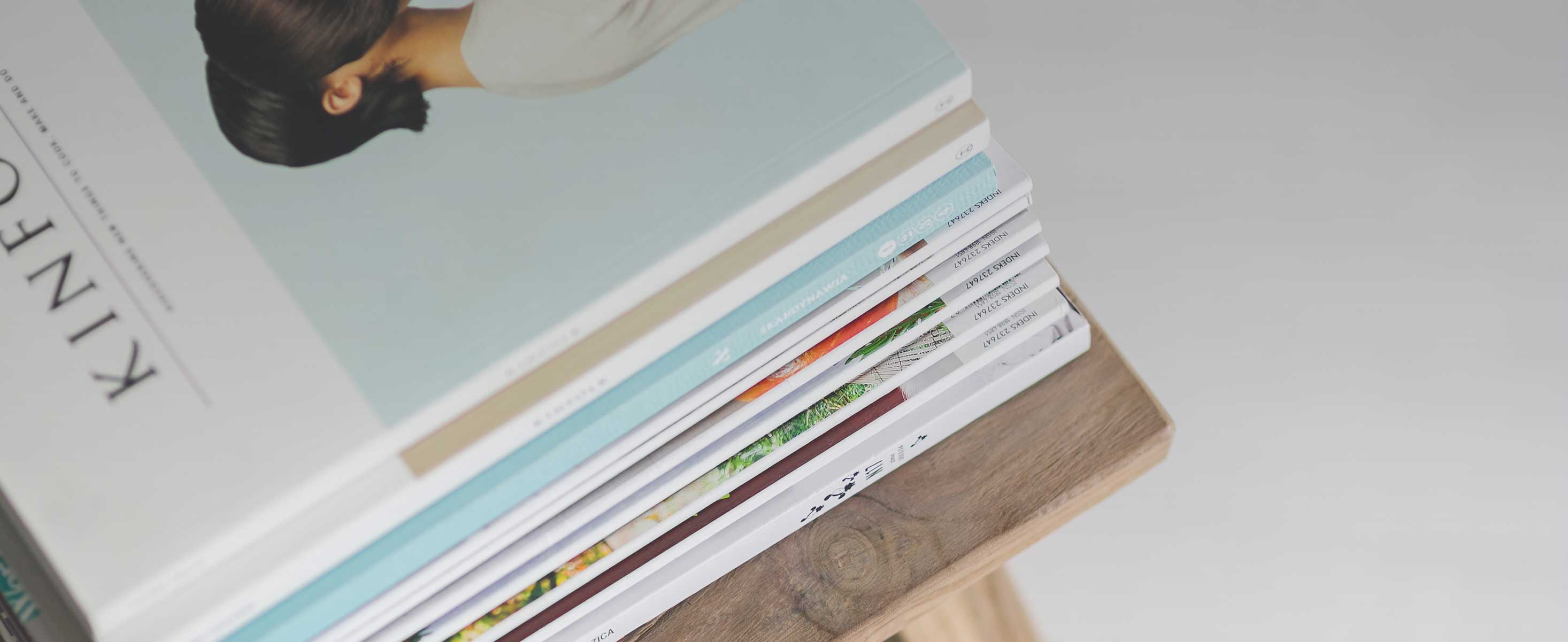
12 minute read
MODERN AND FULLY INTEGRATED ERP SOFTWARE SOLUTIONS ARE THE KEY TO SUCCESS IN THE FLAT GLASS PROCESSING INDUSTRY
In the increasingly competitive world of flat glass processing, industry players are not just grappling with the need to automate their machinery and robotics, but also the pressing challenge of outdated and disjointed administrative processes. With a significant portion of businesses still relying on bespoke software solutions or dated packages designed for the industry, they are left confronting issues such as inconsistent data across different databases and subpar system response times — issues that are further exacerbated for companies operating multiple branches nationwide.
This highlights the importance of moving towards a modern, fully integrated ERP (Enterprise Resource Planning) solution that unifies all essential functions within a single central database, from quotation management and production scheduling to invoicing. Such a shift can significantly mitigate these challenges, ensuring smoother operations, better efficiency, and a stronger competitive stance.
WHAT IS A SOFTWARE ERP SYSTEM?
An ERP software system is an IT-based system of software solutions helping management to keep track of existing resources and business processes. With the help of an ERP system, management can optimally design, influence and manage all processes effectively. ERP systems are integrated programs and modules based on central data management. Part of the claim of an ERP system is that it is integrative and maps the company, both in the cross-divisional basic functions and in the specialist departments or functional areas of a company.
ERP DATA INTEGRATION
The efficient storage of large amounts of data, its collection and analysis represent a serious challenge for ERP systems in larger companies and enterprises. Although an ERP system can consist of numerous software modules, it can only fulfill its task across all industries if the data is unique throughout the company and only available once. Information is derived from data and represents the most valuable asset in companies. That is why clean and valuable data is so important.
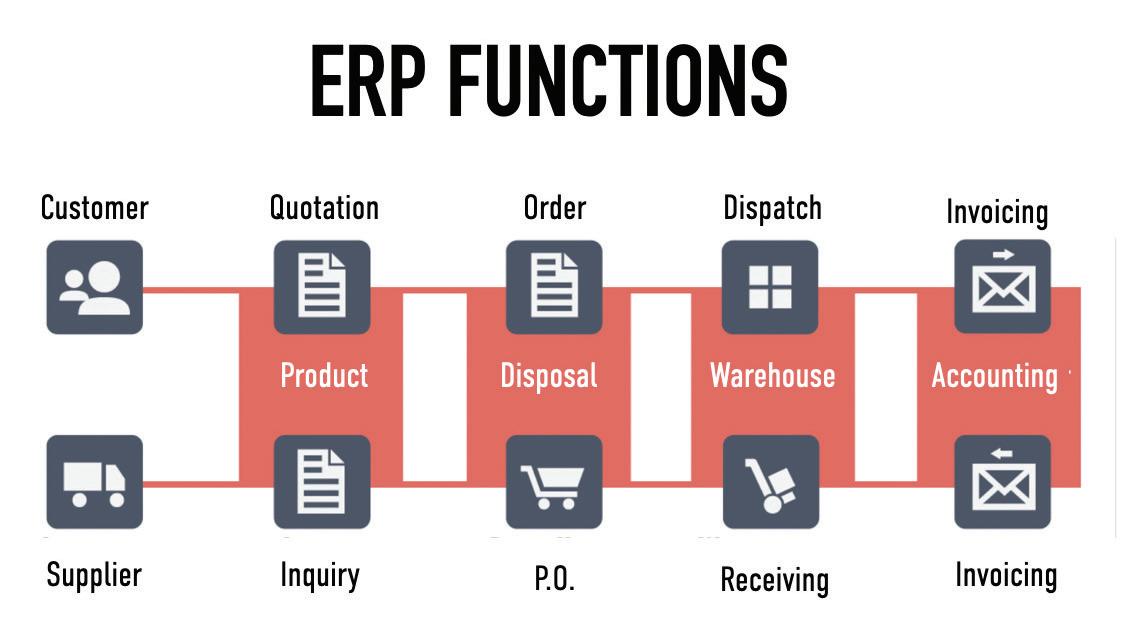
CENTRAL OR DECENTRALISED DATA MANAGEMENT?
The data management itself is one of the most important aspects of modern software ERP solutions. The key is to decide whether to use centralised or decentralised data management. Centralised data management has several advantages over the use of decentralised systems. One key advantage of using centralised data, for example, is the need for a single and central database system. This simplifies the maintenance of collected data, as all data is stored in a uniform structure. This can simplify searching for specific information in the database, as all data is located in the same place. In addition, centralised management will also reduce maintenance costs since there is only a single database system.
An additional advantage of centralised management is improved data security. In a centralised database, permissions can be set for each user so that only authorised individuals have access to specific data. This improved security feature makes it easier to build an overall secure network.
Another important benefit is the streamlining of data access. By using a central database system, users can access the same data even if they are located at different sites. This allows the company to ensure that information is managed quickly and efficiently. In the flat glass processing industry, this is even more important for larger companies and enterprises who operate different branches across the country, but only one server and database is accessed via modern and fast WAN connections. All branches can be created and managed in this central database with their own settings and variations. This includes branch-specific data, such as delivery route information, machinery and capacity variations and restrictions, etc.
The advantage of this concept is that certain database tables such as customer tables, credit limits or pricing data can be maintained centrally for all branches. This facilitates data maintenance a great deal in the case of price increases, for example and eliminates the duplication of customer data in the case of end customers dealing with various branches of the enterprise. A centralised database offers some significant advantages over decentralised management. By implementing a central database system, a company can store its data securely and manage it more efficiently, quickly and cost-effectively.
ERP AS A SERVICE WHAT IS CLOUD ERP?
The term ERP as a Service (analogous to SaaS — Software as a Service) emerged as early as the 2000s. It stands for a new generation of ERP systems — ERP in the Cloud . Soon, these systems will replace today's traditional solutions. The systems will then be Internet-based and platformindependent (Cloud). In addition, they are easily scalable. ERP as a Service is particularly suitable for small and mediumsized companies due to its scalability. Furthermore, adjustments and changes can be made even faster due to the webbased, functional and open architecture. The term ERP as a Service has now been replaced by ERP in the Cloud or Cloud ERP.
SOME OF THE ESSENTIAL SOFTWARE ERP FUNCTIONS IN THE GLASS PROCESSING INDUSTRY
Integrated Capacity Planning
One of the most important aspects in today’s challenging and competitive glass industry is the full integration of the different functions in one central system. A key function is a comprehensive, dynamic and flexible capacity planning tool, not only to balance machinery capacities, but also to ensure on-time deliveries and perfect customer service. Many existing software solutions in our industry do offer such tools but unfortunately, due to the system architecture using multiple databases, capacity planning usually resides on the production side of the system.
It is essential, however, that capacity planning is done right at the point of order entry, completely interactive and in real-time as order items are entered into the system. This ensures that eventual capacity bottlenecks or other technical problems (physical restrictions of existing machinery, for example) are detected right at the beginning and that an accurate delivery time can be confirmed to the final customer. Because of that reason, it is so important that the capacity planning function resides as an integral tool in order processing. In production, while machines are usually available around the clock, the employees can usually only work eight hours a day or a shift. To keep downtime to a minimum, set-up times, which are used for setting up machines or preparing production batches, for example, as well as times spent on maintenance, must be Fig.2 Detailed drawings for both customer and production using integrated CAD kept as short as possible. At the same time, maintenance work is necessary to ensure that the production flow runs without interruption as much as possible. If maintenance on machinery is necessary, it needs to be planned ahead of time, so that time slots can be reserved for these maintenance cycles meaning that production capacity is planned dynamically around these slots.
Why is capacity planning so important in the glass processing industry?
Inadequate capacity planning results in, among other things, an increase in the so-called idle capacity costs in a glass processing company, as excess capacity then becomes a cost factor. For example, staff members who are not needed at a certain point in time must still be paid. Idle costs can also arise from the downtime of machines and systems. In production, low machinery utilisation drives up unit costs due to the high proportion of fixed overheads. When capacity utilisation is high, on the other hand, the fixed costs are spread over a higher number of produced units, so that the proportion of idle costs is reduced. This approach can also be applied to other areas — for example, the service sector or larger projects: over-capacities are always cost-relevant. The same applies to under-capacities, which can bring the entire process of delivery to a standstill. However, many companies consciously accept over-capacities to maintain their flexibility for new orders. This can only be achieved in an optimal way with integrated and powerful capacity planning software.
Other important advantages of capacity planning are as follows:
• Planning deviations and bottlenecks are mitigated by resource planning at strategic, tactical and operational levels. In this way, companies ensure that sufficient resources are available for all activities (machinery time and staff).
• Continuous capacity planning secures the flexibility of glass processing companies better than the automatic provision of excess capacities. Resource requirements and resource supply — including a buffer for unforeseen events — are better coordinated.
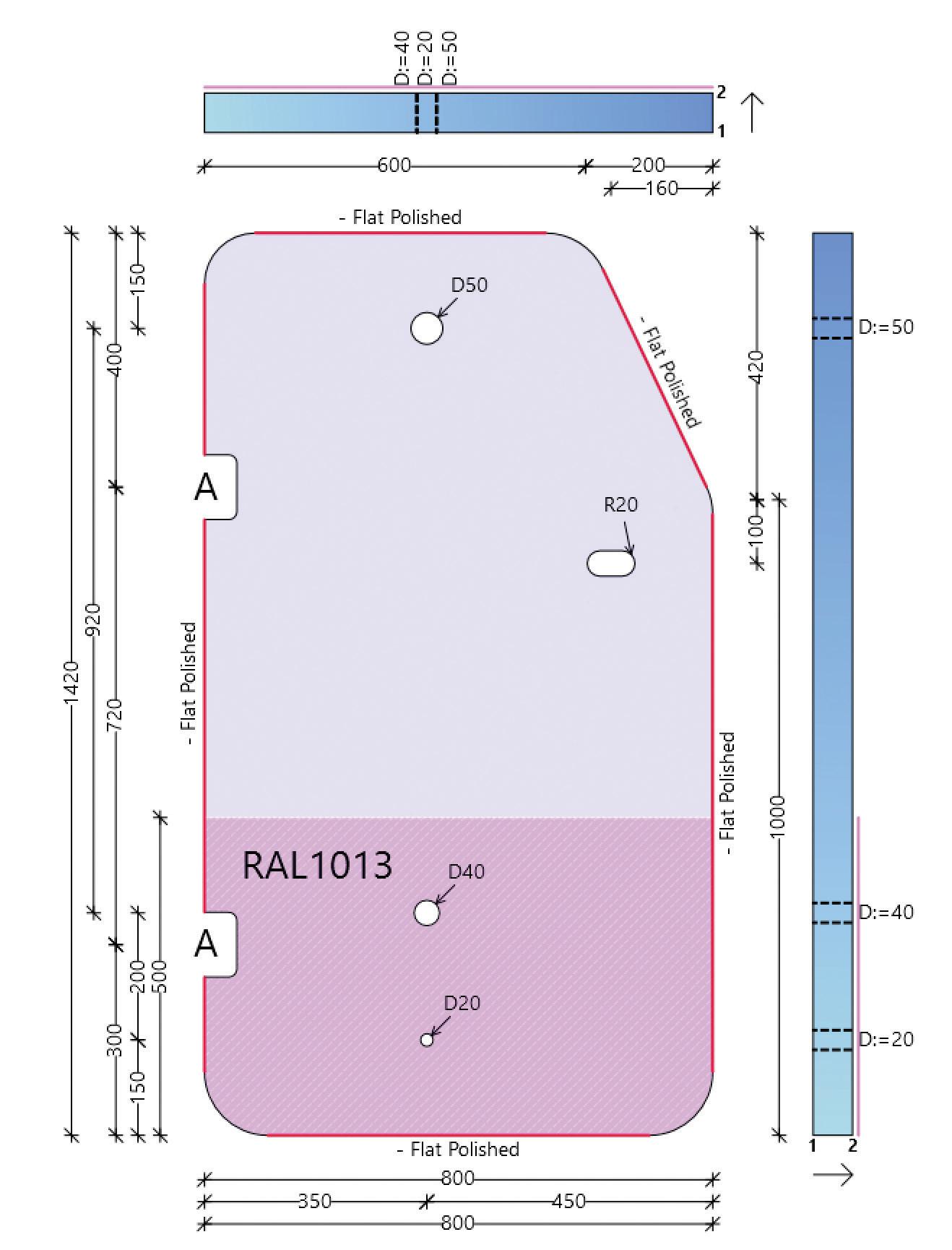
• The results of a functioning resource planning system also include a valid and constantly updated database. The data generated in this way makes an important contribution to forecasts, to the optimisation of processes, to the planning and implementation of new projects or as a basis for change management in the company or to adjust capacity parameters for the future.
• The workload of employees is more balanced. This effectively prevents excessive demands and underdemands on individual employees or groups of employees. Through their human resources capacity planning, companies create important prerequisites for a high level of commitment, motivation and employee satisfaction. In this dimension, too, capacity planning is an important productivity factor in the company.
Integrated CAD functions
The abbreviation CAD stands for ‘computer-aided design’. In concrete terms, working with CAD software means that individual steps in the design process are no longer carried out manually, but are taken over by the computer software. With the help of CAD software functions, all steps from concept development to handover to the production department can be completed directly on the computer and transported in an electronical data format, such as DXF.
In the flat glass processing industry, CAD is extremely important and needs to be an integral part within the complete ERP system. Many existing glass-specific software solutions on the market use standard CAD solutions, such as AUTOcad and try to interface those to their main systems. Most times these solutions do not offer the necessary integration and flexibility and drawings need to be done in a separate system. Furthermore, such standard CAD solutions are very complex and require extensive training, as they were developed for a wide range of applications.
Therefore, a completely integrated software ERP solution for the glass industry needs to have a completely integrated CAD, but tailored to the glass industry to efficiently create complexshaped units, including edge processing, drill holes, cut-outs, surface processing, such as screen printing, edge printing, special tempering stamps, etc. Such a system needs to be flexible and userfriendly, so that users can be trained in minimal time. As with the capacity planning function, the CAD function needs to reside right at the point of quoting and order entry, as the final customer requires a detailed drawing of the ordered unit with their quote or order confirmation document.
One of the other advantages of such an integrated CAD solution is that the system can automatically drive pricing of all processes through CAD entry — no separate entry of processing codes (drill hole categories, cut-out categories, processing articles, etc) is necessary to have the system calculate prices and costs based on processing edge lengths, etc.
Furthermore, using such an integrated solution will eliminate the so-called CADdepartment in a glass processing company, where staff members usually need to create drawings for all shapes, for each CNC machine separately, all day long as many manufacturers of CNC machinery supply their own CAD solution with their specific own format. Using an integrated tailor-made CAD solution as part of the ERP will create all necessary generic DXF files in the background, ready to be imported by all CNC processing equipment available on the market offering the DXF file standard. In that case, sometimes only tool setting is necessary for some of the CNC processing lines, depending on the brand and the technology offered.
Integrated Delivery Rack optimisation
Optimising racks for delivery, such as A-Racks, L-Racks or others becomes as important as optimising glass to ensure that delivery lorries are used to the fullest capacity, while ensuring that weight restrictions and unit sequences are respected. This function should also be part of a modern integrated state-of-the-art software ERP solution for the glass processing industry. On many occasions, final customers, such as window manufacturers require their glass units to be delivered in a certain sequence, streamlined with their own production of window units or sashes to eliminate unnecessary sorting with the risk of breakage or scratches. This process will offer the same advantages to the DGU producer as to the final customer because production, on both sides, will be completely streamlined and manual glass sorting (on both sides) can be eliminated.
The window manufacturer can schedule their own production and then can transmit the scheduling sequence as an order to their DGU supplier, even in electronical data format (EDI). The glass manufacturer on the other hand, using their integrated packing optimisation as part of their own software ERP solution, can schedule their glass unit production using the requested sequence of the final customer. This efficient method saves time and increases productivity, while eliminating sorting and eventual breakage or scratching, especially in the case of soft coated glass types.
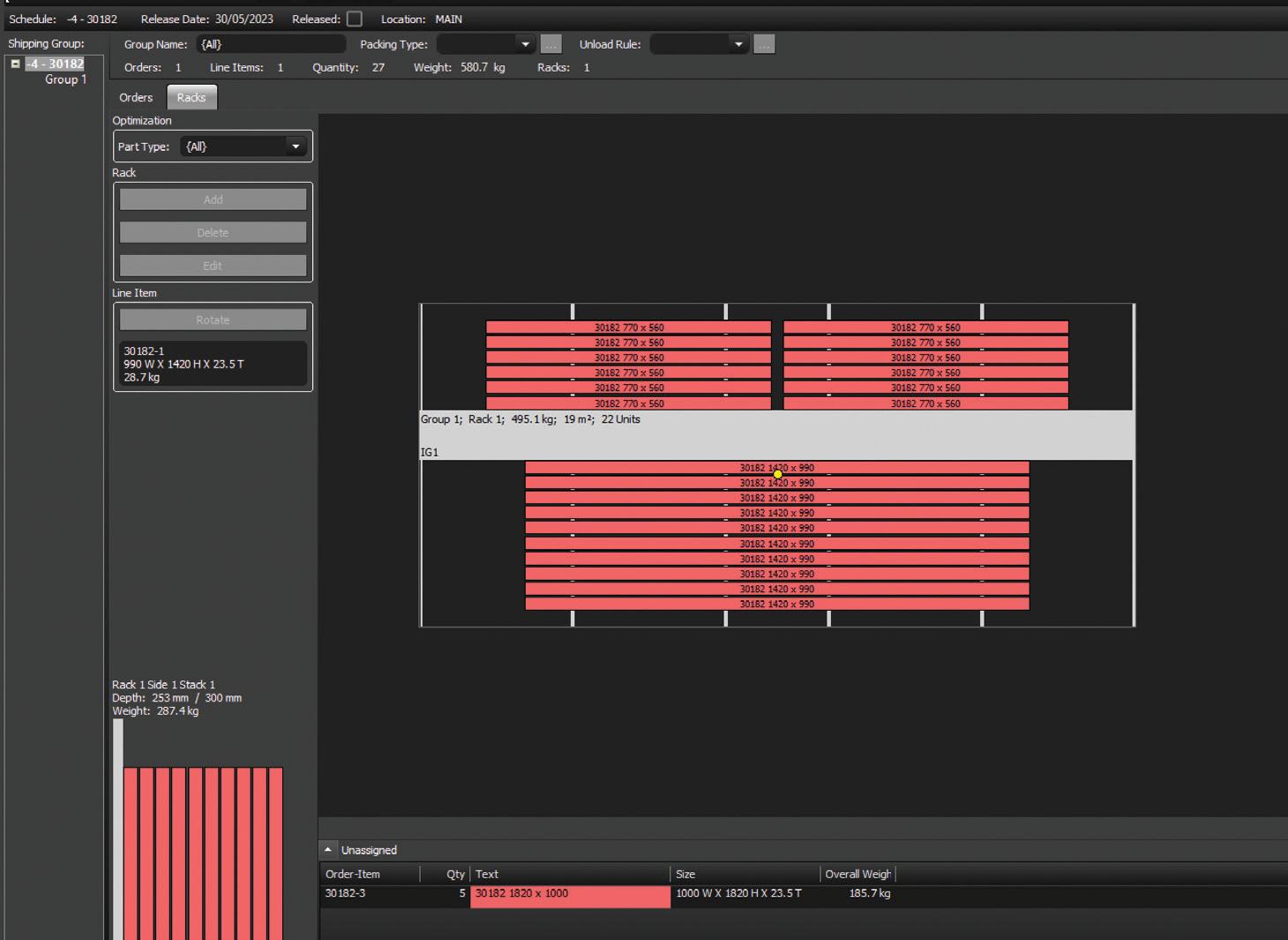
THE BOTTOM LINE
One of the key benefits of a completely integrated ERP system tailored to the glass processing industry is that it allows glass companies to streamline processes, eliminate redundant tasks or activities, and reduce the manual effort required to manage resources. There are different software solutions for glass processing on the market, some of them being supplied by machinery manufacturers. An efficient software ERP solution should be based on one single central database, for the reasons stated above and such a solution should be machinery-independent, yet able to control all glass specific production lines available on the market.
The doors for future machinery purchase decisions remain completely open for the company — a great advantage!
Horst Mertes, VP Sales of EMEA and Strategic Deals, FeneTech, part of the Cyncly group