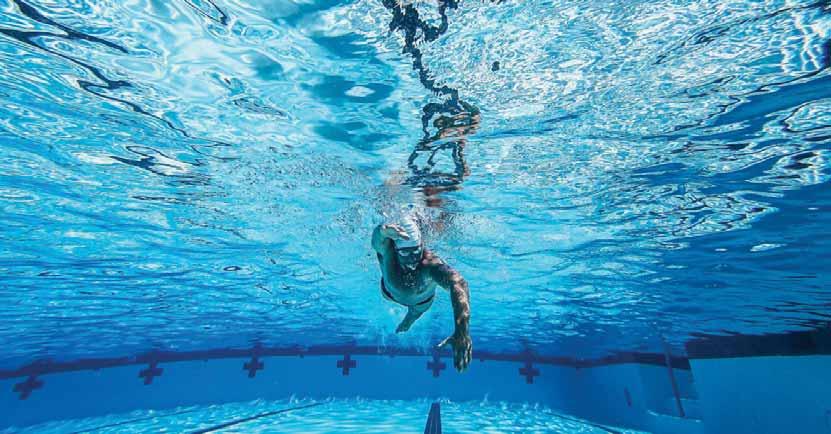
10 minute read
High Energy
Nigel Benton looks at the challenges to maximising the energy effi ciency of Australian aquatic facilities
Rising energy costs and, in particular, the recent surge in the price of gas, has the potential to dramatically increase the cost of aquatic centre operations, highlighting the need for facilities to consider switching to electric appliances and increase their use of renewables.
Advertisement
In a way, as local governments look to achieve net zero emissions by 2050, the current price rises are bringing a sharp focus to the challenges faced by the owners and operators of aquatic assets.
With Australian aquatic facilities traditionally being highly energy inefficient, Derek Harbison, Director at Negawatt Projects, suggests that aquatic facilities consume up to 15 times more energy per floor area compared to an average commercial office building.
Harbison advises “aquatic centres in Australia currently use too much energy and these next price rises are going to push that over the top for some centres.
“After the last price rise for gas in Victoria the aquatic centre industry had a wakeup call and now they are looking down the barrel of severe financial pressure if no action is taken.”
For many operators and businesses the immediate shortterm impacts of surging gas or electricity prices may be tempered by longer-term 12-to-24-month power purchasing agreements.
However, that gain may only be short term, with Paolo Bevilacqua, General Manager at Frasers Property Australia’s wholly-owned behind-the meter energy retailing business Real Utilities, explaining “if you locked into an energy contract 12 or 24 months ago and you’re about to come out of that, let’s say over this winter, you’re potentially going to see a 50% cost increase.”
Harbison urges the Australian aquatic industry to look at best practice in energy use intensity (EUI - kWh energy consumption per square metre per year), a measure that shows many facilities performing poorly.
He also urges aquatic facility owners, designers and operators to consider measures to reduce energy costs including looking for insulation opportunities for walls, ceiling and glazing; moving to electricity for air and water heating; recovering heat wherever possible and using thermal and electrical storage where possible.
He also suggests the introduction of LED lights, pool blankets, solar heating and other technologies, all of which can be retrofitted.
In recent years, to reduce energy consumption there has been a lot of focus on plant and plant upgrades (driven, in part, by the availability of grants, rebates and innovative capital deferring options) as well as on facility design.
With design, architects and many current facilities are aspiring to achieve the Green Building Council of Australia’s Green Star rating, but Harbison questions whether that really is a true measure of a building’s energy efficiency, commenting that EUI “is a better gauge of the efficiency of facilities and is commonly used in measuring European centres”.
Anecdotal evidence suggests that Australian facilities lag far behind international best practice in energy efficiency.
However, among emerging examples of best practice is the Pimpama Sports Hub on the Gold Coast, one of Australia’s first sports and community hubs designed to be 100% energy self-sufficient.
The precinct’s 1924 solar panels generate enough renewable energy to power the site, backed by 444 kilowatts of battery storage. It also includes cogeneration power systems to assist with heating the pool that can be used as a backup in the event of a power outage or grid failure.
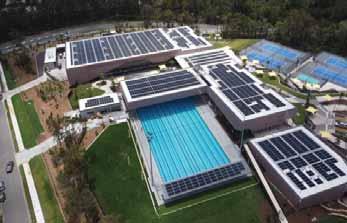
Solar installation at Pimpama Sports Hub’s aquatic centre.
The latest installation eclipses one of the Gold Coast’s largest existing clean energy-generating installations at a leisure facility which is the 312-kilowatt system at the Gold Coast Aquatic Centre, that was completed as the swimming and diving facility for the Gold Coast 2018 Commonwealth Games.
The Pimpama Sports Hub’s power-generating capacity is a major boost to Gold Coast City Council’s Virtual Power Plant, which already harnesses solar energy from more than 47 city buildings. Overall, the Gold Coast has around 3.3MW solar PV system capacity, saving ratepayers around $400,000 a year in energy costs.
Michael Cook, Principal at Hunt Architects, has highlighted how councils need to look beyond plant upgrades to deliver energy efficiency, suggesting “swapping end-of-life or inefficient plant for modern technologies is only half the opportunity.
“Poorly performing building envelopes represent a ready issue to be addressed, with refurbishment offering compounding benefits when combined with plant upgrades.”
Referencing RMIT modelling that shows energy savings in excess of 55% are achievable with a high-performance building envelope compared to a typical aquatic centre, Cook cites insulation, glazing, airtightness and the prevention of thermal bridging as being able to help council-owned aquatic assets reduce energy consumption and move closer to net zero.
He sees this focus on plant upgrades alone and to all-electric systems as being driven in part by the availability of grants, rebates and innovative capital deferring options.
Cook points out “most councils are currently fixated on the shocking energy bills and early failures of mechanical plant. As a result, there is still a lot of confusion and anxiety in councils
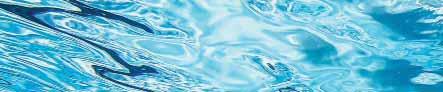
Technical note on aquatic centre design by the SUHO consultancy
In the southeast of Australia, and perhaps beyond, indoor pools have historically been designed in such a way that suggests … continuous thermal enclosures were not a priority. Gaps in a building’s thermal enclosure - including gaps in construction, thermal bridging and low performance glazing - seem ubiquitous. Such gaps result in heat loss as well (as) condensation.
Insulation is a key component of the thermal enclosure. There seems to be a wide variation of insulation levels used in pool halls (above water). Except for some spas, it is unclear if most pools were insulated below ground at all. Some seem to be entirely uninsulated while some seem to have … at times discontinuous insulation. Additionally, water leaks also seem to commonly plague many pool shells.
The historical approach to ‘address’ condensation is to use warm air on cold surfaces - that is, to make the condensation evaporate into the air (as warmer air can hold more moisture than cooler air). The warm air also reduces the heat loss from the pool water, particularly if the air is warmer than the water. This results in a huge energy demand on heating air and subsequently exhausting it. (The air directed at the glazing in a Southbank pool is 40C for example.) Hot air at the glazed facade means thermal bridges leak more heat. And because the air needs to be changed over, there is a very significant amount of energy lost from continuously exhausting warm, moist air and heating intake air. While some pool halls include heat recovery systems to minimise heat loss, it is unclear how efficient these systems are, if they are integrated into ventilation systems and if these are prefabricated, off-theshelf systems or a customised component.
Besides visible condensation, invisible condensation within wall construction is also problematic, as it is associated with risks such as mould, rot and/or corrosion. Noy Hildebrand, Sustainable Design Consultant and Architect. SUHO is the oldest specialised sustainable building consultancy firm in Australia.

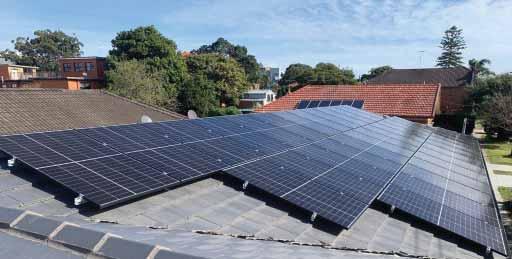
Fit2Swim swimming and wellness centre in Maroubra, NSW.
about how best to proceed.
“But reaching for net zero is not simply about the systems and technology and a like-for-like swap in terms of plant capacity. It’s also about driving efficiencies in the use of energy so that demand is reduced.
“Get the passive, set-and-forget elements right in terms of the building envelope and you can drive down capital expenditure simply by reducing the size of the plant required.
“And with lower operating costs, a centre can draw closer to budget neutrality, returning funds for programs and stabilising entry costs, or simply lowering council overheads.”
Operating 24/7, with high internal operating temperatures (relative to ambient air) and high chemical content, council-owned aquatic assets have disproportionately high carbon footprints.
Glazing typically releases its heat eight to nine times faster than an adjacent wall, while skylights release a staggering 17 times more energy than the adjacent roof. Even a typical insulated wall consumes over 30% more energy to keep warm than a high-performance wall.
A 2019 study by Dr Jean Jonathan Duverge of the Northern Environmental Design Pty Ltd (Energy performance and water usage of aquatic centre, RMIT Dissertation: Abstract) benchmarked “the energy consumption of aquatic centres ranged between 648 kWh/m2 and 2,283 kWh/m2”.
This means some centres are using 3.5 times more energy for every metre of floor space compared to their more energyefficient counterparts.
For those centres facing a bigger net zero challenge, it’s especially good news that the benefits of plant upgrades can be multiplied when combined with general refurbishments.
Cook points out that retrofit approach can also bring significant health and wellbeing benefits for staff and patrons, noting “these include upgraded air quality through improved circulation, temperature comfort and reduced odours.
“Most retrofit options can be undertaken while the centre is operating and most result in a set-and-forget or lowmaintenance outcome. Air quality and condensation issues are also improved.
“With the drive for net zero, it’s well worth councils sitting down with an aquatic centre design specialist who can assess the specific needs and challenges, recommend tailored solutions and model the savings, advise on the grants and rebates available in each state, and look after the refurbishment project from start to finish.”
Cook recently led the delivery of the Fit2Swim swim centre in Maroubra, NSW, built using a unique insulated design.
Prior to its recent addition of rooftop solar panels, the centre was costing less than $100 week to run - with energy costs lower than most modern homes, the new swim school is outperforming even the best-practice benchmark by about eight times at 78 vs 648 kWh/m2/annum.
With its rooftop solar installation now complete, the facility is the most energy efficient swim centre in Australia with owner Dan Glass anticipating zero dollar bills and potential power rebates into the future. Nigel Benton is Publisher of Australasian Leisure Management.
Rebuild or Renew?

With local governments having to weigh up the challenge of Australia’s ageing stock of aquatic centres against the rising cost of new facilities, technology is presenting new solutions for the refurbishment of older aquatic infrastructure.
Robert Savell, Managing Director of Hydrocare Pool Services Pty Ltd, is aware that in refurbishing older centres, an old gravity sand filtration and the carbon content contained is an often overlooked asset.
Fearing that such systems are “simply written off” by many consultants, Savell has experience that upgrading gravity sand filters can be done at a relatively low cost. Savell explains “we have been converting concrete gravity sand filters since 2010 and no new filter system compares. “Our Hybrid Vacuum Gravity Sand (HVGS) filters have been installed on 50 metre pools upgrading flow rates to current codes.”
Savell is passionate about the cost advantages of pool renovations, citing the cost advantages achieved by updating, highlighting that access ramps and extra lanes have been successfully added to old pool structures.
Hydrocare has been involved with concrete filter cells for over 30 years and has specialised in Gravity Sand upgrades for the past 12 years. The performance of the filters is due to the Filter Nozzle design which allows for the improved flow and backwashing.
Concrete Cell Works have been designed for flowrates of up to 694 litres per second.
Gravity sand filtration is an effective and efficient technology that uses coarse sand and other granular media to remove particles and impurities that have been trapped in flocculation (the separation of a solution, commonly the removal of sediment from a fluid).
Currently two HVGS filters are being constructed at the new Casino Aquatic Centre. For further details contact Hydrocare on 02 9604 8396, E: robert@hydrocarepools.com.au