
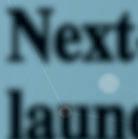


A look at the positions available and skills laundry employees will need in the future
BY MATT POE, EDITOR
Laundry technology constantly evolves, from the hardware to the software and beyond.
It used to be productivity was measured on a clipboard. Today, washers and dryers communicate via Wi-Fi, and adjustments can be made on a touch screen or even remotely.
And who would have thought the term artificial intelligence (AI) would become part of the industrial laundry lexicon? This constantly changing technology
means changes to the jobs available for laundry employees and the skills required in the future.
“We may see robotics taking a role in areas like sorting soil and folding with managers/supervisors relying even more on skills relating to equipment technology for measuring productivity, etc.,” says Sally Mazzola, senior human resources vice president for Core Linen Services.
“We may also see a need for technical engineers with not only mechanical and electronic experience, but software experience, as well.”
While touring some European plants, Umesh Vendargon, COO of Core Linen Services, witnessed increased automation and less heavy lifting/pulling, which leads to a reduction in injuries and claims.
“With the introduction of robotics, employees may see a shift in their job roles,” he says. “They may need to adapt to working alongside robots, monitoring their performance and handling any technical issues that arise.
“Employees will require training to operate and maintain the robotic systems effectively, learning new technical skills related to robotics, such as programming or troubleshooting.”
Automation has a lot of benefits, and it creates many issues, says Deana Griffin, president of The Griffin Group and a member of the American Laundry News editorial advisory board.
“Automation is ideal for tasks that are redundant and require repetitive motions,” she says. “On the other hand, AI isn’t the cure for jobs that require critical thinking, flexibility, reasoning and other soft skills.
“Automation, artificial intelligence and robots are tools to increase production rate,
if humans manage well, rather than replace employees with years of experience.”
Automation defined in a larger scope is the reliance on technology, which removes the formerly required role of human labor, Griffin shares. This would include the deployment of AI and robots because companies switch to automation for higher efficiency and quality, plus lower costs.
This will help employees to enjoy more things about their jobs and satisfaction in their lives.
“In all industries, everyone is replaceable,” says Griffin. “Manual workers would need to educate themselves with automation before they could be replaced.
“The biggest concerns with automation and artificial intelligence are safety and effectiveness of the tools. The most controversial problem is the elimination of jobs.”
It is like an electric car with its innovative design and technology—it still has to have human oversight, Griffin points out. Automated systems will still have the human component for oversight.
“What happened to the maids when the automatic washer and dryer were invented?” she says. “We did more laundry and bought more clothes. Reducing manual labor through automation is nothing new.
“Robots have been around for decades and there will always be a need for manual labor jobs because they cannot do everything.”
Karl Fillip II, CEO of NOVO Health Services, says most new technologies have focused on ergonomics, efficiency and safety.
“Much of our focus in terms of new technology is on providing a great working environment for our team,” he shares. “That involves ensuring we do everything we can to maintain the safest work envi-
MILWAUKEE — Goodwill Industries of Southeastern Wisconsin and Metropolitan Chicago will be closing its commercial laundry business here effective Aug. 3. The organization filed a facility closure/WARN (Worker Adjustment and Retraining Notification) Act notice on June 4.
“We have taken a thorough approach to get to this point and we are confident that although it is not ideal, we have made the right decision for Goodwill Industries of Southeastern Wisconsin and Metropolitan Chicago,” the organization says in a prepared statement.
“We remain committed to our employees during this transition and ensuring people are supported through the closure of the business.”
A total of 136 employees will be affected by the closure.
Goodwill Industries of Southeastern Wisconsin and Metropolitan Chicago shares that it is putting resources in place to help employees connect to new opportunities and maintain employment.
It will provide support services and guidance, including one-on-one counseling, resume and skill set review, and internal application consultations to discuss job opportunities at Goodwill and with Goodwill partners.
Also, the organization is joining with external partners to help employees secure new employment opportunities.
CHICAGO — Mickey’s Linen, a family-owned and -operated textile rental company, reports that it has achieved Hygienically Clean Food Safety certification through TRSA.
The company says the certification reflects its commitment to best management practices (BMPs) in laundering, as verified by on-site inspection and the company’s ongoing capability to produce hygienically lean textiles as quantified by regular microbial testing.
This certification indicates exceptional dedication on the part of Mickey’s Linen in supplying restaurants and other food service establishments with hygienically clean linen, uniforms and facility service supplies meant to keep its customers clean, healthy and looking their best.
“For 90 years, we have been committed to process improvement, implementing the latest technology and laundry processing standards to better service our customers,” says General Manager Peter Brown.
“Achieving Hygienically Clean is a testament to the hard work and efforts our team invests each and every day to produce the highest quality products and services, with the industry’s most recognized certification.
“Our team is extremely proud of obtaining this accreditation and continuing to raise the bar as a best-in-class laundry provider for our customers, and a recognition milestone amongst our people.”
Hygienically Clean certified laundries commit to cleanliness through third-party facility inspection and quantified microbial testing. This combination eliminates subjectivity by focusing on outcomes and results.
Inspectors verify that the textiles cleaned in these facilities meet appropriate hygienically clean standards and BMPs needed to serve hygiene requirements in various industries.
The Food Safety designation applies to products and services for full- and limited-service restaurants, hotels, hospitals, educational institutions and other locations where food is handled and served.
Inspectors assess washing procedures (detergent formulas, temperature, disinfectant, pH, extraction), drying, garment inspection and transportation.
Each certified laundry’s operational flowchart is evaluated, ensuring these procedures (pick up, unloading, sorting of soiled items, and sorting of clean laundry) are mapped. Employees’ use of personal protective equipment must be documented.
During inspections for Hygienically Clean certification, Hazard Analysis and Critical Control Points (HACCP) practices are examined, including the laundry’s techniques for:
• Conducting hazard analysis.
• Determining CCPs, monitoring their control and correcting them if not under control.
• Validating and verifying HACCP system effectiveness.
• Documenting and recordkeeping to show ongoing conformance.
To attain any of the Hygienically Clean certifications, the laundry must submit to a facility inspection, and laundered products must pass three rounds of outcome-based microbial testing, indicating that their processes are producing Hygienically Clean textiles and diminished presence of
yeast, mold, and harmful bacteria. Mickey’s Linen must pass quarterly RODAC (total microbial content) and semi-annual USP 62 (absence of specified microorganisms) testing to maintain their certification. This ensures that laundered product quality is consistently maintained as laundry conditions change (such as water quality, textile fabric composition, and wash chemistry).
Physical re-inspection occurs every two to three years.
For more than a decade, PulseFlow® Technology has proven to wash light soil room linen in as fast as 16-18 minutes and heavy soil in 32-38 minutes, without compromising industry standards of cleanliness. Plus, Milnor PBW TM machines require as little as 0.3 gallons per pound for light soil linen and 0.7 gallons for heavy-soil – both processed without the use of a separate water reclamation system. Milnor CBW® batch washers are in service around the world and have saved billions of gallons of fresh water. Discover more about Milnor’s sustainable laundry solutions at milnor.com.
It’s the kind of story I hope I never have to report on again. Unfortunately, statistics aren’t bearing those hopes.
On May 22, a “disgruntled employee” brought a handgun to Delaware County Linen in Chester, Pennsylvania, and “took out his anger” on co-workers.
Two died and three were wounded (https://americanlaundrynews.com/ articles/2-dead-3-wounded-shootingpa-linen-operation).
The suspect was apprehended quickly in the nearby city of Trainer, but the damage had been done.
This leads to another story I wish I didn’t have to share: being prepared for workplace violence (page 14).
The piece, based on an NFIB webinar presented by Carol Dodgen, owner of Dodgen Security Consulting, details her advice for identifying potential problems and ways to prevent workplace violence. Watch for more on this on American Laundry News outlets.
There are other things laundry operations need to be prepared for such as the jobs and skills next-generation employees will need (cover story).
Also, ways to deal with textile waste (page 12) and using advancing route technology (page 10).
We’re here to help everybody keep it clean … and safe.
Association says industry leaders had ‘dynamic exchange of ideas and insights’
CHARLOTTE, N.C. — The Textile Care Allied Trades Association (TCATA) reports that its 2024 Annual Management and Educational Conference, held April 28-May 1 in Austin, Texas, brought together industry leaders for a dynamic exchange of ideas and insights. During the conference, TCATA President John Silverman of Tschopp Supply installed Mack Magnus of M & B Hangers as its new president, marking a new chapter of leadership under his guidance.
Mack has served as TCATA Conference Chair as well as vice president of the Board of Directors representing supply manufacturers.
TCATA also introduced its newest board members: Terry Hammond of UNX Christeyns, Jack Heaviside of Sunburst Chemicals, Justin Shamion of Colmac Industries, Wes Nelson of Sankosha, and Robb Vacek of Horwath Laundry Equipment.
TCATA celebrated the anniversaries of longstanding members recognizing A-1 Products of Birmingham, Alabama, and Tschopp Supply of Buffalo, New York, for their 50 years of membership, as well as honoring M & B Hangers of Birmingham, Alabama, for 75 years of membership.
Highlighting the spirit of leadership and collaboration within the TCATA community, the inaugural Leslie Schaeffer Member-Driven Award was presented to Leslie Schaeffer, TCATA CEO, acknowledging her outstanding contributions and commitment to the association’s member-driven mission.
TCATA’s 2025 Annual Management and Educational Conference will take place at the Ritz Carlton Tiburon in Naples, Florida, April 27-30.
From AmericanDrycleaner.com:
• ZIPS Partners with Mulberrys Garment Care
• Natural Gas Water Heaters, Boilers Under Attack in LA From AmericanCoinOp.com:
• Tide, Walmart Team Up to Expand Adoption of Washing in ...
• Making the Leap from Wash-DryFold to Commercial Laundry
Don’t overlook water treatment in your laundry operation
I recently celebrated my 40th year in the industrial laundry business.
I was a young veteran of the United States Marine Corps when I went to work for a local laundry.
I was actually involved in building my first laundry as a 16-year-old, but I could tell you virtually none of the specifics that we did because, again, I was 16.
Most of my 40-year career has been centered around the maintenance side of the business. Even though I went on to be a plant manager and general manager, I still spent a lot of time looking at our equipment. I am a firm believer that you should never get promoted far enough up to not use all your knowledge. Preferably using that knowledge to help the next generation, we should never make someone learn the hard way, what we have already learned the hard way.
I AM A FIRM BELIEVER THAT YOU SHOULD NEVER GET PROMOTED FAR ENOUGH UP TO NOT USE ALL YOUR KNOWLEDGE. PREFERABLY USING THAT KNOWLEDGE TO HELP THE NEXT GENERATION, WE SHOULD NEVER MAKE SOMEONE LEARN THE HARD WAY, WHAT WE HAVE ALREADY LEARNED THE HARD WAY.
I have seen this industry go through a tremendous number of changes in those years.
Most notably the machinery is much more efficient and easier to maintain, from the soil room throughout the washroom and clean floor. We have machines that can easily do the job that we might have several employees performing in the ’80s.
Opening an electrical panel on the side of a washer extractor was quite the sight back in the ’80s with twenty cube relays and auxiliary switches sitting on each contactor.
You sure had to bring your thinking cap to work every day. Now, you open a panel and there may be 10 boards with the front display saying which board you need to look at. The folks who build laundry machines have certainly brought the industry a long way.
But one area that hasn’t really changed, and yet we seem to not spend as much time looking at or thinking about, is our water treatment.
Yes, I know we now spend a tremendous amount time and money on treating our wastewater.
Wastewater treatment used to be reserved for only industrial uniform laundries or ones that process ink towels. Now, we all seem to be getting into the wastewater treatment business no matter what our business model is.
What I am talking about is the importance of ensuring we have good, clean, zero grain hardness water for use in our washrooms and boilers.
ENSURING WE CAN CONSISTENTLY CLEAN THIS LINEN SHOULD BE THE NO. 1 CONCERN OF OUR MAINTENANCE DEPARTMENTS. THIS ALL STARTS WITH TREATING OUR INCOMING WATER. HARD WATER ... DRASTICALLY REDUCE(S) THE BOILER’S EFFICIENCY AND CAPACITY.
Our business is still at the core about washing and returning laundry. Ensuring we can consistently clean this linen should be the No. 1 concern of our maintenance departments. This all starts with treating our incoming water. Hard water in the boiler causes scaling that will drastically reduce the boiler’s efficiency and capacity.
Continued from Page 1
ronment possible.
“Working in a laundry presents its own challenges, and we are committed to investing in solutions that make it easier for our employees to complete work.”
“At Arway Linen, a Philadelphia-based F&B laundry with very little to no automation or technology around our process, we know that relocating to a new facility based on technology and automation will change everything for us,” says Mario Stagliano, managing partner of Arway Linen & Uniform Inc.
“Our situation may be a bit different considering we will be relocating vs. investing in a current space. In short, we believe the laundry industry is just scratching the surface of the technology that will come.”
LAUNDRY JOB MARKET
Skilled workers have always been in demand and will be more in demand than ever by the year 2030, says Griffin.
“Rather than replacing jobs, it is more about shifting roles,” she shares. “There will be fewer employees in some areas, but they will be utilized in other areas that will replace different skills and qualifications.
“Employees will be utilized in areas where they will have more of a human connection such as customer service and training departments, instead of mundane monitoring of machines.
“Automated systems and robots can perform more of the repetitive daily tasks that are programmed with a specific set of rules.”
Griffin says some of the new positions in the future may include:
•Automated product managers.
•Automation engineer, manager.
•Analytical managers.
•Project managers.
•Automation technicians.
•Internet tools manager.
•Crisis management team.
•Supply chain specialist, manager.
•Training specialist, manager.
“I don’t believe the majority of jobs in laundry operations are likely to disappear as a result of new technologies,” Fillip says.
“However, I do expect new technologies to make it easier for people to do their
work and overall reduce the number of people it takes to complete various tasks within the laundry environment.”
He concurs that it’s not about new positions with new technology, but evolving positions.
“Our maintenance and engineering roles have become more demanding as the technologies we employ become more complex,” Fillip points out.
“As a result, we often have to look outside the industry to ensure we have the appropriate mix of skills needed to operate and maintain our newest equipment while investing in more ongoing training for our existing team.”
“I think there will be a big push to automate soil sorting,” Stagliano says. “I also believe sales and marketing will be streamlined a bit as well.”
How is technology affecting the sales and marketing side of the laundry industry?
He says that when Arway started in 1979, it grew like many independent operations with a sales force of three to five people “cold calling, pounding pavements.”
“We’ve been able to streamline and be more efficient where leads now come to us via digital marketing, SEO, pay-per-click campaigns and some of these different
apps that are out there,” shares Stagliano.
“These apps are just so simple to use that the organization is able to pull information where you are. You’re kind of fishing where the fish are, in a sense.
“We are accomplishing more with one (salesperson) than we ever did with four.”
Stagliano says there will be a bigger demand for maintenance and engineering positions focused on computer skills vs. just turning wrenches.
Griffin stresses that automated equipment with the latest technology cannot fill all the gaps. Instead, employers need to step up their “A” game in hiring, training and making their company the best choice for employment.
“The laundry industry has a greater adoption of newer technology so that they can do more with less, which affects the number of employees and your current laundry set-up within the plants,” she shares.
“However, the purchase and installation of new equipment can be anywhere from 12 weeks to 12 months, the cost of equipment is expensive, plus we have the greatest labor shortage of skilled workers to manage the equipment.
“Laundries have implemented automated systems with a cost-benefit analysis. This integration has been very costly and has made only a few contributions to filling the labor shortages. When you make changes, it comes with new policies and processes, which require human oversight and interaction.”
According to Griffin, employees will need two types of skills for the new/evolving positions: soft skills and hard skills.
Soft skills include self-management, critical thinking, multi-tasking, foresight thinking, creativity, digital literacy, emotional intelligence, identification and problem-solving skills, to name a few.
Hard skills will include programming, control systems, operating systems, machine learning, robotic process automation knowledge, business process improvement, database skills, web technologies, generative AI, data analysis and more.
“A key factor to keep in mind is not everyone is good at acquiring new skills,” she points out. “In addition, it takes a long
time to do so.
“Most employers should plan to offer internal training supplemented by online training, building relationships with industry experts and external consultants.
“I encourage utilizing well-known laundry recruiters as they have the expertise in locating, attracting, and presenting qualified top talent for faster and better results. Another component is knowing how to work with the recruiting firm.
“As competitive as the labor market is today, finding skilled workers is the most critical component for all business’s success.”
Griffin shares the following ways companies can locate skilled workers:
•Must have a skills list—what are you seeking?
•Utilize online job websites that focus on trades.
•Always be connecting with people: The Clean Show, industry websites and forums, social media.
•Partner with high schools, vocational schools, and/or university and college career centers.
•Offer apprenticeships, internships and build connections with academic departments related to the industry.
•Employee lead/referral program— reward with bonuses if hired.
•Contact a skilled worker temp agency.
•Utilize military/veteran transition centers.
•Hire within the company.
•Train and upskill current employees.
•Contact your industry recruiter.
When it comes to training new employees, Griffin recommends the following:
1.Sign agreements with equipment manufacturers that can offer “handson” training and online 24/7 troubleshooting accessibility.
2.Visit the vendor for training and/ or have them conduct a “hands-on” training at your facility.
3.The Clean Show is coming up soon in August 2025 in Orlando, which is a great way to connect with vendors, build relationships, see new products in operation and ask questions.
Employees in manual labor positions can be reskilled to their jobs more effec-
Continued from Page 6
tively, which means fewer of them will be needed, according to Griffin.
“When a job requires these new skills, a human for the job is the best option,” she says. “Efficiency through technology is a poor excuse to leave human beings jobless.
“Allow and/or encourage your employees to work remotely and embrace the digital age. If not, you will be left behind. Utilize modern technology to further your local or global presence.”
She shares that skills every person will need to get ahead and take on greater leadership roles will include:
•Possess excellent communication skills—lead a conversation.
•A deeper cultural understanding.
•Having initiative.
•A drive to compete when it comes to education and career opportunities.
•Critical thinking—being able to think for yourself and solve problems in real time.
• Adaptability.
“According to FORBES, referencing the article ‘Skills-First Approach to Hiring,’ this approach competes with the four-year college degree era by placing it in second place and skills at the top today,” shares Griffin.
“Since the pandemic, leaders have ditched the four-year degree because it’s no longer necessary for jobs that pay top dollar.”
“It is really up to all of us how we educate others. Encourage governments to rethink education programs to generate the talent pipelines the industry would require and starting at an incredibly early age could be beneficial for the next generation of skilled workers.”
A few suggestions she offers:
•Go to your local career centers and guidance counselors to discuss how to provide tools to the students for successful careers.
•Coordinate groups to visit the plant.
•Promote your company—start at a different entry point versus after they have enrolled in the military, college, university or trade school.
•Schedule half-day shadowing programs at your facility—work release programs and vocational schools.
“It is our responsibility to motivate, educate, encourage and inspire our youth about the rental uniform and linen/textile industry to build the next generation of skilled workers,” Griffin concludes.
Various technical skills are required for these positions, Fillip shares, the most important being adaptability to change and quickness to learn new things.
“As the pace of change accelerates, we need a team that can keep up with everevolving technologies,” he shares.
“Most operators have seen that staffing the technical maintenance jobs has become a challenge over the past several years,” he says. “As a result, we often hire from outside the industry. This presents its own challenges as you need a program to train new hires on equipment specific to our industry.
“Additionally, you need a program that continues to reinvest in and develop your team, creating an internal pipeline of qualified candidates.”
Stagliano says future laundry employees will need greater computer skills and abilities for the technological aspects to come.
“Our investment in employees along the way as technology and automation innovates or evolves has to understand the components of that versus having someone who’s been with me 10 years who loads and unloads a washer by hand,” he points out.
“Our focus is going to be a more skilled employee, even if they cost more. You can have one guy run five tunnel washers, but I have 11 conventional washers that I need six, seven guys to run and those five tunnel washers can do five times the amount of weight in the same amount of time.
“I’d rather invest in someone who can understand how to use the technology of this automation.
“When I mentioned maintenance and engineering, they also have to be even more skilled. I think our focus will shift to technologically inclined people versus we just need somebody to pump a bag on the table and sort this linen as quickly as possible.”
One method Stagliano advocates to find or train employees with more advanced skills is to partner with local technological schools.
“It’s easier to find unskilled labor than it is to find maintenance and engineers who understand our type of equipment,” he says. “If somebody’s mechanically inclined, they could learn, but it’s going to take a little while.
“There’s not a pool of these types of employees out there. We’re a niche business. We have niche pieces of equipment.
“A year and a half ago when we were learning a little bit about the equipment that we’re investing in for the new space, its electrical, its technology, the computers, I was getting overwhelmed because it’s not my strong suit. Our thought is what would be great to find is someone who’s young and may want to come out of a trade school who can build a nice career.
“My partner, Mark Harad-Oaks, said let’s contact these tech schools and see if they have any programs or job fairs or anything like this, which led us to take it a step further to say to some of these higherups in these tech schools, here’s what we’re doing, here’s the type of equipment.
“We would love to sponsor some off-site field-trip-type training on the job intern-
ship programs because there would be nothing better than somebody coming out of a tech school possibly interning with Arway who would love to build a career.”
Griffin says that a good leader will find other roles for displaced workers within the organization. This can be approached through re-training or re-tasking. However, it depends on the speed and cost of automation and how company processes transform. The skill is still valid, but it has been re-tooled.
As with all business decisions, it will mostly depend on the financial calculation of cost for a human to perform the work compared to the cost of purchasing a machine to perform the same job, Griffin points out.
“Employees are expected to perform several diverse types of jobs,” she says. “With this being factored in the calculation, I believe humans will be competitive sources of labor for the next 40-75 years.”
The recent development is that software can automate office workers’ jobs as well, shares Griffin.
“Accountants perform parts of their work automated through technologies such as robotic process automation,” she says. “Plant workers won’t become totally redundant, but their work will become streamlined so fewer of them are needed. The point to be made here is automation will not only replace ‘unskilled labor.’”
“(Manual labor) jobs will not go away anytime soon,” agrees Fillip. “The new technologies will simply make these jobs safer and easier to perform.”
“There will continue to be a need for feeding ironers until that gets automated. Same with soil sorting,” shares Stagliano.
With evolving laundry jobs and skills, management and supervision must also change.
“Supervisor/managers have to adapt to the technology changes before being able to lead a new employee base,” Stagliano says. “If management is older, then there may be a challenge to get them caught up. We will transition some of these people.
“When you talk about supervisors, management of our new business model, it’s
going to be people who are starting from the ground level who are going to help us and have the ability to learn a new model and be motivated for a new model and step into a role—I see how this new model has changed from what we’ve done in the past. Let me step in and use whatever experience I have to help streamline, whether via automation or things like that.”
Fillip says there is better real-time visibility into what is happening in a facility because of new technologies. This makes it easier to measure and course-correct throughout the day.
“One could argue that this allows for a reduced supervisory staff; however, we believe that technology should only supplement what our management staff does and certainly cannot replace what they do,” he says.
“The direct interactions between our leads/supervisors/managers and their staff are key to our success. Our team will need to be well-versed in the tools and technologies we provide in our facilities.”
Griffin points out that embracing innovative technology, automated systems and AI software can help business innovation, but it can’t replace emotional intelligence and human leadership.
“At MIT (Massachusetts Institute of Technology), researchers have found that AI models may make harsher judgment calls than humans would,” she shares.
“Automation of technology has and will allow leaders and employees to perform other roles. For example, work remotely, operate programs and set machines for out-put.
“Work closely with technicians from equipment manufacturers with the newest and latest automated machinery. Instead of relying on your own knowledge, reach out more frequently for answers through AI tools and ChatGPT.”
“At the end of the day, we are still a people business, and new technologies will not change this,” Fillip points out.
“The most important core competency we have in operating our laundry facilities will continue to prioritize strong leadership and interpersonal skills supplemented by the ability to fully utilize the various technologies available to our leaders.”
SHRM study shows 70% of organizations that list pay ranges say it has led to more applicants
ALEXANDRIA, Va. —
Organizations that list pay ranges and engage in pay transparency are more competitive and attract more applicants who are often more qualified, according to research conducted by the Society for Human Resource Management (SHRM).
The research details how organizations are approaching pay transparency as several states and localities implement new laws for employers.
As employers consider how best to approach pay transparency, many have raised concerns that listing pay ranges may lead to negative outcomes such as candidates not considering the total compensation, but SHRM research shows most organizations that list salary ranges lead to favorable outcomes.
Of more than 1,300 HR professionals sampled, 42% say their organization operates in a location that requires pay ranges to be included in job postings.
When not required by law, however, more than two in three (67%) HR professionals say their organization voluntarily lists start pay in their job postings sometimes, often, or always.
Further, 32% of these organizations began including start pay information in their job postings within the past year, signaling some employers may be planning ahead in anticipation of new pay transparency trends.
SHRM advocates for employers to be
transparent with how wage decisions are made and conducts voluntary equity checks.
“The path toward equity requires more than recognizing that there are systemic gaps that adversely impact one group over another and then addressing them proactively,” shares Emily M. Dickens, SHRM’s chief of staff and head of public affairs.
“It requires more directed education on the compensation process, increased
engagement with compensation specialists and HR professionals, and an understanding of how to leverage one’s talent through personal advocacy when armed with this information and allyship within the organization.”
Additional key findings include:
• 70% of organizations that list pay ranges on job postings say that doing so has led to more people applying to their postings.
• Nearly two-thirds (66%) of organizations that list pay ranges on job postings say that doing so has increased the quality of applicants they’re seeing.
• 65% of organizations that list pay ranges on job postings say that doing so makes them more competitive in attracting top talent.
Related to how pay transparency influences applicant behavior:
• 82% of U.S. workers are more likely to consider applying to a job if the pay range was listed in the job posting.
• 74% of U.S. workers say they are less interested in applying to job postings that do not list a pay range.
• 73% of U.S. workers are more likely to trust organizations that provide pay ranges in job postings than ones that do not.
When considering pay transparency in job postings, organizations will also need to prepare for how doing so may affect current employees, and 36% of organizations said this change caused more current employees to ask about receiving a pay raise.
from Page 4
Hard water in the wash wheel will set stains that only scissors effectively remove and cause untold grief while trying to run items across your flatwork ironers.
And, of course, the dreaded rewash cycle usually starts with bad water.
The main issue I have seen with getting this accomplished is that it is so easy to achieve and monitor that nobody wants to look at it. We seem to like to look for super-complicated issues.
This is a devastating issue, but it isn’t complicated.
A good water softener monitored several times daily to ensure it is working properly isn’t hard to accomplish. It just needs to be scheduled into the daily maintenance tech routine.
There are several automated monitoring systems out there that will alarm if your water is incorrect as well.
Most water softeners offer the ability to automatically switch to another tank when hardness is detected. Paying a little more for these systems can pay major dividends down the road in the form of reducing your energy usage and productive labor.
We all like to look and marvel at the shiny machines that can take a waddedup sheet and make it pressed and folded with little effort from production employees.
But don’t ever overlook the old ugly boiler room items that start the whole process off.
That’s where the real savings begin.
David Griggs is director, operations development, for Superior Linen Service in Tulsa, Oklahoma.
BY MATT POE, EDITOR
Technology has infiltrated all aspects of the industrial laundry industry. From automation to sensors, the technology keeps advancing and improving, often providing a benefit to operators.
This is true on the delivery side, as well.
Technological advancements, from telematics to dashcams to handheld devices, are helping laundry route service representatives be more efficient and safer.
American Laundry News reached out to industrial laundry operators for their insights into advancing route service technology. We heard from Thomas Tsolakoglou, route supervisor for Shasta Linen Supply Inc. in Sacramento, California, and Brad Shames, president of American Textile Maintenance in Los Angeles.
What do you consider the most important part of running laundry/linen service delivery routes?
TSOLAKOGLOU: Shasta Linen Supply is a mixed plant with retail medical accounts and food and beverage. We try to balance each route with a combination of accounts, meaning that some are heavy and some are small.
The idea is that we don’t want one driver handling all heavy stops or vice versa, as a balanced route is important from a safety perspective, since there is less opportunity for injuries. It also helps regulate overtime.
We also work hard to keep boundaries on the routes and not have two drivers crossing each other in the same area.
Stop restrictions like timing are also critical when setting up delivery stops.
SHAMES: The two most important parts of running laundry/linen service delivery routes are to create a culture of extraordinary customer experience while always being safe.
How has route planning and safety technology changed over the past several years?
TSOLAKOGLOU: We are old-fashioned and still use a combination of good old index cards along with looking at Google Maps or utilizing a routing program.
We find that writing each account on a
card allows us to mix them up given the restrictions a location might have.
The routing programs that we have looked at put the stops in the most efficient order, but that might not always work due to extraneous variables and the last thing we would want is a driver walking into a restaurant during lunch and trying to lay down mats.
SHAMES: The sophistication of the telematic vehicle tracking system has advanced tremendously in the last several years.
The system we utilize gives us real-time feedback on how safely the routeman is operating the vehicle and how efficiently it is being used. We use that information as a training opportunity with the routemen. What has been fascinating to see is the advancement of the “in-cab” routemen-facing “AI Camera,” which is a part of the telematics system. It can provide real-time safety alerts to the routeman, and we have seen this, firsthand, avoid potential accidents.
How can an operation make the best use of technology?
TSOLAKOGLOU: Technology has changed our industry in so many ways. For example, modern equipment can process our products by detecting stains and holes thus providing a higher quality standard, etc.
The GPS systems on our trucks have really added a new dimension to delivery and driver safety since our drivers are monitored with forward-facing and backup cameras.
Although we have always had a no cell phone use policy while driving, the forward-facing camera has eliminated anyone trying to text or talk while driving.
We can also monitor stop time and how the trucks travel; we want each route to follow the one we have set up.
When we see discrepancies, we can address them immediately.
SHAMES: It is key to partner with vendors that understand your operation and company goals.
There must be internal buy-in from the team that manages this aspect of your operation. The entire staff utilizing this technology must be trained on how to best use the software.
It is important that if you utilize these systems, you must have an ongoing train-
ing regimen addressing the safety issues that may arise.
What benefits does this technology provide for laundries in efficiency and safety?
SHAMES: First off, it helps us to plan. The data gathered by any of our technologies helps us to make better-informed decisions in our overall operations.
Secondly, it helps us to track our safety scores/goals. Because the data is generated, we can measure our safety goals and analyze where we are doing well and where we may need improvement.
Lastly, the technology helps us to stay accountable to each other. It helps our managers and employees to stay focused.
How has the role of the driver changed in terms of route operations?
SHAMES: The driver has become more informed of their driving behavior.
Before, when we did not have any technology to measure harsh driving events, the driver may have thought they were the best driver in the company.
However, with the current technology that we are using it puts everyone on the same playing field, and their success is based on their driving behavior performance. The distance and hours are incorporated into their overall safety driving score.
They know that their managers are aware of their driving behavior and their safety score.
We use this as a motivation for our drivers in our different divisions. No one wants to have the lowest score, and it creates a sound and innocent competition.
We continue to learn and adapt to the upgrades in technology and will continue to provide programs and incentives for our drivers.
What do you consider to be the best method to train drivers in new route technology?
TSOLAKOGLOU: We train a new driver for about a month before they go solo. Customer service is important to who we are and our niche in the market. We also believe that a driver who understands his customers’ needs is watching the shelves, bringing back unused inventory and adjusting delivery amounts.
During the extended training period, they learn the route as we have laid it out in route sequence order. We do not want them Googling their next stop to get to the next location.
Our route stop sequence is built considering all of the variables when running a route and we don’t want the driver to change it randomly.
The driver also learns how to use our handheld. Considering we are paperless, there needs to be an understanding of how to read an invoice and how to discuss any issues with the customer, while also learning what are all the different types of products that are being delivered. This takes time, but using the handheld is probably the easiest part since everyone is already phone tech savvy.
SHAMES: There is not one best method that will help train the drivers with new route technologies, but what we do is address all the different learning styles.
We use visual, auditory and kinesthetic styles to help address everyone as best as possible.
For some it may be a video, for someone else it may be listening to someone in a training course, and for someone else it must be a hands-on approach.
How about training drivers on other route factors, such as efficient vehicle operation, safety and customer service?
SHAMES: The in-cab coaching and the information that is generated by the telematics system help us to pinpoint some of these factors.
With the in-cab, our team may hear a voice that tells them to “increase following distance” or “reduce harsh-breaking.” Other times, they may receive a short training video of a behavior that needs to be corrected, which gets sent to their and their supervisor’s work e-mail.
The coaching and training help the drivers be safe and efficient throughout their day.
We also have onsite safety training that is done in a classroom setting and online training that they may do on the driver app. We usually have visuals, auditory and practical strategies to help them address a safety topic.
We also gather data from their colleagues to help us learn from each other. It may be a good and/or bad example of safety to learn from.
How will electric delivery vehicles impact efficiency and safety?
TSOLAKOGLOU: We recently invested in five electric trucks. We are running them on routes that are local and don’t
travel more than 60 miles in a day. Going electric has already shown us cost savings on gas and a real environmental impact on tailpipe emissions. We have already saved over 40,000 pounds in tailpipe emissions during the short time we have been running the trucks.
Our drivers are proud of this, and they have commented on how quiet it is to drive the truck.
They can hear the surrounding noises more and that is a positive safety feature especially when maneuvering the trucks through crowded urban areas.
SHAMES: EVs have a limited range compared to gas-powered vehicles, which makes the efficient routing of the routeman’s day all more important to ensure the truck can service the customers and be back on a single charge.
Please share anything else you consider important about laundry/linen service route operations.
TSOLAKOGLOU: Our route representatives are the face of our company and investing in their training and giving them the technological tools to succeed is essential to running a more efficient and productive company.
SHAMES: Another aspect that we consider important is the importance of creating a culture that fosters a team-winning culture. When we have our teams working together and accomplishing safety goals or providing stellar customer service, it is a testament to the in-house training that is provided by our HR department or service teams.
THotel/Motel/Resort
Laundry
he standard for reusing and recycling products is a common concern that I often face.
The product we can no longer use is still in good condition and typically has a lot of life left. I strongly encourage donating items to businesses in need, first. We have donated items considered a waste to local businesses, and we allow employees to take items with them for personal use.
If these items have aged out, repurposing for cleaning supplies is a solution that many have used as well.
If either of these options is not available, there are recycling companies that are focused specifically on textile recycling. If these companies use them and operate properly, old textiles can be repurposed in many ways.
I have seen that some recycling centers or companies have made padding for chairs out of these items, for example.
My hope for future textile recycling is that it can become a standard practice.
Hopefully, partnerships can be formed with businesses to ensure that more textiles can stay out of landfills so they can serve another purpose.
AHealthcare Laundry
Jay Juffre
ImageFIRST, King of Prussia, Pa.
s far as textile recycling, Europe is way ahead of North America.
For example, in England, industry leaders came together to launch the Infinite Textiles scheme.
Don’t let the name fool you. Apparently across the pond, “scheme” is actually a very good thing.
The goal was to significantly reduce the annual 6,000 tons of textiles being sent to the landfill every year. The process was basically taking a cradle-to-grave approach for every piece of linen purchased, from sourcing to washing to repair to reuse and to eventual disposal.
Essentially, the organization does everything it can to get the most life out of the linen. Eventually, when it has reached its end of life, it goes to a centralized recycling plant where it is broken down into
“My operation is growing more concerned about textile waste. Where are there opportunities to recycle or reuse aged-out textiles? Have you heard of future recycling developments?”
yarn and sent back to the manufacturers to complete the circle.
Seeing how we produce over 17 million tons of textile waste in the U.S. every year, it is probably where we need to go. And we slowly are.
Some for-profit organizations are looking to capitalize on this opportunity, and with states like Massachusetts starting to ban the disposal of linen and other textiles, there could be a strong market for them.
Some manufacturers have also gotten into the act and offer recycling programs for a little more than what it costs to ship them back the product.
It starts by looking at what you can do.
For example, some companies have repair departments to extend the useful life of a product, but many do not.
Some companies sell their worn textiles to scrap dealers, while others just throw it in the dumpster. And some investigate the recycling programs that are starting to emerge.
If nothing else, donating old products to homeless/women’s shelters, churches and other non-profit organizations is a great first step.
At the end of the day, reusing and recycling textiles will become the norm in this country.
Getting out in front of it is great for the
environment, the community and our industry.
ecycling is a topic that we know quite well.
The only difference is that Streamline Solutions has recycled plastic bags for the laundry industry for about 20 years now and we have recycled over 75 million pounds through the years.
The linen recycling side of it is, no doubt, a different animal as they say. However, there are a lot of similarities between the two types of products when recycling.
For example, certain quantities of product need to be accumulated before it is economically feasible to offer the service to the respective laundry customer.
Both plastic and especially linen must be dry and clear of any types of trash when being “baled.”
On our end at least, when we offer a
plastic recycling program to our customers, the plastic does not have to be separated by the colors or materials, but from what I understand, that is not the case on the linen side of things.
I have heard that certain companies will take different linen-type products together that are acceptable to them, and others want the linen products separated by product before the recycling company comes to pick them up.
I know certain types of linen products that are just not the types that have any value to them when recycled, so they are just thrown away by the laundry.
Like anything else, the market for any product and service will change over time. What could have a high value today recycling-wise may be completely different tomorrow as many factors affect the value of the linen product.
Some of those variables include how good is the quality of the linen that is being returned. Is the pricing/value of the linen higher today due to economic factors or even political unrest?
Factors like these could make the market good today and make it completely unfavorable tomorrow and actually make it where the linen recycling service cannot even be offered to laundry customers
without a charge being passed along.
Regarding what the future holds, it is hard to predict the future and to know what other companies may be interested in pursuing, but what I can say is that my company, Streamline Solutions, is currently in the phase of looking to offer our customers a linen recycling program in the near future.
I would love to get into details but until everything is finalized on our end, it’s hard to say how someone like us can help solve this issue for today’s laundry plants. On our end at least, we are hopeful to be able to offer this service to all laundries in both the United States and Canada.
We know that every laundry has some goal regarding helping the environment and saving money whether it is to recycle plastic bags, linen, water, cardboard or anything else.
Whether it is us or someone else, a linen recycling program would certainly be beneficial to any healthcare, hospitality or industrial laundry company.
Textile waste is a significant environmental issue, and many organizations and technologies are emerging to address it.
Here are some current opportunities and possible future developments in textile recycling and reuse.
Current Opportunities: Charity donations and emergency relief organizations. Organizations like the American Red Cross and various other charities accept used textiles for areas in need of hurricane relief and other natural disasters.
Most areas also have opportunities to sell their worn-out textiles to companies for extended use/life. These companies are
commonly referred to as the Ragman).
Future Recycling Developments: Advanced recycling technologies.
Chemical recycling processes are being developed to break down textiles into their basic fibers, which can be spun into new yarns.
Innovations in mechanical recycling are improving the quality of recycled fibers, making them more suitable for producing new textiles.
Talk to your current textile manufacturers about any current or future programs and opportunities.
Research into biodegradable materials aims to reduce the impact of textile waste.
Regenerative textiles, which can be broken down and used as nutrients for soil, are also under development.
Governments are starting to introduce policies to encourage textile recycling and reduce waste.
For example, the EU’s Circular Economy Action Plan includes measures to improve textile recycling rates.
Industry Collaboration: Collaborations between textile manufacturers, recycling companies and industrial laundries are crucial for creating a sustainable textile ecosystem.
By leveraging these opportunities and supporting future developments, your operation can contribute to reducing textile waste and promoting a more sustainable industry.
The industrial laundry industry is crucial for providing essential services to various sectors, such as hospitality and healthcare. However, it faces challenges related to textile waste.
With large quantities of linens, uniforms and other textiles processed daily, there is a pressing need to address the environmental impact of discarded materials.
Fortunately, there are opportunities for sustainable solutions tailored to the unique operations of each plant.
One way to reduce textile waste is using dyeing techniques to repurpose old or stained aprons, tablecloths or mats by dyeing them black. This helps to conceal stains or imperfections and extends the lifespan of the items.
By incorporating this approach into your laundering process, you can minimize the volume of textiles destined for disposal while maintaining good quality standards and giving new life to old garments that would typically be discarded.
You can do this in-house or outsource this service to companies that specialize in textile dyeing.
Additionally, repurposing textiles in socially impactful ways is a viable option.
This can range from donating unused or damaged terry or garments to a local shelter to sending white sheets to countries like India for cremation rituals.
By being resourceful and thinking outside the box, you will find numerous options to repurpose unused linen, address waste issues and maybe even contribute to noble causes.
Repurposing textiles as rags offers a practical and sustainable solution for industrial cleaning purposes. Instead of throwing away worn-out linens, these materials can be turned into cleaning cloths, which reduces the need for singleuse disposable products for painters, mechanics, or cleaning companies.
Incorporating rag production into your laundry operation not only minimizes waste but also has the potential to generate revenue.
Signs business owners should look for that might indicate vulnerabilities that could lead to violence on company grounds
BY DAVE DAVIS
NASHVILLE, Tenn. — On May 22, tragedy struck the laundry and linen services industry.
A “disgruntled” employee entered Delaware County Linen in Chester, Pennsylvania, with a handgun and shot five coworkers. Two died from their wounds.
No laundry business wants to consider that their workplace could be the scene of violence—either from one-on-one confrontations or something much worse—but the simple act of denying it could happen can set the stage for calamity down the road.
This was the message of Carol Dodgen, owner of Dodgen Security Consulting, during a webinar titled “Staying Safe in a Violent World,” presented by the National Federation of Independent Business (NFIB).
Since 1998, Dodgen’s company has provided services including training, lighting inspections, and security assessments for business and government entities.
She highlighted signs business owners should look for that might indicate vulnerabilities that could lead to violence on company grounds.
“This is kind of a good news/bad news scenario,” she says. “There are so many challenges that we face, and as far as the bad news goes, we’re not going to stop crime. We’re not going to be able to legislate or cause people to obey the laws that we have in place. We can’t legislate people’s hearts and actions. What we can do are things that will make ourselves safer.”
Dodgen has researched hundreds if not thousands of cases of violence during her company’s 26 years.
“I’ve spoken to people who have been shot, stabbed, kidnapped, hijacked and all types of situations,” she says. “My goal has been to try to learn from what they have been through. A lot of times, there are things that were missed. There are things that, when they look back, they say they should have paid attention to them. Sometimes, I’m learning how they survived it. What did it take to survive what they went through?”
She says there are three ingredients to a crime:
1.The desire or motivation to commit the crime.
2.The skills and tools needed to commit the crime.
3.The opportunity to commit the crime.
The first two are out of a business owner’s control, Dodgen says, but the third “is the one thing that we have some control over.”
According to the Centers for Disease Control and Prevention (CDC), more than seven people die a violent death in the United States per hour. In 2019, more than 19,100 people were victims of homicide, and 47,500 died by suicide.
“I know that this has gone up,” she says, “because we’ve seen increases in suicide and homicide over the last couple of years.”
In 2021, the CDC’s National Center for Health Statistics (NCHS) reported that the homicide rate in the U.S. rose 30% between 2019 and 2020. “It is the largest increase in 100 years,” reported Robert Anderson,
(Image licensed by Ingram Image)
chief of the mortality statistics branch at the NCHS, in the announcement.
SUICIDAL DANGERS
Suicide numbers can also impact violent deaths for others, as well, Dodgen points out. She cited a 1994 incident on a FedEx flight. Auburn R. Calloway, a suicidal FedEx employee, attempted to kill the flight crew and hijack and crash the flight.
“He thought he was going to be fired the next day,” she says, “because it had been discovered that he was falsifying records.”
The flight crew successfully fought Calloway off and landed the plane, but had his actions been successful and caused the plane to crash in a populated area, he, the three-person flight crew, and potentially many other people would have been killed.
“He had planned this for months,” Dodgen says. “His planning was in place, and he knew he was going to die. And if he knew he was going to die, he didn’t care how many other people went out as well. So, that’s the short lesson: If someone is suicidal, then they absolutely can be a danger to others. We can’t assume just because someone wants to take their own life, that they’re not a danger to others.”
THE DANGER OF IGNORING SIGNS
One of the first reported cases of workplace violence—and the genesis for the term “going postal”—occurred in 1986. A postal employee, 44-year-old Patrick Sherrill, entered his post office in Edmond, Oklahoma and, in less than 15 minutes, killed 14 employees and injured six before committing suicide. It is still considered the deadliest workplace shooting in the country’s history.
“He was called into his supervisor’s office,
and was reprimanded for something he had done,” Dodgen says, noting that this reprimand was not done behind doors but in front of co-workers. “He was ashamed of this, and that’s something to keep in mind as we talk about handling dismissals and reprimands.”
Dodgen also points out that Sherrill asked one of his co-workers, who he considered a friend, if she was planning to come into work tomorrow—and then said that she probably shouldn’t.
“This is an example of what’s called ‘leakage,’” Dodgen says. “It’s important to recognize these red flags. In so many of these cases, people either brush them aside, don’t report them, and don’t take them seriously.”
These warning signs can be indicators that something is wrong. “You often hear something like, ‘This guy just snapped,’” Dodgen says. “Chances are they didn’t ‘just snap.’ They’ve been on that path for quite a while.”
In the case of Sherrill, his neighbors had reported that he would walk around in camouflage at night, looking into windows, and had a history of taking and torturing neighborhood pets. He had also threatened revenge, according to reports, out of his anger at being disciplined at work.
“One of the biggest questions is, ‘What is the greatest indicator of future violence?’” Dodgen says. “How do you predict future violence? I would look at what they have done in the past. Have they shown this to be a pattern?”
She says that, if you have to deal with one of your employees and have found yourself saying, “I really hate to confront him or her about this because I know how they’ll react,” that can indicate a problem.
Dodgen offered the following observable warning signs that, if noticed, should not be
ignored:
• Violent and threatening behavior and hostility.
• “Strange” behavior, such as becoming reclusive or letting their appearance deteriorate.
• Emotional problems.
• Drug or alcohol abuse.
• Performance problems, including problems with attendance or tardiness.
• Interpersonal problems at work, such as conflicts with others or being hypersensitive.
• Someone “at the end of their rope,” which can include indicators of impending suicide, or an unspecified plan to “solve all problems.”
“In a lot of these cases that I have studied and people I’ve interviewed,” Dodgen says, “I have seen this to be a commonality right before they do what they do: They will withdraw. They will become reclusive. It’s almost like they have reached this point of despair, and the things they cared about in the past are no longer important.”
So, what’s do be done if some of these red flags are noticed?
“We absolutely have to have something in place to deal with this,” Dodgen says. “We need zero tolerance if somebody makes a threat. We have to take that seriously.”
Depending on the situation, dealing with this person can take on many forms.
“If they are exhibiting disturbing behavior,” she says, “sometimes just the intervention—talking to this person, getting a read on
Alliance promotes Endahl to GM in West Region
RIPON, Wis. — Alliance Laundry Systems, a manufacturer of commercial laundry equipment, reports that John Endahl has been promoted to general manager of the Alliance Laundry Systems Distribution West Region South Gate office.
“John has been a proven performer since he joined the sales staff of our Los Angeles area office,” says Craig Dakauskas, senior vice president, Americas Commercial, Alliance Laundry Systems.
“I’m confident he will implement initiatives that will drive continued excellence in customer service.”
Endahl started as a multi-housing and on-premises laundry sales manager with PWS Inc. in 2020 before it was acquired by Alliance Laundry Systems.
Despite the challenges of the pandemic, Endahl and his team delivered excellent results that year through to the present.
Before joining Alliance Laundry Systems, Endahl held several management roles in sales and marketing, including general manager for CompUSA, where he was involved with the first Apple store build-out.
Mitchell returns to Colmac
COLVILLE, Wash. — Colmac Industries Inc., a manufacturer of garment finishers and presses, reports that it has added Jeff Mitchell to the inside sales team.
His responsibility will be assisting dealers and distributors in identifying the proper equipment for their customers and offering suggestions on how to optimize their operations.
Mitchell is returning to Colmac after a brief break. He was a member of the Colmac team for 17 years working with the production department and most recently acting as a service technician.
He is a Universal Technical Institute graduate and has an extensive mechanical and fabrication background.
BEACON FALLS, Conn. — Laundry equipment manufacturer LAVATEC reports that Lisa Thrasher has joined the team as the parts and client services coordinator.
Based in Austin, Texas, she works with members of the company’s parts department to streamline processes and update technology.
She reports to company president Mark Thrasher.
Lisa has worked for a financial services firm and a marketing company since graduating from Roger Williams University with an international business degree in 2020.
It is with heavy hearts that we bid farewell to Rich McKevitt, who passed away on December 7, 2023, after a brief illness. Rich was more than just a colleague; he was a beloved member of our community, known for his wit, warmth, and unwavering dedication.
Rich was not only a consummate professional but also a genuinely kind and compassionate individual. His infectious laughter and quick wit could brighten even the dreariest of days, and his genuine concern for others endeared him to customers and colleagues alike.
Whether he was assisting customers with their inquiries or tackling challenging projects, Rich approached each task with enthusiasm and a can-do attitude. His professionalism and attention to detail were second to none, and his tireless work ethic served as an inspiration to us all.
Rich was a friend and mentor to many, always willing to lend a listening ear or o er words of encouragement. His genuine kindness and generosity knew no bounds, and his legacy of compassion will continue to live on in the hearts of all who knew him.
His memory will forever remain in our hearts, serving as a reminder of the power of kindness, laughter, and friendship. Rich may be gone, but his spirit will continue to inspire us each and every day.
Alongside his professional accomplishments, Rich found his greatest joy in his roles as a loving husband,
She spent the last three years as an advertising account manager at Pushnami, which set the stage for her to join LAVATEC.
“I chose to study international business because I was interested in the work my dad is doing. I always knew I would work at LAVATEC, but I made a point to gain experience from other jobs first so I could learn and use that knowledge here,” she says.
“My time at Pushnami was valuable since it greatly influenced me about technology. The landscape of a tech start-up is so different compared to a traditional corporation like LAVATEC. It really helped me see how technology and software can help the day-to-day work life with organization and the creation of proper processes.
“Things ran smoothly and it allowed us to keep a heavy scope on all the metrics we needed to be successful.”
devoted father, and doting grandfather. His passion for life and unwavering love for his family were evident to all who knew him.
As an avid sports enthusiast, Rich’s heart belonged to the New York Yankees. His dedication to the Yankees was a testament to his unwavering loyalty and his ability to find joy in life’s simple pleasures.
Above all else, Rich cherished his role as a husband and father. He and his wife shared a bond built on mutual respect, laughter, and unwavering support. He also found immense joy in watching his children grow and succeed. He was a source of strength and guidance, o ering unconditional love and support through life’s triumphs and challenges.
The arrival of grandchildren brought light and laughter into his life in abundance. He showered them with love and a ection, cherishing each precious moment.
Rich’s legacy of love, laughter, and unwavering devotion will continue to live on in the hearts of his family, and all who had the privilege of knowing him.
Rest in peace, dear friend.
Continued from Page 14
them and handling it sensitively—can make a difference. If there’s something going on, maybe they’ve had some stressors in their life, a conversation or some kind of help can be rendered to this person, and they can return to being that productive employee.”
There is a spectrum when it comes to workplace violence, Dodgen says, starting at concerning behaviors, and then escalating to threatening behaviors, to physical injury and, ultimately, death.
“What we want to do with awareness and training, which I believe is critical for all employees, is to recognize these things and stop them before they get to that point,” Dodgen says.
“In interviewing people, I’ve heard, ‘We knew this was going to happen’ a number of times. So, we have to do a better job of addressing these concerns. We absolutely have to.”
There are a number of ways violence can enter a workplace, Dodgen says, and listed four types of incidents.
Type 1 — Criminal: The perpetrator has no legitimate relationship with the employer or workplace, other than to enter and commit a crime such as robbery.
Type 2 — Customer/Client: A customer or client of the business directs violence at employees, possibly because of dissatisfaction with the service or product.
Type 3 — Employee on Employee: An employee or former employee perpetrates violence against coworkers, supervisors or managers.
Type 4 — Domestic: Violence is committed in the workplace by someone who doesn’t work there, but has a personal relationship with an employee, such as an abusive spouse or domestic partner.
“Most of us probably think about employee-on-employee violence, because that’s usually what we hear most about,” Dodgen says. “But actually the first type, the criminal type, is responsible for most murders. So, you’re going to be vulnerable to this type if you handle money. This is somebody coming in to commit a crime, such as robbery. So, as we assess our risk, what are we most likely to deal with? We have to put our resources toward that.”
When it comes to angry customers, the most important thing the owner or employee can do is remain calm. “It can be challenging,” Dodgen says, “but it’s important.”
Most angry customers want to feel heard, she says. “Don’t tell them to calm down. That never works. Try to show empathy to this person, and if they think you’re trying to genuinely help them, a lot of times that will calm them down. Identify their needs or wants, and then seek a solution or work through alternatives.”
If the employee or owner finds themselves getting upset, practices like the “combat” or “four square” breathing method—taking a breath for four counts, holding it for four counts, letting it go for four counts and waiting for four counts, and then repeat—can help in this regard.
“What happens when our heart rate goes up and we get scared or upset is that we lose some of our cognitive thinking skills,” Dodgen says. “This breathing helps to slow things down, gets oxygen to the brain and allows you to think better.”
As for the case of domestic violence,
Dodgen says, it can spill over into the workplace because an abusive partner knows the victim’s schedule.
“If I’ve moved into a shelter, or I moved in with friends or family,” she says, “he knows that I still come to work, and he knows that schedule. It’s easier to target me there.”
Leaders should be aware of domestic situations like this, she says, and handle these events sensitively. Leaders who have clear, open lines of communication with their staff are better able to determine when there might be a problem and how they can help.
One situation where violence can become an issue is during employee disciplinary or dismissal sessions, when emotions can run high.
“It’s really important to put some forethought into that,” Dodgen says, “and we need to handle it with as much grace as possible. You’re not trying to humiliate the person.”
Some of the factors that leaders should be aware of in cases of discipline or dismissal, Dodgen says, are:
• Setting — Where are you going to have this discussion?
• Position of Exit — If things go badly, would you be trapped in the room, with the aggressor between you and the door?
• Environment — Are there items in the surroundings that could be used as weapons?
• Second Person Present — Should there be a witness or, in extreme cases, someone there to help defend?
• Alarm Button or Alert System — Is there a way to call for help should it be necessary?
Leaders should also be proactive when it comes to disciplinary or termination discussions.
“When you drag something out, it makes it worse,” Dodgen says. “I spoke to a labor and employment attorney about this, because people say, ‘Well, we’re afraid of lawsuits.’ He basically said, ‘You have a rule. Everybody is made aware of the rule. They
violated the rule. You document it. You do an investigation. And then, you treat everybody the same.’ And then he also added, ‘The threat of violence is always far greater than the threat of a lawsuit.’”
“Our goal is always going to be prevention,” Dodgen says, “and we really need to kind of start with awareness of what’s going on around me. What is the situation? What things are happening?
“Denial is the enemy of preparation,” she says. “You might think, ‘This isn’t going to happen. I don’t want to think about it. That’s not realistic.’ We want to do everything we can on the front end, so that we are prepared.
“Crime prevention is just recognizing risk, apprising that risk and then doing something to remove or reduce it,” Dodgen says.
Some of this removal or reduction of risk is common sense, she says. “We have to know what our current state it. The door doesn’t lock. The window is busted. What is it that we need to fix or remove? What can we do to make ourselves a less attractive target?”
Crime Prevention Through Environmental Design (CPTED) can be a great way to reduce risk and encourage criminals to go elsewhere, Dodgen says. She defines CPTED as the proper design and effective use of the built environment that can lead to a reduction in the fear and incidence of crime, as well as an improvement in the quality of life.
CPTED can use landscaping, lighting and other simple but effective means to increase visibility on the company’s property and parking lot, and give those who mean to cause trouble fewer places to hide. Tending to shrubs that can be hidden behind and trees that can block lighting, as well as using mirrors on blind corners, can limit the ways criminals can lurk in the shadows.
“Different things in the environment can either invite or discourage crime,” Dodgen says. “Be aware.”
Natural surveillance is also a factor in CPTED, which includes not having posters and signs all across windows so that the
interior of the store can’t be seen from the outside.
“If I’m coming in to do harm, I don’t want to be seen from the outside,” Dodgen says. “Criminals are basically looking for the target of least resistance, so you’re looking for things that make you a less attractive target.”
Simply paying attention to your surroundings can be one of a company’s biggest safety factors.
“As people come in, look up, greet them and make eye contact,” Dodgen says. “Sometimes that’s a deterrent, because they don’t want you to look at them. They don’t want you to make eye contact and recognize them if they’re coming in to do something. So that natural surveillance, that kind of meet and greet, can be a big help.”
Thinking like a criminal, Dodgen says, can help determine where areas of risk might be.
“If I’m going to target your business,” she says, “I’m going to look for the easiest place to do it. I’m going to look for the place that doesn’t have good policies, that has overgrown shrubs, that doesn’t have good lighting and that has employees who don’t pay attention. Think like a criminal. Clean up areas and get rid of overgrown landscaping, because that’s going to provide a hiding place for somebody and create ambush points.”
Dodgen says that it can be easy to feel paranoid when thinking about workplace violence, but the key is to have a plan and take as much control over what you can control as possible.
“It’s not paranoia—it’s just having that forethought,” she says. “We know that trained people react much differently from those who are not trained. I like this quote: ‘A person without a plan and a ship without a rudder have a lot in common. They’re both at the mercy of events and conditions beyond their control.’ You don’t want to be the one who is controlled by the storm. Have a plan and take control.”
Dave Davis is editor of sister publication American
It’s important to remember that while these initiatives offer promising ways to reduce waste, it’s crucial to consider solutions that are tailored to the specific needs and capabilities of each laundry plant.
What works for one plant may not be feasible for another, so it’s essential to implement strategies that align with your operational realities.
Unfortunately, textile waste is a very real and significant challenge for our industry, but it also presents opportunities for positive change.
Whether you dye your mats and garments black or explore socially impactful repurposing initiatives, the key is to adopt a solution that is practical and feasible to the specific needs of your plant.
TTextile/Uniform Rental
W. Kirby Wagg
Performance Matters, Sarasota, Fla.
he textile rental industry faces a growing concern over textile waste as sustainability becomes an increasingly important issue.
Recycling and reusing aged-out textiles offer significant opportunities for reducing waste and promoting environmental responsibility.
Several innovative approaches and future developments are emerging, paving the way for a more sustainable industry.
In my over 45 years in this industry at Wagg’s Uniform Services in North Toronto, we were successful with our initiatives— aged-out textiles were repurposed into new products, extending their lifecycle.
For instance, we transformed old linens and uniforms into cleaning cloths, industrial rags and insulation materials. This not only diverted waste from landfills but also created new revenue streams for us.
We collaborated with specialized textile recycling companies to ensure that aged-out textiles were processed and repurposed efficiently. These firms had the technology and expertise to break down fabrics and recycle fibers into new materials for various industries.
At Wagg’s, we donated to charitable organizations. Hospitals, homeless shelters and disaster relief agencies all benefitted from these donations, helping our local community in need while reducing waste.
The healthcare sector presents a significant opportunity for textile recycling.
In a recent interview with Randy and Brian Bartsch of Ecotex Healthcare Linen Service, they explained that Canada is leading the way in the use of reusable personal protective equipment (PPE) in hospitals and clinics.
Canadian hospitals have adopted reusable linens and gowns extensively, in stark contrast to the U.S., where approximately 80% of isolation gowns are single-use disposables. This difference is largely due to Canada’s strong public focus on waste reduction and environmental responsibility.
The disparity in reusable PPE adoption between Canada and the U.S. reflects broader public attitudes toward waste and
environmental issues.
In Canada, there is a strong emphasis on sustainability and reducing waste, which has driven the healthcare sector to embrace reusable textiles.
Conversely, the U.S. market has been heavily influenced by aggressive marketing from disposable PPE manufacturers and a polarized public discourse on environmental policies and climate change.
The textile rental industry has a crucial role in addressing textile waste through innovative recycling and reuse strategies. By leveraging current opportunities and embracing future developments, the industry can significantly reduce its environmental footprint.
Learning from Canada’s success with reusable PPE can provide valuable insights and inspiration.
As public awareness and demand for sustainable practices continue to grow, the textile rental industry must adapt and lead the way in creating a more sustainable future.
TEquipment Manufacturing
Chuck Anderson
Chicago Dryer Company, San Diego, Calif.
here are several opportunities to recycle or reuse aged-out textiles; however, finding the resources to aid in this endeavor can be challenging depending on the city or state you do business in.
In my view, circularity for textiles is not where it needs to be and is hard to scale for many reasons.
Europe seems to be much further along in textile recycling technologies and efforts than the U.S.
Repurposing terry products into cleaning cloths is the easiest and most costeffective way to recycle textiles. One such company, Coachella Valley Rags, collects aged-out or stained terry towels from hotels and commercial laundries and then cuts and sews these discards into highquality cleaning rags sold back to hotels.
CIMA Color Solutions Inc. is another great resource in our industry that takes stained or faded linens, aprons, and mats and uses an over-dye technology with high-pressure dying machines to bring them back to life.
New emerging technologies can separate cotton from polyester, allowing the extracted cotton to be respun into new fiber and the polyester further separated into primary chemicals needed to make new polyester fibers.
Charitable donations are another way to reuse textiles. Check with your local charities, rehabilitation centers, and animal shelters to see which might accept used textiles.
Start a grading system where aged-out textiles can be sold or rented at discounted prices for other uses or where front-ofhouse textiles can become back-of-house items when the time comes.
In closing, I would like to say that prevention can slow the need to recycle. Having a solid wash and rewash/stain program can help.
Also, educating our employees and endusers on handling and care of the rented or owed textiles can go a long way in our efforts to slow textile waste.
ALEXANDRIA, Va. — TRSA, the association for textile services professionals, recently concluded its annual HR, Health, and Safety Summit in Milwaukee.
Professionals from both human resources and health and safety fields gathered for a day of intensive professional development, aimed at enhancing their skills and knowledge.
The event featured educational sessions tailored to each field.
The summit kicked off with a welcome session led by Joyce Marter, mental health thought leader and author of The Financial Mindset Fix
Marter conducted a “mental triage” for the workplace, emphasizing the benefits of positive mental health practices. Attendees learned how fostering a supportive environment positively impacts retention, productivity and overall morale.
Practical tools and resources were provided to address mental health challenges, ultimately reducing accidents, injuries and healthcare costs.
Attendees also received complimentary copies of Marter’s book.
Will Maness of Alsco Uniforms com-
mented that all the material presented in the keynote was extremely applicable to their day-to-day operations.
“It was a great mixture of material presented as well as the opportunity for group discussion,” he says.
In the HR track, Jason Keck, partner at Fisher Phillips, discussed critical updates to
HR laws for 2024. Attendees gained insights into legal best practices to mitigate workplace risks.
Katie Cosgrove, partner at Cosgrove Partners, focused on retaining and developing employees, addressing generational gaps and cultural challenges.
Kortney Overzet, VP of people development and culture at Spindle, shared strategies for employee retention, including recognition programs and the innovative “Work Human” platform.
Lori Stanger, VP of people and culture at Wildman Benefit Group, emphasized aligning rewards with company values and cost-efficient program design.
Safety and health professionals attended breakout sessions, starting with Charlie Edelman, corporate safety director at Unitex Healthcare Laundry Services Inc.
Edelman emphasized safety culture, risk assessments and open communication to mitigate workplace risks.
Colin Giles, regional safety manager at Unitex, joined Edelman on stage.
A panel discussion on chemical safety essentials followed. Cintas executives Stephen Jenkins (director of health and
safety) and Sydney Kelley (ergonomics engineer) engaged the audience in an interactive session on safe ergonomic practices and laundry cart selection.
Brian Varner, owner of Safety Solutions for Healthcare, delivered insights on creating and using safety KPI dashboards.
Maness states, “The summit was a great opportunity to learn about different metrics and dashboards to adequately report and improve safety.”
The summit concluded with two general sessions.
Kriz Mizen, head of loss control at CompScience, explored AI solutions for production ergonomics. Mizen highlighted how AI supports employees by providing real-time feedback, guidance and skill enhancement.
Attendees learned best practices for leveraging AI in production ergonomics as well as the benefits and challenges of AI implementation.
In the final session, Samlane Ketevong, the senior director of certification and accreditation at TRSA, and Varner debuted their plan for a new and improved certification for Safety and Health.
ALEXANDRIA, Va. — TRSA, the association for the textile services industry, recently concluded its second Regional Production Summit and Plant Tour event.
Held in collaboration with WATS (Wisconsin Association of Textile Services), the summit aimed to enhance quality programs and accessibility for all members by bringing them together at a central location within their region.
The event took place on May 1-2 in Milwaukee.
The Midwest Summit commenced with an engaging keynote session by Nancy Roberts, CEO and founder of The DISC Wizard.
Roberts delved into the concept of emotional intelligence (EQ), highlighting the five traits of emotionally intelligent individuals. Attendees gained valuable insights on how to apply EQ knowledge to become more effective leaders.
Roberts also incorporated audience EQ evaluations into her presentation, ensuring a tailored experience.
Jessica Leigh, customer success manager at Spindle, followed with a focus on production managers’ roles in preventative maintenance.
Attendees learned strategies to optimize labor and energy costs by scheduling preventive maintenance during regular working hours. Real-world examples underscored the importance of proactive maintenance practices.
Leigh emphasized the significance of scheduled meetings between production and maintenance staff for organizational efficiency and safety.
Don Bock, an industry consultant, delivered a comprehensive presentation on “Fire Safety: Strategies for Prevention.”
Bock covered common sources of fire in laundries and provided best practices to prevent such incidents. He also discussed various fire suppression systems applicable to laundry facilities.
Christopher Stammer, CEO of Volu Interactive, challenged attendees to reflect on their leadership styles.
Drawing from his experience as a United States Coast Guard licensed Master Captain, Stammer shared real-world scenarios where captains’ decisions impacted outcomes.
An interactive exercise highlighted collaboration and decision-making as essential
leadership skills.
Keith Ware, another industry consultant, explored process improvement and rootcause analysis.
Ware emphasized thinking outside the box and fostering collaborative teams. Attendees participated in a creative challenge, building structures from marshmallows, dry spaghetti and pipe cleaners.
Facilitated roundtables further encouraged discussions on EQ, leadership development and safety.
The summit’s first day concluded with a dynamic panel discussion featuring Doug Roskopf (ITU AbsorbTech Inc.), Chris Gibson (UniFirst Corp.), and Andrew Leonard (Gunderson Group).
Ken Koepper, TRSA’s director of membership and industry relations, moderated the panel.
On May 2, Alsco Uniforms and Superior Health Linens graciously opened their local facilities for guided tours, providing attendees with a tour of their facilities.
First-time attendee Chris Milum, plant manager at Spotless Uniform in British Columbia, found the information and technology shared very useful.
He says, “I look forward to taking much back to implement in my plant.”
The third program in this series will be held on Oct. 15-16 in Newark, New Jersey, for members in the Northeast region.
ALEXANDRIA, Va. — TRSA, the association for linen, uniform and facility services, reports that the Hygienically Clean Certification Portal launched on April 15 as part of the Hygienically Clean Certification Program Enhancement Initiatives.
Hygienically Clean certified plant representatives may now use the Certification Customer Portal for all their Hygienically Clean certification activities.
This includes:
• Online Application Process (new applicants and renewals).
• Certification Dashboard.
• Microbiological Sample Submission.
• Automated Workflows.
“In our pursuit of excellence and maintaining our titanium standard, this portal promises to revolutionize the certification process by providing automatic reminders for quarterly testing and renewals and enabling certification plant contacts to access certification activities at their convenience,” said Samlane Ketevong, TRSA’s senior director of certification and accreditation.
“This portal is a huge technological advancement for our administrative processes.”
Phase two of the Certification Customer Portal will include enhancements to the audit scheduling process and the addition of the Clean Green Certification Customer Portal, which is scheduled for launch in early 2025.
TUCSON, Ariz. — Thermal Engineering of Arizona (TEA), a designer and manufacturer of equipment for the efficient use and reuse of wastewater, energy, and heat, located here, reports that it is celebrating 50 years in business.
“We take pride in engineering solutions for the textile and laundry industry as well
as countless others,” the company says in a press release.
“Our equipment includes, but is not limited to, ceramic filtration, direct contact heaters, heat exchangers, heat recovery systems, pump systems, shaker screen systems, stainless steel tanks, water support systems, etc.”
TEA says its goal is to exceed customer satisfaction by manufacturing reliable equipment designed to maximize customer profits by increasing the effectiveness and efficiency of water and energy use.
“Here at TEA, we want to say thank you to all of you who have helped us grow and evolve over the years,” continues the company.
“We look forward to continuing to create meaningful connections with our partners and customers for many years to come.”
IRVINE, Calif. — Prudential Overall Supply, a provider of reusable image work apparel and related textiles, shares that it is celebrating its 92nd anniversary.
Founded by John D. Clark in 1932, Prudential has grown from a one-man operation to a national brand serving customers throughout North America.
“Our team looks forward, but never forgets that Prudential was founded during the Great Depression,” says third-generation CEO, John Clark.
“Through numerous economic recessions and challenging world events, Prudential has flourished over our 92-year history. Achieving what few companies have ever been able to achieve: national growth, dedicated employees, nearly 30,000 customers, and we continue to reinvent the company by expanding and diversifying our offering.
“We thank every supplier for their dependability, every customer for the trust they instill in Prudential, and we are ever grateful to each employee for their hard work and effort so that we can best serve our customers.”
KENNER, La. — Pellerin Milnor Corp., a laundry equipment manufacturer based here, reports that Pellerin Laundry Machinery was its top dealer performer in Milnor machinery sales for 2023.
“We applaud Pellerin Laundry Machinery for their exceptional performance and dedication to delivering industry-leading solutions and service to their customers,” says Rick Kelly, vice president of sales and marketing at Milnor.
“Their consistent excellence has solidified their position as a leading distributor in the industry, and we are thrilled to celebrate their success.”
The company says Pellerin Laundry Machinery’s leadership in Milnor machinery sales for 2023 reflects its unwavering commitment to its customers.
This outstanding accomplishment highlights the dealer’s dedication to the industry from its entire company, including sales, service, management and all supporting
personnel, Milnor adds.
The company shares that it values its partnership with Pellerin Laundry Machinery and looks forward to continued success together in the future.
Completing the top five dealers for the 2023 sales year are:
• Second Place—PAC Industries, Harrisburg, Pennsylvania.
• Third Place—Steiner-Atlantic Corp., Miami Gardens, Florida.
• Fourth Place—TLC Tri-State Laundry Companies, Valdosta, Georgia.
• Fifth Place—Western State Design, Hayward, California.
Since its founding, Pellerin Milnor says its worldwide dealer network has been a cornerstone of the company’s commitment to exceptional customer service.
The company goes on to say these trusted partners offer strategic laundry analysis, design, layout, equipment specifications and implementation services across the globe.
MIAMI — EVI Industries Inc., a distributor and provider of advisory and technical services for commercial laundries headquartered here, reports that it has completed the acquisition of Dallas-based Ed Brown Distributors.
“With the acquisition of Ed Brown, we add a team of experienced sales and service personnel and new product representations that combined are important to achieving our growth objectives in the central region of the United States,” says Henry M. Nahmad, EVI’s chairman and CEO.
Ed Brown is a distributor of commercial laundry products and a provider of installation and maintenance services to the onpremises and vended laundry segments of the commercial laundry industry.
“As is customary, the company will operate under its existing name and with its current team to provide continuity to customers, employees and vendor partners,” adds Nahmad.
Consideration for the purchase of the company was paid in cash. Terms of the deal were not disclosed.