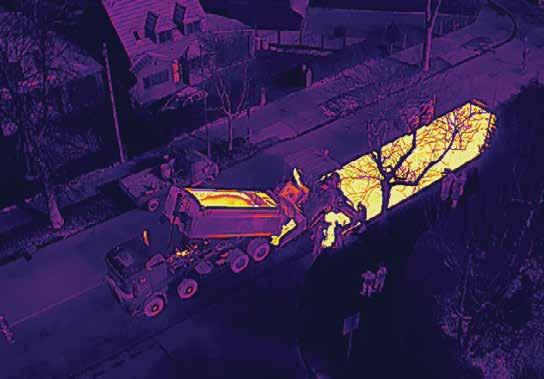
6 minute read
Harsco Mixes Steel Slag and Lignin
The SteelSurf ECO+ mix from SteelPhalt used on Broom Lane in Rotherham incorporated Lineo kraft lignin and featured warm-mix asphalt temperatures during production and placement. Photo courtesy of SteelPhalt
BY JULIAN SMITH
The asphalt industry has come a long way in its sustainability journey. In accordance with a goal set by the National Asphalt Pavement Association (NAPA) to achieve net zero carbon emissions by 2050, many players in the industry have found ways to substitute parts of the asphalt mix for best sustainable practices. Harsco Environmental’s SteelPhalt division, headquartered in South Yorkshire, United Kingdom, uses a unique aggregate to make up most of its asphalt product—steel slag. See the article titled “SteelPhalt Gives Steel Slag a Second Life” in the February 2022 issue for more information.
Because it uses steel slag, a byproduct of steelmaking, SteelPhalt asphalt products remove the requirement of mining for aggregate material. However, SteelPhalt committed to advancing further on its road to developing more sustainable asphalt products. Bitumen was the next part of the asphalt mix to tackle. A commonly used replacement for this asphalt binder is recycled asphalt, including recycled asphalt shingles (RAS).
Every year, according to the National Association of Home Builders, anywhere from 7 to 10 million tons of tear-off waste and installation scrap is generated in the United States alone. That means recycling the 19 to 36% of asphalt content found in the shingles into asphalt binder has been an attractive means to keeping shingles out of landfills. However, asphalt oxidation and the cost of cleaning and recycling tear-off shingles are legitimate concerns when using RAS as an alternative to bitumen. So, SteelPhalt looked instead to another, more natural binder to fit its environmental needs: lignin. As one of the main components of trees, lignin is a strong, sustainable alternative to a percentage of the bitumen in its mix.
Using lignin as an asphalt binder and replacement for part of a bitumen mix is not a new concept unique to SteelPhalt; however, SteelPhalt is the first company to mix lignin binder with steel slag aggregate. Stora Enso, headquartered in Helsinki, is one of the largest private forest owners and in collaboration with GautamZenUK has supplied asphalt companies with Lineo® kraft lignin to partially replace bitumen.
LIGNIN IN STEELPHALT PRODUCTS
All the components in SteelSurf ECO+ asphalt lend themselves to the environmentally friendly product in multiple ways.
SteelPhalt’s products already contain 95% recycled aggregate from the steelmaking industry. This recycled steel slag is a natural byproduct of the steelmaking process, and it would otherwise go to landfill or be used in low value materials if it were not reused in large-scale productions, like asphalt. The remaining 5% of the asphalt mix is the bitumen binder. Historically with SteelPhalt products, this bitumen has been sourced from refining of crude oil and has in turn been a significant contributor to the asphalt’s carbon footprint.
Because binder is one of the key factors determining the performance of asphalt pavement, the company had two main considerations when sourcing more eco-friendly binder replacements for SteelPhalt asphalt products: usability and durability. With that in mind, SteelPhalt chose to replace some of the bitumen with lignin to create SteelSurf ECO+, further reducing the carbon footprint of the finished product as compared to other SteelPhalt products.
Lignin is one of the main building blocks of the tree and provides the second largest source of renewable carbon on the planet. Because it is renewable and bio-based with carbon absorbing properties, it is believed lignin can be used as a responsible alternative to many fossil-based materials, including bitumen, in asphalt.
Lignin comes in powder form, so it is mixed with a small amount of rapeseed oil to condition it for use in SteelSurf ECO+ and allowed to bind the steel slag aggregate similarly to standard bitumen. While the company’s asphalt is traditionally mixed at 302-356°F (150180°C), lignin is adversely affected by heat, so it requires warm-mix asphalt (WMA) temperatures of 275-293°F (135-145°C).
The main sustainability draw of the lignin is its renewable nature and ability to absorb carbon as a main component of trees; however, an added benefit of the low temperatures of the WMA is savings in energy expenditure.
STEELSURF ECO+ IN USE
From ideation to execution, the technical and sustainability teams at SteelPhalt spent one year researching and developing SteelSurf ECO+. Rather than relying on extensive lab testing to identify the ideal formula, SteelPhalt took SteelSurf ECO+ to the roads of Rotherham, South Yorkshire, in the United Kingdom, to conduct a double-blind study on the efficacy of the steel slag and kraft lignin asphalt product.
In partnership with the Rotherham Borough Council, SteelPhalt paved a stretch of road in Broom Lane with different mixes of the asphalt. Two of the test asphalt products were SteelSurf ECO+ with varying amounts of bitumen replaced with lignin. As a control, the third asphalt tested was a standard SteelSurf mixture with steel slag and 100% bitumen. In total, just over 132 tons (120 tonnes) of 3/8-inch (10 millimeter) steel slag surface course material was supplied from SteelPhalt’s Rotherham plant to Broom Lane, Rotherham.
During this study, those testing the product without prior knowledge of which product had the lignin binder in it could not tell a difference between the asphalt with the lignin binder and the asphalt without the lignin binder. Additionally, researchers found no discernable difference in ease of compaction and workability among the asphalt products despite the different temperatures needed to heat the asphalt.
On its own, asphalt mixed with steel slag and bitumen holds up well to normal and commercial wear and tear. The strength and durability of steel slag extends its life and decreases the amount of maintenance it needs while also maintaining high skid resistance. With some of its bitumen replaced with lignin, these core properties of SteelPhalt’s products remain true.
During the blind study in Rotherham, smell was the only differentiator, as the asphalt mixture with a lignin component smelled like trees when heated.
More supply trials are planned from SteelPhalt’s Cardiff plant in the near future.
LEADING BY EXAMPLE
Armed with an eco-friendly asphalt with the same functionality of SteelPhalt’s other asphalt products, SteelPhalt is slated to expand its SteelSurf ECO+ production capabilities to new locations within the next five years. These locations include the United States and two additional locations in North America, Brazil, Turkey, Portugal, Spain and the Netherlands.
When choosing locations for pilot projects, SteelPhalt looks to areas with leaders who are willing and excited to integrate eco-friendly asphalt products into their jurisdictions. Additionally, SteelPhalt looks for areas with steel mills that have steel slag available for SteelPhalt to use to prevent unnecessary use of mined aggregates. This public-private partnership between local governments, SteelPhalt, steel mills, and now GautamZenUK and Stora Enso is vital to upgrading the world’s roadways to improve the planet’s overall carbon footprint.
Passion for sustainability pushes SteelPhalt to achieve aggressive targets for its carbon footprint through continuous innovation. SteelSurf ECO+ is one of the products SteelPhalt uses in its lineup of asphalt products that further the company’s goal of making the asphalt industry one of the most sustainable industries across the globe. This is a goal the company is not only happy to share but also excited to lead among asphalt producers.
With SteelPhalt’s reputation for sustainability, innovation and high-quality products, SteelSurf ECO+ is a welcome addition to its portfolio that will help the company continue its aggressive growth toward NAPA’s carbon goals.
THOSE TESTING THE PRODUCT WITHOUT PRIOR KNOWLEDGE OF WHICH MIX INCLUDED THE LIGNIN BINDER COULDN’T TELL A DIFFERENCE BETWEEN THE ASPHALT WITH THE LIGNIN BINDER AND THE ASPHALT WITHOUT.
Julian Smith serves as strategic growth director for SteelPhalt and is responsible for growth of existing SteelPhalt footprint and supporting its global expansion strategy. Julian joined Harsco in 2019 and has over 20 years of industry experience.
