

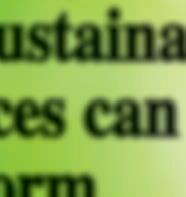
The missing piece is finding the right partner that offers all the services and support you need
BY ARVIN VOHRA
We hear about environmental friendliness and energy efficiency across the business landscape and everyday life (just look at the high-efficiency label on your home washing machine).
Every industry recognizes the value of sustainability for cost savings, increased efficiency, and responsible stewardship— but laundry businesses face unique challenges.
Let’s explore how to navigate the path
to sustainability and transform your laundry operations.
The most significant energy efficiency challenges for laundry companies usually fall into two buckets: optimizing existing systems and technologies and installing new equipment to offset consumption.
You can deploy holistic solutions to achieve your operational goals.
Efficiency Solutions—Solving for sustainability comes down to balancing two things: conservation (using less energy) and efficiency (using equipment more efficiently).
If we look back, LED lighting was the trailblazer for efficiency, but laundries have more opportunities to choose from today.
High-performance industrial laundry machines run long hours, using substantial electricity and power. With the right improvements, a business can boost sustainability and safety, reduce power usage, enhance work conditions, and improve quality control.
Additionally, investing in solar energy can offset electricity consumption. Rooftop solar installations offset up to 50% of electricity consumption per year, and some states offer incentives to fund these projects.
Solution Spotlight—Because Cintas handles delicate products, energy efficiency is vital—from using the best equipment to reducing energy consumption. So, Cintas partnered with Redaptive to retrofit 115 of its 475 locations—7.2 million square feet—with LED lighting on its way to hitting net zero by 2050.
The project yielded outstanding results, including:
• $2.2 million annual gross savings.
• An 18.7 million annual decrease in kilowatt-hours.
• An annual decrease of 7,000 tons of CO2e.
By partnering with Redaptive, Cintas improved its lighting efficiency and elevated morale and safety by providing work environments that help employees focus.
Horsley promoted to VP operations at ALM
Funding Solutions—Customized financing programs give you the resources to tackle large efficiency projects with best-in-class partnerships and interim funding.
The right partner can support energy efficiency upgrades across your laundry business, such as:
• Energy-as-a-Service Solutions: For lighting, HVAC, equipment upgrades and alternative power generation.
• Equipment Financing: Traditional leases and loans for new and used equipment.
Avoid large capital outlays, access multiple funding mechanisms and bypass hidden costs with usage-based, savingsbased or fixed-payment funding options.
Data Collection—Leverage energy data to enhance sustainability reporting and performance analysis. By leaning on expert tools and partner support for reporting, your laundry business can dig into utility data for metered assets, compare performance with industry benchmarks, report Scope 1 and 2 emissions, and more.
Plus, it’s easier to:
• Monitor progress.
• Identify efficiency opportunities.
• Assess a project’s environmental
RICHMOND, Ky. — The Association for Linen Management (ALM) reports Christina Horsley has been promoted to the position of vice president of operations.
Horsley has been a member of the ALM team since 2012, previously serving as director of education and events. In this role, she successfully managed the Laundry & Linen College and notable events such as IMPACT, consistently delivering exceptional results, the association shares.
She brings nearly 30 years of experience in association management to her new role with a history of building and leading teams that significantly enhance member experience and value.
Throughout her tenure at ALM, particularly during the transition to new leadership, ALM says Horsley has demonstrated her ability to contribute positively to her areas of responsibility while showcasing skills beyond her initial scope.
In her new capacity as vice president of operations, Horsley will take on a more strategic role, overseeing all aspects of internal operations to ensure alignment with the strategic goals set by the Board of Directors.
“As I step into this new role as vice president of operations, I am excited to further contribute to ALM’s mission,” says Horsley.
RICHMOND, Ky. — The Association for Linen Management (ALM) reports that Sarah Brobeck, who joined the staff in 2022 as executive director, became its president and CEO effective July 1.
The association’s membership voted to revise its bylaws in early June and restructure its leadership format.
the title of chairman while the chief staff officer will assume the title of president and CEO.
Also, ALM reports that Chip Malboeuf, vice president of operations and engineering at ImageFIRST, has assumed role of chairman of the board; Liz Remillong, vice president of business development at Core Linen Service, was elected as vice chair; and Tiffany Brady, director of customer relations and logistics at West Michigan Shared Hospital Laundry, was elected as a director.
Chris Christie, system linen manager at Ascension Health, was also re-elected as a director.
ALM’s membership voted to revise the association’s bylaws to modernize the organization’s governance structure and enhance the leadership framework.
The Board of Directors’ role has been clarified to become more strategic, allowing it to concentrate on oversight, policy-making and long-term strategy.
As a result of this change, the chief elected officer will assume
In this elevated role, Brobeck will not only drive the association’s strategic initiatives but will represent the association with a keen focus on its growth and development.
She came to the association with more than 15 years of experience working in textile care services, which fortified her business acumen with extensive insight into the industry along with a vast network of connections.
In her first 18 months as executive director, the association says Brobeck led it through two record-breaking IMPACT conferences along with the development of new programs and services designed to provide more value to all members.
She has a rich history in developing teams and fostering individual growth, marked by her strategic vision and empathetic leadership. She has successfully built and managed diverse teams, driving them towards achieving high performance and collaboration.
The association says Brobeck intends to use this experience to build and launch ALM’s future leaders program, which will provide education and mentoring for individuals embarking on their leadership journey.
“Sarah’s passion and dedication to the industry and association,
along with her adept leadership style made her the ideal candidate for the executive director position,” says ALM Chairman Jim Mangini.
“But, her strategic mindset and results-driven approach earned her this promotion to president and CEO. Behind Sarah’s drive, the association is now positioned for unparalleled growth and enhanced member value.”
“I have set ambitious goals for enhancing the value to all members and ensuring the next generation of leaders are well-equipped for success,” says Brobeck. “I’m honored to have the Board’s support behind me as we continue to grow ALM.”
what propels ALM to become even more vital in the textile care services landscape as the premier resource for education and networking.”
“I am deeply honored to ascend to the role of chairman of the ALM Board of Directors,” says Malboeuf. “Building upon the remarkable momentum of the board of directors and the ALM staff, I am committed to advancing our mission and continuing to grow the educational opportunities we offer.
With ALM’s aggressive strategic plan and rapid growth, the association says its new board leaders assume their role in a defining moment for the association.
“Under Chip’s leadership and with the addition of Liz and Tiffany, I couldn’t be more excited about ALM’s direction,” Brobeck says.
“Visionary leaders like them are
“Together, we will strive to help provide leadership development and industry expertise, ensuring ALM continues to be a beacon of learning and development for all.”
“I am so honored to be able to serve the members of ALM,” shares Remillong. “I am excited to work with Chip and the board on all the fantastic initiatives Sarah and her team have been working on.
“It’s a great time to be part of a wonderful organization and am looking forward to all the future offerings ALM will bring to the industry.”
E-Mail:
E-Mail:
When Milnor introduced PulseFlow® technology, CBW® washing was thrust into the future. The idea of balancing time, temperature, mechanical action and chemistry was missing one critical piece of the pie – DILUTION through the efficient use of water.
PulseFlow combines the innovative RecircONE® fast wet down and chemical immersion in the first module with standing bath washing in every spacious process module. Thorough and efficient dilution occurs by way of intermittent high velocity counterflow rinsing and traditional True Top Transfer.
The result is hygienically clean linen using less water (as low as 0.3 gallons per pound/2.5 liters per kilogram) and less energy as proven time and again by hundreds of PulseFlow tunnels in a variety of laundry applications worldwide.
Contact an authorized Milnor distributor or call 504-712-7656 to find out more.
It’s important for industrial laundries to plan for the future.
From equipment needs to industry trends, from customer needs to business expectations, laundry leaders must work to “stay ahead of the game” while meeting today’s production goals.
It’s that “meeting today’s production goals” that always gets me in a bind.
Occasionally, I find myself so buried in today’s tasks that I let future planning slide—which creates headaches for future daily tasks.
It’s vital that I set time aside to plan for future issues and web content, to keep up with what’s going on in the industrial laundry business today and what might happen in the future.
This issue of American Laundry News features some forward-looking content to help you.
One topic that owners/leaders continue to face is sustainability.
The cover story looks at the importance of sustainability in laundry operations and how to make that happen—for the good of the environment and the business’s bottom line.
Another futuristic topic is artificial intelligence (AI) in laundry operations. Also known as machine learning (ML), more and more equipment features data collection and analysis to help improve production and quality.
Turn to page 8 to read more about AI/ ML in industrial laundries.
I’m pretty sure almost every industrial laundry wants to increase pounds per operator hour (PPOH) while maintaining or increasing quality.
To do this, you need quality equipment, products and services, and since The Clean Show isn’t until next year, turn to page 12 for our Exhibit in Print.
In these pages, you’ll learn more about industry suppliers and what they offer so that you can plan for the future.
However, all of the equipment and technology available can’t help future operations if you don’t have the right people. Turn to page 10 for human resources ideas from our Panel of Experts.
All this and more is in this issue to help everyone keep it clean.
Further strengthens presence in Texas market, healthcare laundry provider says
KING OF PRUSSIA, Pa. — ImageFIRST, a national provider of linen, laundry and facility services specializing in the healthcare industry, reports it has completed its acquisition of Imperial Linen Services in Houston.
Terms of the transaction were not disclosed.
“ImageFIRST has a strong presence in the Texas market and acquiring Imperial Linen Services with its 55,000-plus square foot, state-of-the-art facility will further strengthen our position,” says ImageFIRST CEO Edward H. Orzetti.
Imperial Linen Services was founded in 1943 and provides laundry services for the healthcare and hospitality industries, making it an ideal fit for ImageFIRST’s expanding footprint, according to the company.
By integrating Imperial Linen Services into its
operations, ImageFIRST says it will leverage its established framework and customer relationships to deliver enhanced service offerings.
The company says the acquisition enables it to expand its services in Texas and strengthen its regional presence. Existing healthcare customers of Imperial Linen will now be serviced by ImageFIRST, and existing associates will be welcomed onto the ImageFIRST team.
“This partnership marks one of the largest acquisitions in ImageFIRST’s history and will enhance our ability to serve our growing customer base,” Orzetti shares.
“By delivering better quality and support to our healthcare customers, we will continue to set the standard for service excellence and operational efficiency in linen management and facility services.”
No matter which provider you work for, own or operate, differentiating your product and service from the rest of the competition will determine the future health of your business.
Whether you are one of the large nationwide providers or just a smaller local or regional provider, it is important to always work toward being the best.
Since all of us get our product from virtually the same sources, although there are different levels of product design and performance, the difference then must come in the service and processing quality emanating from our plants and the service teams that hit the roads every day. Pursuing excellence in this aspect of the business is the focus of this article, and I hope to spur some thoughts and desires to turn up the effort at your location to be the absolute best at what you do. Let’s review a few thought-provoking points.
Did you ever call some provider and struggle with getting to a live person on the phone? Did you ever call and reach a person who just could not show any interest in helping?
Perhaps they were not the right person with the right responsibility, they got the call by mistake or something, but they just didn’t seem interested in helping you find the right person. That’s frustrating. Excellent customer service starts when the phone rings or a customer walks in the front door. Every employee in the company should have at least some basic training on how to properly address a customer, answer a call if it comes their way and know what to do—even if it is just to drop what they’re doing and find the right person to help.
As a plant manager for part of my career, and later as a heavily traveled engineer, I often encountered customers away from the plant.
First Steps: Offering Value-Added Products, Services
From AmericanDrycleaner.com:
• Battling Burnout at Your Drycleaning Company
• Dry Cleaner Embraces Laundry Ownership for Surprising Gains From AmericanCoinOp.com:
• EVI Industries to Acquire Laundry Pro of Florida
• Alliance Laundry Systems Acquires Star Distributing
Taking down the notes of their issues or needs, getting their contact information and then following up by getting that information to the right person at the right location was an important part of my role in customer service, even though it wasn’t in my title. By having all your employees trained in at least the basics of what to do in these situations, you can begin the process of making your customers fans of your company and keep them for life.
Nothing would chap my hide more than to walk into a plant, my plant or any others I had reason to be at, and see that the plant team didn’t do what they needed. That is, have all the products produced for a given day, ready and loaded out for delivery.
To see route service teams in the plant at 6 a.m. folding towels or rolling mats because the plant didn’t have them ready should cause your management teams to take stock of their focus on the work, systems and processes to track the needs, and finding ways to fulfill those needs.
Being on time with product readiness is critical to getting your delivery teams off on a great start to their day. These customerfacing employees deserve that.
Your delivery personnel, likewise, should assure their customers know when to expect them and live up to those delivery expectations and demands.
EXCELLENT CUSTOMER SERVICE STARTS WHEN THE PHONE RINGS OR A CUSTOMER WALKS IN THE FRONT DOOR. EVERY EMPLOYEE IN THE COMPANY SHOULD HAVE AT LEAST SOME BASIC TRAINING ON HOW TO PROPERLY ADDRESS A CUSTOMER, ANSWER A CALL IF IT COMES THEIR WAY AND KNOW WHAT TO DO—EVEN IF IT IS JUST TO DROP WHAT THEY’RE DOING AND FIND THE RIGHT PERSON TO HELP. See Column on Page 6
Continued from Page 1
impact.
• Verify cost savings.
Collecting and analyzing such information can help your business identify cost savings and develop a roadmap toward net zero.
Prioritizing sustainability is challenging for many laundry companies. Making equipment and infrastructure upgrades may reduce energy consumption, but the added costs of these upgrades are often a roadblock to meeting sustainability goals.
The struggle? Balancing operations with cash-flow-positive projects you can accredit to the bottom line and use to move toward sustainability targets.
Turn the Ship Around—As pressure mounts from investors and shareholders, changing course is like trying to turn the Titanic around right before you hit the iceberg. Many of today’s businesses plan to go net zero, but the roadmap to get there isn’t always clear.
Inefficient equipment loses money, kilowatt hours and sustainability. But if you have limited sustainability staff to oversee projects across hundreds, thousands or millions of square feet, improvements can be slow going.
Such inaction can come off as greenwashing, but the right strategy can help a business accomplish its goals at scale quickly. Installing efficient equipment with a little help improves cost savings and sustainability progress.
Laundry services need to understand the savings potential of sustainability efforts. Being up against limited budgets and personnel shortages to manage proj-
Continued from Page 4
Working with your customers to ensure delivery windows fit the needs of the customer (like not delivering to a restaurant during the lunch rush) will let your customers know you are committed to helping them be successful in their business as well as yours.
PROVIDE A FIRST-CLASS CUSTOMER EXPERIENCE
Never forget who pays the bills. This can get lost in the day-to-day work we all do, but it is the customer who provides the revenue for us to run the operation, pay for maintenance and new equipment, and provide job security. Consequently, every interaction with your customer needs to leave them with the feeling that they are important, that they matter and that you appreciate them. Anything short of that and you’ve failed. Dropping a delivery and running
ects often clouds the bigger picture, but both are easy to overcome with support.
Laundries often fall short in one or more areas required for large-scale proj-
without taking those few precious minutes to visit with the customer to ensure their needs are being met is simply a fast lane to lost business.
Volumes can be written and taught about customer service, building rapport, systems and process design that is customer-focused, and the training involved in this aspect of the business.
But the bottom line is that every employee, no matter what role they fill in your business, must ensure that customers are held in the highest regard and are the reason we exist.
Growing your business depends on that!
Tommy Cocanougher is retired from a 30-year career with Cintas Corp. where his roles included plant management, general management, safety and engineering. Prior to joining the laundry industry, he worked 14 years in the sporting goods manufacturing industry as plant manager and engineering manager for Zebco Corp.
ects:
• Expertise.
• Funding.
• Manpower.
Unlock New Funding Sources—Alone, your budget may run out, but partnering with the right organization can provide virtually unlimited funding to improve sustainability.
Instead of capital on a balance sheet, partner money goes as an operating expense, just like a utility bill.
For instance, smart metering measures usage and savings reflected by variable monthly billing so it can be treated as an off-balance sheet expense.
Increase Manpower and Expertise
Laundries with multiple locations often struggle with limited manpower or bandwidth when a project requires engineers and procurement support across their portfolio.
This becomes a double-edged sword because without people to develop projects, you don’t have a project to finance.
But doing more with less or pressing pause on your efforts aren’t your only options. Supportive partnerships can help you manage and implement projects and make sustainability achievable.
Working with a strategic financial partner presents significant monetary and energy savings opportunities for laundries.
Rapid scalability and deferred payments help your
business shift from being able to handle a few projects a year to many projects and reach sustainability goals sooner—just by borrowing labor and money, which can be paid back with the energy savings generated.
ELEVATE YOUR SUSTAINABILITY WITH EXPERT RESOURCES
Is sustainability shifting into focus?
Improving your laundry business’s efficiency is possible, whether you need help with funding, manpower, expertise—or all three.
The missing piece is finding the right partner that offers all the services and support you need, from fully funded project and program management to proven performance and bottom-line results you can see firsthand.
As a result, you’ll enjoy increased efficiency and cost savings for your laundry operations—all while being a friend to the environment in the process.
Arvin Vohra is the CEO of Redaptive Inc., which he co-founded in 2014. Previously, he was the vice president of project finance at Enlighted, where he created and ran its Lighting-as-a-Service (GEO) platform, which spans multiple Fortune 500 companies and millions of square feet installed. Before joining Enlighted, Vohra spent five years at Barclays Capital on its power and utilities team.
Ways to use a laundry machine’s information to improve efficiency and PPOH while improving the retention quality of processed linens and personnel
BY CLIFF BEISER
KISSIMMEE, Fla. — Consider a quote from J.W. “Bill” Marriott Jr., chairman of Marriott International Hotels and Resorts: “I have never been satisfied with anything we have ever built. I have felt that dissatisfaction is the basis of progress. When we become satisfied in business, we become obsolete.”
Having worked for Marriott both as an employee and contractor, I can personally attest to Marriott’s never-ending pursuit of quality.
What are the three biggest enemies of innovation? Resistance to change, justifying the cost and lack of impartial information to educate all the stakeholders.
How important is change today? Consider the eagle as an example of how important it is to change. An eagle can identify a rabbit a mile away, thus, eagles must know where their prey will be and not just where they are currently to be successful in the hunt.
Artificial intelligence/machine learning (AI/ML) can and is already providing this same ability to laundries worldwide.
This article investigates using AI (machine learning) by using the machine’s information to improve efficiency and pounds per operator hour (PPOH) while improving the retention quality of processed linens and personnel that flow throughout the entire laundry.
How to choose and use the best tool and use it correctly is the key to harnessing this success.
Where there is data there is opportunity (“ML Learns from data to predict outcomes,” Eric Siegel, Forbes, 3/25/24).
We all love benchmarks and want “The Answer.” This is impossible due to each laundry being unique in both layout and equipment. What we can know is how close to peak efficiency we are for our laundry at present.
Whatever type of equipment we use, we need to know the maximum number of pounds we can produce in an eight-hour shift. AI/ML can provide an on-demand status report and where possible bottlenecks are currently and can even predict, with high confidence, what station likely will show a bottleneck soon.
Putting time, attendance and PPOH goals into the peak efficiency formula provides a continuous monitoring of the flow required to meet production and financial requirements.
Shane Suda, the vice president of operations and supply chain at Bay Towel was asked, knowing his interest in Lean Six Sigma, where he sees the intersection of AI and Lean in day-to-day operational life managing the laundry operation.
“Scheduling is a key component that will be helped by AI,” he answers. “More analytics will help laundry companies operate more efficiently. We use a third-party system to track results currently.”
We can see this illustrated in a labor vs. budget calculation.
What does one minute of lost time equal for a plant processing 10 million pounds per year? At 14 cents per pound labor and 10 million pounds per year working an eight-
hour shift five days per week, this equals $11.22 per minute or $673 per hour.
A key ingredient to increasing PPOH in laundry is more efficient scheduling.
Just imagine what AI can accomplish in not just scheduling how many people are necessary but the exact point in time they should arrive at the station. This will improve the flow of the laundry (flow of staff and flow of linen).
Laundry machines have been linked together for some time. Marien van Bezooijen of Gotli Labs explains in a 2022 CNET article, “The focus is currently mainly on the lean side, machine learning real-time links, and information available just in time.”
Retrieving data acquisition, either manually or by writing a small program, directly from equipment has become a key component of using AI/ML in industrial laundries in Europe and more recently in the United States. It is applicable with all sizes of laundry and laundromats that are performing commercial/resort laundry.
“In general, the more data a machine learning algorithm is given, the better it performs,” (“IFR Shares Top Five Robot Trends of 2024,” Automation.com).
A simple example of this is flipping a “fair” coin. There is a 50% chance you will get a head with each coin flip.
However, after five flips you might end up with four heads, yet, as you flip the coin 1,000 times, you will end up at 50% or very close to it.
Just imagine the information your equipment provides such as batch, customer, time started and completed, utility usage, chemical usage, etc. There is so much opportunity as stated at the start of the article.
A current tool being used to increase PPOH and improve employee efficiency is to stagger employee start times which softens the production backlog between stations (Theory of Constraints) (Lean Six Sigma).
Using linear regression taken from the machine’s usage times to pinpoint backlogs that inhibit the flow through the plant or
laundry space (“Achieving PPOH Increase Goals in 2024 (Part 1)”).
I asked Seth Twarek, a laundry consultant at Western State Design what roadblocks, if any, are holding back AI adoption in commercial/industrial laundry.
“Affordability of technology in an already stressed financial environment,” he says. “In addition, workforce education will be vital to widespread adoption of AI.”
Due to his vast experience in current equipment specifications and the latest innovations, I followed up with this question where he sees the most opportunity to use the equipment data that can be accessed to provide ROI info for the plants using AI/ ML as their tool.
“Ability to reduce labor costs and improve quality control,” Twarek shares. “It will reduce rewashes as well due to immediate feedback of data from the machine.”
One of the founding fathers of efficiency and quality, Edwards Demming, summed up why we should be open to change: “It is not necessary to change, survival is not mandatory.”
The point is clear, we must see quality not as it is, but as what it can become. Every laundry, no matter the size, can supervise the production flow in real-time, tracking batches of linen and finding bottlenecks before they occur.
Linen loss is estimated between 17-33% of the total laundry costs, depending on what source you use. During my decades of managing resort laundries, this line item was vital to ensuring profitability for the entire operation.
Labor efficiency was paramount, and limiting linen loss was the topping on the dessert. Whether you own the linen and terry or are processing it for a client, there are two absolutes.
First, they want their laundry returned and not someone else’s. Second, the customer expects you to take great care of the
linen and minimize loss.
Regarding this vital subject, I asked Don Ward, CEO and founder of Laundris what roadblocks, if any, are holding back AI adoption in commercial laundry.
“Education is vital to improve depletion rates along with identifying proper circulation patterns of linen,” he says. “New and emerging technologies, such as Laundris’ patented Precision (IoT + AI/ML) Tech Platform, allow you to see relevant business data in real-time.
“In most cases leveraging an automation inventory and asset tracking platform such as Laundris dramatically reduces costs associated with loss by up to 30%. Especially as it relates to older generations of technology that were utilized in the marketplace.”
Using machine data and applying ML, we gain vital information on the number of times linen and terry are processed and can track new and in-process linen and terry life-cycle costing of each piece.
A small example is a 30% gain on a $250,000 purchase. The bottom line is savings of $75,000. Stephen Few, a leading data visualization expert and visionary wrote the following: “Numbers have an important story to tell. They rely on you to give them a voice.”
In conclusion, “Two engineers were watching a flock of birds. They watched the formation and decided to study why birds flew in a particular V formation.
“What they found was extraordinary because due to the momentum and system of flight as a flock, they gain something close to 70% greater flying range than if they were flying alone,” (Speakers Library of Business Stories, Anecdotes, and Humor, Joe Griffith).
Imagine your laundry operation using AI/ML to flow with ease and accomplish what the birds know instinctively.
It is possible today.
Cliff Beiser is principle of Champions Touch. He was a general manager/regional vice president of multiple hotels/resorts where he trained in laundry operations.
HR strategies for laundry growth
Most of the world has struggled for the last couple of years to find and retain good employees.
With unemployment rates still at historic lows, workers have the upper hand in demanding higher wages and more perks. To find and retain good employees need to be creative and pay more than you may be accustomed to.
First, to maximize your hiring efficiency, you need to disqualify to find the right fit. This may sound funny, but it saves both the employer and applicant time and money. Make sure your job advertisements are honest, and honesty builds trust, right? Don’t use generic templates sourced online. Write a job ad that is specifically tailored to the position, listing both the pros and cons of the job, work environment, pay scale, and often overlooked company culture and values.
Filling certain positions can benefit from a skills-based job posting rather than requiring credentials. Requiring degrees or certain credentials can eliminate a lot of good candidates.
Onboarding and orientation are very important to make sure an employee stays on for more than a couple of weeks. Make sure your company has a solid plan for this and sticks to it.
You have already invested the time and money to get the employee in and if that employee does not feel welcomed and feels like you are not willing to invest in them, they will quickly move on.
I have seen this happen where an employee is thrown to the wolves without direction or maybe paired up with the wrong mentor and it rarely works out.
Feedback on performance is very important to most people, make sure you are regularly communicating with your employees on their performance and guiding them if they need professional development in a certain area.
Over the last year, I have seen a huge uptick in employee spotlights and recaps of employee appreciation parties on social media. This may be a good way to say thank you for a job well done and a good way to engage and retain your employees. Consider flexible schedules, remote-work or hybrid options if the position warrants. This is not necessarily a bad thing if done correctly, and more of today’s workers are looking for work-life balance benefits.
Human resources (HR) should be instrumental in developing plans for pro-
fessional development and opportunities for advancement, which are very important for employee retention.
Performing “stay interviews” is more important than ever to gauge where employees stand on specific issues and overall workplace satisfaction. These should be done quarterly if possible and yearly at minimum.
If an employee does resign, make sure to conduct an exit interview to find out the reason(s) the employee is leaving. You may learn valuable information to tweak your operations for better employee retention.
Ithink the primary thing a company can do is understand the diversity within their population, especially the minority groups and vulnerable populations.
What are the challenges your staff face in their community or at home, and what can you do, as an organization, to alleviate some of those challenges?
Does your organization offer childcare assistance, public transportation, flexible work schedules, social programs or translation services? Does your staff have multi-generations at home and must care for aging parents?
Understanding the needs of your community and population is the first step to employee hires.
“Our laundry is growing but faces challenges in hiring and in employee retention. What can our human resources department do to help facilitate our growth?”
including some sort of job shadowing, so they fully understand the expectations.
And finally, follow the golden rule of hiring: past performance predicts future results. If someone has had four jobs in the past four years, your company will probably just be another one they will shortly leave.
When it comes to who you are hiring, make sure you have high standards for the people you are bringing to the team. No one wants to work with duds, and bringing on weaker employees only discourages the stronger ones.
Now that hiring issues have either been addressed or confirmed as good, let’s look at retention.
To me, this is all about how you treat your team. Get to know them as people. Find out what would make working at your company even better.
Get them to talk about why they choose to stay and what might create a situation where they would leave. Set up potential career paths for those who want it.
And involve them in ways to make the job better.
Additionally, focus on the staff you currently employ to improve retention.
Do you honor the multiple customs and cultures of your team, allow them time to eat and socialize in a manner they are accustomed to, and make the work environment a place where they are comfortable and at ease?
This is an area I am particularly passionate about. Finding and keeping great people seems to be a continuous challenge for many within and outside our industry.
Generally, when I start talking with owners or operators, I get a lot of excuses. “We can’t find enough good people” or “You don’t know what it’s like in (fill in the city).”
A good way to address this is to objectively look at how well the team is hiring. The 90-day survival rate is a quick and easy way to do this. This number typically tells the story and is a great place to start.
If a high percentage of new hires are making it to the three-month mark (say above 85%), you can feel confident that your hiring and onboarding process is solid. However, if a low percentage of folks you bring into the company make it to that point, there are opportunities to improve your hiring process. Have people interviewing candidates dig a little deeper. Ensure that candidates go through multiple interviews,
At the end of the day, hiring right needs to have a process that supports it. Once you have a great employee, work extremely hard to keep them.
To help your laundry grow and tackle hiring and retention challenges, your HR department can adopt several practical strategies.
Start with a comprehensive recruitment plan utilizing social media, job boards and employee referrals to attract candidates. Highlighting your company culture and benefits will make your business more appealing.
Improving onboarding and training programs is crucial. Streamline the onboarding process to help new hires settle quickly and offer regular training sessions to keep skills sharp.
Foster a positive work environment by encouraging open communication and recognizing achievements.
Offering competitive compensation and benefits is essential. Conduct market research to ensure fair salaries and consider perks like flexible scheduling, wellness programs and professional development opportunities.
Develop retention strategies by seeking regular feedback, addressing concerns and implementing recognition programs.
Analyze turnover trends to understand why employees leave and create targeted strategies to address these issues. Boost engagement with team-building activities, social events and wellness initiatives. Flexible work arrangements, such as remote work options or compressed workweeks, can meet diverse employee needs. Implement a mentorship program where experienced employees guide new hires, encouraging knowledge sharing and skill development. Stay current with industry trends to ensure your HR practices remain effective.
By adopting these strategies, your HR department can significantly contribute to your laundry business’s growth and help overcome hiring and retention challenges.
EUniforms/Workwear
Manufacturing
Duane Houvener
ADI-American Dawn Inc., Los Angeles, Calif.
xpanding businesses often face significant challenges in hiring and retaining employees. Your HR department will play a vital role in addressing these challenges. Here are some effective approaches to consider:
Develop a strong marketing campaign directed to future employees with:
•Employer Branding: Highlight your company’s culture, values and growth opportunities to attract talent.
•An Online Presence: Use social media to showcase a positive workplace. Improve job descriptions and outreach through:
• Clear Job Descriptions: Write precise job descriptions to attract suitable candidates.
•Diverse Recruitment Channels:
Use multiple recruitment channels, including job boards, social media
and industry-specific sites.
Streamline the hiring process with the following:
• An Efficient Interview Process: Ensure a quick and efficient interview process to avoid losing candidates to competitors. Consider the use of an applicant tracking system (ATS) to streamline the hiring process, manage applications and track candidate progress.
•A Positive Candidate Experience: Provide a positive candidate experience by maintaining clear communication and prompt feedback.
Competitive compensation and benefits involve:
•Market Research: Regularly review compensation and benefits against industry standards to ensure competitiveness.
•Customized Benefits: When possible, offer flexible benefits tailored to employees’ needs (e.g., remote work options, wellness programs).
Career development opportunities include:
• Training Programs: Invest in continuous learning and development programs for current and future employees.
•Career Pathing: Provide clear career paths and opportunities for advancement.
•Engagement Platforms: Utilize platforms for employee feedback, recognition and communication to boost engagement and address concerns.
• A Talent Pipeline: Build a talent pipeline through internships, partnerships with educational institutions and networking.
Regular check-ins should include:
•Performance Reviews: Conduct regular performance reviews and one-on-one meetings to discuss goals, progress and concerns.
•Feedback: Create mechanisms for continuous feedback to understand employee needs and make necessary adjustments.
Transparent communication should
include the following:
•Company Updates: Keep employees informed about company changes, policies, and achievements to foster a sense of belonging.
• Employee Surveys: Conduct regular employee surveys to gather insights and take actionable steps based on feedback. Implementing these strategies can help your HR department support your company’s growth by attracting the right talent and fostering a positive and engaging work environment.
ECommercial Laundry
Rodrigo Patron
Lace House Linen, Petaluma, Calif.
nsuring employee happiness and satisfaction in the workplace is crucial for the success and stability of any laundry plant.
One of the key factors in achieving this is offering employees something they genuinely appreciate and value. Whether through perks, benefits or a supportive work environment, understanding and catering to employees’ preferences can significantly enhance morale, productivity and retention rates.
Direct communication is one of the most straightforward ways to gauge what employees appreciate. Weekly meetings, suggestion boxes or casual conversations can reveal insights into what matters most to your team.
For some, it might be flexible working hours that allow for better work-life balance. Others may value health and wellness benefits, bonuses or having a say in what kind of food will be served at a company event. By actively listening to employees’ preferences, employers can tailor their offerings to match these needs effectively.
Moreover, offering benefits that align with employees’ interests can foster a sense of appreciation and loyalty. When employees feel valued through personalized perks, they are more likely to feel
motivated and committed to their roles. This, in turn, can lead to higher job satisfaction and lower turnover rates, saving the organization time and resources that would otherwise be spent on recruiting and training new staff.
Creating a positive work environment goes beyond tangible benefits. It encompasses factors like company culture, recognition for achievements, and opportunities for growth and development.
Employees who feel respected and acknowledged for their contributions are more likely to engage actively in their work and stay committed to the organization’s goals.
Offering benefits that employees like also contributes to a more inclusive workplace culture.
Recognizing and accommodating diverse preferences and needs can make employees from different backgrounds feel valued and respected. This inclusivity promotes a sense of belonging and boosts overall morale within the team. From a business perspective, investing in employee satisfaction yields long-term benefits. Happy employees tend to be more productive, creative and collaborative. They are also likely to become ambassadors for the organization, positively impacting its reputation and ability to attract top talent.
In today’s laundry job market, where skilled professionals have many employment options, our plants need to set themselves apart not only through competitive compensation but also through providing high-quality workplace experiences. In general, companies that prioritize employee happiness often have an advantage in recruiting and retaining talent. Ultimately, the importance of offering employees something they like and want cannot be overstated. It enhances employee engagement, satisfaction, and retention—all critical for organizational success. By understanding and meeting employees’ preferences, employers create a more
See Experts on Page 16
The Clean Show is usually the one place and time in the United States where laundry manufacturers, suppliers, managers and operators can come together to check out the latest products, services and more.
But the next Clean won’t take place until next year. How is a laundry industry professional like you supposed to stay on top of the latest goings-on in laundry and linen?
Not to worry, you can tour a “show floor” here this year in the pages of American Laundry News—the Exhibit in Print! Call it a “trade show you can fit in your briefcase.” Or a “trade show that won’t hurt your feet.”
The Exhibit in Print is set up so that you can take a seat, maybe even kick back and put your feet up, and tour the “trade show floor” from the comfort of your own desk.
The “booth” articles have been submitted by the exhibiting companies. Any claims made in Exhibit in Print are those of the participating companies, not American Laundry News Let’s visit the Exhibit in Print floor!
As a global leader with equipment in laundry operations around the world and more than 8,000 machine installations in the United States alone, Lavatec says it is known for manufacturing reliable, custom-engineered equipment that delivers total cost of ownership on your investment.
Many customers have high-performing equipment that continues to deliver outstanding results after more than 25 years of service.
When it comes to simple design, user-friendly operation and low maintenance, start with the energy-efficient continuous tunnel washer systems that offer center transfer, bottom transfer and double-drum construction options.
Many customers are saving thousands of gallons of water a day and improving plant efficiency with reduced run times and utilities savings.
A full range of integrated, end-to-end laundry system components includes front-loading washer-extractors and extraction presses such as LAVAPress ULTRA. It improves workflow and conserves resources by handling 265-pound loads with up to 60 bars of pressure.
Lavatec’s TT transfer-batch dryer machines help extend linen life, and the unique three-tiered LAVACascade continuous drying system recovers and re-uses waste heat with impressive energy savings.
All of these machines, plus the LAVARAIL conveyor system and finishing equipment, can be controlled by the OS Laundry management system, which maximizes performance and saves time with real-time data.
Lavatec also installs remanufactured equipment, provides high-quality commercial spare parts and consumables for over 20,000 machines worldwide via the NewChapterParts e-commerce website, and has a highly experienced Service team available 24/7 to resolve any issues. www.lltusa.com 203-632-8777
Pellerin Milnor Corp. is a leading manufacturer in the commercial laundry machinery industry.
Featuring one of the widest varieties of equipment, Milnor says its machines are ideal for any laundry and have been successfully implemented in healthcare, hospitality, food and beverage, and linen supply applications around the world.
Small washer-extractors range in size from 25- to 170-pound capacities and can be paired with comparable M-Series dryers. Larger washer-extractors can handle loads from 220- to 700-pound capacities and are easily matched with the Industrial Dryer series.
Barrier machines for healthcare and cleanroom markets are available in 60- to 700-pound capaci-
Miele Professional, a global leader in stateof-the-art, commercial-grade appliances, recently inaugurated an advanced technology training facility at its headquarters in Princeton, New Jersey.
The center further demonstrates Miele’s commitment to excellence in service and sales through comprehensive training and development for customers and partners, according to the company.
“We are thrilled to open our new training facility, which offers a comprehensive environment to fully experience our products,” says Scott Lombardi, U.S. Country Director, Miele Professional.
ties as well. Machines feature a variety of control options that offer users varying degrees of flexibility.
Milnor also specializes in continuous batch washing equipment with its PulseFlow® technology tunnel system.
PulseFlow technology offers low water consumption, enhanced chemical performance, low energy usage, and faster washing by combining True Top Transfer with standing bath washing and high-velocity intermittent counterflow rinsing in every process module.
PulseFlow tunnels can process 7,000 pounds per hour or more and can be incorporated into an automated wash system by including Milnor’s extraction devices, pass-through dryers, additional materials handling equipment, Mildata® computer network and Mentor® controls.
Milnor says its machines offer unprecedented wash quality and have a proud legacy of durability.
www.milnor.com
504-712-7656
room space for technical support group meetings.
“The state-of-the-art center enhances learning through advanced tools and resources that allow for effective troubleshooting and additional support and exemplifies our ongoing commitment to maintaining the highest service standards and product excellence.”
The facility is fully operational with running water and electricity for demonstrations and handson training, with specialized areas for laboratory, dental, laundry and dish units, as well as conference
As commercial laundries evolve, diversifying product programs is crucial to staying competitive and meeting client needs.
Previously overlooked, the integration of a menstrual care product program is now essential, providing significant benefits and elevating a laundry business to a comprehensive facility maintenance provider.
Legislative efforts to improve access to menstrual care products are growing.
In the United States, 30-plus states have enacted laws to increase access to or require menstrual products in public schools and other public spaces. New Jersey was the latest state to mandate schools to provide
The new training center is a strategic and significant investment in Miele’s future. By providing a dedicated space for learning and development, they hope to foster a culture of continuous improvement and innovation that benefits its stakeholders.
Customers and partners will receive comprehensive training that enhances their experience and satisfaction with Miele products, and employees can receive product and service training in an environment that empowers them to provide the high standards of service Miele is known for worldwide.
www.mieleusa.com/p/ 800-991-9380
menstrual products in all bathrooms.
Restaurants, hotels, gyms and corporate offices that provide this convenience for their patrons, foster loyalty and repeat business. Commercial laundries have the infrastructure to handle the logistics of supplying and replenishing hygiene products.
Adding menstrual care items to their offerings is a natural extension, leveraging existing know-how and distribution networks.
The Optimal 1-2-3 System, from Monarch Brands and Hospeco, eliminates the guesswork of getting started. Simply choose a dispenser, vended products and a sanitary disposal unit.
These items are as integral to a well-appointed public restroom as toilet paper, paper towels and soap.
Adding menstrual care programs to commercial laundry services increases revenue, boosts client satisfaction and demonstrates social responsibility. This innovative strategy can set businesses apart in a competitive market, driving sustained growth and success. www.monarchbrands.com
Tingue, a provider of laundry parts and supplies, has expanded its product offerings and introduced “How-To” video resources on shop.tingue.com, its innovative E-Commerce platform.
In addition to replacement parts for major industrial laundry machines such as washers, dryers, ironers, feeders, and folders, customers can now access a comprehensive selection of flatwork supplies.
“For over 120 years, Tingue has been dedicated to driving innovation in the laundry industry,” says CEO David Tingue.
“By integrating flatwork supplies into shop.tingue. com and introducing ‘HowTo’ video resources, we’re enhancing our commitment to customer convenience and satisfaction, offering a comprehensive solution for all their laundry needs.”
The inclusion of flatwork supplies simplifies the sourcing process, providing customers with a convenient, one-stop shop to keep their operations running smoothly.
Additionally, the new “How-To” video resources offer their teams valuable insights and guidance for performing routine maintenance and troubleshooting, ensuring optimal equipment performance and longevity.
Ty Acton, Tingue’s president, comments, “At Tingue, we prioritize delivering tailored solutions to support our customers’ success.
“The expansion of our E-Commerce platform and the addition of ‘How-To’ video resources reflect our ongoing dedication to meeting customer needs effectively and efficiently.”
Tingue says it remains steadfast in its commitment to delivering superior service and support to customers.
The expansion of shop. tingue.com, along with the introduction of valuable video resources, underscores Tingue’s ongoing efforts to empower customers with the tools they need to optimize equipment performance and achieve operational excellence. shop.tingue.com 800-829-3864
When dealing with laundry stains, A.L. Wilson Chemical Co. recommends operators get the outstanding results The Laundry Two deliver.
RiteGo laundry spray spotter quickly penetrates to absorb ground-in soil, oils and greases, collar and cuff stains, and more, all without brushing. Then turn to Laundry TarGo to remove any tough oil based stains that remain behind.
Both Laundry TarGo and RiteGo are eco-friendly— California compliant, chlorinated-solvent and NPE free, biodegradable and non-combustible. Use them to deliver stainfree laundry.
www.alwilson.com 800-526-1188
G.A. Braun says its PrimeDry® is an industrial-grade dryer that combines robust performance with a compact design, making it an ideal choice for high-demand laundry processing environments.
Available in processing capacities between 125 and 200 pounds, this dryer sets itself apart with its exceptional throughput and efficiency.
The PrimeDry® gas dryer can handle three loads per hour while the steam dryer manages two-plus loads per hour, outpacing competitor machines that typically only handle one load per hour (processing up to 175-pound loads).
The machine boasts a heavy-gauge carbon steel frame and stainless-steel basket, ensuring longevity and durability even in the most demanding environments.
A side-by-side dryer design reduces floor space requirements significantly, allowing for more efficient use of available space. The top of the dryer is removable, enabling it to fit through standard commercial double doorways for hassle-free installation.
Designed to optimize airflow, the PrimeDry® ensures quick and even drying. The lint drawer is easily accessible, allowing operators to remove accumulated lint during routine operations, maintaining optimal performance.
Equipped with an automatic fire suppression system, the PrimeDry® prioritizes safety in every use.
The touch-screen control panel offers intuitive and user-friendly displays, simplifying operation and programming.
Braun’s PrimeDry® stands out with its combination of efficiency, durability, and space-saving design. Its advanced features ensure superior performance, making it the perfect choice for businesses that require reliable laundry processing.
When laundry is your business, you don’t have time to manage the hassles of production. You want to focus on growing your business and satisfying your customers with clean, fresh, well-laundered uniforms and linens.
You expect a chemical supplier to provide you with products that protect linens throughout the wash process and maximize the efficiency of your capital equipment while streamlining and centralizing the management of the process.
Spartan Chemical says its Commercial Laundry Program simplifies the hassles and headaches of day-today operations making clean simple.
Spartan Chemical Company is a leading national brand manufacturer of superior and cost-effective specialty chemical products, including industrial cleaners, disinfectants, wipes, skincare, food processing, laundry care, ware wash, floor care and commercial vehicle wash products.
Highly focused on supporting the business objectives
As your trusted partner in laundry technology, Kannegiesser ETECH says it is dedicated to developing fully integrated automated equipment solutions for laundry operators globally.
Its commitment lies in fostering strong, reliable relationships, believing that trust is built through continuous support and dependable service. Beyond delivering cutting-edge machine technology, the company says it specializes in crafting solutions tailored precisely to your operational requirements.
Kannegiesser says it stands as a renowned global brand celebrated for its excellence in washing, finishing, and uniform processing systems.
The Kannegiesser ETECH product line exemplifies this legacy with its comprehensive range of logistic monorail and conveyor solutions, complemented by the industry-leading eVue Software. Together, these components form a seamless automation solution perfectly aligned with Kannegiesser’s advanced laundry processing equipment.
The company says its mission extends beyond mere product delivery; it encompasses the provision of end-to-end support, from initial consultation to ongoing maintenance.
By prioritizing customer relationships, it ensures that every solution not only meets but exceeds expectations, empowering laundry operators to achieve efficiency and excellence in their operations.
At Kannegiesser ETECH, innovation is not just a goal but a commitment to revolutionizing the laundry industry through reliable technology and unparalleled service, it shares.
The company invites you to explore how its integrated solutions can transform your laundry operations, setting new standards of performance and reliability in the industry.
www.kannegiesser-etech.com
612-733-1366
of owners and operators of industrial laundering facilities, Spartan offers high-quality chemistry, dosing and facility management solutions that will help you increase your profits, delight your customers and consistently deliver clean, fresh linens in a cost-effective way.
Program components include:
Central Dosing System
• Wi-fi or cellular connected
• Custom-built to facility specifications
• Designed for use with tunnel or washer/extractor equipment
Process Management Software
• Facility management dashboard
• Web-enabled reporting and notifications
• Chemistry: Extend the life of your customer-owned or rental linens with responsible chemistry
o No or low VOCs
o No phosphates, silicates, or harsh solvents
o No alkylphenol ethoxylates
o No nitrilotriacetic acid (NTA)
JENSEN says it understands that the growing challenge of hiring staff for a laundry’s soiled sort section adds to the importance of creating solutions that automate this process.
Since Inwatec first launched a soiled sort solution eight years ago, the system has undergone several breakthrough advancements including improving the capacity to over 2,000 pieces per line per hour, incorporating sorting by camera recognition, and adaptions that allow the system to sort flatwork and towels in addition to garments.
The current version is perfectly refined and proven by years of operation and serves as a concrete solution to the manpower challenges faced by laundries around the world.
Inwatec’s soiled sorting system is a modular solution that fully automates the handling of soiled linen. The
o No toxic or persistent components or by-products
o No ozone-depleting chemicals
www.spartanchemical.com
419-887-9329
THOR module singulates items to allow the processing of individual items.
ODIN uses an X-ray scanner to identify potentially dangerous foreign objects hidden in linen and then removes that piece of linen from the production line.
HEIMDAL utilizes RFID or advanced camera recognition to identify linen, and the BIFROST conveyor automatically sorts linen into bins.
There are more than 150 robots being utilized around the world in a wide variety of markets, including Japan, China, Australia, Europe and North America.
Far from a proof of concept, the company says there are JENSEN laundries sorting 99.8% of the incoming linen automatically, and the largest Inwatec system sorts 8,000 pieces an hour.
Is it time for you to automate your soiled sort?
shop.jensen-group.com/jensen-usa 850-271-5959
FRANKFURT AM MAIN, Germany — There are great expectations for Texcare International 2024, organizers shared during a recent press conference.
The live event will again bring the global industry together in Frankfurt am Main from Nov. 6-9.
The driving themes of automation, energy and resources, the circular economy, and textile hygiene will take center stage at the world’s leading trade fair and provide the market with new impetus.
Leading manufacturers from all over the world and from all product areas of textile care have already registered.
Messe Frankfurt expects more than 300 exhibitors from 31 countries to present their innovations to an international trade audience.
In addition to the large, established manufacturers of machinery, chemicals, textiles and equipment, there will also be many new companies, for example from the fields of robotics and IT.
The industry faces major challenges, which will be the focus of discussions at the trade fair. These include climate-friendly processes, rising energy and material prices, and, last but not least, the labor shortage.
“Texcare offers the industry an urgently needed exchange of ideas and will have a significant influence as an important driving force for the coming years,” explains Kerstin Horaczek, vice president of technology shows at Messe Frankfurt.
“We are delighted with the positive response from exhibitors: companies from all over Europe, America and Asia will be presenting the state of the art from all product areas of textile care.
“For all representatives of the global laundry, cleaning and textile service industry, Texcare 2024 is an event not to be missed.”
The companies that have registered include Alliance Laundry, Beirholm, Biko, Christeyns, Danube, Dibella, Domus
Laundry, Girbau, Ecolab, Electrolux, Fagor, Imesa, Jensen, Kannegiesser, Kentaur, Lavatec, LG Electronics, Macpi, Metalprogetti, Milnor, Multimatic, Pony, Renzacci, Sankosha, Trevil, Texfinity, Union and Veit.
The top exhibiting countries after Germany are Italy, the Netherlands, China, Pakistan, the United States, Belgium, the United Kingdom, Switzerland and Turkey.
A survey of exhibitors and visitors in 2023 resulted in a clear vote in favor of a different order of days and a date in autumn.
Texcare International 2024 will therefore open its doors from Wednesday, Nov. 6, to Saturday, Nov. 9. It will take place in Hall 8 and the Galleria.
Thanks to improved utilization of the available hall space, the exhibition area will remain virtually unchanged compared to the previous event.
Texcare 2024 reflects the topics that significantly affect the business of the exhibiting companies, according to Messe Frankfurt.
At its core, it is about the top themes of automation, energy and resources, cycles, and textile hygiene. They characterize the range of products and services on the stands and the specialist event program:
• Automation and digitalization have made textile care processes significantly more efficient. This not only optimizes the flow of goods and data but also replaces strenuous work and streamlines interfaces with customers. There are also solutions for staff shortages. With the help of robots, sensors and artificial intelligence, companies can compensate for staff shortages, automate repetitive work and become more independent and efficient overall. At the same time, employees benefit
from a higher quality of work and new opportunities for development.
• The economical use of energy and resources has become one of the most important objectives in textile care, not just since climate change began to make itself noticeable worldwide. Many laundries and dry cleaners are re-evaluating their processes considering today’s requirements for consumption, emission avoidance and reduction of the CO2 footprint. The question of the energy sources of the future is also becoming increasingly important.
• The cleaning and reuse of textiles is a perfect example of functioning cycles. The continued use of high-quality textiles makes both economic and ecological sense. The industry can also benefit from a circular approach in other respects. In the production facilities, water and energy are largely recirculated. With the help of state-of-the-art technology, they are used sparingly, recycled and recovered. And even at the end of the useful life of textiles, there is a new beginning. Developments in textile recycling are another hot topic at Texcare International 2024.
• Textile care companies have always specialized in the hygienic treatment of textiles. The industry therefore expects
demand for textile hygiene in the healthcare, hotel and tourism sectors to continue to grow.
In addition to the exhibitors’ highlights, the specialist supporting program sets new focuses. Here, the top themes mentioned will also be examined in detail.
The Texcare Forum will contribute to the transfer of knowledge between manufacturers, users and experts on all four days of the fair.
Messe Frankfurt is working closely with its partners, the German Textile Cleaning Association (DTV) and VDMA Textile Care, Fabric and Leather Technologies, as well as other international associations, to develop the content of the conference.
Under the heading “Young Competence,” activities are planned specifically aimed at young people in the industry.
Guided tours will help visitors to discover and categorize the many innovations that exhibitors are bringing to the fair.
In addition, important associations use Texcare as a platform for their own events.
For example, CINET (Comité International De L`Entretien du Textile) organizes its World Congress and presents the Global Best Practices Awards.
Introducing the new Benchmark Machines, built on the foundation of Miele’s world-renowned engineering and technology. With fast, efficient cycles that reduce operating costs and newly integrated user conveniences, there’s never been a better time to simplify on-premises laundry operations.
• Engineered for high throughput OPL applications
• Ideal for hotels, hospitals and senior care facilities
• High durability: tested for 30,000 operating hours
• Short program cycles that reduce energy consumption
• 25 lbs. - 75 lbs. capacity washers
• 30 lbs. - 100 lbs. capacity dryers For fast, reliable and durable reprocessing of textiles and linens, there’s only one Miele clean.
President, owner of Roscoe Co. in Chicago honored for personal service to association, industry
ALEXANDRIA, Va. — TRSA, the association for linen, uniform and facility services, reports that James Buik, president and owner of Roscoe Co. in Chicago, will be honored with its Operator Lifetime Achievement Award at the 111th Annual Conference & Exchange in September.
“I am humbled to be included on a prestigious list of previous award winners, to include my father Donald, and many industry friends and colleagues,” Buik says.
“I have so many to thank, but especially my wife Teresa, who has supported and encouraged me throughout the journey.”
He previously chaired the Strategic Planning Committee and was a member of the TRSA education and UTSA marketing committees.
The award pays tribute to exceptional personal service to TRSA and the industry as nominated by past linen, uniform and facility services award operator award peers and voted on by the TRSA Executive Committee.
Buik has been recognized for engagement in and personal leadership of TRSA and the Uniform and Textile Service Association (UTSA), which served the industry for 75 years and blended with TRSA in 2009.
For TRSA, he was chair (2018-2020) and a member of the Executive Committee (20142022) and Board of Directors (2012-2014). For UTSA, he was chair (2005-2006) and executive (2003-2008) and board (19931995) member.
His dedication to furthering the industry’s best interests has been reflected in other volunteer leadership positions, as he currently chairs TRSA’s Environmental Committee and serves on the Government Relations Committee.
Continued from Page 11
harmonious and productive workplace where individuals can thrive and contribute their best efforts.
This proactive approach not only benefits employees but also strengthens the organization as a whole, fostering a culture of mutual respect, trust and achievement.
ATextile/Uniform Rental
“Jim’s leadership reflects a belief we share that when any operator makes a good impression on their customers, it serves us all well,” says Jim Kearns, current TRSA board chair and COO of Alsco Uniforms in Salt Lake City.
“The more you get to know him, the more you realize he really does have the industry’s best interests at heart.”
In recent years Buik has empowered Roscoe staff to serve on four other TRSA committees, facilitated extensive Roscoe staff participation in TRSA professional development events and led the company in earning Clean Green and Hygienically Clean Food Safety certifications.
TRSA President and CEO Joseph Ricci commended Buik’s hospitality to TRSA groups seeking to visit Roscoe during professional development events such as the Production Summit and Plant Tours, Maintenance Management Institute and Next Generation Executives Roundtable.
“Jim has upheld TRSA members’ longstanding tradition to welcome industry colleagues to view their teams and machinery at work,” says Ricci.
“Roscoe’s company motto is ‘Take Pride.’ Jim and the Roscoe staff enjoy these opportunities to demonstrate their performance excellence.”
President, CEO of Kannegiesser ETECH to be presented honor at TRSA’s annual conference
ALEXANDRIA, Va. — TRSA reports that Phil Hart, president and CEO of Kannegiesser ETECH, Minneapolis, has been honored with the 2024 Maglin-Biggie Supplier Partner Lifetime Achievement Award.
The association says the award is a testament to Hart’s exceptional leadership; his significant contributions to the linen, uniform and facility services industry; and his steadfast dedication to excellence.
“It is a truly unexpected surprise to be nominated for this award,” Hart says. “Many of the names of the prior recipients are people that I have a great deal of respect for and have learned much from. To be associated with those leaders in our industry is truly an honor.”
Since joining Kannegiesser USA in 2004, Hart’s visionary leadership has played a crucial role in evolving the company from a European supplier to a formidable U.S. corporation. His pivotal role in the acquisition of ETECH stands as a tribute to his strategic foresight and the acknowledgment of American technological excellence by Kannegiesser.
As CEO for the past seven years, Kannegiesser ETECH has become a byword for responsiveness and innovation, always seeking ways to make challenging ideas feasible while maintaining sharp business acumen.
Hart’s TRSA leadership positions and accomplishments include:
s the textile rental laundry market expands, businesses often encounter challenges in hiring and retaining skilled employees.
Human Resources (HR) departments play a crucial role in facilitating growth by developing strategies that attract, engage and retain top talent.
In my over 45 years in business at Wagg’s Uniform Services in North Toronto, I have found we must adopt a multi-faceted approach. Here are several strategies HR or “People Operations” can implement to address these challenges effectively.
To attract qualified candidates:
• Advertise job openings on various platforms, including job boards, social media, industry-specific websites and local community boards. This increases the visibility of job postings and reaches a broader audience.
•Promote your laundry business as an employer of choice. Highlight company values, culture and benefits in recruitment materials. Showcasing employee testimonials and success stories can also attract potential hires.
•Implement an employee referral program that incentivizes current employees to refer qualified candidates. Employees are likely to recommend individuals they believe will be a good fit for the company, increasing the likelihood of successful hires.
A lengthy and complicated hiring process can deter potential candidates. HR can streamline this process by:
•Providing detailed job descriptions that outline responsibilities, qualifica-
Revered by his colleagues for creating an outstanding workplace environment and fostering a culture of success and contentment among customers and staff, Hart’s philosophy is that the team should get the credit, shares TRSA.
This exemplifies his modest approach and belief in shared success.
His core principle, “We Do What’s Right,” has garnered him respect from customers and has cultivated a high level of accountability and trust within the Kannegiesser ETECH team. Renowned for his patience and eagerness to educate, Hart engages meaningfully with individuals, remembering personal details and showing sincere interest in their lives. His actions, such as personally ensuring the safe return of ill team members from job sites, demonstrate his faith in his team’s potential and his role as a true leader.
tions and expectations. This helps candidates understand the role and assess their fit.
•Conduct structured interviews that assess the candidate’s skills, experience and cultural fit. Utilize technology to facilitate virtual interviews, reducing the time and resources required for in-person meetings.
•Maintain timely and clear communication with candidates throughout the hiring process. Inform them of their status and next steps promptly to keep them engaged and interested. Employee retention is significantly influenced by opportunities for growth and development within the company:
• Offer comprehensive training programs for new hires to help them acclimate to their roles and the company culture. Ongoing training opportunities for existing employees can enhance their skills and knowledge.
•Develop clear career pathways that outline potential career progression within the company. Providing opportunities for advancement can motivate employees to stay and grow with the business.
• Pair new hires with experienced employees who can provide guidance, support
• Founding chair and ongoing member of the Supplier Partner Council Board of Directors.
• Member of the TRSA Board of Directors.
• Contributor to the Strategic Planning Committee.
• Instructor at the Production Management Institute (PMI) and Maintenance Management Institute (MMI).
• Steadfast supporter of TRSA programs through advertising and sponsorship.
• Host of international plant tours, promoting global industry insights.
• Proponent for team engagement in TRSA events, both in-person and virtual.
• Participant in DEI Committee meetings at the TRSA Legislative Conference.
and knowledge sharing. Mentorship fosters a sense of belonging and facilitates professional development.
Engaged employees are more likely to remain with the company. HR can boost engagement by:
•Prioritizing workplace safety and health. Regularly assess and improve workplace conditions to ensure a safe and healthy environment.
•Organize team-building activities and events that encourage collaboration and camaraderie among employees. Strong interpersonal relationships can improve job satisfaction and loyalty.
•Stay Interviews: This is the most important aspect of employee engagement and will facilitate growth. If you do nothing else, and concentrate on your team, they will become your recruitment mechanism and your company will soar.
By focusing on these strategies, HR can address the challenges of hiring and retaining employees, facilitating the growth of the laundry business.
An initiative-taking and strategic approach to human resources not only attracts and retains top talent but also creates a robust foundation for sustainable growth and success.
CDC’s leading PPE expert calls for legislative, regulatory changes for more use of reusable products
ALEXANDRIA, Va. — A workshop convened by the National Academies of Sciences, Engineering, and Medicine (NASEM) has recommended greater use of hygienically clean reusable personal protective equipment (PPE) in hospitals and other healthcare settings, according to the official proceedings of the workshop.
Sponsored by the Centers for Disease Control and Prevention’s (CDC) National Personal Protective Technology Laboratory (NPPTL), the workshop brought together technical experts, policymakers, manufacturers, healthcare providers, industrial laundry operators and other stakeholders to examine the safety, environmental sustainability and cost-savings of reusable PPE and to propose opportunities to increase its use.
During the two-day event, Dr. Maryann D’Alessandro, the government’s leading PPE
She pledged to “identify partners” who can help advance the legislative and regulatory changes that will be needed to “increase the use of reusable PPE.”
“The National Academies brought together an incredible group of experts who made clear that greater use of hygienically clean reusable textiles in healthcare must be a national priority,” says Joseph Ricci, president and CEO of TRSA, the association for linen, uniform and facility services, after the release of the workshop’s proceedings.
“Reusable scrubs, surgical gowns and other textiles provide a critical opportunity for the healthcare industry to lower costs, improve sustainability and protect patients and providers.”
The NASEM was tasked with convening the workshop following a bipartisan, congressional request to U.S. Secretary of
• High quality and safety: Reusable hygienically clean healthcare textiles meet the highest standards for safety and performance, with robust tracking and inspection to ensure the integrity and safety of garments during their use. TRSA’s hygienically clean certification program is based on CDC guidelines and meticulously crafted to ensure healthcare facilities can rely on clean and safe reusable textiles.
• Reduced waste and environmental impact: Reusable PPE has a smaller environmental impact, even after factoring in the manufacturing, transporting, and reprocessing of reusable textiles. The workshop discussed research that shows one reusable gown can replace 75 disposable gowns, and using reusable surgical gowns in place of disposable gowns can reduce greenhouse gas emissions by 66%.
• Lower costs: Reusable PPE generate significant savings. Research was presented showing hospitals that use reusable isolation gowns experience 52% cost savings over disposable products.
Other healthcare textiles—such as surgical gowns and incontinence pads— delivered up to 90% cost savings.
• Enhanced pandemic preparedness: The recent COVID-19 pandemic revealed the risks of relying on single-use PPE, which left hospitals and other healthcare providers facing supply shortages. A better balance between hygienically clean reusable textiles and disposables can lead to a more resilient supply of PPE in future public health emergencies.
“Despite the superior benefits of hygienically clean reusable textiles,” continues Ricci, “the United States lags behind other countries in their use. I’m hopeful this workshop will be a catalyst for change.
“Director D’Alessandro mentioned that NIOSH will identify partners who can help advance greater use of reusable PPE, and TRSA and its members are eager to be a partner in those efforts.
“I applaud everyone who provided their knowledge and expertise during this important workshop, including leaders in America’s textiles and laundry industries.”
Simonetti retires from G.A. Braun
SYRACUSE, N.Y. — Laundry equipment manufacturer G.A. Braun reports that Pamela Simonetti, the company’s director of marketing for 26 years, retired at the end of July.
Traci Anelli was hired in April to step into Simonetti’s role.
The company says Simonetti was responsible for developing the strategic planning and full tactical implementation of a wide variety of marketing programs. They range from the company’s worldwide corporate communications brand management to advertising, eMarketing and digital platform programs, video production, publicity and public relations programs, and exhibit and conference management.
North Carolina.
Anelli graduated from the State University of New York at Fredonia with a Bachelor of Science in communications/ video production, studied journalism abroad at Bond University in Australia, and earned a product marketing certificate from Cornell University.
Before joining Braun, she was the U.S. marketing and communications manager at Marquardt, a global leader in developing and manufacturing electromechanical and electronic switches and systems for the automotive, power tool and home industries.
Mitchell retires from Becks Classic after 36 years
BRENTWOOD, N.Y. — Becks Classic Manufacturing Inc. reports that Director of Sales Greg Mitchell is retiring after 36 years. The company says he will enjoy the future years with his wife in Southwest Florida.
Before Braun, she served in several marketing and corporate communications positions within Eastman Kodak Company in Rochester, New York, New York City, and Charlotte,
Mitchell worked at Western Textile Healthcare for the first part of his career before joining Becks Classic. The company says he has been very instrumental in helping develop it into a dominant domestic manufacturer of
reusable incontinent products.
Throughout his career, Mitchell was active on numerous TRSA and ARTA committees and established lifetime friends.
“The industry will miss him,” says Becks Classic. “We wish him nothing but health and happiness in his retirement along with a huge thanks for all he has done for both Becks Classic Manufacturing and the textile rental industry.”
VIC, Spain — Girbau, a provider of total textile care solutions, reports it has appointed Diego Hervás as its new president.
Hervás takes on this role with the aim of supporting Girbau’s planned growth, contributing his strategic vision and results-oriented approach, in line with the company’s values and legacy.
“Girbau is an extraordinary project and a company whose values I share,” says Hervás. “I see great potential for contributing to growth and advancing together.
“In line with Girbau’s purpose, I am fully aware of the importance of sustainability, both as a company and that we provide for our customers with our solu-
tions and services.”
Mercè Girbau, chair and CEO, and Pere Girbau, CEO, the third generation of this family firm, will continue to perform their functions and work on long-term strategy, innovation, sustainability and corporate culture.
Both highlighted Hervás’ career in multinationals and family firms, emphasizing “his ability to fit into Girbau’s strategic plan and vision.”
Hervás’ career includes more than 20 years of experience in executive positions in multinationals like Xerox and major family businesses like Comexi. In these projects he has proven his capacity for leadership, innovation and team management, the company says.
Hervás studied telecommunications engineering and has complemented his training with a range of courses and master’s degrees in management at prestigious institutions including IESE and INSEAD.
B&C Technologies honors top
PANAMA CITY, Fla. — Commercial laundry equipment maker B&C Technologies recently celebrated the 2023 achievements of its top distributors here during the company’s annual meeting at its headquarters.
Laundry Systems of the Carolinas in Spartanburg, South Carolina, was honored as B&C’s top distributor the year.
Second place went to E. Weinberg Supply Co. in Minneapolis, Minnesota, and third was Image Distributors Canada, Calgary, Alberta.
The company says these distributors’ efforts have been crucial in expanding B&C’s market presence across various regions, the manufacturer says.
The highlight of the event, according to B&C, was the presentation of the President’s Legacy Award, an honor bestowed upon longstanding partners who have significantly contributed to the company’s success.
This year’s recipients included Laundry
Systems of the Carolinas, E. Weinberg Supply Co., Image Distributors Canada, and Washex Machinery Co., Burbank, California.
The company says these partners have demonstrated an unwavering commitment to excellence and have been instrumental in its sustained growth.
B&C also used the event to debut its new line of HX washers, described as cutting-edge hard-mount machines designed to cater to a wide range of laundry needs. Capacities range from 22 to 110 pounds and are available in on-premises (OPL) and coin-op configurations with 200 and 400 G-force options.
Also unveiled were stack dryers, in 2x35 and 2x50 configurations.
“B&C Technologies is proud to recognize the outstanding achievements of our top distributors and is excited to introduce the HX line, which represents the pinnacle of laundry machine innovation,” says Al Adcock, vice president of sales and marketing for B&C.
“Our partners are the backbone of our business, and with these new products, we are set to revolutionize the market, providing unparalleled solutions that
meet our customers’ diverse needs.”
FAIRFIELD, Iowa — This year marks 130 years of business for commercial laundry equipment manufacturer Dexter Laundry, helping people and companies all over the world process laundry faster and more efficiently.
Its journey began in tiny Dexter, Iowa, in 1894, the era of hand-powered wringer washers.
As wringer washers gained popularity, Dexter founder W.H. George realized he could improve upon the existing designs and capabilities. He wanted to provide customers with an affordable laundry solution that would withstand the test of time.
As the years passed, the Dexter business grew in size and prestige. When it outgrew its space in Dexter, George looked for a new location and new partners, and he found what he was looking for here in Fairfield.
Fairfield was a rural town with a growing population and both an east-west and a north-south railroad for shipping and receiving goods and materials. A group of businessmen saw the company’s potential and a purchase agreement was signed August 10, 1911. Ground was broken for a new plant, and Dexter moved to Fairfield in 1912.
As the company’s journey progressed through that century, it manufactured many types of laundry equipment. Its wooden hand-powered wringer washers gave way to single and twin tub wringer washers made of zinc, copper and porcelain. These washers featured a variety of power options, including belts, steam, gas and electricity.
Around mid-century, Dexter began to manufacture top-load and front-load laundry equipment for the home and
commercial markets. These machines were the precursors to the home and commercial laundry equipment that are familiar today. A couple of decades later, Dexter restructured its product offering and began focusing solely on commercial laundry products.
More than a century later, Dexter says it’s still proud to call Fairfield home. The employee-owned company designs, engineers, and manufactures all of its products from start to finish.
It offers a complete line of washers, dryers, and management systems for laundromat owners and managers across the globe.
“With an emphasis on quality and a refusal to compromise, we have flourished and grown into a premier brand and leader in the vended and on-premises laundry industries,” the company reports.
“While our company and products have evolved over the years, we haven’t forgotten our roots. Our Dexter horse icon logo reminds us of our champion namesake and symbolizes our dedication to performance, unmatched strength, unrivaled endurance and loyalty to our Dexter customers. We look forward to continuing our Dexter legacy while wowing and supporting our customers for another 130 years.”
CLEVELAND — Evergreen Cooperative Laundry reports it held a ceremonial groundbreaking on June 27 for the expansion of its facilities in Cleveland’s Glenville neighborhood.
“As a worker-owned cooperative, ECL is dedicated to creating quality jobs and empowering its employees,” says John McMicken, CEO of Evergreen. “This expansion represents our continued commitment to fostering economic opportunity and building a stronger, more vibrant community.”
The project includes the acquisition of eight vacant lots adjacent to the existing facility in addition to the construction of a new 5,000-square-foot building. This expansion aims to increase capacity, address parking needs, and foster job creation.
With the support of the City of Cleveland’s Land Bank, Evergreen Cooperative Laundry has acquired the necessary space to accommodate its growing operations.
The expansion project will not only enhance the company’s ability to serve its clients, including healthcare companies under linen supply contracts, but also create between 10-15 jobs with competitive starting wages and additional benefits.
Recognized as the first commercialscale LEED Gold-certified laundry in Northeast Ohio, Evergreen Cooperative Laundry says it has continuously demonstrated its commitment to sustainability and community impact.