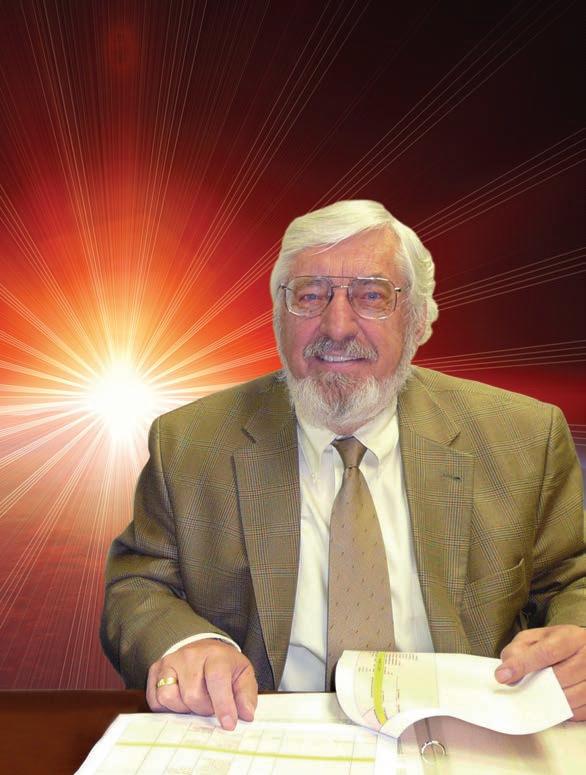
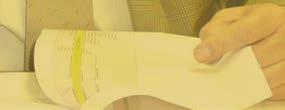
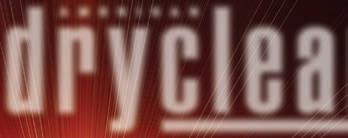

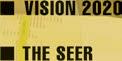
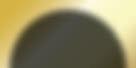
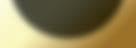

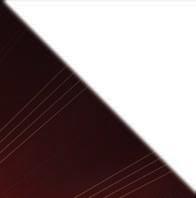

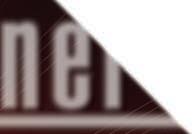






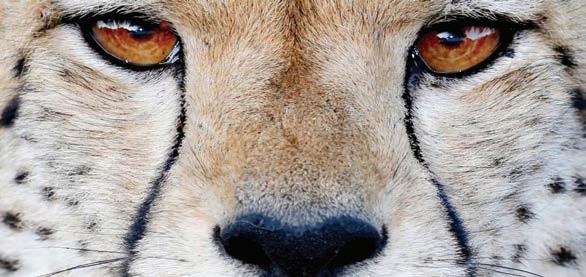
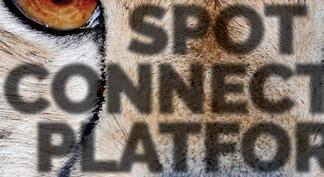




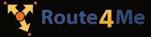








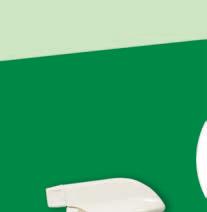
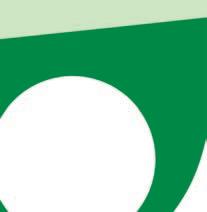

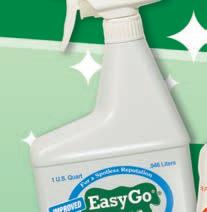
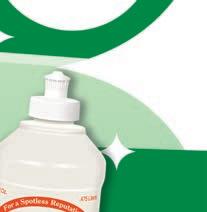
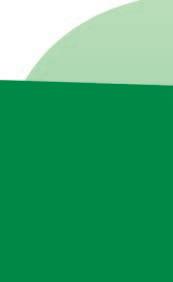
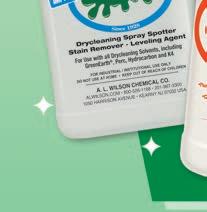
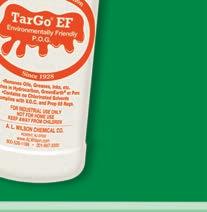
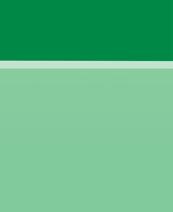

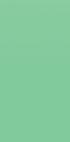
For all he gave to fabricare during his life and career, Dr. Manfred Wentz is the recipient of the first ever American Drycleaner Publisherās Impact Award! In this feature article, Looking Ever Forward, his achievements and his vision for the industry, and indeed the world, are highlighted. Listen to colleagues, friends and family talk about why he was so vital to the garment care world he loved. He meant so much to the people around him, and he asked all to look beyond, to a better world.
Tim Burke, Editor
Do you dream the dream, then put it into action? Thatās what two drycleaning owners, one in Pacific Palisades, California, and the other in Pittsburgh, Pennsylvania, will tell you they have done to start the new year. One expanded by buying out a competitor, something that is happening frequently in the market these days. The other is expanding his brand in new and different ways. Read how they turned hopes into plans, then plans into realities.
Tim Burke, Editor
Scan this QR Code for help in finding the hidden hanger on this monthās cover. Good luck!
āThe support from CBS was great. Even before we signed up, they were responsive and ļ¬exible in their approach. They have helped our team become more efļ¬cient.ā
Since 2003, CBS has given me consistent updates and easy to understand tech support, all at a price that our industry can afford. I would recommend CBS, and I have, to anyone who is still wasting their time and money on those over priced POS systems.
Welcome to a new year and a chance to make a fresh set of goalsā¦. āWait, wait wait,ā youāre thinking, āNot one of those tired old, ānew year, new challenges,ā blah-blah-blah things!ā
No, this isnāt one of those.
A drycleaning owner recently said to me: āItās not about the change of calendar, itās about our continual efforts to serve our clients now, today.ā
Think about your own drycleaning operation. How happy are your clients today? Where is your business at financially at the moment? And how are your own dreams coming along right now? Your dreams donāt follow a calendar, they follow opportunity. Itās really all about getting a win today, isnāt it?
In Vision 2020, two drycleaning owners discuss turning their dreams into realities. One in California grew by buying out a competitor, the other in Pittsburgh is expanding his brand.
Publisher
Charles Thompson
312-361-1680 cthompson@ATMags.com
Associate Publisher/ National Sales Director
Donald Feinstein 312-361-1682 dfeinstein@ATMags.com
Editorial Director
Bruce Beggs 312-361-1683 bbeggs@ATMags.com
Editor Tim Burke 312-361-1684 tburke@ATMags.com
Digital Media Director
Nathan Frerichs 312-361-1681 nfrerichs@ATMags.com
Production Manager
Roger Napiwocki
Advisory Board
ADC
Speaking of dreams ā now and future ā on the front cover is a special feature highlighting the career of scientist, educator, speaker, family man and visionary, the late Dr. Manfred Wentz, who gave so much to fabricare during his brilliant career and lifetime. Starting on page 6, Looking Ever Forward, honors his vision of āsustainability,ā with our first-ever American Drycleaner Publisherās Impact Award. Columnist Diana Vollmer asks you to update perceptions in The Seer. Martin Young explains More About Bleach. In, Protecting Public Health, Eric Wade reminds you of the Federal ban on co-located residential perc machines coming Dec. 21, 2020; thereās a new Off The Cuff; and more. Also we welcome three new editorial advisory board members: Jan Barlow, Kyle Nesbit, and Wesley Nelson, and we say a big thank you to Steven Dubinski, Herron Rowland and Ellen Tuchman Rothmann for their service. So maybe Iāve got you thinking a little bit more about The Now (about how your business and your dreams are doing ā today). Living in the now is what we all do, sure; and keeping your clients looking great, always, is what you do!
American Drycleaner (ISSN 0002-8258) is published monthly except Nov/Dec combined. Subscription prices, payment in advance: U.S., 1 year $46.00; 2 years $92.00. Foreign, 1 year $109.00; 2 years $218.00. Single copies $9.00 for U.S., $18.00 for all other countries. Published by American Trade Magazines LLC, 650 West Lake Street, Suite 320, Chicago, IL 60661. Periodicals postage paid at Chicago, IL and at additional mailing offices.
POSTMASTER, Send changes of address and form 3579 to American Drycleaner, Subscription Dept., 440 Quadrangle Drive, Suite E, Bolingbrook, IL 60440. Volume 86, number 9. Editorial, executive and advertising offices are at 650 West Lake Street, Suite 320, Chicago, IL 60661. Charles Thompson, President and Publisher. American Drycleaner is distributed selectively to: qualified dry cleaning plants and distributors in the United States. The publisher reserves the right to reject any advertising for any reason.
Ā© Copyright AMERICAN TRADE MAGAZINES LLC, 2020. Printed in U.S.A. No part of this publication may be transmitted or reproduced in any form, electronic or mechanical, without written permission from the publisher or his representative. American Drycleaner does not endorse, recommend or guarantee any article, product, service or information found within. Opinions expressed are those of the writers and do not necessarily reflect the views of American Drycleaner or its staff. While precautions have been taken to ensure the accuracy of the magazineās contents at time of publication, neither the editors, publishers nor its agents can accept responsibility for damages or injury which may arise therefrom.
American Drycleaner, January 2020
Jan Barlow Mike Bleier John-Claude Hallak Wesley Nelson Kyle Nesbit Mike Nesbit Fred Schwarzmann Beth Shader
Contributing Editors
Dan Miller Diana Vollmer Martin Young
Office Information Main: 312-361-1700
Subscriptions 630-739-0900 x100 www.american drycleaner.com
He gave fabricare a reason to believe it could be better than it was. He asked all to look beyond, to a better world. He believed in people first ā always. He brought scientists, lawmakers, companies, and drycleaning professionals together to make a healthier, safer garment care world, and to better understand their own responsibility. He sought this not only for the environment, and the fabricare industryās health, but for all future generations. For all these reasons and more, American Drycleaner hereby recognizes Dr. Manfred Wentz with its inaugural Publisherās Impact Awardāfor everything he gave to the world today.
When people think of Dr. Manfred Wentz, they think of all he gave to the future of the fabricare industry, and the world. He was a scientist, educator, speaker, and a voice of hope for the future.
That is why Wentz is being recognized with the American Drycleaner Publisherās Impact Award for all he has meant to garment care, dry cleaning, and the overall betterment of our planet.
āWhen I think of Dr. Manfred Wentz, a single word immediately comes to my mind: sustainability,ā notes Martin Young Jr., well-known drycleaning industry consultant, popular American Drycleaner Spotting Tips columnist, and owner of Young Cleaners in (continued)
White Conveyorsā OAS is the perfect solution to expand your existing business, improve customer service and increase proļ¬ts. Order Assembly couldnāt be easier.
The OAS signiļ¬cantly reduces your labor costs while greatly increasing productivity. Whatās more, order accuracy is optimized, and employee morale is improved as fatigue is virtually eliminated.
And if that were not enough, savings from reduced labor costs combined with increased productivity typically results in a return on investment in less than one year.*
The system can be delivered and operational the same day. As an option, it can be mounted on wheels for mobility or storage. It couldnāt be easier. Isnāt it time to realize remarkable time and money savings?
Easy to Use clear and easy-to-read color touch screen, plus audible instructions
Increase Productivity while Reducing Labor Costs capable of assembling over 2000 garments per shift with one operator
Fast Return on Investment typical ROI in less than 1 year*
More Capacity standard 5 slots per foot have 50-80% more hanger capacity than competitors, reducing the need to split large orders
Flexible software customization is available for specialized customerās requirements
Highly Accurate and Reliable greatly reduces the chance for human errors
Reliable, Robust and Durable Construction with average operational lifespan of 25+ years
USA Based Manufacturer for over 75 Years remote diagnostics, setting adjustments and troubleshooting assistance reduces downtime, and minimizes the need for an on-site service technician
* ROI is based on the Bureau of Labor Statistics
Concord, N.C. āDr. Wentz forced many of us to face the future, and embrace the need for change.ā
Young nominated Wentz for this award, which is being presented for the first time ever.
Wentz had many key stops along his textile career path, beginning at Bardusch Industrial Laundry in 1959-62 where he worked as a plant manager. He then went to work for Hohenstein Textile Research Institute in Germany, in 1962-65, as manager of its laundry research division. He came to the United States to work at the National Institute of Drycleaning (NID) / International Fabricare Institute (IFI), first as a research chemist in 1965-69, then as director of research in 1972-74.
Wentz was a professor at the University of Wisconsin in 1974-85, then at North Carolina State University in 198588. He worked for R.R. Street & Co. in 1988-98 as vice president of research & development and environmental affairs. He finished his great career at Hohenstein Institutes USA as director, and also served as head of the textile label and standards body OEKO-TEXĀ® Certification USA in 1999-2009. Wentz retired in 2009, and died in 2016.
Wentz was born May 6, 1939, in Germany, a son of Christof and Emilie Hermann Wentz. He married Gisela Rosch on July 13, 1962.
He graduated from the College of Textile Chemistry and Engineering in Hohenstein, Germany, in 1959. Later he earned from North Carolina State University a Ph.D. in polymer science in 1973.
Dr. Wentz, on right, shown conferring with Prof. Dr. Stefan Mecheels, third generation family owner and CEO of the Hohenstein Institute. Wentz came to work for Hohenstein, located in Germany, in 1962, as manager of its laundry research division. Upon Wentzās retirement in 2009 Mecheels had said, āThe shoes we have to fill, namely yours ā Manfred Wentz ā are big. We will make every effort to continue the work you have been pursuing.ā
Wentz came from Germany to work at the NID, which later became the Drycleaning & Laundry Institute (DLI) of today.
āI first met Dr. Wentz in the late 1990s,ā Young recalls. āI had read several of his contributions to trade publications, many times challenged by his scholarly approach to garment care.
āThe State of North Carolina had mandated a study of the predominant drycleaning solvents at the time. I was recruited to offer insight to the day-to-day operation in the newer isoparaffin petroleum/hydrocarbon plants. I had no idea that the vision of Dr. Wentz went beyond the room and into the future.ā
That vision Young speaks of was always on display throughout fabricare. A Technical Bulletin from 2000 pointed out that the IFI joined a study on setting standards for wet cleaning and petroleum dry cleaning. It noted how research would play a key role in evaluating those methods and Wentz was shown prominently in an accompanying photo.
Bill Fisher, CEO of DLI from 1995 to 2011, relates this about Wentz: āI think Manfred is best remembered and celebrated for his work while at N.C. State, essentially showing that ānotā drycleaning garments was
Dr. Wentz, on left, having fun with Bill Fisher, CEO of DLI from 1995 to 2011, during an Australian convention. Fisher started at the National Institute of Drycleaning (NID) working for Dr. Wentz in 1965. Recollections from Fisher: āI was Manfredās lab technician from 1965 to 1969, and a research engineer under him from 1972 to 1976. Manfred was an excellent teacher. He helped instill in me an ethic that I think helped me as I became director of research after him.ā (Photos courtesy of the Dr. Manfred Wentz family: wife Gisela, daughter Sabina and son Chris.)
more harmful than dry cleaning. Keep in mind that this was in an era where many consumer advocates stated that dry cleaning āwore out clothes,ā because of the deleterious effects of dirt particles abrading and damaging fibers.ā
Fisher worked for Wentz. āI was Manfredās lab technician from 1965 to 1969, and a research engineer under him from 1972 to 1976. Manfred was an excellent teacher. He helped instill in me an ethic that I think helped me as I became director of research after him.ā
Fisher recalls that Wentzās work at the NID was related to research on drycleaning chemistry.
āHe spent a lot of time on aspects of primary, secondary, and tertiary solubulization. Thatās where the solvent dissolves the detergent and the detergent will carry and dissolve small amounts of water in itself,ā he explains. āWe also worked extensively on the water-carrying abilities of commercial drycleaning detergents.ā
Fisher remembers Wentz as a warm, genuinely caring person who was devoted to his family.
āWe had a good working relationship. I admired him greatly.ā
Worldwide textile research group the Hohenstein Institute notes that Wentz held many leadership positions in textile industry organizations, such as the American Association of Textile Chemists and Colorists (AATCC), and the International Organization for Standardization
American Drycleaner,
(ISO) among others.
āAlso, he was an active member of the American Apparel & Footwear Association (AAFA) where he was integral in the development of the Restricted Substances List used industrywide today,ā it notes.
He served as a delegate and expert at ISO meetings that develops safety standards on textile and apparel performance. He collaborated with Nike, Walmart, Target and LLBean, among many other Fortune 500 companies on many levels.
Wentz was widely published, with more than 100 articles in both domestic and international trade journals, including American Drycleaner. He also gave more than 100 presentations or keynote addresses at U.S. and international trade shows, conferences or business meetings.
āHe had the credentials to meet with leaders in fabric manufacturing, garment manufacturing, and most importantly the government bureaucracy,ā says Young.
āDr. Wentz knew, long before many in the garment care industry, that our immersion solutions were going to need modification.ā
Wentz shown receiving a George M. Shepherd Award given by the International Drycleaners Congress (IDC) to strengthen international understanding and goodwill in the fabricare industry. āThe award is being presented by Bill Pulley to Dr. Manfred Wentz
May 6, 1998, at the IDC convention in Munich. It is in recognition of many years of service to the drycleaning industry and IDC,ā notes Chris Wentz.
Wet cleaning is better & faster than dry cleaning. We wet clean anything from wool suits to wedding gowns.
Poseidon offers innovative programmability for complete control over every conditional aspect of the wet cleaning, drying and ironing process. Thatās why professional fabricare operations rely on Poseidon equipment to perfectly wet clean the most delicate items including tailored wool suits, cashmere sweaters, silk wedding dresses, and so much more! CALL 800-482-3400
ā
ā
ā Gary Heļ¬in, Owner, Perfect Cleaners
Young explains that, āEach time we talked, in a group or one on one, he would touch on the subject of sustainability of our industry. Dr. Wentz wanted to do his part to ensure the future good health of the garment care industry for the foreseeable future.ā
The strong voice and vision were on display when Wentz talked about the role people played in getting things done. He was quoted as saying: āIf you treat problems holistically, you can solve them in the long run with solutions that are economically and technically feasible. But that requires a constructive approach and less self-interest.ā
Wentz wanted the industry to look ahead. He once related in an article in American Drycleaner, āIf I have one criticism of the fabricare industry, it is that it is reactive, rather than proactive.ā
Young says he came to understand that though they were pursuing the same goal, their perspectives were different.
āI quickly learned to listen closely when he spoke, his words were on point, and his baritone voice and accent commanded respect. Dr. Wentz forced many of us to embrace the need for change, and to keep looking for a more
environmentally friendly method of handling textiles.ā
David Dawson, retired president of R.R. Street & Co. Inc., reflects on Wentz: āHe served as vice president of research & development and environmental affairs at Street for about 10 years before retiring with serious health issues. However, he continued to be involved in many aspects of textile science.ā
Wentz was a true scientist, Dawson says. āHis intellectual curiosity and thirst for information was insatiable, and he immersed himself in the work of textile research and standards-setting organizations around the globe.ā
Wentzās son Chris describes his father as always curious to learn.
āThis included developing meaningful relationships with the people that shared the same interests. He knew those relationships formed the foundation for the great things he and his colleagues accomplished.ā
Gene Damaso was director of new product development at R.R. Street in 1995-2010. āManfred, be-
āFond memories include driving a U-Haul truck to move Manfred and family to North Carolina ā Chris and Sabrina in the VW, with Manfred and his wife Gisela, their cat Whiskey, and me in the U-Haul for eight hours! Whiskey was decidedly unhappy with the arrangements!
āThen thereās the time we did work for a large fabric company who needed a finish removed from a fabric, and the only way to do that was in a drycleaning machine loaded to the gills with chloroform. Unfortunately, the machine we had leaked vapors like a sieve so we had to close-off that end of the building and wear oxygen tanks!ā
ing a college professor, knew the value of R&D and let me explore totally new concepts. This proved important since the R&D we did provided new concepts for dry cleaning and in the end was profitable. Manfred was a very kind and gentle man who supported his people.ā
Chris reflects that his fatherās life was a beautiful mosaic of overcoming challenges.
āFrom being a young man in Germany that loved to read and study in a setting that made it extremely challenging to do so, to coming to America with his wife and daughter to study in a foreign land during a post-war time frame.ā
Wentz battled healthcare issues and took the challenge of
cancer with grace, never seeing himself as a victim, Chris says. He understood his condition, what needed to be done, and fought it for 19 years.
Wentz told his son he was grateful for the leaders of R.R. Street & Company, such as Ross Beard, Dawson and others. Chris related how they continued to support his fatherās healthcare efforts and issues even after he left the company.
Tim Racette, who worked for Wentz at Streetās from 1988 to 1993, notes that Wentz was a great mentor, always giving of his time and willing to entertain virtually any question, but he was steadfast in his technical rigor, even in the most seemingly casual conversation.
āHe was quick to pose technical questions and challenges that, more often than not, required digging deep to find the answers. In the process, I developed a more thorough understanding of the subject matter and became a more critical thinker,ā Racette says.
Today, Racette is the chief technology officer at Green Arrows Laboratories LLC, a specialty chemical manufacturer of environmentally friendly solutions.
What did Wentz meant to the fabricare industry?
āDr. Wentz was a significant contributor to the drycleaning industry in multiple capacities,ā he says. āHis ability to distill complex processes and principles down to easy to understand terms, and his enthusiasm and willingness to share his knowledge, made him a particularly effective educator and highly-sought-after public speaker.ā
Wentz was a strong industry advocate in regulatory matters, working collaboratively with the U.S. Environmental Protection Agency, the textile cleaning industry, and the textile manufacturing industry, on a range of issues, according to Racette.
The Venice Wetcleaning System by Imesa gives you complete control over the washing and drying cycles providing superior results.
While others choose to take an antagonistic approach to addressing regulatory matters, Dr. Wentz was always a proponent of addressing issues objectively with a focus on facts instead of emotion, he points out.
āThis approach earned him the respect and ear of the EPA and industry officials. It also enabled him to build important bridges across seemingly wide divides that led to more constructive dialogue amongst all parties.ā
As a scientist, Wentz contributed to a better understanding of textile cleaning processes and their effects on textiles. He was active in industry trade groups that addressed
a range of important issues, not the least of which included care labeling standards, and garment and textile testing standards, Racette says. āMuch of his work had immediate practical benefits for those working in the textile care industry.ā
Wentz served for more than 25 years as the U.S. delegate and expert to the International Standards Organization that develops international consensus standards on textile and apparel performance, according to a biogra- (continued)
Left: Dr. Wentz and one of his graduate students, Lynne Olson, look at results of their new infrared spectrophotometer. Wentz also used this tool to get results on pre-Colombian textiles like the Tianako tapestry, the family notes.
phy written by Hohenstein.
The Institute notes that Wentz was an active stakeholder in the U.S. EPAās Design for the Environment, Garment and Textile Care program, among others.
At Wentzās retirement from Hohenstein in 2009, Prof. Dr. Stefan Mecheels, third-generation owner and CEO of the Institute related: āWe pay homage to what you, Manfred Wentz, have done for the textile industry in such an outstanding way. During all the years, youāve always been there rendering many different services and setting decisive initiatives for the market. For that, I would like to personally express my gratitude. You have earned our unstinting respect for your lifeās achievements.ā
Prof. Josef Kurz, associate director of the Hohenstein Institute who has worked there 62 years says: āManfred Wentz was a strong supporter of environmental protection in the drycleaning industry and made a significant contribution to the implementation of higher standards in the handling of organic solvents, which contributed to a significant reduction in emissions. These successes have also been acknowledged throughout the world.ā
In the early 1990s when there was concern about the drycleaning industryās role in pollution contamination issues cited by the EPA, Wentz was called upon to be a steadying voice of reason, one who could talk from experience to all sides.
In those days, Wentz also helped create, along with other
industry leaders, a grassroots group called the Fabricare Legislation and Regulatory Education Association, or FLARE, to bridge the gap between drycleaning owners and politicians over environmental concerns.
From even earlier days, Wentz was quoted in a U.S. Department of Labor bulletin about job safety called OSHA and Small Business. He was quoted about solvent hazards in drycleaning plants saying a āmore serious hazard involves something weāre just now in the process of learning more about ā cleaning solvent vapors.ā
He went on to say that perc vapors can get in the air, giving off what he described as a āfaintly sweet ether-like smell at 50 parts per million of air.
āIāve personally been overcome twice,ā Wentz was quoted in that same 1974 article. āYou feel as if you are enormously drunk and canāt stand up straight and donāt really care too much about it either!ā
Group photo of FLARE, the Fabricare Legislation and Regulatory Education Association. From top: Ross Beard, Bill Fisher, Chris Edwards, Bill Seitz, Dr. Manfred Wentz, Steve Fazit, Frank Kean, Brooksher Banks, Ken Adamson, Ellen Gorny, and Insoo Hwang. FLARE was a volunteer organization created in the early 1990s to develop mutual understanding between drycleaning owners and politicians during the beginnings of SuperFund cleanup of the environment in the U.S.
Wentz left an enormous legacy. He had a great scientific mind and a gentle way connecting with people, reaching out to others to share his curiosity of the world.
He also gave fabricare a lifetime of achievement in creating awareness to raise up textile standards and certification systems, while always looking to help make our world a better place.
On Sunday, June 12, 2016, while residing at Rex Healthcare in Raleigh, N.C., Wentz died.
Young provides some lasting thoughts about this inaugural Publisherās Impact Award recipient: āMy fondest memory is a time when we finished a group lunch at a restaurant, after a morning meeting.
āI had asked for his insight to solving an industrywide problem. The stripes were coming out of laundered shirts. He stayed behind at the table, after everyone else had left the restaurant. We talked about time, temperature, and pH. He cared enough to give me the benefit of his
knowledge and experience.ā
The problem turned out to be the strength of the sour being used in the laundry. The sour, otherwise known as the acid neutralizer, reacted with the wear points in the shirt, and the colored threads were being loosened and flushed away. āBut to listen as he broke down the possibility of āthermal crackingā was something special for me,ā Young says.
Wentz cared enough to share the wealth of his knowledge and insight to a single cleaner, as well as government and business leaders around the world, Young says. āHe was focused on the health of garment care for the future.ā
It can be said that, in his lifeās work, he truly cared deeply about the people he met, the fabricare industry, and about the health of our world. Thatās why Dr. Manfred Wentz is our first-ever recipient of the 2020 American Drycleaner Publisherās Impact Award. ADC
Besides his work in garment care, Dr. Manfred Wentz was ļ¬rst a dedicated husband, father, and grandfather, as his son Chris, daughter Sabina, and wife Gisela reļ¬ect.
Speaking by phone recently with American Drycleaner, Chris and Sabina shared thoughts about their dad and his home life and his work relationships.
āHis life, business and personal decisions were shaped by his devotion to the family and how it would enhance our lives,ā says Chris.
His son relates that their father was never one to shy away from doing what was right both in his personal life and his business life. Relative to the businesses of dry cleaning, garments and textiles, he understood the major impact these services and industries had on the environment and, more notably, how they affected people. āAnd we know thatās pretty much everyone. He knew that. It was a guiding tenet to the way he approached his work,ā relates Chris.
āTraveling with him was always fun and interesting,ā Chris continues, relating how the family could always count on their dad telling them that he āgave a talk there,ā when they went by a famous hotel, university, or institute. āIt became a game to ļ¬nd a place in which he didnāt give a talk.ā
Sabina provides these closing words about their dad: āMy dad was Chrisā soccer coach and had a big impact on all of the players on his teams through the years. They were consistently one of the top teams in Wisconsin and won a state championship as well.
āAlso, he orchestrated trips for all of us when we lived scattered across the country. Dad was all about family.ā
Surely the legacy of Dr. Wentz, devoted family man and famous fabricare scientist, is that he reminded us all, always, to keep looking ever forward to a better and brighter new day! ADC
āHands
SMRT POS was built from the ground up by dry cleaners, for dry cleaners. Itās everything you need to get the job done ā cheap, quick and easy.
Turbocharge your revenue with delivery & lockers. Automatic reminders, change alerts and integrated payments make mobile business a snap.
Your customers prefer communicating by text. Automated messaging and easy-to-use templates will radically improve your productivity.
SMRT records whoās doing what, where and when with every item, order and customer. Employee theft is a thing of the past.
With SMRTās built-in message center and issue tracker, youāll never miss an opportunity to delight your customers with excellent service.
SMRT looks and acts like your phone, so itās easy to teach and easy to learn. We do all the set-up for you, so you can start rocking it on day one.
New Year, New Store! Tommy Goulla is the owner of Ogdenās Cleaners in Pacific Palisades, Calif., and now owns a new store The Cleaning Baron, in Marina Del Rey, Calif.
āGetting a new store had been a plan of mine for some time,ā Goulla says.
āI was just waiting for the right timing and to find the perfect location.ā (Photo
Meet Tommy Goulla, owner of Ogdenās Cleaners in Pacific Palisades, Calif., and now The Cleaning Baron in Marina Del Rey, Calif.
Q. āWeāre in a new year and a new decade, whatās new for your drycleaning operation?ā
A. āI have just acquired a new dry cleaners in Marina Del Rey called The Cleaning Baron which em-
phasizes high-end drycleaning, laundry and tailoring services, open seven days a week,ā Goulla says.
āThe acquisition took about six months to complete. I am very excited to bring to Marina Del Rey what I have been providing in Pacific Palisades,ā relates Goulla.
āThereās been lots of changes in the last decade in our industry. Some areas have
Two owners reveal their dreams, hopes, and realities for this year.
seen a significant drop in sales due to the fact that more and more clothing manufacturers are making washable garments,ā he notes. āFortunately,ā he continues, āWe are located in a high-end area and this has not affected us as much.
āAnother big change is the cost of labor here in Los Angeles and finding good employees,ā Goulla says. āI have put more focus on quality control and customer service so I can better justify my increases in pricing.ā
Q. āHow long have you been planning to expand?ā
A. āGetting a new store had been a plan of mine for some time,ā he explains. āI was just waiting for the right timing and to find the perfect location. The Cleaning Baron was a perfect candidate due to its location and size, as Marina Del Rey is growing at a very fast pace.ā
Q. āOne way to measure the health of a business is growth of a brand; how healthy will your brand be in Year 2020?ā
A. āOur brand, I can say, has been growing in
healthy levels because I have put lots of emphasis on customer service and quality.
āIn my opinion the dry cleaners who sell themselves on price-only will eventually fail as our industry needs more than just price as a selling point. I also believe that to be healthy you must take steps to be environmentally friendly,ā Goulla points out.
Q. āCan you share a tip with other owners about how to make time to dream, plan, and launch that vital growth in the Year 2020?ā
A. āMy advice to other owners is find out who their clientele is and what they want and build based upon that,ā he suggests, and adds: āEvery store has been built on a different foundation and in my opinion finding out what your customers want and trying your best to providing that is key to every store.ā
Goulla shares this final thought: āThe best ideas pop up in my head when I am driving. Later I try to make notes to see what that idea can do for me. Believe it or not lots of amazing ideas were made into reality that way!ā
Meet Joe Ferrante, owner, Duro Cleaners in Pittsburgh, Pa.
Q. āWeāre in a new year and a new decade, whatās new at your dry cleaners?ā
A. āA new year, indeed! Wow, I never really thought of it as a new decade prior to reading this question. Thatās some ātake a deep breath,ā kind of news,ā Ferrante says.
āWe are looking to expand Duroās home delivery division. We do currently operate several routes in the Pittsburgh area however weāre ready to take it to the next level.ā
Q. āAre any of your new plans already implemented or are you somewhere along in the process?ā
A. āWe are always in the process! Last year we purchased a new point of sale system which has been huge. It provides us with ā20/20 visionā of how and what the business is doing daily,ā relates Ferrante.
āWith any new point of sale, there is a learning curve and we feel that we are finally over the hump and are able and ready to fully optimize all it has to offer. With its real time reporting, integrated messaging system, and route management software, we feel that it is the one tool that will allow us to stand out from others in the business,ā he notes.
āLast year we also purchased a new delivery van that will allow us to build upon our image. We didnāt want to come to the market with a cracker jack approach and throw just any vehicle on the road.
āIt was important for us to establish that we are serious about the line of work we are in and let that reflect from the vehicle that we put on the road all the way down to the uniform our drivers will wear.ā
Q. āDid any of these Year 2020 plans start out as dreams on your wish list?ā
A. āThe whole thing started out as a dream,ā Ferrante relates. āI always knew that I would own my own business but after working years in my familyās cleaners I realized I only had a 10-year āPh.D.ā in one thing, and that was dry cleaning!
āWth the support of my family, I was able to purchase my own cleaners and start implementing all the things that I personally thought would help move the needle,ā he adds.
Q. āOne way to measure the health of a business is growth of a brand; how healthy will your brand be in year 2020?ā
A. āOnce you get past the fact that your dry cleaners is no longer just that, you start to realize that in this day and age, you need to establish a brand,ā Ferrante says.
He indicates that, āIf you look at what some of the bigger players in our industry are doing, they focus maybe 75% on their brand and 25% on their production.
āBeing a smaller drycleaning operator, itās easy to lose focus on this; however, after spending some time at the Clean Show and listening to Jason Loeb, I then understood that its not the size of the operation, rather itās the size of the brand.ā
Q. Youāve mentioned that your business has had to overcome things from the past, what things?
A. āFor example,ā he points out, āWe struggled with negative reviews left over from previous ownership
and lack of an online presence.ā But he says that with, āJust some old school customer service, we were able to generate good reviews organically over time.ā
Right now he relates that his business is currently ātrending upward.ā
However, Ferrante says, when it comes to brand, āThere is never a time to relax and think that weāve done enough. We will always be working toward establishing a brand. This year will give us a fresh start on getting our message out there: Personal, Professional Service.ā
Q. āCan you share a tip with other owners about how to make time to dream, plan, and launch that vital growth in the Year 2020?ā
A. āFirst, Iād say, take some time to reflect on why you wanted to enter this business in the first place,ā Ferrante relates. āA lot of us got into it because we had family ties or tons of experience.
āDrycleaning owners are not the type of people that take the easy way out of anything. If we did, we wouldnāt be in this industry.
āSo when you think back five or ten years, you may think of something that you wanted to do and didnāt. This year is a fresh start. A fresh decade. Take that thought and capitalize on it,ā he says.
āSecondly,ā Ferrante notes, āBuild your team and trust them. It is so hard to give the keys away to your business but if you really want to accomplish anything, you must surround yourself with a team that you can trust not only with your operation, but also with your brand.ā
Q. āAnything else youād like to add about your vision and growth for 2020?ā
A. āLike any year, 2020 is a fresh start to build upon history. Itās a leap year, Olympic year, and an election year. We will see the completion of the new world trade center,ā he says. āThe world will keep building and so should your business!ā
Ferrante concludes with this: āIn our business, we will answer every phone call; respond to every text and email; and greet every customer with a smile. With this core of established values, it will allow us to move our business forward with whatever we decide in 2020, and 2021, and beyond!
So you heard from two drycleaning owners expanding this year. Take your own ideas, hopes, and dreams and make them into realities. Follow your vision. Itās really the year of you! ADC
This year is momentous, in part due to the end of one decade and the beginning of a new one.
Preparing for this significant new era can give you a handle on the near future and make your company a leader that overcomes the ever-increasing challenges that face business in general and the fabricare industry specifically.
As we know from Monday Morning Quarterback discussions over coffee, hindsight is much clearer than foresight. So, letās do what the Las Vegas bookies do to set their odds in the betting world: Do the homework!
Gather all available information and synthesize current and historical data in conjunction with future indicators to gain the best insight and knowledge possible.
Examine the relevant issues from all available angles to reveal the most significant factors that will impact your business and the appropriate related strategies and
tactics to apply through your management.
Then prepare a formalized winning strategy to apply to this year and beyond. What past, present and predicted trends influence the way you do business today and how your model must change in the future to keep your organization moving forward at the head of the pack?
Consider past and current projections and trends in: 1. The Economy; 2. Retail Consumer Sector; 3. Commercial Sector; 4. Fabricare Trends; 5. Your Status.
Caution: Relying on the past alone is unwise and can be dangerous. The same is true for future predictions. Even agreement by experts is not a sure bet. Note the example of recent Federal Funds rate predictions and actual numbers: Despite the 2018 consensus of economists predicting interest rate hikes through 2019, the actual comparison of Sept. 2018 to July 2019 was flat at 2.25%.
(https://www.thebalance.com/when-will-the-fed-raiserates-3306131)
Justification for more research and information gathering on various trends from several sources is that no single source of information is sufficient to rely on, and your business is affected by many influences.
Some of those components are reliably predictable but most are not. The more you can factor into your preparation, the closer to 20/20 your vision can be.
The economy is multi-faceted and differs dramatically by geographic location from the micro-market around your specific locations (that hopefully have a population inclined to use your services) to the global economy that affects general consumer spending and your pricing on equipment and supplies.
Local town, county, state and national economic factors also vary dramatically and affect your achievable results.
Examples that are beyond your control, but need to be factored into your plans are: Changing neighborhoods, unemployment rates, quality of education, relocating cor porations, displacement of employees, housing afford ability, access to capital, commercial and retail rents, population density, traffic patterns and interruptions.
Changing lifestyles and shopping habits of consumers can work in your favor or against your business.
A very positive influence is consumersā desire for more time to do non fabricare-related activities, whether work, play, socialize or just getting some much-needed sleep.
The more you do for time-starved customers and prospects, the more your sales and profit will grow. Remind them of all the services you provide so they donāt just slot you into the āwardrobe cleaningā role.
The declutter trend lead by Marie Condo is a contributing factor to owning fewer things in general and
particularly clothing and accessories. The disappearance of shoppers from stores is at least in part due to this influential trend.
There may be a small positive upside to the resulting organization of the remaining wardrobe in that it becomes more apparent when wardrobe items need care.
The anti-Amazon attack from traditional retailers may provide more opportunities for your business as consumer-attracting events are scheduled to repopulate empty shopping malls. Brainstorm what you can contribute to the activities to interact with customers and prospects.
Retail rents are also being impacted by the online purchase, wardrobe rentals, and curated shopping trends, such as StichFix. com, TrunkClub.com and their proliferating competition.
These companies and their curators can be huge customers for you if you can provide the service they need within the schedule and locations required.
Use the retail store vacancies in your market to negotiate the best rents possible in the locations where you want to have physical stores and/or plants. Donāt wait for your lease expiration to renegotiate.
Rent The Runway, which operates three of the largest drycleaning plants in the world, proclaims that: āThe renting revolution is here.ā It says it provides: āFashion freedom; total wardrobe flexibility; smarter closet; and a smaller clothing footprint.
āClothes end up in the back of closets or landfills. Power the sharing economy and rent instead.ā
They are a force in both the sustainability movement and the sharing economy trend.
Thredup, a thriving consignment resale company, is also leading the sustainability trend and joining with a range of partners from Amazon to Macyās and JC Penney where physical Thredup pop-up stores are being installed.
Success is a direct result of providing what customers want....
....And providing it when, where and how they want it.
(https://www.bizjournals.com/sanfrancisco/ news/2019/08/22/thredup-with-macys-penney-secondhand-retailers.html)
Would you have predicted that Macyās would support selling used clothing? Leap on this trend to do the cleaning for resale consignment customers and shops both online and in store.
The service economy is strong, growing and competitive. According to vault.com: āThe fastest growing industries in the United States are:
#1 Energy #2 Pharmaceuticals and Biotechnology #3 Engineering #4 Information Technology #5 Investment Management #6 Private Equity #7 Consulting #8 Social Media #9 Hedge Funds
#10 Media and Entertainment #11 Commercial Banking #12 Advertising #13 Accounting #14 Hospitality #15 Wealth Management #16 Insurance #17 Real Estate #18 Public Relations #19 Nonprofit Sector #20 Investment Banking.ā (https://www.vault.com/industry-rankings/fastest-growing-industries)
Obvious opportunities exist to do business with com panies that provide healthcare, hospitality, delivery, facility cleaning, location security, building and grounds maintenance.
As commerce moves online, warehouse and industrial parks are fertile ground for route activity. Explore the ways that you can tap into these service providers as customers for your business.
Example: Hotel occupancy rates are up and many of them need refurbishment after a long stretch of minimizing expenses and delaying much needed maintenance and cleaning projects.
Drapes, rugs, furniture, lampshades, accent pillows
American Drycleaner, January 2020
and seat cushions all need refreshing in addition to the ongoing daily linens, uniforms and guest and manager garment cleaning.
Half of the āfastest growingā list are financial services related, a very active sector, and the managers and their teams must still dress to impress, even if the preferred attire has moved to casual.
Looking professional is even more challenging in casual clothing, so they need your services as much or more than ever.
The industry has had much press exposure about the shrinking number of companies reported in the drycleaning and laundry business.
A closer look shows very healthy growth among the competitors that are taking an innovative and proactive approach to expanding their businesses.
Many have acquired profitable volume by buying businesses from owners who want to get out of the business and who are tired of the required management involvement.
Consolidating two or more compatible businesses can result in much higher profit percentages due to the efficiencies and economies of scale gained with the added volume and reduced supporting expenses.
Other successes are represented by diversification of services provided and/or expansion of current services to more prospects through proactive sales and marketing.
Examples include: Electronic and toy cleaning; family laundry; accessory cleaning; expanded household cleaning; recreational vehicle, airplane and boat cleaning.
The key to this strategy is savvy sales and marketing to let them know what you can do for them.
Leapfrog common industry technological approaches to communicate with customers by implementing new ways to interact. One effective component is a creative, informative, and possibly humorous blog.
Two examples:
First, McDonaldās did both promotion and damage control for a sauce shortage and hit iTunes top-100 podcast chart. Go to this link: https://io9.gizmodo.com/ mcdonalds-is-bringing-back-rick-and-mortys-belovedszec-1797372297.
Next, Keeping You Organized produced by Smead, a file-folder maker, is one of the longest running brandpodcasts since 2013, as a series of weekly interviews
with a professional organizer focused on specific projects. It informs consumers and sells their products at the same time. Go to this link: https://podcasts.apple.com/ us/podcast/keeping-you-organized/id698985975.
(David Yaffe-Bellany, SFChronicle.com, 8/26/19)
If you think professional photography is out of your price range for your electronic and print media, check https://unsplash.com/ for free, high-quality, high-resolution, royalty-free images that have been gifted to the site by their creators.
Success is a direct result of providing what customers want. And providing it when, where and how they want it. Make their lives easier to make your company more profitable.
Take a clear-eyed, objective look at your company from top to bottom both past and present. Assess your current status in your market, the strengths that differentiate you from competitors, and the opportunities for growth.
Look at the outside factors that are threats to your organization, such as: Availability and increased costs of quality employees; and changing or new regulations. Evaluate the areas for improvement that can propel
you to greater success. Document what is working and the areas that are not, and what to do to improve both.
Take a scientific approach to profiling your best customers and adding more prospects like them.
Disrupt how consumers and businesses think about your business. Move them from default thinking of you as their cleaner for their ābest clothes,ā to an expanded role as their wardrobe, household, business, vehicle and recreation care and maintenance providers.
Help them change their current habits of usage to new patterns of behavior that make you a trusted provider of more and more services and support for them, their families, their friends, and their associates.
Being complacent about new trends and cultural changes has resulted in many operators closing their doors. Donāt be discouraged by the bad news, but rather use your vision and creativity this year to be a winning survivor instead! ADC
Diana Vollmer is a managing director for Methods for Management, which has served dry cleaners and launderers with affordable management expertise and improved profitability since 1953. For assistance ana lyzing your market status, the trends that affect your future, and planning for a prosperous 2020, contact her at dvollmer@mfmi.com or call 415-577-6544.
Perc is a big issue in our drycleaning world. Anything related to perc gets our attention.
Coming later this year in December, the Fed will ban co-located residential perc machines. Does your business use a perc machine in a location shared with a residence? If so, are you taking steps to make the needed adjustments? Iāve invited Eric Wade, retired chief of the enforcement section of the New York State Department of Environmental Conservation, to a Q&A session all about this topic, where we can hear his views, expressed as a private citizen, about this coming regulation that concerns public health protection and our fabricare industry.
Letās join the chatā¦. Welcome Eric, letās get started:
Tim: āFirst, tell our readers about your former employer and yourself.ā
Eric: āI worked for the New York State Department of Environmental Conservation for 41 years in the division of air resources. I retired recently as the chief of the enforcement section. As such, I no longer represent the Department and my views are being expressed as a private citizen. Prior to my retirement, I was responsible for revising and updating the drycleaning regulation in addition to my other duties.ā
Tim: āA Federal Regulation stating there can be no more co-located residential perc machines goes into effect on December 21, 2020. How will this affect drycleaning owners across the country?ā
Eric: āNationwide, the operation of any perc drycleaning machine at a co-located residential facility will be prohibited after December 21, 2020. A co-located residential facility is a drycleaning facility that is located in a building with a residence. Any dwelling or housing in which people reside, excluding short-term housing that is occupied by the same person for a period of less than 180 days, such as a hotel room, is considered a residence.
āWhen the Federal ban was proposed in 2005 and adopted in 2006, it was anticipated that most perc colocated residential drycleaning facilities would switch to an alternative solvent during the 15 year transition period leading up to the 2020 prohibition date. After this date, all affected co-located residential perc drycleaning facilities must switch to an alternative solvent, shut-down, or become a drop shop collecting articles for dry cleaning at another site.ā
Tim: āAre drycleaning owners across the country aware of this coming change, and for owners in co-located residential locations, are they taking steps to be in compliance?ā
Tell us where you were born, grew up, and reside today?
āI was born and raised in Brighton, on the south coast of England. My co-founder David and I grew up together there, and it was a great place for us to be kids. Then I moved to London, where I have been for almost my entire adult life.ā
Hobbies (that youāll admit to)?
āWhenever I get a chance I like to read the latest business books. I prefer a crazy story to a bland leadership manual. Lately Iāve been reading Billion Dollar Whale: The Man Who Fooled Wall Street, Hollywood, and the World. Iām a big sports fan too. Iām a lifelong Tottenham
fan and there has never been a more exciting time to say that! I try to get to a game once a month
What gets you excited at work?
āComing up with new features for our system, rolling them out, and seeing how it impacts our customers. Getting positive feedback from our 5,000 users, which changes their stores and how they do business, is a thrill that I will never get tired of.ā
Lastly, tell us a secret (keep it clean) nobody knows about you?
āUntil CleanCloud I never thought I would be able to stay focused on one business for more than a couple of years at a time. I was too impatient to get going on the next idea! But with this business going from strength to strength, for the first time in my life, I donāt feel like Iām standing still.ā
(Do you want to take part in an Off the Cuff, or know someone who does? Email tburke@atmags.com.)
ADC
Eric: āAll co-located residential perc drycleaning facility owners should be aware of the 2020 pro hibition date that was discussed in EPAās 2005, 2006 and 2008 rulemaking documents. Individual states have also provided outreach to affected facilities as most have been delegated the authority to enforce the provisions of the Federal rule.ā
Tim: āNew York City has the most co-located residential perc machines, how does this coming change in perc regulation affect drycleaning owners there?ā
Eric: āLike all other areas of the country, all co-located residential perc drycleaning facilities in New York City must stop using perc after December 21, 2020. While the 15 year phased-in transitional period has worked well for most parts of the country, it has not worked as well for the New York City area where most of the perc drycleaning facilities are located in co-located residential buildings.
Eric Wade is retired chief of the enforcement section of the New York State Department of Environmental Conservation, where he worked for 41 years in the Division of Air Resources. āAs such, I no longer represent the Department and my views are being expressed as a private citizen,ā he notes. āPrior to my retirement, I was responsible for revising and updating the drycleaning regulation in addition to my other duties.ā
automatic sprinkler systems where alternative solvent machines are equipped with integrated fire extinguishing systems and/or safety features that minimize the fire/ explosion risk.
āAlternative solvent dry cleaners in New York City are also affected by the local zoning code require ments for most commercial districts which limit facility size to 2,000 square feet of floor area and the total aggregate machine capac ity to 60 pounds. Both of these requirements indirectly effect the transition to alternative solvents by limiting future expansion and allowing only one drycleaning machine per facility.ā
Tim: āIs December 21, 2020, a firm date, or is there a possibility of it being changed, and when do you think that might be announced?ā
āThe transition to an alternative solvent has been slowed or blocked by the local fire and zoning code requirements. Because of these local fire and zoning code requirements I expect many affected perc drycleaning facilities will shut-down or become drop shops.ā
Tim: āCan you explain New York Cityās unique situation and how its more restrictive fire codes play a part?ā
Eric: āIn New York State, 92 percent of all co-located residential perc drycleaning facilities are located in New York City where the local fire code requires the installation of costly automatic sprinkler systems for facilities that switch to an approved class III alternative solvent.
āThese sprinkler systems can be very costly and most of these facilities typically have a five-year lease with a five-year option to renew. This required building improvement, payable by the tenant, is not typically seen as a sound long-term investment, especially when compared to the much cheaper option of open ing a new shop where the corresponding regulations are less stringent.
āOutside of New York City and under the New York State fire code, dry cleaners are not required to install
Eric: āIt is my belief that the 2020 ban date will not be changed because it was first proposed and adopted following an in depth study almost 15 years ago in EPAās 2005 and 2006 revisions to the National Perchloroethylene Air Emission Standards for Dry Cleaning Facilities, 40 CFR Part 63, Subpart M. This view is shared by the National Cleaners Association and the Halogenated Solvents Industry Alliance.ā
Tim: āCan you share a tip with drycleaning owners about how to find out more information about this coming regulation?ā
Eric: āInformation and a summary of the new regulatory requirements of New York Stateās recently revised and adopted drycleaning regulation (6 NYCRR Part 232) can be found on the departmentās webpage at: https://www. dec.ny.gov/chemical/8567.html/.ā
Tim: āAnything else youād like to add about this new national law on co-located residential perc machines coming December 21, 2020?ā
Eric: āI support the 2020 Federal ban as I believe it is needed for public health protection.ā
Thanks Eric for being with us today and explaining the topic of the coming Dec. 21, 2020, Federal Regulation banning co-located residential perc machines. ADC
The Mods are coming!ā
Echoes of this phrase might be bouncing around in your brain, calling to you from days past. Or from classic television show reruns. Can you envi sion those 1960s Mod hipsters?
Wait a second. Thereās another āModā weāre concerned with here. Itās called Modacrylic.
Modacrylic is described as a fiber often used in fake furs, fleece robes, blankets, stuffed toys, and wigs. It is resilient, soft, and warm, and it resists mildew, sunlight damage, and wrin kling.
A modacrylic is a synthetic copoly mer, says Wikipedia. āModacrylics can be easily dyed, show good press and shape retention, and are quick to dry.ā
In American Drycleanerās Spotting Guide, author Norman Oehlke says it is a group of synthetic fibers used in making many imitation furs. āHeatsensitive, it must be given a short, low-temperature drying cycle, under 120 F. Usually no steam finishing or light buck steam only can be applied; dry thoroughly before touching or moving.ā
About Mods, Wikipedia notes: āMods and rockers were two conflict ing British youth subcultures of the early/mid 1960s to early 1970s.ā It
also notes that the mod subculture was centered on fashion and music, and many Mods rode scooters and wore suits.
Some Mods may very well have worn fake furs made of synthetic copolymers. But thatās guessing.
Whether they also wore fleece robes is supposition too, but it was probably hard to drive a scooter with a robe flying up over oneās face. And how cool can you look, after all, ridinā the slab in a bathrobe? I mean really, Mods, really! ADC
The word BLEACH scares most cleaners. It shouldnāt. Find joy in its uses. Your bleaches are just another chemical tool to impress your clientele or get yourself out of a jam (claim).
Reducing bleaches, also called ādye strippers,ā can give you spectacular results. Any bleach should be a last resort. Reducing bleaches have the potential to offer a greater impact than oxidizing bleaches.
There is a time and place for this more aggressive tool. When you are faced with fugitive dye and all other methods fail, there is no better choice than one of these chemical tools.
Sodium Bisulfite is the mildest choice of all the reducing bleaches. It is used on a regular basis in laundry operations to neutralize chlorine bleach. It is the anti-chlor . This is important to you as a cleaner.
If the customer has been doing whites at home using chlorine bleach, double-layered areas may look dull and off-white due to retaining chlorine after the rinse cycle. A quick soak in bisulfite dissolved in water that is body temperature will neutralize the chlorine and restore the whiteness. You are a hero and validate your professionalism.
To use bisulfite at the spotting board dissolve a teaspoon of the white powder into a few ounces of water at around body temperature. It will need to be āmade-upā each time you use it.
On larger areas you can apply directly from a spare spotting bottle, while smaller areas my be addressed by using a cotton swab dipped in the bisulfite solution or even a wooden toothpick for pinpoint accuracy.
To use bisulfite in a soak, dissolve a tablespoon of the white powder for each gallon of warm water (95 F to 120 F). You can make it more aggressive by adding just a little acetic acid, no more than ¼ ounce.
There is only minimal additional risk to reducing the
water temperature and leaving out the acetic acid, to deal with any fiber and pastel colors. But test first. Bisulfite is my go-to chemical tool for stubborn berry stains, most medicines and wine.
Sodium Hydrosulfite is the more aggressive ācousinā of bisulfite. I often think of it as grabbing a bigger hammer. It has many of the same characteristics, but, with a more aggressive result.
Use the same formula at the spotting board of a teaspoon to four ounces of water, with the water being no warmer than body temperature. When testing on an inside seam, you should add a drop of acetic acid to speed up the reaction. I do not recommend doing this when spotting, since the reaction can āget awayā from you quickly and cause a claim.
For greatest effectiveness when spotting, bisulfite and hydrosulfite should be made up only as needed. This chemical is especially effective on the color red; and like bisulfite, it will usually enhance the āwhitenessā of a dull white garment. Do not use on or around metallic fibers, the area may take on a charcoal or black appearance.
Hydrosulfite is used in a bath the same way as bisulfite, keeping in mind that your are dealing with a more aggressive tool. You should use one tablespoon of powder for each two gallons of water in the container. I use more hydrosulfite than bisulfite, but each have a place in
Reducing bleaches go the extra mile to make your clients clothing look great
More About Bleach!(Image licensed by Ingram Publishing)
the plant. Hydrosulfite is available under various trade names, from various manufacturers; most with slightly different brand specific formulations.
Titanium Sulfate is the strongest of the reducing bleaches. It is a purple liquid rather than a powder. The best way to apply this chemical tool is with an eye dropper or cotton swab to strictly limit the chemicalās travel after application.
Heat the area with a wisp of steam to accelerate the chemical action. I have found it to be safe for most fabrics, but I limit my use to garments with white or a light pastel background.
When using it in an immersion, begin by using cool tap water, one ounce of titanium to each gallon of water. Stay with the garment and keep the garment moving. Gradually heat the solution until you receive the results you want.
Slowly warming the solution will allow you to no tice small changes in the fugitive dye and the garments original base color, so you can stop at the first sign of trouble. Titanium Sulfate is easily available from your distributor, under a variety of trade names.
In addition to the dye strippers, there is an old school chemical tool that is seldom mentioned. Potassium Per-
manganate still has a place for those that wish to go the extra mile. It is a great tool for those operations doing white cotton and white poly/cotton blend garments such as lab jackets and lab coats.
It is intended for the restoration of whites only. An example is a white lab jacket where there was a glob of ink at the bottom corner of the pocket. After you have exhausted all other options and removed most of the ink by normal methods, you have the option of flushing the area with steam, applying potassium permanganate with an eye dropper or cotton swab, waiting two minutes, flushing the area with steam to remove the chemical and then neutralizing with hydrosulfite or rust remover.
Potassium permanganate will get the last traces of color when all else fails. This is a strong, aggressive, chemical. It works and it is an option.
Finally, take this professional care tip with you all throughout the year: Going the extra mile never goes out of style. Superior service includes technical expertise. ADC
Martin L. Young Jr. has been an industry consultant and trainer for 20 years, and a member of various stakeholder groups on environmental issues. He grew up in his parentsā plant in Concord, N.C., Young Cleaners, which he operates today. Phone: 704-786-3011, e-mail: mayoung@ctc.net.
Lavanett, a full-service laundry and drycleaning distributor based in La chine, Canada, recently welcomed Brian Hatt, of Toronto, as sales di rector.
In his new role, Hatt will work to ex pand market share and sales throughout Ontario, with special focus on Toronto, according to Lavanett owner Earl Eichen.
āBrian brings a lot to the table in terms of industry experience and customer relationships,ā says Eichen. āHe is key to Lavanettās expansion into the Ontario market, where plans are underway to estab lish a full-service branch.ā
āI am extremely excited to join the Lavanett team as I return to the Canadian drycleaning and laundry industries,ā says Hatt. āThe La vanett team is a great fit as we all believe in honesty, integrity and professionalism to provide the best advice on all of our customersā busi ness needs.ā
Hatt, who has more than 38 years of drycleaning industry experience, got his start as part of the clean up crew at a Toronto-based drycleaning plant, in 1981.
He earned a dry cleanerās ap prenticeship in 1987 and quickly climbed the ranks to manage one of Torontoās largest drycleaning plants, the firm notes.
In his new role at Lavanett, Hatt plans to use his expertise in wet cleaning and dry cleaning to help owners create more efficient, pro ductive and eco-friendly operations.
āThere is pressure on dry clean
ers to transition from solvent-based dry cleaning to wet cleaning,ā says Hatt. āWe are seeing a growing number of landlords refusing to al low the use of perc or alternative solvents.
āThe good news is that we have wet cleaning solutions that are now as effective as dry cleaning. My goal is to work closely with custom ers to create cost-effective solutions that make them more productive and profitable.ā
Established in 1996, Lavanett notes, it provides laundry and dry cleaning solutions, parts and service to customers throughout Canada.
The Board of Directors of Rich clean announced the promotion of Matthew Gilman to president of the company.
āMatthew succeeds his father, Barry Gilman in this position,ā the firm says. āBarry held the leadership position since the compa ny began in 1975,ā it notes.
Richclean serves the cleaning in dustry in Virginia, Maryland and D.C. with quality supplies and ex pertise for dry cleaners, laundries, lodging, healthcare, and coin-ops, the company relates.
āBarry decided that it was time for him to scale back his activities and responsibilities at RichClean and partially retire. There has been a long-time strategy in place for Mat thew to step into Barryās position
www.americandrycleaner.com
when he retired,ā the firm says.
āFor the last 21 years, Matthew has been ālearning the ropesā and the Richclean Board of Directors felt that he was ready to step up to the leadership position,ā the company indicates.
Vernon Norris, Chairman of the Board says, āI am proud of Mat thewās accomplishments over the years and have full confidence that
he will successfully lead Richclean going forward.ā
Norris also states that, āBarry will still be around, fulfilling various roles and offering advice and wis dom when needed.ā
Richclean operates from a 20,500 square foot warehouse facility in western Henrico County just out side of Richmond, Va., the company points out. ADC
Matthew Gilman2020 RATES: One- to five-time rate: $2.20 per word, boldface $2.30 per word. Minimum charge: $25.00 per ad. Call or write for our three- and 12-time rates. If box number is used,
add cost of 5 words. Display classified rates are available on request. All major credit cards are accepted. DEADLINE: Ads must be received by the 1st of the preceding month.
For example, for a June ad, the closing date is May 1st.
PAYMENT FOR CLASSIFIED ADS: Must accompany order.
Great Proļ¬ts
⢠Located in the State of Ohio
⢠$1.8 million annual retail sales
⢠Strong brand, compact market
⢠Family owns all biz real estate
⢠Proļ¬table, mature, growing biz
⢠New equipment in top shape
⢠25% capacity growth available
⢠Modern fully automated plant ⢠Experienced staff in place ⢠Constant proļ¬t, stable growth ⢠Buyer ļ¬nderās
F-CBI
10 YEARS AGO. The U.S. economy expanded at a 2.8% annual rate in the third quarter, somewhat slower than the predicted 3.5% gain. Consumer spending, which accounts for about 70% of U.S. economic activity, rose 2.9%, with smaller-than-expected gains in household purchases shored up by business spending on equipment and software.
35 YEARS AGO.
Problems Back. IFIās Textile Analysis Department has seen an increasing number of garments with complaints of color changes after normal drycleaning procedures. Most of these articles exhibit a change in color from peach or salmon to pink. The color change is usually from darker to lighter shades. Some garments have changed from tan to green. In most cases, the affected garments are cotton or cotton/ polyester blends. Many of them are labeled washable.
50 YEARS AGO. Magic Carpet. A carpet has been developed by a company in California which may make electrical outlets obsolete. Also television antennas and telephone connections. The ācarpetā is actually a laminated pad which fits under ordinary carpeting, and itās wired for sound to transmit radio, TV and telephone signals with enough electricity to operate other appliances. All thatās necessary to turn on an appliance the company says, is insert a pronged probe anywhere in the carpet. The carpet may
The front cover of the January 1945 issue of American Drycleaner asks: Whatās Ahead For Cleaners In Wages? In Silk Finishing? In Modernized Stores? And inside the issue, in this two-page spread, the headline asks: Whatās Ahead in Modernized Stores? (Editorās Note: In our last issue, Nov/Dec 2019, the feature titled Modernize was on our front cover ā So whatās changed in 75 years? Certainly not a drycleaning ownerās desire to stay up with the times!)
be āmagic,ā but wouldnāt it also be miserable to clean?
75 YEARS AGO. Whatās Ahead in Modernized Stores? According to the teaser at the top of the two-page spread feature (see photo) in the January 1945 issue of American Drycleaner, āStores can modernize now or at least soon. This detailed example, an actual case, should provide plenty of ideas.ā It goes on to say in the body of the article: āWhen they look ahead to improving their stores, we believe, clean-
ers are more interested in the kind that they can have now, or at least soon. Not some idealized store of the future. The possibilities of improving a store, even in these times, are almost endless. Especially if a cleaner is willing to wait a while for materials. To get a better idea of some of these possibilities, walk into the real store shown here. Look at it, first as the designer did when he walked in. Then see just what he did, in detail, to modernize it.ā ADC
ā Compiled by Tim Burke, Editor
To read more of American Drycleanerās chronicling of the industry over the years, visit www. americandrycleaner.com.
101-105 Series
We expect 15 to 25 years from our interchangeable tube bundles, and 30 to 40 years of life our more out the boiler.
209-211 Series
We normally expect 10-25 years out of the copper heat exchanger, 30 to 40 years out of the boiler.
207 Series
We expect 30 to 50 years out of our thermal fluid heater models
On all of the above units we have continued to build, and will continue to have available any part of the pressure vessel, burners, cabinet, and controls meaning that for as long as a customer wants, they will be able to infinitely repair their equipment rather than replace the equipment.
We are asked by many new and existing customers on what is our projected life expectancy of our products. We are not always the lowest initial price but know we have one of the lowest cost of ownership of any boiler manufactured in North America. These facts are based on our 90 plus years of boiler manufacturing, feedback and experiences from our end users, service departments, and all of our representatives and dealers worldwide. These life spans are based on our boilers being installed properly, and do receive our minimal recommended care, are applied to the correct application, and include the proper maintenance and water treatment programs.