Late
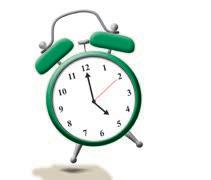
ST CHARLES, Ill. — Healthcare Linen Services Group (HLSG), a portfolio company of York Capital Management’s private equity group and a provider of healthcare laundry services in the Midwest and Central United States, reports it has acquired Reino Linen Service.
The acquisition expands HLSG’s operations into the Ohio and Michigan markets, expanding its customer base and adding automated facilities that provide additional capacity to its existing footprint throughout the Midwest. Terms of the transaction were not disclosed.
Founded in 1943, Reino is an independent healthcare linen solutions provider that has the capacity to process more than 150 million pounds of laundry annually for hospitals and healthcare facilities.
Daniel Darr, president of Reino, will continue in a key leadership role as the vice president of strategy for HLSG.
Following this transaction, HLSG now operates 14 state-of-the-art processing plants across five premier regional brands.
BY MATT POE, EDITORCHICAGO — Many changes have taken place in the laundry and linen services industry over the past few years.
And many challenges have appeared and are ongoing.
So, what is the state of the industry today? What could happen in the future? Where is the industry strong, and where does it need to improve?
American Laundry News communicated with three operator representatives to find out their insights, hopes and concerns for their businesses and the industry.
Those involved in the discussion included Bryan Bartsch, president of EcoTex Healthcare Linen Service in British Columbia, Ontario, Washington, New Mexico, Oklahoma, Nebraska, and Iowa; Eric Yeakel, vice president of administration for Hospital Central Services Cooperative Inc. serving New York, New Jersey, Pennsylvania,
The past few years have been challeng-
ing, to say the least, and the challenges continue. Start by sharing a brief look at the status of your business today.
BARTSCH: Ecotex has experienced
DURHAM, N.C. — EverGreen Linen Solutions is led by a management team of three women with more than 50 combined years of experience in the industry.
Minashia Haynes, Sam DiGiulio and Rose Batista joined EverGreen in 2020 and helped to open EverGreen’s Durham laundry plant.
Haynes, EverGreen’s general manager, has worked in the linen industry for 17 years. Formerly regional co-workers with Haynes at Angelica, EverGreen CEO Jeff Hoffmann and COO Leon Johnson had a chance encounter with her in a hotel lobby in Raleigh years after last working together.
With plans to establish an EverGreen laundry in Durham, Hoffmann
Healthcare and mixeduse facility representatives share their soil sort procedures.
In this issue, the Panel shares ways for laundries to ease employee stress, burnout.
Maryland, and Delaware; and Asit Goel, vice president of marketing for UniFirst, one of the largest workwear and textile service companies in North America.COO says leadership team chosen because ‘they were the most qualified individuals for the role’
Operator representatives offer insights into the issues facing the textile care industry, what’s coming(Image licensed by Ingram Image) EverGreen Linen Solutions’ leadership staff (from left): Rose Batista, plant manager; Sam DiGiulio, corporate controller; and Minashia Haynes, general manager. (Photo: EverGreen Linen Solutions)
ALEXANDRIA, Va. — TRSA reports it hosted a star-studded 109th Annual Conference in Nashville, Tennessee, from Sept. 13-15, featuring keynote addresses from a well-known country singer, songwriter, and actor and a former major league pitcher, in addition to industry-specific education sessions for both operator members and supplier partners.
The three-day confab kicked off with a Supplier Partner Council meeting on Sept. 13. Supplier partner members were given two opportunities to hear the latest prognosis for the PFAS regulatory burden that linen, uniform and facility services are likely to face.
Suppliers first heard about this issue on Sep. 13 at the Supplier Partner Council meeting and again in a conference general session a day later.
Following a networking reception to close out the opening day of the conference, the action continued the next day with a morning keynote session titled “The Stories Behind the Songs: Chronicling the Journey through Music and Narrative” by Charles Esten, a singer, songwriter and actor best known for his role as the country singer Deacon Claybourne on the ABC/ CMT hit drama “Nashville” from 2012-18.
Industry-specific breakout sessions included:
• Bulletproof Selling: Building Sales Systems in the Textile Rental Industry, Shawn Rhodes
• The Elements of Value, John Brandt, The MPI Group
• Three Things You Can Do to Enhance Trust and Teamwork in Your Organization, Dan Gonder, Strategic In/Sight Partners
• The Value Proposition of an Effective Training System, Ian Bigelow and Keith Ware
During lunch, Kevin Schwalb, TRSA’s vice president of government relations, gave attendees an update on legislative and regulatory issues. Joining him was John Schaffer, EEC Environmental, who talked about PFAS regulations and their expected impact on the linen, uniform and facility services industry.
The conference closed on Sept. 15 with the Annual Membership Meeting where its new board members for the upcoming year were announced.
Jim Kearns, executive vice presi-
dent and chief financial officer, Alsco Uniforms, was elected chair of TRSA’s Board of Directors.
“I am grateful for the opportunity to serve as TRSA chair,” Kearns said. “Over the next two years, I’m going to focus on advocacy and the sharing of best practices to boost the industry as a whole.
and Board Recognition Dinner.
During the event Brian O’Neil, president of California Linen Services, received the TRSA Operator Lifetime Achievement Award; and Kevin Minissian, former president and CEO of Norchem Corp., was posthumously awarded with the TRSA Maglin/Biggie Lifetime Achievement Award.
TRSA acknowledged Noel Hammer Richardson as she completed her two-year term as Board Chair. The selection of a preferred charity by an outgoing TRSA chair is a tradition at the association.
Publisher
Charles Thompson
Phone: 312-361-1680
E-Mail: cthompson@ ATMags.com
Donald Feinstein
Phone: 312-361-1682
E-Mail: dfeinstein@ ATMags.com
Bruce Beggs
Phone: 312-361-1683
E-Mail: bbeggs@ ATMags.com
Matt Poe
Phone: 866-942-5694
E-Mail: mpoe@ ATMags.com
Mathew Pawlak
Nathan Frerichs
Phone: 312-361-1681
E-Mail: nfrerichs@ ATMags.com
David Barbe
Janice Ayers Davis • Nick Fertig
Deana Griffin • Cecil Lee Edward McCauley Jim Slatcher
Main Phone: 312-361-1700 Fax: 312-361-1685
www.americanlaundrynews.com
“Our industry provides an essential service, and we need to safeguard the trust of our industry customer base and help solve problems with our products and services.”
A closing keynote address was given by R.A. Dickey, a former major league pitcher and Cy Young Award Winner with the New York Mets. Dickey also is a New York Times best-selling author of “Wherever I Wind Up: My Quest for Truth, Authenticity and the Perfect Knuckleball.”
The final day also included an Economic and Industry Update from Andrew Wittmann of Robert W. Baird & Co. and an Industry Legends Panel Discussion. The latter session featured Robert Fesmire Sr., Ellis Corp.; Bill Mann, TRSA; Steve Larson, Alsco Uniforms; and Michael Potack, Unitex. CEO Joseph Ricci moderated the discussion.
The conference concluded with the TRSA Lifetime Achievement
TRSA members were encouraged to show their appreciation by donating to Richardson’s charity of choice, Women’s Empowerment, whose mission is to enable women who are experiencing homelessness to gain the skills they need to get jobs, maintain healthy lifestyles and regain homes for themselves and their children.
As TRSA’s first female chair, Richardson’s choice was particularly appropriate. Shasta Linen Supply pledged to match up to $10,000 for any money donated to the organization in honor of Richardson up to Sept. 30.
In addition to the education and awards, the 109th Annual Conference also featured several networking events, including tours of Studio B Recording Studio and the Country Music Hall of Fame, an interactive Goo Goo Cluster Candy Challenge and a tour of the worldfamous Grand Ole Opry.
The 110th Annual Conference will be held in Naples, Florida, at the Ritz-Carlton Golf Resort Oct. 10-12, 2023.
American Laundry News (ISSN 1091-9201) is published monthly. Subscription prices, payment in advance: U.S. 1 year $50.00; 2 years $100.00. Single copies: U.S. $10.00. Published by American Trade Magazines LLC, 650 West Lake Street, Suite 320, Chicago, IL 60661. Periodicals postage paid at Chicago, IL, and at additional mailing offices.
POSTMASTER, Send changes of address and form 3579 to American Laundry News, Subscription Dept., 125 Schelter Rd., #350, Lincolnshire, IL 60069-3666. Volume 48, number 11. Editorial, executive and advertising offices are at 650 West Lake Street, Suite 320, Chicago, IL 60661. Charles Thompson, President and Publisher. American Laundry News is distributed selectively to qualified laundry and linen management and distributors in the United States.
© Copyright AMERICAN TRADE MAGAZINES LLC, 2022. Printed in U.S.A. No part of this publication may be transmitted or reproduced in any form, electronic or mechanical, without written permission from the publisher or his representative. American Laundry News does not endorse, recommend or guarantee any article, product, service or information found within. Opinions expressed are those of the writers and do not necessarily reflect the views of American Laundry News or its staff. While precautions have been taken to ensure the accuracy of the magazine’s contents at time of publication, neither the editors, publishers nor its agents can accept responsibility for damages or injury which may arise therefrom.
When Milnor introduced PulseFlow® technology, CBW® washing was thrust into the future. The idea of balancing time, temperature, mechanical action and chemistry was missing one critical piece of the pie – DILUTION through the efficient use of water.
PulseFlow combines the innovative RecircONE® fast wet down and chemical immersion in the first module with standing bath washing in every spacious process module. Thorough and efficient dilution occurs by way of intermittent high velocity counterflow rinsing and traditional True Top Transfer.
The result is hygienically clean linen using less water (as low as 0.3 gallons per pound/2.5 liters per kilogram) and less energy as proven time and again by hundreds of PulseFlow tunnels in a variety of laundry applications worldwide.
Contact an authorized Milnor distributor or call 504-712-7656 to find out more.
www.milnor.com
T here are many “moving parts” that come into play to run a successful commercial laundry operation.
This issue of American Laundry News features several important elements of success.
On Page 1, you’ll find the beginning of an important dis cussion with several operator representatives about the status of their businesses, challenges and successes, and what they see for the future.
From The Editor’s Desk MATT POEAnother key to laundry suc cess? Soil sorting. Turn to Page 10 where you’ll find out
CINCINNATI — Uniform, prod ucts and services provider Cintas Corp. reports it recently presented a total of $50,000 in financial awards to four Cincinnati-area charitable organizations.
Company representatives made the presentations during the AllStar Skills Challenge presented by Cintas, one of several pre-event activities focused on women’s lead ership that were held on Sept. 6 at Cincinnati’s Kenwood Country Club ahead of the LPGA Kroger Queen City Championship present ed by P&G.
Cintas Senior Vice President and Chief Marketing Officer Bob Mitchell and Cintas Director of Marketing Communications Monica Dressing were on hand to present awards to:
• First Tee of Greater Cincinnati/ Northern Kentucky ($20,000).
• Dress for Success Cincinnati ($15,000).
• Fernside Center for Grieving Children ($10,000).
• SCRATCHgolf via First Tee of Greater Cincinnati/Northern Kentucky ($5,000).
“Philanthropic organizations are
how a healthcare laundry and mixed-use operation sort soiled goods safely, efficiently and costeffectively.
Leadership is important, of course, and on Page 16 you can read about new leaders at two industry associations and a sourcing network.
And nothing would work without employees, and on Page 12, our Panel of Experts shares how to help ease their stress and potential burnout.
It’s all important to help keep it clean, everybody!
the true all-stars of our communi ties, and these groups are tremen dous representatives of both the great work being done in our area and the amazing impact charities can have in a region,” Mitchell says.
“Cincinnatians have a long tradi tion of supporting one another and we were thrilled to have an opportu nity to recognize these groups with awards at the LPGA’s All-Star Skills Challenge. We hope these funds can help further the direct impact that First Tee, Dress for Success, the Fernside Center and SCRATCHgolf have in the Cincinnati area.”
Cintas says it was a proud cor porate sponsor of the pre-event activities, which focused on wom en’s leadership and empowerment, and included the All-Star Skills Challenge presented by Cintas, a private clinic and a Q&A ses sion with LPGA Legends Annika Sorenstam and Amy Alcott, as well as the morning’s Women’s Leadership Conference.
Additionally, Cintas is a found ing corporate partner of “Queen City Game Changers,” a new wom en’s leadership initiative tied to the event. The goal of the program is to
help prepare, support and advance 130 area females succeeding in busi ness, education and sports indus tries into executive leadership posi tions.
“The LPGA’s vision to bring female leaders together to learn, share and network will have a last ing impact on our region long after the tournament ends,” says Max Langenkamp, Cintas senior vice president of human resources and chief diversity officer.
The Queen City Game Changers’ inaugural class is represented by diverse women from top local companies, entrepreneurial orga nizations and the various Greater Cincinnati chambers of commerce. The eight-month program includes opportunities for both practical experience and mentorship from Cincinnati-area senior executives and business leaders.
“We’re eager to witness our female leaders benefit and grow from this tremendous program, and we look forward to identify ing opportunities to further sup port them and their efforts to lift our company—and region—even higher,” adds Langenkamp.
One of the success stories our industry has made over the years is our reduction of water used to wash a pound of laundry.
For the most part, the washrooms where the operators wear rubber boots all day due to the water pouring out to the washers are gone.
I know we had a facility where when we first started tracking water usage, we were almost five gallons per pound! Wow. We were able to get that facility to under .60 gallons per pound over the years.
As much progress our industry has made, there are still improve ments to be made. I think it is our industry’s obligation to constantly work at being better custodians of our environment, in particular our water.
There are three levels of water reduction laundries can take. Some of the fastest water savings will cost a company zero investment while others may take a substantial invest ment. I will briefly comment on each one:
AS MUCH PROGRESS OUR INDUSTRY HAS MADE, THERE ARE STILL IMPROVEMENTS TO BE MADE. I THINK IT IS OUR INDUSTRY’S OBLIGATION TO CONSTANTLY WORK AT BEING BETTER CUSTODIANS OF OUR ENVIRONMENT, IN PARTICULAR OUR WATER.
1. Be a better operator. This may sound simple, but water waste is everywhere. Start by taking a water reading at the end of the day and then again at the beginning of the following day to ensure you have no valves leaking. A steady leak that you may not hear during the day can cost you .25 gallons per pound or more during your offproduction hours.
Check the water controls on your washers. Some washers are very prone to getting clogged up causing the washer to use more water since it is not properly sensing the water level.
Check your washer drains for leaks. Leaky drains can substan tially raise your water usage.
Steam system. Steam return should always be captured and sent back to your boiler feedwater tank to be reused. Allowing steam traps to discharge into your wastewater pit is a waste of resources.
Excessive steaming in the washroom. Steaming in your washer takes more water. Try and preheat your water as close as possible to your final wash temperature.
Restrooms. Upgrade your toilets for low water usage per flush and ensure they are not leaking.
2. Work with your chemical provider.
You can work hand-in-hand with your chemical provider to reduce your water usage. This takes time and you must work together.
Unless you have chemistry training, going off on your own and working on your formulas can usually damage linen or no longer clean linen. A few steps that can be taken in the wash area:
Lower rinse water levels. This can be a risky step. Rinse water is helping flush out debris or lower the pH of the product. Perform this step when your chemical provider is present to test the water after the change.
Remove rinses. Chemical providers have made great strides with their chemicals that allow for the reduction of rinses used. This is done if your alkalinity isn’t so high in the wash zone, which allows for the removal of rinses that were there to reduce the pH.
These rinses are also present to remove debris so removing them can be a little tricky. I couldn’t tell you how many times a vendor says they can remove these rinses but then puts them back within six months due to poor wash quality.
Watch your rewash. It doesn’t do any good to have a fast wash formula and then rewash 25% of the linen.
A good wash formula that cleans your linen the first time through is always cheaper in the long run.
3. Mechanical Reuse.
There is no better method of lowering water usage than reusing
growth during the pan demic, adding new accounts and new prod ucts. We have also expe rienced a 6% volume erosion from current customers who restrict ed the hospital capacity to manage COVID and are dealing with their own staffing shortages. I expect demand for our reusable products will remain strong into the foreseeable future.
The current challenge we are all facing is with staffing. The back bone of the laundry industry is the large workforce that serves customers each day.
Currently, all laundry operators are challenged with the low work force participation and increased wage rates. Right now, there are two jobs available for every person who is seeking employment and the workforce continues to shrink as baby boomers retire.
The underlying supply of workers needs to be addressed. Increasing eligibility and immigra tion are both immediate ways that the government could improve the workforce situation and help businesses fill the many vacant service sector jobs.
The laundry industry requires more access to service sector workers and further plant auto mation into the future.
YEAKEL: Hospital Central Services Cooperative has been, and continues to be, a leader in healthcare linen rental services throughout the MidAtlantic region of the United States. We differentiate ourselves through our top-tier quality and service pro
grams, which are instilled in our mission statement of “Partnering Together to Enhance the Patient Experience.”
We have five linen process ing plants operating in Pennsylvania, New Jersey and Maryland. Our new est plant in Camden, New Jersey, was built during the height of the pandemic through our partnerships with JENSEN and ARCO/ Murray.
We currently serve 135 acute care hospitals and over 2,200 outpatient centers through our Ambulatory Care division.
GOEL: UniFirst continues to have stellar performance in terms of overall revenue and contin ues to be financially strong with no debt. This means that we can invest in the future and in con tinuing to build out our service capabilities for our customers.
Yes, the last few years have been challenging, first with the COVID19 pandemic and now an increas ingly inflationary environment. We are thankful to thousands of our team partners, who continue to deliver for their customers, their teams, and their communities.
Our main focus is and will always be to be there for our customers as they build their businesses in these challenging market conditions.
What crisis has been most challenging for your operation to over come? Why?
BARTSCH: Early in the pandemic we faced immediate labor shortag es because of the uncer tainty related to safety. That initial fear was replaced by countless government programs that made employment situations worse for essential ser vice companies.
A survey conducted by the U.S. Chamber of Commerce reported that 70% of the respondents who used employment insurance pro grams during the pandemic made more money by not working. Currently, the low unemployment has made it difficult to fill open positions and we are seeing greater quit rates.
Parts and equipment availabil ity issues have been challenging over the past six months from some of the key equipment.
YEAKEL: This is difficult to answer because there are so many different variables at play for all of our operations. I’ll focus on the human resources piece.
We went through a “Great Resignation” with some of our local office staff while enduring months without anyone filling out applications for our open pro duction positions. There was a
severe lack of CDL-A drivers and a very small pool of mechanics with acceptable qualifications.
Most of these jobs are union positions, so to be competitive with wages, we needed to open up collec tive bargaining agreements (CBAs) and renegotiate.
GOEL: In my opinion, the impact of the pandemic has been the most challenging crisis. Virtually every business on Main Street across North America was affected. The pan demic and the resultant supply chain issues hit every business hard.
This reminded us that because we serve essen tial businesses and work ers, be they vaccine manufacturers or be it Aunt Amelia’s trattoria down the street, the work we do here is essential because our cus tomers depend on us for critical uniforms and services to do what they do best.
What steps did you take to overcome that challenge?
BARTSCH: We have needed to be resourceful in finding sources to hire staff. Ecotex carried larger stocks of parts and linen inventory to help mitigate delays that impact our customers.
YEAKEL: We viewed the wage piece as an opportunity to extend union CBAs, keeping most lan guage discussions out of the nar rative and focusing on increasing the hourly rate.
We were successful with this strategy. The employees had the immediate gratification of a wage increase, and we avoided negotiat ing more vacation and personal time, among other things.
We started getting more appli cants through the door via wordof-mouth and referrals, which was a win-win situation.
GOEL: We remained success ful as a business throughout the
entire pandemic and remain suc cessful today as we are navigating a post-pandemic world.
This is because we continue to listen to the business needs of our customers and have a strong ser vice culture in our team partners all over North America. This allowed us to focus on the basics of taking care of the customers and provid ing them with what they need exactly when they need it. Period.
Has 2022 been a better business year for laundry and linen services? In what way? Why do you say that?
BARTSCH: Demand for laundry services has increased in 2022, along with the market rates for our services.
Unfortunately, 2022 has brought a worsening labor situ ation and cost inflation resulting in margin compression. Currently, consumers are feeling the impact of inflation; however, businesses have not kept up recovering their lost margins.
So, it’s safe to say that we’re doing more work this year, charg ing more for our services, but costs continue to rise faster than we can offset them.
During 2022 we are living with the widening gap between job openings vs. number of unem ployed workers. Currently, there are two jobs available for every person who is seeking employ ment, and the workforce contin ues to shrink as baby boomers retire.
YEAKEL: Because of inflation ary pressures on labor, utilities and cost of linen, we were forced to have difficult conversations with our customers. I’m not sure that constitutes a better business year.
This puts us in a situation where our services become com moditized. We have spent decades of time building relationships, and
third-party contract facilitators don’t necessarily care about that.
It becomes challenging and frus trating when the expectations con tinue to be lowering pricing when the entire world is experiencing unprecedented inflation and the negative impact on businesses.
GOEL: We are seeing a growth in secular demand for uniforms and services from both exist ing and new customers across a variety of industries throughout North America.
We continue to look at the lon ger-term horizon and are increas ing our service capacity in key mar kets and expanding our footprint.
What ongoing challenges do you see as most concerning for the industry today and in the near future and why?
BARTSCH: The largest forwardlooking issue is correcting the sup ply imbalance for the workforce. Why? Wages and quit rates are impacting productivity and output.
Secondly, I am also concerned for the European suppliers who will be burdened with additional economic pain this winter as the war drags on. Why is this concern ing? Europe has many equipment manufacturers who make equip ment and support our industry.
YEAKEL: Developing internal candidates for growth within the company.
I have been happy to work for HCSC for 28 years and am a true “company guy.” I’m not sure the mindset of millennials, Gen-Z, etc., have any intention of staying with a single company through out their entire careers.
GOEL: The fragility of the sup ply chain as exposed in these past years and the increasing inflation are two key issues that continue to affect customers, service pro viders and suppliers.
Service providers that are posi tioned to weather these challenges and have the cushion to invest in their infrastructure are more likely to come out stronger and custom ers are starting to value that.
How has the industry changed because of the past few years and what further changes do you see in the coming years?
BARTSCH: Industry consolida tion has continued and in some cases was propelled during the early days of the pandemic as capital was looking for a safe place to invest.
Consolidation was fueled by decades of ultra-low interest rates, but with the current federal reserve policy around rising inter est rates, I suspect that valuations will decline and some deals simply won’t get done.
I also expect that prices for ser vices will continue to climb as companies seek to restore margins and struggle to find staff to fulfill the work.
YEAKEL: HCSC has changed because we have attempted to do more with less. Sometimes we’ve been successful, other times we fall victim to the planning fallacy (the
tendency to underestimate the time needed to complete future tasks, displaying optimism bias).
Operations need to continue to invest in automation, including robotics to improve productivity and eliminate the need for per sonnel to perform tasks that can otherwise be done autonomously.
GOEL: Virtually every industry has been affected and changed by the pandemic. Many have had to adjust to a new way of doing business. It’s apparent with more businesses accelerating their digi tal transformation.
However, in our business, per
son-to-person relationships mat ter. We recognize that and also recognize that talented team part ners equipped with the right skills and tools are going to be key in supporting our customers.
As such, we are investing in tech nology to streamline our operations and manufacturing capabilities, to enable our team partners to deliver a better customer experience.
If you could share just one message with your laundry and linen services colleagues about the future of the industry, what would that be?
BARTSCH: The industry needs further equipment and automa tion. We are needing to automate the remaining manual tasks, such as sorting.
We need the industry’s equip ment suppliers to develop new equipment that radically reduces the number of people needed.
YEAKEL: The future of health care linen rental services is bright, as long as under any and all circum stances the needs of the customer continue to be the primary focus.
HCSC’s “Brand Promise” con sists of serving a hygienically clean quality product with a 100% fill
rate delivered on time every day. This may be oversimplified but, if we continue to be successful in these efforts, everything else will take care of itself.
GOEL: The uniform and tex tile services industry has immense opportunities on the horizon.
Workers across a broad spec trum of businesses wear uniforms both for safety reasons as well as for presenting an image or an identity. The macro factors will accel erate the development of this industry and it is for each one of us to raise the bar of customer expectations.
distraction and increase comfort.
• Increased driver visibility: Proxima’s purpose fully designed dash, windshield, and side- and rear-view screens optimize driver sight lines for maximum visibility and significant blind-spot reduction.
• Improved driver safety: Proxima’s design puts a premium on driving position and improved vis ibility to aid in parking, maneuvering and avoiding obstacles—contributing to overall driver safety.
Parker Boiler has launched its new 206 Series (Low NOx) stainless steel boiler. It reaches tempera tures up to 210 F and pressures up to 160 PSI.
Parker says it offers a modern stainless-steel verti cal firetube condensing pressure vessel packaged with conventional boiler controls for simplicity and highefficiency operations for use in closed-system heating applications.
EAVX and Morgan Olson, both subsidiaries of JB Poindexter & Co., have revealed the first image and additional details of its new Class 5 walk-in step van body design that offers unprecedented integrated technology and aims to lead the way in the develop ment of next-generation commercial delivery vehicles.
Named Proxima, the body is said to build off Morgan Olson’s reputation for durable and depend able commercial vehicle bodies while introducing new technologies to enhance driver ergonomics and efficiencies that will transform the industry.
Proxima’s chassis-flexible design means it offers significant advantages for both electric and internalcombustion powertrains, as well as new features that aim to positively impact safety, comfort and overall driver experience.
Proxima’s key design highlights and product fea tures include:
• Improved aerodynamics: Delivering a significant reduction in drag for maximum efficiency with out compromising functionality.
• Enhanced driver ergonomics: Proxima is designed to accommodate drivers of all sizes with a focus on every interior detail to reduce
Enhanced technology integration: EAVX’s pro prietary VX Control™ is a digital vehicle infra structure that enables the widest array of tech nologies to be connected, configured and com municate with each other and with drivers, no matter the chassis or powertrain. For Proxima, VX Control will unify lighting, equipment, tools, cameras, sensors and driver-assistance technolo gies into a single, intelligent system that works continuously to deliver higher efficiency, lower operational cost and greater value in every appli cation.
Proxima is said to feature a flexible design that offers design options for all types of chassis regardless of powertrain or power source.
For this first proof of concept, EAVX and Morgan Olson are partnering with automotive technology company REE Automotive for its P7 electric chassis, where the body will be powered by the REEcorner’s drive-, steer- and brake-by-wire technology.
The companies are evaluating Proxima with select potential customers at dedicated events. These events will allow potential customers across delivery, logistics and retail segments to experience the vehicle and its technology firsthand.
www.morganolson.com 800-624-9005
The sealed combustion design raises efficiency with lower excess air and minimizes heat loss to the room, according to the company. It also has a 10:1 turn-down ratio, a small footprint space-saving design and silent operations due to the variable speed blower.
Units easily fit through 36-inch doorways and can be fired on natural gas or LPG propane.
www.parkerboiler.com 323-727-9800
Gerard Daniel Worldwide has intro duced a cost-effective rescreening program to users of vibratory separator machines, also referred to as sifters and sieves.
With Gerard Daniel’s rescreening pro gram, users can recycle their screens and save money—in most cases more than 25% per screen. Gerard Daniel devel oped this program in response to dra matically increasing commodity prices for stainless steel, which have doubled since 2020.
Using a proprietary process designed to preserve the rings in as-new condition, Gerard Daniel’s rescreening program removes old worn-out screens from original frames, and after removing the epoxy and mesh from the rings, the screens are replaced and the assemblies are returned to the customer, ready to use.
www.gerarddaniel.com 800-232-3332
Shannon Global Energy Solutions, which engineers and manufactures reusable acoustic and thermal insu lation for a sustainable planet, is introducing a removable and reus able LT450-TT Thermal Blanket and LT500HS-TC Heat Shield for plant operators at institutional, commercial and industrial laundries to improve safety and energy efficiency for equip ment like presses and boilers.
The LT450-TT removable insu lation blanket, part of the firm’s INSULTECH® line, creates a ther mal barrier that enables machinery to use steam energy more efficiently, which reduces the cost of steam, and protects workers from burns. The LT500HS-TC Heat Shield delivers safety and energy efficiency for boiler doors by lowering surface tem peratures.
The company says plant operators can easily and quickly remove and reinstall the model LT450-TT Thermal Blanket and LT500HS-TC Heat Shield from equipment to adjust settings or for maintenance. Insulation that a worker can easily remove and replace on a piece of equipment makes for a sustain able solution, adds Shannon GES.
Model LT450-TT has a maximum thermal capacity of 450 F. Model LT500HS-TC has a
maximum service temperature of 500 F.
Facility owners can use these removable and reusable insulation blankets and shields on equipment made by many different man ufacturers.
Each Shannon GES reusable thermal blan ket and shield includes an I.D. tag to describe the component to which it belongs and a hot-surface label to warn workers of high temperatures. If a customer needs to reorder an insulation blanket or shield or obtain a replacement part, they can easily do so because Shannon GES says it stores produc tion drawings for up to 10 years. www.shannonglobalenergy.com 716-693-7954
Reflective Apparel, a manufacturer of a complete line of high-visibility apparel, has launched RAflect50, high-visibility gar ments engineered to withstand the high temperatures and harsh chemicals of indus trial laundries.
After 25 washes, the company says tra ditional hi-vis garments may begin to lose their colorfastness and reflective properties, adding that hi-vis garments may be out of compliance with ANSI/ISEA 107-2020 stan dards in only 12 weeks.
RAflect50 hi-vis garments have been independently tested to withstand at least 50 washes in this industrial laundry environ ment, ensuring that the quality and integ rity of the entire garment remain intact throughout the life of the rented garment, according to the company.
RAflect50 products feature 3M™ Scotchgard™ soil release for easy care and
3M™ Moisture Wicking finish. The performance fabric wicks away moisture three times faster than cotton. Comfort and cooling features also include vented underarms and back yoke and Silverplus® technology to minimize odors.
RAflect50 products are available in mul tiple styles including rental-friendly T-shirts, woven work shirts and polos.
All RAflect50 products feature segmented reflective tape for high visibility, comfort, lon gevity and durability and comply with ANSI Class II High Visibility standards. The micro pique fabric used in RAflect50 hi-vis garments received third-party certification for ANSI/ ISEA 107-2020 High Visibility Compliance.
www.reflectiveapparel.com 866-998-2649
Manufacturers: Have you introduced a new product? Revamped your system? Released a new catalog? E-mail your product news, along with a high-resolution image, to mpoe@atmags.com and we’ll consider publishing your news free in Tools of the Trade.
Rescreening program for vibratory separator machines introduced
and Johnson invited Haynes to join EverGreen as the general manager.
“Minashia had never been a general manager, but that role needed a client-centric individual and that was right up her alley,” Hoffmann says. “She does a great job taking care of our employees and our clients.”
“If the people are taken care of, then the business is taken care of, and I think that’s what Jeff and Leon saw in me, that ability to lead,” shares Haynes. “For Rose, Sam and myself, that’s the culture we wanted to build.”
As Hoffmann and Johnson con tinued to build out their leadership team for the Durham plant, they invited Batista, another linen ser vice industry veteran, to be plant manager, and DiGiulio, a new face in the industry, to be their office manager.
Even as women continue to make strides in the typically male-dom inated linen industry, fully female management teams are an uncom mon sight—especially having women of color, Haynes and Batista, in two out of these three roles.
The management at EverGreen’s plant importantly reflects the demo graphics of Durham, a city that celebrates diversity and inclusivity.
“Working in a women-managed office was something I felt was going to be somewhat magical,” says Haynes.
“One thing about this industry is it’s male-dominated, so I wanted to pride myself on establishing relationships with both (Sam and Rose). Being their general manager and having them work with me,
I wanted Sam and Rose to know they were fully supported, and I was behind them 100 percent with any goals they had—personal or professional.”
DiGiulio, now EverGreen’s cor porate controller, entered the linen industry in 2020 after previously working for a manufacturing com pany.
“This just seemed like a perfect combination of hospitality and manufacturing,” she says. “It was actually quite funny because when I saw the posting, I just knew it was mine. I knew immediately—this was it.”
Batista has worked in the laun dry industry for an impressive 34 years, 27 of those at Angelica where
she spent almost two decades working alongside Hoffmann and Johnson.
She was asked to join the Durham management team as plant manager, and she relocated to Durham from Jacksonville, Florida.
“When Leon and Jeff asked me to join them as plant manager, I didn’t even think twice about it,” Batista says.
DiGiulio described how her working relationships with Batista and Haynes have developed to become much deeper than coworkers.
“The word that keeps coming to me is family,” she shares. “We’ll get together outside of work and just
enjoy each other’s company. We value each other on a professional level but also on a personal level. We care about what’s going on in all our lives.”
Employing 360 people across North Carolina, Alabama and Florida, roughly half of EverGreen’s workforce is women.
According to McKinsey & Company, based on 2020 statis tics on the leadership gap, “For every 100 men who were pro moted to a managerial role, only 85 women advanced to the same position. This gap is even greater for women of color as only 71 Latinas, and 58 Black women received a promotion.”
Representation and visibil
ity across all industries are more important than ever. For Haynes, a Black woman, and Batista, a Latina woman, holding senior manage ment positions continue to pave the way for normalizing women, especially women of color, in simi lar roles now and in the future.
“What message does it send when all you do is bring in male management? Elevating women leaders inspires our workforce,” says Johnson.
“They see we believe in Rose, Minashia and Sam, and I think it has helped us be a better business because of it.”
Early in Batista’s career, Johnson suggested she try out an operations role and introduced her to Rosario, a woman working in California as a general manager of two laundry plants.
“I said, ‘Operations? I’ve never seen a woman running a laundry,’ and Leon said, ‘Oh, yes, they do,’” says Batista.
“So I met Rosario and realized I could do it, too. That’s how I decided to start that role.”
When Hoffmann and Johnson hired for these leadership roles, Haynes, DiGuilio and Batista were chosen because they were the best people to do the job.
“Simply put, they were the most qualified individuals for the role,” Johnson points out.
“We wanted free thinkers, peo ple who would think differently. We wanted people to expect more, to expect better. And those three individuals are Rose, Sam and Minashia.”
Madison Adair graduated with a B.A. in media and journalism from the Hussman Journalism school at UNC-Chapel Hill. She now lives in Richmond, Virginia, working in the film industry.
TUMWATER, Wash. — In software engi neering, the cost of detecting and fixing defects increases exponentially the farther they are discovered downstream.
A bug found during the design phase is simple and inexpensive to fix. Conversely, a bug found by an end user in a finished sys tem costs orders of magnitude more.
The final consequences of downstream defects may even be injury or death as in the case of commercial aircraft or other mass transportation systems.
We follow this same principle with the healthcare laundering process at Sterile Surgical Systems. A high-quality soil sort for us is the first step in producing highquality, hygienically clean healthcare linens for infection prevention and patient safety.
Errors in the sort lead to successively more severe and more expensive problems downstream.
In a worst-case scenario, a bad sort may even lead to serious injury or death for hos pital patients or laundry/healthcare work ers. Less severe, but still impactful, items missed in the sort may cause damage to expensive laundry equipment, causing cost ly downtime and quality problems.
Imagine a complex software system that was built with no design process. It would not work.
Now imagine a healthcare laundry with no soil sort process. Imagine a laundry where received soiled goods are emptied together into a washer, unloaded and then dried, and then sent to the finish for folding and shipping to the hospital.
Think of the abysmal quality of the final product. Visualize this contaminated linen touching sick patients. Picture the associat ed safety issues … needles, controlled sub stances, garbage, food and more all mixed together with the washed but unclean linen! A quality soil sort operation prevents this condition. The purpose of the soil sort oper ation in our healthcare laundry is to separate received goods into categories so they can next be handled safely and appropriately.
In our accredited healthcare laundry, we generally have from 15 to 30 different soil sort categories. These can be broken down into bulk linens, specialty items, non-linen items and stain/out-of-service items.
Examples of bulk linen items include bath blankets, patient gowns, sheets, terry items pillowcases and incontinent pads.
Examples of specialty items include sur gical textiles, cubicle curtains, lifter slings, microfiber cleaning devices, lab coats, scrubs and isolation gowns.
Non-linen item examples include gar bage, sharps, pharmaceutical waste, surgical instruments, patient personal items, pens and staff personal items. Some non-linen items are harmless, but others must be handled carefully according to local and federal laws. For example, pharmaceutical waste received must follow a strict protocol.
Finally, stain/out-of-service items include textile items that should be taken out of service due to permanent stains, tears or simply overuse.
In our plant, the soil sort process and technology have evolved considerably.
Originally, we had a team of six sorters stand around a spring cart. One person opened bags while five others sorted into 10 carts on the perimeter. This was slow, messy, dangerous and error prone.
Later, we built a sort platform with an incline conveyer moving goods up to another 60-foot straight conveyer. A bag
ger opened bags onto the incline conveyer while six sorters stood behind the straight conveyer and dropped given items into carts below.
This was faster, safer and more accurate but still a largely manual process. Cart weights were estimates and employees were responsible for manually moving full carts to the wash area and replacing them with empty carts.
Still later we installed a sort rail system from a reputable material handling vendor. We use this system currently.
This system also consists of a sort platform with an incline conveyer moving goods up to another 60-foot straight conveyor.
A bagger still opens bags onto the incline conveyer while six sorters stand behind the straight conveyer pulling given items. However, with this system the items are dropped into a hopper hooked to a sling bag.
The items are weighed and when the desired weight is reached, the sling bag is automatically removed, stored and replaced with a new bag. Sort productivity is measured, and sling bag contents are identi fied and tracked throughout the process.
This process is much more effi cient, flexible, accurate and safe.
Moving forward, we want to
take advantage of several emerging tech nologies that enhance safety accuracy and productivity. These include the following:
X-Ray Technology—Systems now exist that scan soiled textile bags for foreign objects including sharps, pharmaceuticals, pens and other non-linen items. When found, these bags are kicked out so they avoid employees, washers, extraction presses, dryers, etc.
Imagine, no more pens destroying a load of scrubs or sharps rupturing a press mem brane.
RFID Technology—Like most healthcare laundries, we struggle with scrub losses and inventory tracking. There are now systems that can scan a load of scrubs (or other items) and then count how many came from each facility.
This will enable us to accurately report to customers how many scrubs they were sent and how many they returned to us.
Automatic Picking, Identifying and Sorting—This is “The Holy Grail.” I have seen demonstration artificial intelligence systems that perform the very human tasks of picking up a piece of linen, identifying it, and then sorting it into the proper bin.
I have yet to speak with laundries using these in production but when these systems mature, they will revolutionize the industry and we will be first in line to implement them.
As with any complex software engineer ing project, the first step in establishing a high-quality healthcare laundry process is to focus resources to get the upstream correct. Invest the time and resources to develop an accurate high functioning sort operation.
The few extra seconds it takes employees to sort items accurately will pay exponential dividends in the safety, quality and produc tivity of your healthcare laundry operation. More importantly, these rela tively small investments will pay immeasurable gains downstream ultimately in infection prevention and patient safety!
spend a great deal of time with our employ ees to identify all the different pieces, where to separate and the importance of discarding hazardous items.
We often meet with customers to explain to them about separating items at their loca tions to avoid damage charges and to extend the life of the linen.
Another key to soil success is open com munication and collaboration between driv ers and our soil department. We encourage them to work together to ensure that there is a thoughtful flow from unloading laundry bags to sorting and ultimately to the wash house so that items are processed timely.
We ensure employee safety with personal protective equipment (PPE) such as goggles, gloves and gowns, and we clean the soil belts and floor twice a day.
BY PHOEBE ELLISPETALUMA, Calif. — Lace House Laundry and Linen Supply operates a mixed plant in Northern California primarily ser vicing restaurants and hotels and a small number of uniforms.
This mix creates a very dirty, smelly, busy soil sort department each day. We have a very traditional process for our soil depart ment—all manual, hand sorting by item, dis carding garbage, identifying damaged goods and after all those steps, hopefully clearing the soil rails daily.
Because we do so much customer-owned goods (COG) for our hotel customers, we need two distinct processes for food and beverage (FB) items and the COG accounts.
The FB process begins with the drivers unloading their trucks on a lift rail system when they return to the plant. If there is an overflow of soiled bags, the drivers stack them in carts labeled by day.
The soil department shift begins at 4 a.m., and the employees are expected to sort 20-25 bags an hour. Most items go onto the conveyor belt where one employee clears to
different wash slings.
High-volume items, such as bar mops, aprons and white napkins, are sorted at each table directly into a sling.
The employees are trained well to identify problem items such as corks, pens and silver ware that come mixed with the linen. This is a major benefit of hand sorting—all these items are discarded before going through the washing machines and possibly damaging the equipment.
We are fortunate to have several employ ees who have worked in our soil department for more than 10 years, and they crush it!
The hospitality sorting belt is a much more streamlined, quicker and cleaner process.
The cart dumper unloads onto an elevated belt, and the employees sort the hotel linen into carts by item. The carts are immedi ately rolled to our continuous batch washer (CBW) for washing.
This work has a very specific order and timeline as many of our hotel customers require daily deliveries.
Training of our employees and customer education are key to our success in soil. We
We have improved the lighting in our soil department, and we have emphasized the importance of managing and measuring the daily soil so that we can be prepared for the next day. If we know where we are with counting soil, we can plan accordingly for production hours in the finishing departments.
Some of our highest-paid pro
duction employees work in this department as we recognize that although this is not the most glamorous job it is very important to the success and effi ciency of Lace House.
Cheers to all the soil depart ments out there—thanks for doing our dirty work!
Phoebe Ellis is co-owner of Lace House Laundry and Linen Supply in Petaluma, California.
Employee burnout seems to be a newer hot-topic discussion item as businesses continue to struggle to fully staff their operations.
As business leaders, we turn to our key players to carry the workload when our workforce is short, and they are typically all too happy to do so.
But what happens when you lose that key player due to burn out? Who are you going to turn to then? If you’re like me, I don’t want to think about losing any of my key players due to a series of manageable events.
There are many ways to address employee stress and burnout, many of which don’t require you to reinvent the wheel.
First, evaluate the workload of your staff. If your production manager is working 12 hours a day six days a week, they are not likely to be able to maintain that workload for a long time.
Second, evaluate the controls in place within your facil ity. Does your team leader or account manager have the autonomy to make the necessary decisions to get the job done?
Third, foster a sense of com munity. This can be as simple as planning fun events like themed days, employee cookouts, etc.
Lastly, and arguably most importantly, ensure that your leadership teams are actively involved in supporting the needs of your workforce daily.
and calm times, alike.
Get back to the basics. Ensure that your personnel is taking breaks and lunches. This is typical ly required for frontline employees but make certain that your man agement team is doing so, as well.
Especially with this latter group, encourage them to fully disconnect and limit the “shop talk” when away from their offices and workstations. Set up a nice break/lunch area with amenities like snack machines, comfortable tables and seating, music, and/or TV (but maybe keep the channel off of political talk shows).
As it is every year, the upcom ing season will surely be busy for laundries, but the holidays also typically coincide with spikes in burnout. Therefore, be sure that personnel is taking their vaca tions. Support them in balancing time with work and family.
Explain priorities and pro cess flow to your employees.
Telling them how their piece fits into the overall puzzle will pro vide a perspective that leads to pride in—rather than burnout from—their jobs. Provide details on business statistics: volume produced, revenue generated, improvement initiatives com pleted, etc.
On that subject, one of my coworkers has previous experience with a trucking company. They created a “Wow” board, which would highlight miles driven, loads delivered, and—especially for this time of year—the num ber of gifts that made it into the hands of children.
Above all, thank your employ ees for their hard work. Show them that they are appreciated. Hold an employee picnic. Maybe invite their families and add to that sense of pride by letting them show off what they do and how they support those around them.
Managing stress is a tough situation in most work envi ronments.
As a director or manager, the most important thing you can do is to prevent pushing the “have to get it done yesterday” mentality. If you want quality work, your employees need to be able to slow down and get things done right the first time in a quality manner.
glaze. The team who basketed up the most pans got a lunch paid for by me.
Another game involved the whole shift. If they got the pans in the baskets before a set time, they got an extra five minutes of lunch break. For washing the pans before a set time, another five extra minutes and so on for each phase of the process.
Another way I reduced stress was for employees who had a history of showing up on time day after day. If they called and were running late, I would per sonally clock them in on time.
On paydays, if someone’s check did not come in I would pay them something out of my pay check until theirs did come in.
So, in a job that was physically demanding and normally high stress, my crew worked stress free knowing they were appreciated for good timely work habits, and they knew they could count on me.
A way to avoid burnout is to make sure that employees are not made to feel guilty for taking their full breaks. No job is worth the health and well-being of the people who do that job.
The aforementioned ways to avoid stress also avoided burnout because my employees actually looked forward to coming to work; it wasn’t just a job for them.
I learned from the plant superintendent and plant man ager that we were a family that got to know each other. The higher levels of upper manage ment got to know the employees and most of their immediate families.
They also let their family members know how much they appreciated their husbands or spouses for working there and that they were there to help them. When you get to know your people and what they are going through, then you can bet ter tailor the job to avoid stress and burnout.
S
ince it can’t be seen until it manifests into poor perfor mance or employee conflict, burnout is something to regular ly address. It can occur in busy
Knowledge will help them to handle stress in their own job responsibilities and to better deal with the situations around them. An understanding of plant opera tions might avoid having “Chicken Little” overreact to small concerns.
Let employees know the importance of what they do.
Have management from the top down thank individuals for what they do.
Even when employees enjoy their work, they can get burned out. Do your best to encourage them in what they are doing and provide the occasional distraction so that they can disengage and come back refreshed. Good luck!
If your main goal is quantity, your employees need to be able to work at their pace. As they get better at the tasks, their speed should automatically improve. If not, then they either don’t care or are not willing to try.
A method I have used to increase the quantity of work and reduce employee stress is to look for ways of making a game out of work.
One game we played was with basketing pans for stripping the
Another very effective method I employed was when an employee was getting over worked or had something going on that was affecting them at work, I would take over doing their job once in a while to give them a break or a chance to deal with whatever they had going on.
You can get your best out of people when they don’t think
“With the labor challenges all businesses are facing, my employees are working harder than ever. How can I help them manage stress and avoid burnout?”Healthcare Laundry William Muse United Hospital Services, Indianapolis, Ind. Hotel/Motel/ Resort Laundry Kelly Reynolds Sea Island Acquisitions, Sea Island, Ga. Consulting Services Jon Witschy Spindle, Woodridge, Ill. (Image licensed by Ingram Image)
you’re out to get them for some thing or always looking to write them up when performance drops off.
Usually, that happens when there is something going on in their life either at home or work. If you can find out what is both ering them, you can avoid most stress and burnout.
machines.”
Maybe this is the best piece of the pain some of us experience now. We can all be excited about streamlining the process.
Iwould say the key factor here is that their manager or super visor addresses issues that the employees have.
Y
ou don’t have to talk to many laundries, whether they are in a group you share or a competi tor, to find out that most of us are struggling with labor.
Somehow, even after the “gimmes” of COVID are done, many people have chosen to stay out of the workforce. Hard to offer remote work to production and maintenance personnel, and now it has become nearly a bid ding war for capable bodies.
Now we must practice, as well as we can, retention. This entails much more than money alone, even if you have people skipping for an Amazon promise of a bet ter wage and life balance. The people that jump ship for a buck, and a buck alone, are not the people that would be with you for a generation.
The people that we work with/ for/under all need to feel a level of respect and appreciation.
My boss should know I respect his risk and wisdom, and he has
always made me feel like my input is valued.
The people I manage in main tenance could job shop—perhaps they are. The best I can do is hope they remember getting full weeks during the pandemic and let them know that I appreciate their tenure, effort and ethics.
I truly believe this goes a long way in contributing to retention, as replacement is always such a painful process.
We have a coffee stand across the street from our facility. I will occasionally buy a guy a drink, or sometimes the crew gets treated.
It gives you a few minutes, on the clock, of course, to talk about other things. How is your family?
You seeing any bucks where you are hunting? Your car is looking good … you wax it?
All trivial stuff, but you might find out you enjoy their answers, and it feels good to see cowork ers light up about something.
We all, or most of us, really wish for happiness and success for our peers. It is easy to be prideful of their accomplishments.
Enter overtime. So ugly, in so many ways. It chokes the bot tom line. It can create a fatigued worker, potentially leading to safety concerns and burnout.
This is, I think, the toughest issue in our industry right now. So many plants are approaching pre-pandemic poundage and piece
counts with less staff … less expe rienced staff … less reliable staff.
We try the donuts and always ask for volunteers for overtime. So far, it seems to pay dividends, but we still must recognize that we need to make sure the same people that say yes, every time, are also encouraged to take that weekend for themselves, and their families.
Automation is obviously the best answer to labor, but it is expensive and slow for many of us.
If we show our loyal partners a commitment to making the process easier, they will appreci ate that, and it is also viewed in a positive manner. People worry less about “being replaced by
Employees need to know that their manager will support them, fight for them and have their best interests in mind.
Make sure your managers value their employees. This is a key factor in keeping your employees and having them avoid stress and burnout.
Talk with your employees; find out how you can help them.
Could it be periodic breaks throughout the day? Could it be more flexible work schedules? Could it be rotating job duties and responsibilities?
Maybe they have ideas to improve the workflow. Maybe they have ideas to improve efficiency and make their jobs less stressful.
Praise them for their work.
Perhaps create a “who did a good job today” board where you can post things your employees have done that were good for your business and your customers.
Praise can go a long way in making employees feel valued for their work.
WOODSTOCK, Ill. — Keeping your safety workwear and uni forms clean and free of contami nants is essential. Not only will this help you stay safe on the job, but it will also prolong the life of your clothing.
However, when washing safety gear, it’s essential to follow specific tips to ensure that the clothing is not damaged and that you remove all contaminants.
The process of washing work wear is different from washing regular clothing. Let’s look at some tips for washing your safety workwear and uniforms.
Commercial laundry tasks aren’t without risk. In fact, there’s a good chance you or someone you know has had an accident while doing laundry. Some of the most common risks include:
Fires. Lint buildup in dryers is a leading cause of house fires. Be sure to clean the lint trap after every load of laundry.
In addition, don’t overburden the dryer by trying to dry too
much clothing at once. Doing this will significantly increase the time it takes for the clothing to dry, which could lead to lint buildup.
Injuries. Wet floors and laundry carts are common causes of slips and falls. Be sure to wipe up any spills immediately and use caution when walking around wet areas.
In addition, be careful when moving laundry carts as they can be heavy and difficult to control, whether in wet or dry areas.
Contaminants. Contaminants in laundry rooms include bacte ria, mold and mildew. Be sure to wash your hands after handling dirty laundry and use gloves when possible.
In addition, don’t forget to clean the washing machine and dryer regularly.
Chemical burns. Many laundry detergents contain harsh chemi cals that can cause skin irritation or even burns. Be sure to read the labels on all laundry products and follow the instructions carefully.
In addition, wear gloves when using any chemical cleaner. You can also use other personal pro tective equipment (PPE) such as aprons, safety glasses, and face masks to protect yourself from harmful chemicals.
If you want to keep your safety workwear and uniforms in good condition, it’s essential to follow some specific tips. These tips can help you avoid accidents and keep your clothing clean and contami nant-free.
Select the right wash cycles. One of the most important things to consider when washing safety workwear is the fabric the cloth ing is made from. Doing this will determine what wash cycle you should use.
For example, if you’re wash ing a uniform made from 100% cotton, you’ll want to select the delicate cycle.
However, if you’re washing syn thetic fabric, you may be able to use a regular cycle. Remember that you may need to test a small area of the material first to ensure that it can handle the selected cycle.
You don’t want to damage the material by using the wrong cycle.
Use of chemicals. As men tioned earlier, many laundry detergents contain harsh chemi cals. These chemicals can cause skin irritation or even burns. That’s why it’s essential to read the labels on all laundry products and follow the instructions carefully.
In addition, you should wear gloves when using any chemical cleaner.
Doing this is especially impor tant when it comes to workwear and uniforms. Since you use these garments in hazardous environ ments, they can become contami nated with dangerous chemicals. By using gloves, you can help
protect your hands from these contaminants.
Right washing and drying temperature. The temperature at which you wash and dry your safety workwear and uniforms is also important to keep in mind.
You’ll generally want to wash these garments in cool or warm water. Hot water can damage some types of fabric, and it can also set stains.
As for drying, it’s best to use the low heat setting; doing this will help prevent shrinkage and dam age to any customized uniform design.
For example, if you’re wash ing a pair of 100% cotton pants, you’ll want to wash them in cool water and dry them on a low heat setting. If not, you could end up damaging the pants.
In addition, you should avoid using fabric softeners when wash ing safety workwear and uniforms. These products can leave a residue on the fabric that can attract dirt and other contaminants.
Follow instructions from the manufacturer. When washing safety workwear and uniforms, it’s always best to follow the instruc tions from the manufacturer.
These instructions will consid er the specific fabric of the cloth ing and the type of environment where you wear the garments. As a result, they’ll provide you with the best guidelines for washing and caring for your garments.
By following these instructions, you can help ensure that your clothing lasts as long as possible. You can find the manufacturer’s instructions on the garment’s care label; read it carefully before
washing or drying your safety workwear and uniforms.
Use of PPE. Finally, it’s impor tant to remember that you should always wear PPE when handling or laundering safety workwear and uniforms. The reason is that these garments can become con taminated with hazardous mate rials. By wearing PPE, you can help protect yourself from these contaminants.
Some of the most common items of PPE include gloves, aprons and facemasks. If you’re unsure about what type of PPE to use, you should consult with your employer, and they’ll be able to provide you with the proper guidance, mainly as you deal with different types of safety workwear and uniforms.
As you can see, there are a few things to remember when laundering safety workwear and uniforms.
Following these tips can help ensure that your garments are properly cleaned and cared for.
Following proper washing tips will help extend the lifespan of your safety workwear and uni forms while keeping you safe dur ing wear.
Be sure to consult the care label of your garments for specific instructions. And, if you’re unsure what to do, don’t hesitate to ask your employer for guidance.
Nick Warrick is the sales man ager at All Seasons Uniforms, a professional workwear company based outside of Chicago that has been in business since 1991.
A1 American says its product line includes ready-made garments with superior soil release and wicking properties, consisting of a variety of workwear products such as chef coats, kitchen shirts and kitchen baggy pants in solid or checker.
The company says its whites stay white, and its fabric is engineered to reduce pilling with fewer SKUs to hold in inventory.
A1 American says it is a leading manufacturer and distributor of reusable textile and hygiene products, and its nationwide distribution of workwear, reusable masks and essential care products will maximize business safety readiness as a source for preparedness.
www.a1americangroup.com 833-205-2200
SANMAR
SanMar says its Port Authority® Long Sleeve SuperPro React™ Twill Shirt is designed to provide the ultimate in professional performance.
The wrinkle-resistant shirt also releases stains, and the soft,
smooth fabric gives a polished look that’s comfortable enough for year-round wear.
Highlights of the shirts include:
• 4.3-ounce, 55/45 cotton/ poly twill.
• Stain release.
• Wrinkle-resistant.
• Easy care.
• Button-down collar.
• Dyed-to-match buttons.
• Left chest pocket.
• Rounded adjustable cuffs.
• Back yoke with box pleat.
Port Authority® Long Sleeve SuperPro React™ Twill Shirts come in sizes ranging from XS–4XL in nearly 20 colors.
www.sanmar.com 800-426-6399
Encompass Group says its reusable Synergy and Essentials institutional apparel blend durability and value with a fashionable variety of styles and colors, all in a long-lasting blend that’s comfortable, opaque and quick drying.
Synergy and Essentials scrubs offer minimal shrinkage, and they’re constructed for durability and institutional processing, according to the company.
They’re available in a comprehensive collection of fashionable and functional styles, including
V-Necks and long-sleeve modesty tops, elastic and drawstring waist pants, and warmup jackets. Sizes range from XS to 5XL. www.encompassgroup.com 800-284-4540
Fashion Seal Healthcare, a signature brand of Superior Uniform Group, says it has combined WonderWink® fashion, fit and fabric with its industrial apparel manufacturing experience to launch the WonderWink® INDY line of scrubs.
Fashion Seal Healthcare says INDY scrubs are designed with fit, finish and designs that flatter all body types. Wrinkle-resistant, soft-feel fabrics stretch for maximum all-day comfort.
The company says the line is loaded with additional features and is available in both unisex and women’s styling.
www.fashionsealhealthcare.com 888-491-5818
Nov. 1 from retiring longtime executive director
RICHMOND, Ky. —
The Association for Linen Management (ALM) reports it has appointed Sarah Brobeck as its new executive director.
She will succeed retir ing executive director Linda Fairbanks and assume respon sibilities on Nov. 1.
Fairbanks first met Brobeck when she attended the Laundry & Linen College and described the journey as “a joy to watch her grow into various aspects of the textile care services industry.”
ALM says Brobeck has served in roles from laundry opera tions to vendor sales, providing a unique perspective and in-depth knowledge of the many differ ent aspects of the textile care industry.
“Sarah’s firsthand experience will provide a great value to the
industry in the days and years ahead,” says Fairbanks. “I wish Sarah, the Board of Directors, staff and the membership the very best.”
ALM says that Brobeck’s more than 15 years of experience work ing in the textile care industry, extensive knowledge and positive approach will ensure the asso ciation remains steadfast in its commitment to advance excellence in the textile care industry through edu cation, certi fication and best practices.
“I am very proud of ALM and the major milestones we have achieved over
the past years, and excited for this new milestone,” says James Mangini, ALM Board presi dent.
“Sarah brings a wealth of experience to this role, as well as an abundance of strong industry relationships. I am thrilled to welcome Sarah to the team.”
Brobeck is no stranger to ALM. Previously, she served as ALM Board secretary and director, taught CLLM reviews, presented at IMPACT, as well as instructed and acted as a facilitator at the Laundry & Linen College.
“I am honored to join the ALM staff,” she says. “ALM is an associ ation that is a leader in providing professional development for the textile care industry.
“This is an important time for ALM to strengthen educational opportunities and resources as well as build a supportive net work that will aid in our success.”
As ALM continues to evolve and grow, it says its purpose and core values will continue to be the resource for safety, efficiency and quality expertise.
FRANKLIN, Tenn. —
The CSCNetwork Board of Directors reports that it has appointed textile rental industry veteran Jeff Landry to the position of executive director.
CSCNetwork says that since 1979, its mission has been to help independent laundries stay inde pendent. As a result of Landry’s comprehen sive indus trial laundry and supply chain expe rience, CSC says it will be able to further ful fill its mission: To help members compete and profitably grow their business.
“Jeff Landry’s appointment is viewed by the Board as a significant strategic move to improve CSC’s buying power
and positively impact its mem bers,” says Ed Heilman, presi dent of CSCNetwork’s Board of Directors.
“Jeff’s broad industry experi ence in purchasing and sourc ing should help us form deeper relationships with our vendor partners. We’re confident that Jeff, along with Lisa (Wacker), Chinook (Deveraux) and Renee (McCollum), will give CSC a solid foundation to take us into the next decade.”
Landry is a 34-year veteran of the textile industry, with a pri mary focus on the rental laun dry and healthcare markets.
During this time, he has honed a deep understanding
of manufacturing, product development, sourcing and importing goods from the global marketplace. From chemicals and trucks to fuel and plant services, his exper tise encompasses all aspects of rental laundry, negotiating and purchasing.
Additionally, CSCNetwork says Landry’s approach to engi neering bottom-line results has led to strategic improvements in all aspects of industrial laundry operations.
“My participation as a vendor over the years has led me to develop a deep admiration for CSCNetwork while observing the productive work done on education and saving members millions of dollars in the pro cess,” shares Landry.
“I look forward to supporting the independents while leading the organization in the upcom ing years as the industrial laun dry and global supply chain con tinues to evolve.”
ALEXANDRIA, Va. — TRSA, the association for linen, uniform and facil ity services, reports that Jim Kearns, executive vice president and chief financial officer, Alsco Uniforms, was elected chair of its Board of Directors.
He was elected at the Annual Membership Meeting on Sept. 15. during the association’s Annual Conference in Nashville, Tennessee, where its new Board members for the upcoming year were announced.
wake of the COVID-19 pandemic, we have in Jim Kearns a wellrounded, seasoned executive with a demonstrat ed record of growth and a knack for working with com panies large and small,” says TRSA President & CEO Joseph Ricci.
“Our thanks go to outgoing Chair Noël Richardson for success fully leading us through the worst of the pandemic. We now look for ward to continued progress with Jim Kearns guiding the association.”
—JIM KEARNSA graduate of the University of Utah, Kearns joined Alsco Inc. in 1993 as the internal audit direc tor and advanced steadily to his current position in January 2019. Alsco is a global leader in uniform and facility service rental and has been since 1889. It provides these services to over 355,000 custom ers in more than 180 locations worldwide.
“I am grateful for the opportu nity to serve as TRSA chair,” Kearns says. “Over the next two years, I’m going to focus on advocacy and the sharing of best practices to boost the industry as a whole.
“Our industry provides an essential service, and we need to safeguard the trust of our indus try customer base and help solve problems with our products and services.”
“As the linen, uniform and facil ity services industry continues to pursue renewed growth in the
In other news from TRSA’s Annual Membership Meeting, Randy Bartsch, CEO of Ecotex Healthcare Linen Service Corp., Vancouver, Canada, was elected vice chairman, while Dempsey Uniform & Linen Supply CEO P.J. Dempsey was elected treasurer. Additional directors elected during the conference included:
• Pierre Ferron, president, Buanderie Blanchelle, Montreal, Canada.
• Bob Hager, president, Miller Textiles, Wapakoneta, Ohio.
• Jim Rozakis, president & COO, Cintas Corp., Mason, Ohio.
• Kelsey Van Miert, presi dent of customer rela tions, Northwest Health Care Linen, Bellingham, Washington.
In addition, the TRSA Supplier Partner Council has submitted Rick Kelly, vice president, sales and marketing, Pellerin Milnor Corp., Kenner, Louisiana, as the director candidate representing the hard goods category and Jake Gurtler, vice president, corporate accounts, Gurtler Industries, South Holland, Illinois, as the director of other goods.
“I AM GRATEFUL FOR THE OPPORTUNITY TO SERVE AS TRSA CHAIR. OVER THE NEXT TWO YEARS, I’M GOING TO FOCUS ON ADVOCACY AND THE SHARING OF BEST PRACTICES TO BOOST THE INDUSTRY AS A WHOLE.”
BALTIMORE and BOSTON — Arctaris Impact Investors LLC reports it has made a fol low-on growth equity invest ment in Up To Date Laundry.
One of the largest healthcare laundry facilities on the East Coast, Up To Date Laundry provides laundry services to healthcare providers across the Mid-Atlantic, including the University of Maryland Medical System, Johns Hopkins and Einstein Medical Center.
The investment in the laun dry is part of the Arctaris Baltimore Program, a $25 mil lion commitment to invest in Baltimore’s underserved neigh borhoods, created in partner ship with The Abell Foundation and Neighborhood Impact Investment Fund (NIIF) and with support from Erie Insurance (ERIE) through its investment in the Arctaris Opportunity Zone Funds.
In March 2021, Arctaris made an initial investment in Up To Date Laundry to aid the com pany’s continued growth and expansion.
The additional growth equity investment from Arctaris will fund projects such as increased automation at the company’s main plant on Desoto Road, multiple energy efficiency improvements and the ability to purchase linens for new linen rental customers.
These upgrades will allow the company to create additional highly skilled jobs, improve pro duction efficiencies and reduce overall energy consumption.
Up To Date Laundry is a longstanding business in Baltimore and is a significant driver of sustainable job creation, paying above-market wages and ben efits.
Located in an economically distressed neighborhood with a 15.9% unemployment rate, the company has a diverse base of 200-plus full-time employees, as well as 300-plus temporary employees.
“Arctaris Impact Investors is a value-add financial partner who not only provides capital but supports the team, through its relationships, in the areas of business development and workforce training,” says Mark Carter, president and CEO of Up To Date Laundry.
The operation aims to add up to 50 jobs in Baltimore over two years.
With medical laundries deemed an essential service industry during the pandemic, Up To Date Laundry provided critical services allowing its hos pital clients to focus their efforts on fighting COVID and facili
tating safer care for patients. In addition to the invest ments, the Arctaris Portfolio Services Group has actively worked with and advised Up To Date Laundry management in securing concessionary capital such as workforce development grants and obtaining Property Assessed Clean Energy (PACE) financing which upgrades cur
rent equipment to improve water utilization and reduce energy consumption. These improvements are pro jected to benefit not only the local water systems and the balance of aquatic life, but the anticipated reduction in green house gas from energy produc tion is 1,900MT CO2e annu ally.
“Up To Date Laundry is a prime example of a company seeking to balance its commit ment to its customers, work ers and the city of Baltimore, all while not compromising the health of the nearby ecosystem,” says Anita Graham, Arctaris managing director respon sible for Maryland, eastern Pennsylvania, and Washington,
D.C.
The almost $14 million Arctaris investment in Up To Date Laundry is the corner stone of the $25 million Arctaris Phase I Baltimore Program.
Arctaris is currently sourcing new real estate, infrastructure and operating company opportu nities to expand its mission and commitment to Baltimore.
SAN DIEGO — Emerald Textiles, a portfolio company of Los Angeles-based private investment firm Pacific Avenue Capital Partners LLC, reports that Jeff Gennuso has joined the executive management team as chief financial officer.
“We are extremely excited to have Jeff join the Emerald team,” says Andrew Kratky, CEO of Emerald.
“Jeff complements our strong performance-oriented culture, and we believe his impressive reputation for execution and achieving results makes him the right choice to lead our financial and accounting organization.”
Gennuso served most recently as a senior director at Riveron where he worked in several advi sory roles, including Angelica’s chief financial officer since 2019.
He has more than 30 years of professional experience in execu tive leadership, restructuring and turnaround, financial advisory, and treasury roles within the manufacturing and healthcare industries.
“I am very excited to join the team at Emerald Textiles,” says Gennuso. “The unwavering focus by the ownership group and man agement team to provide best-inclass service to their customers and employees is outstanding.
“With new facilities, continued investment in new equipment, and an excellent team with deep indus try knowledge, Emerald is well
positioned for success. The com pany’s continued focus on growth, both organically and through M&A acquisitions, will only improve the strength of Emerald.
“It is my pleasure to join this exceptional management team and continue scaling the organi zation going forward.”
NEW YORK — Eastern Funding LLC reports that Nancy Robles has been pro moted to president. She previ ously served as chief operating officer.
Michael Fanger, Eastern Funding’s CEO, says, “Nancy has distinguished herself in holding our teams account able for performance. She has led Eastern to an ethos of organized policies and procedures.
“Nancy has been instrumental in the phenomenal growth of our portfolio all while ensuring our Company culture and values are upheld. The future is bright for Eastern with Nancy as president working with our outstanding team.”
Robles has been with Eastern Funding for 17 years and has served in multiple roles ranging from documentation specialist to chief operating officer.
“Eastern Funding’s success is built on providing best-in-class service and products to our customers as well as providing a work environment that embraces and promotes diversity, equity and inclusion of all team mem
Continued from Page 4
your wastewater. There are different methods of accomplishing this. Reusing rinse water. The use of dual drains on your washers that allow the rinse water to be sent to a different wastewater pit is a good choice. This is hard to do with existing laundries since they do not usually have dual wastewater pits.
I have utilized pipes on washer drains versus digging trenches though that can help with this. The decision to use a reclaim drain must be figured in on the initial washroom machinery purchase since a reuse drain is not normally a standard item.
Continuous batch washers. CBWs can get their water usage to under .50 gallons per pound by basically always reusing their rinse and extractor water.
Wastewater filtration. There are several vendors out there that have exceptionally good systems for cleaning up your wastewater to the extent that you can reuse the water in your washroom.
bers,” says Robles.
“I am excited to continue work ing with all of our stakeholders to make Eastern Funding an even more successful company”
The company shares that Robles is an industry leader in the equipment finance industry. She serves on the Equipment Leasing & Finance Foundation’s Board of Trustees and the Board of the Berkeley College Scholarship Foundation.
Robles is a member of The Coin Laundry Association’s Diversity and Inclusion Committee and Brookline Bank’s Diversity, Equity and Inclusion Committee. Further, she is a Board member of Equipment Finance Cares and the Monitor’s editorial board while actively supporting other charitable organizations within the equipment finance industry and in the New York area.
COLUMBIA, S.C. — FOLTEX USA, a provider of finishing equipment, reports that it has hired Jake Blaney as another technical account manager.
The com pany says he has an extensive background in account manage ment from various industries and an exceptionally high dedication to customer service.
FOLTEX USA adds that it looks forward to seeing how Blaney can strengthen its promise of providing simple and reliable equipment backed by excellent customer care.
OSHKOSH, Wis.— Girbau North America recently wel comed Muzi Sitshela of Buffalo Grove, Ill., as an inside sales associate.
In his new role as inside sales associate, Sitshela interfaces with GNA staff, distributors and cus tomers on a daily basis; manages GNA’s lead qualification process; and handles inside sales and customer relations duties, includ ing some reporting and product pricing responsibilities.
Sitshela, who is bilingual in English and Spanish, earned a
bachelor’s degree in marketing from the University of Wisconsin Oshkosh in 2022. He also holds a certifica tion in social media marketing from LinkedIn Learning.
“It’s amazing to have such a talented new member as part of our team,” says Director of Strategic Business Efficiencies & Solutions Pam Kuffel.
“Muzi will be a great addition to the GNA group. The customer compassion he brings to all our new customers will help grow GNA to new levels.”
“I’m very fortunate to have this opportunity to be part of a hard working yet caring atmosphere here at GNA,” says Sitshela. “Everyone here has mutual respect for one another, which makes the work environment quite inviting.
“Furthermore, my role as an inside sales associate is far more interesting than I had anticipated. I get the opportunity to speak and work with people from all over the world.”
FOOTHILL RANCH, Calif. — Textile provider Venus Group reports that Errol David was pro moted to vice president, opera tions, in September.
All manu facturing and distribu tion activi ties nation wide will be consolidated under this new posi tion.
Among other responsibilities, David will take complete ownership of Venus’ Made-In-America table linen production system, which the company says is “a true jewel” and one of its leading differentia tors in the market.
“Errol has been an invaluable leader for Venus and has an unri valed operational understand ing of what it takes for Venus to promote such a unique domestic supply chain for table linens,” says Raj Patel, Venus Group’s president and co-founder.
David has been with Venus since 2012 and celebrated his 10th anniversary with the com pany in August.
Before joining Venus, David enjoyed a long and illustrious
career at Aramark for 28 years. The company says his deep understanding of the industrial laundry business will allow Venus to better position its domestic operations in service to its cus tomers.
“Errol and his team take a customer-first approach to every thing they do operationally,” says Steve Crow, vice president of institutional sales.
“Our customers benefit from Errol’s commitment to quality and consistency in our domestic operations.”
GREENVILLE, N.C. — UNXChristeyns reports that Matt Ellington has joined the company as a territory manager. He joins the team after serving in a similar posi tion at Ecolab for 10 years. Based in Valdosta, Georgia, Ellington will be serving custom ers in southeast Georgia and the northern tier of Florida.
UNX-Christeyns is a recent partnership that brings together more than 100 years of experience in the textile care industry.
ITASCA, Ill. — Ellis Corp. reports it has hired Scott Voss as director of technical engineering for Ellis and Ludell Mfg.
“Scott has talents and experi ence in many aspects of our customers’ lives, from water and energy recovery to wastewater, wash aisle design, efficiency anal ysis, installations … he adds to our capabilities and thereby adds value to our customers,” says Bob Fesmire Jr., president/CEO and the fifthgeneration family mem ber in the business.
“We are very excited to have Scott on our team.”
Voss was previously executive vice president of engi neering at Aramark Uniform Services and was at Aramark for over 20 years before joining Ellis.
Before his years at Aramark, Voss served in the U.S. Navy for nine years as a Navy Nuke. He received his Bachelor of Science at The New School in New York.
Suite 320, Chicago, IL 60661-1036 Cook County. Donald Feinstein, American Trade Magazines LLC, 650 West Lake St., Suite 320, Chicago, IL 60661-1036 Cook County. Nathan Frerichs, American Trade Magazines LLC, 650 West Lake St., Suite 320, Chicago, IL 60661-1036 Cook County. John S Suhler, 200 Long Neck Point Rd., Darien, CT 06820 Fairfield County. 13. Publication Title: AMERICAN LAUNDRY NEWS 14. Issue Date for Circulation Data Below: September 2022 15. Extent and Nature of circulation:
Pellerin Milnor Corp.
P.O. Box 400, Kenner, LA 70063 504-467-9591, Fax: 504-468-3094 www.milnor.com
Pellerin Milnor Corp.
P.O. Box 400, Kenner, LA 70063 504-467-9591, Fax: 504-468-3094 www.milnor.com
Y=0. (4)Requested Copies Distributed by Other Mail Classes Through the USPS (e.g. First-Class Mail®): X=0, Y=0. (c) Total Paid and/or Requested Circulation (Sum of 15b (1), (2), (3), and (4)):X= 9,200, Y=9,251. (d) Nonrequested Distribution (By Mail and Outside the Mail). (1)Outside County Nonrequested Copies Stated on PS Form 3541 (include Sample copies, Requests Over 3 years old, Requests induced by a Premium, Bulk Sales and Requests including Association Requests, Names obtained from Business Directories, Lists, and other sources): X=3,676, Y=3,886.
(2)In-County Nonrequested Copies Stated on PS Form 3541 (include Sample copies, Requests Over 3 years old, Requests induced by a Premium, Bulk Sales and Requests including Association Requests, Names obtained from Business Directories, Lists, and other sources): X=0, Y=0. (3)Nonrequested Copies Distributed Through the USPS by Other Classes of Mail (e.g. First-Class Mail, Nonrequestor Copies mailed in excess of 10% Limit mailed at Standard Mail® or Package Services Rates): X=0, Y=0. (4)Nonrequested Copies Distributed Outside the Mail (Include Pickup Stands, Trade Shows, Showrooms and Other Sources): X=3, Y=3. (e)Total Nonrequested Distribution (Sum of 15d (1), (2), (3) and (4)): X=3,679, Y=3,889. (f)Total Distribution (Sum of 15c and e): X=12,879, Y=13,140. (g)Copies not Distributed (See Instructions to Publishers #4, (page #3)):X=500, Y=244. (h)Total (Sum of 15f and g): X=13,379, Y=13,384. (i)Percent Paid and/ or Requested Circulation (15c divided by f times 100): X=71.43%, Y=70.4%. 16. Electronic Copy Circulation:(a) Requested and Paid Electronic Copies: X=345, Y=111 (b) Total Requested and Paid Print Copies (Line 15c) + Requested/ Paid Electronic Copies (Line 16a): X=9,545, Y=9,362. (c) Total Requested Copy Distribution (Line 15f) + Requested/Paid Electronic Copies (Line 16a): X=13,224, Y=13,251. (d) Percent Paid and/or Requested Circulation (Both Print & Electronic Copies) (16b divided by 16c x 100): X=72.18%, Y=70.65%. I certify that 50% of all my distributed copies (electronic and print) are legitimate requests or paid copies. 17. Publication of Statement of Ownership for a Requester Publication is required and will be printed in the November 2022 issue of this publication. 18. Signature and Title of Editor, Publisher, Business Manager, or Owner: I certify that all information furnished on this form is true and complete. I understand that anyone who furnishes false or misleading information on this form or who omits material or information requested on the form may be subject to criminal sanctions (including fines and imprisonment) and/or civil sanctions (including civil penalties): Charles Thompson, Publisher, Date 9/7/2022
Ph.: (704)372-3890; Fax: (704)342-0758 www.gardnermachinery.com
Pellerin Milnor Corp.
P.O. Box 400, Kenner, LA 70063 504-467-9591, Fax: 504-468-3094 www.milnor.com
Pellerin Milnor Corp. P.O. Box 400, Kenner, LA 70063 504-467-9591, Fax: 504-468-3094 www.milnor.com
Pellerin Milnor Corp. P.O. Box 400, Kenner, LA 70063 504-467-9591, Fax: 504-468-3094 www.milnor.com
Pellerin Milnor Corp. P.O. Box 400, Kenner, LA 70063 504-467-9591, Fax: 504-468-3094 www.milnor.com
ATLANTA — During this year’s Clean Show, equipment manufacturer Pellerin Milnor Corp., based in Kenner, Louisiana, hosted a dealer banquet and awards ceremony for its dealer network to celebrate the previous year’s sales efforts.
“Pellerin Laundry Machinery Sales Company had a tre mendous level of sales activity for 2021,” says Rick Kelly, vice president of sales and marketing for Pellerin Milnor Corp.
“Their success in finishing as Milnor’s 2021 top dealer was achieved through their continuing commitment to fostering customer relationships and product solutions of our industry-leading products.”
The following awards were presented to authorized Milnor dealers on July 30 by Pellerin Milnor President and CEO James W. Pellerin.
The 2020-2021 Key Man winners were:
• Bill Bell of Steiner-Atlantic Corporation (Miami).
• Grant Ellis of Pellerin Laundry Machinery Sales Company (Kenner, Louisiana).
Steve Hickey of TLC Tri-State Laundry Companies (Valdosta, Georgia).
• John Janz of Herb Fitzgerald Company (Butler, Wisconsin).
• Andy Jeninga of Western State Design (Hayward, California).
• David Johnson of Pellerin Laundry Machinery Sales Company.
• Gabe Rees of Loomis Bros. Equipment Company (Fenton, Missouri).
• Brendan Ristaino of Yankee Equipment Systems (Barrington, New Hampshire).
• Shawn Ryan of Pellerin Laundry Machinery Sales Company.
• Ralph Tuccillo of Steiner-Atlantic Corporation.
• Barry Spiezman of TLC Tri-State Laundry Companies.
• Prescott Spigner of TLC Tri-State Laundry Companies.
• Derek Ward of Pellerin Laundry Machinery Sales Company.
• Kyle Zabrin of Equipment International (Skokie, Illinois).
Ron Hirsch of Direct Machinery Sales Company (Hicksville, New York) was presented with the “Lifetime Achievement” award for his countless contributions to Milnor throughout his career.
Randy Gutkowski of Pellerin Laundry Machinery Sales Company and Craig Kind of Western State Design were named “Star Performers” for their sales achievements.
Troy Willis of Loomis Bros. Equipment Company was awarded the “Bulldog” plaque for his persistence and suc cess in his sales efforts.
Steve Jankowski of Direct Machinery Sales Company and Drew Lamas of TLC Tri-State Laundry Companies were each named “Rookie of the Year.”
Milnor also awarded nine dealers with the “100/100 Club” Award for achieving 100% of their quotas for vari ous sales categories. These nine dealers included East Coast
Laundry Systems, Herb Fitzgerald Company, Horwath Laundry Equipment, Loomis Bros. Equipment Company, Mendenhall Equipment Company, Pellerin Laundry Machinery Sales Company, Steiner-Atlantic Company, TLC Tri-State Laundry Companies and Western State Design.
BOSTON — CFS Technologies LLC, a portfolio com pany of Union Park Capital, reports it has acquired Knight LLC.
Knight, based in Irvine, California, will join CFS Technologies’ existing businesses, Lafferty Equipment Manufacturing and Lavo Solutions, bringing together a suite of premium brands and technologies for dispensing equipment and cleaning solutions.
The company says that together these entities will provide chemical dilution, dispensing and dosing equipment across a diverse set of cleaning applications including healthcare, janitorial, laundry, farm, dairy and food production to help create a cleaner, more sustainable world.
“We are excited to welcome the Knight team to the CFS family,” says Chip McAslan, CEO of CFS. “With this acquisition, CFS has significantly enhanced its chemical dispensing technologies and positioned itself for continued growth.
“The addition of Knight not only brings a premium brand, but also complements and expands our existing offering, and together will allow us to best serve our cus tomers with innovative sanitization and hygiene solutions.”
CFS says that Knight has been successfully dedicated to the challenge of developing advanced chemical delivery and dispensing systems for its users since 1972.
For several decades, Knight has developed a reputation for innovation through industry-leading best-in-class tech niques in developing chemical delivery systems that ensure a safer and cleaner environment.
“Knight is a natural strategic fit for CFS Technologies,” McAslan says. “We share several common customers, mar kets, and applications and are extremely enthusiastic about bringing more innovative and deeper solutions to our customers by combining the Knight technical leadership with the unique connected IoT technology of Lavo and uncompromising quality of Lafferty.”
RICHMOND, Ky. — The Association for Linen Management (ALM) reports that registration is open for its IMPACT 2023 Conference.
The educational conference will be held in Charleston, South Carolina, March 13-15, 2023.
ALM says the IMPACT Conference gives textile care ser vice professionals the expertise to create efficient, effective laundry management, services, and products.
Attendees can network and learn from industry leaders and peers about best practices and trends in the textile industry, according to the association.
Early-bird pricing is available until Jan. 15, 2023. This rate for members is $415 and $515 for non-members.
After Jan. 15, prices go to $475 for members and $575 for non-members.
Fees cover all sessions, all conference evening events and full access to printable files.
Guest passes are available for evening events at $75. Regular attendees may add a guest at checkout when they register.
ALM’s hotel blocks are at Hyatt Place and Hyatt House in the Historic District. Room block reservations will close Feb. 13.
LAVAL, Quebec — George Courey Inc., a 112-year-old linen and textile business, owned by the same family for four generations, has undergone a successful transition from the third to the fourth generation.
Taking a century-old business into the future requires business acumen and maturity of leadership, which Jeffrey
Courey and Robert Courey bring to the table.
On Sept. 15, the George Courey Inc. headquarters in Laval hosted the transition ceremony in the presence of representatives from the House of Commons, clients and employees.
Mindful of the wealth of experience Jeffrey accumulated in the company as chief operating officer for seven years, he was promoted to the role of president and CEO in January 2020.
Robert, who served for 16 years as the director of busi ness development became the vice president in May 2022.
Against the shifting sands of uncertainties induced by the COVID-19 pandemic and the high demand for limited supplies of personal protective equipment, George Courey Inc. says it never wavered in its mission to actively support governments in bringing much-needed relief to hospitals and care homes.
The company says it is known as a leader in North America’s linen and textile production and distribution.
Inching closer to the creation of new warehouses in dif ferent locations across Canada and the United States is the next milestone unfolding.
Jeffery says this is “the passing of the torch to a new gen eration of Coureys, well-positioned to steward this com pany into the next century through our focus on People, Planet and Progress.”
This will partly entail, in his own words, “continued success in the growing USA market while promoting reus able textiles across multiple sectors, offering our clients outstanding value, sustainable product innovation and an unparalleled customer experience.”
With Jeffrey and Robert at the helm, the company says its reputation as one of North America’s most reliable and respected linen and textile providers will continue to grow.
ROSENBERG, Texas — Seatex LLC, a specialty chemi cal manufacturer and formulator, reports it has acquired ChemQuest Chemicals LLC, a custom chemical manufac turer headquartered in Pasadena, Texas.
Terms of the deal were not disclosed.
For more than 25 years, ChemQuest has provided custom toll manufacturing services to customers glob ally, with expertise in complex blending and reactionary synthesis.
Seatex says the acquisition provides it with enhanced production capabilities, increased capacity and a comple mentary customer base, representing a diverse set of endmarkets.
The acquisition will take place immediately, with cus tomers enjoying continuity of business operations and the benefit of the broad range of chemical services offered by both companies.
With the acquisition of ChemQuest, Seatex says the new company will be one of Texas’s leading custom toll manu facturers, with the ability to deliver creative and sustainable chemical solutions for all customers.