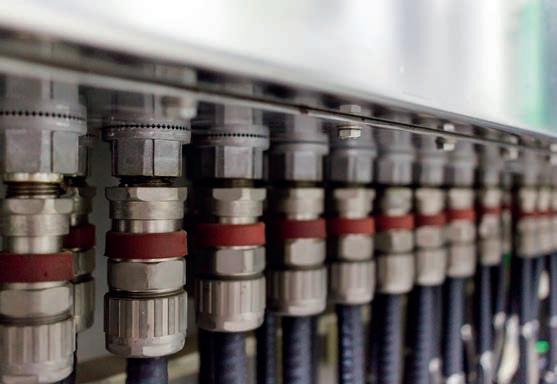
5 minute read
Cable gland installation standards: what you need to know
Though they are sometimes overlooked, cable glands can be a vital part of many different types of industrial networks and systems, writes Scott Jones, General Manager of Northern Connectors.
By reinforcing vulnerable connection points between cables, or from a cable to a device, cable glands can ensure that these systems operate consistently and efficiently with minimal wear. For challenging applications, glands can also provide significant ingress protection against heat, water, foreign objects and other elements, which makes them fundamental to the safety and efficiency of a variety of setups.
Advertisement
The basic advantage of a cable gland is that it relieves pressure on a connection by gripping a cable (which can prevent disconnection and reduce the wear and tear that connections can otherwise experience) and ensure that signal transmission remains strong across the connection. Glands provide grounding, bonding and sealing protection that supports signal transmission and, beyond this, there are many glands on the market that provide specific benefits for complicated or niche applications – so, while in some cases a cable gland is an add-on, in other cases it is an absolute necessity.
In order to gain the maximum benefit from a cable gland (especially if your system needs high levels of ingress protection, heat resistance or other technical advantages designed to mitigate risk), you need to ensure that it is installed correctly. Understanding the International Electrotechnical Commission’s (IEC) standards for the manufacture and installation of cable glands can help to make sure that a system meets the utmost requirements in terms of safety and efficiency.
In order to gain the maximum benefit from a cable gland, you need to ensure that it is installed correctly
Here, Scott explains some of the ways that you can ensure you are using the right cable glands for each application, and outline the installation standards that can help you to maintain safe and effective practices when upgrading a system.
Identifying the correct gland
If you are responsible for purchasing components, Scott advises that you source all of the parts you need from the same manufacturer, wherever possible. If you are upgrading an existing system, this might mean doing some research to determine where the original components were bought, or in some cases it may be easier to replace all of the parts at the same time. While parts from different manufacturers should be compatible, you can benefit from maximum efficiency in the system by using matching components.
The other consideration should be the specific requirements of the individual system in which you are installing the gland. For example:
• Will it be situated outdoors, and therefore require extra protection from inclement weather or other elements? • Will the system need resistance to extreme high or low temperatures, or sudden temperature changes? • Is there a risk of explosions or fire? • Could the system or connection interact with corrosive substances?
Cable glands can offer additional protection against any of these risk factors, but rarely all of them, and so you will need to identify which requirements your components must meet. You may also decide to fit a cable gland with an earthing tag or clamp, where applicable.
The final considerations are straightforward practical concerns – making sure that the gland you choose is the right size to accommodate the cable, for example – and it is important not to overlook these specifications among the other considerations you are making.
International standards for cable glands
Like with all electrical components, there are international design and safety standards for cable glands that aim to set minimum requirements for effectiveness, reliability and safety.
The IEC’s technical standards for cable glands are followed in most countries around the world, and these will be explained in more detail below. In some cases, different standards may apply, but Northern Connectors would typically advise that you ensure that any products you purchase meet the relevant IEC standards, which are often compatible with local standards. For example, the US uses the American Wire Gauge (AWG) standard to indicate the cross-sectional area of a cable, but each AWG value can be converted to a metric value to ensure parts are compatible and meet the IEC’s standards.
The main IEC standards for cable glands in the UK are called EN 62444:2013, which govern the construction and performance of these components. It is good practice to familiarise yourself with these standards before undertaking any work related to the installation of cable glands. The standards also detail tests through which you can demonstrate the reliability and safe installation of components.
Additional standards are also available for some of the more challenging applications alluded to above, and you must be aware of and meet these standards if they apply to your network or system. For example:
• IEC 60079, for applications and environments where there is a risk of explosions • IEC 61892, for mobile and fixed offshore applications where there is a risk of water ingress • IEC 60092, for all electrical installations in ships
A final consideration that might help to ensure that installation is carried out safely is to perform a risk assessment. This can not only help to identify any potential dangers unique to a particular setup, but can reduce your legal liability in the unlikely event that something goes wrong with the installation.
For example, while you may be very familiar with the requirements of electrical safety during installation, there are other factors that could pose a risk to your components. Exposure to solvents, chemicals, dirt or other foreign bodies can all contaminate a gland and render it unable to function correctly, or create a fire hazard or other risk. If the cable is screwed together too tightly, this can also damage threading or make it difficult to replace the component whenever necessary. However, with all of these factors taken into consideration, you can ensure that you select the right component for every application and install it according to the highest standards of safety.