Late
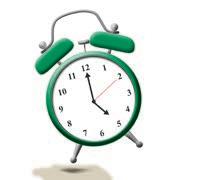
ELMSFORD, N.Y. — Unitex, a regional business with locations throughout the Northeast in the healthcare laundry industry, reports it has acquired United Linen Service, located in Lawrence, Massachusetts.
Terms of the deal were not disclosed.
“United has continually provided great service, value and support to its customers, and we are excited to build on that legacy as we welcome their customers to Unitex later this year,” says David Potack, president of Unitex.
“The coming together of these two companies is a natural evolution of Unitex’s expansion into the New England market, and we promise a seamless transition for customers with a continuation of extraordinary service.”
United has long served the healthcare industry in Massachusetts, New Hampshire and Maine, providing exceptional laundry services to area hospitals and extended care facilities, according to Unitex.
Unitex says it will be transitioning these customers over to its newly constructed 188,000-square-foot facility in Lawrence in late 2020. ALN
BY MATT POE, EDITORHI A O hemicals are necessary when it comes to the laundry process, and with the potential for personal and en ironmental harm, numerous regulations ha e to be followed regarding usage, storage and safety.
ederal re uirements are often top-ofmind with chemicals, so operators might o erlook local and state regulations.
There can be wide ariations in chemical storage and use regulations, but most general re uirements are based on national or international building and fire codes, says li ryderman, director-technical serices for laundry chemical pro ider urtler Industries Inc.
These regulations will specify the amounts of ha ardous chemicals that can be stored on-site the type of building, con-
tainment and fire protection re uired and any other storage and use considerations.
“ ery state is different and it would re uire that an operator research what standards their local state agencies follow and who those state agencies are,” says Vaughn inissian, director of operations for chemical solutions and water technolo-
gies company orchem orp.
“Local state federal re uirements are aried, and operators should always employ a bottom-up strategy, focusing on local re uirements first,” adds Ryan ontroneo, chief technology officer for chemical manu-
HI A O or laundry and linen ser ices that pick up and deli er goods, a properly functioning plant is only one side of the customer-ser ice coin.
The other side is the functionality of the deli ery fleet. If trucks aren’t running and the customers aren’t receiing their linens, the best processing in the industry won’t make a difference.
So, what makes the difference between a truck that runs and one that doesn’t leet maintenance.
“ leet maintenance, that’s the difference between trucks that are going on almost - years of ser ice, but they were built to be -year ehicles,” says enn lein, director of marketing and communications for walk-in an pro ider organ Olson in Sturgis,
In this issue, Eric Frederick writes about not turning a blind eye to employee behavior.
Looking for ways to stand out against the competition? The Panel of Experts offers ideas.
Keeping laundry trucks moving depends on scheduling, technology, communication
Experts share thoughts on how laundry operations can stay on the right side of local/state regulations(Image licensed by Ingram Image) Fleet maintenance keeps laundry delivery vehicles on the road, servicing customers—instead of in the shop or on the side of the road. (Photo: Morgan Olson)
SOUTH HOLLA D, Ill.
Laundry chemical specialist Gurtler Industries, located here, reports that Kevin McLaren, director of research and development for the company, recently presented a teleclass offered through Webber Training (www.webbertraining.
com entitled “Hospital Laundry and .difficile Spore Inacti ation,” in conjunction with course partner/ sponsor the American Reusable Textile Association (ARTA).
The teleclass focused on healthcare laundering, including factors that impact the antimicrobial properties of the wash cycle, features of the modern tunnel washers, the role of laundry bleach for stain removal
and microbial control, the factors involved in the selection of laundry chemicals, and the sporicidal properties of the modern laundry process.
The session presented a brief historical perspective of the healthcare laundry as it pertains to microbial removal/kill. There was a summary of many of the evolutions which have occurred within the healthcare laundry space during the period from 1938 to today.
Focusing on the current healthcare market, the spore-forming bacterium Clostridioides difficile was addressed as a pathogen of concern specific to healthcare-associated infections (HAIs), and a life-
form (spore former) that requires additional research.
A summary of ARTA’s research was presented as evidence that a tunnel washer process inclusive of peracetic acid bleach may be effective at achieving spore destruction. McLaren was the main researcher who de eloped ARTA’s recent investigation into the effect of certain laundry processes on C. diff.
Lynn Sehulster, Ph.D., of Environmental Infection Prevention LLC, and previously with the Division of Healthcare Quality Promotion, National Center for Infectious Diseases, U.S. Centers for Disease Control and Prevention (CDC), also presented
during the session.
Webber Training presents an international lecture series on infection prevention and control topics. Its objective is to share the latest and best information on infection prevention and control with the largest possible audience.
The teleclass was free and available to countries in the Americas, Europe, the Middle East and Asia.
Webber Training estimates that nearly 900 attended the live broadcast, and more than 4,500 have reviewed the online recording.
The teleclass can be viewed on the Webber Training site: https:// webbertraining.com/recordingslibraryc4.php ALN
Charles Thompson
Phone: 312-361-1680
E-Mail: cthompson@ ATMags.com
Donald Feinstein
Phone: 312-361-1682
E-Mail: dfeinstein@ ATMags.com
Bruce Beggs
Phone: 312-361-1683
E-Mail: bbeggs@ ATMags.com
Matt Poe
Phone: 866-942-5694
E-Mail: mpoe@ ATMags.com
Mathew Pawlak
Digital Media Director
Nathan Frerichs
Phone: 312-361-1681
E-Mail: nfrerichs@ ATMags.com
David Barbe • David Carter
Janice Ayers Davis • Nick Fertig
Deana Griffin • Steve Kallenbach
Edward McCauley
Main Phone: 312-361-1700 Fax: 312-361-1685
630-739-0900 x100 www.americanlaundrynews.com
LA HA , d. The U.S. Department of Labor reports that its Office of Federal Contract Compliance Programs (OFCCP) and Alsco Inc., a linen, uniform rental and facility services company, have entered into an Early Resolution Conciliation Agreement to resolve allegations of systematic hiring discrimination at the company’s facility here.
Alsco Inc. has agreed to pay $75,000 in back pay and interest to the affected applicants, to extend 13 job opportunities to affected applicants who expressed an interest in them, and review its selection process at nine other establishments located in six states.
“At Alsco, we celebrate and support employee di ersity,” says
John Jaggi, director of human resources and administration. “We build teams that reflect the rich variety of backgrounds, viewpoints, and abilities of our employees.
“This proacti e agreement with the Department of Labor affirms our commitment to maintain an inclusi e workplace.”
The Department of Labor says that preliminary findings of O P’s routine compliance evaluation show that from Jan. 1, 2018, through Dec. 31, 2018, the linen and uniform rental and facility services company discriminated against 43 African-American applicants for entry and mid-level operative positions in violation of Executive Order 11246, which prohibits discriminatory hiring practices by federal contractors.
While not admitting liability, Alsco Inc. agreed to an Early Resolution Conciliation Agreement and to enhance future compliance proactively.
“The Office of ederal ontract ompliance Programs’ arly Resolution Procedures are designed to enable federal contractors and the Department to work together to address and resolve issues of non-compliance efficiently,” says Office of ederal Contract Compliance Programs Director Craig E. Leen. “This agreement will pre ent
hiring discrimination practices from happening again at any of Alsco Inc.’s facilities,” adds Office of Federal Contract Compliance Programs Regional Director ichele Hodge. “We will work cooperatively with Alsco Inc. to ensure future compliance.”
Headquartered in Salt Lake City, Utah, Alsco North America has received federal contracts from 2017 through 2020.
These contracts covered services and products to multiple federal agencies, including the U.S. Department of Agriculture; Defense Commissary Agency; Departments of the Air Force, Army and Navy; U.S. Drug Enforcement Administration; U.S. Forest Service; Indian Health Service; and National Oceanic and Atmospheric Administration.
In November 2018, OFCCP issued a directive establishing Early Resolution Procedures, launching an initiative to promote early and efficient resolution of supply and service compliance evaluations. These procedures allow OFCCP and contractors with multiple establishments to implement corporate-wide compliance cooperati ely with O P’s regulatory requirements, and resolve identified issues efficiently.
In turn, contractors are exempt from future OFCCP evaluations for five years. ALN
American Laundry News (ISSN 1091-9201) is published monthly. Subscription prices, payment in advance: U.S. 1 year $46.00; 2 years $92.00. Foreign, 1 year $109.00; 2 years $218.00.
Single copies: U.S. $9.00; Foreign $18.00.
Published by American Trade Magazines LLC, 650 West Lake Street, Suite 320, Chicago, IL 60661.
Periodicals postage paid at Chicago, IL, and at additional mailing offices.
POSTMASTER, Send changes of address and form 3579 to American Laundry News, Subscription Dept., 440 Quadrangle Drive, Suite E, Bolingbrook, IL 60440. Volume 46, number 11. Editorial, executive and advertising offices are at 650 West Lake Street, Suite 320, Chicago, IL 60661. Charles Thompson, President and Publisher. American Laundry News is distributed selectively to qualified laundry and linen management and distributors in the United States.
© Copyright AMERICAN TRADE MAGAZINES LLC, 2020. Printed in U.S.A. No part of this publication may be transmitted or reproduced in any form, electronic or mechanical, without written permission from the publisher or his representative. American Laundry News does not endorse, recommend or guarantee any article, product, service or information found within.
Opinions expressed are those of the writers and do not necessarily reflect the views of American Laundry News or its staff. While precautions have been taken to ensure the accuracy of the magaine’s contents at time of publication, neither the editors, publishers nor its agents can accept responsibility for damages or injury which may arise therefrom.
The new Milnor MWB series washer-extractors are built to help decontaminate. Available in loading capacities of 60-200 lb. (26-90 kg), these hospital-grade machines are built with an aseptic pass-through barrier system that reduces the risk of cross contamination by separating soiled linen from clean linen. Automatic safety interlocks on two sets of doors maintain complete separation. Intuitive MilTouchTM controls offer unprecedented insight into your wash, utilizing full color graphic display and resistive touchscreen technology. Contact an authorized Milnor distributor or call 504-712-7656 to find out more.
A
s I write this letter, we’ e ust finished planning for American Laundry News
As a team, we mapped out ideas for print features, podcast topics and online industry coerage.
I belie e we’ e come up with some interesting and informati e ideas to help you try to maintain and grow your laundry business.
ou’ll notice that I used the word “maintain” first. With e erything going on in the world today, many businesses are doing e erything possible to stay open.
That means ha ing contingency plans in place.
Simply put, a contingency plan is a plan de ised for an outcome other than in the usual plan.
During our planning time, we talked about se eral contingency
From The Editor’s Desk MATT POEplans for articles and other content more than other years. ut contingency planning isn’t a new concept. ood business leaders are always keeping an eye on the ups and downs of the industry, looking ahead, trying to be ready for changes.
Of course, no one could expect a iral pandemic, economic recession and ci il unrest.
Still, we ha e to plan for the future, and in this issue, you’ll find articles to help your laundry business, like the chemical regulations and fleet maintenance articles on Page .
Or how about making your business stand out in your community Our Panel of xperts shares ideas starting on Page .
These articles and more are in this issue to help you plan for the future, near and far.
What contingency plans has your laundry operation established for the coming year What aspects of the industry do you think will be “normal” -mail your thoughts to me at mpoe atmags.com so we can share ideas and come together as an industry in upcoming issues of American Laundry News
That way, as many laundry businesses as possible can keep on keeping it clean. ALN
During my years of management experience, I had a number of employees who thought their way was the best way to get the ob done.
I first ran into this concept one summer when I was a seasonal worker at a chemical factory. I soon learned there was a right way to do things, a wrong way to do things and there was Senor Pla as’ way of doing things. oth the correct way and Pla as’ way got good results.
ut Pla as’ way used more hoses and more e uipment than the right way. anagement ust shook their heads, and because of a language barrier and good results, simply let him do it his own way. In this instance that was okay because either way was safe and got good results.
When I ran a laundry in Hunst ille, Alabama, I had a dri er with an excellent dri ing record and who got the linen deli ered on his assigned route faster than any other dri er.
y accident one day I ended up following him on part of his route, or at least I attempted to follow him after I recogni ed our truck while on an errand for my wife. I say attempted to follow him because he was going way o er the established speed limit and changing lanes in a rapid manner. His dri ing scared me.
The next day at the laundry my management team discussed what I had seen and shared our opinions with each other. The uestion of liability came up in the discussion.
If we know we ha e a dri er who routinely exceeds the speed limit and dri es in an aggressi e, almost reckless manner, what is our responsibility He had no tickets on his dri ing record and had not been in an accident in the past se en years.
One of my managers pointed out that by ha ing this discussion we were acknowledging an employee who was working in an unsafe manner.
HONOLULU and NORWICH, onn. Due to the continuing effect of the OVID- pandemic and subse uent go ernment restrictions, two laundry operations in the PureStar portfolio ha e filed to continue mass layoffs that began in arch.
A Linen Supply in orwich filed a Worker Ad ustment and Retraining otification Act WAR notice Sept. about layoffs of
employees who were temporarily furloughed around arch .
United Laundry Ser ices in Honolulu filed a similar notice Sept. regarding employees temporarily furloughed around arch .
In both filings, the companies share that the notices aren’t plant closures but expect the mass layoffs to continue for six months or longer, or be permanent.
“The company fully intends to
resume operations once it is deemed to be prudent to do so under pre ailing go ernmental restrictions and economic conditions,” representati es for both companies wrote in the WAR notices.
A Linen Supply and United Laundry Ser ices are both hospitality-related laundry operations, so the businesses ha e been hard hit by the global pandemic and associated tra el restrictions. ALN
ailure on our part to address this problem in a timely manner could lea e us all indi idually liable if the employee were to cause an accident and the company was sued for damages in court. Any good in estigator or lawyer would uickly learn that his manner of dri ing was well known in the company at all le els and management had done nothing to try and change his beha ior.
Another manager mentioned that by our failure to take action we would be encouraging other dri ers to dri e in a similar manner. We had openly praised him for his on-time and prompt deli eries. What kind of a message were we sending to our other dri ers
We decided to issue a formal warning to the dri er in uestion and ad ise him that we would not tolerate dri ing o er the speed limit or in a reckless manner. This warning went into his file and stated that a repeat incident would result in further disciplinary action.
Too often I ha e isited laundries were some employees are allowed by management to bypass certain safety regulations in an attempt to increase production. These shortcuts seldom lead to an immediate conse uence but greatly increase the possibility of an in ury or damage to the e uipment.
The same principle and points discussed with the dri er abo e also apply to this situation there should ne er be tolerance for beha ior that puts e uipment or people in danger. We simply cannot look the other way and hope for a good outcome.
If we tolerate bad or dangerous beha ior than in essence, we are appro ing of it and thereby increasing our liability. ALN
Eric Frederick served 44 years in laundry management before retiring and remains active in the industry as a laundry operations consultant. You can contact him by e-mail at elfrederick@cox.net, or by phone at 540-520-6288.
facturer UNX Industries Inc.
“These re uirements will likely in ol e the most audits wastewater and are specific to the community and the infrastructure human mechanical they ha e in place.”
Local state en ironmental regulations that go ern a chemical laundry application ha e to do with wastewater discharge, say asey Wahl, director of sales and marketing, and ohn oduru, director of safety, regulatory and uality, for Washing Systems, a provider of products and services to the commercial laundry processing industry.
ryderman says, “These restrictions are typically dri en by the site’s local geography, the municipality’s wastewater processing capabilities and degree of en ironmental awareness. The authority most often cited is the ederal lean Water Act and the ational Pollutant Discharge limination System PD S to restrict or eliminate certain chemicals in waste streams.
“A laundry situated on a large watershed, go erned by a small municipality whose main source of income is deri ed from tourism and outdoor acti ities will likely face more restricti e storage, use and wastewater discharge limits than a laundry located in a large city, with a well-de eloped water treatment system and many large and aried industrial operators.”
When building or mo ing into a new facility, attention needs to be gi en to the chemistry being employed in the wash process and its effect on plant water discharge, shares Peter errio, director of business de elopment for Pariser Industries, a manufacturer of specialty cleaning chemicals, and hea ier soil plants will necessarily ha e more effluent, chemical and soil by-products to contend with.
“States and municipalities ha e arious and specific approaches to super ision of wastewater along with allowable limits of potential contaminants in the waste stream,” he says.
errio adds that chemical suppliers are typically con ersant with local rules and should be relied upon to re iew their safety data and formularies with the operators to anticipate future regulatory in ol ement as it relates to the following
• Phosphate limits statewide.
• Local POTW publicly or priately owned treatment works pH and OD biological oxygen demand limits.
• The potential need for composite sampling and or routine effluent analysis reporting re uirements.
• Product flammability s. exist-
ing lease erbiage and building insurance provisions.
“ ost regulatory re uirements for handling and use in the laundry industry are based on OSHA guidelines for the handling of corrosi e or toxic chemicals,” shares Ste en Tinker, senior ice president of research de elopment, marketing, for urtler Industries Inc.
“Accordingly, local and state regulatory agencies defer to the federal standards. The critical information on chemical handling re uirements is included on the Safety Data Sheet SDS .”
The storage of chemicals onsite comes with the responsibility to complying with the local, state and federal emergency response regulations, shares Wahl and oduru. These re uire the business owners to prepare an annual in entory of all chemicals, which meet the threshold planning uantity TP set forth by the regulators.
At the federal le el, the TP is , pounds per year of ha ardous material or pounds of an extremely ha ardous material.
“Howe er, in certain states such as alifornia, the UPA ertified Unified Program Agencies program’s TP is pounds per year of any ha ardous material and pounds per year of extremely ha ardous material,” they share.
When it comes to processing textiles in a laundry, chemical use is not generally regulated, Tinker points out.
ick Wagner, principal technical account specialist at colab’s Research, De elopment and ngineering enter, says that there ha e been recent industry discussions about how to determine if a product can kill and or be effecti e against SARS- oV- , the irus that causes OVID- , in the laundry process.
According to the PA, “ leaning products that claim to kill and or be effecti e against iruses are pesticides and must be accepted and registered with the U.S. n ironmental Protection Agency PA or the agency prior to distribution or sale. These products may not be sold or distributed unless they ha e been properly tested and are registered by the PA.”
“To erify the products used in your wash process that claim to be effecti e against iruses like SARS- oV- , the irus that causes OVID- , it is critical that you ask your chemical endor to proide you with the PA registration number and PA appro ed documentation stating that the product is effecti e against the irus,” Wagner says.
“If they cannot pro ide PA documentation, it is likely that those claims ha e not been re iewed or accepted by PA and, therefore, may present a risk to consumers, and healthcare pro-
iders in particular.”
urthermore, he points out that e en if a product is registered through the PA, the product must specifically ha e a registered claim, or emerging iral pathogen claim, for the target organism in this case, the SARS- oV- irus. Wagner suggests referring to the PA’s list for products that are known to, and ha e been appro ed by, the PA to be effecti e against SARS- oV- , the irus that causes OVID- .
“After all, it’s all about brand protection, pro iding the right product with the right registration and kill claims, so that you ha e peace of mind that the product you are using kills OVID- ,” he says.
“ ost states ha e some regulations on the processing of healthcare-related textiles,” Tinker says. “These regulations can ary from state to state. Some states defer to enters for edicare edicaid Ser ice S and or D enters for Disease ontrol and Pre ention recommendations.
“Some of the regulations on healthcare textile processing re uire a minimum processing temperature and time. Some re uire the use of chlorine bleach for sanitation. ut with the increased use of lower temperature laundering and alternati es to chlorine bleach, many of these regulations are being reformed.”
Wahl and oduru say that chemical safety programs must include a written ha ard communication program, which addresses maintaining current SDS, container labeling, PP , emergency response plan and training.
“The chemical supplier must ensure that the information supplied to a laundry on each chemical must be current and up to date with all go erning regulations,” they say. “Laundry operators are responsible for assimilating that information into their own written Ha om’ program as a part of a company’s o erall safety program.”
SDS should be read thoroughly and completely, as they will contain detailed health and safety information, as well as storage, handling and any pertinent regu-
latory data, says ryderman.
“The re ised lobally Harmoni ed System HS adopted by OSHA makes reading SDS easy and intuiti e, with simple to understand phrases, pictograms and technical information,” he says.
“Sections - are likely the most important for an operator to re iew in-depth as these sections co er the most pertinent information for a user, such as the product ha ards Section , irst Aid measures to follow after an exposure incident Section , what to do in the e ent of a spill Section , how to store properly Section , and what type of personal protecti e e uipment or facility safety e uipment is necessary Section .”
Also, ryderman says SDS should be read and understood before recei ing the product to ensure the facility and staff are properly e uipped and trained to handle the material, as well as complying with any applicable regulations.
“They must pay attention to the ingredient list, comprehend corrosi eness, oxidation, fire safety, noxious nature of each ingredient,” inissian says. “Pay attention to compatibility of product with other products.
“ or example, acids and bleach cannot mix, alkali and sour cannot mix. They must study the sections of the SDS sheets that touch on these sub ects.”
ontroneo says a laundry operation should familiari e itself with the following uick cards and briefs from OSHA
• OSHA uick card on standard pictogram design and meanings www.osha. go PublicationsOSHA uick ardPictogram.pdf).
• OSHA uick card on SDS layout and section purposes www.osha.go Publications OSHA uick ardSafety DataSheet.pdf).
• OSHA in-depth briefing on SDS layout and section purposes www.osha.go Publications OSHA .pdf).
“These uick cards briefs gi e the operator an understanding of the purpose of each section and where to get specific infor-
mation,” he says. “All operators should ha e a familiarity with the chemicals within their plant before they are used in any operation.”
any factors influence whether cleaning chemicals can cause health problems, errio shares, and important matters to consider and where related information is found include
• hemical ingredients of the products label, SDS .
• How the cleaning product is being used or stored label, SDS and chemical endor training .
• Ventilation in the area where the cleaning product is stored or used label, SDS .
• mergency response should there be splashes or spills or contact with skin eyes label, SDS .
• Whether mists, apors and or gases are released label, SDS . errio suggests that e ery laundry should identify and appoint a ualified employee to administer to the operation’s chemical handling and emergency response.
The person should ha e experience or training in the following
• Proper use and storage of the chemicals in the laundry.
• acility protocols in the e ent of a chemical spill or related accident.
• Administration of SDS placement at point of use and in corporate files.
• An understanding and familiarity with the nature, contents and use of SDS.
ontroneo says that a laundry operator’s “first line of defense” in na igating local state chemical re uirements is its endor partnerships.
“Local re uirements are generally not aggregated in singular place online,” he adds. “Operators will need to search for a specific re uirement along with their county’s name and the associated regulatory body.”
“The local building, water and fire departments will be able to answer any uestions and some will e en pro ide a liaison to help ensure compliance with local laws and regulations,” shares ryderman. “It’s best to ha e an initial discussion at the inception of the relationship and regular dialogue between operator and endor with regard to regulatory compliance.
“And endors may want to ask uestions of their own to prompt discussion about what is needed at the plant.”
He shares that some uestions that may help both operator and endor understand the situation could include
• What type of training is needed to handle and use these products?
ichigan.
There’s a lot to fleet maintenance, and any ad ice could be ery “granular,” as lein puts it, but detailed checkpoints for fleet managers can be found in sources like the organ Olson’s ideo maintenance library. These checklist items can include lubrication points, safety checks, tire inspection, and more.
“We talking about maintenance, but the real word is preentati e maintenance P ,” he says. “Pre entati e maintenance is something I became familiar with in the a y, and the longevity of our vehicles is achieved by having a good preventative maintenance program.”
And a good preventative maintenance program comes from scheduling, technology and effective communication.
lein recommends scheduling maintenance items about e ery three months, depending on usage.
“When you ha e a personal package truck that’s making a hundred stops a day and using their roll-up door a hundredplus times a day, then the use rate is ery high,” he points out.
“Whereas in the laundry and textile rental industry, the usage may not be as high. So, the maintenance may not require every three months. They’ll establish that by doing an inspection.
“We are ad ocates of inspecting items like the rear roll-up door or the side sliding door, the bulkhead door, which is the door between the dri er’s area and the cargo area. Those are heavily used areas that we highly recommend. Inspection and maintenance are needed.”
Proper scheduling, and following the schedule, can be the difference between a laundry delivery arriving on time or the
truck breaking down on the side of the road, miles away from mechanical service and the customer.
“ ou’d rather take and replace the starter instead of taking the chance for it to fail in the field,” lein points out. “The same thing with headlights. Some operators change them every eight months, replacing both headlights. Their headlights are working, but they’re not waiting for a headlight to burn out before they replace it.”
randon Scantlen, corporate service director for Superior Linen Ser ice, head uartered in Tulsa, Oklahoma, agrees that scheduling preventative maintenance is key to keeping trucks on the road.
“We do, daily, we call them DVI tours, deli ery ehicle inspection tours,” he says. “We do daily walkarounds with our ehicles. It’s a little bit more than just walking around and kicking the tires, but it’s making sure that everything is operational.”
Scantlen says that since Superior leases its fleet ehicles, the company relies more on technology to follow a vehicle maintenance schedule.
“It’s similar to an oil change that you would get on your own personal ehicle, but leasing companies) schedule preentati e maintenance,” shares Scantlen. “We ha e scheduling apps through websites that we use with different lease providers, and they contact us.”
He says a lease company will e-mail Superior one month to six weeks ahead of time to let them know that maintenance is coming up, along with what trucks are on that schedule.
“That way we can coordinate and drop those vehicles off to get that preventive maintenance done,” Scantlen says.
or the DVI tours he mentioned pre iously, Superior has a checklist on its electronic devices used for routes.
“We use a logistics app, and it
has a daily record-keeping that we go through and make sure that there are no defects on a consistent basis with each vehicle that we’re dri ing,” shares Scantlen.
“If there is an issue, we can log it right there and contact the shop and get it in before its P is due if the need is there.”
He says that Superior has devices that tie into the electronic control module of each vehicle.
“If it recogni es a check engine light comes on, it’ll diagnose that, and it will actually send an alert to whoe er’s e-mail is tied to that ehicle,” Scantlen says. “That way we understand and know that there is a flag issue with that vehicle. Then we can contact the shop and speed up the process.
“This is all really ties into preenti e maintenance, but it also ties into eliminating or diminishing downtime as much as possible. We started using this particular device a little over a year ago, and it helps us diagnose a lot quicker than what we were doing before.”
or Scantlen, the key to effective fleet maintenance is communication.
“It’s trusting that whoe er is operating your ehicles, whether it be a route service rep or a truck dri er or whate er, is communicating issues when they occur and not letting it go,” he says. “That’s the most important thing.
“It’s getting your team to communicate with each other and then the shop or whoever is working on the vehicles.
That also means maintenance needs to communicate when a job is finished.
“That way you can you can have that peace of mind that it was done and move on to the next issue,” Scantlen says. “ ou have to have some accountability there and trust that they’re going to take care of those vehicles, whether you own them or lease them.”
ALN
ï Is my facility equipped with the proper PPE and facility safety equipment?
ï How will the containers be moved around the plant?
ï Where will they be stored?
ï Are there limits to the amount of chemical I can store on my property?
ï Are there limits to how much I can use or that can be in my discharge?
ï Are there any special reporting requirements for this product?
ï Is the facility permitted by the local wastewater treatment authority?
ï What are the permit details?
ï What is the local fire code in force?
ï Do I need to notify the local fire department of the quantity and type of hazardous materials onsite?
Common mistakes at the local and state level are usually incidental to “unknowns,” the items that an operator doesn’t e en know exist and is in iolation of, Cryderman says.
“An annual fire inspection may reveal that the operator is storing product in a room that is not designed to house chemicals, nor have the proper sprinkler density or en ironmental protections,” he shares. “A change in regulatory language could make a normally compliant use invalid overnight.
Or a revised SDS includes a new hazard and concomitant change in PPE use.
“Ignorance of the law does not absol e liability, and as such an operator should be proactive as part of their regulatory compliance tasks and partner with their endor, local authorities and regulatory bodies to stay abreast of the current regulations.”
One of the areas that laundries should consider is the regulations of the local fire department, according to Tinker.
“ ire departments will ha e requirements to provide information concerning the types and
amounts of hazardous (corrosive) chemicals that may be stored onsite, especially bulk containers,” he says.
“These regulations, permits and reporting requirements are generally fashioned after the PA ational ire Protection Association) standards. The regulations are designed to protect firefighters in case of an incident in the laundry that may cause a spill of a ha ardous chemical.”
“ ery operator should know their POTW and their state and local agencies that regulate hazmat storage,” inissian says.
A proactive approach where both the vendor and operator collaborate is the best method for achieving local/state requirement compliance, according to Cryderman.
“ hemical suppliers need to sit down with laundry operators and design the chemical program to be compliant with their facility and local wastewater regulations,” ontroneo says. “ enerally, a chemical supplier will have multiple programs for the same job in order to ensure that the operator is compliant while maintaining uality.”
“Always work with chemical vendors who can offer products that are compliant with local and state re uirements,” ad ises inissian. “ ind chemical endors that offer safer chemical storage, less ha ardous discharge, safer chemical handling, and other risk factors that can be mitigated.”
“A endor cannot supplant an operator’s en ironmental health and safety department, but they can provide technical information and help sleuth out local regulations and interpret the text,” ryderman points out. “An operator can also help by providing information such as wastewater permit details, building occupancy ratings and aspects of their health and safety programs.
“Together, they can help identify the requirements and determine the method to achieve compliance before any regulatory burden is unduly imposed.” ALN
Like it or not, prior to this year people outside of our industry rarely considered laundry services until and unless they needed them to support their own restaurant, bar, medical office, car dealership or hotel.
Now that people from all walks of life are sharply focused on cleanliness, hygiene and infection prevention, our industry has emerged not only as an essential service, but also as one that provides an important layer of protection for people’s health and safety things we’ e all known throughout our careers.
We all appreciate the attention on our industry, especially when it means the potential for more customers, but with this increase in attention comes the need for each of us to demonstrate our value proposition to both prospective and current customers.
The best way to stand out from your competition is to really and truly focus on ensuring that your present customers are not just satisfied, but that they are, in fact, delighted. A person is said to be satisfied when their minimum expectations have been met; one who is delighted has had their expectations exceeded.
The dictionary also notes that those who are delighted are those who are, “feeling or showing great pleasure.” reat pleasure With a laundry ser ice Absolutely
When you have customers who are consistently delighted, your sales and customer-service teams can ask for and follow-up on referrals. Unfortunately, however, statistics show that while a whopping 91% of customers would give referrals, only 11% of salespeople ever ask for them. That is a tragedy.
Whenever I teach a class on sales or customer service and give the above statistics I look out across the audience and see more than a few surprised and skeptical faces. When I inquire about their incredulity, the inevitable answer is a belief in the value of cold calling. And that suits me just fine because
that’s when I hit my attendees with another set of statistics.
To wit, I explain how a study from the Wharton School of Business found that the lifetime value of a referred customer is 16% higher than other customers, while the Journal of Marketing found that these referred customers are 18% more loyal.
In other words, while countless salespeople around the world slave away each day making cold calls, these calls have a success rate of just 1-2%, while companies whose salespeople rely on referred sales calls close with a 55-80% success rate.
All of this is to say that if your teams aren’t asking for and following up on referrals, they’re lea ing your money on the table.
While your sales and customer success teams are following up with your satisfied customers (they are doing that on a regular basis, right and using this time to collect referrals, they should also be collecting testimonials and positi e “proofs” that they can use on future sales calls.
These kinds of personal and demonstrable stories of your success provide objective and verifiable evidence of what makes your company great to do business with.
It is 2020 after all, so be sure to spread these good news stories as widely as possible using your social media channels and be sure to encourage (perhaps even incenti i e happy customers to lea e
positive reviews on the Internet in places like Yelp, Facebook and oogle Re iews.
Of course, referrals, testimonials and proofs are only possible if your company culture is one that prioritizes a focus on providing superior customer service, value, and quality to your customers.
One of my favorite books on this subject is Delivering Happiness, written by Zappos founder and former O Tony Hsieh. Hsieh’s book is a history of the founding of Zappos but it also reads like a manual on how to build a culture of serving customers.
Some might argue that Hsieh’s ideas and methods are too progressive or alternative for an industry like ours, but I would argue that this kind of thinking about building a company culture based upon customer service and, as the title says, delivering happiness, is exactly what is needed to ensure your ability to differentiate your company from those of your competitors.
According to Hsieh, “for individuals, character is destiny. For organi ations, culture is destiny.”
He further says, “The o. driver of our growth at Zappos has been repeat customers and word of mouth. Our philosophy has been to take most of the money we would have spent on paid advertising and invest it into customer service and the customer experience instead, letting our customers do the marketing for us through word of mouth.”
And if you’re still not con inced, bear in mind that Zappos was founded in 1999 and was sold to Amazon just 10 years later for $1.2 billion that’s billion, with a . Customer service is not just at the core of appos’ internal company culture, it is also front and center in all of the company’s internal and external communications and branding.
If you’ e e er done business with them, you’ e recei ed one of their iconic white boxes emblazoned with their company logo and the phrase, “powered by ser ice.” This message is ubiquitous at Zappos, including their famous four-week employee training program, every e-mail signature, signage, website and social channels. Service is their ethos.
What’s your company’s ethos and what does your company’s branding say about it Some of the most successful companies in our industry, any industry, are those that demonstrate their commitment to their culture through their branding.
Providing consistent and memorable branding not only builds awareness in your company, but it also helps convey your company culture, vision and value to current and prospective customers.
Those who have done it right have their branding on trucks, employee uniforms, customer invoices, company brochures, buildings and packaging.
Consistent, ubiquitous and
genuine messaging pervades these companies’ cultures and, therefore, in the attitudes of their employees.
As Tony Hsieh says, “ ood service comes naturally from the satisfied employees who embrace the company culture.”
So, if you want to stand out from your competition and see consistent and sustainable growth in your organization, analyze your company, its culture, its brand and its customer service through the eyes of your customers. The lessons you learn will continue to pay back for many years to come.
The wisest laundry manager I ever met and worked for would always say, “The laundry that does everything all laundries know they should be doing will be the most successful.”
There are no real secrets or big technological breakthroughs that will differentiate one laundry from the next. We are all producing basically the same linen as our competitors. Still, there are ways to separate your company from the pack.
Here are a few items that I believe a good laundry can do to stick out from the rest. It would not be accurate for me to say that our laundry always hits these marks, but I can say that we always strive too.
Professionalism. There are many procedures that a laundry can implement that may raise your costs. However, being professional every day does not cost you anything.
Are your employees professional when they interact with your customers How do they treat your customers when they are speaking with them, either on the phone or in-person Do your employees look professional when they are interacting with your customers
Packaging. How well are your carts packed Do you pack a cart with the end-user in mind or do you just think about putting the linen in the cart to ship
Bundles. How do your bundles
“How can I differentiate my operation from others in my area so that I truly stand out as a local laundry services leader?” Standing out from the competition(Image licensed by Ingram Image) Consulting Services David Bernstein Propeller Solutions Group, Park City, Utah Commercial Laundry David Griggs Superior Linen Service, Muskogee, Okla.
look? Everyone can put 10 sheets in a bundle, but not everyone takes the extra time to make sure the folds are neat and the bundles look uniform.
Certifications. TRSA, the association for linen, uniform and facility services, and the Healthcare Laundry Accreditation Council (HLAC) have several certifications that will show that your laundry is performing all the duties needed to produce a quality product.
I do not care how good you may think your plant is performing, when you start the certification process, you will discover some areas that you are deficient.
Route Performance. Are your trucks delivering when they are expected to deliver? Your customers should be able to set their watches by what time your trucks deliver daily.
your value.
Lastly, laundry services can be viewed as leaders by operating with positive economic, social and environmental outcomes as part of the framework for their business model. Keeping safety a priority benefits the company and its employees while communicating social responsibility to your customers.
Look for opportunities in every step of the service you proide from pickup and deli ery to the wash process to linen selection to identify opportunities to conduct business in a more sustainable manner.
Some industries have only two or three main suppliers. Our industry, like laundry operators, has many competing players. Differentiation is a key to survive and thrive in a crowded marketplace. Without differentiation, only the lowest priced players win
any business.
When we embarked on retooling our marketing messaging five years ago, the first thing we had to do was boil down who we were and why people bought from us.
It wasn’t enough to point out that we were one of the few domestic textile manufacturers still in existence. We had to understand why people were willing to pay a little more money for our products to get features like better durability, better service, a more socially and environmentally responsible supply chain, and faster deliveries from stocked goods and turn-around times on custom
products.
Then, knowing why people were willing to pay a little bit more to get our products, we had to develop marketing tools to explain these features to new prospects while at the same time “walking the walk” and staying true to our core reasons for being in business.
Therefore, I encourage local laundries to look critically at why people use your services, commit to executing your core differentiating factors, develop marketing methods and materials based on them, and school your salespeople on how to express them to current and potential customers. ALN
Ecolab strives for as a chemical supplier are allied to those of the laundry service providers we service as well. Through innovative solutions that deliver consistent quality, a customer-service model that instills confidence in the product while building relationships, and operating with ethical core values, laundry service providers can start to stand out as leaders in their field.
Regardless of the classification of linens being laundered, customers expect the product being delivered to them is reliably clean. This is achieved not just from chemicals applied in the wash process, but products and procedures followed throughout the entire plant and delivery trucks.
Staying on top of industry news and emerging trends can help keep you be at the forefront of industry recommendations and improvements. Marketing the products used and procedures followed to your customers helps them feel confident in what you are doing behind the scenes to ensure you are providing clean linens to them with every delivery.
Accompanying your product with superior personal service helps build a partnership between you and your customer. Route drivers directly interact with the customer and represent the company, so they should be experts in the product they are delivering and be equipped with the tools to address immediate customer concerns.
Listen to customer goals, concerns and shifting priorities to identify opportunities to meet their needs and communicate
Now more than ever laundry is mission critical. For small businesses, it’s the uniforms that represent the brand, the towels and linens that comfort the customers and the tablecloths and napkins that set the tables. Every day fabrics and textiles need efficient and superior hygienic cleaning – reputations depend on it. The all new Miele Little Giants washers and dryers provide superior disinfection and fabric care in a high-efficiency, compact system.
• M Touch Flex user interface (no buttons or dials)
• Heat pump dryer technology rated Energy Star Most Efficient
• 19-gallon drum size (18 lb. capacity)
• 49-minute Cotton 140° F program (with HW connection)
• 25-minute Express wash cycle
• 50+ washing programs; 5 customizable
• 35 drying programs; 5 customizable
• High temperature disinfection (up to 200°F)
Thomaston Mills produces a pastel color institutional sheet line.
Used in hospitals, assisted living facilities, camps and hotels, the company says these colorfast sheets are made to withstand the intense institutional launderings and last much longer than lower-quality sheets.
Venus Group says its Performance Twill® bed linens bring together hotel luxury and high performance, combining the softness and comfort of cotton with the strength, durability and easy care of polyester.
Monarch Brands says its Lulworth sheets feature SILVADURTM, an antimicrobial technology that uses silver ions to eradicate the presence of undesirable microbes from the surface of the sheet. SILVADURTM inhibits the growth of bacteria, yeast and algae on the fabric so sheets feel and look fresh longer.
To promote the use of SILVADURTM, Monarch Brands gained its Certificate of Compliance once testing found that after 50 wash cycles, SILVADURTM was still at least 99.5% effective in preventing degradation by microorganisms.
Geared toward the vacation rental and hospitality markets, each Lulworth SILVADURTM inner pack is equipped with tent-cards to inform guests that an antimicrobial formula protects sheets for guests’ peace-of-mind. Sheet care labels contain similar messaging and use color-coding to aid size recognition in the laundry.
In addition:
ï Lulworth SILVADURTM is approved as non-toxic by Oeko-Tex® International Standards.
• SILVADUR™ is registered with the U.S. EPA and supported under the EU BPR.
ï Sheet specs: T180, 60% cotton 40% polyester construction, made in Bangladesh.
ï Sheets will be in stock midNovember 2020.
www.monarchbrands.com 866-412-4414
Dyed in an environmentally responsible way at the Thomaston finishing plant in Easley, South Carolina, where all wastewater is recycled, the company says the line is a leader in sustainability.
Crafted into fitted sheets, flat sheets, pillowcases, draw sheets and other bed linens by workers at the main plant in Thomaston, Georgia, Thomaston pastels are available in four main colors and
The linens are a Venus-engineered patented blend of 100% premium spun cotton and textured polyester spun yarns: 70% cotton, 30% polyester.
Venus says that 100% cotton sheets are generally regarded as providing the greatest comfort and absorbency. However, durability of sheets is also an important consideration, especially for commercial applications in which sheets are subjected to high temperatures and harsh chemicals during laundering and ironing.
The company says the life cycle of a 100% cotton sheet is approximately 50 to 60 industrial launderings and ironings. Given many clients require sheets to be changed daily (e.g., healthcare, cruise ships, hotels, resorts) the replacement cost of sheets can bear a significant expense.
California Textiles says that its high-end Platinum Line goods are used in a variety of lodging projects.
The towel is made on dyna terry looms at its Pakistan Mill and has 12 yarn in warp and weft and 16 pile for a luxury hand feel.
The company says the line is “affordable luxury” and has a 2-inch diamond cam so it looks great on a rack.
The mill-direct bar mops in the line come in all yarn weights and stripes 20 different kinds, according to California Textiles.
cal suggestions needed.
www.catextiles.com 951-272-1200
Domestic Fabrics & Blankets offers a full line of healthcare bottom-fitted sheets in sizes that fit incubator up to the largest bariatric mattresses.
Domestic says its knit sheets are made from its patented Healthmesh® knit fabric that resists holes and runs, resulting in exceptional service life.
What’s more, Healthmesh® is available in a variety of bleachproof colors that allow for easy linen segregation and are resistant to staining or spotting that can occur when facilities introduce COVID-19 cleaning protocols that involve surface disinfecting with bleach.
stocked in dozens of standard sizes.
The company says it is able to create custom colors on demand with sufficient minimum quantities.
www.thomastonmills.com 877-474-3300
Venus Performance Twill® linens have been tested at SGS Labs for up to 200 industrial launderings, delivering a lifetime value that is four times longer than that of the average 100% cotton sheet, with no pilling, according to the company.
It adds that patented linens have been successfully commercialized in target markets for the comfort and feel of 100% cotton.
www.venusgroup.com 800-421-6599
The company adds that it only carries first quality, no irregulars mixed in, so a client can sell its customers on quality and service. Both products are 100% cotton grown in Pakistan.
California Textiles now also carries Green Stripe microfiber bar mops. It has 20 doubles, as well as 10 yarn.
The company has been a supplier to the commercial laundry and hospitality markets since 1990, stocking all items in California and Georgia. It also sells overdye products and will give any techni-
Domestic says its products are U.S.-made and sold through most healthcare linen distributors.
www.domesticfabrics.com 252-523-7948
ADI American Dawn offers its Marbella towel and sheet collections for customers.
Marbella towels are designed with 86% ring spun cotton and 14% polyester, for a balance of
durability with a soft, plush hand.
The company says the product has a beautiful dobby accent, with reinforced side hems and end hems. They are available in 10 size/weight options of wash, hand, bath, mat and pool.
Marbella T200 solid sheets are designed with 60% ring spun cotton and 40% polyester in percale, says ADI American Dawn. These luxurious sheets and cases feature a 3-inch hem and are available in eight options of flats, fitted and cases.
The Marbella T200 stripe features a tone-on-tone 9 mm in six options of flats and cases.
ADI American Dawn says it offers same-day shipping on most of its 16,000 stocked SKUs, from five U.S. distribution centers.
www.americandawn.com 800-821-2221
INC.
MIP offers its laundry, longterm care and senior-living partners the UltraKnit Optimum bedding line. These essential products benefit care recipients with their soft hand, enhanced comfort and a smooth, wrinklefree fit that virtually eliminates pressure points, according to the company. Laundering benefits include
MIP Inc.
quick drying times and reduced piling and snagging, meaning less lint and improved weight retention as compared to traditional cotton/poly and other 100% polyester sheets. Enhanced stain release performance keeps them looking clean and fresh for an extended time.
Offered as bottom sheets, top sheets, pillow cases and stretcher sheets, the UltraKnit
Optimum line of bedding solutions is a key component to any care experience, says MIP.
As a global supplier of healthcare textile solutions, MIP says it provides comfort and efficiency for the healthcare community and its people, based on the belief that real, vital impact exists within the seamless integration of science and caring around the world.
www.mipinc.com 800-361-4964
A division of Bed Bath & Beyond, T-Y Group & Harbor Linen offers a Softwear Plus Microfiber Sheet Collection.
The company says the wrinkleresistant, heavyweight sheet collection has been designed specifically to withstand the demands of institutional processing while staying white and crisp.
Featuring pillowcases that are smooth and slick on the inside for faster and easier on and off, T-Y Group & Harbor Linen says the Softwear Plus Collection is extremely durable, outlasting most traditional sheeting two to one.
Using less water in washing and shorter drying time, the company says the collection is economically and environmentally friendly.
T-Y Group & Harbor Linen says it provides great selection, quality and value. Multi-million dollar inventory and strategically placed distribution centers ensure convenient one-stop shopping, along with fast and reliable delivery.
Services range from design consultations to always-in-stock “anchor” products. The company says that’s why its products are found in leading hotels, resorts, spas, cruise ships and country clubs around the world.
www.tyharbor.com 305-805-8085, 856-435-2000
AL A DRIA, Va. TRSA, the association for linen, uniform and facility services, reports it has embarked on a Strategic hange Initiative focused on core deliverables that maximize member alue and best le erage TRSA’s resources for 2020 and 2021.
Based on a series of internal and external qualitative and quantitative research and interactive sessions with stakeholders, TRSA acti ities for the balance of 2020 and those expected to be budgeted for will include
• Ad ocacy including proacti ely encouraging increased use of commercially laundered reusable linens, uniforms and healthcare personal protective equipment (PPE) such as isolation gowns and scrubs for a more sustainable, hygienic supply chain.
• onitoring, responding, and educating federal, state, and local regulators and legislators to ensure a focus on continued recognition as a ritical ssential Ser ice.
• Hygienically lean and lean Green certifications.
ï Dissemination of information and training focusing on best practices for impro ing employee and customer safety and super isor training.
• Increased information-sharing through irtual networking communities, and print and digital communications.
“In reco ery from the pandemic, TRSA needs stakeholder sup-
port and assistance in identifying how the industry has changed, and will continue to evolve, over the next few months and years,” says TRSA hair im uik, Roscoe o., hicago.
“ ember and sub ect matter expert input provides invaluable information for review and discussion by the TRSA Strategic Planning ommittee and oard of Directors.”
TRSA began its Strategic hange Initiati e in early April
immediately following the stayat-home orders that shut down the economies in North America and across the world.
“We knew the impact on the industry would be significant but aried based on geography, market and product mix,” says TRSA President and O oseph Ricci, A .
“We immediately began our Strategic hange Initiati e that included 10 weeks of two-hour weekly facilitated discussions
between TRSA senior management and association sub ect matter experts S s co ering membership, events, certification, non-dues re enue, globali ation and other issues. These association colleagues and consultants shared valuable insight and perspecti e, often without charging for their time.”
These internal discussions with S s feed directly into discussions with external stakeholders including leaders of related organi ations including TRSA’s coun-
terparts in Europe and Australia. TRSA hosted market-sector and regional oom discussions and facilitated a Strategic Industry Town Hall in une with more than 120 linen and uniform serices professionals. These discussions led to the development of an Industry Looking Forward report indicating that sur i al and recovery are top of mind with both operators and supplier partner members suffering significant impacts to their bottom lines.
ear-term challenges ha e made it more difficult for both to focus on longer-term planning post- OVID- , such as
ï Increased costs and competition.
ï Decreased sales and workforces.
• onsumer shifts in preferences and overall economic fears.
• Increased regulations and standards.
Discussions concluded that promotion of linen, uniform and facility services to the variety of industries they serve can focus on three growth opportunities
ï Reusables as a more cost-effective and sustainable supply chain.
• leanliness standards that ensure the products are hygienically clean.
• ommercial ersus home or on-premises laundering OPL . Since mid- arch, TRSA has hosted nearly 50 webinars, town halls, roundtables and other acti ities, as well as benchmarking sur eys to facilitate the exchange
Standard Textile says its Aller ase® Professional Duraflex™ Zippered Mattress Encasement pro ides superior mattress protection, engineered exclusi ely for hotels to protect this aluable guest room in estment.
attresses collect bacteria, fungus, mildew, dust mite debris and other dirt particles o er their lifetime. Remo ing debris isn’t easy, but it is possible to pre ent accumulation.
The company says Aller ase®’s patented four-sided remoable top with Duraflex™ ase
was designed in partnership with executi e housekeepers, o ercoming installation and maintenance challenges other mattress protection products ha e. The Aller ase® Professional Duraflex™ ippered ncasement features
• An antimicrobial fabric finish that inhibits the growth of microbes.
• D Le el irus barrier, meaning iruses cannot migrate into mattresses.
• Temperature-balancing technology to keep guests cool and comfy.
• edbug and allergen barriers and a secure ipper to lock out pests, plus a waterproof layer to pro ide complete
protection.
• A -degree ip-off top for easy laundering and installation.
• orner anchor bands to hold encasement in place.
• Six-sided protection that fully encases the mattress.
• asy installation by one person.
• Options with additional plushness le els a ailable and interchangeable with a single Dura lex™ ase.
The company says pillow protector options with antimicrobial properties are also a ailable to shield and extend the life of a customer’s pillows.
Le eraging textile design, manufacturing, and laundry expertise, and its global infrastructure, Standard Textile says it ser es customers in the healthcare, hospitality, interiors, workwear and consumer markets worldwide.
www.standardtextile.com 800-999-040, 800-323-5246
eacon Linens says its Safe Ha en Linens line sheets and pillowcases is a solution for controlling unwanted bacteria, iruses and fungus in healthcare
and hospitality linens.
The company says the line is made in the United States with PA-registered sil er and PA-registered copper in a special way to produce a germ-free bedding en ironment. It does not affect the flora good bacteria on the skin, and the process is protected by three patents.
eacon Linens says the efficacy remains the same washing after washing. Tests comparing the same sheets before laundering and then after , , and commercial launderings show no change in efficacy.
The company shares that Safe
Ha en Linens
• Are comfortable.
• Are easy to care for. They can be washed in cold water and can be bleached chlorine or peroxide .
• Don’t shrink and the fitted sheet is made with a patented construction that guarantees not only the fit, but also that it will stay on the mattress until it’s purposely remo ed.
• Outlast typical sheets by about four times.
www.beaconlinens.com 828-689-5271
OSH OSH, Wis. As a college student, Craig Myatt spent the summers working as a bartender in a touristy North Carolina beach community. That’s when he noticed a need for clean linens within the vacation rental market.
“I started in a garage in ,” he says. “I’d rent sheets and towels, put them into a bedsheet package and then I’d deli er them to rental properties.”
In the years since, yatt’s Seaside Linen Rental Co. in Wrightsville Beach, North Carolina, grew exponentially.
Today, Seaside Linen rents beach chairs, umbrellas, bikes and baby strollers, in addition to more than , pounds of sheets and towels per week. ery piece of linen is washed, sanitized, ironed, folded and packaged in-house.
“As we grew, we encountered linen outsourcing issues that impacted our uality and efficiency,” says yatt.
So in , he brought all laundering in-house using fi e largecapacity washers and dryers. But with one problem down, another surfaced.
“We were hand-folding e erything and couldn’t keep pace with our wash production,” he shares.
To find a solution, yatt connected with en Royal, of Consolidated Laundry Equipment Inc. in harlotte, orth arolina, and Seth Willer of irbau Industrial, in Oshkosh, Wisconsin.
Per their recommendations, yatt in ested in a I ompact 5-in-One.
“I couldn’t afford a three-line ironer, nor did I ha e the space and utility setup for one,” he says. “When Seth put the ompact in front of me, it was a match made in hea en. It was affordable, ironed and folded fitted and flat sheets, and created consistent folds and stacks.”
Seaside Linen’s new ompact automatically feeds, irons, dries, folds and stacks up to three-sheets per minute or hour with a single operator more with two operators.
Additionally, it processes damp linens straight from the washer without need for dryer preconditioning by automatically ad usting ironing speed and temperature.
ecause it’s simple to operate, ust one employee is re uired to run the ompact during the offseason. During the busy season, two operators are used: one person feeds linens, while the other
off-loads the folded stacks.
Other perks beyond production uickly surfaced as a result of the ompact , as well. irst, because the ompact folds king sheets differently than twins, doubles and ueens, it simplified the sorting process for employees as they put bedsheet packages together.
Second, because the sheets are opened and iewed before feeding them into the ompact for processing, more stains are noticed and linens are re ected before they’re dispersed into the field impro ing efficiency.
All said and done, the ompact significantly streamlined operations, improved production, and enhanced the quality and presentation of Seaside’s product to the customer, according to Myatt.
“This created opportunities we didn’t ha e before,” he says.
Suddenly the bottleneck with linens was solved.
It also eliminates laundry pre-sorting and associated labor hours. Instead, a ariety of dried items can be fed into the machine one after another where they are automatically folded according to pre-programmed fold specifications, sorted and stacked. With the T- A I, Seaside Linen drastically boosted productivity and operates more efficiently.
“We would ha e ordered our second T- A I sooner but the OVID- pandemic hit and we were shut down for six weeks,” Myatt says.
Since we opened back up, our business umped .”
With his second T- A I now installed, yatt reflects on the impact of automation on his business.
Thanks to the new ironing and folding systems, Seaside Linen outputs a higher quality product, in significantly less time, using drastically fewer labor hours, according to Myatt.
of best practices for impro ing safety and operations during the OVID pandemic and access to resources to assist in recovering from its economic impact.
Thanks to members’ in estment and support, TRSA says it continues to fulfill its charge as an ad ocate for the industry at the federal, state, and local levels, most recently:
• aining nationwide recognition for the industry as a ritical ssential usiness.
• Defeating initiati es re uiring disposable products at restaurants.
ï Highlighting the supply chain sustainability of hygienically clean linens and uniforms.
In addition to addressing OVID impacts, TRSA says it continues to proactively pursue e ery opportunity to fulfill its mission to expand, protect and professionali e the nearly billion U.S. linen, uniform and facility services industry.
“ ow we had a bottleneck with towels,” says yatt. “We couldn’t hand-fold uickly enough and consistently enough to match the towels coming out of our washing line.”
He quickly invested in a machine recommended by Willer and Royal the I T- A I towel folder. He liked it so much, he installed a second T- A I ust fi e months after installing the first.
“When we opened back up, it was ero to hero in two hours. A lot of the owners of acation rentals, who had been doing laundry themselves, came to us because we hygienically sanitize linens.
“Looking at what I spent outsourcing, I anticipated a return on in estment of the e uipment in fi e years,” he shares. “ ow, I’d say my anticipated ROI is only three years.”
ALN
ALN
“Throughout the OVD- crisis, TRSA’s leadership, olunteers and staff ha e worked hard to consistently deliver timely, pertinent information and resources to help members survive and recover from the economic impact of business closures and promote the industry as a critical infrastructure business,” Ricci says.
To use the T- A I, an operator feeds dried towels into the towel folder, where they are automatically classified, folded and stacked at a rate of up to , pieces per hour.
“The T- A I immediately changed production flow,” says yatt. “We didn’t reali e how uickly it folds towels. It forced us to uit hand-folding. The T- A I only re uires one operator, is simple to feed, and has impro ed uality and consistency.”
PAT RSO , . . Pariser Industries, a manufacturer of industrial cleaning chemicals based here, reports that Peter errio has oined the company as director of marketing and business de elopment.
Scott Pariser, president, says that errio has more than years of leadership experience in the cleaning and sanitation chemical business focusing on the institutional and industrial markets.
He spent much of his early career with colab Inc., holding most sales and ser ice positions from territory manager to ultimately becoming ice president of sales for its e uipment care di ision.
errio has also held senior positions with se eral other chemical companies.
The director of marketing and business de elopment role is a new addition to Pariser, the company says. It is designed to pro ide continuing impro ement by supporting the o erall sales growth through business de elopment, process formali ation, ser ice deli ery and marketing enhancements.
LAS V AS PureStar, a pro ider of laundry ser ices and linen management to the hospitality industry in orth America, reports it has appointed rian Herington as chief executi e officer, and to the company’s board of directors, effecti e immediately.
“ rian has a pro en track record across multiple industries
with decades of leadership experience in both public and pri ate companies,” says ail andel, executi e chair of the PureStar board.”
Herington has more than years of industrial and commercial experience leading complex, technology-dri en businesses both regionally and globally.
He most recently ser ed as senior ice president and chief commercial officer of Uni ar Solutions, a publicly-traded, global distributor of chemicals and ingredients, following Uni ar’s ac uisition of exeo Solutions, where Herington ser ed as executi e ice president of chemicals from to . efore that, he was a region di ision head, Americas, at A and a president at Thomas etts. arlier in his career, he spent more than years in arious positions of increas-
ing responsibility in the United States, Latin America and urope at eneral lectric, SA I , a portfolio company of Sun apital, and Amoco hemical.
He has a achelor of Science from Illinois State Uni ersity and an A from Ashford Uni ersity.
“I am honored and excited to lead PureStar, which has continued to deli er for customers throughout the OVID- pandemic,” Herington says. “As the only national pro ider of linen management ser ices to the hospitality industry, the company has tremendous potential to accelerate growth and profitability.
“In partnership with ornell apital, management and our hard-working employees, I am eager to start building on our highly scalable customer alue proposition, le eraging our orth America footprint and executing our growth strategy.”
O TR AL IP Inc., a supplier of healthcare textile solutions, reports that hris Healey has oined its U.S. sales team.
Healey will be a sales consultant co ering the state of Texas and surrounding states.
IP says that he is an industry eteran, first spending time on the textile side as a salesman and a sales trainer, and most recently on the textile-processing e uipment side.
Healey li es in League ity, Texas, with his family. He is an a id outdoorsman and muscle car aficionado, but his real passion, when not at work, is de oting time to olunteer locally and abroad. ALN
Dave Balliet, director of customer relations for Hospital Central Services Cooperative (HCSC), offers his insights into enhancing customer service at all levels of a laundry operation.
Guest Paul Jewison, vice president of
neering at Healthcare Linen Services Group and general manager at Textile Care Services in Rochester, Minnesota, talks ways to keep a laundry operation clean.
PARTS, PARTS, PARTS
Huge stock of parts for most laundry equipment & boilers. Also traps, valves and lubricants. Overnight delivery. Steiner-Atlantic, 800-333-8883 Fax: 305-751-8390 parts@steineratlantic.com www.steineratlantic.com
In need of service and or parts for all your finishing equipment manufactured by BB&D, Lavatec, Washex, and Voss? Contact Michael @ 203-232-4004 or E-Mail me: mtenhave66@yahoo.com
Pellerin Milnor Corp. P.O. Box 400, Kenner, LA 70063 504-467-9591, Fax: 504-468-3094 www.milnor.com
Pellerin Milnor Corp. P.O. Box 400, Kenner, LA 70063 504-467-9591, Fax: 504-468-3094 www.milnor.com
Pellerin Milnor Corp.
P.O. Box 400, Kenner, LA 70063 504-467-9591, Fax: 504-468-3094 www.milnor.com
Pellerin Milnor Corp. P.O. Box 400, Kenner, LA 70063 504-467-9591, Fax: 504-468-3094 www.milnor.com
HI A O The Association for the Health are n ironment AH of the American Hospital Association, together with sponsor Tork, a hygiene product supplier, has announced the recipients of the n ironmental Ser ices VS Department of the ear Awards.
This year’s recipients of the VS Department of the ear Award are
• - beds ohen hildren’s edical enter, ew Hyde Park, ew ork.
• beds Uni ersity of Vermont edical enter, urlington, Vermont.
This year’s honorable mentions are
• - beds hildren’s Health Plano, Plano, Texas.
• - beds aro ont Regional edical enter, astonia, orth arolina.
The n ironmental Ser ices Department of the ear Award pro ides national recognition for the significant contributions made by an en ironmental ser ices department to the o erall patient experience and achie ing a healthcare organi ation’s mission.
It highlights the outstanding achie ements of a cuttingedge en ironmental ser ices team in maintaining high le els of performance in cleaning, disinfecting, infection pre ention, en ironmental sustainability and stewardship, technology use, patient satisfaction, education and training in critical areas.
All award recipients will be recogni ed in the September issue of Health Facilities Management maga ine.
behalf. This allows ig Table to target the most critical needs uickly throughout the community.
The type of support ig Table offers is personali ed for the recipient’s needs but can include mental and emotional health and life coaching, housing stability, medical and dental care, ob readiness, and addiction reco ery.
i en the extremely challenging circumstances that restaurant and hospitality workers are facing during the pandemic, Alsco’s Spokane ranch wanted to help support ig Table’s efforts.
“All of our employees here at Alsco work and li e in our local community,” says oey ink, general manager of the Alsco Spokane ranch. “Alsco has ser iced our restaurant customers for o er years in astern Washington. Supporting the folks who work in our local restaurants during these challenging times is an honor.
“Our hearts go out to the restaurant community and hope for a speedy reco ery. Alsco is here to help.”
priority. The certification also highlights employee satisfaction on their role within the company reinforcing HLS as a place for employees to succeed in their careers.
ISSIO , an. The American Reusable Textile Association ARTA oard of Directors reports it has confirmed the selection of officers and directors for - . Directors erry artin of Prudential O erall Supply and Duane Hou ener of American Dawn were recently appointed and appro ed as first and second ice presidents. ecil Lee of Standard Textile was elected and eff ourey of eorge ourey was re-elected as directors for - .
Lee is director of the healthcare laundry marketplace for Standard Textile orp., a ertically integrated manufacturer and distributor of institutional textiles and apparel, where his years of experience in managing healthcare laundries allows him to support customers and Standard Textile’s consultants in sales and ser ice to the industry.
arlier in the year, ARTA President abriel oardman appointed as directors icole rubich, West ichigan Shared Hospital Laundry W SHL and Hou ener.
rubich is a healthcare laundry executi e with extensi e experience. She pre iously worked for Sodexo and has ser ed as executi e director for W SHL since , increasing pounds processed from million to million pounds. In addition to oining ARTA as a director, rubich was recently elected secretary for the Association for Linen anagement AL .
Hou ener has o erseen alue-added solutions for American Dawn since . He pre iously ser ed as executi e director for W SHL and understands the industry from both sides as an operator and a supplier. The Army eteran is skilled in linen utili ation to reduce costs for both customer and laundry facility and has an excellent background in training, policy de elopment, and implementing benchmarking goals.
Longtime ARTA Director Scott Delin of ashion Seal Healthcare has assumed the role of legislati e director with the recent retirement of Howard ins. arlier last year, Da e alliet of H S stepped into the treasurer role for ARTA and ryan artsch of cotex was elected as director.
The complete roster for ARTA’s - oard of Directors includes
ST. HARL S, Ill. Healthcare Linen Ser ices roup HLS , which pro ides healthcare laundry ser ice through four companies and nine plants, reports that it has achie ed reat Place to Work® certification.
The reat Place to Work® program gathers and e aluates employee feedback and recogni es companies that ha e built “high-trust, high-performance” company cultures.
ï President abriel oardman of IP, ontreal, uebec.
ï Past President rendan O’ eill of London Hospital Linen Ser ice Inc., London, Ontario.
ï st Vice President erry artin of Prudential O erall Supply, San Diego.
ï
SPO A , Wash. Alsco Inc., a linen and uniform rental ser ices company, reports it has donated , to ig Table.
As its name suggests, ig Table is a nonprofit focused on helping workers in the restaurant and hospitality industry. These indi iduals are often society’s most ulnerable members.
As many as one in six working in the restaurant industry li e below the po erty line, and are ust abo e it double any other segment of the population, according to ig Table.
To help these industry workers, the organi ation pro ides a referral-based program, where a manager or colleague who recogni es an indi idual is in crisis can ask for help on their
“In our ongoing pursuit of best in class, we recogni e that our associates are our most important asset,” says oseph LaPorta, president O of HLS . “We will continue to work toward making this an organi ation that welcomes di ersity, collaboration and inno ation.”
According to the reat Place to Work® sur ey, of the company’s employees say it’s a great place to work, and say they feel like they make a difference. Also, say that when they look at what they’ e accomplished, they feel pride.
In terms of management, say they can take time off when necessary, and belie e management would only lay off employees as a last resort.
inally, of HLS employees indicated on the sur ey that when an employee oins the company, they are made to feel welcomed.
The company says the certification demonstrates its strong commitment to making the employee experience a
nd Vice President Duane Hou ener of American Dawn, ompton, alifornia.
ï Secretary Ste en Tinker of urtler Industries Inc., South Holland, Illinois.
ï Treasurer Da e alliet of H S , Allentown, Pennsyl ania.
ï Director ryan artsch of cotex, Abbotsford, . .
ï Director eff ourey of eorge ourey, ontreal uebec.
ï Director Daniel elac of annegiesser, ontreal, uebec lea es board Dec. .
ï Director icole rubich of W SHL of rand Rapids, ichigan.
ï Director ecil Lee of Standard Textile, incinnati.
ï Director d c auley, United Hospital Ser ices Inc., Indianapolis.
ï Director Dan Sanche of edline Industries Inc., undelein, Illinois.
ï Legislati e Director Scott Delin of Superior Uniform roup, Seminole, lorida.
ï xecuti e Director ancy enkins of enkins Integrated arketing, Lee’s Summit, issouri. ALN