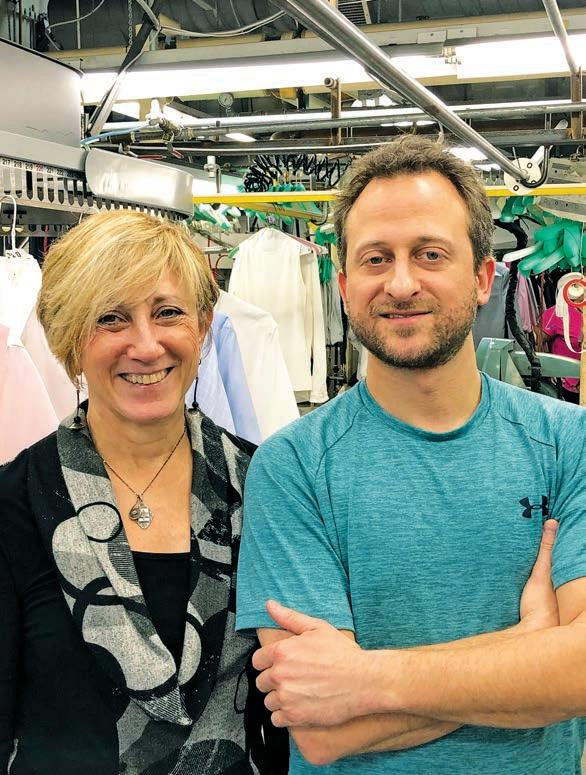


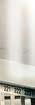

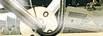


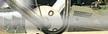


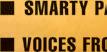
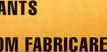
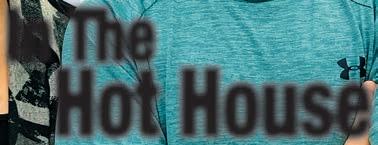




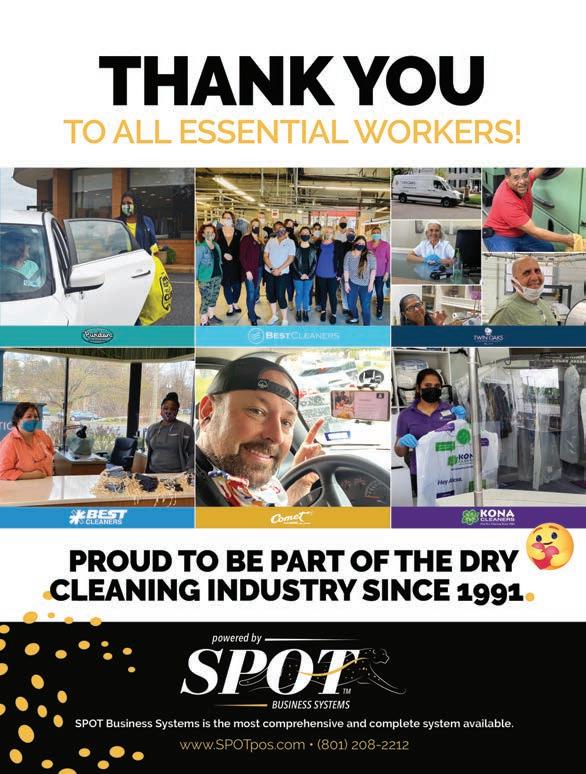
The Poseidon system offers innovative programmability for complete control over every conditional aspect of the wet cleaning, drying and ironing process. Customers are thrilled when even their most delicate garments including tailored wool suits, cashmere sweaters and silks come back with a cleaner smell, better odor removal and an overall superior clean.
“ We’re excited to be leaders in the industry by making the switch to wet cleaning and happy to do our part in minimizing our environmental footprint. ”
— Miriam Choi, daughter of Hyeon-Dong & Young-Sook Choi Owners, University Cleaners
June 2020
Vol. 87, No. 3
DEPARTMENTS
Pre-Inspection 4 Cool Warming
Talk of the Trade 6 Local, Locale
Yarns Spun Here 21 Organza Bag!
Special Feature 22 Voices From Fabricare
Special Feature 24 Ripples of Wet, Jeff Quail
From Tennessee to Texas, two garment care operators share how they best manage their team members who have to work in the plant. Conditions are often loud, warm and claustrophobic but great teams find ways to get along with each other’s personalities. That might mean a pizza party, several breaks from the heat, wearing headphones to enjoy their own music, and more. Learn tips and hear stories from these owners — straight from in the hot house, at a plant just like yours!
Tim Burke, Editor
Today’s smart machines and technology, and the well-trained team members who have to know how to operate them efficiently, go together better than ever. Find out from two separate owners located in California how they find a match to the best people working smartly with modern tech. It’s not only big machines out in the plant, but everywhere at your operation — like modern POS, apps and more up at the counter.
Tim Burke, Editor
Off The Cuff 27 Get to Know ... Colleen Unema
Around the Industry 28
Classified Ads / Ad Index 30-31
Wrinkle in Time 32 Large Volume, Small Space!
Scan this QR Code for help in finding the hidden hanger on this month’s cover. Good luck!
June is a warm month. Hot even, for many.
On the cover, that’s Rhonda Wernick, half of the husband and wife team, Alan is her husband, who own Nashville’s Oakwood Cleaners, and she’s standing in their plant with their son Aubrey.
In The Hot House is my own description of an often crowded, but usually sort of fun and upbeat plant, full of noise, steam, newly cleaned garments hung up, and aisleways so tight you can hardly make them out. To me, secretly, when I’m walking through, they feel more like passageways through an almost living, breathing animal, that sustains your businesses.
Your team members have to work in that ‘hot house’ environment and it’s not only busy and exciting but challenging and…. quite warm! Especially as summer rolls at us. This feature looks at how two owners, in Tennessee and Texas, manage their teams and try to keep them comfortable and happy as they put out the work — and keep everyone sane! And let them rock out to their own beat! That’s cool!
The other feature, Smarty Pants, talks to owners, in different parts of California, about combining smart technology and machines of today’s garment care operation with well-trained team members to find just the right fit to get the best efficiencies.
Special features this issue include Voices From Fabricare, hearing directly in words and also seeing images as some owners share how they have been working to get through COVID-19; and Ripples of Wet from Jeff Quail about wetcleaning programming, the how and why.
We also bring you some other specials you’ve come to enjoy, including a new Yarns Spun Here, a new Off The Cuff, a new Wrinkle In Time and more.
Garment care continues to serve its clients the best it can, with great service, great quality, mindful of health and welfare, and at the end of it all, determination. June is warm for sure, but keep on truckin’ like you do, and that’ll be real real cool! ADC
American Drycleaner (ISSN 0002-8258) is published monthly except Nov/Dec combined. Subscription prices, payment in advance: U.S., 1 year $46.00; 2 years $92.00. Foreign, 1 year $109.00; 2 years $218.00. Single copies $9.00 for U.S., $18.00 for all other countries. Published by American Trade Magazines LLC, 650 West Lake Street, Suite 320, Chicago, IL 60661. Periodicals postage paid at Chicago, IL and at additional mailing offices.
POSTMASTER, Send changes of address and form 3579 to American Drycleaner, Subscription Dept., 440 Quadrangle Drive, Suite E, Bolingbrook, IL 60440. Volume 87, number 3. Editorial, executive and advertising offices are at 650 West Lake Street, Suite 320, Chicago, IL 60661. Charles Thompson, President and Publisher. American Drycleaner is distributed selectively to: qualified dry cleaning plants and distributors in the United States. The publisher reserves the right to reject any advertising for any reason.
© Copyright AMERICAN TRADE MAGAZINES LLC, 2020. Printed in U.S.A. No part of this publication may be transmitted or reproduced in any form, electronic or mechanical, without written permission from the publisher or his representative. American Drycleaner does not endorse, recommend or guarantee any article, product, service or information found within. Opinions expressed are those of the writers and do not necessarily reflect the views of American Drycleaner or its staff. While precautions have been taken to ensure the accuracy of the magazine’s contents at time of publication, neither the editors, publishers nor its agents can accept responsibility for damages or injury which may arise therefrom.
American Drycleaner, June 2020
Publisher
Charles Thompson
312-361-1680 cthompson@ATMags.com
Associate Publisher/ National Sales Director
Donald Feinstein 312-361-1682 dfeinstein@ATMags.com
Editorial Director
Bruce Beggs 312-361-1683 bbeggs@ATMags.com
Editor Tim Burke 312-361-1684 tburke@ATMags.com
Digital Media Director Nathan Frerichs 312-361-1681 nfrerichs@ATMags.com
Production Manager Mathew Pawlak
Advisory Board
Jan Barlow Mike Bleier John-Claude Hallak Wesley Nelson Kyle Nesbit Mike Nesbit Fred Schwarzmann Beth Shader
Contributing Editors
Dan Miller Diana Vollmer Martin Young
Office Information Main: 312-361-1700
Subscriptions 630-739-0900 x100 www.american drycleaner.com
White Conveyors’ OAS is the perfect solution to expand your existing business, improve customer service and increase profits. Order Assembly couldn’t be easier.
The OAS significantly reduces your labor costs while greatly increasing productivity. What’s more, order accuracy is optimized, and employee morale is improved as fatigue is virtually eliminated.
And if that were not enough, savings from reduced labor costs combined with increased productivity typically results in a return on investment in less than one year.*
The system can be delivered and operational the same day. As an option, it can be mounted on wheels for mobility or storage. It couldn’t be easier. Isn’t it time to realize remarkable time and money savings?
Easy to Use clear and easy-to-read color touch screen, plus audible instructions
Increase Productivity while Reducing Labor Costs capable of assembling over 2000 garments per shift with one operator
Fast Return on Investment typical ROI in less than 1 year*
More Capacity standard 5 slots per foot have 50-80% more hanger capacity than competitors, reducing the need to split large orders
Flexible software customization is available for specialized customer’s requirements
Highly Accurate and Reliable greatly reduces the chance for human errors
Reliable, Robust and Durable Construction with average operational lifespan of 25+ years
USA Based Manufacturer for over 75 Years remote diagnostics, setting adjustments and troubleshooting assistance reduces downtime, and minimizes the need for an on-site service technician
* ROI is based on the Bureau of Labor Statistics
When asked in this 2020 American Drycleaner Your Views survey to tell us: “How do you rate your store location on a scale of 1-10? (With 10 being best.)” Here is what respondents reveal:
Almost all of the answers were rated 8 or above. There were a few 10s. Also, a few rated in the 3-4 range. No respondents rated their business location below a 3. The survey then poses this: “Which best describes your location?”
“Stand-alone building” received 32%. “Strip mall” received 24%. “On a block with other stores” received 24%. “Shopping center complex” got 16%. “Industrial area” got 2%. “Mixed.” got 2%. (See graphic.)
The survey asks: “Tell us what you like, and what you don’t, about your location?” Keep in mind respondents received and answered the survey just before COVID-19 was hitting and affecting business. Answers are as follows:
• “Like the location. But limited parking.”
• “We’re short on parking.”
• “The shop is in a reasonably busy area, but the age and appearance of the building and surrounding buildings needs urgent attention. Parking is also a huge problem.”
• “Corner, one block from the intersection of the traditional travel routes going north, south and east, west.”
• “Love the area, but not the crime.”
• “I built it myself. Busiest corner in town.”
• “Highly visible with a double drive-thru. Great existing demographics with a fast growth rate.”
• “I like the close neighborhood feel. I dislike the minimal traffic that flows through the corner.”
• “I am in a great upscale location but would love to have a drive-thru.”
• “Perfect.”
• “No drive-thru.”
The survey asks respondents: “How much customer parking do you have?”
Forty-two percent say they have a, “Big parking lot.”
Twenty-nine percent have a, “Few places in a small lot.”
Thirteen percent have, “Street parking.” Eleven percent
American Drycleaner, June 2020
Stand-alonebuilding. Stripmall.Onablockwithotherstores.Shoppingcentercomplex. Industrialarea. Mixed.
have, “Other.” (Such as “Shared non exclusive.”) And five percent have, “A couple reserved spaces.”
Lastly the survey asks: “If you could move your business, would you? And why?”
Many respondents simply answer “No.” Or say that they would not move. But some did say that they would move, as follows:
• “Yes, only for pickup and delivery. Not the plant.”
• “I would move if I had the same exposure, better parking, and cheaper rent. Connecticut is killing small businesses.”
• “I would move it to my own building. Right now I’m renting a space.”
• “Yes in a heart beat, because we need parking and more space.”
• “Yes, owning a building is the ultimate goal.”
The Your Views survey offers a current snapshot of the trade audience’s views. Qualified subscribers to American Drycleaner e-mails are invited to participate anonymously in the unscientific poll.
You might say that catacombs have nuthin’ on some drycleaning plants. The plant can be all at once: Hot! Humid! Noisy! Claustrophobic!
We’re getting through COVID-19 and working to get on the other side of it. We’re looking at the garment care plant in general in this article. As work gets processed, all the while team members have to do their job, and deal with the historically loud, steamy, cramped confines of plant workspaces.
Two owners, one from Tennessee and one from Texas, are going to tell us how they take these challenges seriously and work tenaciously, and with care for their team members, to solve hot house conditions.
For the first of our two Hot House operators, we visit Alan and Rhonda Wernick, who became the proud owners of Oakwood “The Greener” Cleaners in April, 2011. They have 28 employees between production, route service, maintenance and customer service.
What do they think of working conditions today in the drycleaning plant and the stressors at play?
Rhonda Wernick relates that: “In an effort to operate efficiently, maximize space utilization and to minimize physical exertion of production staff, many dry cleaners attempt to squeeze as much equipment as possible into a limited space.”
She adds that in some situations, the impact on staff can be exacerbated by overstaffing work space or poor quality of air or temperature and
that can lead to employee fatigue, poor quality and inefficiency.
At their business, Oakwood Cleaners, like many other dry cleaners, she notes that, “We are production-space challenged but we do attempt to combat employee stress in several ways.
“We assign each production employee a primary function that gives them a feeling of ownership and belonging,” Wernick says, “as well as making them comfortable within their designated work space.”
Also, she says, they organized equipment efficiently to reduce the employees movement when the task requires more than one machine or procedure. They provided rubber mats to reduce foot and leg fatigue. They insulated steam pipes and traps to reduce heat and humidity, and they air conditioned their plant to help keep staff energy up.
“We also make sure our staff are allowed breaks throughout the day to get some fresh air or sit in our break room to eat or relax. We exclusively use GreenEarth® solvent so there is no odor or harmful chemicals to hurt our staff or the earth around us,” Rhonda indicates.
She adds that: “Precautions are taken with some spotting agents, such as gloves, masks or eye gear to help prevent toxins from entering the body.”
Wernick talks specifically about their plant area: “Production space is a major issue that affects our operation. To free up production space, we rely extensively on both assembly and storage conveyors to more efficiently use our available space.”
She notes that, “The assembly conveyor auto-
The plant is often hot, humid, loud, and claustrophobic with garment cleaning to be done. Come explore with two owners options to help you solve, and soothe, some of the challenges from the Hot House.
matically matches our orders prior to bagging, reducing errors, saving time and reducing space requirements. The storage conveyor is used to rack all completed tickets that will leave the production facility. This conveyor stores the orders near the ceiling and allows the space below to be used for servicing items in process.”
Wernick explains that repetitive motion can be a problem for their pressers as well as their other staff. “We are working on ways to help them such as an anti-gravity system to reduce weight to our staff using irons on repetitive tasks.”
One of the challenges in any plant is matching people to their skill comfort for greatest efficiency and Wernick shares an example of their solution:
“We had a wonderful young woman working as a CSR. Our customer service manager noticed she was having a difficult time keeping focused while markingin. We gave her an opportunity to work in production on the weekends, and she excelled.
“We offered her a full-time position in production and our production manager worked with her to train her in the laundry department as well as sorting items in preparation for pressing. She is excelling and is eager to learn every thing about the production department,” Wernick notes.
She points out that: “This is a great example of recogniz ing that the job might not fit the individual and moving them to another area to be able to retain a great employee.”
Is the plant today getting better designed; giving more thought to helping alleviate stressors?
Wernick believes with more modern technological advances on drycleaning equipment that today’s plant is becoming more efficient and a less stressful place to work. As it has become more difficult and more expensive to attract quality staff, dry cleaners realize that a good working environment is required to acquire and hold onto them, she relates.
“This not only includes the physical conditions of the plant, but also the intangibles such as communication, camaraderie, sense of belong and benefit package,” she says.
She shares tips for helping other owners solve common hot house issues.
Wernick says: “If possible, add some kind of cooling, whether it be air conditioning or watercooled air. We have put large fans in place that help move the air.”
Also, Wernick notes, they try to cut down on lint building up on their equipment. “We are on a constant lookout for steam leaks or bad traps not only to eliminate energy waste, but to help keep the environment comfortable for employees.”
Finally, Wernick reminds you to, “Think outside the box and be creative. Approach problems as challenges. We do this at Oakwood Cleaners and as a team. We work together to provide the most up to date working environment possible for our staff.”
Approach challenges as a team effort. Those are sound words in today’s world as we all face the challenges of the recent coronavirus.
Now we go South by Southwest to visit with our second owner, who talks about all the dynamic personalities on her “hot house” team.
Vicky Maisel is the second generation owner of Cowboy Cleaners located in San Antonio, Texas, a business started by her dad Donald Maisel more than 60 years ago. We asked her to describe working conditions in the average drycleaning plant today along with some of the various types of common stressors on team members we might find.
Maisel relates this: “I think that although heat and noise probably on occasion add to the stress.
What I find the most difficult at times, but also can be delightful, is we have in our drycleaning and laundry plant about 20 different personalities with 20 different perspectives on everything.”
She notes how, in the past, her team wouldn’t agree on lunch, or on how to properly press a special request by a customer, or what radio station to listen to!
But when challenges in the plant needed to be addressed, keep in mind these are pre-coronavirus examples, she talked about what she would do: “I have found that when it looks like everyone is hot or just starting to get a little cranky — doughnuts and pizza really help.”
Every now and again, Maisel points out, “I think after a week when we have achieved something special, like a lot of extra garments or a piece of equipment goes down and everyone is scrambling to move around and get the work done, a nice gesture helps express my gratitude to the employees for hanging together and making everything work out.”
When everything is going smoothly, she relates, “I like to surprise them with doughnuts to say job well done and thanks. These folks can pull together and help in ways you cannot imagine. We will have dry cleaning step in and help laundry when needed and vice-versa.”
Maisel says that, “Even though we have the ‘class clown’ and the ‘serious, no-nonsense’ folks working together — and they may occasionally drive each other nuts — a nice pizza lunch will remind them we are a team and we appreciate all of their diverse talents and personalities.”
Can you tell us a story or two of how you
Down in Texas, Cowboy Cleaners’ Hot House team spends some time in the break room. This photo was taken back in February. (Photo by Cowboy Cleaners)
solved a particular situation for your team members in your plant and the positive result?
Maisel relates this story: “One day the boiler went down. So needless to say nothing, and I mean nothing, could get done. So while we waited for the boiler to be repaired, we cleaned machines and did whatever we could. Hours later we were very far behind on production, but everyone pitched in, and as we finished the last shirt at what is our closing time 6:30 p.m., my sister Shannon ran over to store and picked up some beer and pizza and we all celebrated making it through day and a job well done!”
Just before the coronavirus had hit, we had asked her to describe her team, and she related that her team typically would come in at 5 or 6 a.m., so that was one long hard day. But Maisel reflects that it was nice to be able to toast their hard work and celebrate their teamwork.
“Let’s be honest,” she says, “no one wanted to be there all day.” But she notes how they all pitched in and the drycleaning team came over to help the laundry team and everyone was doing something to get customers their clothes. “So it was great to be able to sit down together and enjoy each others company after that very, very long day,” Maisel relates from a pre-virus example.
Plants are better designed today, no doubt. But it always comes back to the special people owners have on their teams.
“I think that there are times when it is 100+ degrees, and we are standing over steam and heat, and no amount of ice, fans and air will really make it refreshing. But I do think on those days, that is the time to bring in something different to let your folks know they are appreciated,” Maisel says.
Spirit and professionalism are on display from a team member deep in the crowded quintessential Hot House found in many plants. The photo is from last summer when the author visited Zengeler Cleaners in Northbrook, Ill. (Photo by Tim Burke)
So even though we design our plants to try alleviate the noise and heat, she notes, “We need to remember the folks we work with are all different — they have different problems, needs and desires and bring those together to create a team who want to do the best they can for the customer.
“They care about each and every garment, and that is what matters. Yes they get a paycheck, but sometimes it helps to just show them how important and special they are to me and Cowboy Cleaners.”
Maisel relates this tip: “I found that letting my employees wear headphones really helps keep squabbles to a minimum. Everyone can listen to whatever music they like and there are no more arguments over the radio!”
Maisel says: “They still do a great job and seem to actually concentrate more on their work.… but sometimes when they sing along, it does sound like a cacophony.Guess it just means I need to buy my own headphones!”
These two owners great ideas and creative solutions show there are many ways to helping your team to get through tough days, loud days, and warm days all together and successfully.
Of course we are getting through a big challenge in the world, the coronavirus, and looking ahead.
Many garment care operators no doubt do so many things to solve their own hot house challenges. It comes down to keeping your teams comfortable, working at their best, and being safe, healthy, (more true today than ever with COVID-19), and also efficient in the plant.
Hopefully soon, with headphones blasting out their own favorite tunes, team members might be once again rocking out and having a hot time in the hot house!
Smart Machines and Smart People go together in garment care operations today. Advanced technology walks forward hand-in-hand with a well-trained team, well-suited to handle the smartest of smart tech in your garment care world. Our two panelists, from Bryan’s Cleaners and from Greene’s Cleaners, answer questions all about getting smart today.
By Tim BurkeThe team at Bryan’s Cleaners works smarter than ever before and is helped to be at their most efficient with equally smart machinery in today’s operation. They stand here with a classic copper kettle
In today’s garment care world, that just might not be a boast, it might be the honest truth about your technology and your team working together at highest efficiency. That’s really, um, smart!
These operators share their experiences with melding new machines and technology with well-trained, great
piece of washing history, a subtle, retro reminder of where we’ve all come from in the industry, yesterday to today, working smarter with our garment care advances. (Photos by Bryan’s Cleaners)
CRDN is looking for qualified candidates to acquire these franchise territories immediately. Additional territories may be available.
CRDN, as a network, has grown every year since its inception in 2001, including through tough economic times in the US and Canada, including the events of 9/11 and the recession of 2008 and 2009. There is no offperiod for residential and commercial insurance claims and, as such, we believe there will always be a need for insurance restoration services.
This information is not intended as an offer to sell, or the solicitation of an offer to buy, a franchise. It is for information purposes only. This offering is made by prospectus only. The franchisor, Certified Restoration Drycleaning Network, LLC, is located at 2060 Coolidge Hwy, Berkley, MI 48072, and is registered as File Number 4214 in the state of Minnesota.
team members for best efficiencies. Hear this special Q&A style panel talk all about smartness in their tech, smartness in their people, and the smarts to manage it all and do it well. Let’s get smart….
Our first panelists is Scott Bell, owner of Bryan’s Cleaners & Laundry, started in 1938 by Garnet Bryan in Pasadena, Calif. Bell says his company markets to busy professionals with large disposable incomes who enjoy the perks of having clothes picked up and delivered by route and valet.
Q: Can you tell us, generally speaking, how much smarter has machine technology become in cleaning operations today?
Scott: “It’s become a lot smarter. I can think back when there was a real dry spell in our industry. Technology left us from the 1950s to the 1980s. Now, in the front end, we’ve become computerized. We can all remember when there were Vis-A-Files and receipts to find the location of our customer’s clothes.
“Now all of that has disappeared and the front end has become very clean with computer screens and credit card machines. On the finishing side, we’ve almost completely disappeared with manual presses. Our plant was completely manual; now everything is hydraulic or pneumatic and the only fatigue our employees experience is from the heat in the summer when they’re having to work hard on getting the linens finished.
“The third area that has really improved is in the cleaning department. When we had a cleaning machine back in the fifties and sixties, it required carbon filtration to keep the colors from bleeding into the solvent and exposing it into the next load of clothes. All that is completely gone now with filtration that uses paper cartridges and makes clean up much easier and quicker.”
Q: Along with modern technology, owners need the labor to run these smart machines, so what’s that like right now trying to match up new technology with the team members who have to run it?
Scott: “I think that’s something that has been a benefit to the drycleaning industry. With the advent of computers it has really been an easier challenge because the people are forced into a routine on both the machinery side and the computer side. It has made it easier for training because the machines and the computer require the people to com ply with a uniform and systematic way of doing things.”
Q: Share some of the challenges owners face training their team members on new machine tech?
Scott: “We have pre-training where they can sit and go through manuals and read it to begin with and know what they’re going to be exposed to. Once they get up there, they watch someone else do it and observe systems and routines. There is always personalized aspects to everything; Things the employee will implement on his own. If they don’t follow the proper steps in running the machinery, it won’t respond to them and they won’t be able to perform their job.”
Q: Where has technology improved the most in today’s machines?
Scott: “The computerization and creation of the database. I remember when computers first came out, the talk was that everyone would be working a 30 hour work week and there would be less hours in our work week. That couldn’t have been more wrong, but I can see where they were coming from.
“Actually what the result was it brought technology that was only available to Fortune 500 companies all the way down to the mom and pop store. With the creation of databases, we all knew what services our customers are using. We could then in turn provide them with coupons for services they weren’t using. We’re able to track their clothes and their habits.”
Q: About efficiency, is it hard to find the right fit between an individual team member and the specific machine?
Scott: “I don’t think it’s any harder than it has ever been. It depends on the screening you’ve done in the interview process for the right person. You can find the right person but you still have to work to get them to buy into that machine.
“Part of it might have to do with how interested they are in getting a job and keeping that job. I don’t think that tech is so advanced that it left anybody behind. Tech is more mechanical and more buttons that no one can just walk up and intuitively know what to do and expect it to work. Dexterity is important but so is the process.”
Q: Can you share a memorable story about when a team member and their machine just clicked?
Scott: “I have an employee who was doing pants for me and I told him that I was going to change his system. I brought in a topper that was going to blow the pants at the top and then he was just going to have to leg them on the press. I brought the topper and the legger in. He went from 30 pants an hour to 50 pants an hour.
“This didn’t happen overnight, but by the time he
Drycleaner,
was a couple of months into it and for years after that he could really put out the pants. I was really shocked. When you looked at him you would not think he was working hard. He was one with the pants machine, one with the double legger.”
Q: Can you share a tip for readers on how they can best combine smart new technology with their smartly trained team?
Scott: “Getting them to buy-in for the betterment of the team is key; to realize that efficiency makes their job easier and the result adds to increase in company profits and his or her bottom line.”
Q: Better tech along with a welltrained team improves efficiency, but what should an owner watch out for along the way?
Scott: “Tech today is a lot more reliable but it has turned into a doubleedged sword. The machines we use now aren’t manual anymore. They have hydraulics, electronics, pneumatics and if you can’t read a schematic for the electronic part of it and if you don’t have the tools for the pneumatic part of it, you’re not going to get it fixed.
owner with husband Alonso, fourth owners of the business. The company name comes from George Greene, who established the company, she relates.
Laurie says she grew up in the business which her parents purchased the year before she was born. At the time, they had one employee other than themselves. Thirty years later the company has 30 employees.
“Alonso and I moved to Napa in 2003 when Alonso began working with my parents to learn the business. In 2009, we purchased it and they fully retired. The success of Greene’s has largely come from maintaining a strong commitment to quality and community.”
Bryan’s Cleaners owner Scott Bell. One of our panelists an swering questions about smart machines and smart people in garment care operations today.
Q: Can you tell us, generally speaking, how much smarter has machine technology become in cleaning operations today?
Laurie: “One of the big leaps in the machine technology I’ve seen over the years is how specific we can get with cleaning programs and the ability to create a program for specific items that our business services a lot of, which may differ from a cleaners in another area.
“Even if I can trouble shoot a problem with the machine, it’s probably going to require a mechanic with the necessary tools and parts to get it up and running again.”
Q: Anything else you’d like to add about ‘Smart Machines, Smart People’?
Scott: “Be sure that you don’t rely on machine technology or machines in general to carry your company. You still need to have a great team member atmosphere in your building because that’s really what’s going to carry your business. A long standing problem, obviously is labor, but in the end, what customers want and what’s really going to make your business outstanding is your staff and their approach to the business and everything else.
“While tech is important, I don’t think it is the end all to make your company last a long time.”
Our second panelist is from Greene’s Cleaners, which celebrated it’s 100th year in business in 2019. It has grown with Napa Valley, in the process becoming an important community partner, says Laurie Greene, co-
“Recently, the technologies we are seeing in new equipment address energy efficiencies in addition to cleaning or finishing efficiencies. For many years, equipment design focused solely on operational efficiency and garment quality. Recently, I have seen manufacturers who still focus on those key areas, but incorporate energy or water conservation as well.”
Q: Along with modern technology, owners need the labor to run these smart machines, so what’s that like right now trying to match up new technology with the team members who have to run it?
Laurie: “My experience has been that as technology improves, it is actually easier to hire and train staff to operate the equipment, primarily because of the incorporation of programming and automation.
“I don’t necessarily need a garment care expert when equipment can be programmed to differentiate garment needs. For example, we found we were cleaning a lot of embellished garments. In the past, an operator would
have needed to know how to override a cycle to set a shorter time, lower temp, spin, etc., to ovoid damaging the garment. Now we can contact our Kreussler rep to add a program that has settings to best care for that type of garment. And they are able to do it in very little time.”
Q: Share some of the challenges owners face training their team members on new machine tech?
Laurie: “Over the last few years, my focus has been on implementing systems and procedures to ensure consistency and quality throughout our operations. Training staff to follow a procedure is simple compared to training someone to understand how a machine works or the differing properties of various textiles.
“The biggest challenge we face is when we hire an experienced operator and we need to undo bad habits or teach someone to trust the equipment. Maintaining equip ment so it can be trusted to operate as designed is key.”
Q: Where has technology improved the most in today’s machines?
Laurie: “The ability to make adjustments has improved all around. From temperature settings to pressure settings to fit settings, like length, the improved tech enables an operator to fit the machine to the garment and their operation style rather than adjust how they handle each and every garment.”
Q: About efficiency, is it hard to find the right fit between an individual team member and the specific machine?
Laurie: “We do a lot of cross training so that our production staff is comfortable with most of the equipment. In doing so, we have sometimes identified where someone thought they were best suited to one station, they actually excel at another.
“I wouldn’t say it’s difficult, but it requires a flexible outlook and to approach hiring in an untraditional way. For example, years ago we would look to hire a pant presser. Now, we hire production staff and counter staff. The only real differentiators in those two types of people are schedule availability and English fluency. Mindset and work ethic are more important to us than technical skill.”
Q: Can you share a memorable story about when a team member and their machine just clicked?
Laurie: “Last year we had Liz Davies out for a week working with our production manager and staff. A presser who has worked for us for 14 years and is one of the most skilled pressers I have ever seen learned a new technique for using the SAM unit that changed her world. She
Drycleaner,
learned to trust the equipment and use the available set tings to get the most out of what it was designed to do. At first, she was skeptical. Then she embraced it and it made her so happy because she reduced her need for touch-up, and garments like chef coats were no longer avoided or put off because they interrupt her flow.”
Q: Can you share a tip for readers on how they can best combine smart new technology with their smartly trained team?
Laurie: “First of all, ask questions. Assuming you know all of the capabilities of the equipment hinders the ability to utilize tech. Equipment manufacturers, reps, consultants are all available.
“The garments we process change in style, construction, materials. Reaching out and asking if there is a technology to address a new issue provides the possibility of making the job easier and more successful for your team. Then, create a procedure around it and train on the procedure.”
Q: Better tech along with a well-trained team improves efficiency, but what should an owner watch out for along the way?
Laurie: “Some things should never be short cut. Testing garments, especially ones with unfamiliar materials will never go away. No matter how much we improve our processes and utilize smarter equipment, we can not control garment manufacturers or trust the ability to process an item.”
Q: Anything else you’d like to add about ‘Smart Machines, Smart People’?
Laurie: “The area we have recently found the most ef ficiency improvement and cost savings from technology implementation has actually been on the customer service side. Because we are in an area with a hospitality centered economy, there is a lot of competition for that type of labor.
“By utilizing tech which replaces some of the traditional customer service functions, such as answering basic questions, we are able to have fewer people serve more customers.
“And those people provide better service because their time is freed up to focus on the more involved customer issues. In prior years, the technology around item tracking and inventory management allowed for huge time savings across departments.”
Our two panelists, each garment care operators, imparted their knowledge of smart machines and smart people working together to achieve top efficiencies.
Are you smarter now?... Huh smarty pants?! ADC
Organza! There. I said it.
Think: Sheer.
Have you ever owned an organza bag to use in your garden to protect your flora and fauna?....
Maybe not. Organza is used in bridalwear and eveningwear. Double-width organzas, in viscose and acetate, are used in sheer curtains, according to Wikipedia.
Silk organza is woven by mills along the Yangtze river in China. Deluxe silk organzas are woven in France or Italy.
According to American Dryclean-
er’s Spotting Guide, author Norman Oehlke pens that, “Organza is a thin and usually transparent plain weave fabric often used in evening dresses. Care must be exercised in spotting to avoid yarn distortion. Keep the steam gun six to eight inches above the fabric.”
While Organza sounds like the rebel leader straight out of a Star Wars movie, the weave discussed here is really just the sheer material that some dresses, costumes, veils — and even an organza bag used to cover plants in the garden — are made out of. Yes, a sheer bag!
Order one of those sheer bags for your garden if you like. Feel free,
even, to excitedly holler to passersby: I own an Organza Bag! If you so choose. It’s fine with me. Just do it when I’m not around. ADC
Presidential Cleaners says it has, “Launched our Front Line Relief effort. We are offering free drycleaning and laundry service to all first responders, front line medical and front line grocery staff. This is a whole family offer as we want to take the stress of all laundry needs off the family. This is a community funded effort that we hope to continue as long as we can. We launched this great effort April 15.”
— Steven Fry, owner, Presidential Cleaners, Brighton, Mich.
Steven Fry, owner, Presidential Cleaners, Brighton, Mich., at left. His company, “Launched our Front Line Relief effort. We are offering free drycleaning and laundry service to all first responders, front line medical and front line grocery staff.” (Photo by Presidential Cleaners)
Drycleaning by Dorothy says that, “Although this virus hit like a ton of bricks I believe we have managed a way to keep working. With sales off about 80% we at first laid off all employees. We adjusted our hours to Mon.-Fri. 9-3, and Sat. 10-2. Closed Wed. and Sun. My wife and I are waiting on customers every day and so far we have taken in enough dry cleaning and shirts to have the entire staff come back and process on Thursdays.
“We have seen several new customers every day and also our regular higher volume customers for the most part. It’s worth noting that our average customer piece count is much higher. We are taking in an unusually large amount of $100 plus orders.
Dutch Girl Cleaners says it is providing, “Free uniform cleaning to all first responders and front line medical staff. We plan to keep this offer going throughout the duration of the pandemic. We have been mentioned several times in the resent weeks on the local news and radio. I really want this to be an inspiration to other cleaners to step up if they are able and help by giving back to those who give so much.”
— Joe Baughman, general manager, Dutch Girl Cleaners, Walnut Creek, Calif.
“As more people realize that we are open my hope is that we’ll slowly graduate to process two days and then three and so on. I think the most important thing for dry cleaners to do is to let their customers know that they are open and their new hours. Flags, Facebook, Twitter and email are great, inexpensive ways to accomplish this. Stay safe!”
— Bob Devaney, owner, Drycleaning by Dorothy, Boston area
Above, the team wears masks at Drycleaning by Dorothy. Bob Devaney, on right, is the president and works with his wife and gets help from their masked pooch.” (Photo by Drycleaning by Dorothy)
Max I. Walker relates: “We volunteered to launder 375 pairs of scrubs for a local hospital, in partnership with our local Goodwill. Also, we have volunteered to launder 10,000 plus reusable fabric masks for another hospital system on an ongoing basis for the duration of the COVID-19 pandemic.”
Max I Walker delivers cleaned scrubs to Bergan Mercy Hospital after they were laundered.
Fabrix Drycleaners says: “We have three locations, two drops and one plant/drop. The plant drop is hanging tough. We are open 8-5 Monday; 9-1 Tues.-Sat. It’s time to get back strong to get new customers. Two drops stores are 9-1 Mon., Thur., Sat. I’m expecting business to be off the charts sooner than later.”
Scott
— Scott Spruill, owner, Fabrix Drycleaner, Medford, N.J.
Spruill,
N.J.
Mastercraft Dry Cleaners explains its, “COVID-19 precaution: For my two front counters I use my long poles and clear tape to hold the seams together and staple it to pine posts.”
— Steve Berglund, owner, Mastercraft Dry Cleaners in Fresno, Calif.
Dry Fresno,
The front counter at Mastercraft Dry Cleaners in Fresno, Calif. (Photo by Mastercraft Dry Cleaners)
Those are some of the voices from the fabricare industry about getting through!
Aessential to properly cleaning a variety of items and fabrics.
If you’ve got one on the floor, you can safely wet clean everything from delicate silk blouses and wool suits to casual wear, shirt laundry and household items — even pillows, stuffed animals and luggage.
But not all wetcleaning machines are created equal. So, when you invest in one, be sure it offers essential programmability and adaptability. Read on for what to look for when it comes to programmability and learn methods for customizing wetcleaning programs for exceptional results.
First, though, let’s understand the four essential components of cleaning. The four components — mechanical action, chemistry, temperature, and time — each work in balanced concert with the others to properly clean. If any one of the factors is reduced or increased, the opposite needs to happen to one or more of the other components. As time increases, we can decrease temperature and/or mechanical action. If we increase chemistry, we can decrease time and/or temperature.
Mechanical action is the movement of garments within the wash wheel. The more mechanical action, the more movement of chemistry and water through the textiles. Rotation action and drum speed work together as mechanical action.
Chemistry refers to the types and concentration of
chemicals in the wetcleaning process. Chemistry includes water, detergents, softeners/surfactants, bleach and sours/neutralizers. The improper use of chemicals can lead to damaged or discolored items.
The chemicals work in concert with water temperatures. As water temperatures rise, chemicals react more quickly and efficiently. Generally, when water temperatures are lower, more chemicals are required to properly clean.
Time refers to the number of minutes for each wash step. The ability to control time is critical to economical cleaning.
Using a highly programmable wetcleaning machine ensures the above components can be customized ac-
cording to fabric and item type — making it easy to achieve the perfect, consistent clean no matter who’s operating the machine. Thus, programmability is extremely important in the fabricare business. It allows virtually anything coming in the door to be properly cleaned using water, using the most productive and energy-efficient manner possible.
To get the most out of a wetcleaning machine, choose one that allows programmability of number of phases, bath levels, water temperature by degree, bath cool-down by degree, rotation action, rotation time, extract speed, number of baths and rinses, and automatic chemical injection. Let’s take a closer look:
Rotation Action and Drum Speed – Heavy garments need more drum speed during agitation to get them up and out of water so they can drop back in. Lighter garments require a slower drum speed or they don’t fall properly. The more options for programmable timed drum speed and rotation action, the better.
Water Levels – When washing durable goods, like towels, jeans and blankets, it’s important to use lower water levels when introducing chemistry. Lower water levels create a situation where clothes are closer together, creating more mechanical action. When wet cleaning, we make up for low mechanical action by raising water levels to ensure all garments stay saturated throughout the cycle.
Water Temperatures – As water temperature is lowered, more chemistry is required. Being able to set water temperatures by degree is essential. Certain synthetics and blends can experience fabric shock if cleaned at a high temperature and then rinsed in cold water. A gradual cool down before the wash water drains should be programmed into the cycle.
Extract Speed – As extract (spin) speed increases, more moisture is removed from a load. This ultimately shortens dry time and improves throughput. While cranking up extract speed makes sense on durable goods, it doesn’t on items like stuffed animals, sneakers, draperies, wedding dresses and other fancy gowns because you run the risk of deforming/damaging them. Look for a
machine with timed programmability in minutes or seconds and programmable extract speeds ranging from 5 to 400 G-force.
Number of Baths and Rinses – The more soil, the greater the number of baths and rinses required to get items clean. Fire restoration items, for example, need multiple bath exchanges to eliminate contaminants, whereas typical wet cleaning uses only two baths.
Automatic Chemical Injection – To guarantee optimum cleaning, look for wetcleaning machines with 12 chemical injection signals and programmable, timed dosing and flush flexibility. Automatic chemical injection eliminates potential dosing errors that can damage garments.
Delayed Start – A delayed start feature allows you to load at night and set the machine to begin operation the next morning. It’s a great tool for improving daily throughput.
Overnight Soak – Greasy, heavily soiled items might require an overnight soak. Be certain you’ve got this feature.
Auxiliary Heat Options – When processing hospital items, the CDC recommends obtaining 165 F for 25 minutes. Some wetcleaning machines offer auxiliary heat options that boost water temperatures using steam or electricity. Be sure this is an option for any wetcleaning machine you are looking to purchase.
Ozone – Ozone gas can be injected into some wetcleaning machines as a form of additional chemistry. Ozone relaxes fibers, works best in cool water and sanitizes textiles by removing nearly all viruses and bacteria. Ozone sanitizes laundry with fewer chemicals, and no bleach, while using reducing hot water usage. If the use of ozone is in your future, be certain new wetcleaning machines are ozone compatible. ADC
Jeff Quail, co-owner of Poseidon Textile Care Systems®, has more than 30 years of hands-on industry operations experience in dry cleaning and wet cleaning. E-mail: jquail@poseidonwetcleaning.com.
American Drycleaner, June 2020 www.americandrycleaner.com
Tell us where you were born, grew up, and reside today?
“Born and raised right here in Bellingham, Wash., where my laundry is located. I went to college and grad school in Michigan, met and married my husband out there before moving back to Washington.”
Hobbies (that you’ll admit to)?
“I have wholesome hobbies like sewing, reading — actually I play Candy Crush — and knitting.”
What gets you excited at work?
“It is new every day. The good, the bad, the ugly keeps it interesting. Laundry is still easier than teaching high school. I am a believer in ‘know your limit and play within it,’ philosophy so I have surrounded myself with really great people who like to do what I don’t like, or I simply
don’t know how to do it with smarts. My best days are when I circulate amongst customers and chat up a storm.”
Lastly, tell us a secret (keep it clean) nobody knows about you?
“I was born and raised in retail! My father was one of 12; and nine siblings owned their own retail or service stores. My dad sold appliances with my uncle. That store is still in business. I have 65 first cousins and the vast majority own stores, businesses, practices or the like. Two cousins owned competing furniture stores down the block from one another. Not even kidding! My own siblings are or were selfemployed. Owning Brio Laundry and Brio Cleaners comes pretty natural — the late night calls, the double checking doors.... I grew up this way.”
ADC
(Do you want to take part in an Off the Cuff, or know someone who does? E-mail tburke@atmags.com.)
Colmac Industries of Colville, Wash., reports that Tom Murgatroyd has joined the Colmac sales team as an ap plications engineer.
Murgatroyd is a 2019 graduate of Washington State University with a Bachelor of Science in mechanical engineering, the firm says.
MurgatroydColmac Industries describes itself as a privately held company and the cornerstone of Colmac’s 200,000 square foot corporate office, manufac turing, and research and development campus.
Colmac Industries calls itself the worldwide leader in garment finishing equipment, automated soil sorting and counting for the laundry and manufacturer of heat pump water heaters for commercial and industrial applications.
Pilgrim Dry Cleaners, Minneapolis, is celebrating its 80th year in 2020 and describes itself as the, “Twin Cit ies favorite eco-friendly dry cleaner.”
Founded in 1940, it notes that it was established on, “The principle that our success is dependent on three key ingredients; Convenience, Quality, and Service.”
Founder Don Rosen’s commitment to family and com munity is still evident in the business today, it relates. Three generations, family-owned and operated, the op eration consists of 26 branch locations and more than 200 employees.
Also, it points out, Pilgrim Dry Cleaners became a woman-owned and operated business when Rosen’s daughter Bonnie Engler became CEO of the family busi ness in 2004. “We strive to improve and serve our custom ers and communities in the best way possible,” Engler says.
The company relates that Engler has maintained Rosen’s commitment to family and community over the years and its employee’s loyalty is very apparent. More than half of their 200 employees, it points out, have been
The late Don Rosen, who founded Pilgrim Dry Cleaners in 1940, shown with daughter Bonnie Engler and grandson Derek Engler. Three generations of family ownership have run this cleaners, now celebrating its 80th year. The cleaners says it is tentatively planning a company party for employees and their families in later summer, as well as offer ing their loyal clients many give-aways and opportunities to win prizes. (Photo by: Pilgrim Dry Cleaners)
with the company for over 10 years and 22 of those em ployees have been with Pilgrim for over 20 years.
Rosen founded the Pilgrim Cleaners Coats for Kids Pro gram in 1986 and has since donated over 422,000 coats to help Minnesota families in need, the firm says.
Pilgrim adds that it has multiple community drives throughout the year to give back to children in their local community including Costumes for Kids and Scouting for Uniforms as well as donating thousands to local charities in need.
“One of our secrets to success is that we are easy to do business with,” says Derek Engler, vice president, son of CEO Bonnie Engler, and grandson of the late Don Rosen, and now the third generation working for Pilgrim Dry Cleaners.
Pilgrim is tentatively planning a company party later this summer to mark its 80th year.
Girbau, a leading manufacturer in commercial and indus trial laundry equipment and services, located in Santa Fe Springs, Calif., reports it has appointed Serge Joris as its president.
“Joris has a solid professional career spanning over 25
years working internationally in critical roles at companies in the technology and industry sectors,” the firm notes.
“His appointment comes as a result of a drive to bolster the management team at Girbau and promote the com pany’s growth,” it adds.
Pere Girbau and Mercè Girbau, the company writes, the current CEOs and the third generation in the fam ily business based in Vic, Spain, will remain in their roles, focusing on de veloping strategy, new technologies, innovation and sustainability.
Girbau North America describes itself as the largest of 16 subsidiaries within the Girbau Group, which markets laundry products throughout 100 countries worldwide.
Lapels Dry Cleaning of Wilmette, Ill., with head offices in Hanover, Mass., notes that in January it concluded a successful Winter Gear Drive to benefit Connections for
the Homeless and the people it works with in the greater Chicagoland area.
Starting on December 20 and running through January 15, this cleaners accepted donations of new and lightly used winter gear. Items accepted included: men’s and women’s winter coats, hats, and gloves, it relates.
“We’re coming up on our one year anniversary as a Lapels Dry Cleaning store. So, we wanted to do some thing special,” says Fahim Zuberi, owner. “I can’t think of anything better than partnering with Connections for the Homeless to help provide some warmth to the homeless people in the communities they serve.”
Connections for the Homeless serves 2,100 people annually in 52 Chicagoland communities. Those ser vices include drop-in day-time shelters, overnight shelter, housing, eviction prevention and advocacy. This Lapels cleaned all the clothing collected, which will be dispersed among people utilizing Connections for the Homeless.
“Congratulations to Fahim and the folks at Connections for the Homeless on this very successful drive,” notes Kevin Dubois, CEO of Lapels and co-author of Entrepre neurial Insanity in the Dry Cleaning Business. “As one of our newer owners and first in Illinois, we commend Fahim on his efforts.” ADC
American Drycleaner, June
. . . . . . . . . . . .1
EzProducts International . . . . . . . . . .30
Fabricare Systems, LLC. . . . . . . . . . .11
iDryclean . . . . . . . . . . . . . . . . . . . . . .21
Iowa Techniques . . . . . . . . . . . . . . . . .7
Kleerwite Chemical. . . . . . . . . . . . . .30
Luetzow Industries. . . . . . . . . . . . . . .31
Newhouse Specialty Co. . . . . . . . . . .31
Olin Corporation . . . . . . . . . . . . . . . .19
Parker Boiler Co.. . . . . . . . . . . . . . IBC
Realstar . . . . . . . . . . . . . . . . . . . . . . .13
Redstone Payment Solutions . . . . . . .25
SPOT Business Systems . . . . . . . . IFC
The Huntington Group. . . . . . . . . . . .15
Transworld Business Advisors . . . . .30
Union Drycleaning Products . . . . . .BC
White Conveyors. . . . . . . . . . . . . . . . .5
2020 RATES: One- to five-time rate: $2.20 per word, boldface $2.30 per word. Minimum charge: $25.00 per ad. Call or write for our three- and 12-time rates. If box number is used, add cost of 5 words. Display classified rates are available on request. All major credit cards are accepted. DEADLINE: Ads must be received by the 1st of the preceding month. For example, for a June ad, the closing date is May 1st.
10 YEARS AGO. U.S. Payrolls Jumped the most in four years, with non farm employment rising 290,000 in April. Private employers added 231,000 workers, mostly in manufacturing, professional and business services, healthcare, and hospitality. Federal employment also rose, with the mass hiring of temporary workers for the 2010 Census. Nonetheless, unemployment edged up to 9.0%, as many long-term jobless started looking for work again.
35 YEARS AGO. Leather Trims Increasing. Many of the newest fashions incorporate suede and leather trim and decorative patches. The analysis laboratory at IFI has been receiving an increasing number of sweaters containing decorative leather trim of this type. In many of the articles received, the dye in the leather trim has bled and migrated into adjacent areas, resulting in self-staining. Many of the articles have care labels indicating that the garment should be cleaned using a leather cleaning process.
50 YEARS AGO. Do-It-Yourself Dresses. More and more women are making their own clothes. Rising clothing prices and complaints about “shoddy workmanship” have turned increasing numbers of women into seamstresses. In fact, it’s estimated that 40 million women make all or part of their togs. Old fogies? No, indeed! Teen magazine reports that 75% of its readers in the 12-to-17year-old age bracket are making their own clothes. Simplicity, reported to be the largest dress pattern
Reversible Switch for Slide Racks, reads the front cover of the June 1945 issue of American Drycleaner. The feature article inside looks at a dye operation and the owner relates that these switches allow garments to be pushed around to make more room.
maker, boosted its sales by 23% to $72.8 million last year. Do these facts and figures give you any diversification ideas?
75 YEARS AGO. Large Volume, Small Space! Reversible Switch for Slide Racks! That’s what it says on the front cover of the June 1945 issue. Inside the issue is the feature story with photos of a drycleaning operation in Milwaukee using the reversible switches. The article points out
that, “With metal pin swung up, hangers can be pushed under end of rack and along another.” The owner of the dye works business notes in the article that, “With these switches, inspected garments can be pushed around on various lines and there is always temporary space for garments somewhere. Thus a large volume can be handled in a relatively small space”
— Compiled by Tim Burke, EditorThe Parker Boiler tube bundle is extremely flexible and offers a long life with a 25 year warranty against thermal shock.
Each unit is Factory Assembled & Fire Tested. 4 years of Field Testing.
Extra heavy boiler tubes 1-5/16” OD. minimum 0.12” (11GA) heavy thickness steel, built for long term service life.
5:1 Burner Turndown Ratio. Digital Pressure Control. Boilers require access on two sides only. Reflex Prismatic Sight Glass. Up to 4” of insulation and 1/2” thick steam drum.