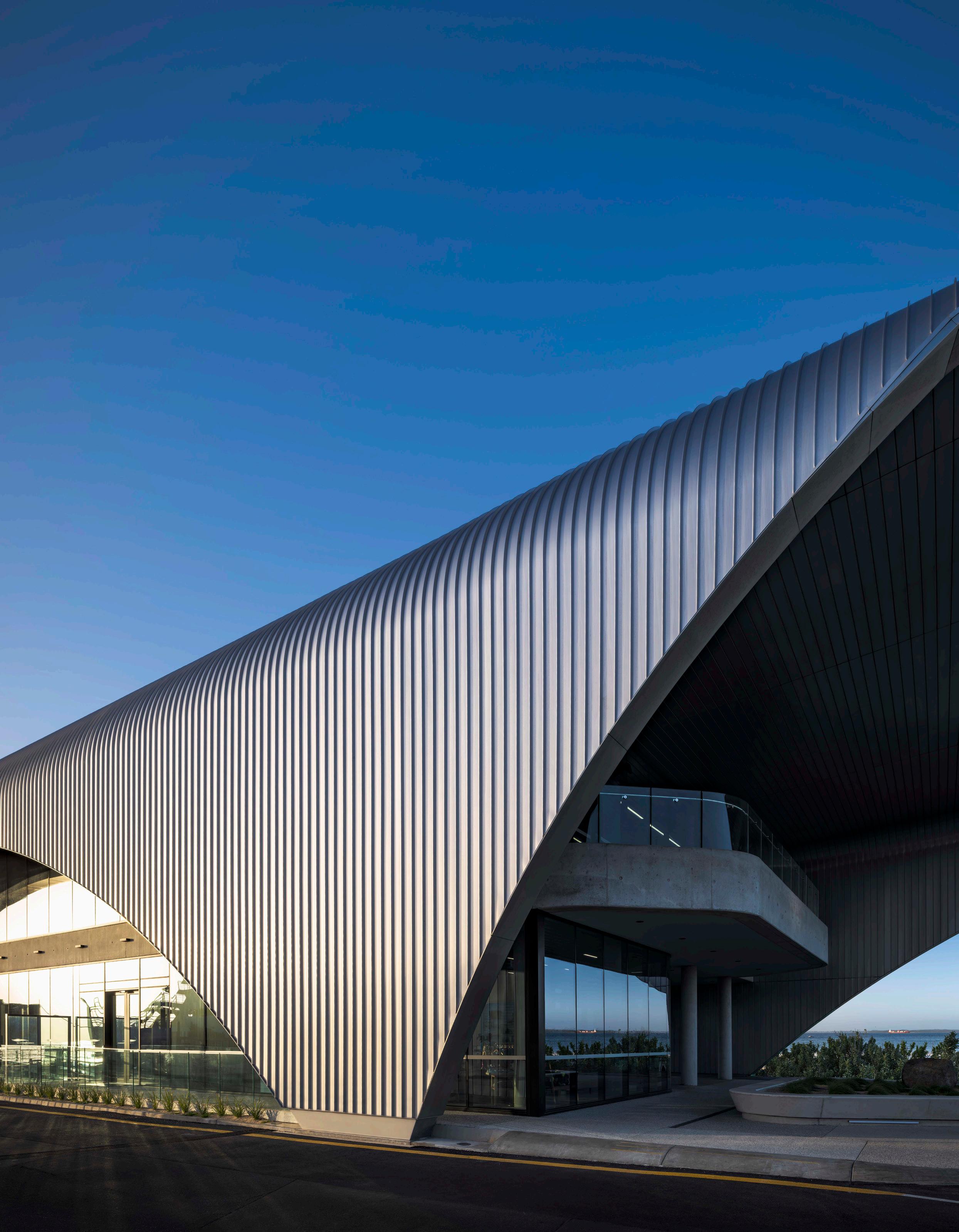
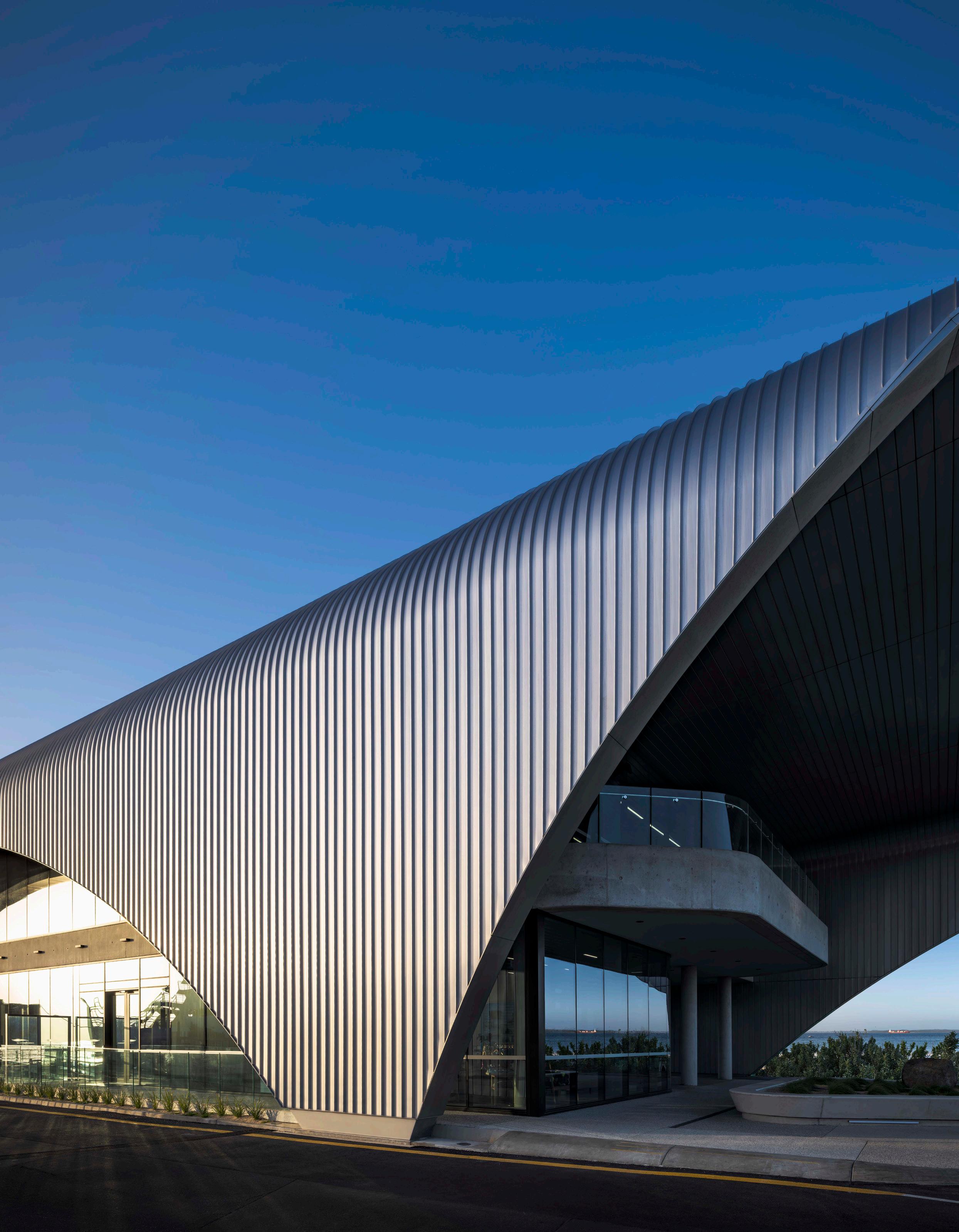
Specialising in stainless steel and its applications
Architectural marvel in stainless steel
QUEENSCLIFF FERRY TERMINAL
At the ingress of Victoria’s Port Philip Bay stands the Queenscliff Ferry Terminal – a beacon of architectural prowess and stainless steel ingenuity. Opened in April 2023 after a decade-long collaboration between visionary architects and dedicated clients, this world-class structure epitomises the marriage of functionality and aesthetic allure.
Linking Queenscliff to Sorrento and beyond, the terminal serves as a gateway to the scenic wonders of Geelong, the Bellarine Peninsula, and the iconic Great Ocean Road. As the bustling hub for Searoad Ferries’ car and passenger services, it orchestrates over 8,200 crossings annually, welcoming more than 960,000 passengers.
Designed by F2 Architecture and built by Kane Constructions, the terminal transcends mere functionality, drawing inspiration from its surroundings and historical context. Its roof, a masterpiece of engineering, stretches gracefully with a nod to the curved profile of this unique stretch of coastline.
At the core of this architectural marvel lies stainless steel, a material renowned for its durability and timeless elegance that will withstand the test of time.
ASSDA Member Austral Wright Metals supplied 445M2TM ferritic stainless steel sheet with a 0.7mm thickness and 2DR finish for the project. Ferritic stainless steel offers a lower expansion coefficient than 316L austenitic stainless steel, a similar thermal expansion to carbon steels, and it can be readily bent, rollformed, pressed to shape, or spun. Offering superior corrosion resistance, it is a desirable and aesthetically pleasing material choice for mechanically fastened roofing and cladding applications in marine environments.
ASSDA Member Mack Bros Roofing Products took up the mantle of transforming the stainless steel into a symphony of form and function.
Employing cutting-edge techniques and a newly developed curving machine, the stainless steel panels were meticulously shaped ensuring both precision and consistency.
The panels were manufactured in batches where matching profiles were critical to delivering the architectural vision and installation requirements. Mack Bros also designed and built a testing rig to ensure the structural integrity of the roof sheet installation and compliance with AS/NZS 1170.2:2011 Structural design actions, Part 2: Wind actions. Various installation methods were modelled to overcome challenges with curved reveal soffit panels and intricate sub-structure alignments. All panels were mechanically fastened on site.
Transporting the stainless steel panels posed its own set of challenges, necessitating specialised racks to safeguard against damage during delivery.
ASSDA Member Fabmetal Specialists delivered the curved stainless steel fascia and supports using 600mm wide, 10mm thick, 316L stainless steel plates supplied by ASSDA Member Midway Metals. The fascia panels were electropolished by ASSDA Member MME Surface Finishing to achieve a 0.5 R a finish.
The installation proved challenging, with the structure design beyond the allowances specified in Australian standards. Fabmetal Specialists leveraged their expertise in 3D modelling and drafting to deliver custom bracketry tailored to the installation requirements. Collaboration with Mack Bros Roofing Products ensured the delivery of a high-quality, world-class finish for the terminal’s stainless steel cladding and roof structure in line with the architects’ vision.
The impact of the Queenscliff Ferry Terminal extends far beyond its functional role. It’s a testament to the power of stainless steel to transform landscapes and elevate experiences, boosting local tourism and business while garnering global recognition.
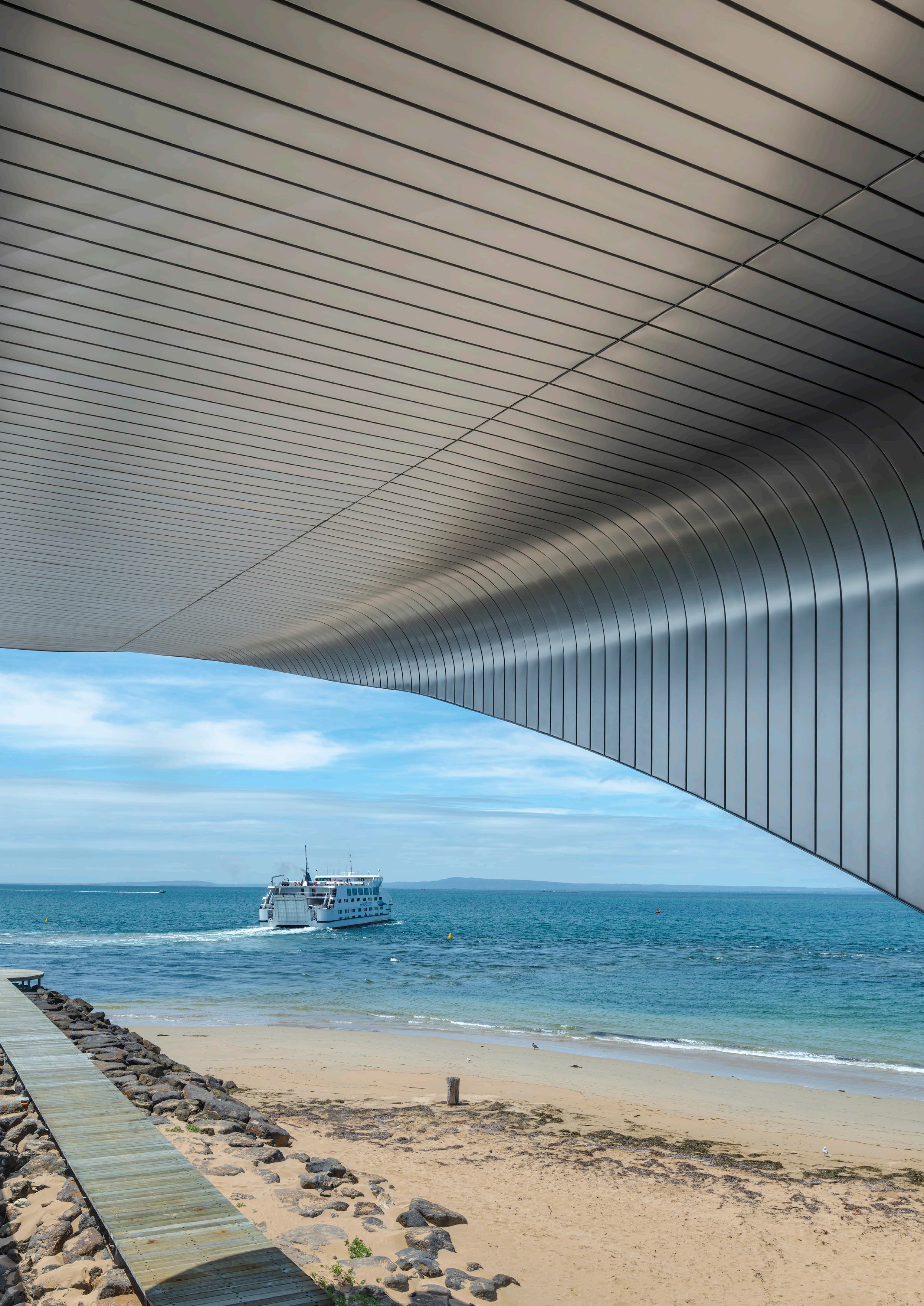
”Stainless steel is renowned for its durability and timeless elegance that will withstand the test of time”
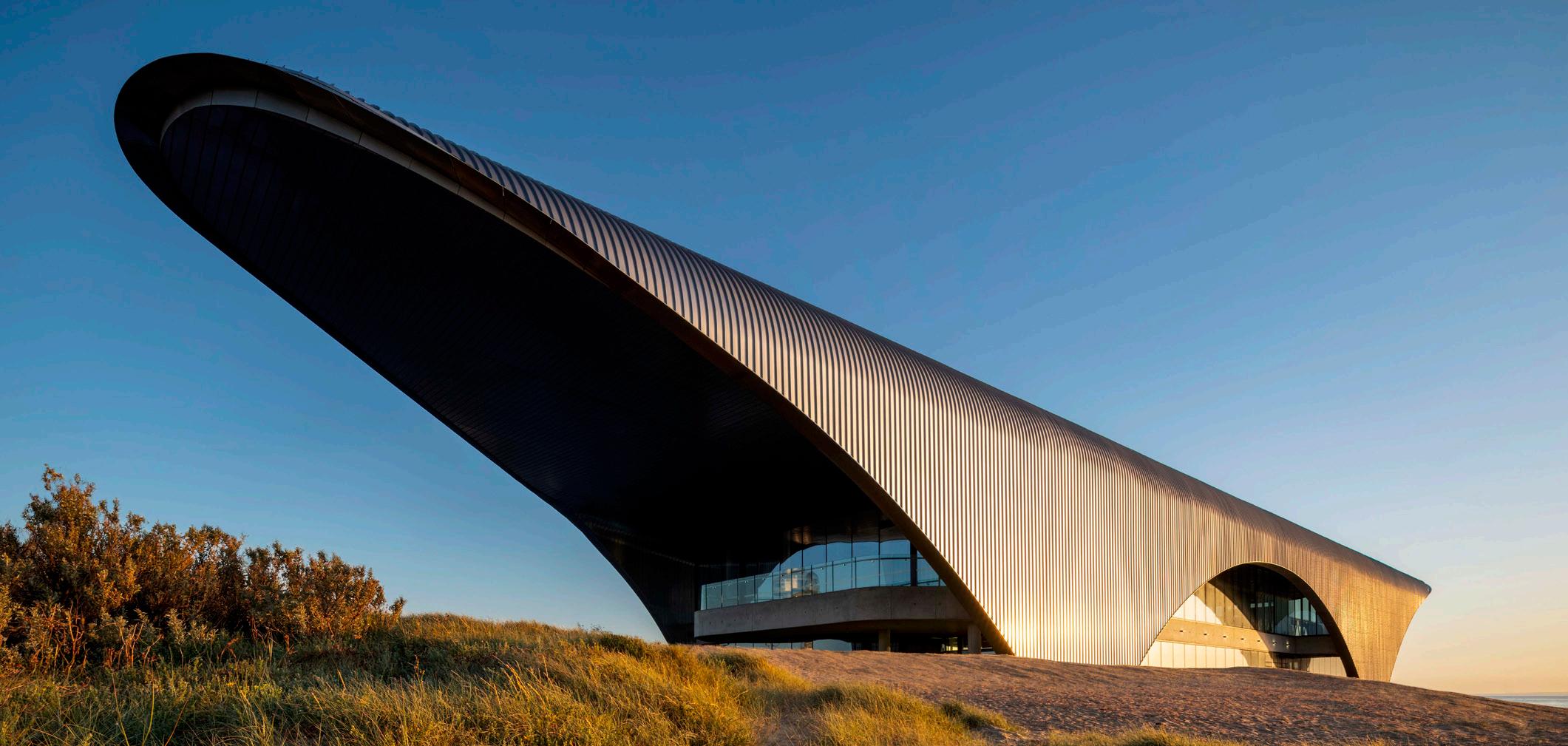
Recipient of ASSDA’s prestigious 2023 Stainless Steel Industry Fabricator Award in the Architecture, Building, and Construction category, the terminal continues to shine on a global scale. Honoured at the 2023 Victorian Architecture Awards and recently celebrated with the international Architectural Masterprize “Best of the Best” in the Transportation category, it stands as a symbol of innovation, excellence, and the enduring allure of stainless steel.
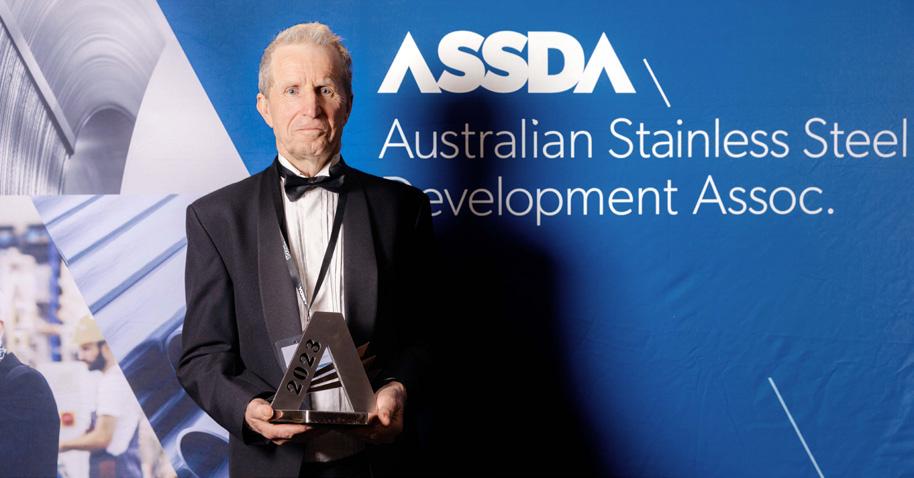
Ian Mack, Director of Mack Bros Roofing Products, accepting the 2023 ASSDA Fabricator Project of the Year Award in the Architecture, Building and Construction category for this project.

\ mme.com.au
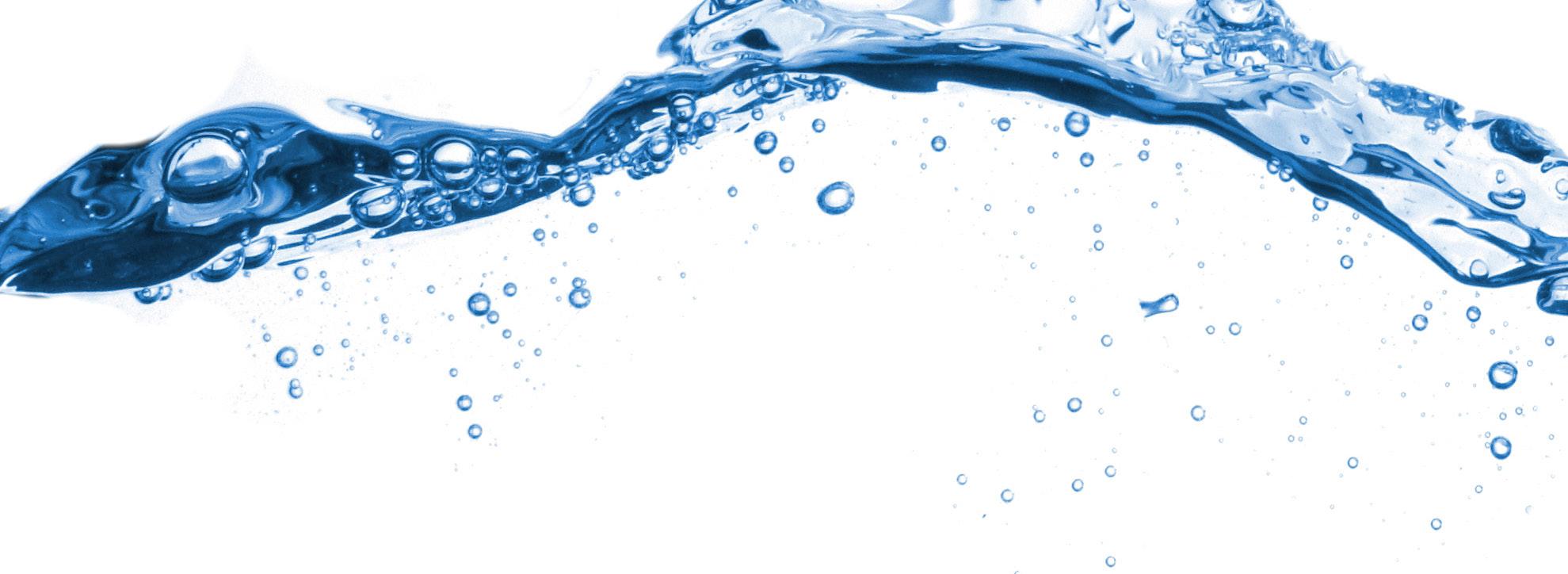
Rheem delivers sustainable hot water solution
Located in Pilbara of Western Australia, Gudai-Darri is Rio Tinto’s first Greenfield mine in the region in more than a decade. Stretching across both Banjima and Yindjibarndi country, both Traditional Owners were engaged through the planning and development stages in Rio Tinto’s most technologically advanced iron ore mine yet. Gudai-Darri features the world’s first autonomous water carts, trucks, drills, and trains, as well as a robotic ore sampling laboratory and solar farm. Gudai-Darri has a 40-year mine life and will support thousands of jobs moving into the future.
THE CHALLENGE
Rio Tinto faced the challenge of providing a sustainable hot water solution for the site’s transit shower block, tasked with meeting the demands of 400 end-of-shift showers, totalling 24,000L of hot water. The project required reliability, energy efficiency and adaptability to the region’s limited energy infrastructure.
ASSDA Member Rheem Australia was engaged by SPP Group to work with Primero and Aussie Modular Solutions in delivering a solution tailored to meet these rigorous demands.
THE SOLUTION
Rheem Commercial stepped in with a robust solution, supplying ten 35kW air-to-water heat pumps, nine 30kW electrical heating units, and nine large-volume storage tanks, each equipped with boost elements to deliver water at temperatures up to 65°C, all while maintaining energy efficiency. Available in vertical, horizontal, and stackable options, the heat pumps were oriented to best fit the space and reduce footprint. The hot water plant design was split into two, for male and female shower blocks.
To enhance safety measures, Rheem incorporated LAN cables into the plant solution design. These cables enable groundlevel monitoring of the stacked heat pumps via the master heat pump at ground level, mitigating potential OH&S risks associated with working at heights.
Central to the design solution was the use of stainless steel storage tanks from Rheem’s RT series, selected for their unparalleled durability, corrosion resistance, and hygienic

properties. The 3,000L grade 316L stainless steel storage tanks not only adhere to rigorous safety standards but also offer the flexibility and footprint efficiency necessary for large-scale projects like Gudai-Darri. WaterMark certified and conforming to AS3498 Safety and public health requirements for plumbing products – Water heaters and hot-water storage tanks, the tanks have a maximum working pressure of 850kPa and a thermal relief capacity of 900kW. Stainless steel’s ability to withstand harsh mining conditions, minimise maintenance needs, and ensure long-term water quality and reliability underscores its indispensable role in the hot water solution.
By integrating stainless steel storage tanks into the infrastructure, Rheem Commercial not only addressed the immediate needs of the Gudai-Darri mine but also laid the foundation for a sustainable and future-proof system that aligns with Rio Tinto’s commitment to innovation and environmental responsibility.
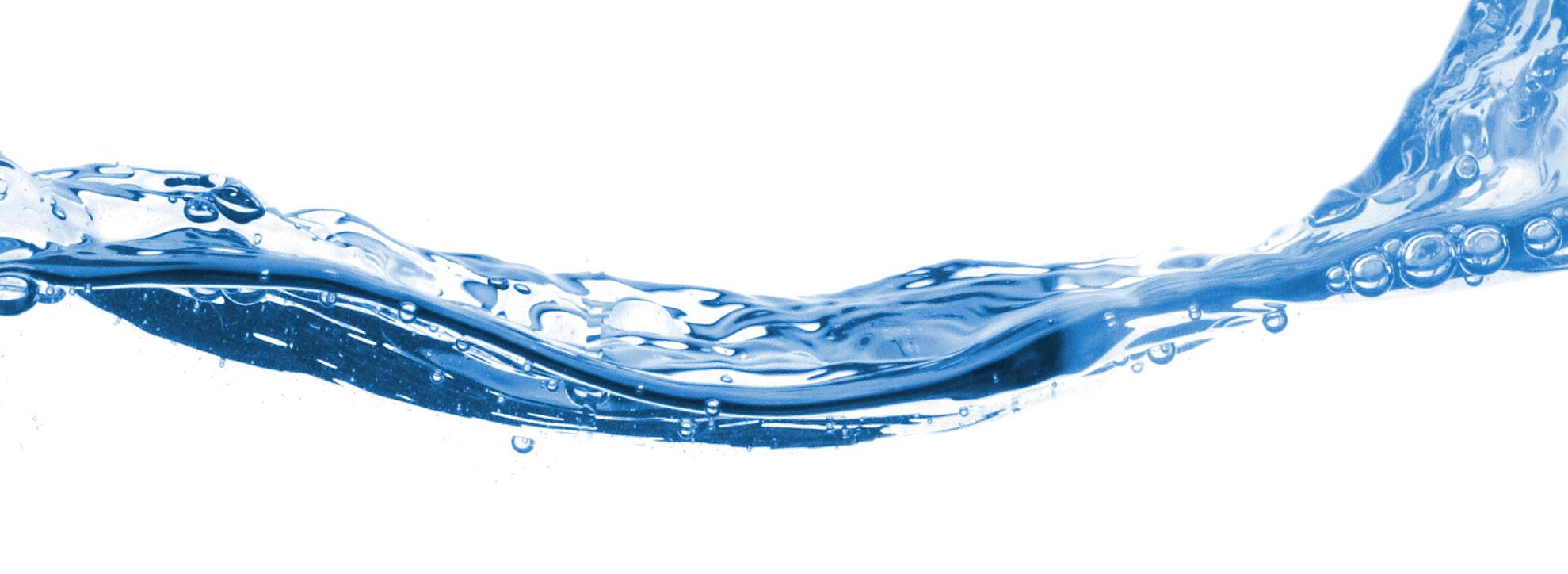


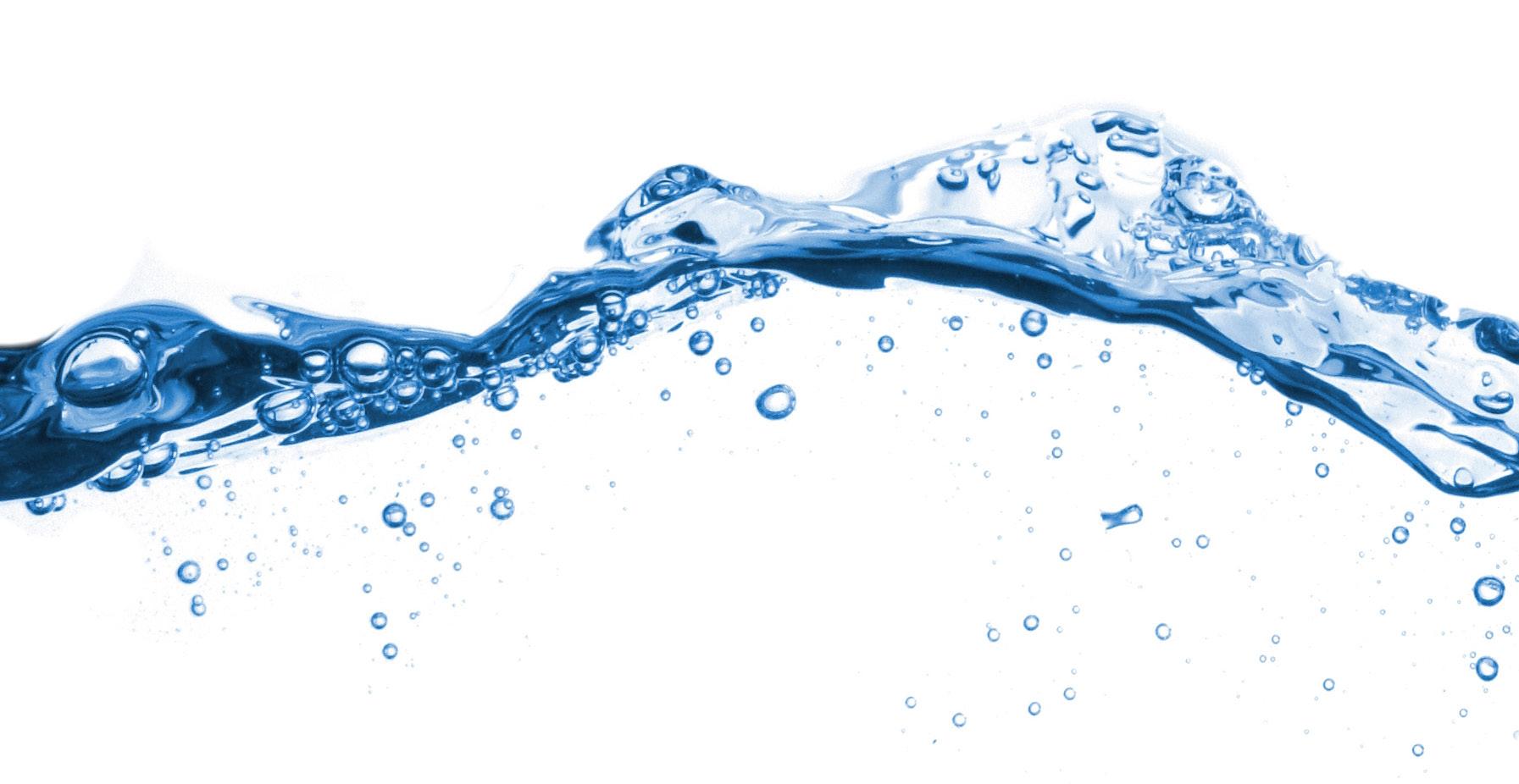
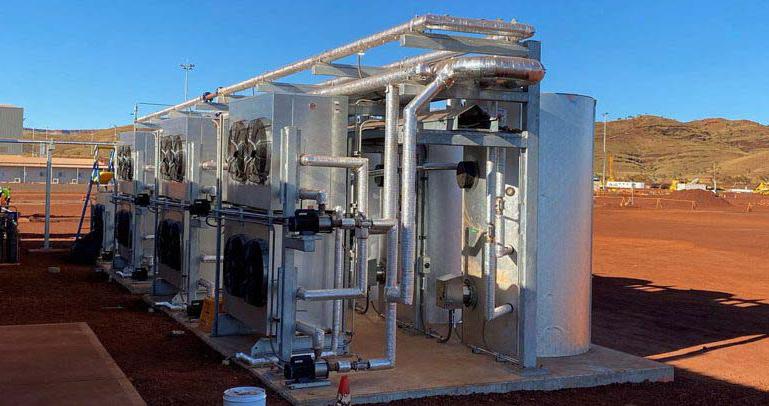
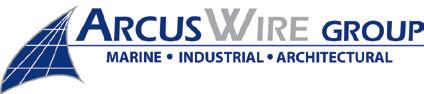
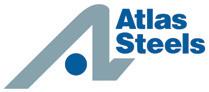
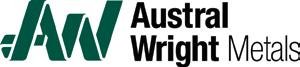
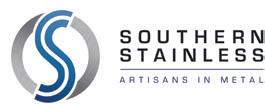
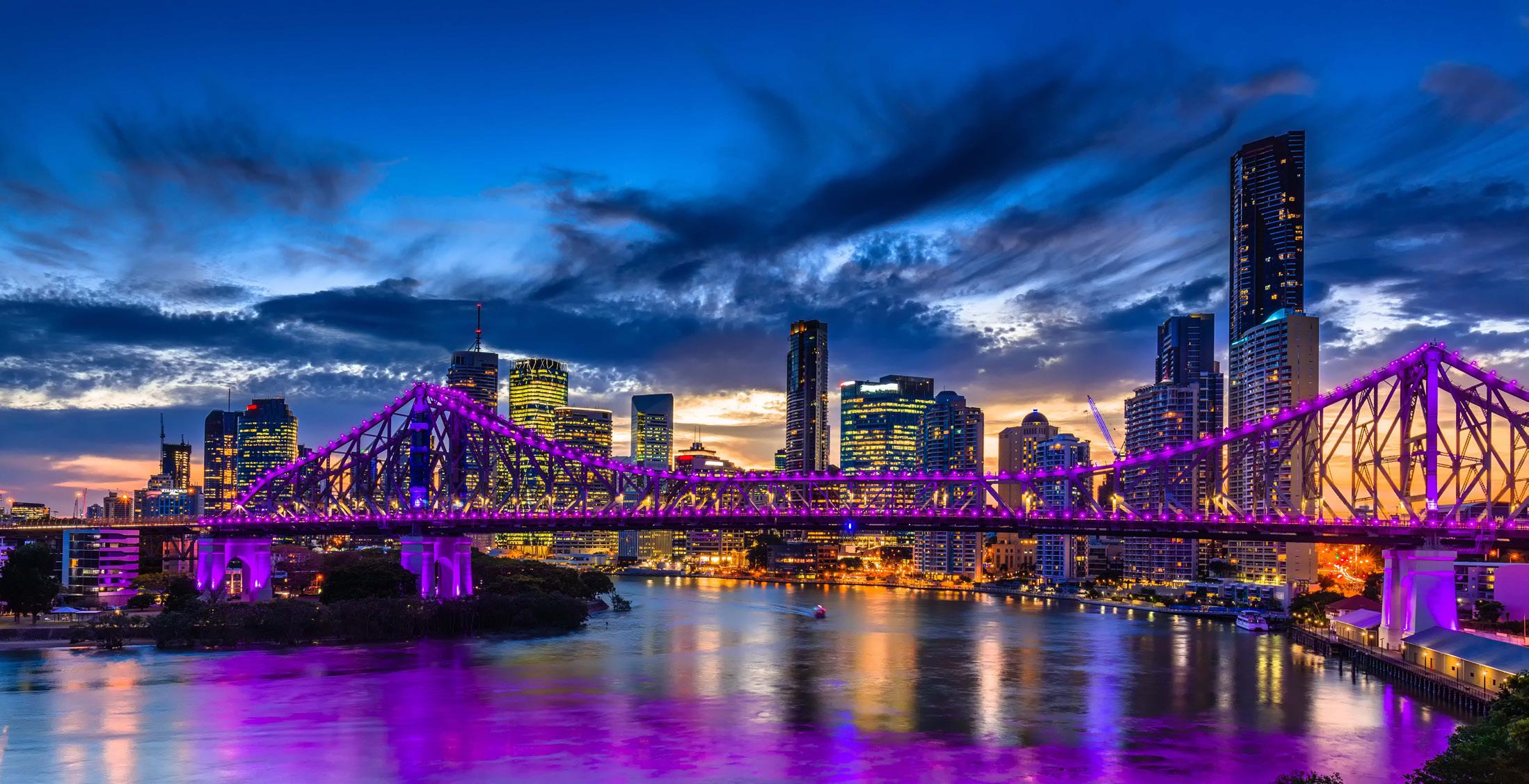
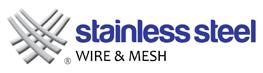



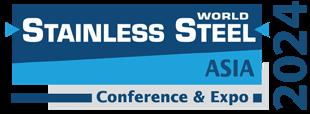
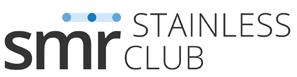
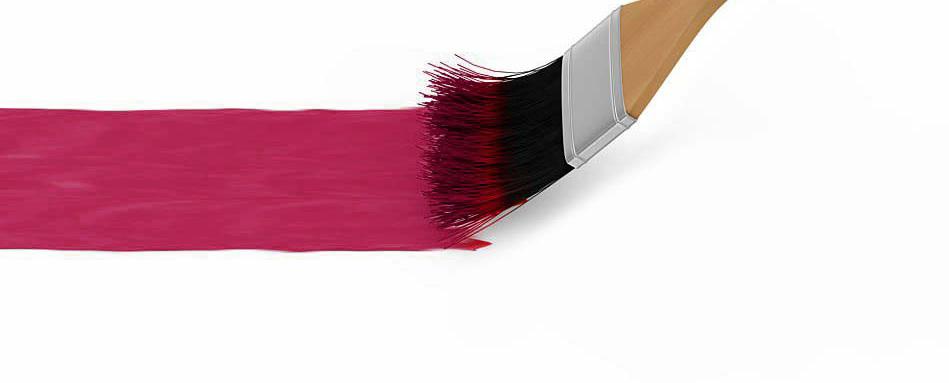
Guidelines for painting
STAINLESS STEEL
When considering painting stainless steel, the initial question arises: why paint it in the first place?
If the design choice is simply about colour or aesthetic purposes and the product form has a smooth surface (i.e. sheet or round products), using factory-supplied coloured stock attached with fasteners might be the preferable option. This construction method is commonly used for non-contact areas such as walls or facades, as exemplified in ASSDA FAQ 12: Coloured and patterned stainless steel
Similarly, in new constructions, there are often reflectance limits to consider. While highly polished stainless steels offer extreme reflectivity, embossed surfaces, like the panels seen on the Petronas Towers in Kuala Lumpur, Malaysia, provide a bright appearance with lower reflectivity.
However, if adding colour is necessary for an existing structure, painting stainless steel is feasible but requires certain precautions. Unlike carbon or galvanised steel, a primer undercoat will not form a chemical bond with the stainless steel surface, necessitating a clean and profiled surface to provide a mechanical key for adhesion. Profiling by chemical etching is possible, but safety concerns make using pickling acids impractical. A relatively mild etch profile can be achieved using oxalic acid, but the most common method of profiling involves abrasion either by blasting or using abrasive belts with aluminium oxide grit, which MUST be free of carbon steel. Garnet is used for blast profiling of carbon steel, but it is not recommended for stainless steel because of potential contamination from this natural mineral.
Before abrasive profiling, the surface must be free of grease and dirt, and any heat tint from welding or thermal cutting must be removed by pickling or abrasion. Due to surface tension, liquid coatings tend to draw back from sharp edges. This requires rounded edges as specified for painted carbon steel (refer to AS/NZS 2312.1 Protection of steel against atmospheric corrosion by the use of protective coatings: Section 3.4). In addition, if thin lacquers are used for an aggressive environment to reduce maintenance cleaning compared to a bare stainless surface, then a spider web of filiform corrosion can creep from sharp cut edges along the stainless-lacquer interface. For small projects, it is not uncommon to use abrasive belts, with typically 80 grit size. If blasting is possible, it should provide a profile of 30 to 50 µm R a for an inert primer, typically a two pack epoxy, with thickness at least three times the
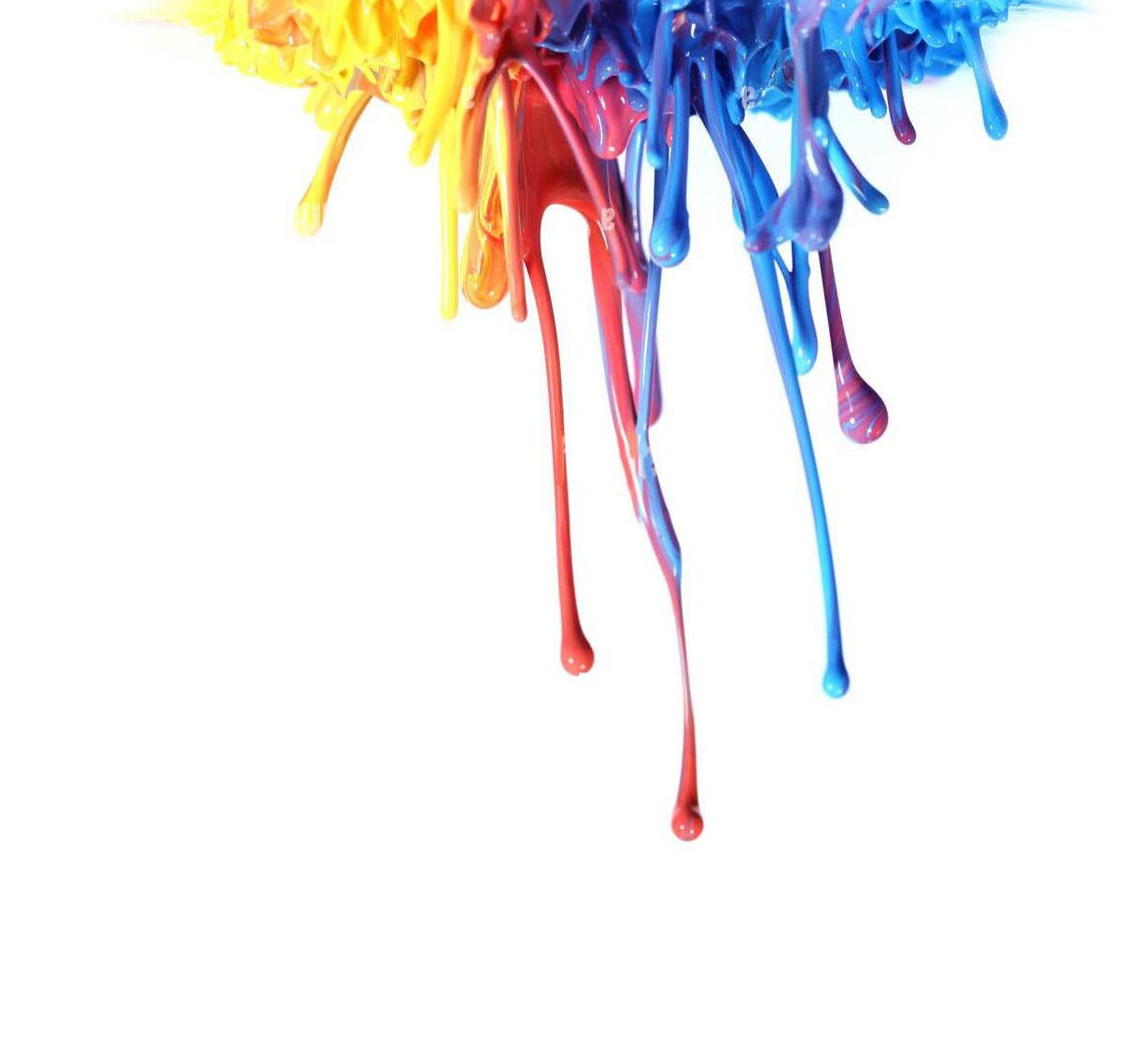
profile to ensure peak coverage and a similar thickness top coating of a UV-resistant formulation for exterior applications. The coatings must contain less than 50 ppm of available chloride. It is critical that the primer is inert, as zinc-based primer systems will galvanically react with the stainless steel and degrade the coating. Other inhibitors may add expense without enhancing corrosion resistance for the stainless steel. These stainless profiles are much greater than the 0.5 µm R a value for uncoated stainless steel because the surface profile for painting is about adhesion of an aesthetic/protective coating rather than avoiding corrosion of a bare stainless steel. With the right process, the successful application of paint on stainless steel will deliver both aesthetic appeal and enduring protection against corrosion, ensuring longevity and visual appeal of the structure.
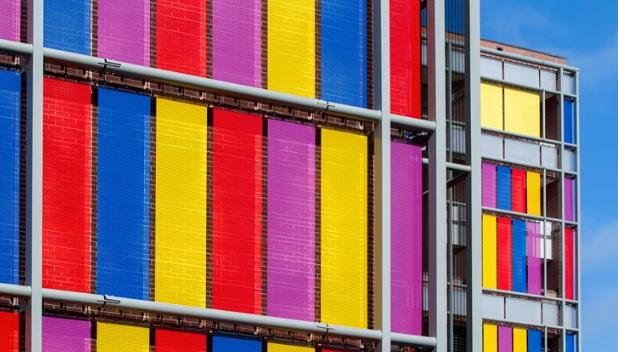
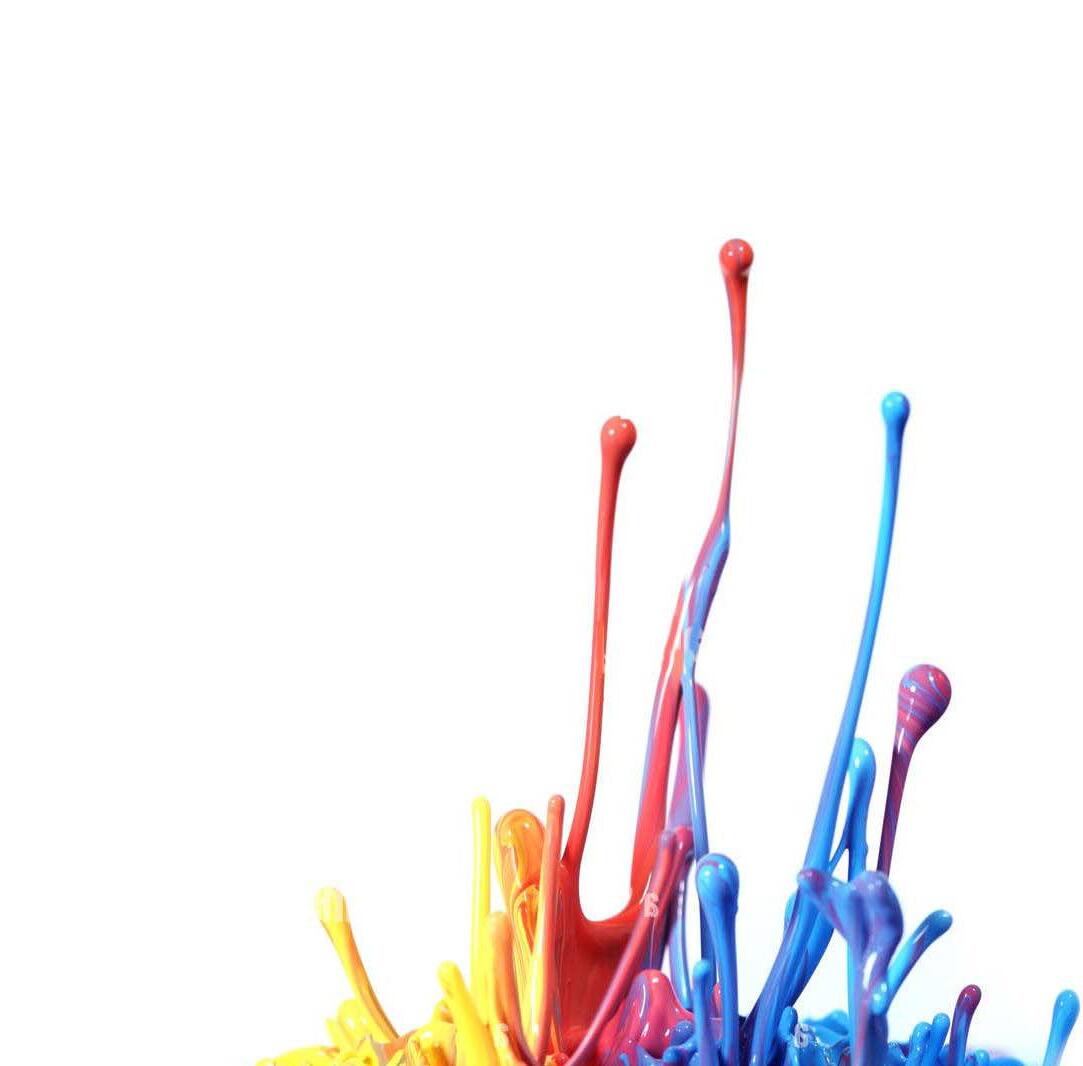
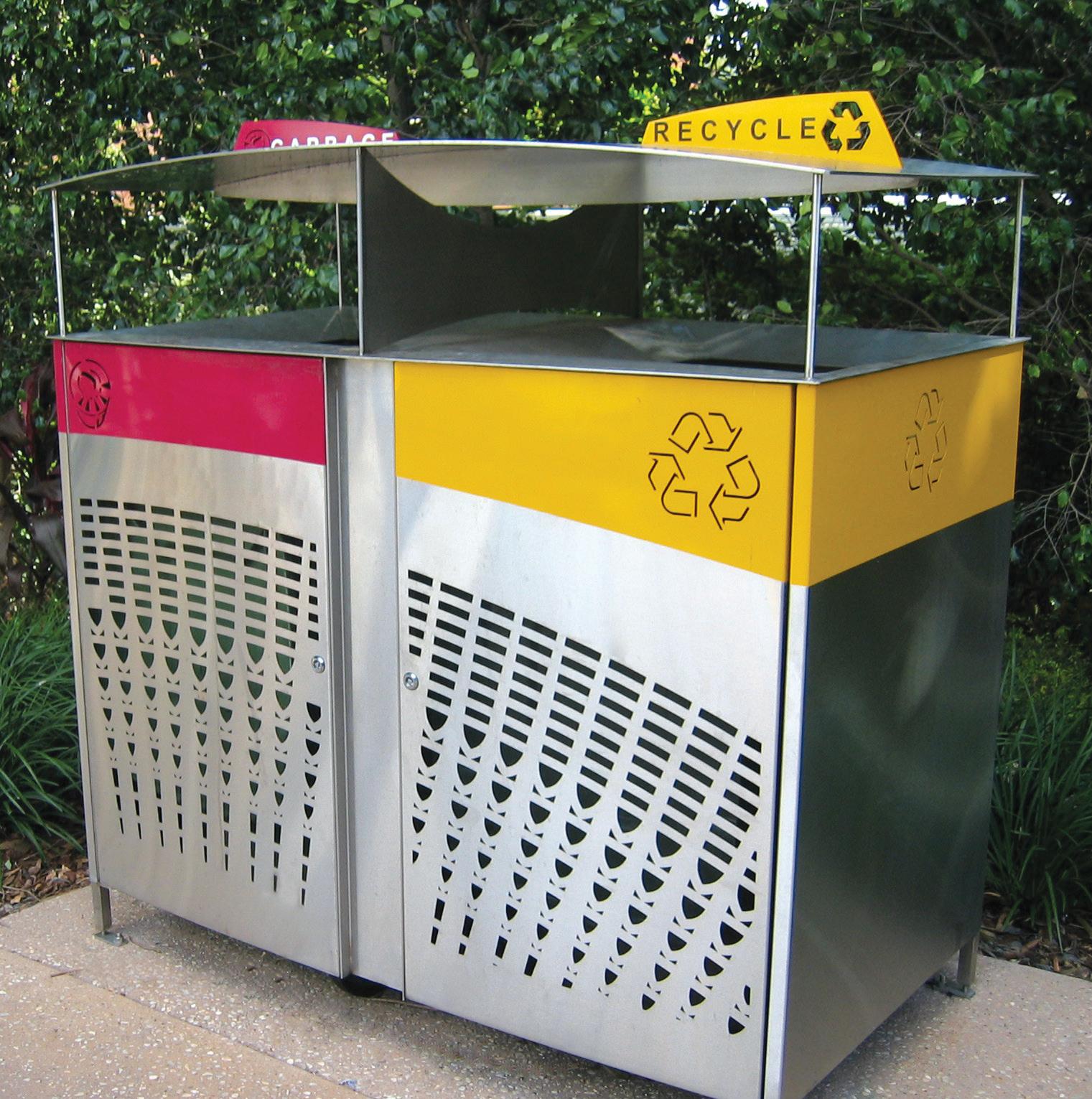
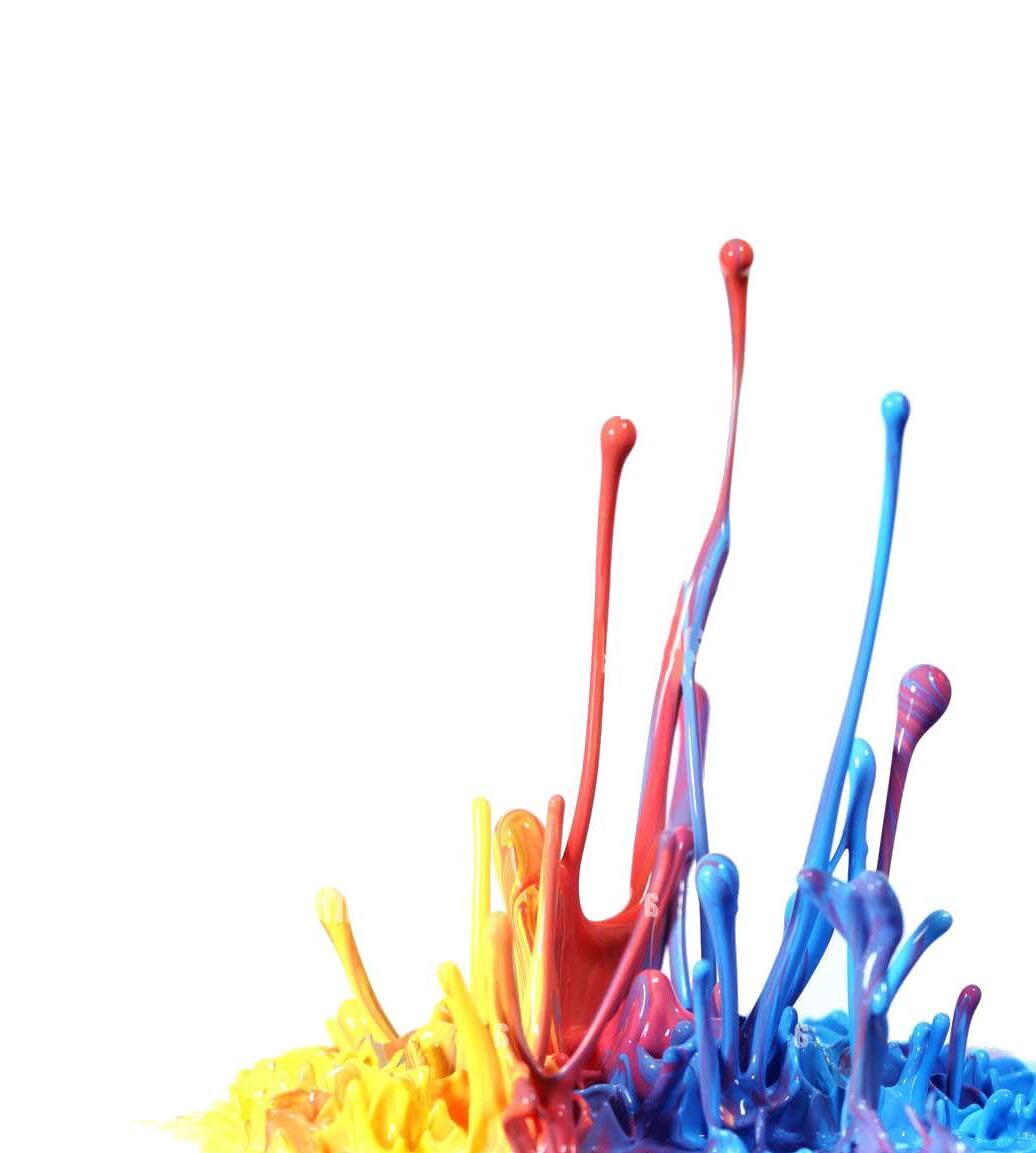

CROWN SYDNEY:
A showcase of stainless steel excellence
Located at One Barangaroo Avenue on the foreshore of Sydney Harbour and opened in 2022, Crown Sydney epitomises luxury with its opulent hotel, world-class casino, signature restaurants and top-shelf bars. At the heart of this luxury, stainless steel plays a crucial role, enhancing both the functionality and aesthetics of the resort.
ASSDA Member and Accredited Fabricator Stoddart was instrumental in delivering a bespoke solution for 136 different food and beverage areas for Crown Sydney. They fabricated, supplied, and installed an extensive range of stainless steel commercial kitchen and food equipment. This included Halton ventilation exhaust hoods manufactured under license at their Karawatha workshop in Brisbane, along with Stoddart’s own range of custom-manufactured commercial kitchen equipment. Additionally, wash basins, work benches, counters, shelves, wall sheeting, and spine walls were fabricated and supplied to the resort.
Stainless steel is a versatile and attractive material offering corrosion and heat resistant properties. Its non-porous surface ensures it remains less reactive and does not affect the taste of food, making it the material of choice for commercial kitchens. These properties are essential in the hospitality industry, where the busiest areas demand high standards of hygiene, cleanliness, and durability. Stainless steel not only meets these standards but also boasts a long
service life of over 20 years for food service equipment.
The project utilised over 107 tonnes of grade 304 stainless steel, comprising 4,993 linear metres of tube, 7,376 square metres of coil, and 859 flat sheets ranging from 1-2mm in thickness. All stainless steel used on the project (coil, tube, and flat sheet) was supplied by ASSDA Members Dalsteel Metals and Midway Metals.
TIG welding techniques were employed across the various goods and services provided, ensuring the strict requirements of food equipment manufacture were met. Important considerations such as correct surface finish, avoiding cross-contamination of materials, and maintaining hygiene and cleanability were all meticulously managed and addressed.
Stoddart’s expertise in stainless steel design and fabrication was critical in meeting the high standards expected in a luxury resort, dedicating over 26,000 hours of manufacturing to the project. Creating the bespoke and customised equipment and cabinetry demanded
extensive effort from Stoddart’s R&D and design team, showcasing their exceptional dedication and innovation. The integration of mirror finish stainless steel into individual units contributed to the resort’s deluxe, luxurious feel. The design and installation process presented significant challenges, requiring precise measures and delicate methods. However, the successful completion of the food and beverage areas showcases the seamless integration of stainless steel, quality, and luxury at Crown Sydney.
This achievement underscores stainless steel’s crucial role in creating spaces that not only meet functional needs but also elevate the overall aesthetic of high-end hospitality environments.
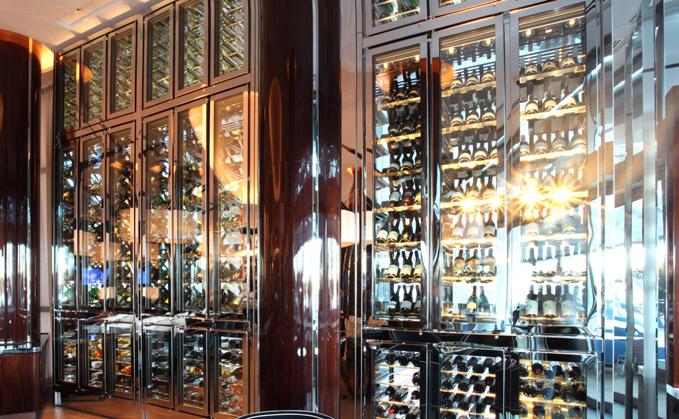
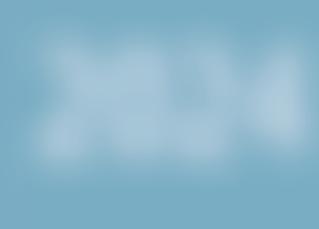
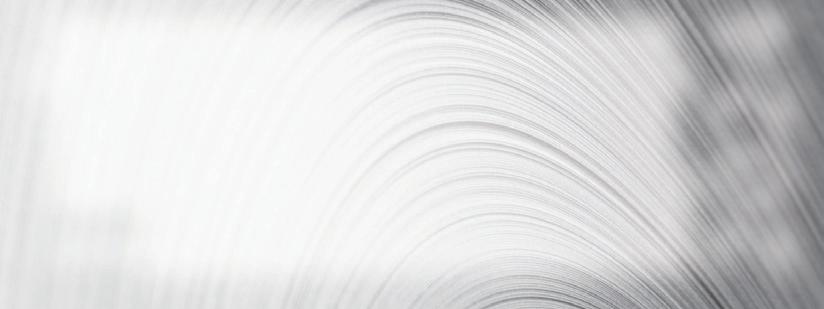

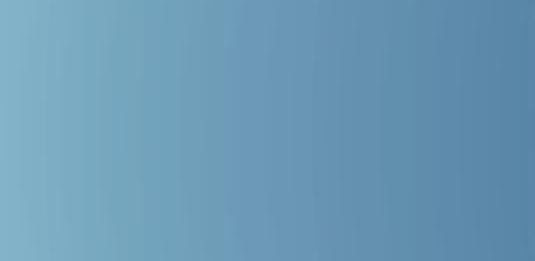

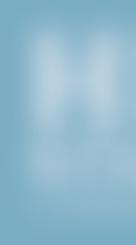



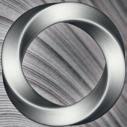
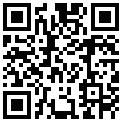
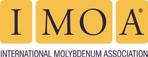

MEMBERS:
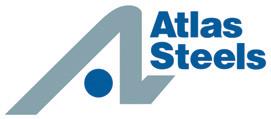
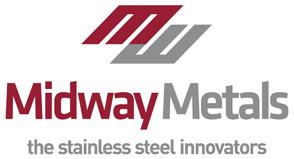

GOLD MEMBERS:
Daming International Import & Export Co., Ltd.
Prochem Pipeline Products
Stanch Stainless Steel Co., Ltd.
Stoddart
YC Inox Co., Ltd.
AUSTRALIAN STAINLESS MAGAZINE
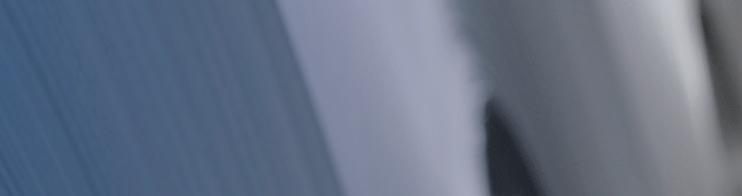
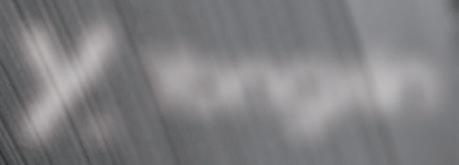
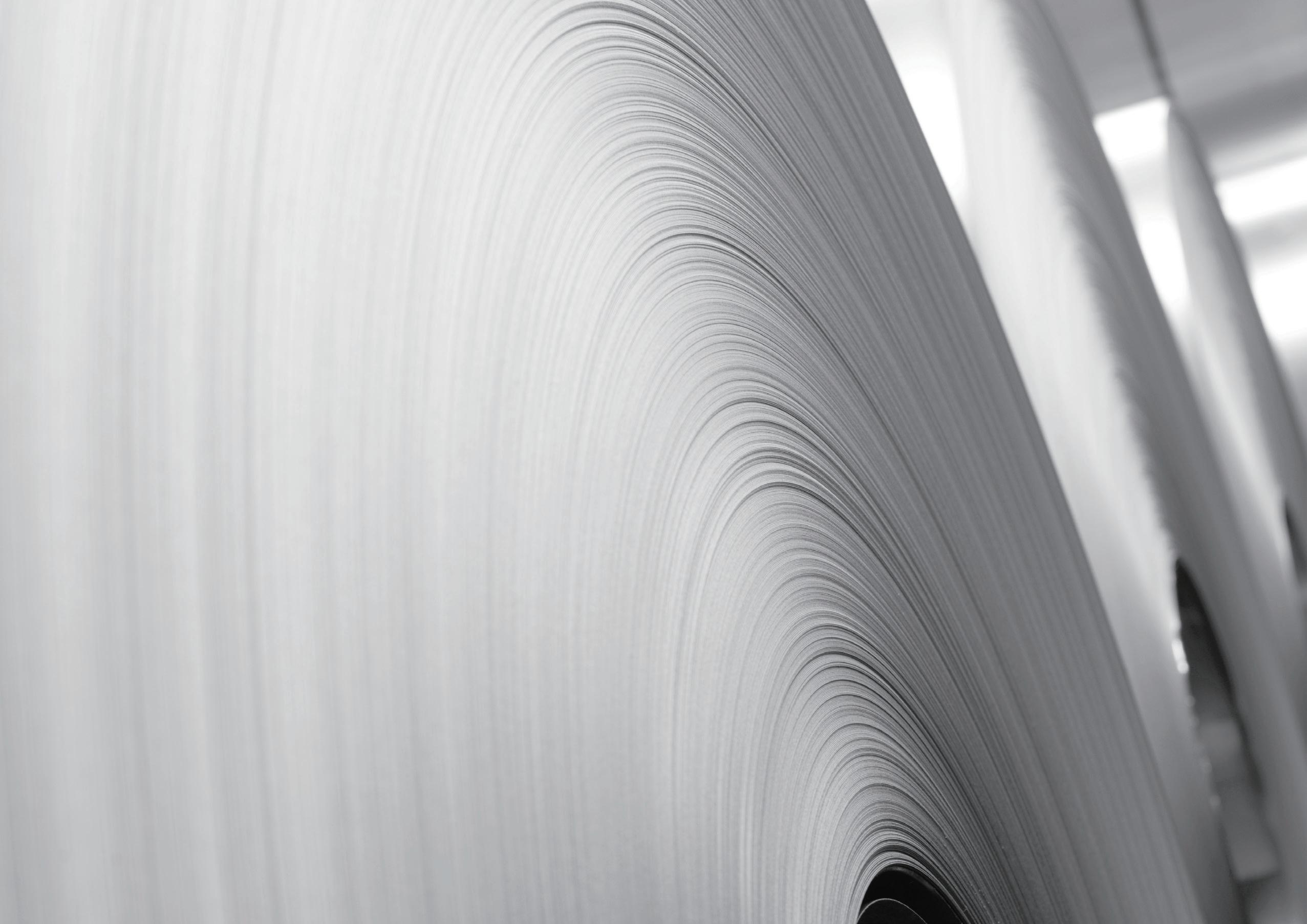
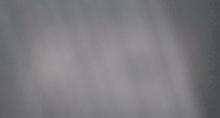
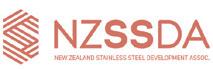
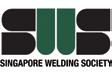
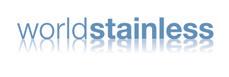

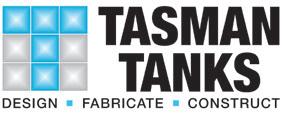
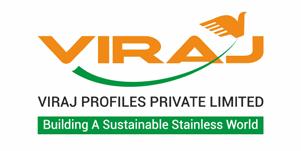
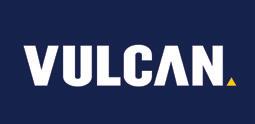
SILVER MEMBERS:
\ Aqseptence Group \ Arcus Wire Group \ AusPress Systems \ Austral Wright Metals \ Amity Pacific \ Australian
MORE INFO: Enquiries or further information on any material presented in this publication should be directed to ASSDA:
Level 6, 200 Adelaide St, Brisbane Qld 4000 \ +61 7 3220 0722 \ assda@assda.asn.au \ assda.asn.au
EDITORIAL: Contributions of story ideas specialising in stainless steel and its applications are welcome from Members of ASSDA.
ADVERTISING: Advertise in the only publication that reaches a targeted group of 5000+ in the Australian
industry. Rates available at www.assda.asn.au.
CONTACT: Lissel Pilcher, Editor: lissel@assda.asn.au