SHOWCASE SHOWCASE SHOP AND PRODUC T SHOP AND PRODUC T
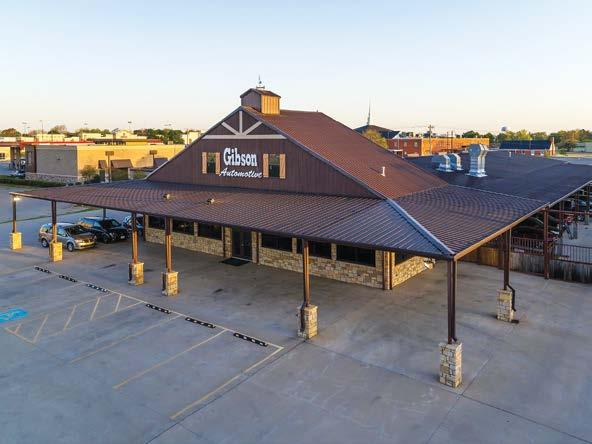
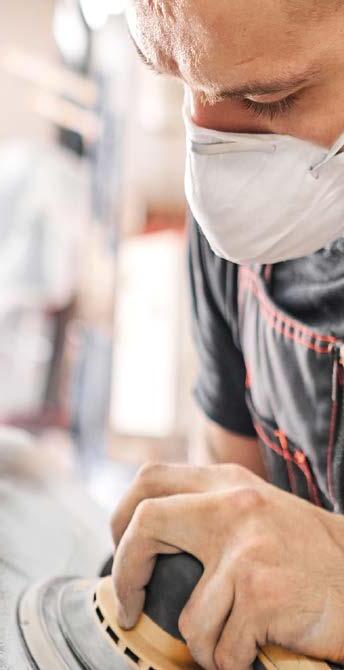
PPG 32-33
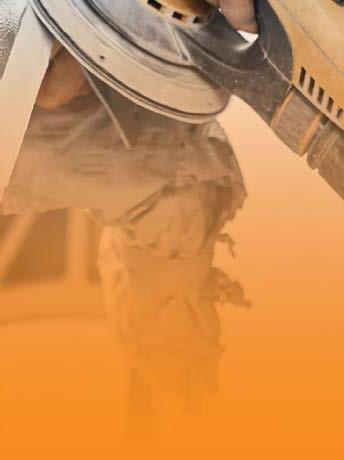
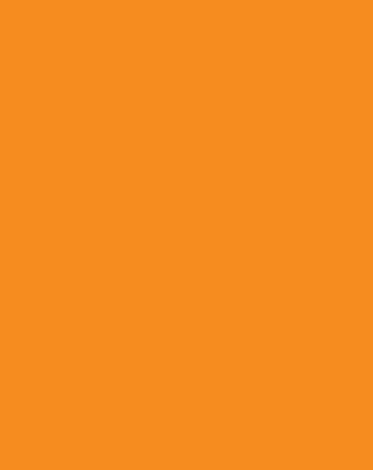
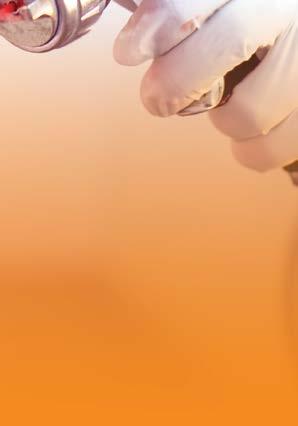
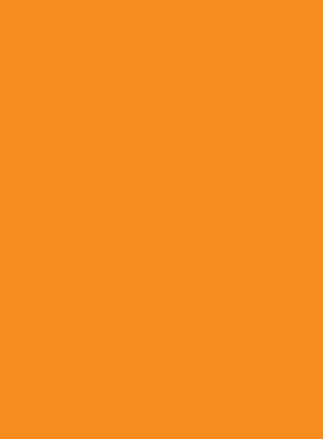

Spanesi 38-39

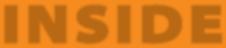
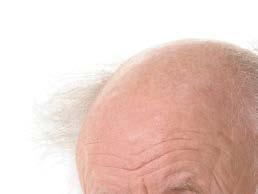



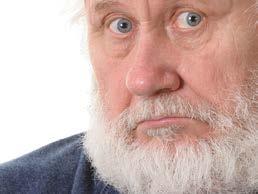
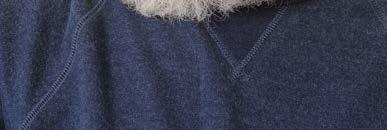
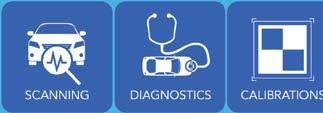
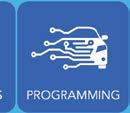
PPG 32-33
Spanesi 38-39
Since opening his first collision repair facility in Beaverton, OR, 49 years ago, Ron Reichen said Precision Body & Paint’s philosophy has remained the same: “Dedication to excellence means consistent quality, fair pricing and unsurpassed customer service.” In addition to the flagship store in Beaverton, Reichen operates four additional locations in the state: Bend, Gresham, North Hillsboro and South Hillsboro. This year, they are opening a standalone mechanical and calibration center in Beaverton.
The business prides itself on being a certified auto body repair facility. “We grew from our first Audi certification in the early 2000s to over 15 manufacturer certifications today,” said Reichen.
Precision’s facilities are the only ones in Oregon certified by Audi, Porsche and Maserati; new certifications include Rivian, Lucid Motors and the electric Hummer. Reichen said the business strives to stay up to date with the latest technology and innovation in the collision industry.
“Our commitment is to create an undetectable repair through training and having the right tooling and facilities to have a positive outcome for our clients,” he said.
Prior to entering the collision industry, Reichen spent about eight years in the aircraft construction industry focused on molecular structure and energy pathing.
As an entrepreneur with a passion for working with metals, Reichen began working as a collision repair and refinish technician.
In 1974, the day after he turned 21, Reichen and two business partners opened Precision Body & Paint in a 10,000-squarefoot rented facility with three employees. He eventually bought out his partners. Over the years, the business has grown to include five locations and currently has 70+ employees.
“I learned at a very young age that you never wasted a move,” recalled Reichen. “You were always efficient and consistent about what you did; hence, the company’s name is Precision.”
In addition to running Precision Paint & Body, Reichen has served as the chairman of the Society of Collision Repair Specialists (SCRS) and is involved in many facets of
the industry.
One of his priorities has been to create a learning culture for employees. “I have a philosophy that the most important person in our business is the employee,” he said. “You take care of the employee, the employee takes care of the customer, and the bottom line will follow.”
The company also focuses on the relentless pursuit of rebuilding the car, following all OEM procedures and creating an undetectable repair. Working with AirPro Diagnostics, which specializes in remote automotive scanning, diagnostics and ADAS calibrations, is an important part of this pursuit.
AirPro uses OEM software and comprehensive multi-brand diagnostic applications directly connected to the vehicle while remotely operated by brand specialist diagnosticians.
Reichen has known the AirPro Diagnostics team for many years, being part of Collision Industry Conference (CIC) committees and seeing each other at tradeshows and SkillsUSA competitions.
Precision began using AirPro’s services when it was established in 2016. Working with the company’s remote brand specialists for so many years, Reichen has found the team has always been ahead of the game.
“They are constantly in a research and development stage and they do a really good job of staying up with current trends,” he said. “When a new product line comes out, they’re prepared for it.”
He has also been impressed with AirPro’s training and support. As new EVs come on the market,
such as Rivian, Lucid and Polestar, Reichen said the AirPro team helps them navigate through the repair.
When Precision employees have a unique situation with a calibration or scan, they are matched with someone with that level of expertise. He said it makes a huge difference having a technician talking to a technician.
“The AirPro technicians are skilled in their product line and if they can’t solve it, they will find somebody within their organization and call us back so we’re never left without a resolution,” he said. “They are always a phone call away. They truly are specialists.”
For shops that feel they have the capability to service 45 brands on their own, Reichen said it’s not a reasonable expectation. With the price of OEM scan tools and targets, it can become very costly for a collision repair facility to invest in the equipment needed to repair vehicles.
By using AirPro’s services for scanning and calibrations, Reichen said they can rest assured that vehicles are being scanned with a factory scan tool and a certified repair was completed.
“We know when we finish the repair and give the vehicle back to the customer, we can be very comfortable that we’ve restored the safety features,” he said.
Since using AirPro, Reichen has always admired the products they produce and their commitment to ensuring the vehicle is repaired properly.
“What I appreciate is they have their hand on the throttle and that’s a testament to that fact that they know what repairers need,” he said.
Beaverton, OR 503-793-0656
precisionfirst.com
Company At A Glance...
Type: Collision Repair
Facility Employees: 70+
In Business Since: 1974
Number of Locations: Five Combined Production Space: 106,000 square feet
By using AirPro Diagnostics’ services for scanning and calibrations, Reichen said they can rest assured that vehicles are being scanned with a factory scan tool and a certified repair was completed.
When Precision employees have a unique situation with a calibration or scan, they are matched with someone at AirPro with that level of expertise.
AirPro Diagnostics
904-717-8693
airprodiagnostics.com
Facebook: @AirProDiag
Twitter: @AirProDiagnost1
Instagram: @airprodiag
LinkedIn: @airpro-diagnostics
YouTube: @airprodiagnostics1282
Much has changed in the years since Walt and Ruth Stinnett established Stinnett’s Auto Body Services in Maryville, TN, in 1965. While the family-owned business has built its reputation on top-notch workmanship and generations of satisfied customers, early repair techniques have given way to factory-approved procedures, technician training and investments in facilities, equipment and technology.
From the original 3,500-squarefoot shop with a handful of bays, the third-generation facility now spans 25,000 square feet, including a new 12,500-squarefoot addition that houses a stateof-the-art body shop, paint shop and paint booth. The company also boasts multiple OEM collision repair certifications, with ADAS calibrations performed on site.
The shop is now owned by Zach Stinnett, the founders’ grandson, who took the reins when his father, Lee, retired in 2016. Though he grew up in the shop, running the business wasn’t on Stinnett’s radar. He majored instead in pre-med at East Tennessee State University while working part time at the shop. He ultimately found his calling and earned a degree in business administration.
Determined, however, to broaden his knowledge and elevate the company to a higher level, he attended his first AkzoNobel Sikkens meeting with his dad. It was a revelation.
“I didn’t have much industry knowledge and I needed to learn the ropes,” said Stinnett. “The meeting was eye-opening. I formed relationships on that trip that I still have today.”
Stinnett is now a member of the Sikkens Acoat Selected Services Team and the North American Performance Groups (NAPG). Participation in the NAPG meetings is exclusive to Acoat members. The 20 Group-style meetings facilitate sharing best practices and strategies, as well as networking.
“The networking relationships are the biggest value,” said Stinnett. “It’s a bunch of shops talking shop. Everyone has similar issues and solutions you might not have
thought of. Every time I’ve attended a meeting, I’ve learned something new or made a change that benefits the business. We also use products like Carbeat® that we were introduced to at the meetings.”
Carbeat technology combines software, hardware and services to improve production efficiency. It features a touch-screen monitor, providing real-time workflow from the cloud and a production analysis dashboard. As a car goes through the production pipeline, the touchscreen displays a vehicle’s progression from one department to the next. Employees can track an individual car’s status and the shop’s workflow. It also helps identify trouble spots.
“For a volume shop, it helps with real-time production,” said Stinnett. “We get reports on the average time each department keeps each car, so we can nail down where it takes too long and try to improve. It’s a huge benefit. It’s also a real perk, because Carbeat is exclusive to AkzoNobel Sikkens customers.”
Given the complexity of today’s high-tech-equipped vehicles, Stinnett is also a stickler for adhering to OEM guidelines and standards. And he’s proud of the company’s reputation as a certified collision repair facility for more than a dozen automakers, including Honda, Acura, Subaru and Mopar brands.
“We are committed to ensuring the quality and safety of every repair and that repairs meet factory standards,” said Stinnett.
Along with skilled, factorytrained ADAS technicians, Stinnett recently established a separate company devoted to conducting
calibrations in-house. He’s also invested in tools and equipment that meet OEM requirements.
But Stinnett doesn’t rely solely on scan tools and other diagnostic equipment from one source. He’s cobbled together multiple resources. “I didn’t buy just one of the ADAS packages,” he said. “I’ve pieced it together by each individual OEM instead of investing in a one-size-fits-all package.
“The company has been open about a year,” he added. “It’s still a learning process. My goal is to open a storefront off site to attract collision work.”
He’s also pursuing other avenues to grow the business and anticipates the new building’s oversized paint booth will draw new customers. “There are a lot of tour companies and wedding venues in the area, so we’re going after the Sprint and Transit van market.” With Rivian slated to service a local Amazon distribution center, he’s also seeking Rivian certification.
An active community leader, Stinnett has drawn upon his AkzoNobel NAPG experiences to network locally, helping to establish the Tennessee Collision Repair Association and serve on its board. “I’ve gained so much from those NAPG conferences. It’s one of the reasons for our success,” he said.
“I enjoy the business. I enjoy entrepreneurship. We’re fortunate we’ve been established for many years. And we’re fortunate to have a great team and repeat customers whose families’ cars were repaired by my grandfather and my dad,” Stinnett said. “Not only are we a third-generation business, we’re working with third- and fourthgeneration customers.”
Stinnett’s Auto Body Services
Maryville, TN
865-982-7050
stinnettcollision.com
Company At A Glance...
Type: Collision Repair
Facility Employees: 16
In Business Since: 1965
Number of Locations: One
Production Space: 25,000 square feet
Attention to detail is a hallmark of the company’s commitment to meeting or exceeding OEM guidelines.
State-of-the-art equipment and expert color matching ensure vehicles are restored to precollision condition.
AkzoNobel Coatings
800-618-1010
www.SikkensVR.com/us-en
Facebook: @AkzoNobelNARefinish
Twitter: @AkzoNobel_AACNA
Instagram: @AkzoNobelRefinish
LinkedIn: @AkzoNobel
YouTube: @AkzoNobel Refinish
Optimized, Uniform Coarse Atomization For Standard/Waterborne Base Coats
Fast, Coarse, Center Wet Atomization For Wet-On-Wet Waterborne Technologies
Where Passion, Innovation, and Creativity Meet.
Fast, High-Delivery Fine Atomization For Clear Coats
Before the owners of Freeman Motors, a certified Toyota and Lexus dealership in Santa Rosa, CA, broke ground on a soon-to-bebuilt auto body shop, they toured the country to check out other top-notch shops. The resulting facility—a 43,000-square-foot body shop—opened its doors in 2001.
Freeman Collision Center currently holds structural repair certifications from Toyota and Lexus and was professionally recognized as the 2022 Lexus Shop of the Year. According to Shop Manager Jesse Parks, the company is the only dealerowned, Lexus-certified collision center between Bakersfield and the Oregon border, a distance spanning some 800 miles. It is also the only Toyota-dealership-owned collision center within a 300-mile radius. But these are not the shop’s only claims to fame.
“What sets us apart is the quality of work we perform. We only use OEM parts, we perform all calibrations in-house using OE software and scan tools, and we’re very rigorous in adhering to the OEM procedures,” said Parks, who joined the company in 2019.
“The owners built what is still considered a state-of-the-art facility. We have only the best of the best equipment,” Parks said— everything from Car-O-Liner frame racks and an overhead Eurovac dust removal system to lighted and heated down-draft paint prep stations as well as drive-through Blowtherm paint booths, to name a few.
As a high-volume shop that services an average of 100 to 120 vehicles monthly, and prides itself on superior-quality workmanship, it’s equally essential for technicians to have access to the latest and most advanced tools. Having worked with ANEST IWATA for many years, the company had an opportunity to test some new spray guns. Parks said the reaction was overwhelmingly positive.
“I’ve been using ANEST IWATA spray guns for almost 20 years,” said Joe Piehoff, painting production technician. “I currently spray base coat with a 1.3 LPH-
400 with an LVX orange cap (and) clear coat with a 1.3 LPH-400 with an LV cap.”
Piehoff noted he was able to demo the new WS 400 Series 2 digital line of base and clear guns. He was also able to test both the OBS and the OBS + 1 tips for the base gun.
“These guns are visually stunning,” said Piehoff. “The finish on the Series 2 far exceeded my expectations. And the removable digital gauge is icing on the cake. The base gun atomized and sprayed beautifully.
“Laying down soft and undetectable blends with the Series 2 base was easy. I could see the OBS +1 being beneficial when the summer months heat up and the humidity drops, although I had no problem spraying wet, beautiful base coat with the OBS tip even at 80 degrees booth temperature and 20% humidity.
“The WS 400 Series 2 digital clear gun was equally impressive,” he added. “Applying a clear coat finish that was very close to the factory appearance has never been easier. ANEST IWATA really hit a home run with the Series 2.”
While having the best equipment and tools are essential to running a top-tier body shop, technicians also need to be at the top of their game. To this end, Freeman focuses as much on technician training and certifications as it does on fostering a culture of merit.
“We provide extensive
technician training. All of our technicians are master certified,” said Parks, who holds four I-CAR platinum certifications and is working on attaining a fifth. Parks is ASE certified and also holds many factory OEM certifications.
The shop itself has achieved I-CAR Gold status as well as the ASE Blue Seal of Excellence designation, both the result of continuous training and a determination to enhance key performance indicators (KPIs) that measure operational and procedural performance.
But what ties these efforts together is the company’s unwavering commitment to a positive workplace environment, one that encourages employees’ personal and professional development through a meritbased culture that motivates team members to keep improving.
“I was brought into this organization to take the culture and the team to the next level,” said Parks. “I encourage everyone to lead by example—we are all role models—whatever it takes to support the team. In a culture of merit, anyone can excel based on their own merit.
“It’s been a wonderful experience. I go out of my way to identify ways we can set ourselves apart from the competition and provide a unique work experience. We have a great team and great processes and we continue to build a culture of merit every day.”
Freeman Collision Center
Santa Rosa, CA 707-542-2349
freemancollisioncenter.net
Company At A Glance...
Type: Collision Repair
Facility Employees: 33
In Business Since: 2001
Number of Locations: One
Production Space: 43,000 square feet
ANEST IWATA
800-470-7068
www.anestiwata.com
Facebook: @AnestIwataUSA
Twitter: @anestiwatausa
Instagram: @anest_iwata
asTech®, Driven by Repairify™, simplifies your repair workflow by providing access to OEM and OEM-compatible diagnostic tools, ADAS insights and calibrations, and programming capabilities all from a single device.
REDUCE CYCLE TIME AND KEEP MORE SERVICES IN-HOUSE WITH ASTECH
From blueprint to post-repair scan, asTech is your partner. We provide the tools, diagnostic data, expertise, and insights required for a quality, fast, and safe repair.
DIAGNOSTICS
INDEMNIFICATION
CALIBRATIONS
INTEGRATION
The most accurate and cost-effective scan for every vehicle
Verified scans backed by warranty for liability protection
Tools and guidance to perform dynamic and static ADAS Calibrations
Seamless estimating platform integration and reporting
Lexus of North Miami started as solely a dealership. That changed in 2009, when it followed in the footsteps of Lexus of Pembroke Pines, which had added a collision center 20 years prior in 1999.
“We converted half of the service department at Lexus of North Miami into a body shop with outside paint booths,” said Brian Martin, director of auto collision at Lexus of North Miami Collision Center and Lexus of Pembroke Pines Collision Center. “Then Lexus of Pembroke Pines Collision Center won Lexus Collision Shop of the Year in 2012, and Lexus of North Miami Collision Center won Lexus Collision Shop of the Year in 2018.”
Martin, who has held his position for 17 years, said he feels the shops earned these accolades by “focusing on fixing the car right from the beginning.”
“We work for the customers— there’s no greater focus we have than providing excellent customer service,” he said. “And in light of all the challenges we face from the insurance industry to using aftermarket and salvage parts, paint reduction and more, we stay steadfast on working for the customer, in hopes that they buy their second vehicle from us regardless of where they bought their first one.”
On top of a Lexus certification, both locations have collision repair partnerships with Nissan, Infiniti, Honda, Acura, Hyundai, Kia and Fiat, as well as I-CAR Gold Class titles.
Martin said since Lexus of North Miami Collision Center and Lexus of Pembroke Pines Collision Center use OEM parts, they implement equipment and products that meet factory standards. So, when it came time to find a company to provide diagnostic data for the scanning and calibration processes, the same rule applied.
“In the last few years, calibrations have been a huge point in the repair process and returning cars to their pre-loss condition,” Martin said. “And since we are part of the Collision Advice Legacy Group with Mike Anderson, we had been attending those meetings, and it was very evident
how important calibrations were for a quality repair.”
Martin explained with the sheer volume of cars at each location—more than 300 repair orders a month—“it became a challenge for the facilities to promptly complete all calibrations and pre- and post-scans.
“An essential part of why we chose asTech is because their certified technicians run OEM equipment for all calibrations and pre- and post-scans,” he explained. “These calibrations are not being done with any aftermarket equipment.”
Lexus of North Miami Collision Center and Lexus of Pembroke Pines Collision Center house John Bean machines from asTech. Martin said the asTech devices hook up to cars in each shop so in-house technicians can communicate with asTech technicians in Texas.
“One of the main benefits of using asTech is having the pre- and post-scans printed,” he said. “This allows us to understand the vehicle damages when they arrive at our facility and also helps us determine what is related and not related to the accident.”
Martin explained why having this printout gives them peace of mind.
“We receive a printout and a copy that state how all the calibrations were completed,” he said. “That way, if we have a return and somebody tries to say, ‘Well, you guys didn’t fix something correctly,’ we have a date and timestamped report showing exactly when and what we did.”
Martin said the printouts are also very important to their insurance partners.
“Our insurance partners prefer to have those reports when the cars come in because it helps them also determine if the damage at hand is related to the loss,” he explained. “This is possible because the asTech reports give specific information to the code that may be on in the car.”
Martin said the average vehicle at Lexus of North Miami Collision Center and Lexus of Pembroke Pines Collision Center has between two and four calibrations, not including the pre- and post-scans.
“Using asTech for calibrations has allowed our facility to decrease cycle time by approximately two days while increasing the quality of the repair,” he said. “Plus, the asTech portal makes it possible for our associates to access all invoices and scan reports minutes after the scans finish.”
Martin said Lexus of North Miami Collision Center and Lexus of Pembroke Pines Collision Center consider asTech one of their essential business partners.
“At the end of the day, if a shop isn’t performing calibrations, they’re not returning the car to pre-loss condition,” he said. “If you’re not calibrating the blind spot monitor, how do you know where the radar is aimed? If there is a lane keep assist in the front, how do you know without calibrating that the lane keep radar is aimed toward the center of the road? So, when you’re not returning a car to pre-loss condition, it creates a lot of liability.”
Lexus of North Miami & Lexus of Pembroke Pines
North Miami & Pembroke Pines, FL 786-528-3926 & 954-443-2770
www.craigzinncollisioncenters.com
Company At A Glance...
Type: Collision Repair
Facility Employees: 110
In Business Since: 2009 (North Miami), 1999 (Pembroke Pines)
Number of Locations: Two Combined Production Space: 90,000 square feet
Lexus of Pembroke Pines Collision Center uses asTech for pre- and post-scans to uncover hidden vehicle damage.
asTech, Driven by Repairify 888-486-1166
astech.com
Facebook: @astechdrivenbyrepairify
Instagram: @asTech_official
LinkedIn: @astechdrivenbyrepairify
They say things move quicker in New York, and people expect their cars back faster as a result. A demanding customer base wants it today—and don’t think about skimping on the quality.
That’s why Knights Collision & Auto Care Center in Brooklyn, NY, uses the IA800 Intelligent ADAS Optical Positioning System on roughly 100 cars every month. The crew has been using it for more than a year and is still raving about its accuracy, reliability and ease-of-use. It helps them get their discerning customers’ cars back fast—and earn top notch reviews as a result.
President Sean Cusick assumed control of this 75-yearold shop in 2013 after working his way up the ladder. He designed the company’s state-of-the-art workflow, integrating production, accounting and HR methodologies to build the business to where it is today. Acquiring top equipment like his Autel IA800 has been another big part of the formula for success.
Hiring and retaining talent has also been instrumental in helping Knights Collision to shine in a very competitive market.
“I have people who have been here for 15-20 years and we don’t get them jumping to the competition,” Cusick said. “My partner, Chris Kalinowski, came here 25 years ago from Poland, and now he is a New York State licensed appraiser and I-CAR Platinum, for example. We create a family atmosphere and let them know they’re valued and it works well. We don’t have any vocational schools around here, so it’s not easy, but we actually have people all the time who want to come here. If I see someone who has potential, I will usually give them a shot, and we have hired a lot of people that way.”
One employee who Cusick gave a great opportunity is Josh LaTouche, an estimator who accepted the role of running the company’s ADAS department. He is the company’s go-to guy when it comes to the shop’s diagnostics, a position he is proud of.
“Josh was a tech and then he had to take off some time off
,when he got a knee operation and we discovered that he was very computer savvy,” Cusick said. “During that period, he became a certified state estimator and also began learning about automotive diagnostics.”
When customers come into Knights Collision, they can see LaTouche working on the Autel IA800 displayed in full view.
“Twelve years ago, we moved into this building that was previously a car dealership,” Cusick said. “We put the Autel machine right in the middle of what used to be the dealership’s showroom and the customers see it when they come in. It’s a beautiful piece of equipment and we want to show it off.”
LaTouche is already an expert at working on the Autel IA800 and learns more about it every day, he said.
“Our Autel rep is amazing and he is always available if I have any questions, but the whole system is very intuitive,” he said. “To get started a year ago, the rep came here for two days, and we covered everything during that time. Every once in a while, we have a tricky calibration and I will call him or he comes here. He’s very close [in New Jersey] and he is so knowledgeable, it’s great.”
The most common recalibrations LaTouche performs are on front radar and blind spots on newer vehicles. “I can safely say that Josh is a black belt when it comes to using this equipment and that’s why he is a valuable part of
the team here at Knights Collision,” Cusick said.
The Autel IA800 is well-known as the fastest and most precise calibration frame positioning without mechanical measurement. The Autel Intelligent ADAS Optical Positioning System features six high-resolution cameras to deliver three-dimensional adjustment for the most accurate frame centering and vehicle distance recognition.
Compatible with Autel’s existing Standard Calibration Frame, and designed for seamless integration, this system optically measures two-wheel clamp targets to significantly cut down setup time and increase placement precision. It features the most extensive camera, radar, lidar and night vision calibration coverage in the industry today.
“We can scan and calibrate any car we get here and that has been huge,” Cusick said. “The equipment is well-designed and sturdy and the codes are always updated with the newest OEM information, so we are never surprised by anything. When the car comes in, we are already planning the diagnostics, which makes the entire process seamless and timely.
“We get a lot of newer vehicles here all the time and we never have to job out any calibrations, so our Autel IA800 is making money for us. We can highly recommend this piece of equipment because we are stressing quality and safety with this machine. When the car leaves here, we have that piece of mind, and that is very important.”
Knights Collision & Auto Care Center
Brooklyn, NY
718-963-4447
knightscollision.com
Company At A Glance...
Type: Collision Repair
Facility Employees: 16
In Business Since: 1948
Number of Locations: One
Production Space: 30,000 square feet
Autel
855-288-3587
www.Autel.com
Facebook: @auteltools
Twitter: @AutelTools
Instagram: @auteltools
LinkedIn: @autel-us
YouTube: @AutelTools
Bamford’s Collision Service in Fredericton, NB, Canada, has stayed in business for more than four decades by living by the motto “Good enough is not good enough—it has to be right.”
Owner Jerry Bamford opened his shop in its first location in 1982, after training and working at other area shops for several years. Later, he seized an opportunity to relocate his business to a larger building, increasing the number of work stations from four to 15.
Since then, Bamford’s Collision Service has built its reputation as an independent shop producing high quality repairs that come with a lifetime guarantee, with a staff that believes in the mission, several of whom have worked for Bamford’s for more than 30 years.
“That’s a testament to how [Jerry Bamford] operates and how the business works,” said General Manager Chad Farrell, who has been with the company for a decade.
“We’re not connected to any banners,” Farrell said. “We’re proud to be independent, as we have more flexibility that way.”
In May 2020, the singlelocation, 6,000-square foot shop bought A Plus Auto Glass, an auto glass business to which it used to sublet work.
“It just went hand in hand with collision repair,” Farrell said of the reasoning. A Plus also sells accessories, like tonneau covers and vent visors, that can get damaged in a collision and need to be replaced. “It makes sense to have your own avenue to buy those,” Farrell added.
Farrell said he got into the collision repair industry in a “roundabout way.” An electronics engineering technician by trade, he started in the gaming industry, then worked in the security industry for nine years. A friend who happened to be the accountant for Bamford’s Collision Service thought Farrell would be a good fit at the company, and introduced him to Bamford.
Farrell had grown up “tinkering
around cars” since he was 8, with his uncle, a mechanic in a small town. “I always had a fascination with cars,” he said. “It became a perfect match.”
Farrell said he has been able to apply some of the things he learned about management in the gaming and security industries to collision repair. His electrical engineering background also gave him experience with things like sensors and modules, which came in handy as the technology on cars rapidly evolved.
“I can help train our techs and teach them some of that technology that I’ve learned in the past,” he said.
Axalta has been the paint vendor of choice for Bamford’s Collision Service since it opened, and in 2022, it switched to Axalta’s Spies Hecker® Permahyd® Hi-TEC.
Axalta describes it as “one of the more advanced waterborne technologies available,” with a unique base coat formulated to help meet VOC regulations— Canada requires shops to spray waterborne paint—and to help technicians achieve dramatic results in less time.
Farrell said Axalta representatives came to the shop and helped the company’s two painters—one with 30 years of experience, and the other having been licensed for only one—make a “seamless changeover” from the Axalta system they were using previously.
“We were up and running in a half day,” Farrell said.
Farrell said there were a few differences between the shop’s
previous system and the Spies Hecker Permahyd Hi-TEC that caused a slight learning curve, but less than a year later, he can say it was a great upgrade.
“We’re using less product, so it’s reducing costs,” he said. “Also, seeing some of the technology advancements—we can do weton-wet— we can save time as well. Reduced time and material mean savings for the company.”
The base coats are a little more costly than those of the previous system, but the shop’s painters are using less of it, saving money.
“Insurers don’t seem to be paying enough for materials to cover repairs,” Farrell said. “We weren’t making enough on materials, but we’re seeing that gap close for us.”
And while the quality of the Spies Hecker Permahyd Hi-TEC is important, even more so, Farrell said, is that of the customer service Bamford’s gets from Axalta.
“Axalta provides exceptional customer service; that’s key to us, we need to have those relationships with our suppliers,” Farrell said. “We need to be able to call when we have an issue and get it resolved quickly, and that’s what Axalta has done for us over the years. We have been approached by other suppliers, but we don’t give them the time of day because of that support that we get.
“Excellent service is something we value and strive to provide to our customers, and we expect it from our suppliers,” Farrell said. “And we absolutely get that from the Axalta team.”
Bamford’s Collision Service
Fredericton, NB, Canada
506-458-8448
bamfordscollision.com
Company At A Glance...
Type: Collision Repair
Facility Employees: 14
In Business Since: 1982
Number of Locations: One
Production Space: 6,000 square feet
Axalta Coating Systems
610-358-5353
www.axaltacs.com
Facebook: @AxaltaNArefinish
Twitter: @axalta
Instagram: @axaltarefinish
LinkedIn: @axalta
YouTube: @axalta
With three busy locations in Vernon Rockville, Columbia and East Windsor, CT, Olender’s Body Shop is an 84-year-old third-generation business. Part of their success is the fact that they’re not afraid to embrace the newest, state-of-theart equipment to repair vehicles back to their pre-accident condition. Their “extended height” Blowtherm paint booth is expanding their total capabilities by bringing them a whole slew of new business. Their painters love it, the support is outstanding and the finished product is consistently pristine.
Olender’s Body Shop has maintained their unsurpassed reputation for generations, now servicing grandchildren of their original clients. They perform both mechanical and collision repair and are an I-CAR Gold shop. With a large and growing customer base, the high-production shop is in demand, and their Blowtherm in seemingly continuous operation.
When Olender’s began repairing cars, the most popular vehicle on the market was the Packard or a Woody. But with today’s sophisticated cars, shops need cutting-edge tools like a great paint booth. People want a paint job that exceeds their expectations, and Blowtherm delivers.
That’s why they have Blowtherm’s newest extended height spray booth at their East Windsor location, complete with premium LED lighting, and Air Speed/Waterborne hi-solid flash-off system. In their other locations, they have enhanced heat recuperation Blowtherm drive-thru and Blowtherm backout spray booths, and a Blowtherm Mix Room.
For Shop Foreman Joe Scavotto, he would agree that his Blowtherm is a world-class piece of equipment. “The fact that it is much higher and larger, we are able to paint larger vehicles such as ambulances and stretch limos.”
We asked Mark Miller, VP/ National Sales Manager of Blowtherm USA, about the need for this size spray booth in the industry. He confirmed that “Commercial vehicles are growing in the form of cargo size vans, utility box trucks, e-commerce delivery vehicles (i.e. Amazon, special courier, etc.);
there’s larger SUVs and crossovers; extended dually pick-ups and trucks overall. The decision to install an extended height, width and length spray booth broadens our customers’ capabilities to service those vehicles, which ultimately increases their business.”
Scavotto continued, “The Blowtherm also provides us with a much cleaner surface, which is a must when using a paint spray booth. Our painters love it and they like to work cleaner. This is very good because it positively impacts our efficiency and improves our cycle time.”
Olender’s Body Shop originally purchased several standard automotive Blowtherm booths in 2014, but this larger booth is a whole different machine. “This new booth is considerably brighter with the LED hip and wall lights. When your painters can see better, the finished job will always come out considerably better across the board.”
Scavotto is impressed by the increased production of 30% thanks to Blowtherm’s air-speed/ waterborne flash-off system. He added, “The quicker flash time is a huge deal!” Blowtherm’s quick dry air speed is known to provide shorter flash-off times between coats, provide faster removal of volatile components before the recirculation process, with zero additional energy costs.
Olender’s gives major kudos to Blowtherm’s overall excellent customer service. “The support we get from our distributor (Mike Hites, Autoquip, Newmarket, NH) is also very efficient.”
When asked what he would say to someone in the market for a new spray booth, Scavotto got straight to the point: “It’s a
long-lasting piece of high-quality equipment,” he said. “By all means, buy this Blowtherm booth—you will definitely not be disappointed!”
Special Projects Manager
Dave Olender is a big fan of Blowtherm’s heat recuperator system. “I can’t even imagine my fuel bill without using Blowtherm’s heat recuperator system,” he said. “Considering we’re hitting record low temperatures this winter, with the Heat Recuperation system, we are witnessing rapid temperature rise to ‘called for temps’ in the spray and bake cycles, which helps lower our fuel consumption. Very impressive.
“We looked at several other booth manufacturers but like the construction of the Blowtherm Extra. We were really sold on the Heat Recuperation and Air Speed/ Waterborne, Hi-Solid Flash-Off systems. The air movement is so incredible, no extra fans or blowers are ever needed.
“We’re actually kicking out an additional four cars per day. Plus, Blowtherm’s technology is giving us a much cleaner finish. Blowtherm will remain our spray booth vendor of choice.”
The finished product is always spectacular when a car comes out of a Blowtherm booth. Here are a sample of customer reviews featured on autobodyreview.com: “Excellent job, car looks new!! Car looks great.” “Back sooner than expected.” “Excellent work and very timely. Beautiful.” “My car looked amazing. At first I didn’t recognize it. JOB WELL DONE!” “I am very completely satisfied with the outcome of my Lexus repair. I know that it was a difficult task in getting the correct paint color, but Olender’s team of professionals did the job... love it!!”
Vernon Rockville, Columbia & East Windsor, CT 860-654-1715
www.olenders.com
Type: Collision Repair
Facility Employees: 26 (East Windsor)
In Business Since: 1939
Number of Locations: Three
Production Space: 13,000 square feet
“Blowtherm gives us a much cleaner surface,” said Joe Scavotto, Shop Foreman, Enfield Region.
Premium LED lighting comes standard on all Blowtherm spray booths.
Blowtherm USA & Training Center
855-463-9872 or 262-269-6265
www.blowtherm-usa.com
sales@blowtherm-usa.com
O’Hare Auto Body prides itself on being a top-tier collision repair facility. In operation since 1985, the Bensenville, IL, facility services the Chicago metro area. Known for its top-notch customer service, technical expertise and adherence to OEM guidelines, the shop holds structural repair certifications from Tesla, Porsche, MercedesBenz, Honda, Acura, Ford, General Motors, Nissan, Infiniti, Kia, Hyundai, Fiat/Chrysler, Dodge, Jeep, VW and Nissan GTR.
With the arrival—and rapidly growing number—of high-tech vehicles equipped with advanced driver assistance systems (ADAS), many body shops have had to shift gears and upgrade their technical capabilities. To keep up with an increasing need to perform vehicle calibrations and ensure the shop would continue to meet current OE repair standards, O’Hare created a new position within the company.
Lee Serling joined the O’Hare team as the lead ADAS/ scan technician in 2019. “We are a high-volume shop. That’s why O’Hare decided to bring on a dedicated ADAS tech like me,” said Serling, who has a background in information technology (IT) and previously held an ADAS tech position at a friend’s body shop.
“A lot of shops have the estimator or a body tech perform the scans, but that’s not necessarily their expertise,” noted Serling. “To resolve some of the technical conundrums we find ourselves in during the repair process, you need to use your critical thinking skills, be dedicated to problemsolving and appreciate the sense of accomplishment that comes with getting the job done. That’s my favorite part.
“With the OE certifications, we have to be knowledgeable and keep up with the latest technologies, equipment, software and manufacturer procedures. Those are our strengths and what makes us unique.”
To drive the shop’s performance and streamline operations overall, O’Hare relies on CCC ONE®
software from CCC Intelligent Solutions. With CCC ONE, shops can improve workflow, convert estimates to repair orders, order parts electronically and standardize operations, among other services. The company also provides training on how to use its products as well as tech support.
“For a high-volume shop like O’Hare, it’s helpful because we need organizational standardization,” said Serling. “CCC ONE helps us with scheduling, estimates, cycle time and ordering parts.”
O’Hare implemented CCC® Diagnostics to manage scanning and calibration work.
“With CCC Diagnostics, we are able to set up certain criteria based on vehicle manufacturer or the type of payer—if it’s DRP or a different insurance company, for example,” added Serling. “The diagnostic tool also makes sure that we don’t miss anything on the estimate, such as a scan or calibration. If we do, it’s flagged, so we can make the adjustment. That helps us to catch any errors and stay in compliance.”
Serling said compliance with OE repair guidelines is always a critical consideration given the shop’s certification status. He noted some diagnostic work is performed in-house using OEspecific scan tools in accordance with factory guidelines. He said O’Hare also relies on third-party providers Opus IVS and asTech, which offer remote diagnostic solutions and services.
“asTech and Opus have all the software and the OE scan tools,” said Serling. “We are able to hook up remotely and talk with their technicians as they use their scan tool to retrieve the diagnostic trouble codes. It’s one of our main sources of knowledge. Having access to the technicians helps us identify what needs to be repaired and recalibrated. We also save on cycle time with a faster turnaround and we know the repair was done the right way.”
Doing repairs the right way is essentially O’Hare’s mantra. “We are 100% responsible for every repair,” said Serling. “As a certified repair shop, we want to protect the brands we represent. It’s on us to make sure that every car is safe and was repaired properly and restored to pre-accident condition.”
In reflecting on O’Hare’s accomplishments beyond the technical and operational aspects of the company, Serling said, “It’s our longevity. Tom Stiefbold, the owner, has been here almost 40 years. We have that sense of community that a newer shop can’t reproduce.”
He also noted Stiefbold plays an active role in advocating on behalf of the collision repair industry, serving on the board of the Alliance of Automotive Service Providers of Illinois (AASPI). “Being involved in legislative and regulatory issues demonstrates the high quality of our commitment to safe and proper repairs,” said Serling.
O’Hare Auto Body
Bensenville, IL 630-766-6668
ohareautobody.com
Company At A Glance...
Type: Collision Repair
Facility Employees: 30
In Business Since: 1985
Number of Locations: One
Production Space: 18,500 square feet
O’Hare performs blind spot calibrations, essential for adherence to OE guidelines.
877-208-6155
www.cccis.com
Facebook: @CCCIS
LinkedIn: @ccc-intelligent-solutions
When Star Body Works, a fourshop regional MSO in Southern Oregon that also has a suspension calibration shop and a towing business, decided to expand its repertoire to include auto glass services, General Manager Jake Jennings asked around for recommendations on the best way to do it.
“They all said, ‘Hands down, Equalizer,’” Jennings said.
Jennings and three other Star Body Works employees have since completed Equalizer’s oneweek, 40-hour course at its Auto Glass Academy in Round Rock, TX, taught by Global Education Director Gilbert Gutierrez. After hiring another employee who already had experience in auto glass, Star Body Works can now keep all its collision repair facilities’ glass work in house—saving money and cycle time.
Star Body Works repairs an average of 450 cars per month between its four I-CAR Gold Class locations in Medford and Grants Pass, OR. The shops hold numerous OEM certifications, including Tesla, Subaru, Honda, Acura, Nissan, GM, Ford, Volvo, Chrysler, Kia, Hyundai and Mazda, and is close to achieving Mercedes-Benz.
Jennings said the shops pull away all glass from any panels being painted, for a factory-like finish that doesn’t expose paint lines to UV rays. “That’s almost every car if we’re doing a quarter panel, lift gate or pillar,” Jennings said.
Before, Star Body Works sublet that work to a mobile glass company that visited all four shops nearly every day. Now, it has its own van, staffed by its employees, who can do all the glass work themselves.
Jennings said bringing glass work in-house has several advantages.
First, the shop can make a bit of a profit off glass work now. When it was subletting the work, insurance companies would not allow Star Body Works to charge them any more than Star paid the mobile glass tech. “If I keep that in house, now I pay a labor cost, but I can
make a profit off of it,” Jennings said.
Second, the shop has more control over scheduling repairs and replacements. “The glass industry is stretched so thin with how much work is out there,” Jennings said. “Two years ago, we could get (the sublet company) in same day (to do glass work.) Now, it’s two to three days minimum.”
Jennings said that is only going to get worse, as several glass companies are leaving the collision repair industry because insurance companies are putting pressure on how much shops are allowed to charge for the work. The 30-squaremile area of Oregon where his shops are located is down to only one such company.
Third, Star Body Works can ensure calibrations are correctly performed on its customers’ cars, which is becoming increasingly important in glass work.
“People who’ve been doing (auto glass) for 20 years don’t understand the importance of recalibrations, and it’s putting lives in danger,” Jennings said. “That’s the shadow lurking behind the windshield business.”
Jennings said he reached out to Shannon Kern, education program director at Equalizer, to find out what it would take to get trained. Soon after, he and another employee went to Texas for the one-week course. Jennings, who started in the collision repair industry with a high school internship more than 20 years ago, said the course “was a lot more
than people anticipate,” but he saw students who started with no knowledge of the industry build their skills as quickly as people who already had years under their belts.
Over the five days, the students learned about laws related to glass repair and replacement and were taught—both in the classroom and in a hands-on shop—how to correctly prepare a vehicle, including pre-scanning ADAS features, and perform the work. The course was capped off by a final written test and a handson replacement observed by instructors.
When the students passed the final, they were certified by Equalizer and eligible to take the national certification test, which Jennings also passed.
Equalizer also gives students a tuition credit to purchase tools, which Jennings took full advantage of. He said Star Body Works uses the Viper and Raptor cord and wire glass removal tools, as well as Equalizer’s glass stands, knives and chip and crack repair tool.
“I like the tools and the way they work,” Jennings said. “You know they’re going to have the tool that works the best. All their tools work together.”
Jennings said he has only had to send back one tool to be repaired, which Equalizer did, under warranty, and returned in two days.
“We get really good support,” Jennings said. “I’m constantly ordering stuff from them. They know me and answer with ‘Hey Jake.’”
Star Body Works
Medford and Grants Pass, OR 541-779-5621
starbodyworks.com
Company At A Glance...
Type: Collision Repair, Glass Replacement
Facility Employees: 65
In Business Since: 1948
Number of Locations: Four Combined Production Space: 65,000 square feet
Equalizer® Industries, Inc. 512-388-7715
www.Equalizer.com
www.autoglassacademy.com
Facebook: @equalizertools
Twitter: @equalizertools
Instagram: @equalizertools
YouTube: @equalizervideo
Gibson Automotive in Greenville, TX, has undergone several transformations since its doors opened in 1969.
“We originally opened as Joe Gibson Ford, then transitioned to Oldsmobile Cadillac,” explained Brent Ash, the estimator at Gibson Automotive. “In 2016, we changed operations to focus primarily on collision repair.”
The family owned and operated business holds an I-CAR Gold Class title and stands out by providing customers with a “miraculous quality of work,” said Ash.
FindPigtails.com, a long-time vendor partner, has helped Gibson Automotive offer dependable repairs and efficient turnaround times to its tight-knit community.
“With all the expanding electronics and how hard harnesses are to get, there are certain things you just need a pigtail for,” Ash explained. “So, FindPigtails.com has fulfilled a huge need for us.”
Ash said typically, Gibson Automotive contacts the vendor for fog light pigtails.
“There are connectors— pigtails—throughout the car—front end, rear end, headlights, tail lamps and radar connectors for cruise control systems. So any time one of these areas gets damaged, hopefully, the shop catches it ahead of time, which Gibson Automotive always does,” said Ruston Blanchard, general manager for FindPigtails.com. “Some shops don’t catch that they need a connector until the very end when they’re about to ship out the car. This happens because they’re not used to looking for a connector, which is basically a needle in a haystack.”
Blanchard, who initially worked in vehicle diagnostics, said deciphering whether the car needs a pigtail is an acquired skill.
“You’ve got this huge impact with all this other damage, so a little plug on the end of two wires can easily get missed,” Blanchard explained. “So, as the shops work with us, we help them identify what they need, or if what they think they need, is correct.”
He said body shops eventually get to the level Gibson Automotive is at and will know they need a pigtail sooner than later.
“At that point, the shop sends us a picture through our website chat, text line, email or the FingPigtails.com app,” Blanchard said. “I then send back a price, they tell me to ship it, and we’re done. It makes everybody’s life super easy.”
Ash said he uses the convenient text line FindPigtails.com offers.
“I can’t remember the last time FindPigtails.com didn’t have something we needed,” Ash said. “They treat us right, and they take care of us. Ruston is my main salesman over there, and he’s awesome.”
On the rare occasion FindPigtails.com doesn’t have a compatible connector in-house, Blanchard said he will hunt one down for the client.
“If all we can find is a used part, we’ll get it and, of course, let the client know it is used,” Blanchard explained. “To keep up with competitors and meet niche demands, we started carrying a small percentage of aftermarket parts.”
Ash said the vendor’s reliability has been key.
“They have helped us speed up repairs, which aids cycle time,” said Ash. “I don’t have to wait seven or eight days to get a pigtail out of Michigan from the OEM. I can call Ruston on, let’s say, a Tuesday afternoon, and it’s at my door Wednesday around lunch.”
The fast delivery paired with high-quality connectors gives Ash peace of mind.
“Our philosophy since we started working in diagnostics has been, ‘I don’t want to worry about my repair down the line.’ If something’s wrong, I want to know that my repair is OK and that it’s something else on the car,” Blanchard explained.
“So, that’s why we started with OEM plugs, which comprise 98% of our inventory.”
FindPigtails.com has secured distributors that sell OEM connectors, including ones with factory part numbers, and the company works directly with most car insurance companies.
“We make our wires and terminals in-house,” said Blanchard. “Ninety percent of the time, shops buy our OEM-plus plug that we’ve upgraded with higher temperature wire,” which deters rodents and “knocks down and absorbs flames,” he explained.
Kyle Gibson, vice president of Gibson Automotive, said his company’s core values align nicely with those of FindPigtails.com.
“Our core values are not a printed statement, but the beliefs of all that work here,” Gibson said. “We are all united by a simple phrase, ‘Do the right thing.”
Gibson said he and his team apply this philosophy to all daily activities “to keep the body shop machine rolling.”
“We break it down to its simplest form; make one decision all day: do what’s right to ensure all parties involved are taken care of,” he said. “That includes the customer, the vehicle, the insurance company, the vendor and Gibson Automotive.”
Apart from implementing toptier products and procedures, Ash said Gibson Automotive creates a welcoming environment for every customer.
“There are so few people in this town who don’t know the Gibsons since they’ve been a part of the community for so long,” he said. “Everybody feels at home when they come here, and that’s the vibe we like to keep.”
Gibson Automotive Greenville, TX 903-454-9111
gibsonautomotive.com
Type: Collision Repair
Facility Employees: 21
In Business Since: 1969
Number of Locations: One
Production Space: 15,000 square feet
FindPigtails.com
844-255-5899
findpigtails.com
Facebook: @findpigtails
On-Time Rate:
During the pandemic, auto body shops were struggling to get parts, cycle times were impacted negatively and it became more like a scavenger hunt that parts people weren’t enjoying for obvious reasons. In many cases, cars sat while customers and insurers fumed.
But one company excelled during the pandemic by providing CAPA-certified quality parts for shops throughout the country. By filling orders others couldn’t, GoParts became a savior during highly uncertain times.
Freedom Collision Center in Morgantown, WV, is one shop that benefitted greatly. Parts Director Jack Sloan was able to save the day by working with Go-Parts, tapping into its inventory of approximately 200,000 parts to get parts on time.
With more than two decades of experience in the parts game, working for dealerships and independent shops over the years, Sloan has seen the industry evolve dramatically, and pivoted accordingly.
“In the old days, we could work with a limited number of vendors to get what we needed for each and every repair,” he said. “Now, we have to work with multiple vendors on almost every job. With three vendors minimum per vehicle, we never know who we will call upon and, in many cases, we have to reach out to more than that to get what we need.”
To repair 118-135 cars every month without exception, Sloan uses PartsTrader for the lion’s share of his repairs.
“We love working with this software because it gives us a lot of information that makes all of our jobs much easier,” he said. “We put the job out there, and the parts suppliers tell us everything we need to know, including availability, our cost, list price and of course, our profit margin, which is a huge part of it. With Go-Parts, they have been very successful in filling many of our orders, which is vital when we work on so many brands. From a bracket all the way to a headlamp, Go-Parts. com helps us to streamline the
entire process from start to finish. In many cases, they are getting parts the dealership does not have and by using PartsTrader, we can get that data quickly.”
In the old days, an estimator would have to see the vehicle firsthand, but now many of the repairs start out with a photo estimate.
“In some cases, we can get all of the parts we need up front, but sometimes we will discover a bracket behind a fender that wasn’t on the sheet,” Sloan said. “It’s very easy for us to jump on their website to get that single part, and their delivery times are very prompt.”
A perfect scenario that often transpires involves a pre-order, so when the car comes into the shop, Sloan and his crew are ready to roll.
“When the technician gets the job, he already has everything he needs, which means we can meet our ECD [estimated completion date] and it won’t impact our cycle time,” Sloan said. “We have a lot of DRPs, and the insurance companies like it when we hit our numbers in that regard. It’s frustrating when a car is sitting waiting for a molding or a bracket, and Go-Parts has been able to come through for us on more than a few occasions.”
Another major plus is the overall quality of the parts Sloan gets from Go-Parts.
“Price and delivery are a major deal, but quality is No. 1,” he said. “We won’t get a part unless we are confident that it is just as good as the OE, because
we guarantee every repair for the life of the vehicle.”
Order accuracy and followthrough is what makes or breaks any parts supplier, and Sloan said Go-Part’s track record is awesome.
“I have only one person working with me in the parts department, so we are constantly busy. When I come in at 7:30 a.m. every morning all the way until 4:30 p.m. at the end of the day, parts are coming in and we need to know what they are and what we still need,” Sloan said. “Go-Parts has no restocking fees and no cancellation fees, and they stress quick turnaround, so their customer service has always been excellent.”
Communication is paramount and that’s why tracking every part accurately and on time is mandatory if Sloan wants to keep his customers happy. Stockchecking and acquiring parts is like a big puzzle and Go-Parts is enabling Freedom Collision Center to put the pieces together easily and seamlessly.
“We want to know in real-time where are parts orders are, and Go-Parts has enabled us to achieve that,” Sloan said. “If someone has a question when it comes to where a part is and when we will be getting it, we always have the answers.”
Go-Parts is taking the good ol’ over-the-top customer approach and leveraging the latest technology—a combination making shops more effective and positioning them for continued success.
Freedom Collision Center
Morgantown, WV 304-241-1325
www.freedomcollisioncenterwv.com
Company At A Glance...
Type: Collision Repair
Facility Employees: 35
In Business Since: 2021
Number of Locations: One
Production Space: 34,000 square feet
Freedom Collision Center has a busy parts department, and Go-Parts is helping them tremendously.
Sloan appreciates Go-Parts’ customer service and extensive inventory.
Go-Parts
844-321-PART (7278)
Order.go-parts.com
Facebook: @gopartsautoparts
Instagram: @GoPartsRacing
YouTube: @GoPartsAutoParts
Tik Tok: GO_PARTS
Kevin and Meredith Bradshaw opened K & M Collision in 1991 in Hickory, NC. Over the last three decades, the mom-and-pop operation has grown from three employees to 35, earning 33 OE certifications and becoming I-CAR Gold Class.
“Our facility is right at 35,000 square feet, and we’re adding 12,000 hopefully by the end of the year,” said Michael Bradshaw, vice president of operations and son of the founders.
When Bradshaw started working at the family owned and operated business in 2006, it earned under $1 million a year.
“Last year, we eclipsed $1 million dollars in monthly revenue,” he said.
Bradshaw said his and his family’s foresight has led to success.
“We got ahead of the OE certification curve,” he explained. “We trended toward the higherend brands like Porsche, Lucid, Jaguar and Land Rover, which we now specialize in.”
Bradshaw added K & M Collision makes a “commitment to quality.”
“We won’t use aftermarket parts in our facility,” he said. “We operate on being the best at what we do, and we don’t make any apologies for that.”
K & M Collision houses top-tier equipment from Hunter Engineering Co. to meet multiple manufacturer certification requirements. The body shop uses Hunter’s Flush Mount Rack and Aligner, the Road Force® Elite wheel balancer, and the Auto34S tire changer (TCA34S).
Bradshaw said K & M Collision started using an aligner from Hunter Engineering after a conversation with a local dealership.
“At that point, we were subletting all of our alignments,” Bradshaw said. “We had a vehicle that stayed at the respective dealer for about a month; they kept changing parts on the vehicle because they claimed they couldn’t get it to align properly.”
Shortly after, one of K & M Collision’s other dealer partners put in a new Hunter aligner and gave away its old alignment console.
“We put the old alignment
console in our shop to test out, and within three months, we purchased a brand new Hawkeye Elite® machine,” Bradshaw said. “From then on, we’ve performed prealignment checks on every vehicle that comes through the facility.”
Bradshaw explained a “conventional shop” alignment process versus the process K & M Collision implements with the Hunter aligner.
“If you have a conventional shop environment, where they’re following OEM information to the letter on every repair, only about 30% to 40% of the vehicles they’re repairing will have alignments at the end,” he said. “So, an additional 20% to 30% of vehicles come through, and using the Hunter aligner, we’ve been able to identify suspension misalignment on impacts that largely, as an industry, go unidentified.”
Bradshaw reported alignment checks fail “62% to 68% of the time in any given month.”
“So, using the Hunter aligner has been a major profit center for us,” he said.
On top of that, K & M Collision does a lot of ADAS in-house.
“Many of these manufacturers require suspension alignment to be within factory specifications before performing ADAS calibrations,” Bradshaw said.
The Hunter aligner has also helped K & M Collision identify suspension misalignments in vehicles whose wheels appear unscathed.
“These are accidents, where the impact is from a direct front or rear hit,” Bradshaw said. “And based on what the industry typically looks at, they’re not considering
suspension alignment issues on those cars.”
However, Bradshaw said the pre-alignment check tells a different story.
“Even in these situations, we find misalignments outside the tolerance,” he explained. “And regarding driver safety, the vehicle manufacturers require a steering angle sensor initialization or zeropoint calibration after the battery’s disconnected and reconnected. If you’ve got a shop that assumed the suspension alignment is within specification, that can create some issues in the future.”
Based on the impact and manufacturer requirements, K & M Collision uses Hunter’s Road Force® Elite diagnostic wheel balancing machine to check each tire and wheel assembly. A collision repair technician then uses the TCA34S tire changer for tire replacements when needed.
Regarding support from Hunter Engineering, Bradshaw said K & M Collision has had a “very positive” experience.
“The sales rep we have— David—has been accommodating,” Bradshaw said. “When I’m interested in new equipment or have questions, he’s here within a day or two. He also sometimes brings in new equipment for us to demo.”
Bradshaw deals with Todd on the service side, who has a schedule to meet K & M Collision’s needs proactively.
“I can’t think of many times we’ve called Todd, and he hasn’t answered his phone,” Bradshaw recalled. “And when he isn’t available, he always gets back to us immediately.”
K & M Collision
Hickory, NC
828-569-1275
kandmcollision.com
Company At A Glance...
Type: Collision Repair
Facility Employees: 35
In Business Since: 1991
Number of Locations: One
Production Space: 35,000 square feet
K & M Collision, which holds 33 OE certifications, trusts Hunter Engineering for factory-grade alignments.
K & M Collision, a family owned and operated body shop in Hickory, NC, opened its doors in 1991.
Hunter Engineering Co.
314-716-0469
tmaitz@hunter.com
Facebook: @hunterengineeringcompany
Instagram: @hunterengineering
LinkedIn: @hunter-engineering
YouTube: @HunterEngCo
On the Road Garage is a busy auto body shop with two I-CAR Gold Class locations, in Irving and West Dallas, TX, where 25 employees repair a total of about 150 cars per month.
But it’s also part of a larger mission. Its parent company, On the Road Companies, was founded in 2011 by CEO Michelle Corson, and has since grown into a portfolio of a wide array of ventures aimed at getting people and communities “on the road” to success by bringing down transportation-related costs.
On the Road Garage joined the fold in 2020. Not only does it provide quality collision repair services to the area, but it also boasts a Department of Laborregistered paid apprenticeship program to train people in collision repair, ADAS and other smart car technology, filling a skills gap and talent pipeline shortage. With I-CAR Gold Class recognition, On the Road Garage is demonstrating to its customers and community it is employing trained professionals who are acquiring the knowledge and skills necessary to perform complete, safe and quality repairs.
The apprenticeship program includes five pathways: body repair, painting, estimation, mechanics and technology, and office management. Each provides a blend of classroom and hands-on training, all provided by master technicians and senior management leaders.
Roy Villarreal, vice president of operations for On the Road Garage, is a 30-year industry veteran who took his first auto repair class in high school because a classmate assured him it would be an easy A. “It sucked me in,” he said with a laugh.
After high school, Villarreal attended WyoTech in Laramie, WY, then landed his first job at a LincolnMercury dealership, sweeping floors and cleaning bathrooms. He had worked his way up to doing small body work jobs when the advent of computerized estimating – which his manager didn’t understand – got him promoted to a service writer, and he progressed from there.
He has been with On the Road Garage since it opened. “One of my former bosses told me I needed to
come check [On the Road Garage] out,” Villarreal said. “I met Michelle, and I learned about the vision behind the work.”
Villarreal said I-CAR’s training subscription plays a major role in training everyone from apprentices to the 45-year industry veterans and employees teaching them because it includes live, online and virtual courses for everyone at the shop.
Villarreal said the apprenticeship program at On the Road Garage takes about three years to complete, so the first cohort of six apprentices is still in it. He said the garage envisions having room to hire everyone in at least the first two cohorts and give recommendations to anyone who wants to venture elsewhere.
“The overarching mission is to give people an opportunity in life,” Villarreal said. “We bring somebody in, teach them a skill, and they can make a good living for themselves. We can also replenish the technicians in the industry.
“We use I-CAR’s solutions to leverage the theory behind it,” Villarreal said. “We want them to know why they’re doing what they’re doing. That’s one of the ways we use I-CAR.”
I-CAR’s training subscription provides unlimited training for all technicians and shop employees and is available to Gold Class shops. I-CAR says its program lets shops manage and plan their training more effectively while helping reduce training costs due to technician turnover. It also enables
shops to build their bench strength and increase employee retention.
The training subscription includes live, virtual and online courses, which covers the majority of the Gold Class required courses, and offers flexible payment options.
Villarreal said I-CAR’s training allows them to accept into the program apprentices with zero industry experience, as well as those who have already taken relevant courses in high school or college.
Every single apprentice and employee of On the Road Garage takes ADAS courses through I-CAR, Villarreal said, as both locations work on more technologically advanced vehicles. The Irving location is now a certified Rivian repair shop.
“Even five years ago, we were [repairing vehicles] differently,” Villarreal said. By achieving Gold Class recognition, On the Road Garage is committing to training that helps its technicians keep up with the latest advancements with each Gold Class renewal cycle. For that reason, continuing training is just as important for technicians with years of experience, he said.
Villarreal also appreciates the I-CAR training subscription plan’s ease of use. “You have the entire catalog in front of you. You can be assigning classes even outside of a learning path, so people can explore other subjects or specialty areas.”
For On the Road Garage, I-CAR training is a key partner in its mission.
“It’s important to us to train the next generation, to give someone a great opportunity,” Villarreal said.
Irving & West Dallas, TX 214-736-4976
ontheroadgarage.com
Company At A Glance...
Type: Collision Repair
Facility Employees: 25
In Business Since: 2020
Number of Locations: Two Combined Production Space: 44,000 square feet
On the Road Garage’s paid apprenticeship program trains people in collision repair, ADAS and other smart car technology, filling a skills gap and talent pipeline shortage.
By achieving Gold Class recognition, On the Road Garage is committing to training that helps their technicians keep up with the latest advancements with each Gold Class renewal cycle.
I-CAR
800-I-CAR-USA
www.I-CAR.com/GTGC
Facebook: @icareducation
Twitter: @I_CAR_Education
Instagram: @icareducation
LinkedIn: @company/i-car
YouTube: @user/icartraining
1
Gas-catalytic, medium-wave infrared curing is adaptable to a broad range of applications.
To determine how US Autocure systems can help you, we start with 3 simple steps:
2
CHEMICAL ANALYSIS: First, our chemist will review a list of the coatings products and other technologies used in your application. He’ll be able to tell us what to expect in terms of your particular coatings and their response to infrared energy.
ROI ANALYSIS: Every opportunity is unique. We’ll work with you to determine the areas of savings and gains that apply to you, and we’ll help you estimate the financial impact of incorporating a US Autocure system into your specific application.
3
PROCESS ANALYSIS: Once we’ve determined that your coatings will respond favorably to infrared energy and the initial financial analysis is positive, our engineer will outline a system designed to meet your needs. We will compare this to the ROI analysis to help you make the best decision for your profitability.
There are no costs associated with these steps and we will not share this information with anyone but you. These activities can be completed quickly, but we won’t rush you.
We believe in our technology. We want you to be comfortable that it’s right for you.
When you’re repairing the finest vehicles in the world, you need to work with world-class companies to ensure your success. Co-owners Bryan Thompson and Dan Schimpke at Beverly CoachCraft in West Los Angeles, CA, know this very well.
So, back in October when they were looking for a new paint jobber, they hoped to find the right company, and they did. Industrial Finishes and Systems matches their culture in many ways, and the move has already benefitted them greatly on multiple levels.
In 1985, Schimpke was hired as a technician and two years later, he acquired half the business from its founder, Peter Sardi. Last year, Thompson became the company’s co-owner, and today he and Schimpke run the show together at Beverly CoachCraft. It has become a special relationship between partners who share the same goals.
Beverly CoachCraft is a Mercedes-Benz Elite and EQ Certified shop, and also certified to work on Teslas. Thompson said the shop also specializes in working on exotic and “hyper-exotic” vehicles and unique vehicles.
To thrive in that “top tier” arena, Beverly CoachCraft needs to hire and retain the industry’s best techs, estimators and painters.
“The short story is we’re looking for winners to meet our revenue goals while heavily focusing on the culture of the shop,” Thompson said. “As we know, the current market has elevated demands for technicians’ salaries. That is why we have to choose our projects wisely, so that we can support top technicians and attract new talent.”
For that reason, they do a lot of little things that go a long way with their employees, Thompson said.
“We have benefits, and we buy them lunch once a month. We have a gaming area for the employees to unwind. We have more of a European business model, where labor has a voice in our operations,” he said. “We bring in young people as apprentices to even out the workload from the journeyman technicians. The guys are treated
with dignity and respect, which is probably the most important thing.”
In return, the employees at Beverly CoachCraft are expected to work safely and perform factory quality work.
“We do regular factory service engineer document lookups during each repair,” Thompson said. “All of the structural and mechanical repairs have service engineer lookups done and carefully documented. Things like torque wrenches are calibrated annually. The technical aspects of riveting, bonding and welding are addressed during regular training. As a result, we have a culture where all of our people are a very valuable part of our business, and I believe it works well for that reason.”
Referrals are a big piece of the puzzle at Beverly CoachCraft. “We walk the walk as far as car repairs go, and as a result, we have created a large amount of goodwill in the trade and with the customer. We have a ton of repeat business in a very interesting high-end market on the west side of Los Angeles.”
When Thompson and Schimpke were looking for the right company to provide all their AkzoNobel paint supplies and allied products, they traveled to the Industrial Finishes and Systems headquarters in Eugene, OR.
“We spent a few days with the owner, Stu Barr, and their team and realized rather quickly that our beliefs aligned strongly with theirs,” Thompson said. “They are the real deal, there’s no doubt about it. They’re straight shooters and we
respect that because the reputation doesn’t fix the car. We have to climb that hill every day.”
Thompson and Schimpke were looking for market share in Los Angeles and wanted a new business partner that could help them.
“Industrial Finishes had a lot of innovative ideas with regards to helping us with our billing to the insurance carriers,” Thompson said. “In addition, they have some great technology to monitor our liquid consumption and our consumables, which was important to us. They’re definitely interested in us being successful so that we can buy more of their services and products. It’s a win-win, and I can rarely say that about a vendor-buyer relationship.
“We are very impressed so far and they’re continually impressing us more and more,” Thompson said. “They have really gone the extra mile to be sewn into our business. We share their core values, which made the change an easy decision.”
With four people dedicated 100% to providing exemplary customer service for Beverly CoachCraft, Thompson is delighted with everyone at Industrial Finishes and Systems, and looking at a bright future with them on his team.
“They are a lot more than a distributor,” he said. “Product support is so vital in this industry, and Industrial Finishes and Systems is a lot more than just being our jobber. It was very easy to onboard them and everything has happened just like they told us it would.”
Beverly CoachCraft, Inc. Los Angeles, CA 310-477-6561
www.beverlycoachcraft.com
Company At A Glance...
Type: Collision Repair
Facility Employees: 31
In Business Since: 1979
Number of Locations: One
Production Space: 30,000 square feet
Industrial Finishes.
Industrial Finishes and Systems
800-531-1305
www.industrialfinishes.com
Facebook: @industrialfinishes
Twitter: @indfinishes
Instagram: @industrialfinishesandsystems
LinkedIn: @Industrial Finishes and Systems, Inc.
YouTube: @IndustrialFinishesTV
European Motor Car Works has deep roots in Southern California. Founded by Kye Yeung in 1975 in a small industrial park, the multigenerational Costa Mesa company is now housed in an ultramodern 33,000-square-foot facility. The shop services elite automobiles, having earned a reputation as a premier certified collision repair center for luxury British vehicles.
Yeung’s affinity for British brands dates to his youth in Hong Kong, then a British Crown colony. After immigrating to the U.S., he later enrolled in Golden West College, where he signed up for an auto body repair course.
“That was my introduction to automotive repairs,” said Yeung. “I was an architect major, but my passion was automobiles. I’ve always been loyal to British brands. They’re more difficult to repair, so that’s how we found our niche.”
The shop specializes in Jaguar, Land Rover, Aston Martin and two EV brands, Rivian and Lucid, and holds collision repair certifications from the five automakers, all of which produce aluminum-bodied vehicles. The company is also the exclusive Aston Martin Works Factory for North America.
Yeung has seen firsthand the changes over the years in auto body repair tools and processes. But there were always limitations. “Back in the day, there weren’t a lot of options. I just always tried to access panels with the least amount of intrusion for the best repair.
“Then along came Glue Pull Repair. With the KECO GPR system, you don’t have to access from the back side, because they have such a huge array of tools and accessories. I’m a tool freak. I own every tool known to mankind to make the job better, and here comes KECO with a tool for most every angle and dent. It’s mindboggling.”
The relationship with KECO is beneficial in other ways. Glue Pull Repair tools can be used on
steel- or aluminum-bodied vehicles and they can replace spot welders that could damage a panel. Glue Pull Repair can also be used on electric vehicles without powering down the EV. Plus, the GPR system complies with many OE procedures for repairing EVs as well.
From a technical standpoint, Yeung’s shop repairs both aluminum-bodied ICE-powered cars and aluminum-bodied electric vehicles. Knowing the GPR system complies with OE guidelines for EVs is a plus.
“Some of the EV OEMs we work with recommend the use of the KECO GPR system in the repair process,” noted Yeung. “They prefer the Glue Pull system to whatever else is out there. It’s less intrusive, less labor intensive and allows us the ability to produce a quality repair.”
Over the years, the company has made hefty investments in tools and equipment, OE certifications and staff training. Which accounts, said Yeung, for a door rate significantly higher than most body shops’. The average repair ticket runs at least $17,000.
In lieu of replacing costly panels or dealing with the current parts shortages, Yeung said, “GPR allows us to offer customers a quality repair and adhere to OE recommendations. Those are reasons why KECO fits so well into our shop.”
Staff training is another factor. “Another unique thing about KECO is that they offer training. A lot of older professionals don’t like change and regress to original techniques. When KECO comes to train with a hands-on approach to their newest products and 6C process, it helps the technicians buy into the system, because the new techniques are so much better.”
In reflecting on his 40plus years in business, Yeung credits the company’s success to multiple factors. In addition to a highly skilled and certified staff, his family plays a prominent role.
Daughters Jennifer Yeung and Nichole Hubbard now oversee the business. Son-in-law Mike Hubbard is the ace ADAS tech, while grandson Connor Kelly is earning certifications in welding and structural repairs.
Yeung also attributes the company’s growth and profitability to the KECO GPR system and believes other shops would benefit significantly from integrating KECO GPR into their businesses.
“The conventional way of using an older process is more intrusive. If shops adapt to Glue Pull Repair, it will allow for less cycle time, it’s a better-quality repair and they will be more profitable.
“The key is to buy into the system and train technicians. It will improve shops’ bottom line. The ROI is very, very good.”
Costa Mesa, CA
714-957-1290
europeanmotorcarworks.com
Company At A Glance...
Type: Collision Repair
Facility Employees: 20
In Business Since: 1975
Number of Locations: One
Production Space: 33,000 square feet
KECO Body Repair Products
405-745-2145
www.kecotabs.com
Facebook: @KECOBodyRepairProducts
Twitter: @kecotabs
Instagram: @kecodentrepair
LinkedIn: @keco-body-repair-products
YouTube: @KECOBodyRepairProducts
To achieve precision color matches, Helfman Collision Center in Houston, TX, uses PPG’s tools for amazing results. Shop Director Greg Luther recently acquired PPG’s MOONWALK® automated paint mixing machine, in conjunction with PPG’s VISUALIZID™ 3D visualization software, which takes information from the DIGIMATCH™ spectrophotometer to help users find dead-on color matches from PPG’s extensive color portfolio.
Helfman Collision Center is a part of the Helfman dealership group, a respected family owned and operated car dealer serving Houston and the surrounding area since 1959. The collision center is certified by Chrysler, Dodge, Jeep, Ram, FIAT, Alfa Romeo and Maserati, making Helfman the only Maserati Alfa Romeo FIAT dealership in Houston to offer a certified body shop on site.
In 2002, the company established the Helfman Collision Center with Luther at the helm. Luther has more than 30 years of industry experience—he entered the business in 1992 right after graduating from high school by working for a tire retailer, working his way up to management.
Luther is confident his team of 28 people is a strong unit because he hired all of them himself. By treating them right and proactively pursuing things such as training and cutting-edge equipment and processes, Luther has built a crew producing high-quality repairs at the rate of 200-plus vehicles monthly.
The crew’s PPG DigiMatch multi-angle spectrophotometer helps them to match colors easier and faster. It features a lightweight, ergonomic design that can be used with one hand. The camera’s six imaging angles and six reflectance angles provide color and texture information to help retrieve the correct formula matches quickly and efficiently.
PPG VisualizID software takes information from PPG DigiMatch or PPG’s other spectrophotometers to help users find the best color match. It is the first software of its kind in the industry, digitizing a process
that used to involve trial and error, resulting in reduced waste.
The PPG MoonWalk system is an automated refinish paint mixing system for the ENVIROBASE® High Performance waterborne toners that saves labor time, reduces waste and creates a clean and safe mixing environment. Paint technicians and body shop managers benefit from the extreme accuracy coming from the automation of the mixing process, improving speed, quality and color consistency.
PPG and its ENVIROBASE® High Performance waterborne paint line has played a huge role since Helfman converted from solvent in 2015 in its high-production shop, where their paint has to perform seamlessly at a high level at all times.
Luther has streamlined the color matching process by making sure everyone plays a specific role.
“First, our blueprinter takes the photo with the spectrophotometer and then the painter reviews the software and usually does just one spray-out to dial it in,” Luther said.
“Then our production manager or a porter does the mix at the MoonWalk mixing system and delivers it to the painter. It works out well, and the fact that we don’t have to do multiple spray-outs surely helps. We’re definitely saving time by using PPG’s tools.”
By wasting considerably less product, Luther’s new equipment can pay for itself very quickly.
“You can waste as much as 7 to 8 ounces of paint every time doing multiple spray-outs, so doing just one to succeed is a big deal,” he
said. He estimates he is saving at least $500 of product every month by cutting down on spray-outs, without even factoring in the time element.
Using all of the paint in the bottle is also a huge plus, Luther said. “Previously, a lot of the extra paint and toners were wasted, but not anymore. Now we are getting paid for the paint and it is going on the car and staying out of the waste stream.”
Earlier this year, PPG came to Helfman Collision Center for a twoday training that set up everyone for success using the mixing and color matching system.
“Six of our people went through the training and it was surprisingly easy,” he said. “We’ve integrated it into our production system well, and we know that we will get better the more we do it.”
The crew has been crosstrained on every aspect of the PPG VisualizID software, DigiMatch spectrophotometer and MoonWalk mixing system, so anyone can step up when needed.
Helfman has been an I-CAR certified shop since day one. Luther said PPG’s mixing and color matching tools keep his customers happy with a great finished product every time. The shop will also benefit from increased efficiency and a crew that is set up for ongoing success.
“It’s worked very well and we are pleased with the results,” he said. “Our goal is to give our people the right tools so that they can do the best job they can.”
Helfman Collision Center
Houston, TX
877-599-3919
www.houstonbodyshop.com
Company At A Glance...
Type: Collision Repair
Facility Employees: 28
In Business Since: 2002
Number of Locations: One
Production Space: 25,000 square feet
PPG
440-572-2800
rusnak@ppg.com
www.ppgrefinish.com
Facebook: @PPGRefinish
Twitter: @PPGRefinish_NA
Instagram: @ppgrefinish
YouTube: PPG Refinish (USA/Canada)
A famous Zig Ziglar quote goes like this: “If people like you they’ll listen to you, but if they trust you they’ll do business with you.”
This quote perfectly sums up Salinas Collision Repair’s relationship with Pro Spot International. Manager Mark Duliba, an I-CAR instructor, has been turning to Pro Spot repeatedly, not only because the products are reliable and made to last, but because he has an amazing relationship with his Pro Spot distributor Adolph Cosio, built on trust.
Being based in Carlsbad, CA, Pro Spot dominates the California market. Cosio is a popular and beloved rep who is as knowledgeable as he is trustworthy and supports his customers at every turn.
Beyond knowing him well, Duliba relies on Cosio to deliver the goods—literally. Some of the Pro Spot products Cosio has delivered to the Salinas Collision Repair team include an SP-5 MIG Welding Machine, i4 Spot Welder, PR-5 Riveter, NP-3 Nitrogen Plastic Welding Machine, Aluminum Pro Spot Welding Station with AL-5 Capacitor Discharge Stud Welder and a Pro Spot Fume Extractor FE110P.
Duliba has been in the collision repair industry since 1984 and has strong roots with vehicles, including classic and custom show cars, and has worked with Rod Powell, a respected custom painter and builder. In advancing to the complex cars of today, he’s seen his share of repair products and lauds Pro Spot for its excellence and quality.
He began working for Salinas Collision Repair in 1988 in its paint department before moving into production, parts and general management. As the manager, he oversees an “awesome” team of collision technicians, repairers and painters.
Another reason Duliba chose to work with Pro Spot was Salinas Collision Repair was the first Ford collision repairer in California to be aluminum certified in 2014, to work on the Ford F-150. Pro Spot has a
special partnership with Rotunda, a Ford purchasing program, through which Ford dealership shops can purchase equipment.
Because of Duliba’s I-CAR instructor background, he knew Ryan Swanson, a fellow I-CAR instructor and the training and development manager for Pro Spot.
“Ryan does all of the Pro Spot YouTube training videos, and I knew we would be well supported. I’m a big believer in service after the sale,” he said.
Duliba said he and his team love Pro Spot products because they are user-friendly, readily available—even during the height of the COVID-19 pandemic—and meet the standards for all OEM certifications they hold. In addition, he said, Pro Spot’s reliability and durability are unbeatable.
“For example, we purchased the Smart SP-5 MIG welder in 2014, and as long as you maintain and care for them, you get consistent results and quality,” he said.
He also appreciates Pro Spot’s equipment for another factor—it is all “technician proof.” Most good techs, he said, can figure out the features and master them in a short amount of time.
Duliba describes the Aluminum Pro Spot Welding Station with AL-5 Capacitor Discharge Stud Welder as a “simple system” that gets the work done. The Aluminum Weld
Station system is equipped with a portable repair station cart, and all accessories necessary for aluminum dent pulling and repair.
Duliba said the detailed features of Pro Spot’s equipment are designed with a technician in mind. For example, the PR-5 Riveter is battery-operated, so a tech doesn’t have to deal with messy cords or hoses. Regardless of the battery voltage level, it provides the correct hydraulic pressure and delivers 200 rivets per charge.
Another indispensable Pro Spot tool at Salinas Collision Repair is the Nitrogen Plastic Welder. This equipment uses nitrogen gas with heating element to restructure common plastic components in automotive repair, from cracked bumper cover surfaces to hinged tabs. The way it works is that nitrogen is used as a shielding gas to prevent the plastic from burning during the welding process, producing a strong, lasting weld, according to Pro Spot. Compressed air is used to maintain a consistent temperature between welds; that way, the nitrogen is only activated when pulling the trigger so it’s not wasted between welds.
As an industry veteran, Duliba values timeless principles that guide collision repair shops to produce quality work with an eye for efficiency, cycle time and service excellence. He is grateful to partners like Pro Spot who are 100% invested in their customers’ goals.
Salinas Collision Repair
Location: Salinas, CA 831-444-4459
Company At A Glance...
Type: Collision Repair
Facility Employees: 15
In Business Since: 1978
Number of Locations: One
Production Space: 18,500 square feet
Pro Spot International
877-PRO-SPOT
www.prospot.com
Facebook: @prospotinternational
Twitter: @prospotwelding
Instagram: @prospotwelding
YouTube: @Pro Spot International
Leap into spring with the SATA BBQ promotion and get yourself a stylish, strong and functional BBQ apron as well as solid, innovative and multi-functional BBQ tongs in stainless steel. Whether at the next family picnic or at the campground - with the SATA BBQ Kit you are perfectly set.
At participating SATA dealers, SATA customers will get the limited edition BBQ Kit along with the purchase of SATAjet X 5500 (any technologies or versions) as a gift. Available only from your local authorized participating SATA dealer – while supplies last.
Head Painter Kaci Sallee received a fast education from great teachers about how to paint a car along her fast track to success. With her SATA guns in her arsenal and knowledge she garnered from multiple painters at Premier Collision CARSTAR’s three locations in Washington State, Sallee was ready to shine. As of December 2021, she is a full-time head painter at the company’s Olympia location and loving every minute of it.
Sallee, 24, was hired as a detailer in 2018 and held the same position for two years. In the summer of 2020, she applied for a painter prepper’s position and got the job. She began working with Joe Cairns, a veteran painter, who showed her how to apply paint and avoid many of the rookie mistakes some fledgling painters can make.
“By March of 2021, they let me jump in without a lot of training, but I adapted quickly,” Sallee said. “I was able to go to all of our three shops (Tacoma, Yelm and Olympia) to learn the most I could. Each painter has their own style and sprays differently, and I took what I could from each one.
“I started using SATA guns because my teachers were using them and I wanted to do it the same way. They really liked their SATA guns, so it was a fairly easy decision. Everyone recommended them and I have stuck with them because they do an amazing job. I love the way they feel in my hand and the finished product always looks spectacular.”
Now Sallee uses her SATAjet X 5500 HVLP for bases and clears and her SATAminijet 4400 for UV primers and the occasional spotin. “The coverage is great and I can usually cover everything with two coats, depending on the colors,” she said. “The more I use them the better I get. I can see some progress every time, which is so encouraging.”
Sallee agreed the three things you want from a spray gun are control, accuracy and comfort. “My hands get a little tired at the end of the day, but the next morning they feel fine and I’m ready to roll out again. I plan on painting for a few years now,” she said with a laugh, “so the way the guns feel in my hands is very important to me.”
Maintenance is never an issue with her SATA spray guns or accessories. “After a few colors, I disassemble and reassemble them and it’s become a routine,” she said. “If I go to a silver from a white, for example, I may have to wash them more often. But in most cases, the maintenance has been easy and doesn’t feel like a chore.”
Sallee learned SATA RPS Cups are also a winner, she said. “The painters here showed me that they store much easier than the other non-SATA cups. If we have to do some touch-up or spot work, we can always store a little color in the cup and go back to it with the RPS Cups.”
To make the picture more complete, Sallee wears her DanAm Pro Series SATA ladies paint suit whenever she’s in the booth. Offered in sizes 5 to 26, the suit is machine washable, made from 100% polyester calendered materials and antistatic built-in
carbon fiber threads. She loves the way it breathes and the heavy-duty zippers on the sides. “Because it can get hot around here in the summer,” she said. “The suit makes me feel comfortable and it fits perfectly.”
When she first started using the paint suits the shop provided, Sallee ran into sizing issues. “The arms and legs were way too long and the whole suit was way too baggy. Now with my SATA ladies’ suit, there’s less material and I can move around more easily in the booth.”
Sallee also likes the fact her SATA rep is accessible and accommodating. “I was interested in an RP gun and he came and did a demo for me,” she said. “Wow, this is a great gun, I thought. This can really lay the product down and it’s so smooth. I think that will be the next gun to add to my small collection.”
With her SATA guns by her side, Sallee is pleased about her job. Using SATA guns is part of the journey, she said, and every day is a different adventure. “My plan is to be a career painter and do this job as long as I possibly can. At first, I didn’t think I would like this as much as I do. But I love everything about painting and I am getting some very positive reviews. It’s really fun and I have no complaints!”
Premier Collision CARSTAR
Olympia, WA 360-754-3893
www.carstar.com
Company At A Glance...
Type: Collision Repair
Facility Employees: 11
In Business Since: 2007
Number of Locations: Three
Combined Production Space: 27,500 square feet
Dan-Am Company
800-533-8016
www.satausa.com
Facebook: @SATA by DanAm Company
Twitter: @SATA_DanAm
Instagram: @sata_by_dan_am
LinkedIn: Dan-Am Company/SATA Spray Equipment
Electronic Measuring System
Electronic Measuring System and Multibench
Structural Repair Workstation are designed to work together seamlessly.
The Multibench allows technicians to drive most vehicles directly onto its low-profile ramps. After the vehicle is disassembled to evaluate the damage, the Touch rolls right up, letting the technicians gather measurement data in no time.
With its 10-ton pulling column, the Multibench also serves as a single-bay repair solution. Finally, technicians use Touch to check structural repairs and ensure proper OEM specifications are achieved.
Spanesi
123
MULTIBENCH
Structural Repair Workstation
Touch Electronic Measuring System:
Comparative Measurements
Complete Documentation
Mechanical Parts Measurements
Suspension Parts Measurements
User Added Points with Photos
Vehicle Frame and Structural Items
Wheel and Tire Alignment Checks
Multibench Structural Repair Workstation: Loading Capacity 3,175kg (7,000lbs)
Lifting Height 1.45m (4’ 9”)
Lift Time (Ascension) 45 seconds
Pulling Force 10 Tons
Chase Schultz and the team at Schultz Collision Center often tell customers that no matter what damage their vehicle has, the Springfield, IL, collision center will take care of their needs, from dent removal to frame straightening.
Schultz began working in the collision industry as a senior in high school, sweeping floors in a body shop, and continued helping at different shops while attending college.
After graduating, he worked in an agrochemical company while doing auto body work out of his home garage. As business increased, he decided to focus on collision repair full time and opened Schultz Collision Center with his business partner, Maddie Brown, in May 2019.
Since the pandemic, Schultz said business has been non-stop and Schultz Collision Center has become a one-stop local solution for every vehicle owner in the area.
With a focus on providing personalized care where customer service is key, the shop’s employees take time to keep their customers notified about what is taking place throughout the repair process.
“If there are issues with their car or the insurance company, we usually let our customers know first to see what route we want to take,” Schultz said. “I like to say we work for the customers; we don’t work for the insurance companies.”
When the business opened, Schultz purchased some used frame equipment and found it wasn’t meeting the shop’s needs. He and his employees researched other options and really liked what they learned about Spanesi products.
After Schultz contacted the company, Robert Wells, sales specialist at Spanesi Americas, visited the facility and helped determine the equipment that would best fit the crew’s needs.
They demoed the Touch Electronic Measuring System and were impressed with the equipment’s ease and functionality.
“We went from using our old system, which took about three
hours to measure a car after setting it up, and found we could do the same measurements within 20 minutes,” said Schultz.
“By cutting down this time, we found we could be more productive and save about 10 to 12 hours each week, allowing us to repair more vehicles.”
With a strong focus on following OEM procedures, Schultz said the Touch Electronic Measuring System ensures the measurements are accurate and are 100% within spec.
“I am proud how Spanesi products are showing our clients record improvements in their productivity,” said Timothy Morgan, chief operating officer (COO) for Spanesi Americas. “It’s great to help customers grow and expand so quickly.”
Within the first week of using Spanesi products, Morgan said Schultz called and ordered more equipment because of the drastic change in workflow.
Although the shop repairs all makes and models of vehicles, it specializes in big trucks and vans. Schultz bought two Multibench Repair Workstations to perform minor to medium structural repair operations on vehicles. At the same time, the workstation allows for effortless ergonomic solutions to minimize technician fatigue.
The shop also purchased the six-meter 106 EXT Structural Repair Bench for longer, heavier vehicles up to 11,000 pounds. The pulling column
can be mounted in 12 locations surrounding the bench, delivering 360-degree pulling capabilities around the car. The equipment has removable wheels so it can be moved throughout the facility.
“My team really likes using Spanesi’s state-of-theart equipment and has found it is reliable and accurate,” said Schultz.
A safe and proper repair with attention to detail is Schultz Collision Center’s mantra and the standard it has set to achieve for every customer’s vehicle. Schultz said Spanesi equipment helps them achieve that.
Since first working with Spanesi, Schultz has been impressed with the company’s training and support. Each time new equipment was purchased, a representative came out to demonstrate the products and answer questions. Schultz employees have also traveled to Spanesi’s training facility in Chicago for more in-depth, hands-on education.
“Service and support after the sale is key to our relationships with clients,” said Morgan.
Schultz said when future equipment needs arise, whether it’s a paint booth or other tooling and equipment, Spanesi will be the first call.
“We’ve been able to depend on them for customer service and support,” he said. “If we ever need anything, they are right there, Johnny-on-the-spot.”
Schultz Collision Center
Springfield, IL 217-679-6464
schultzcollisioncenter.com
Company At A Glance...
Type: Collision Repair
Facility Employees: 17
In Business Since: 2019
Number of Locations: One
Production Space: 7,200 square feet
With a strong focus on following OEM procedures, Schultz said Spanesi’s Touch Electronic Measuring System ensures the measurements are accurate and are 100% within spec.
Spanesi Americas Inc.
224-SPANESI (224-772-6374)
www.spanesi.us
Facebook: @spanesiamericas
Twitter: @spanesiamericas
Instagram: @spanesiamericas
LinkedIn: @spanesi-americas
YouTube: @spanesiamericas_official