,” he said. RIGHT: Roughly 80 percent of KLS’s work is parking lots.
“On my last bid to a general contractor, I was basically told we had the job,” he said. “When I went to discuss the work with him, he ran me off and said he couldn’t be responsible for me. I was crushed. I had a kid on the way and no money. I walked out of that building destroyed.”
He sat down on a bench right out front and stared into the parking lot nearly in tears. “Then it hit me,” he said. He noticed that the parking lot in front of him needed striping, so he went home, looked up property tax records and mailed the property owner a letter. Soon, he got the job. “I had effectively eliminated the middle man and there was no need for anyone to feel like they had to be ‘responsible’ for me.”
Although Keathley’s brother briefly striped parking lots many years ago, Keathley is a self-taught striper. But, as he learned, he noticed a lack of training resources.
“There isn’t much offered on how to learn to become a pavement markings specialist,” Keathley said. So, he began creating his own library of training videos that are useful to both deaf and hearing people. “The inability to hear is not the disability. It is the lack of access to language and information that is the real disability.”
The videos also improved his own performance. “I used to race motorcycles at the track and watching videos of our body position was critical to learning how to ride faster,” he said. “I applied that same logic to line striping.”
He would tape cameras to his striper and watch the videos over and over, improving each time. “Before I knew it, the videos started being shared and now people often turn to me for advice on how to line stripe.”
Mr. Fix-It In the summer of 2020, Keathley received a call from a paving company KLS often works with, who asked Keathley to correct a striping project at a 5A high school in Texas that had been performed by another striping company. When Keathley showed up on the job, the prior subcontractor had done such a poor job that the paving company had to sealcoat the lot so KLS could start from square one.
The school had been facing a unique problem. It had a rich football tradition, as well as a competitive marching band. The football team
held practice after school on the football field, but the band also needed the field to practice their formations.
The football field was right next to a large parking lot, onto which KLS striped a football field layout. “By day, it was a parking lot for students,” Keathley said. “By night, it was a practice field for the marching band.” It was a job that was easily fumbled by crews lacking KLS’s attention to detail.
The job required a lot of thought and planning among Keathley, the school’s grounds keeper and its athletic director. “The biggest obstacle was making sure the lot was up to code after merging the football field grid onto the parking stalls,” Keathley said.
To do so, the crew used yellow paint for the parking stalls and white for the football grid. The fact that the parking lot is used by the same students day after day, who are familiar with the lines, also helps. They also had to take care to ensure that the fire lanes were clear. In total, the job required 120 gallons of paint.
Furthermore, all of this had to be done within a week, before the start of the school year. After pulling through for the school under tight deadlines, KLS maintains an active working relationship with that school district to this day. “The customer was very happy with our work, and it has led to many other opportunities within that school district,” Keathley said.
Although people facing disabilities should not have to prove themselves any more so than others, Keathley has made the most of this circumstance and built a company known and respected for its performance and precision.
“We are professionals in every sense of the word,” Keathley said. “We know what we’re doing. All we ask is that people let us do our jobs.”

San Antonio Takes Pothole Patching to the Next Level
FFounded as a Spanish mission and colonial outpost more than 300 years ago, San Antonio, Texas, today is home to 2.3 million residents within its metro area. In fact, it is the seventh most populous city in the United States— and just 10 years ago it completed a streak where it was named the fastest growing of the top-10 largest cities in the country.
The city endures long, humid, sweltering summers that are bookended by spring and fall rains. With cool winters, the remnants of an occasional hurricane, and also stretches of hot, dry periods, the city truly experiences all manner of climate extremes throughout the year—all of which can cause havoc with the city’s 4,167 centerline miles of streets and roads.
“The extremely hot weather in our region, along with bouts of rain, create expansion and contraction of asphalt pavement, allowing water to seep into the asphalt and create potholes,” said Frank Orta, operations manager, Street Operations-West, for the City of San Antonio. “Our challenges also include high-plasticity soils with a lot of sand and clay, which hinder our pavement preservation program. With the combination of climate and soils, pothole repair is a year-round effort for us,” he added.
But San Antonio has stepped up its pothole repair game in the past several years, with the addition of four new spray injection pothole patching trucks to its fleet. The SP5 spray injection patchers, manufactured by Bergkamp Inc., are each capable of patching 100 potholes a day, where the city’s conventional trucks typically repair just 30 a day each. They have allowed the city to increase repairs from 35,000 potholes annually in 2016 to more than triple that output in fiscal 2019—while increasing safety for operators and the motoring public.
Safety First In 2016, the San Antonio City Council, after listening to community concerns and requests, chose to invest in revamping the city’s street maintenance program—including improvements in the methods used to repair potholes. Pothole patching is a hazardous undertaking for any city, much less a city the size of San Antonio. With a large number of 5-lane arterial and collector roads, the city wanted to find a solution that could not only improve and increase the patching efforts, but also keep crewmembers safer.
“Even with total lane closures, there is still a safety concern for our crews when they are out working on repairs,” Orta said. “And when you close a full lane, it is also expensive—costing more to close the lane than it does to repair the pothole.”
The city ultimately swapped its aging fleet of pothole repair trucks for all-new equipment in 2017, purchasing 16 new trucks—12 conventional patchers and four Bergkamp SP5 spray injection patchers. While Orta said safety is first and foremost for the city, the fact that the spray injection patchers are capable of repairing 100 potholes a day also factored into the decision to purchase the units.
By Mary Foster
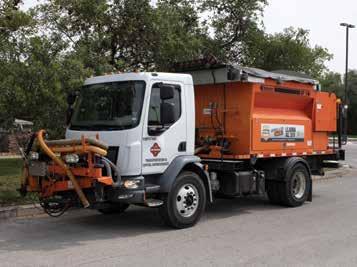
In 2017, the City of San Antonio, Texas, swapped its aging fleet of pothole repair trucks for all-new equipment—purchasing 12 new conventional patchers and four new SP5 spray injection patchers by Bergkamp Inc. One of the city’s spray patchers is pictured here.
Ready to Repair Spray injection is a less invasive patching technique than traditional patching methods, allowing the damaged pavement to be air-blown and repaired in minutes. On the SP5, a front-mounted boom provides a working radius of up to 13 feet in front of the truck. Fully operable from inside the cab for increased safety, the unit requires only one crewmember to operate.
The SP5 features three injectors in a rotating nozzle, which provides the emulsion and aggregate coverage. In a four-step process, the operator blasts compressed air through the unit’s hose to clean out and dry the hole. The damaged area is then sprayed with asphalt emulsion. The operator selects the proper gradation of aggregate from one of two chambers in the hopper to best match the characteristics of the road, and sprays that over the emulsion. Finally, application of a protective layer of clean stone protects passing vehicles from coming into contact with the asphalt emulsion.

Frank Orta is the operations manager, Street Operations-West, for the City of San Antonio.
Orta stated that the department liked the fact that “the units are always ready,” in that the operator mixes the emulsion and aggregate onsite as the pothole is repaired. “There is no prior mixing at the shop or material that can go bad,” Orta said.
He shared that they had to experiment some to find the right material and right aggregate for their roads. “For instance, we’ve learned that a Grade 4 washed rock works best for us. Also, we were using a rapid-set oil, but because of our climate, we were constantly having to clean and remove it from the nozzle, so then we went to a CSS1H slow-setting asphalt emulsion, and later to a PHPMS0.”
The spray injection patchers were fully integrated into San Antonio’s fleet by mid-2017. Orta said there was a bit of a learning curve involved in learning how the patchers best operated with San Antonio’s climate. “It’s definitely a skillset. The longer an operator is there in the position, the better the performance you will get from the repair.”
Bergkamp partnered with department members to help overcome the learning curve. The SP5 units the city purchased were among the first-generation units from the company. So, for the 2016 demos, Bergkamp sent engineers, in addition to sales team members, to both demonstrate the unit and answer questions. Then, after San Antonio purchased the four SP5 units, Bergkamp team members came back in 2017 and worked on the learning curve together with the city. Orta said the city has also cross-trained employees so that more crewmembers are familiar with the spray injection patchers. Engaging and Empowering the Public Around the same time that San Antonio revamped its pothole patching program, it also provided a big push to empower citizens to call in potholes via the city’s 311 system. With spring being the peak pothole season, the city has created an April awareness campaign for potholes that ties in with the annual Fiesta. “We have a phone bank, hand out literature, conduct interviews with the media and engage the public as much as we can,” Orta said.
The city also has incorporated a full-time pothole investigator into its team, joining four other street maintenance investigators who travel the city’s streets in 10 council districts and proactively call in potholes. For identification purposes, San Antonio defines a pothole as being 3-foot x 3-foot or smaller.
“We now have a two-business-day guarantee, where from the moment the pothole is identified or reported to our completing the repair, we promise to fix it. So, from Monday through Friday, that’s typically within 48 hours,” Orta said. “It took us about six months to get the program running the way we want it to run. Our goal is to have the machine, the operator and the materials reach perfection,” he added.
As a result of these efforts, Orta said the culture has changed, explaining that eight out of 10 calls in 2015 involved complaints from citizens. Today, only one in 10 calls may involve a complaint, and often that turns out to be a misunderstanding.
Spray injection patching with the SP5 takes place without the operator ever leaving the cab. First, the operator blasts compressed air through the unit’s hose to clean out and dry the hole. Then, the damaged area is sprayed with asphalt emulsion. After that, the operator selects the proper gradation of aggregate to best match the characteristics of the road, and sprays that over the emulsion. Finally, the machine applies a protective layer of clean stone to protect passing vehicles from coming into contact with the asphalt emulsion.
“Since we’ve revamped our program, getting the public engaged and proactively searching out potholes, we hear consistently that we are doing a great job. The citizens know we have their backs. When they call in, they trust that we will get out there and repair the potholes quickly. They are seeing the power of a community that invests in its streets,” Orta said.
Checklists Make Preservation Perfect
IIn the mid-2000s, the Federal Highway Administration (FHWA) published a set of checklist pocket guides to help state and local highway preservation, maintenance and inspection staff. The FHWA said the goal of the checklists was to help these professionals use “innovative pavement preservation techniques.”
However, anyone in our industry knows that what was innovative in the mid-2000s is likely standard practice today. That’s why the FHWA has revised its old checklists and created new checklists for additional strategies.
In keeping with the FHWA’s e-construction initiative, the Administration has launched a free mobile app to make these checklists easier to access and assist agencies and contractors with the transition to a paperless construction environment.
The app, called Checklist, allows users to create a file for each project and choose appropriate checklists for that project. Users can also use the project file to collect notes and add pictures to the checklists. It’s also possible to export project file checklists from the app, as well as accompanying notes and photos as a PDF to share or save.
Checklist houses a wide variety of checklists outlining key activities to perform before, during, and after pavement and maintenance construction activities.
For example, the app’s microsurfacing checklist outlines documents to review before the project begins, including project plans, specifications and special provisions; the traffic control plan; safety data sheets; and a handful of other important documents. It also guides the user through a review of the project to ensure it is a good candidate for microsurfacing and specific types of distress to watch for. There is also a checklist related to materials (aggregate moisture content, asphalt emulsion temperature, etc.), steps to prepare the surface (patching has been completed, thermoplastics removed, etc.), equipment inspection checklists (sweeper, microsurfacing paver and spreader box, etc.), weather requirements (temperature, humidity and wind recommendations), and application rates and calibration tasks. The checklist then guides the user through best application practices for every step of the process, including opening the road to traffic and troubleshooting common issues.
The latest series of pavement preservation checklists on the app includes resources on crack treatment, chip seal, thin hotmix overlays, fog seals, slurry and scrub seals, microsurfacing, cold in-place recycling, patching, full-depth reclamation, and ultrathin bonded wearing courses, among other topics.
The app is available for both iOS and Android devices. On Android devices, search the app store for “pavement preservation checklist,” and on Apple devices, the app can be found by searching for “Iowa State University pavement preservation.” The checklists are also available as PDFs from the FHWA website at fhwa.dot.gov/pavement/preservation/ppcl00.cfm
The checklists are part of the FHWA’s Every Day Counts (EDC) program, which promotes strategies for the improvement of the United States’ transportation systems.
By Sarah Redohl

Busby Construction Co. Inc., Atkinson, New Hampshire, utilizes its Roadtec SX-8e for fulldepth reclamation work. Photo courtesy of Roadtec Inc., Chattanooga
Vermont’s Most Populous City Executes, Monitors Sustainable Fog Seal
TThe City of Burlington recently applied an advanced penetrating asphalt rejuvenator fog seal to residential streets—the first time Vermont’s most populous municipality has used the sustainable preservation treatment. Previously, the city of approximately 43,000 residents has used crack sealing as its primary pavement preservation technique.
A regional college town, Burlington is home to the University of Vermont and Champlain College, functions as the seat of Chittenden County, and serves as a major historic and cultural center for the Green Mountain State. As the most populous city on Lake Champlain, Burlington is also the repose for 295 streets that are maintained by the city’s Department of Public Works, headed by Chapin Spencer.
DPW’s Maintenance Division is responsible for performing some of the more obvious tasks of the Department such as installing and maintaining nearly 130 miles of sidewalks, and maintaining the 95 centerline miles of streets. The latter includes crucial services such as street sweeping, pothole patching, painting road lines and crosswalks, and most importantly, protecting and preserving the pavements of those streets.
The travelled miles of Burlington roads are categorized into four classes for state aid apportionment: They are approximately 7 miles of Class 1, 20 miles of Class 2, and 65 miles of Class 3. Class 4 town highways are all those that are not Class 1, 2, or 3 town highways or unidentified corridors, and currently amount to less than three miles.
VTrans and the state share the responsibility and cost of maintenance, repair and replacement of Class 1 and 4 roads, but the lion’s share of responsibility and related costs for Class 2 and 3, which together amount to 90 percent of all travelled miles, are borne primarily by the City.
Class 2 town highways are the most important highways in Burlington. As far as practicable these secure trunk lines of im-
By Paul Fournier

A full-lane-width application of Delta Mist is performed on one of several streets fog sealed by the contractor indus. The crew used a Ford 750 Super Duty truck mounted with a 2,000-gallon Etnyre tanker to spray the product at ambient temperatures.
proved highways from town to town and to places that have more than normal amount of traffic.
Class 3 town highways have simple, clear-cut minimum standards: They have to be “negotiable under normal conditions all seasons of the year by a standard manufactured pleasure car. This would include but not be limited to sufficient surface and base, adequate drainage, and sufficient width capable to provide winter maintenance…”
Until recent years, Burlington has relied heavily on an annual Street Reconstruction Program to keep its Class 3 streets up to standards. Work under the program typically occurs between April and November. Mailings are sent out to property owners to inform them where paving will take place. For example, the 2020 program called for milling and filling five streets. This involves removing the top course of pavement and applying a new top course to the road.
In addition, three streets were slated to undergo pavement patching whereby work crews fill and repair localized voids and address other pavement distress in the roadway with hot mix asphalt.
Furthermore, four streets were marked for winter patching—this calls for repairs on roads suffering from winter deterioration.
The penetrating asphalt rejuvenator fog seal was applied by indus of Braintree, Massachusetts. Formerly known as Sealcoating Inc., the company has been applying various types of pavement seals and other pavement preservation treatments for about 60 years. Typically, fog seals have involved applying a light application of slow-setting asphalt emulsion diluted with water and without the addition of any aggregate. If applied in time, fog seals have been shown to renew aged asphalt surfaces by sealing small cracks and surface voids, coating surface aggregate particles, and even adjusting the quality of binder in newly applied chip seal. By doing so they can preserve the functional integrity of the pavement and delay a more costly rehabilitation treatment in the near future.
More advanced fog seals contain asphalt rejuvenators to boost the penetration of the treatment into the asphalt pavement. The rejuvenators may be petroleum or biobased products.
The treatment applied by indus to three selected Burlington streets was a fog seal using Delta Mist, a penetrating asphalt re-

Cleaning crew prepares a Burlington, Vermont residential street for Delta Mist fog seal application.
A worker unrolls a black fabric to mark the end of the application of penetrating asphalt rejuvenator seal.

juvenator. The topically applied treatment was created with organic plant-based Delta S rejuvenator technology developed by Dr. John Warner and a staff of research scientists at the Warner Babcock Institute for Green Chemistry (WBI). Delta Mist is manufactured, marketed and sold by Collaborative Aggregates LLC of Lowell, Massachusetts, as an emulsified version of Delta S that is spray-applied at ambient temperatures.
Formulated with “green” or sustainable technology, the product is designed to protect the environment while increasing pavement life by restoring oxidized asphalt and reducing loss of fines and aggregates. It also

Initially following Delta Mist application, Crescent Road displays a white surface that in less than two hours returns to normal asphalt pavement color as seal becomes transparent.
Pavement markings in front of hydrant reappear as fog seal dries. Notice curb is not stained black by Delta Mist application.

improves cohesion while retarding crack propagation of the pavement surface. According to the manufacturer, with proper pavement surface preparation and application rate, Delta Mist slows the asphalt oxidation process for up to three years or more with each application.
Burlington has invested many millions of dollars in its road system—100 percent of its 95 miles of travelled roads have asphalt pavement. There are no gravel or dirt roads. This compares favorably with Vermont overall. According to VTrans, about 45 percent of the state’s 15,800 miles of roads are paved, while 38 percent are gravel, and the remaining 17 percent consist of graded earth, unimproved or primitive, and untraveled roads.
The City is interested in protecting its sizeable investment in roads—one of the reasons it is testing the effectiveness of rejuvenating fog seal, according to Art Baker, regional manager for indus.
“They were concerned about raveling of some asphalt pavements soon after they were installed,” Baker said. “There was very little or no asphalt coating of the fine aggregate taking place. They were also interested in pavement preservation treatments that could extend the life of pavements with the added benefits of cost savings while utilizing sustainable technology.”
Baker has been working with City personnel to investigate possible preservation treatments for their pavement management program. A strong proponent of pavement preservation, he has a 25-year background in municipal infrastructure installation, maintenance and repair. With a Bachelor’s degree in civil engineering, he started out in the private sector, then switched to the public sector and served as Public Works Director in Connecticut and Massachusetts and later returned to private industry when he joined indus. As regional manager for the company, he has been counseling DPW pavement managers in cities and towns in western Massachusetts, Connecticut, Vermont and southwest New Hampshire.
Baker oversaw the recent application of Delta Mist on several residential streets in Burlington: Birch Court and Cayuga Court in northern Burlington, and Crescent Road in the southeast corner of the city.
“The pavements on those streets were three to six years old,” he said. “We were interested in the depth of penetration of the rejuvenator into the pavement. According to tests at NCAT [National Center for Asphalt Technology], the optimum depth of penetration for a rejuvenator would be about 3/8th of an inch. And we also wanted to see if the treatment would reverse the problem they were having with raveling.”
The indus crew used a Ford 750 Super Duty truck mounted with a 2,000-gallon Etnyre tanker to spray Delta Mist at ambient temperatures on the roads. They applied between 0.08 and 0.1 gallons per square yard of the penetrating rejuvenator over the streets— the application rate was varied to address the mixed existing pavement conditions in some areas. Overall, approximately 14,500 square yards of pavement received the treatment. The treated streets each opened to traffic within about one hour of application.
Baker said the streets receiving the Delta Mist treatment would be checked periodically to see the long term results of the applications. But one benefit was obvious almost immediately.
“We didn’t have to cover manholes or drain inlets before the applications. When we first sprayed the seal, it was a milky white color. When it dried it turned transparent. So at any traffic markings like crosswalks, the pavement and markings returned to their natural color, and no curbs had to be cleaned,” Baker said.