Rising concerns: Laundry operations and water issues
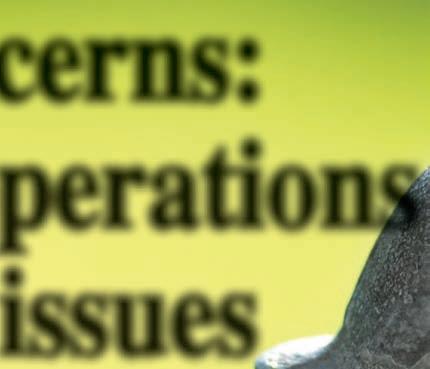
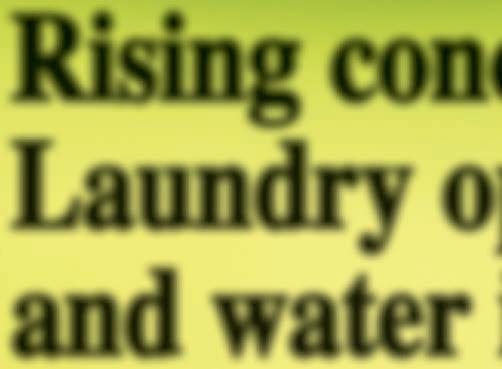
Water is one of the most important substances on the planet.
People and animals need water to survive. Plants and ecosystems need water to grow and produce food and other essential elements. And laundry operations need water to process soiled goods for their customers.
The U.S. Environmental Protection Agency (EPA) states: “Water is essential for life and the vitality of our economy and communities. It is EPA’s mission to
protect human health and the environment, and there are a number of challenges we are facing when it comes to water.
“Across the country, our water and wastewater infrastructure is in need of replacement and repairs to deliver clean, safe water to residents.
“Infrastructure upgrades must be addressed even in the midst of other challenges such as legacy toxins, emerging threats from pathogens and contaminants, population changes, climate change, including natural disasters and aging infrastructure.”
The challenges mentioned by the EPA reach deep into industrial laundry operations. Year after year, plants have to deal with drought, pollution and other factors to have the water necessary to process goods and to help ensure the availability of clean water once the job is done.
And every year, water pressures seem to grow.
“Every laundry operator is faced with different regulations and compliance factors,” says Richard Marzo, vice president of marketing and sales for Lace House Linen Supply in Petaluma, California.
“As an operator in California, we typically see new environmental laws first and then they trickle out to the rest of the U.S. Needless to say, being compliant in California can be a steep learning curve and also very costly.
“The statewide drought and environmental concerns over micro-plastics and PFAS/PFOA (per- and poly-fluoroalkyl substances) are issues that are here to stay and preparing for the most intense (regulatory) outcome is key. Plants that have an existing wastewater treatment process are in a better position to add the right technology to meet new requirements.
“Eventually, these new regulations will
make their way to every state and operators should anticipate investing in wastewater treatment equipment.”
Bob Corfield is president and CEO of Laundry Design Group, a commercial laundry consultant with main offices in Las Vegas, which is one of the most waterconscious and water-efficient metropolitan areas in North America.
“The water levels of Lake Mead and Lake Powell are reported on weekly as if they were sports results for the NFL, MLB or NHL,” he says. “A major shift in water policy was enacted this past year which basically changes a very old costing model: larger users pay less than smaller users based on volume. This was true for residential and commercial users.
“As of 2023, a residential user with a 1-inch water line will pay the same rate as a residential user with a ¾-inch line. The rate increase impact amounts to 300%400% cost for the 1-inch meter user.
“The driver here is to get large water consumers to curb use in what has been a drought concern and is now the new normal for water availability.”
The impact on commercial and industrial users is considerable not only in the drought-impacted Western United States, but nearly everywhere Corfield’s company has performed laundry site investigations.
“The concerns are not only water cost but water availability and finally water quality and sewer discharge requirements,” he points out.
“I presented on water/sewer cost trends 10 years ago and noted from 2000-2010
MIAMI — EVI Industries Inc. reports that it simultaneously executed a definitive asset purchase agreement and completed the acquisition of Express Parts and Services (EXP), a distributor of commercial laundry products and a provider of related technical installation and maintenance services based in Sykesville, Maryland.
The addition of EXP increases EVI’s presence and market share in Maryland and will enable the company to provide increased customer service throughout the region.
“We believe that each acquisition is integral to achieving our long-term growth goal to build North America’s largest value-added distributor of commercial laundry and related products and the most dynamic network of commercial laundry technicians through which we may best support commercial laundry customers,” says Henry M. Nahmad, chairman and CEO of EVI.
“We are pleased to welcome Max Usik and the EXP team to the EVI family and look forward to working together in pursuit of our long-term growth goals.
“The thoughtful execution of our buyand-build growth strategy has earned us a positive reputation in and around the commercial laundry industry, including among owners of quality businesses.”
A look at some of the water challenges linen services face, from drought to PFAS(Photo: © eric1513/Depositphotos)
ALEXANDRIA, Va. — TRSA, the association for linen, uniform and facility services, hosted its Annual Production Summit & Plant Tours in Kansas City, Missouri, in May.
During this two-day event, 91 attendees traveled from across the country for a full day of professional development focused on plant production followed by a day of touring two Kansas Cityarea facilities.
The opening day of the Production Summit kicked off with a keynote speech from Dr. Melissa Furman, MS, DBA, founder and consultant at Career Potential LLC. Furman’s speech was titled “Managing and Leading the Future Workforce.”
During her keynote address, she gave guidance on challenges that affect the future workforce such as burnout, generational gaps and acknowledging personal biases. Attendees were then given the chance to attend two of four breakout sessions.
The first breakout session was on preventative maintenance and was delivered by Joel Bell, engineering director at UniFirst. Bell coached attendees on the importance of technology investment and forethought in keeping operations in satisfactory conditions.
The second breakout on automation and emerging technology was delivered by Gerard O’Neil, owner and CEO of American Laundry Systems, and Scott Voss,
vice president of technical engineering and installations at Ellis Corp.
Their session centered on the emergence and implementation of new technologies to decrease cost, starting with incremental gains that will likely remain manual labor intensive.
The final two breakouts were on energy efficiency and water
“Identifying People/Equipment and Productivity Measures” and was delivered by Todd Leeth, strategic growth leader at Spindle.
The attendees then broke into small groups of their choosing to have facilitated roundtable discussions on issues affecting the industry such as automation, training, and recruitment and retention. The attendees were able to air
plants of both Crothall Healthcare and Cintas.
Crothall Laundry began processing laundry in its 50,000-square-foot facility in 1973.
Crothall specializes in healthcare laundry and averages 260,000 pounds of laundry per week at this branch.
The facility utilizes one, sixmodule (220 pounds) tunnel washer with seven dryers, one 14-module (105 pounds) tunnel washer with six dryers, two 165pound extractors with two dryers and two 65-pound extractors with two dryers.
Publisher Charles Thompson
Phone: 312-361-1680
E-Mail: cthompson@ ATMags.com
Associate Publisher/ National Sales Director
Donald Feinstein
Phone: 312-361-1682
E-Mail: dfeinstein@ ATMags.com
Editorial Director Bruce Beggs
Phone: 312-361-1683
E-Mail: bbeggs@ ATMags.com
Editor Matt Poe
Phone: 866-942-5694
treatment and usage and were delivered by Michael Lewis, senior client advisor at APPI Energy; John Schultz, director of water solutions at Ellis Corp.; and Keith Ware, an industry veteran who is currently a consultant.
After a brief lunch and legislative update by Kevin Schwalb, vice president of government relations at TRSA, attendees reconvened into one group for a session on how industry colleagues are faring with pounds/pieces per operator hour under post-COVID labor scenarios that can result in laundries paying more for less production. This session was titled
their pain points and offer advice at a peer-to-peer level.
The first day of the Production Summit ended with a General Manager’s Panel Discussion where three panelists were able to discuss operational factors at their plants and their perspectives on their roles within the industry.
The panelists were Peter Brown, general manager at Mickey’s Linen; McKenzie Lee, general manager at Alsco, Naples; and Matt Shapiro, general manager at Walker Medical Linen Service.
On day two, the attendees broke into two groups to participate in plant tours of the Kansas City
Cintas welcomed TRSA and the summit attendees to its 44,000-square-foot facility, where it kicked off the tour by discussing the company’s employee-partner engagement concepts that help promote workplace safety, a key component in a multi-faceted optimization program that emphasizes its employee-partners voices.
Visitors were then guided through the facility to show the organization’s safety procedures across different aspects of the plant including fleet safety, industrial wash alley safety and much more.
Lewis summed up the Summit experience as both a presenter and attendee when he said, “I enjoy meeting the people of the industry as they tell their stories.
“You get a wealth of knowledge when you get to speak to people who have decades of experience running plants.”
E-Mail: mpoe@ ATMags.com
Production Manager
Mathew Pawlak
Digital Media Director
Nathan Frerichs
Phone: 312-361-1681
E-Mail: nfrerichs@ ATMags.com
Advisory Board David Barbe
Janice Ayers Davis • Nick Fertig
Deana Griffin • Cecil Lee Edward McCauley Jim Slatcher
Main Phone: 312-361-1700
Fax: 312-361-1685 www.americanlaundrynews.com
Subscriptions 847-504-8175 ALN@Omeda.com
When Milnor introduced PulseFlow® technology, CBW® washing was thrust into the future. The idea of balancing time, temperature, mechanical action and chemistry was missing one critical piece of the pie – DILUTION through the efficient use of water.
PulseFlow combines the innovative RecircONE® fast wet down and chemical immersion in the first module with standing bath washing in every spacious process module. Thorough and efficient dilution occurs by way of intermittent high velocity counterflow rinsing and traditional True Top Transfer.
The result is hygienically clean linen using less water (as low as 0.3 gallons per pound/2.5 liters per kilogram) and less energy as proven time and again by hundreds of PulseFlow tunnels in a variety of laundry applications worldwide.
Contact an authorized Milnor distributor or call 504-712-7656 to find out more.
www.milnor.com
This issue of American Laundry News covers a broad spectrum of topics.
First, and one of the most important to the industry, is water. Challenges and issues concerning this vital resource aren’t going away.
The cover story examines some of these water issues that laundry operations are facing.
Another challenging issue is maintaining supplies, especially much-needed parts. On page 10, Lee Baldauf, chief engineer for Superior Linen Service in Tacoma, Washington, shares his expertise on keeping a spare parts inventory in a supply-chain-issue
world.
Both water issues and spare parts relate to laundry operation technology, and on page 12, our Panel of Experts offers their ideas for successful technology investments and training.
Related to technology investments, this issue has two laundry operation case studies. Both Brightwater Laundry (14) and JVK Operations (16) have made recent equipment purchases and upgrades with some impressive results. The issue also offers Tools of the Trade (page 8) and industry news (page 23), all to help everybody keep it clean.
ALEXANDRIA, Va. — For almost 60 years, attendees have gathered for TRSA’s Ehrlich-Stempler Executive Management Institute (EMI).
This August in the Washington, D.C., area, attendees will access educational, networking and professional development opportunities through this unique course for leaders of the linen, uniform and facility services industry.
Enrolling a promising manager or two in EMI, set for Aug. 6-10 at the University of Maryland in Hyattsville, Maryland, drives home a company’s willingness to invest in training that will create a greater opportunity for industry leadership success, according to TRSA.
Once a week for four years, attendees of EMI return to the University of Maryland to experience cumulative skill building over four days, taught by universitylevel instructors. Sessions are divided as follows:
• Session I – Management Development
• Session II – Advanced Management
• Session III – Personal and Interpersonal Relationships
• Session IV – Business Management in Linen, Uniform and Facility Services
The benefit of learning together and building relationships with others in the industry is invaluable, says TRSA.
My wife enjoys musicals. Whenever we are in New York, we will catch one, or go when they come through our hometown of Tulsa.
I must admit I have become quite fond of them myself. We generally catch at least three or four a year. Some are great; others not so much. But they are all worth the time.
Her favorite musical is Hamilton When it comes to town, we may go all four nights it is playing.
Most generally when I come home from work the next day, the soundtrack will be playing throughout the house. I think our dog Woody may also be a fan.
There is a line in a song that strikes home with me every time I hear it, “Be in the room where it happens.” Seven words that have a powerful meaning.
Edwards Jimenez, a recent graduate of the EMI program states, “It is an amazing program. I learned a lot through the years. The industry changes and I wish other types of industries were allowed to participate because no matter what business you are in, everyone could benefit from these EMI classes.”
EMI has a well-rounded attendance of independent companies’ owners, executives and next-generation leaders to chains’ headquarters (including HR/administration) and plant- and depot-based management (GMs, branch and department heads).
Travis Sohn of Sohn Linen completed his first year of EMI last summer and states, “The event was a perfect confluence between professional development and networking. It was great to learn the practical skills and strategies of leadership, and it was great to connect with so many bright minds in the industry.”
EMI is hosted concurrently with TRSA’s Roger F. Cocivera Professional Management Institute (PMI).
Now in its 33rd year, PMI program participants spend free time, meals and evening social outings with EMI attendees. These activities and events create unique opportunities for professional networking and camaraderie among leaders in the linen, uniform and facility services industry.
Learn more at www.trsa.org/emi
The song is about the meeting between Alexander Hamilton, Thomas Jefferson and James Madison. No one really knows what was said since no one else was in the room where it happened. But some huge decisions were made when they met.
THE REASON WE ALL WANT TO BECOME MANAGERS IS SO THAT WE CAN BE A PART OF MEANINGFUL DECISIONS. BE IN THE ROOM WHERE THEY ARE MADE. WHETHER DECISIONS TURN OUT GOOD OR BAD, WE ALL WOULD LIKE TO THINK WE WERE A PART OF THEM.
The reason we all want to become managers is so that we can be a part of meaningful decisions. Be in the room where they are made. Whether decisions turn out good or bad, we all would like to think we were a part of them.
This statement is true of all levels of supervision or leads. Leaders want to be heard or part of a team. Everyone wants their voice to be heard.
I know there are always managers who will come to meetings and never give any input. They just sit there and listen to others.
A lot of employees are the same way. I have led countless production staff meetings where I am the only one talking and no one seems to give any feedback.
But when you haven’t had a meeting for a while, they are all asking why we haven’t had a meeting. They want to be in the room. To be part of the team.
You read all the time that employees don’t quit for money, they quit their supervisor. There is probably some truth to that.
I THINK WE ALL STRIVE TO MAKE OUR TEAMS BETTER AND KEEP IT TOGETHER. WHILE I DON’T HAVE ALL THE ANSWERS TO ACCOMPLISHING THAT, I DO BELIEVE THAT STEP ONE IS MAKING SURE THE WHOLE TEAM KNOWS THEY ARE IN YOUR ROOM.
There are probably a lot of reasons someone leaves a job. I do know shutting managers or employees out of discussions will sure make them start looking around. If they are no longer a part of your room, then they will go find another room to be in.
•
•
I think we all strive to make our teams better and keep it together. While I don’t have all the answers to accomplishing that, I do believe that step one is making sure the whole team knows they are in your room.
So that they may feel they were in the room when it happened.
Continued from Page 1
certain cities’ water/sewer rates were 150%-248% higher. The higher rates were mostly tied to failing infrastructure or growth or both.”
Corfield says that every project Laundry Design Group is evaluating or specifying looks at core utilities, and every project looks at water recycling technology.
“Industry segments (healthcare and hospitality) that never really looked at water recycling in the past are focused on finding room to address resource or mandatory compliance in waste discharge limits,” he says.
“Our industry continues to develop new technologies to help address water challenges,” shares Marzo. “Gallons per pound washed is a key metric to demonstrating your company’s commitment to conservation and sustainability.
“Manufacturers and chemical providers understand that water reuse and reducing energy consumption are integral to the future of our industry.”
Corfield says that water recycling technology is a maturing industry with technologies that work to reduce consumption while removing contaminate to sewer.
“Water reductions in the 60% to 80% range are very realistic, but we caution that this is not a toaster and does not just plug in and do the job,” he points out. “Water is the main chemical used in laun-
dry, and once you add a recycle system, your world will change drastically. You will be restricted by what you can run and how you can run production based on your system design and regulatory limits.
“It is also inevitable that you will need to address water/sewer cost and compliance issues. The rate of how, what and when a laundry may need to comply is directly related to where they are located as these are mostly regional.”
Corfield says that the quality of water is changing in different areas based on drought and groundwater contamination.
“Laundries are having problems based on high iron, high calcium, high chloride, which are new to them,” he shares. “Meaning the water source or quality has changed. Titrating fresh water before the process is now a best practice in affected markets.”
The most notable challenge is the attention to PFAS, which have been integrated into many textile products which laundries are a concentration for, shares Corfield.
“Vector testing for specific textile sources is ongoing, but the early indicators are barrier or protection fabrics are a major source (barrier gowns, incontinence pads, fire-resistant uniforms, etc.),” he shares.
“Also noted are single-use disposable items are major sources of PFAS, most notable of those is toilet paper. All environmental reporting on this is considerable and global.
“The current technology available for removing PFAS at the laundry is HP membrane and RO (reverse osmosis),
“OUR INDUSTRY CONTINUES TO DEVELOP NEW TECHNOLOGIES TO HELP ADDRESS WATER CHALLENGES. GALLONS PER POUND WASHED IS A KEY METRIC TO DEMONSTRATING YOUR COMPANY’S COMMITMENT TO CONSERVATION AND SUSTAINABILITY. MANUFACTURERS AND CHEMICAL PROVIDERS UNDERSTAND THAT WATER REUSE AND REDUCING ENERGY CONSUMPTION ARE INTEGRAL TO THE FUTURE OF OUR INDUSTRY.”
but these systems do not fit most modern laundry plants based on how our industry uses water, so the current industry focus is on eliminating PFAS at the source.”
Marzo observes that growth and development are great for potential business, but it also means more people and businesses are competing for water, which is a finite resource.
“Because of the scale of our industry, it is easier for politicians to draft legislation that affects us rather than the individual consumer,” he says.
“It is best to assume that regulations and requirements will continue to be more onerous, and being prepared is the best and only way to survive. Depending on the current regulations in your area and your facility’s existing wastewater treatment, an operator should be prepared to make significant upgrades.
“Even operators with existing wastewater equipment will need to add new filtrations because the new limits for PFAS/ PFOA are being measured in ‘parts per million.’ This is a significant departure from existing compliance limits and more resources will need to be allocated to meet
the new requirements.”
One of the most important roles that the laundry industry can play in these new regulations is to participate in the legislative process, Marzo says.
“In California, we have been active through TRSA’s lobbying efforts to meet with elected officials and help them understand that industrial laundries are not adding PFAS/PFOA to the groundwater,” he shares.
“We are a ‘pass-through’ industry that is processing the same materials that individual consumers are washing at home. The main purpose of these new regulations is to reduce ‘fast fashion’ items from going to the landfill and then into the water table.
“Our industry is reusable, and our actions are better for the environment versus disposable products. We need to educate our elected officials of our industry’s stewardship of resources.”
Ken Koepper, director of member and industry relations for TRSA, says that clearing the way for the industry to continue installation of systems everywhere to reuse and recycle water remains a priority for the association.
“Local authorities, the International Association of Plumbing and Mechanical
Officials (IAPMO) and the National Science Foundation (NSF) all have been parties to derailing this practice,” he says.
IAPMO, keeper of the United Plumbing Code, is the current key target, according to Koepper. Some municipal authorities use the Code’s provisions that make water reuse/recycling difficult.
“In St. Paul, Minnesota, for example, heat reclamation systems can be disapproved,” he says.
“Los Angeles County also adheres closely to these provisions. Reuse/recycling projects proceed, however, where authorities don’t follow the Code to the letter. TRSA is working with IAPMO to revise the Code to create consistency.”
Local authorities’ use of the Code provision that incorporates NSF’s voluntary standard for reused water quality is largely responsible for this obstacle, Koepper points out.
“Its terminology referring to laundries is meant for coin laundries, which don’t pretreat; it calls for reused water quality calls equivalent to the cleanliness level stipulated for publicly owned treatment works’ (POTW) discharges into water sources after they’ve treated sewer influent,” he says.
“Linen and uniform service laundries need not achieve that level to produce hygienically clean textiles but often come close.”
Koepper shares that TRSA secured a letter from NSF clarifying that such laundries don’t fall under the NSF standard, but it still needs to be eliminated from the Code, as TRSA has proposed language to strip it.
“Otherwise, the risk continues that reuse projects could be derailed, including tunnel washer installation,” he points out.
This issue is becoming timelier as pressure grows to reduce water use in states in the Colorado River basin, particularly the lower portion, which contains California and Arizona.
“They’ve been strong followers of the NSF standard and implemented it through various plumbing codes,” Koepper says. “With Nevada, they agreed in principle with the federal government in May to conserve about 13% of their total allocation from the river. Washington will dedicate $1.2 billion in federal funds to cities, farmers, Native American tribes and others who voluntarily forgo their supplies.
“The federal deal with the states is an agreement to enable the Department of the Interior to analyze the funding package, which would include water recycling and treatment projects, pipelines, delivery systems, groundwater storage, rainwater harvesting and aquifer recharge. TRSA is monitoring the review to ensure linen and uniform services are protected.”
Sarah Brobeck, executive director of the Association for Linen Management (ALM), says PFAS is a very large concern impacting every aspect of the industry, including manufacturers of textiles, equipment, and chemicals, as well as laundry processors.
“To prepare, laundry processors should become educated on PFAS and monitor both federal and state efforts to address PFAS concerns, including wastewater testing and impacts to their specific operation,” she says.
“While educating and prepar-
ing operations are vital components, they are a small piece of a much larger picture. The magnitude of these changes and the potential impact on the entire textile care industry requires government officials be educated and understand the industry when making decisions addressing PFAS concerns.”
This industry representation is what TRSA provides, Brobeck says, and they are working diligently to represent the interests of the entire industry regarding PFAS.
“As part of these efforts, ALM
and other industry associations (such as the American Reusable Textile Association) are in collective agreement with TRSA’s position on ‘Addressing PFAS in the Environment,’” she shares. “By supporting their efforts, we strengthen our industry’s position and increase efforts with lawmakers.”
In the statement, TRSA shares that it is committed to partnering with key stakeholders on pragmatic and effective solutions to PFAS challenges.
“We believe that these approaches need to include risk-
based federal regulation based on strong science, as well as collaboration on effective treatment and disposal technologies for wastewater and solids,” the association writes.
TRSA goes on to say regulation is important to all stakeholders and should be based on the following principles:
•The federal government should implement a consistent approach for assessing and regulating specific
217 psig.
With new airend designs and IE4 Super Premium Efficiency motors, the CSD compressors now have even better specific performance (kW/100 cfm) and deliver up to 25% more air than competitive models, according to Kaeser.
The standard SIGMA CONTROL 2 includes external communication capabilities and data storage for better asset and energy management, the company says. Routine maintenance is easier with an open package layout, oversized access doors and convenient placement of fluid level indicator and fill port.
Hydro™, a developer of chemical dispensing and dosing solutions for the facility cleaning, janitorial/sanitation, laundry, kitchen, animal health, vehicle wash, horticulture, laundromat and industrial markets, reports it has developed a new AccuMini dispenser.
Kaeser Compressors says its redesigned CSD series screw compressors offer better energy efficiency and easier service access.
CSD series compressors now feature five models from 60 to 125 hp with improved efficiency over a wider range of flows and pressures. Capacities range from 261-693 cfm at pressures from 80 to
Standard features also include a frequency-controlled fan with a brushless DC motor and an ecofriendly fluid filter element.
All five models are available with integrated refrigerated dryers and Eco-Drains. us.kaeser.com 877-417-3527
Stack economizer reduces gas, recovers nearly 100% heat
Kemco says its stack economizer can safely reduce stack gases as low as 40°F and will recover nearly 100% of the heat going up the stack.
The amount saved on fuel in just one year may be enough to pay for the cost of the system, according to the company.
The AccuMini is available in low-flow (LF) and high-flow (HF) models, and its capabilities are targeted to meet the needs of space-conscious facility owners and those who favor eco-friendly products, according to the company.
Building off the design and multi-market success of Hydro’s AccuMax™ dispenser, the AccuMini offers similar operational benefits but in a smaller size.
At only 4.3 inches wide by 8 inches long, the company says the AccuMini is among the smallest dispensers currently available on the market.
An optional plug add-on narrows it to 3.9 inches wide, making it the slimmest of all top-choice dispenser models.
The size reduction makes it ideal for use in a wide range of applications and reduces its environmental footprint, given the 46% less material required for production.
(ASSE) 1055B-approved backflow protection without the need for additional hardware.
The Swivel AirGap’s construction is made more environmentally sustainable by requiring up to 42% less construction material with up to 40% reduced space.
Powered by Hydro’s patented AccuPro Pressure Regulation Technology, the company says the AccuMini delivers industry-leading accuracy of up to 95% dilution control in both high- and lowwater-pressure applications.
Hutchinson, a designer and manufacturer of smart solutions based in Paris, recently presented an innovation to laundry markets: a fire hazard risk prevention device (detect, extinguish and notify).
The Stop Fire® is a recyclable thermoplastic tube filled with an environment-friendly inert fluid, low GWP, F-gas regulation compliant, designed to stop in record time fire outbreak in closed conditions (dryers) by releasing the extinguishing fluid when pressure and temperature reach the trigger point, the company says.
When the Stop Fire® has triggered, a notification is sent to the machine’s control panel through a P&T sensor (pressure and temperature) or to a smartphone (IOS and/or Android) through a sensor connected to a communication module.
This connected system with a sensor is capable of monitoring and allows it to detect unusual, abnormal or unforeseen events, according to the company.
www.hutchinson.com
818-843-1000
Typical gas-fired heaters and boilers send 20% or more of their consumed energy out the exhaust stack, says Kemco. This loss can mean that for every dollar spent on fuel, the boiler system returns only 65 to 70 cents worth of useful heat after transmission losses.
The company says that traditional finned-tube units cannot reduce boiler stack temperature below 280°F without self-destructing from coldend corrosion.
Kemco says it provides commercial laundry water treatment solutions with the highest energy savings possible while gaining rapid return on investment that exceeds other conventional economizers on the market today.
www.kemcosystems.com
800-633-7055
Additionally, the AccuMini allows the use of Hydro’s new Swivel AirGap eductor option, which employs a 1-inch gap of air between the water source and the chemical inlet to provide American Society of Sanitary Engineering
The standard E-Gap eductor also provides backflow protection via the presence of an ASSE 1055B-approved elastomeric sleeve.
www.hydrosystemsco.com
800-543-7184
ing area of the laundry.
The company says it is fully adjustable in width and height to adapt to the dimension of almost any entry gate, and its wide reading area covers a large surface and ensures maximum reading performance.
Datamars says it’s the ideal reading point to instantaneously provide laundry operations with accurate data regarding which customers have returned soil textiles and how to parametrize their upcoming washing programs.
Datamars says its UHF Portal 201 is a heavy-duty reading portal designed to read trolleys on the soil side, typically at the truck unload-
The UHF Portal 201 is usually configured as a continuous reading point but optionally can be triggered by an external event.
www.textile.datamars.com
254-598-3440
Continued from Page 7
PFAS with clear timelines.
•Regulations should be based on the best available science.
•Specific PFAS should be regulated based on risk to protect human health and the environment.
•Regulatory outcomes should not be predetermined.
•PFAS compounds should be regulated independently or as appropriate sub-categories, not as a single group.
•Agencies should provide meaningful risk communication and regulatory transparency.
•EPA and other federal agencies
should establish regular consultation with stakeholders.
•Congress should provide regulatory agencies with the proper oversight and funding necessary to evaluate and address specific priority PFAS.
“Water/sewer issues are very local or regional and cannot be trended nationally,” Corfield points out. “Yes, there are EPA regulations that can affect every market, but adoption and funding for your local districts are what every laundry needs to keep an eye on.
“Stay connected to your local water district and POTW to determine their challenges or possible changes.”
Water issues aren’t going away anytime soon, so laundry operators need to be
prepared with solutions to the challenges mentioned—and those to come.
“As an operator in California, which happens to be the sixth-largest economy in the world, we need to be prepared to work with less water, not more,” shares Marzo.
“The need to meet new regulations will be met by our industry, which is exactly what we have been doing since the EPA started enacting laws. Manufacturers have created new equipment with tremendous water savings and chemical companies continue to develop new products and formulas to work in conjunction.”
Corfield says that whatever technology a laundry selects, it is advisable to do a 360-degree water process review.
“Consider all formulas processed in whichever equipment you run and do not
lose focus on your primary role: get linens/uniforms clean,” he says.
“We are involved in numerous investigations with textiles with bioburden in excess of hygienic standards due largely from not using enough water to clean. How little water you use can be a direct conflict with how clean your linen is.”
“The holy grail of the laundry industry washhouse is to have a closed loop with 100% recycled water but, in the meantime, we will continue to work on reducing the gallons per pound washed without affecting our ability to deliver a clean product,” Marzo says.
“Our industry understands the need to reduce energy consumption and increase water efficiency, and it is utilizing the latest technologies to help achieve these goals.”
Most of us survived a pandemic, and now business is going as close to all out as it could be. Labor can still be a challenge, and skilled labor is even more of a challenge. These are givens across the board in our industry.
So are the challenges of sourcing parts.
How ready is your parts room, cabinet, box, shelf behind the boiler, whatever, for the daily operations of your plant?
In a perfect world, we would have enough space and money to have one of everything, including the elf to organize and catalog this. Sure, many of us have a computerized maintenance management system (CMMS), but very few have the space and resources for “everything.”
I don’t always win the parts war, but generally I have a pretty good idea of what to expect in the search for parts, and I have some knowledge as to what original equipment manufacturers (OEM) have on the shelf … mostly.
Knowing what is “easy” to source and what is nearly impossible to find should have a significant impact on what you decide to keep as an inventory part.
We are fortunate to have some very capable, and usually well-run and managed laundry equipment manufacturers right here in the United States.
Hopefully, if you are the person sourcing parts for your plant, you already know the names of the people in the parts department at the appropriate manufacturers. If not, start building relationships with these folks.
All machines break. You already know if you have a part on backorder. Some
manufacturers are experiencing issues with their suppliers, but most can suggest options to bridge the gap between breakdown and part availability.
Maybe an odd horsepower and revolutions per minute (RPM) spec motor is proprietary, but your source is waiting for some parts themselves. A capable motor rebuilder in your zip code may be able to rebuild your failed one far faster than waiting. You are still down, but maybe for just a couple of days, versus a couple of months, or longer.
I have a reasonable expectation of what I can get overnight, and what may be a bit harder to get. This influences what I might keep on hand, and what I might wait until I need to purchase.
Almost all of us have some degree of equipment from overseas. This is a beast of another nature. Do they have a parts warehouse in the United States? How many of the parts are proprietary?
Belts, fuses, relays, etc., you can supplement with no OEM parts, and at least keep on keeping on. What if it is a programmable logic controller (PLC) that must come from the OEM? Do they have this readily available?
How long can this particular machine be down while you wait for a part to arrive from Europe? What hours can you order these parts, and what is their fastest arrival under the best circumstances? An important consideration for your spare parts inventory.
I am cautious to avoid mentioning specific brands of equipment here, as these articles aren’t for advertising purposes, but what about old stuff, like Super Sylon and Hypro?
The company that cast these machines burned down in 1962, and not one has been produced since. Enter the aftermarket parts vendor. Somebody, somewhere,
Chief engineer shares thoughts on maintaining spare parts inventory in a ‘supply chain issue’ world(Image licensed by Ingram Image) (Image licensed by Ingram Image)
has virtually every part ever made for these available as original used or duplicated new.
If you have any of this old equipment, and many of us do, there are a few parts you know are going to give you grief. Gears, bearings, chains, sprockets, pads, covers, springs, etc.
You already have a vendor that helps support you on these items, but keep relationships and opportunities alive with all of them. It is important to think about how your relationship with one particular vendor might change if, suddenly, your rep wasn’t there anymore.
A good to great rep is often what controls your access to goods and services from these companies.
Take care of the good ones, but spread some love around. We work in a big, small world. If you have multiple of these machines, maybe you keep one of each type of gear on the shelf. If you only have one, you probably really need it, so you probably should consider having one of each gear on the shelf.
Chain and sprocket items are easily had at your local bearing house, but it doesn’t cost a bunch to have a box of 80, 60, and 40 chains and links around for those before 7 a.m. and after 5 p.m. breakdowns. Only we work these hours, not our parts houses.
Now we are getting into a potential mess, and sometimes very expensive parts. We all use water. Lots of water. The things we should consider are what aspects of our system are for reclaim, like heat exchangers. What are our recycle systems, and what associated utility costs occur when we lose either?
The other part of this, and probably the most critical, is compliance. Hopefully, you have redundancy built into your system. A couple of pumps for recirculation, a couple for waste, etc. This is really nonnegotiable.
Pumps fail. Whether it is a motor that decided it has put in its 20,000 hours saying goodbye, a backflow check coming apart, someone’s soda bottle or rag, or just plain lint clogging the works, they fail. Having a secondary pump can make the solution as easy as switching some valves and energizing a starter.
I try to make sure my crew alternates weekly between these two systems, as I wish to know if a pump is sounding distressed before switching to backup, only to find out the backup is not operational.
Believe it, or not, many people have a hard time with this thinking. Their thought process is that if we leave it offline, it will still be new when we crossover. I get the thinking, but I disagree with it.
You will make your own choice, but I do switch these systems over periodically for peace of mind.
I also recommend keeping some EPDM rubber on hand for the flappers that are on so many of these self-priming pumps. Or, even better, spare flappers ready to bolt in. Actuators, I think, can be a lot easier to be ready for. Try to keep consistent in your choices. Either try to be ball valve or butterfly and either spring return or air return. You will still have different sizes to contend with, but it greatly reduces the number of parts you need on hand and facilitates a quick and easy repair.
Don’t forget to have a standalone backup pump of some sort that can get you
through the inevitable “what do you mean they are both broke” occurrence.
Now, the biggest nemesis we’ve had since the pandemic is the availability of electrical and electronic parts. Let’s start with breakers and fuses.
Back in early 2022, I needed a single pole 20-amp breaker that has got to be one of the world’s most prolific 20 pole breakers. I went to my local electrical house which is the local authorized hub for these breakers and was told that they were on backorder until July, which was about a five-month wait.
So many things go through your mind, like should I try a 15, or a 30 will do it— ha. Then you come back to the engineering realities and possible liabilities and fires or whatever and wonder if you can find one on eBay.
For me, I was fortunate enough to have a good relationship at this wholesale house and asked if we could go back and see what they did have. I found a full rack of split mini 20s.
Now, oftentimes, the person at the counter is really good at seeing what the computer shows them, but they never even wired a light switch in their life. I took four of these, and when I left, they were calling customers offering this alternative.
I am not a smart man (I’m using speak and spell to write this), but I did know what I needed. We all do at this level. Don’t be afraid to ask if you can peruse what they have.
There exist many brands of bolt-on breakers that interchange with one another. By the way, I still have three split mini 20s, if you need one.
Fuses were also difficult for a while, particularly in the common and the big. This has subsided but be aware of what your fuse needs are.
You most likely have multiple disconnects that use the same fuse. You probably should have a half dozen or so of the ones you need on hand.
You need to really think about your equipment when you consider everything electronic that we use. All things electronic are a bear to get right now. Even the people that built your equipment are struggling to get their allotment or even changing PLCs to get through their next production cycle.
This is going to affect our industry for quite some time. If these companies find success in their new relationships, your equipment becomes suddenly obsolete.
A longstanding major player in conventional washers has switched operating controls, not because of the supply chain, but for the power and ease of use of their new system.
There are many of the old systems out there, and switching up to new controls, while it is probably an eventuality, is very expensive.
I found supporting slot cards for the old system for a very reasonable price online. I needed one but bought three. They arrived from China within a week in factory packaging. I am not sure if they are legitimate, but they operate as they should.
Sometimes you need to look outside of the box.
I absolutely send my old slot cards, and recently a PLC, to an electronics repair company. Source one of these companies, and I encourage you to have your old elec-
tronics repaired, if possible. This allows you to enjoy some more life out of a machine that is mechanically sound, but technically challenged … I suppose like many of us.
Now, the two hearts of a laundry operation. Almost all of us rely on a boiler and a compressor. Keep the obvious, and relatively affordable, on the shelf: flame scanner, fuses, safety valve, etc.
More importantly, have your relationship with your local rental company and your boiler mechanic on the tight.
Speedy delivery of a backup compressor or having the boiler guys direct cell for that 2 a.m. no start on the boiler can make the difference between running and not.
I have the national warehouse for a fastener supplier within a mile of our plant. I don’t need to keep hundreds of specialty screws in stock, as they have almost everything.
Maybe you have a pipe manufacturer across the street, so you don’t need to eat up real estate storing 90s and nipples.
I say it all the time. Many of us are within a stone’s throw of each other and share the same equipment. I trade parts with a few other plants. It almost makes a one-off independent plant feel like it has the support of a national.
I also communicate with the other chiefs as to what their inventory for a particular machine is and we conspire a bit to share the burden of keeping on inventory some of the more critical and expensive parts. Maybe you have a PLC and they have a frequency drive.
I really didn’t cover what parts you need on hand, but rather some, and just some, of the things you should consider when building and/or maintaining your parts inventory.
Have plenty of able people in your contact list who can supplement your needs and the shortcomings of traditional suppliers.
Keep critical, hard-to-find parts close to your vest. Consider acting as if you are in an engineer’s cost bureau group and partner up, as it were, with some of the competing laundries around you.
We are not sales and service, but probably best to run it by the folks in the C-suites, first.
It is easy for everyone to see our failures and what we may not have gotten done, but uptime will be the main calculator in determining our value.
Exploit every resource you can to be the best steward possible for the people that sign your check, and the people who count on you to be able to earn theirs.
Lee Baldauf is chief engineer for Superior Linen Service in Tacoma, Washington.
In the fast-paced world of industrial laundry, incorporating new technologies is crucial to staying competitive. Among the numerous advancements, water recycling equipment stands out as a game-changer, offering significant operating savings and environmental benefits.
Water recycling has revolutionized the sector by minimizing water consumption and maximizing efficiency.
Traditional laundry processes involve extensive water usage, leading to exorbitant costs and environmental concerns. By embracing water recycling technology, laundries are significantly reducing their dependence on freshwater resources and reaping substantial financial benefits.
Operators are drastically reducing freshwater intake, leading to lower utility bills, reduced wastewater disposal costs and utility surcharges. The financial impact is especially significant in regions where water scarcity or high water costs prevail.
Furthermore, water recycling equipment often employs advanced filtration and purification technologies, resulting in better cleaning outcomes and reducing the need for excessive chemical usage.
This, in turn, minimizes chemical expenses and enhances the lifespan of textile products, reducing replacement costs.
The environmental benefits of water recycling technology cannot be overstated. By reusing and treating water, industrial laundries can significantly reduce their ecological footprint.
Conserving resources helps alleviate pressure on local water supplies and protects the environment from excessive extraction. Embracing sustainable practices not only benefits the laundry business but also aligns with the growing focus of customers on environmental stewardship at a local level.
Mustering the courage to invest in these types of systems can be difficult because the price tags often scare owners away; however, the returns are similarly substantial and last well beyond simple payback periods.
Additionally, when compared to recycling equipment deployed 15-20 years ago, the technology is much more intuitive to operate and maintain and the health of the equipment can easily be monitored by the manufacturer.
While integrating new technology is a critical step toward plant efficiency and competitive advantage, it is equally important to establish regular service and train-
ing intervals. These agreements ensure the smooth operation of the equipment over time and provide ongoing support and training for staff, even in the face of operator turnover.
Regular service enables laundries to schedule routine maintenance visits, ensuring the optimal performance of their equipment. Trained technicians can conduct inspections, diagnose potential issues and carry out necessary repairs promptly.
By adhering to scheduled maintenance, plants can prevent unexpected breakdowns, avoid costly downtime and extend the lifespan of their equipment. Additionally, service plans often provide access to a dedicated customer support line, ensuring prompt assistance in case of emergencies or technical queries.
Operator turnover is a common challenge faced by industrial laundries. To maintain operational efficiency, it is crucial to partner with the manufacturer in delivering comprehensive training programs for both existing and new staff members.
Training plans facilitate knowledge transfer and equip employees with the necessary skills to operate and maintain new equipment effectively. By proactively empowering the workforce, plants can mitigate the risks associated with turnover, ensure consistent operations and maximize their return on investment.
The incorporation of new technologies in laundry presents a remarkable opportunity for cost savings and environmental sustainability. By minimizing water consumption, reducing chemical usage and maximizing operational efficiency, laun-
dries can thrive in a competitive industry while contributing to a greener future. However, to unlock the full potential of these technologies, establishing regular service and training agreements is essential. By prioritizing continuity and investing in the expertise of their workforce, laundries can maintain seamless operations, even amidst operator turnover, and fully capitalize on the benefits of water recycling equipment.
made the worker’s jobs easier.
I would frequently get asked by the material manager how the in-service went. My typical response was, “They will tell you that they hated it.”
The reason why I would say that is because many of the people who were listening to my in-service were not that interested in what I had to say primarily because they just did not want to change doing or using what they were used to.
They were basically against the idea of change.
So, I always had to go back for that second in-service, and once they found out that was the route that the facility was going with, they all listened in, and all was smooth sailing moving forward.
For a company like ours that has gotten more involved in offering new automated equipment to our laundry customers, the question really should be, “How can we help the laundry make the switch to an automated system easier for them and without issues that they would have to deal with?”
I certainly cannot speak for everyone else, but I personally feel that in a lot of cases, people are not thrilled about change—no matter how good it may be for them and the company.
Before starting Streamline Solutions, I had worked for a company where we did many different in-services on products with our customers. Many of those products were far superior to what the customer was using and would have certainly
Soon after checking in with the customers, I was thrilled to find out that there were no issues and people were then thrilled with the new product and/or service that they were now using from us.
So, the question is how can we help the laundry and its staff to make the change to a new system easier initially and down the road and to make sure that the new “change” is only a positive one?
We feel that it is very important to discuss with our laundry customers not only everything about the equipment itself but how those advantages can be put into place easily and safely to give the laundry a quick and positive ROI.
No doubt we would need to discuss all the key advantages of the new equipment and technology so that everyone understands how this will make their lives easier and jobs more productive. Explanations of
“Incorporating new technology into an industrial laundry, like automated sorters or folders, can be a challenge. What strategies can I use to successfully invest in training and tech improvement?”Equipment Manufacturing Tom Vanden Heuvel Kemco Systems, Clearwater, Fla. Equipment/Supply Distribution Ross Sanders Streamline Solutions, Orlando, Fla. (Image licensed by Ingram Image)
all key equipment parts and how they are used must be done.
Key information in writing is vital as well for easy reference down the road.
We would always make sure that our tech people are readily available for questions and explanations when needed. We would get as involved in the training and teaching process as our customers feel that we should be.
Follow-ups on our end would be key as well. Just because we do not hear anything from our customers doesn’t mean that we shouldn’t be following up with them after the equipment is installed and the workers are trained.
Again, at times, people feel that change may not be good but as long as the equipment company outlines all of the advantages to the workers and makes sure that all training and teaching bases are covered with positive reinforcement, it won’t take long for positive results for all parties involved.
As noted in my prior articles, your employees (team members) are the most important in any decisions that you make each day in your business.
You must make them feel part of the process if you want to retain them, especially the top performers. Everything you do in your workday is geared toward engaging them and making their day very fulfilling.
If you do not let them participate in decisions that impact them each day, you will lose them.
As part of your due diligence when investing in training and technology, check out all the relevant suppliers in the industry to make sure that the equipment and/or methods will blend in with your company culture.
Do not discount a supplier simply
because you have not dealt with them in the past; you may be pleasantly surprised at what is available in the market currently.
Training and tech improvements can be negotiated in the purchase price and keep you up to speed for many years after you have installed the equipment in your plant. Whenever there is a significant improvement in the software, you will benefit from the upgrade if you have discussed this with the supplier in writing.
Reach out to your colleagues in the industry as well as ask the supplier to furnish you with at least three contacts that are currently using the equipment or the process. It will be enlightening to discuss “laundry” with your fellow industry people, and you will get honest answers to your questions.
I always found that an e-mail with a follow-up phone call works best when discussing any equipment, training and supplier questions. You will be able to “hear” the
answers whereas a text or e-mail sometimes does not give you the necessary feedback.
In my career at Wagg’s Linen & Uniform, I reached out to an industry veteran that was using a new spreader-feeder, and he mentioned that a 4-foot pit in front of the equipment allowed longer sheets (queen and king-size) to shake out as it was taken away by the spreader to be fed into the Ironer.
This improved efficiency by 20%, which in turn helped us achieve a much better pounds per operator hour (PPOH).
Your safety coordinator (in-house or an outside contractor) is an excellent resource. They will guide you in your decisions to establish a safe working environment for your employees.
Even if it is not a grave issue, it will show that you are taking the employees’ health and welfare seriously.
Remember, if your employees trust you,
they will look after your customers. To me, this is the best strategy.
Hotel/Motel/Resort Laundry Rodrigo Patron Lace House Linen, Petaluma, Calif.
In the industrial laundry industry, the idea of implementing new technology is not a novel one.
Nowadays, it’s commonplace to receive e-mails advertising “new and improved” ways to enhance plant efficiency and employee productivity.
See Experts on Page 15
BEACON FALLS, Conn. — In the business world, medical community or the sports and entertainment industry, experience is often the harbinger for success.
For Vinny Samuel, his 40 years in the engineering field and the commercial laundry business are paying off.
With the recent addition of more LAVATEC equipment, he’s forecasting a banner year for JVK Operations with a huge increase in volume.
“We processed 36 million pounds of laundry last year,” says Samuel, who is the president and co-owns the company with Mike Connell. “I anticipate we will add another eight million more by the end of 2023.”
JVK is headquartered and operates two facilities in Amityville, New York, on Long Island, and has another processing plant in New Jersey, just south of Philadelphia. The three plants combined offer 80,000 square feet of space to keep the work flowing.
Samuel has achieved success for JVK by developing a well-designed blueprint.
He began working in the industry after arriving in the United States with business and engineering degrees. He gained experience at several companies, starting as a plant engineer in 1985 and later designing laundry plants around the world.
After learning the ins and outs of the business, it was time for Samuel to open his own company in 2004.
“We have been servicing healthcare institutions almost since the first day,” he says. “Today it accounts for 50% of our business, and the other half is hospitality driven.”
JVK services customers on Long Island and in other parts of New York, in addition to New Jersey, the Philadelphia market and some customers in Connecticut.
Known for processing customer-owned goods (COG), they handle the linen and garment rental side of the business with a lot washing program. By keeping client linen
separated, they find it improves overall lot integrity and boosts customer satisfaction.
Samuel takes pride in the high-quality work JVK provides its customers, believing it forms a winning combination with timely delivery and the best customer service possible.
To achieve this, the foundation begins with the equipment on his floors. He determined years ago that partnering with LAVATEC gives him the best return on his investment.
“There are many manufacturers of laundry equipment, but during my association with them the past 35 years LAVATEC has displayed a very consistent manufacturing process,” shares Samuel.
“I believe in getting it right the first time is best, and I have seen them keep the production standards at a higher level. They haven’t chased the unnecessary goals for cosmetics. Instead, they’ve kept it simple and safe with user-friendly controls.”
Starting in 2008, JVK installed a new 200pound, LT90 tunnel washing system with 16 compartments at its Amityville processing facility. Recent upgrades include six 330pound capacity dryers that are now helping operations to run more efficiently.
“Our tunnels are a perfect fit for these dryers,” says Samuel. “We have already seen a 40% utility savings by doing all the work with six dryers instead of 10.”
Another tunnel washer JVK employs is a model built 27 years ago that Samuel purchased and has run regularly since 2008.
All told, they now utilize five LAVATEC tunnel washing systems and 20 dryers to go with six LAVAPress press extractors.
“It still runs very efficiently and is a perfect example of what I think about LAVATEC equipment,” Samuel says about the older tunnel system.
“The quality of materials which were used
many years ago have proven to be better than any other manufacturer.”
Having a machine of that age providing output every day is remarkable unto itself. Operating it at a high-performance level also means having available access to parts, a task that Samuel says is uncomplicated.
“LAVATEC machines are built so the maintenance is simple and easy, and we keep track of each and every part,” he points out. “We also have a preventive maintenance policy in place to replace any sensitive parts prior to them breaking down.
“In accordance with the quality of our equipment, we study and plan ahead. That’s why we have trained our technicians this way to maintain the equipment.”
When the need arises, Samuel says he and his staff are confident in LAVATEC’s abilities to resolve any issues, and this makes for a strong partnership.
“We keep in touch with their engineering and service departments, and from time to time we ask them for support of the older equipment,” he shares. “Surprisingly, they deliver all the parts for us, no matter what we need.
“Commercial laundry businesses do not attract highly educated engineers or technical personnel. It is a struggle for every laundry with the issue of retaining knowledgeable employees because they are in such high demand.
“That’s why it is important that LAVATEC’s equipment is simple to maintain, and the training for our operators and technicians is helpful and fairly easy.”
Continued from Page 13
Naturally, everyone wants to improve their operations, and the age-old saying, “You can’t improve what you can’t measure,” rings true.
However, it’s important to note that not all plants are alike. Even if they share similar clients, square footage, employees or equipment, each plant has its unique characteristics and needs.
Therefore, before investing in any new technology, take time to introspectively analyze your plant’s requirements and what you want to measure. After identifying these key factors, it’s crucial to train your team to understand the benefits of the technology fully.
Remember, having top-of-theline equipment means nothing if your team isn’t motivated to use it. It’s like buying a treadmill that ends up as an expensive clothes hanger in your garage.
So, make sure your team is 100% on board to ensure that your investment in new technology is worthwhile.
There is a huge turnover rate among laundry workers; they often stay on the job for less than a year. And if they are never trained properly on how to load the machine, then they are likely doing it wrong for the entire year.
Turnover is expensive, costing employers one-and-a-half to two times the employee’s salary according to the Society of Human Resource Management (SHRM). That resource goes into the cost of hiring, onboarding and training, learning and development, and the cost of time with an unfilled role.
But there are soft costs of this equation to consider, as well. High turnover leads to woes such as depleted employee morale, lost productivity and diminished employer branding.
After all, a company known for its revolving door of employees will not inspire much loyalty or engagement.
The following is an item I have used and seen be successful no matter the size or location of the laundry: Periodically surprise employees with something fun. Spontaneous gestures go a long way toward keeping the
atmosphere light and letting attendants know their dedication is noticed and appreciated.
On the technology front, when we upgrade to a machine that folds quicker, irons and folds faster, or even make the big move to a tunnel washer, the key is to have people on board and support from the manufacturer.
This leads back to training and fully understanding linen flow and the various “time traps” that can occur when the flow becomes out of balance.
Lead time is how long it takes you to deliver your service once it
is required. Lead Time=Amount of Work-in-Process/Average Completion Rate. This equation tells us how long it will take any item of work to be completed (lead time) simply by counting how much work is sitting around (laundry in this case) waiting to be completed (things in process) and how many towels, sheets, etc., we can complete each hour, day, week, etc. (average completion rate). In both training and tech improvement, the following quote applies: “What is not tracked will be wasted and never returned!”
This is an interesting question to consider as the specific strategies can be quite regionalized and size-related in the approach to be successful.
From a technology (maintenance included) standpoint, it is imperative to know which parts take the longest to obtain having a trained mechanic or timely support from the manufacturer.
Three suggestions will help you get the best from your team members. First, you need to train team members.
Second, you need to motivate the team so each one feels valued and wants to help each other and the company.
Third, you need to effectively evaluate each member to ensure overall team success.
Make sure your team members know how important their roles are in your business. This can begin as early as including this point in their job interview.
Be very clear with your examples during training, and I have found the following quote to work very well when training in laundry and cleaning: “Tell me and I forget; teach me and I may remember; involve me and I learn.”
My last suggestion would be that if the effort to learn is being expended, be patient as sometimes the person may become a top performer over time because you showed them patience.
OSH KOSH, Wis. — Brightwater Laundry of Tennessee in Sevierville recently completed a massive automation project that positions the company to process up to 10 million pounds of customer-owned goods (COG) per year, according to Laundry Project Manager Matthew Shadle.
The commercial laundry, which serves the booming vacation rental and hospitality markets of Eastern Tennessee, immediately launched laundry productivity, lowered labor costs and improved end-product quality.
The icing on the cake? An anticipated return on investment of just two years.
A functioning commercial laundry when it was purchased in 2019, Brightwater Laundry had utilized Girbau Industrial open-pocket washer and dryer lines for several years.
Those lines included multiple GI 255-, 130-, 90- and 60-pound capacity soft-mount washers and 170-, 120- and 75-pound capacity dryers.
In September 2021, in order to grow business, the laundry completed the installation of additional equipment, including a GI 8-module Continuous Batch Tunnel Washing System, two PC-120 ironing lines with DRE Feeders and FRB Folders, and two auto-sort FT-Maxi towel folders.
Now Brightwater Laundry processes 2,000 laundry pounds per hour with room to grow. Moreover, the elimination of an eight-hour shift drastically lowered labor costs.
To pull the automation project together,
Shadle and the Brightwater Laundry team worked closely with Jeff Large and his team at Laundry Systems of Tennessee, which is also in Sevierville.
“GI makes fantastic equipment and the relationship between GI and Laundry Systems makes for a great combo for a super-efficient plant,” says Shadle.
“Laundry Systems has been integral to this process; we couldn’t have done it without them.
“Jeff and his team are laundry experts who showed us our potential for growth and taught us about GI automation, and they are always quick to respond to our concerns and questions.”
The workhorse of the plant, a new eightmodule GI TBS-50 Continuous Batch Washing System, operates with water reclamation, water filtration and drain-water heat recovery systems for maximum efficiency.
It includes a loading conveyor, press, dual-cake delivery shuttles and four ST-2700 Dryers; processes 2,000 laundry pounds per hour; is programmable by module; uses .8 gallons of water per laundry pound; and completes 110-pound loads every three minutes.
“Multiple programs allow us to process many different items for many different customers,” Shadle says. “The tunnel automatically tracks loads by customer.”
Once laundry passes through the tunnel washing system, no-iron items, like towels and blankets, are completely dried and run through the laundry’s automated sorting and folding systems.
Meanwhile, ironed items, including sheets and duvets, are shuttled into the dryers where they are quickly unbound and separated. Then, while still damp, they are fed into one of the two ironing lines.
On the ironing side, Brightwater Laundry has two GI ironing lines. Each features a DRE multi-station Spreader Feeder, a PC-120 Two-Roll Chest Ironer, and an FRB Folder and APB1 Side Stacker.
“We iron fitted and flat sheets, pillowcases and duvets, among other items,” says Shadle. “The ironing automation allows us to keep pace with the tunnel’s production, reduce our labor hours and costs, and improve the quality of our final product.”
Gas-operated and 93% efficient, the GI ironers automatically adapt cylinder speed
according to linen type and moisture content—eliminating the need to pre-dry items.
Each ironing line allows up to three operators and processes flat goods at a rate of 150 feet per minute.
At the front of the ironing lines, a DR-Series multi-station spreader feeder automatically straightens items and feeds them into the ironer for maximized processing speeds and ironing quality.
Meanwhile, on the dry work side, fully dried towels, washcloths and blankets are fed into one of two FT-MAXI triple-sort folders.
The FT-MAXI eliminates pre-sorting, according to Shadle, so items of varying dimensions can be folded, sorted and stacked according to pre-programmed specifications.
“We’ve saved a ton of time on labor because we can run a mix of items through the machine and they are automatically classified and put into stacks,” he shares.
With each FT-MAXI, Brightwater Laundry folds up to 750 pieces per hour—a huge improvement over hand-folding.
In another area of the plant, the openpocket washers and dryers also serve an important purpose.
Because Brightwater Laundry caters to the hospitality and cabin rental COG market, it often handles specialty bedspreads, spa linens and pillowcases.
“We like running specialty and heavily soiled items through our GI open-pocket washers because we can do custom chemistry and water temperatures,” shares Shadle.
The GI soft-mount washers reach extract speeds up to 408 G-force to effectively reduce moisture retention in loads for quicker drying using less energy.
Simultaneously, highly programmable controls deliver complete management over everything from number of baths, water temperature, fill levels, rotation action, chemical injection and extract speeds, to
overnight soaks and more. This allows for very precise programming and improved laundry productivity.
The open-pocket line also serves as a safety net in case the tunnel system is down for maintenance or repairs, according to Shadle.
Two months in, Brightwater Laundry grew 15% and is on target to meet its twoyear production goal of 5 million laundry pounds annually, and hopefully, its long-
term goal of 10 million.
“We are the only commercial laundry in the area with such sophisticated equipment,” says Shadle, “and it shows in our end product.
“We’ve not only significantly reduced labor costs and upped production, we now put out a much higher quality product that sets us apart.”
Haley Jorgensen is a freelance writer operating from her business, Public Image, in Green Lake, Wisconsin.
Bryan Cutsinger, assistant professor of economics at Angelo State University in Texas, and Mike Knowles, COO of Superior Linen Service in Oklahoma, talk the economy, the possibility of recession and ways to ride out the downturn.
Events of the past three years have changed workplace dynamics along with employee attitudes and expectations.
Annette Jones from Huebsch Services and Katie Rowland from Plymate Inc. talk challenges and solutions in laundry HR today.
Bill Sullivan, fire protection engineer for the City of Madison Fire Department in Wisconsin, and Markus Tarin, CEO of MoviTHERM, an innovator in fire detection technology, based in Irvine, California, talk about steps to take in the event of a fire along with detection/ prevention ideas.
offers engaging, industry-specific conversation with an expert, including business-building tips you won’t find anywhere else. And you can listen anytime, either online or download for later!
Give us a try!
BEACON FALLS, Conn. — Commercial laundry equipment manufacturer LAVATEC Laundry Technology Inc. reports that Jim Shaw has joined its executive team as vice president and national accounts sales manager.
He is based in Cincinnati and reports to President Mark Thrasher.
LAVATEC says that Shaw has been successful during his 40 years in the industry. In the last 10 years as the president of VEGA Systems USA, he expanded the equipment roster and was involved in the redesign and expansion of product lines to address market needs.
This followed a 21-year run as senior vice president at Ellis Corp. USA, where he worked closely with the engineering, sales, parts and service departments to expand the product lines and sales support. He plans a similar mission at LAVATEC.
“Mark Thrasher has successfully built LAVATEC Laundry Technology in the United States, and it is an organization with a great reputation,” Shaw says.
“It is well established with solid equipment, automated technology and a highly responsive support network. I appreciate being a part of LAVATEC.”
Shaw and his wife, Aljeanne, have been married for 44 years. They have four adult children and four grandchildren who keep them busy during their free time.
IRVING, Texas — Alliant Systems, a provider of business management systems for textile rental companies based here, reports that it has appointed Lisa Wacker as its director of community.
In her new role, she will focus on building a robust and cohesive community of textile rental operators to enable them to communicate, learn, share ideas, collaborate and help one another more easily.
“We are thrilled to welcome Lisa Wacker to the Alliant family, and her joining our team is a huge step forward for us,” says Mayron Herrera, CEO.
“At our most recent conference, we announced that the development of a formal community program for Alliant customers was a top priority. This hire is a big
step in achieving that vision.”
As part of her responsibilities as director of community, Wacker will manage Alliant events including AlliantCon, as well as develop partnerships and sponsorship programs with industry suppliers.
For the previous 13 years, she served as the supplier relations manager for CSCNetwork, a national network of independent linen, textile and uniform rental companies.
“The role of director of community is a completely new position at Alliant Systems that we are very excited about,” says Eric Smith, director of sales and marketing. “Today, one of the things we see are lots of smaller, informal groups of Alliant users that are successful in sharing information with one another.
“We want to take that concept and create a formal community that is accessible to all users as a valuable resource and at the same time provides valuable feedback to Alliant Systems. Lisa is a perfect fit to join the Alliant Systems team and take our community to the next level.”
The company says that throughout her career, Wacker has excelled at building relationships with operators and suppliers as well as planning and running large conventions, educational seminars, supplier exhibitions and networking events.
“I am excited to start this next chapter of my career with Alliant Systems and am so pleased to be able to continue to work with so many wonderful operators,” Wacker says. “In today’s business environment, our users need a dedicated resource and space to interact.
“In my role, I will be working on new ways for Alliant customers to search for and share knowledge, learn best practices, provide feedback and collaborate with other users.
“Ultimately, we want to empower our customers, improve their experience and strengthen the entire Alliant community. I can’t wait to get started!”
LENEXA, Kan. — Brightwell, a designer and manufacturer of dosing and dispensing systems headquartered in the United Kingdom, reports it has extended its senior management team in the United States by appointing Don Courville as its new Midwest business development manager.
The company says he will continue to build upon Brightwell’s reputation for highquality, trusted products designed for every hygiene environment to suit each business’s unique needs and style.
Courville’s focus will be to maintain, grow and develop relationships within the Midwest United States, with a particular focus on the hospitality, food service, janitorial and sanitation, and industrial markets.
He has 35 years of experience in various management roles, specializing in those sectors and healthcare.
“Brightwell has a great track record for bringing the latest technology and innovation to the field, custom design capabilities and sustainable practices, to support our customers’ hygiene requirements,” Courville says.
“I am excited to be further building on this excellent reputation, with customer needs at the heart of our business.”
Andy Lewis, executive vice president, Brightwell Inc., says, “Don is a fantastic addition to the team. His detailed market knowledge and extensive experience ensure we continue to grow our relationships with customers, distributor partners and new contacts, to help create a cleaner world through our hygiene solutions.”
SOUTH HOLLAND, Ill. — Gurtler Industries Inc., a manufacturer of advanced detergents and specialty chemicals for the commercial laundry industry based here, reports it has promoted Bill Mitchell and added Michael Phillips.
Mitchell has been promoted to the post of vice president of field operations. He started at the company in 2019 as regional vice president.
Before that, he was vice president of national sales and customer care with Norchem Corp. Mitchell has 32 years of experience in the laundry industry.
Phillips has joined Gurtler as manager of market development in the Georgia and Southern Tennessee area. He served eight years in the Marine Corps.
MENTOR, Ohio — Avery Dennison Corp., reports it has appointed leaders for its two business segments.
Hassan Rmaile has been named president of the materials group (label and
graphic materials and industrial and healthcare materials). Francisco
Melo has been named president of the solutions group (formerly retail branding and information solutions), a role that has been open since Deon Stander’s appointment to president and chief operating officer in March of 2022. Rmaile and Melo report to Stander.
“Hassan most recently led our label and graphic materials businesses in Europe as senior vice president and general manager, driving a significant increase in EVA over the last three years,” Stander says.
“As president of the materials group, he will continue to focus our teams on delivering for our customers through innovation, technology and the advancement of sustainability, driving outsized growth in high-value categories and growing profitably in our base businesses.”
Before joining Avery Dennison in 2016, Rmaile served as vice president, chief technology and innovation officer at H.B. Fuller. Prior to that, he held executive positions at Ashland businesses.
Rmaile holds a Ph.D. in materials chemistry from Florida State University, an MBA in finance from the University of Delaware and a bachelor’s degree in chemistry from the American University of Beirut, Lebanon.
“For the past nine years, Francisco has led the significant growth in our intelligent labels platform,” says Stander.
“As president of solutions group, he will continue building on our strong market position at the intersection of the physical and digital worlds by leveraging segmentation and industry leadership, marketdriven innovation and advancement of digitization and related solutions to deliver exceptional value to our customers.”
In his previous position, Melo led the company’s intelligent labels platform as the senior vice president and general manager for Avery Dennison Smartrac.
Before joining Avery Dennison, he was a cofounder and CEO of Creativesystems, an RFID systems integrator and software development company. His earlier career includes experience in R&D and business development at Philips Electronics and consulting with Synectics and Altran.
Melo holds a Master of Science in instrument design and applications from the University of Manchester in the United Kingdom and a Bachelor of Engineering in electrical engineering.
In
NEW ORLEANS — Laundry industry veteran Wm. Blaine Jackson died May 9 here after a four-and-ahalf-year battle with pancreatic cancer.
He was 74.
The family says he always wanted to serve others, and the laundry industry knew Jackson as a generous, kind, and overall great guy to be around and always gained some sort of detailed technical knowledge while around him.
He made many things better in the laundry industry throughout his 43-year career. He retired in 2015 from Kannegiesser ETECH, and his efforts were rewarded that year by TRSA with its Maglin/Biggie Lifetime Achievement Award.
Jackson had an unwavering passion for innovation and excellence and once served on the American Laundry News Panel of Experts.
Jackson was a veteran of the U.S. Army, entering the service in 1970. After basic training in Ft. Leonard Wood in Missouri, he served in Germany, elevating to Specialist 5 position. He stayed busy playing football and softball with his fellow soldiers.
Years later, Jackson’s love of sports kept him on the sidelines of endless soccer, volleyball, baseball, softball, basketball, and football games for his children and grandchildren.
He is survived by his wife, Pat, and fur babies Lexie and Sophie who reside in New Orleans.
Jackson’s legacy continues to live on in his children in the Cincinnati area, Mia (Tim)
August
6-10 TRSA
58th Annual Executive Management Institute (EMI) Hyattsville, Md.
Info: 703-519-0029
6-10 TRSA
33rd Annual Professional Management Institute (PMI) Hyattsville,
Neckel, Tony (Angela) Jackson, Monica (Kenyon) Commins, and son-in-law Steve Risola (husband of late daughter Michele).
He is also survived by his former wife, Beverly Redmond-Jackson.
In lieu of flowers, donations can be made in Jackson’s name here: https://everloved.com/ life-of/wm-jackson/donate/?flow=203
Penn Emblem honored for innovations
TREVOSE, Pa. — Penn Emblem Co., a 76-year-old textile manufacturing and fullservice brand decoration company located here, reports it has won two honors in the 2023 NAUMD Innovation Award Contest.
NAUMD (Network Association of Uniform Manufacturers and Distributors) serves hospitality, entertainment, healthcare, branding, promotional product, safety and uniform manufacturer companies.
The Image Apparel Institute division promotes the manufacturing, sale and brand awareness of image and identity apparel worn each day by millions of workers.
One of Penn Emblem’s winning submissions was a PVC emblem created for Propper, a leading supplier of uniforms to the U.S. military and police, and of tactical gear, as a promotional giveaway for a recent tradeshow event. They wanted something funny, different, and well-known in pop culture.
The concept of the “Dumpster Fire” became famous in the aftermath of 2020’s pandemic. The design itself appears cartoonish. The use of PVC allows for the design elements to appear three-dimensional and realistic.
In addition to the PVC Dumpster Fire emblem, Penn Emblem also accepted an innovation award for the PennFlex™ Penn Emblem Logo Design. PennFlex™ is an intricate, thermoplastic emblem that creates a superior, three-dimensional effect for any design.
In 2022, Penn Emblem celebrated its 75th
anniversary, using the PennFlex™ design to create a logo that incorporated both a modern image and a nostalgic tribute to one of the vintage logos.
“Penn Emblem is proud to accept these prestigious awards and was honored to be recognized for such achievements,” the company says.
“Along with a tremendous lineup of anniversary celebrations, great success at tradeshows, and new product innovations, winning the NAUMD Innovation Award is a tremendous accomplishment to end the 75th year.”
CINCINNATI — Standard Textile, a provider of institutional textiles serving customers in the healthcare, hospitality, interiors and consumer markets worldwide, reports it has been selected as a 2023 U.S. Best Managed Company.
Sponsored by Deloitte Private and The Wall Street Journal, the program recognizes outstanding U.S. private companies and the achievements of their management teams.
The 2023 designees are U.S. private companies that have demonstrated excellence in strategic planning and execution, a commitment to their people and fostering a dynamic culture, as well as strong financials.
Designees propelled their businesses forward and remained true to their purpose and values by investing in their people, creating advantage through digital transformation, taking measurable action on sustainability, and demonstrating their commitment to diversity, equity, and inclusion.
Applicants are evaluated and selected by a panel of external judges focused on assessing hallmarks of excellence in four key areas: strategy, ability to execute, corporate culture and governance/financial performance.
They join a global ecosystem of honorees
from more than 46 countries recognized by the Best Managed Companies program.
WARSAW, Ind. — Wildman Business Group, based here, reports it has acquired WM Uniform, located in Holland, Michigan. Together the combined entity operates from six locations throughout Indiana and Michigan with 440 employees, serving more than 12,000 customers.
For the most seamless customer experience during the integration, both companies will retain their independent names and individual branding and continue to serve customers with the same sales and service teams.
In addition to the services customers already received from WM Uniform such as uniforms, mat and towel rental, and restroom programs, customers will have access to additional product lines such as first aid and safety essentials and restroom hygiene cleaning known as CleanTeam.
“The opportunity to come together was driven by president of WM Uniform Patrick Van Tuinen’s eye toward succession planning and was made easy with alignment on our shared core values around honesty, integrity, relationships, excellence, living by faith and treating others as they would want to be treated,” says Josh Wildman, CEO of Wildman Business Group.
“We’re excited about the synergies created from our shared values and the ability to use business to change lives.”
The two leaders share years-long professional admiration and collegiality, as well as a personal friendship. Both share a commitment to remaining independent to ensure best-in-class service and preserve the culture they have intentionally built for their organizations.
“We are stronger together,” Wildman says. “This partnership provides the opportunity to accelerate our growth—not just in revenues but with investment in our people.”
Wildman’s goal is to be the preferred Midwest supplier and a destination employer—positively changing lives through business.
As Steve and Mitch Van Tuinen transition into retirement, Nick Porter, who spent his entire career in the uniform and linen industry and currently serves as general manager at Wildman’s Griffith branch, will oversee WM Uniform’s production, maintenance and stockroom.
Patrick Van Tuinen will remain on the team as regional vice president.
Both companies are proud of the high percentage of long-tenured employees. Many have been with them for 20 years or more. The combined business is on track to continue its 15% annual growth, add 20-25 employees each year, extend service offerings and expand into additional locations in the region.
Wildman says it seeks to partner with other independent laundries looking for a transition to provide an alternative succession plan to large nationals to continue the families’ legacies.