
4 minute read
Meet Women in Construction

What led you to join the construction industry? I never thought I would find myself in construction. I found a post on Indeed for a “Women’s Pre-Apprentice Carpenter Program.” Through some research and phone calls, I became more interested. More importantly, I was gaining confidence in my abilities to commit to this program, continue into a career, and transfer into the full carpentry apprenticeship.
With my prior experience in home renovation projects, combined with my mechanical skills used to maintain my vehicles, trainer, and race ATV, I felt I should be able to learn just about anything!
Rebecca Rodriquez
Halfway through the program, I was on break, talking to a fellow ATV rider about rebuilding my race quad for the next season. I felt someone looking over at me with a sideways grin, and he said, “You’re not a carpenter, you’re a millwright!” I said, “I don’t even know what a millwright does!” Later that night, I looked up “millwright.” I was so inspired; this was right up my alley! I love to be able to recognize the problem and the cause, then move into how we can fix it and get it working properly again.
Also, I’m able to specialize in areas where smaller-frame people can excel. Being 5’4” and 130 pounds on a heavy industrial job site isn’t easy unless you can do the right job. I finished the carpenters’ program, passed the entry test, then entered it into the millwrights program.
Describe your current role and duties. I am a third-year millwright apprentice currently working with a local contractor where I’m teamed up with a journeyman. I’ve done many different types of work which makes me very well-rounded. Some jobs include unloading equipment from trucks and staging for upcoming jobs and outages, installing new equipment, repairing,and maintaining existing equipment, retrofitting and R&D projects, and precision alignment.
Did you previously hold other positions or perform other duties? I played with Lego for hours on end and was heavy into sports. I just like being constantly active. When I was 15, I was able to get my first dirt bike. My uncles and neighbors had dirt bikes. It wasn’t long until I had the bike on a bucket in the garage, cleaning it with a toothbrush.
At age 16, I was in a terrible car accident that put me in a wheelchair for four months. Two surgeries later, my broken pelvis was just as good as new, and I was able to buy a car and start learning how to change my car’s oil. I took great pride in the work I was learning — fixing up small things on the car and hanging out with grease monkey friends doing more involved work.
I still do all of my vehicle maintenance to this day, along with working on my ATV. I’m currently teaching myself how to rebuild a blown-up 450cc engine. Last year I replaced my truck’s entire front end myself on jack stands in my garage. I just learned how to do a rear axle seal and wheel bearing on my truck. I learn how to fix things as I’d rather be doing the work.
What doesn’t your educational training prepare you for?
There are many things. First, how to be a good human being. It is the easiest thing to do and still for some reason, it’s something we deal with every day. I’ve learned that everyone has bad days, but when you clock in at work, leave the home drama at the door. The same goes for the end of the day. Maybe you had a rough day, fought alignment all day, struggled to rig a piece, and caused damage — worst case being someone got hurt. It is so crucial to leave that at the job site. Go home and rest your body and your mind. Second, the ways of the field. The technique that is taught versus the technique used on site are different. The field experience is needed to really understand.
What is the best part of your job? I love when we solve unique issues, often when the existing crew doesn’t have the tooling or manpower. We lift incredible amounts of weight, with unbelievably tight clearances in some of the worst work conditions you can imagine. We throw a harness on, jump in a boom lift, and use the crane hook to move a 50,000 lb. piece. We put it on roller skates and push it in place. It is mind-blowing.
I also enjoy the guys I work with. I prove myself every day, and that’s OK because I want to be the best. I want to be called upon as someone who know what needs to be done. The guys don’t treat me differently because I’m a woman. I look forward to working with certain partners and company reps. Being a construction worker and carrying on a professional conversation at the same time is a quality I hope will take me far in the field.
Is there an aspect that you would like to see changed? Stop treating women differently. I’m sorry to the ones who think we should have special treatment, but there is no reason for it. Being able to follow OSHA requirements is easy. But the biggest thing is saying, “Hey, guys” — I promise you are not offending me.
What is the biggest challenge on the job? Getting the guys to listen to me. It’s a little frustrating, but I do understand I am an apprentice. I spend as much time as possible watching my partners and how they solve issues. I often think, “OK, what would I do here?’’ If it wasn’t a safety issue, I just stand back, watch, and wait and see what the crew ends up doing. Recently some of my ideas have been used, and they worked well. When my idea worked, I was happy. That feeling of success is what drives me to keep doing better. I keep challenging myself daily; it’s the only way to progress.
What can be done to encourage more women to join construction? I feel that trades need to be pushed in the school systems. If I knew what a millwright was in high school, I probably would have joined the program earlier. I stand very proud knowing that some of the jobs we do have helped our customers serve the public with minimal interruptions because of our training and craftsmanship. KC

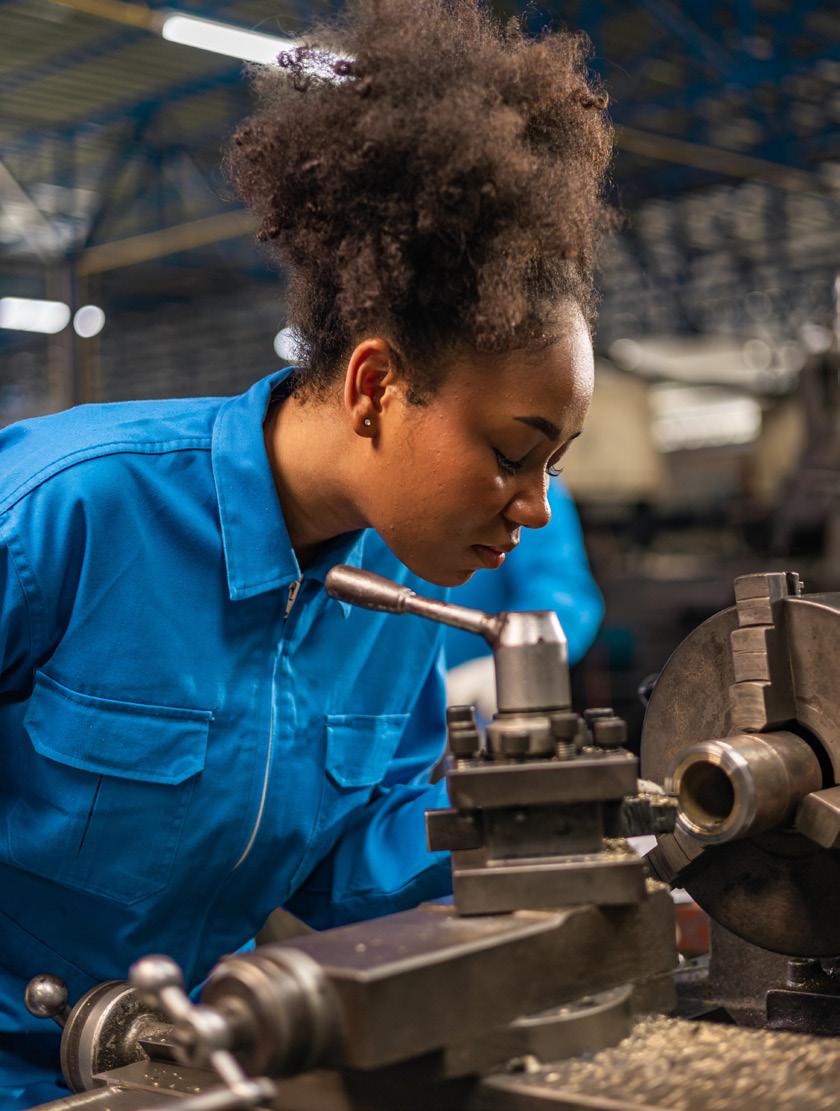