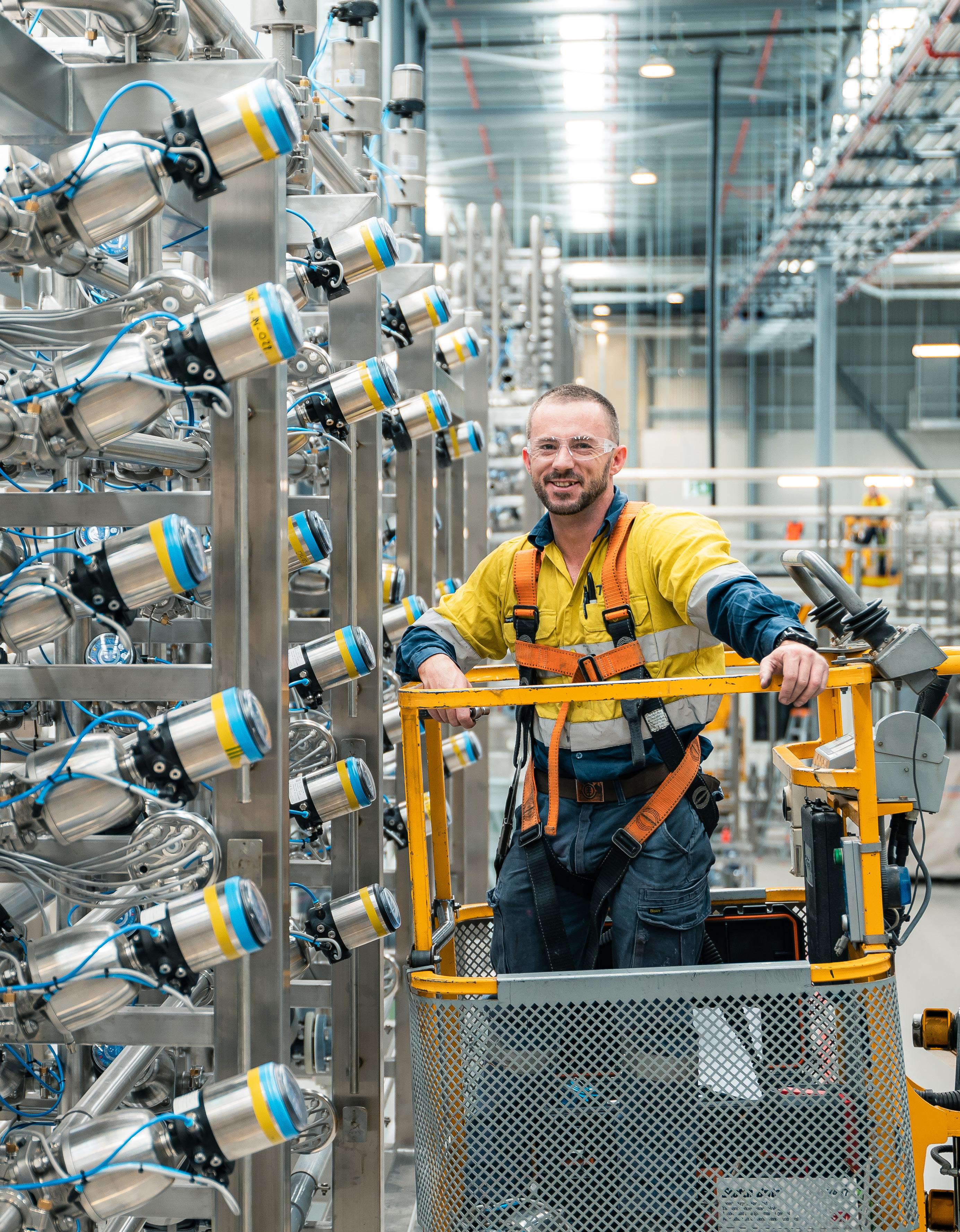
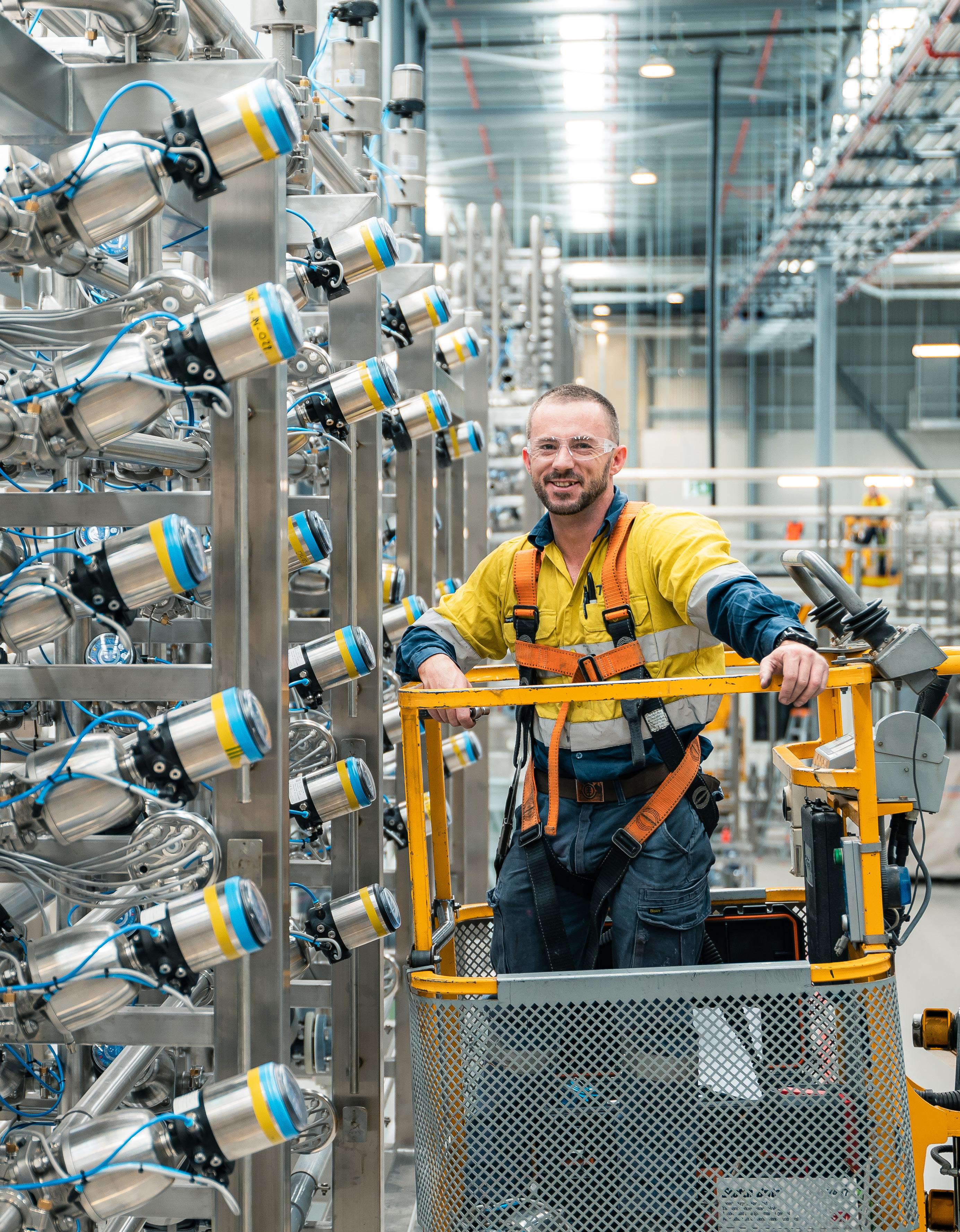
Specialising
in stainless steel and its applications
Photo credit: Shannon Johnston – Risen Film.
Drives Success STAINLESS STEEL
ASSDA Member and Accredited Fabricator TFG Group has showcased its exceptional expertise in stainless steel design, fabrication and installation through the delivery of a greenfield project in New South Wales. Completed in September 2023, the Horsley Park Mixing Plant is a state-of-the-art liquid manufacturing facility set to redefine operational excellence in the production of household and personal care products.
The facility features world-class capabilities, including five standard production lines and a high-volume line capable of filling bottles ranging from 250mL to 5L at speeds of 30 to 100 bottles per minute.
Innovative design and sustainable execution
Engaged in late 2022, TFG was tasked with the fabrication and installation of support structures, stainless steel pipework and valves, along with the integration of free-issue equipment such as tanks and heat exchangers. Stainless steel was the material of choice for all pipework, offering unmatched sanitary properties and chemical tolerance critical for cleaning processes in such environments.
TFG’s proactive role in the design phase proved pivotal. Recognising the project’s goals and the circular economy principles of the client, TFG proposed substituting the initially specified galvanised mild steel support structures with stainless steel. This recommendation not only met the client’s expectations but also revolutionised the project lifecycle.
The adoption of stainless steel delivered numerous benefits, including reduced lead times, improved structural integrity, and a simplified supply chain. Welded connections replaced bolted joints, saving valuable time while enhancing durability and hygiene. By eliminating the need for galvanising, TFG further reduced project complexity and environmental impact.
This forward-thinking approach exemplified TFG’s commitment to long-term sustainability, creating an installation that seamlessly combined functionality, aesthetic appeal, and operational efficiency.
Precision in stainless steel fabrication and installation
The scale and precision of the Horsley Park project are demonstrated in its key installation components:
• 10,000m of grade 316 stainless steel tube
• 2,000m of grade 304 stainless hollow sections (SHS)
• 1,200m of jacketed pipework
• Installation of a 70m long central pipe rack
Over 15,000 welds were completed across the project, highlighting the complexity and attention to detail required to meet the stringent standards. The service gantry alone used nine tonnes of SHS, while all tubes, couplings and fittings were manufactured from grade 316 stainless steel, fully compliant with AS1528.1 Tubes (stainless steel) and tube fittings for the food industry, Part 1: Tubes. Additionally, the clamps were made from grade 304, and stainless steel was incorporated into the electrical conduits to enhance durability. All stainless steel materials for the project were supplied by ASSDA Members Stirlings Performance Steels and Atlas Steels.
Leveraging its national workshop network, TFG strategically divided pre-fabrication works between facilities in Melbourne and Brisbane. Key components, including pipe fences, valve trees, jacketed pipework and flow plates were prefabricated in 12m modules before being transported to the site. The offsite preparation reduced on-site installation time and enabled comprehensive quality assurance checks.
TFG employed orbital welding extensively throughout the project, with parameters such as amperage, gas flow rate, and arc timing carefully calibrated to achieve consistent weld quality. This automated technique is particularly advantageous for stainless steel as it minimises heat distortion and preserves the material’s corrosion resistance.
Delivering excellence
The Horsley Park Mixing Plant stands as a testament to TFG Group’s capability to deliver large-scale, technically complex projects. Despite its ambitious scope, the project was delivered on time, within budget, and with zero safety incidents – an achievement that underscores the professionalism and expertise of TFG Group.
With stainless steel at its core, the Horsley Park facility reflects the material’s enduring appeal and practical advantages, setting a benchmark for future industrial projects.

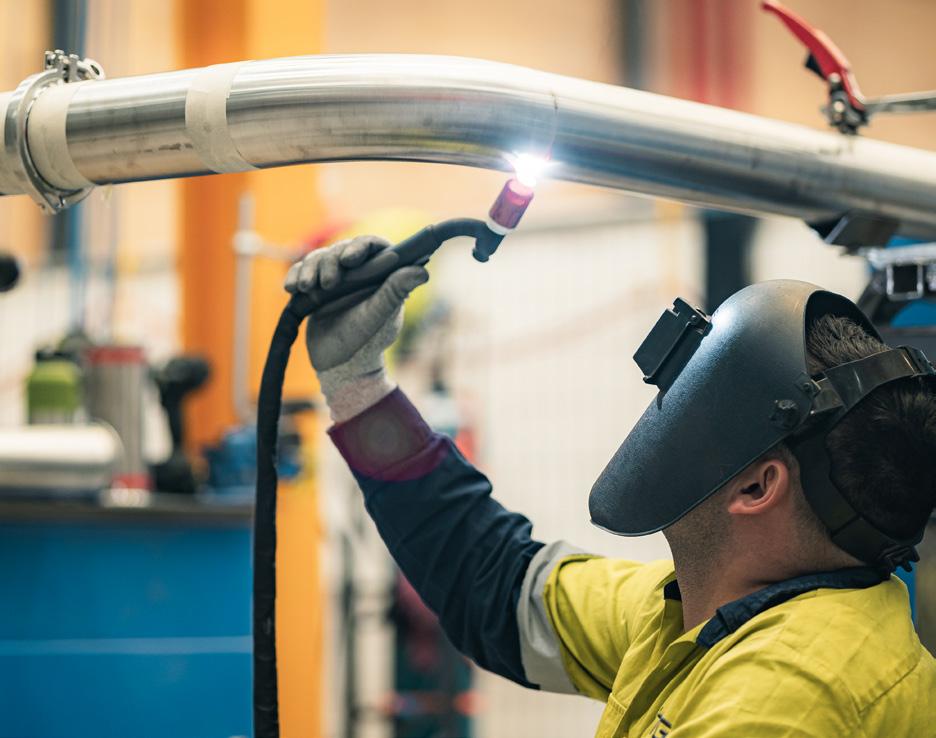
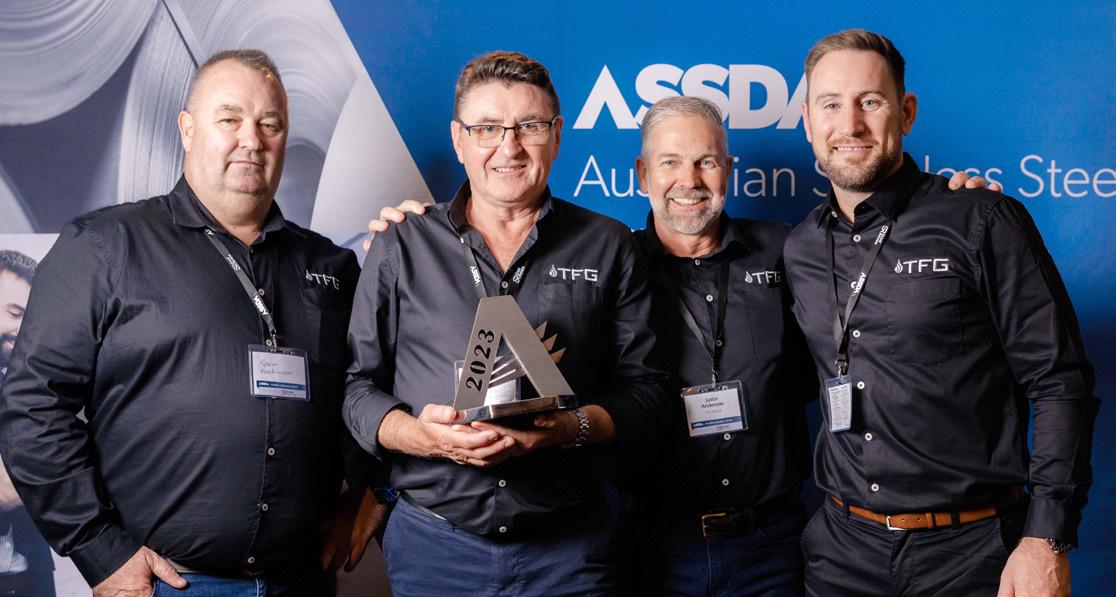

Pictured (left to right): Norm MacKinnon, Tom Moultrie, Justin Anderson, and Paul Byrne. TFG Group
Fabricator Project of the Year Award in the Process Industries
the Horsley Park Mixing Plant.
Photo credit: Shannon Johnston – Risen Film
Outokumpu’s mill in Tornio, Finland, where Circle Green sustainable stainless steel is produced.
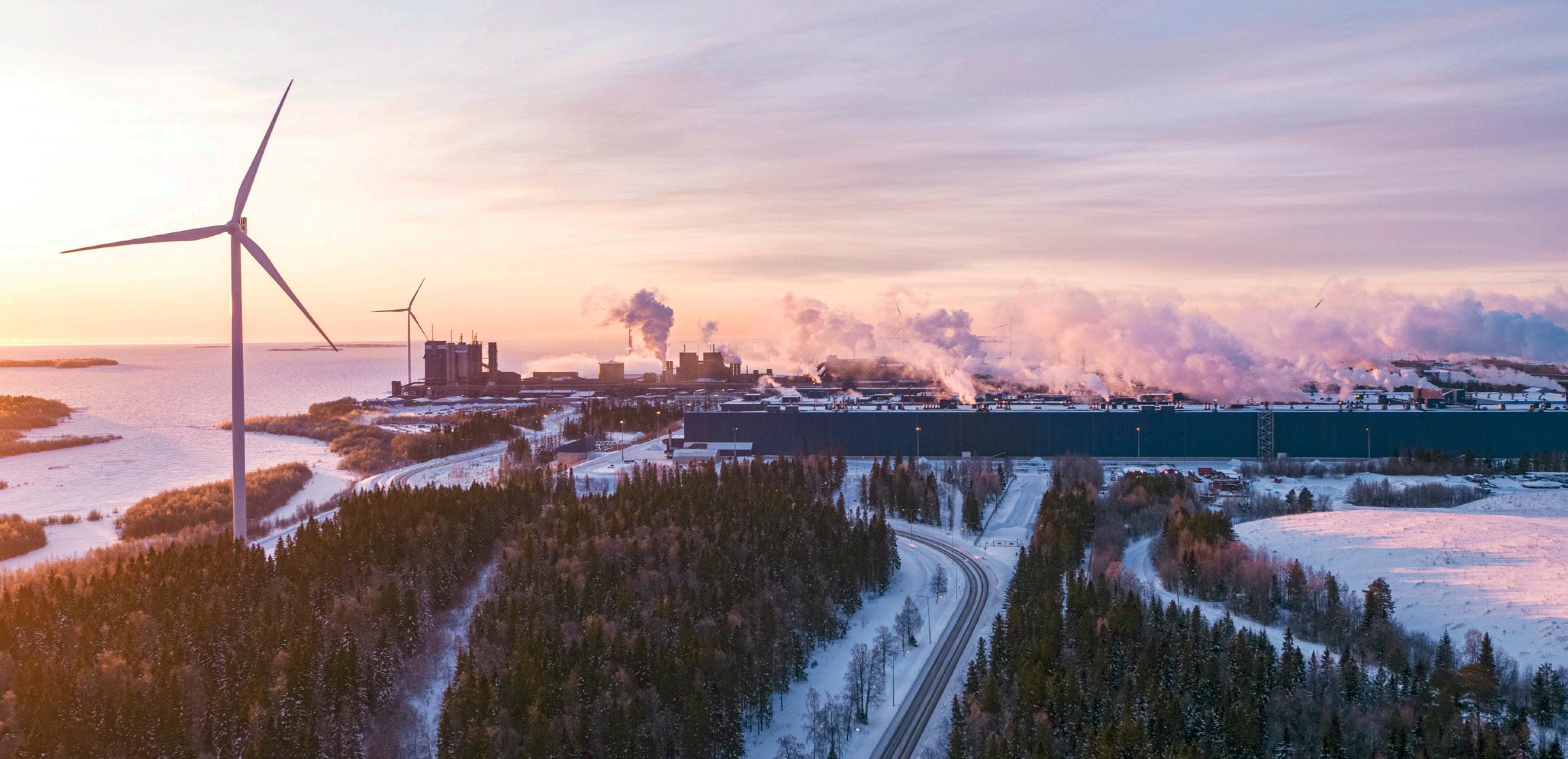
OUTOKUMPU:
Pioneering sustainable stainless steel with Circle Green
ASSDA Member Outokumpu is leading the way in producing emission-minimised stainless steel, with its Circle Green product line boasting a 92% lower carbon footprint than the global average.
As the only stainless steel producer currently approved by the Science Based Target initiative (SBTi), Outokumpu is committed to reducing its carbon footprint by 42% from 2016 levels by 2030, aiming for carbon neutrality by 2050.
One of the key factors in Outokumpu’s low carbon emissions is the high utilisation of recycled materials, achieving 95% recycled content in its stainless steel in 2022. Outokumpu also benefits from having its own chromium mine and ferrochrome production, further reducing its carbon footprint by 42% compared to the industry average.
Outokumpu’s approach includes full transparency, reporting emissions for all Scope 1, 2, and 3 emissions for every product. This transparency supports customers in achieving their emission reduction goals and contributes to Outokumpu’s long-term sustainability strategy. The company delivers productspecific carbon footprint data based on continuous production data, allowing customers to manage their CO2 emissions more effectively.
The Circle Green product line stands out for its unprecedented emission reduction, achieved through meticulous production and quality optimisation, along with the use of biogas, biodiesel, biocoke, and low-carbon neutrality. This innovative approach has enabled Outokumpu to reduce 95% of all Scope 1 and 2 CO2 emissions in its production process. Importantly, while the global average for CO2 emissions is approximately 7 tonnes per 1 tonne of stainless steel produced, Circle Green has achieved an industryleading reduction to just 0.5 tonnes of CO2 per 1 tonne of stainless steel. This means Circle Green customers can cut CO2 emissions by at least 50% compared to conventional stainless steel offerings, delivering a clear and measurable step toward effective CO2 management.
Circle Green’s low-emission stainless steel has already garnered significant interest from customers, particularly in the consumer goods and automotive industries, where sustainability is increasingly becoming a procurement criterion. The first batch was delivered to Fiskars Group for use in cookware products, and demand is growing in both European and US markets.
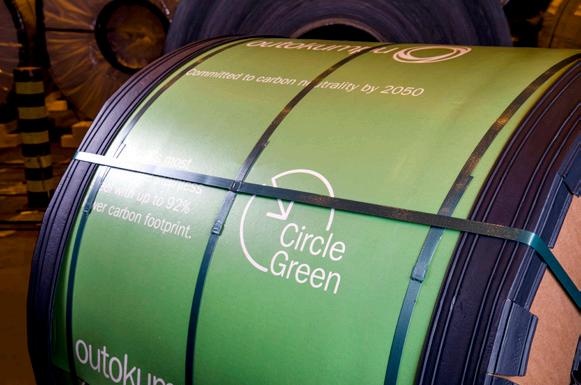
Outokumpu’s approach to carbon emission reduction did not require significant investments in new assets but rather a selective approach to raw materials, fossil-free energy use, and careful production control. What sets the company apart is its unique position as the only major stainless steel producer with direct ownership of a chromium mine and ferrochrome production facility. Paired with access to fossil-free electricity in the Nordics, this advantage places them at the forefront of sustainable stainless steel production.
Looking ahead, Outokumpu aims to integrate sustainability and carbon footprint considerations into every procurement decision. The company is planning a significant investment in a biocoke and biomethane plant, which could further reduce CO2 emissions by over 200,000 tonnes per year and increase self-sufficiency in energy in Finland.
Outokumpu’s persistence and determination to cut carbon emissions demonstrate its commitment to a cleaner, greener stainless steel sector. By focusing on sustainability, Outokumpu is paving the way for a world that lasts forever.
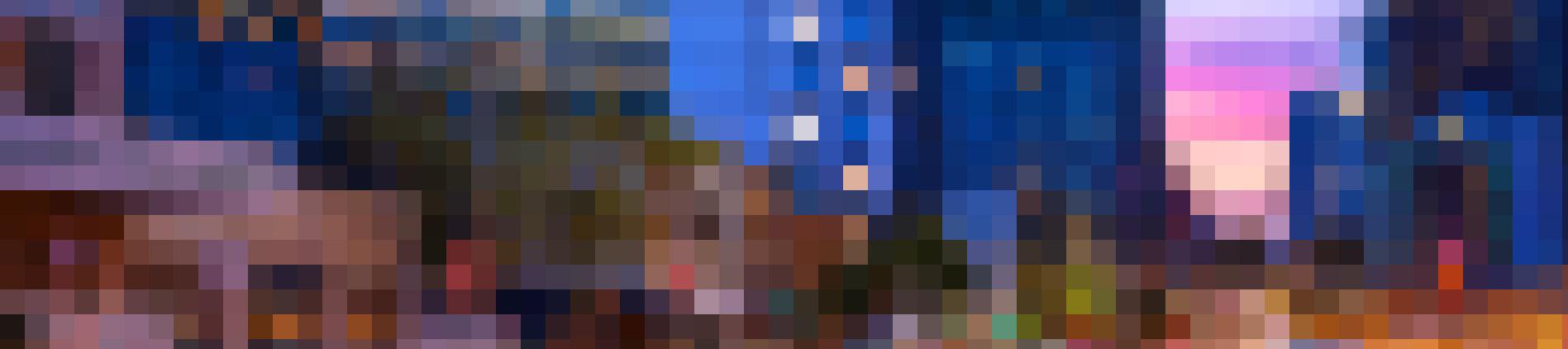
Stainless steel and digital art unite
ASSDA Member and Accredited Fabricator, B&R Enclosures, delivered a custom stainless steel solution for a striking public art installation that transformed the western façade of the Central Club Hotel in North Melbourne. Commissioned by the Australian Nursing and Midwifery Federation (ANMF), the project highlights the versatility, durability and aesthetic appeal of stainless steel in creating unique and functional architectural designs.
A vision in digital windows
Designed by Melbourne studio RAMUS, the artwork titled Silhouettes, consists of 10 low-resolution LED screens housed in custom-made stainless steel window boxes. These ‘digital windows’ intermittently illuminate the façade with scenes of silhouetted figures engaged in everyday activities, offering a glimpse into community life. Integrated seamlessly into the building’s architecture, the installation activates the previously unused façade, blending art and light to enhance the surrounding cityscape.
Located at 249-280 Victoria Street, the ANMF’s building provides affordable, high-quality accommodation for members attending conferences and seminars in Melbourne. The building’s owners sought a façade that was not only innovative and visually striking, but also durable and low maintenance to withstand environmental challenges.
The stainless steel solution
B&R Enclosures delivered 10 window boxes, each measuring 2600 x 1700mm, using over 2.4 tonnes of grade 316 stainless steel with a 2B finish and PE coating. Renowned for its corrosion resistance and structural integrity, grade 316 stainless steel was crucial for ensuring the longevity of the installation in Melbourne’s harsh urban environment, less than 5km from the ocean.
The frames also needed to protect sensitive electronic equipment while integrating seamlessly with materials like glass, silicone, plastic and masonry. Positioned on an exposed western wall, the installation faced additional challenges from Melbourne’s unpredictable weather, making stainless steel’s durability and low maintenance properties indispensable.
Precision fabrication and installation
B&R Enclosures manufactured and operationally tested the window boxes at their factory in Heathwood, Brisbane, incorporating advanced thermal performance engineering to mitigate expansion and contraction issues. The panels were fabricated to exacting specifications and precision, leaving no room for error during installation.
Sustainability was also a key focus. B&R Enclosures’ digitally integrated manufacturing platform reduces waste through initiatives like powder recovery on the paint line and extensive recycling efforts across their operations.
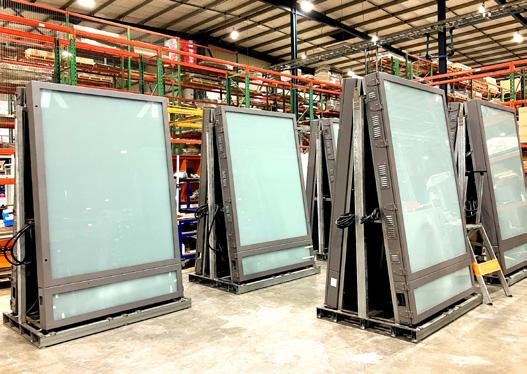
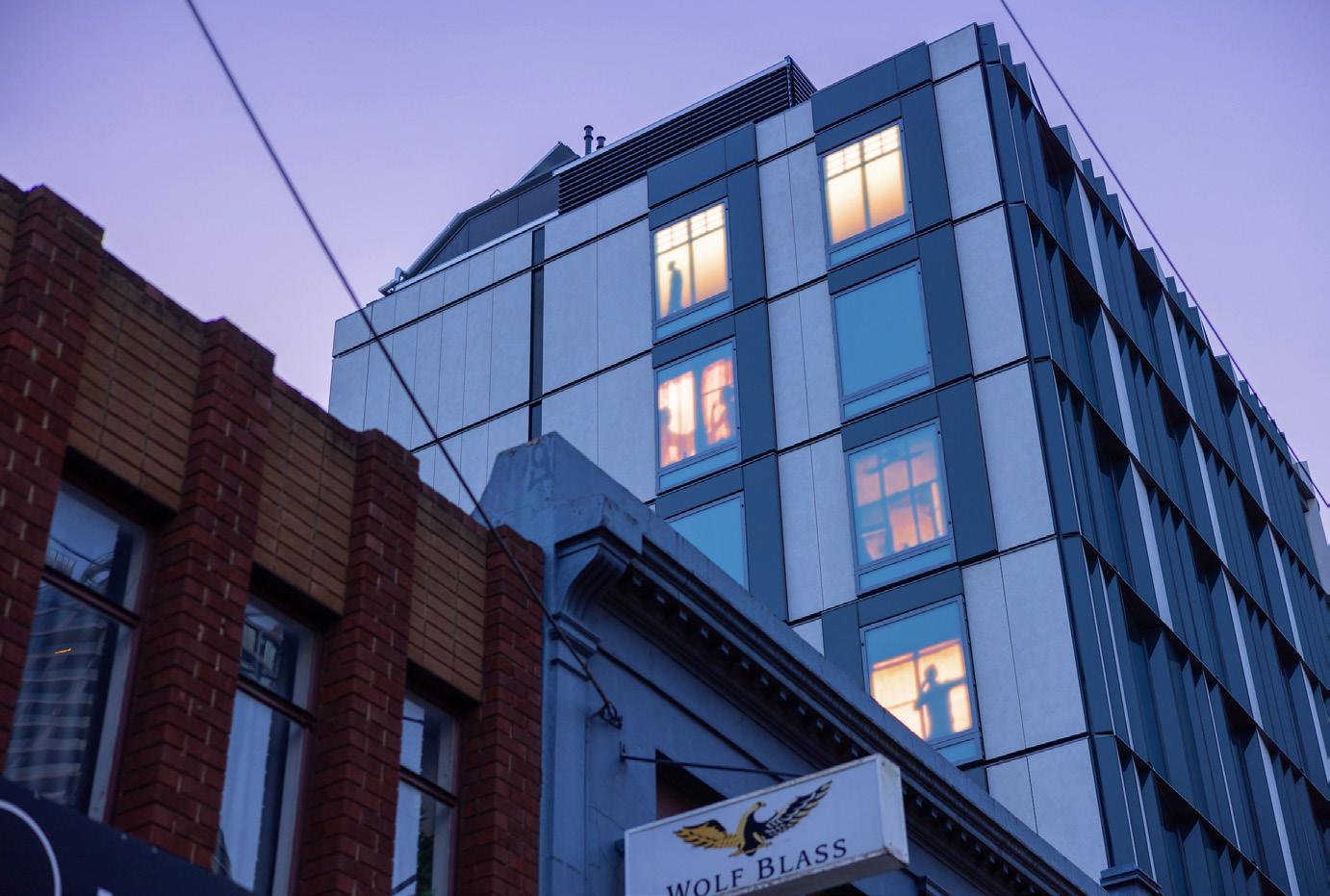
Transported as finished pieces to Melbourne, the stainless steel panels were craned into place and installed within a tight timeframe, ensuring minimal disruption. The final installation now stands as a testament to the collaboration between B&R Enclosures and RAMUS, showcasing the beauty and functionality of stainless steel in architectural design.
From dusk to midnight each evening, Silhouettes quietly animates Victoria Street, inviting passersby to reflect on the beauty of everyday life. This project highlights how stainless steel enables the creation of durable, sustainable, and visually captivating public art, cementing its place as a cornerstone of modern design.
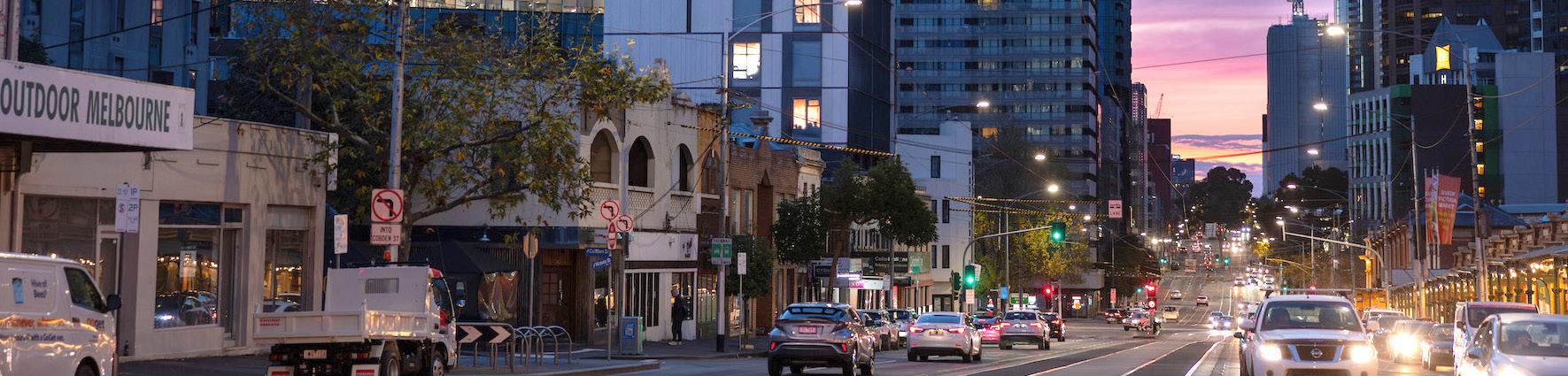
Photo credits: RAMUS
Storage and handling
OF STAINLESS STEEL
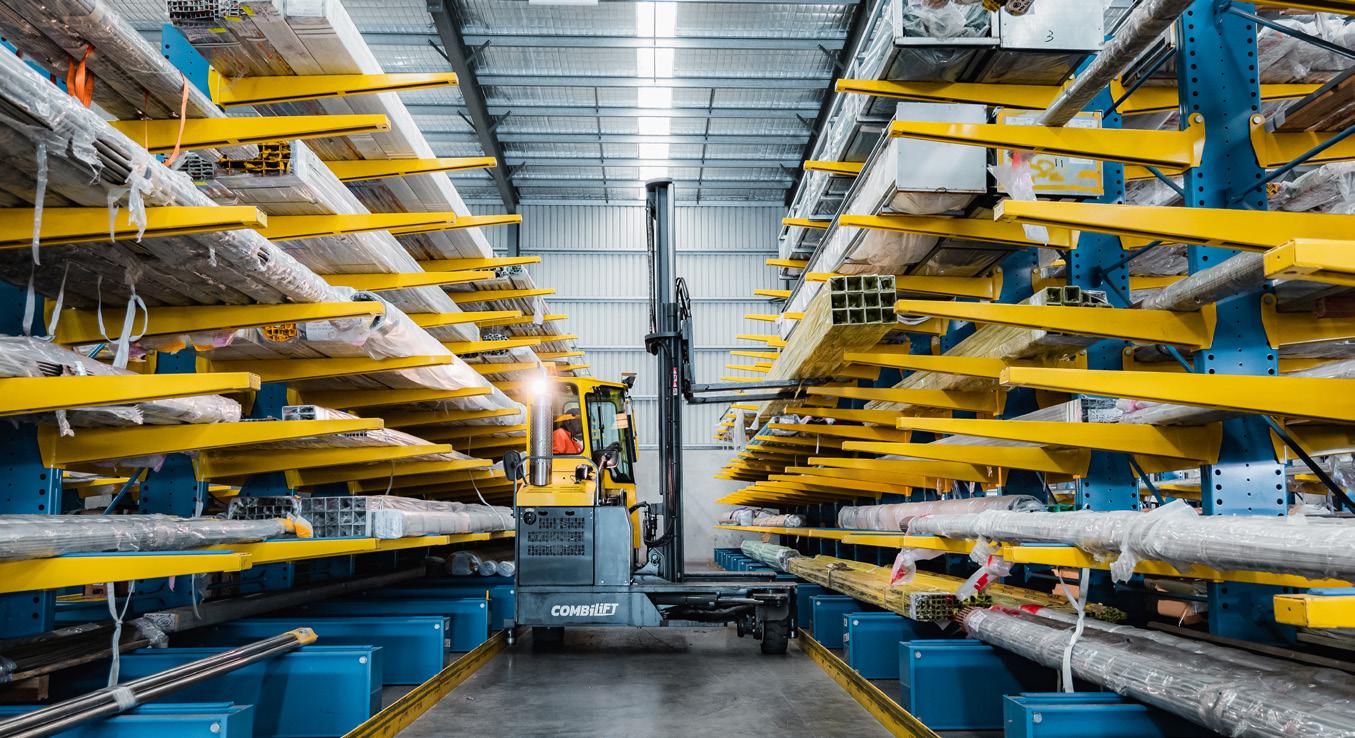
Proper storage and handling of stainless steel are crucial to maintaining its bright, durable finish. Care must begin at delivery and continue through storage, fabrication, transport to the end customer and beyond.
Potential issues:
Scratches or burrs: Can occur due to unprotected metallic rack supports, rough handling, inadequate packing, or contact with forklift tines. Use protective materials like wood, plastic, or carpet to minimise damage.
Distortion or dents:
Thin sheets and small-diameter tubes need adequate external support (e.g. boxes) to prevent kinking, flattening, or deformation.
Stainless steel is vulnerable to contamination from carbon steel and chlorides, which can lead to corrosion.
Carbon steel contamination: Grinding or polishing carbon steel will produce fine particles that spread unless there is proper local extraction. Avoid processing carbon steel and stainless steel in the same workspace.
Shared tools and equipment: Presses and guillotines used for both materials must be cleaned thoroughly between uses or else lines of steel (and subsequent rust) can occur. Beds should be covered and wiped down immediately before handling stainless steel. Tools used for carbon steel should not be used on stainless steel.
Tie-down straps: Avoid carbon steel tie-downs, as fretting and deposits can cause staining and pitting. Galvanised straps are also problematic due to zinc deposits, which can lead to corrosion and, in welding, liquid metal embrittlement.
Surface contaminants: Dust, dirt, or marks from carbon-based materials (e.g. pencils, sooty flames, boots) can cause sensitisation during welding, reducing corrosion resistance. If residual dust poses a risk in tubes or pipes, end caps may be necessary.
Chloride exposure: Common sources include seawater, sweat, hydrochloric acid fumes from brick cleaning, and food and drink residues. When the relative humidity exceeds 55%, chlorides can absorb moisture, breaking down the stainless steel’s passive film and causing rust spotting. Best practice is to shield stainless steel from chlorides, but if contamination occurs, prompt washing with low-chloride water followed by thorough drying can mitigate the risk.
Hydrotesting considerations: Use low-chloride water free from suspended solids. Ensure the design allows for complete drainage and drying after testing to avoid long-term corrosion risks.
Improper storage:
Poor support in pigeonhole or rack storage can lead to physical damage.
Store stainless steel separately from carbon steel or thoroughly wrap it if shared storage is unavoidable. Clean surfaces thoroughly after unwrapping.
Indoor storage is ideal, but for outdoor storage, ensure periodic cleaning based on environmental exposure. Longterm outdoor storage of materials and fabricated goods (including after delivery to site) requires careful consideration of environmental factors, as exposure to moisture, chlorides, and pollutants can lead to corrosion, staining, and other surface damage.
Use tie-on tags or non-aggressive markers for labelling offcuts. Avoid sticky labels, as they can degrade and promote crevice corrosion in aggressive environments.
Minimise extended exposure to sunlight for plastic-wrapped items to prevent polymer and adhesive degradation.
By
you
Photo credits: Shannon Johnston – Risen Film
Winners of the 2024 ASSDA Fabricator Project of the Year Awards AWARDS
The Australian Stainless Steel Development Association (ASSDA) celebrated innovation and excellence in stainless steel design and fabrication at its 29th National Conference, PacRim Stainless 2024. The prestigious awards were presented during the Gala Dinner held at Blackbird Brisbane on 16 October.
Launched in 2017, the ASSDA Fabricator Project of the Year Awards recognise outstanding achievements across Australia’s stainless steel industry. The 2024 winners are:
CATEGORY:
Architecture, Building and Construction
Ronstan International
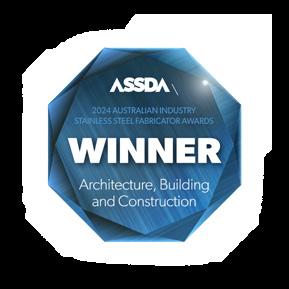
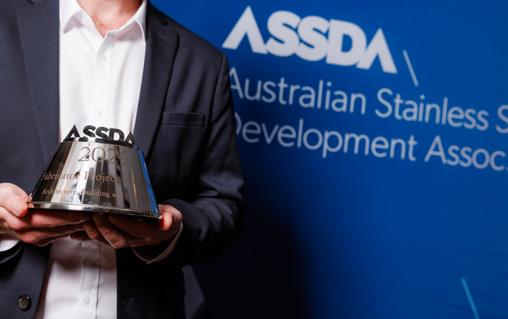
Ronstan Tensile Architecture revolutionised the Narre Warren Station rebuild by replacing 30 tonnes of carbon steel with just 3 tonnes of stainless steel cable. The new cable truss system, comprising precision-engineered stainless steel cables and fittings, supports the station’s ceiling with minimal material use. This innovative design not only reduced the overall weight and complexity of installation but also offered superior corrosion resistance, setting a new standard for sustainable infrastructure as part of Melbourne’s Level Crossing Removal initiative.
CATEGORY:
Process Industries
Total Piping & Mechanical (TPM)
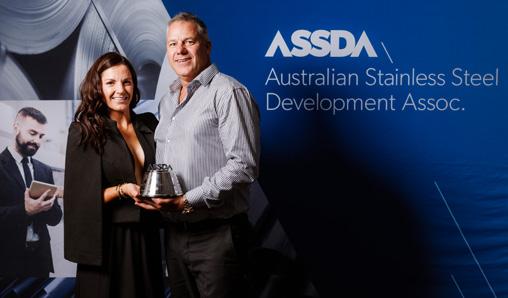
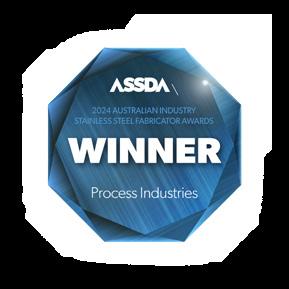
The Gisborne Recycled Water Plant Upgrade in Victoria enhances wastewater treatment capacity for the Gisborne and New Gisborne townships, accommodating an average dry weather flow of 5.57 ML/day. TPM executed the mechanical works, installing critical equipment, including seven blowers, aeration pipework, and a centrifuge unit, all using stainless steel. The upgrade also featured advanced chemical dosing systems, an odour control unit, compressed air systems, and a UV treatment system.
CATEGORY:
Food, Beverage Pharmaceutical
Pure Piping
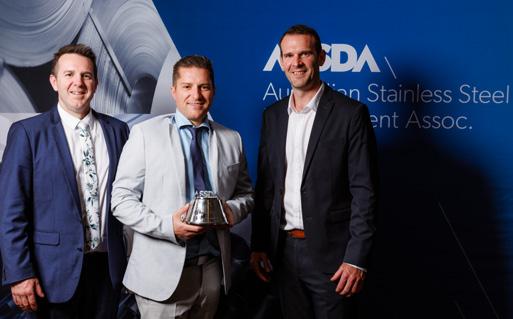
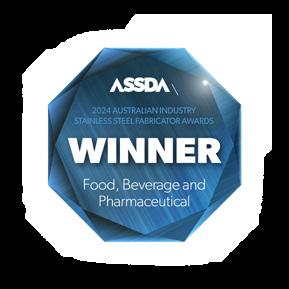
Australia’s first large-scale mRNA research hub and vaccine manufacturing facility will produce up to 100 million vaccine doses annually including COVID-19 boosters and vaccines for respiratory viruses. Pure Piping was engaged to deliver the mechanical pipework and electrical scope, covering design, procurement, installation, pressure testing, passivation, and commissioning.
CATEGORY:
Small Project, Big Impact
Bespoke Wire and Rope
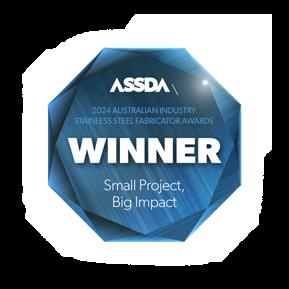

Bespoke Wire and Rope partnered with Plant Based Building Solutions to design and engineer the ‘Urban Arbour’ concept, aligning with existing powder-coated aluminium shelters. To address past corrosion issues, stainless steel was selected for its durability in moist conditions where living plants thrive. This pilot program of six urban arbours aims to yield positive results for future expansions across the Melbourne network.

Congratulations to the winners and all participating ASSDA Members, including Aflex, Arcus Wire Group, Bridgeman, Carlson Stainless, Fineweld Stainless Steel, and Mack Bros Roofing Products.
Special thanks to Midway Metals for sponsoring the event and Southern Stainless for sponsoring the award trophies.
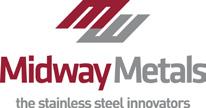
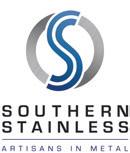
Ronstan International
Mark Owen, Chris Vella, Andrew Owen
Sam Bellis, Daniel Jamieson
Michelle Davis, Matt Taylor
YOUNG PROFESSIONALS NETWORK
Supporting the next generation of stainless steel professionals
The ASSDA YPN is a dynamic initiative designed to empower the emerging generation of stainless steel professionals and leaders. It creates a vibrant community that connects, supports, and enhances knowledge and leadership skills, ensuring a prosperous future for the industry.
Benefits include:
Educational resources:
Access tailored industry materials, trends, and best practices. Learning opportunities: Enhance skills through webinars and training sessions.
Networking events: Build valuable relationships with peers and industry leaders.

Professional and career development: Benefits from leadership tools and career support.
Exclusive to professionals aged up to 40 years from ASSDA Member organisations. Whether you’re an engineer, sales rep, fabricator, or involved in any facet of the stainless steel industry, thrive with us!
For more information about ASSDA Membership and the YPN, contact ASSDA: +61 7 3220 0722 / assda@assda.asn.au / assda.asn.au

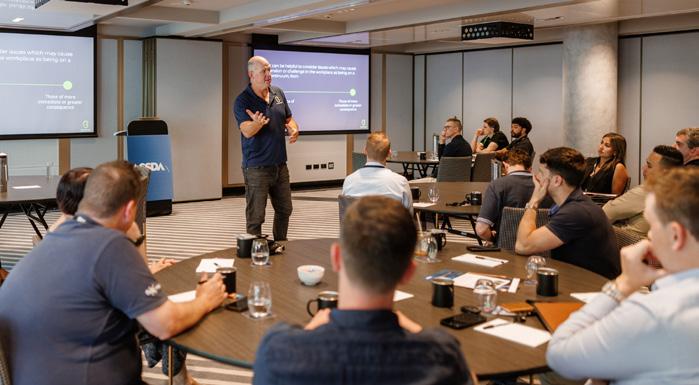
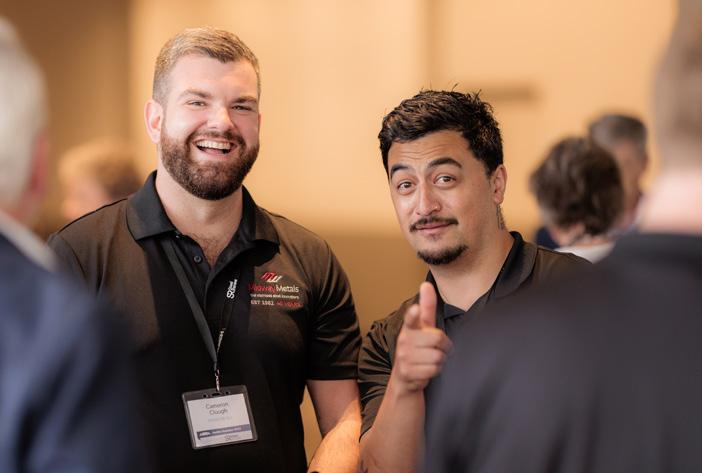
PLATINUM MEMBERS:

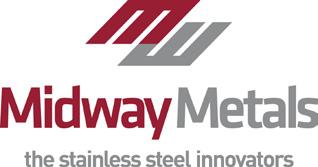
GOLD MEMBERS:
Daming International Import & Export Co., Ltd.
Prochem Pipeline Products
Stanch Stainless Steel Co., Ltd.
Stoddart
YC Inox Co., Ltd.
AUSTRALIAN STAINLESS MAGAZINE
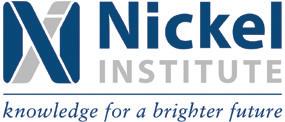


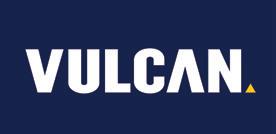
MEMBERS:
Acerinox \ Aqseptence Group \ Arcus Wire Group \ AusPress Systems \ Austral Wright Metals \ Amity Pacific \ Australian
Distributors \ B & R Enclosures \ Callidus Welding Solutions \ Dalsteel Metals \ Fagersta Steels \ HH Stainless Pte Ltd \ Metal Centre Australia \ Outokumpu \ Sanwa \ Stainless Bar & Wire Company \ Stainless Steel Wire & Mesh \ Stirlings Performance Steels \ Yue-Seng Industrial Co., Ltd.
MORE INFO: Enquiries or further information on any material presented in this publication should be directed to ASSDA:
Level 6, 200 Adelaide St, Brisbane Qld 4000 \ +61 7 3220 0722 \ assda@assda.asn.au \ assda.asn.au
EDITORIAL: Contributions of story ideas specialising in stainless steel and its applications are welcome from Members of ASSDA.
ADVERTISING: Advertise in the only publication that reaches a targeted group of 5000+ in the Australian
steel industry. Rates available at www.assda.asn.au.
CONTACT: Lissel Pilcher, Editor: lissel@assda.asn.au
DISCLAIMER: ASSDA
SILVER