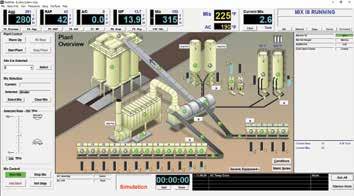
3 minute read
Automate Profit with Controls
Asphalt producers can navigate rising costs with efficient production controls, automation solutions
In Libra Drum, clarity for newer plant operators comes in the form of dynamic, color-coded graphics that provide at-a-glance status pertaining to valve changes, material flow, tank levels, temperatures, interlocks and alarm conditions that require the operator’s attention. Image courtesy of Command Alkon
BY KERRY DOUGAN
PPrice increases and supply chain issues are putting more pressure on the ability to carry out projects. Inflation has undercut funding from the Infrastructure Investment and Jobs Act (IIJA), and resources to complete work are scarce. Most companies are paying employees more to adjust to inflation, on top of offering competitive wages to attract them to the industry. Not to mention, if an operation must purchase new equipment, the cost of the equipment can be up to 30-40% higher than it was a few months ago.
The combination of climbing energy prices, rising cost pressure and the skilled labor shortage is pushing producers to implement digital tools that streamline operations and reduce costs to maintain business continuity, stay competitive and be profitable.
A COMPLETE PICTURE OF THE OPERATION
Every plant operator understands how one disruption can significantly impact the entire organization’s financial health. Libra Drum monitors motor currents and plant parameters to aid optimization of efficiencies and allow predictive maintenance before failures take down the plant. To meet the need, plant controls are a must.
Libra Drum is designed to be easy to use, helping to alleviate some of the onboarding struggles producers might encounter with new, inexperienced plant operators. Every industry is struggling to recruit new workers, and businesses across the construction industry are feeling the pressure from the shortage of human resources as well as the cost per worker. Automating operations allows asphalt plants to operate with fewer employees while still getting loads out the door.
The user can design custom software switches, create reports, and adapt to the current and future plant control requirements. A fully graphic interface monitors complex drum control operations, increases production and accuracy, and integrates with overhead loadout.
In the future, burner controls will be integrated into Libra Drum. Instead of having a separate tabletop control system sitting on the desk, the plant operator will have burner controls and dashboards available in Libra Drum on the PC and up on the screen so the plant operators can monitor everything that is going on in the plant in one place.
This allows owners and operators to calibrate the burners and make comparisons between the type of fuel being burned and the most efficient flow rate for that burner, as well as helping them to make decisions for upgrades.
NO ROOM FOR ERROR
One accident can cost asphalt producers big bucks, or worse—potentially someone’s life. For example, once the silo gates open for loadout, tons of scalding material drops in a matter of seconds. The Silo Safety System in Libra Drum can help ensure operators do not make costly or potentially life-threatening mistakes here. The Silo Safety System features infrared sensors to enable each silo, if and only if, the truck is in the proper position. As the truck pulls through to the loadout station, it will break the infrared sensor beam to enable the silo to be opened.
STREAMLINE DATA FLOWS
Automating processes ultimately gets more loads out the door and more cash flowing to a producer’s pockets. Site-automation technologies such as auto identification technology, driver kiosks, mobile loader application, traffic signals and remote driver displays can enhance asphalt operations by connecting dispatch processes with the back office, sales personnel and management staff. When data flows seamlessly across the operation, management is empowered to make better decisions and manual processes are eliminated, giving operational personnel the ability to do more with the staff available and the freedom to focus on other important tasks.
When working entirely around outdated information, producers can make mistakes that dramatically affect the profitability of a job but when working from consistent, accurate data, guesswork and poor decision-making are greatly reduced. In today’s unique economic environment, producers are realizing that sharing real-time data is crucial for success and that they must add real-time data to the management mix to improve production efficiency and productivity while also monitoring power consumption and costs.
Kerry Dougan serves as the market manager for the Bulk Materials Segment at Command Alkon.