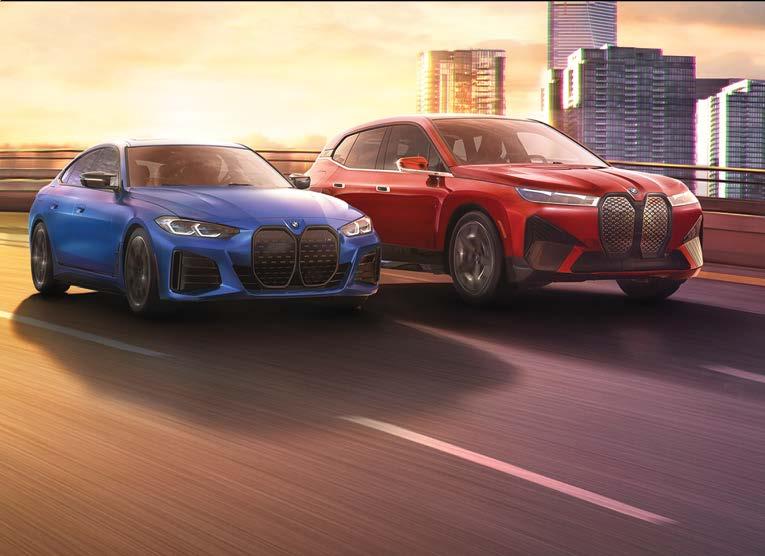
8 minute read
Classic BMW���������������������������������������������������
rate (82% in September; up from 77% in June), indicating a promising way forward for the most at-risk population.
Each state health departmenthas a tailored plan for vaccination rollout in the U.S. Currently, the three vaccines authorized and recommended to prevent COVID-19 by the CDC are Pfizer-BioNTech COVID-19 vaccine, Moderna COVID-19 vaccine and Johnson & Johnson’s Janssen COVID-19 vaccine.
Advertisement
Source: Long Island University Steven S. Hornstein Center for Policy, Polling and Analysis that can generate sulfuric acid when exposed to air and water. When this acid drains from the mines, it can devastate rivers, streams and other aquatic and terrestrial environments for a very long time.
Where the batteries for EVs are made is also an important factor when considering their environmental impact.According to Forbes, batteries produced in China produce somewhere in the region of 60% more carbon dioxide than internal combustion engines.
If China could be convinced to adopt Western standards for production, this could be significantly reduced. The report also found these factoriescould cut their emissions by up to 66% if they adopted manufacturing techniques used in America or Europe manufacturing techniques. If this were to happen, the extraction process and production of batteries would be on a par or slightly higher than the manufacturing process of ICE vehicles.
EV batteries also tend to be pretty heavy. This can result in other, often overlooked, environmental impacts like the need to attempt to reduce the weight in other parts of the car.
Lighter materials like carbon fiber-based polymers tend to be more energy-intensive to produce and difficult to recycle.
Another issue with EVs is the way in which the electricity used to charge its batteries is generated. While leaps and bounds have been made in adding renewable technologies to many countries’ energy mix, many are still heavily reliant on carbon-based power stations.
This is not insignificant either. According to some sources, EVs, on average, emit around 4,450lbs of CO2 each year indirectly. To put that into perspective, conventional gasoline cars emit at least twice as much. However, it is important to note that this varies widely around the world.
Battery production is only half the story, however. The way that batteries are disposed of at the end of their life can also potentially damage the environment.
At present, there are few countries that regularly attempt to recycle lithium-ion batteries. This has led and will continue to lead to large amounts of spent batteries ending their days in landfills.
This is incredibly wasteful, as many of the main components, like lithium, could be recovered and reused. While recycling can be achieved, most of the current research has focused on improving durability, efficiency and reduced cost of production.
Current practices involve simply smelting (high-temperature melting and extraction) of old batteries in a process fairly similar to the mining industry. This is a very energy-intensive process, compounding the hidden CO2 cost of EVs during their construction.
Improving the methods of recycling these old batteries could be potentially very lucrative, however. It may also become ever more geostrategically essential as time goes by.
Where does lithium come from? Lithium, one of the main com-
AUTOBODY
Don’t Miss the Weekly Industry NEWS Your Shop Needs. Sign Up Free Today!
www.autobodynews.com
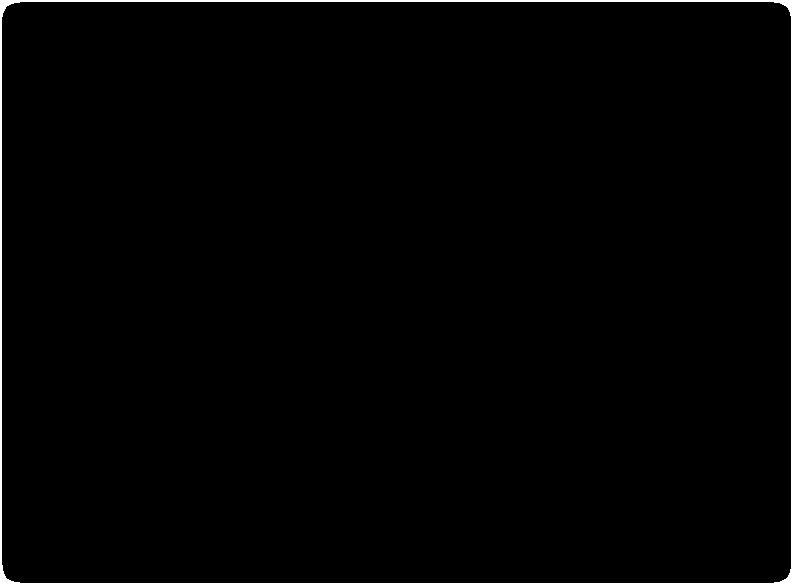
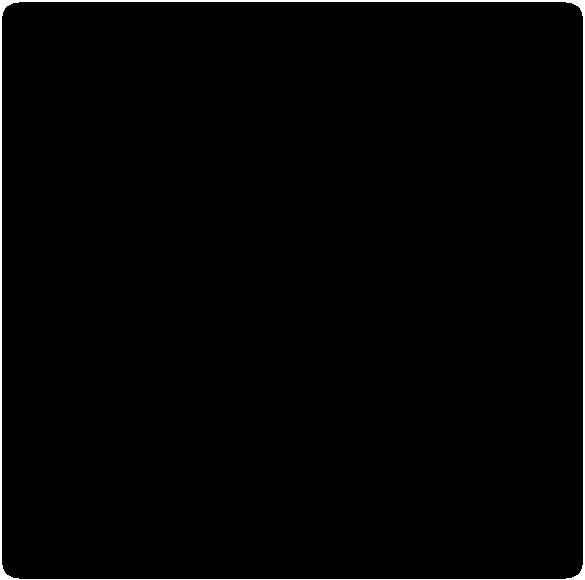
ponents of lithium-ion batteries, comes from two major sources: brine and hard rock deposits. The former is generally found in salt lakes and is extracted by evaporating off the water to leave lithium-concentrated salts.
Brine evaporation is the simplest and most common form of lithium extraction, but tends to yield the lowest grade of the material. At present, more than half of the world’s lithium resources lie under the salt flats in the Andean regions of Argentina, Bolivia and Chile.
Extraction is conducted by pumping huge amounts of brine groundwater from drilled wells to be left to evaporate in brine pools or ponds. Also called salterns, salt pans or salars, here the lithium-rich brine water is left to evaporate in the sun.
Depending on the makeup of the groundwater, this tends to lead to a concentrated mixture of manganese, potassium, borax and lithium salts. This is then filtered, and placed in another evaporation pool until a commercially viable amount of lithium carbonate salt can be extracted.
These pools or ponds can become havens for some types of wildlife, including algae and some endangered birds. As a general rule of thumb, it takes about 2 million liters of water to produce a ton of lithium.
Hard rock deposits, on the other hand, tend to produce the best yields of lithium. So, how is lithium mined?
Hard lithium mining requires significantly higher investment costs as well as extensive geological mapping and exploration to find suitable deposits. Once found, drilling equipment is used to extract the lithium ore, which provides better quality lithium at the cost of increased monetary burden.
There are various lithium ores including, but not limited to,petalite (LiAl(Si2O5)2, lepidolite K(Li,Al)3(Al,Si,Rb)4O10(F,OH)2, spodumene LiAl(SiO3)2. To date, the largest hard rock sources of lithium include Australia and Chile.
Hard rock lithium extraction tends to require about three to four years of capital investment before becoming productive, and mines― depending on the ore reserves―tend to have an average productive life of about 16 years.
Brine evaporation extraction methods tend to require five or so years of investment prior to production but will tend to last much longer than hard rock mining, with average lifespans of about 30 years.
According to some estimates, at the current rate of consumption and production, there is expected to be a shortfall in lithium by the mid2020s.
Can lithium-ion batteries be recycled?
As we have previously touched upon, lithium-ion batteries most certainly can be recycled. However, the current practices of Li-ion battery recycling, and projects currently in the works, are still very much in their infancy.
For example, in Australia, only about 2% to 3% of spent batteries are currently collected and sent offshore for recycling. European and U.S. rates are not that much better, at around 5%, give or take.
“There are many reasons why Li-ion battery recycling is not yet a universally well-established practice,” Linda L. Gaines, of Argonne National Laboratory, said in an interview with C&EN. The reasons include things like technical constraints, economic barriers, logistic issues and regulatory gaps, to name but a few.
At present, most suppliers and their clients are currently focusing on improving the battery’s lifespan and efficiency and lower their costs rather than seriously focusing on recycling them at the end of their lives.
The most common method of recycling the batteries is to melt spent batteries at high temperatures to recover the precious metals within them. This takes a lot of energy and is actually more expensive than extracting and refining new materials from raw sources.
Research is ongoing, but most efforts are still small-scale projects conducted by independent research groups or startups. However, some government initiatives have also been launched to attempt to stem the growing tide of used batteries.
For example, in January 2019, the U.S. Department of Energy (DOE) launched the country’s first Li-ion battery recycling R&D center, the ReCell Center. The idea is to help make battery recycling profitable and allow the U.S. to become self-sufficient in battery resources it lacks, like cobalt.
The U.S. DOE has also launched a $5.5 million Battery Recycling Prize to help encourage the free market to find innovative solutions for the collection, storage and recycling of spent batteries.
Across the pond, in the UK, a group of researchers from various universities has also created a consortium to achieve a similar goal. Called the Reuse and Recycling of Lithium-Ion Batteries project, it brings together 50 scientists and engineers from eight institutions and 14 industry partners.
What can be done to make EVs truly “green”?
So, given the very real environmental impacts EVs have on the planet, what can be done to make them truly “green”? Here are some examples. 1. Dispense with Li-ion batteries altogether
Since EV batteries are hazardous to the environment, from cradle to grave, the most logical step to take would be to stop using them altogether. However, this is a lot harder than it sounds. There are, after all, good reasons why Li-ion batteries have become so ubiquitous (as we detailed earlier).
That being said, there are some potential avenues to explore.
One example is the salt-based batteries currently under development through a collaboration between the University of Nottingham and six research institutes across China. By combining the performance of oxide fuel with metal-air batteries, these batteries could prove to be a viable replacement for Liion batteries. The best part? These batteries would be fully recyclable, affordable, safe and, in theory, “green.”
Other interesting examples include titanium-nitride batteries or using the “wonder material” graphene.
Other exciting initiates include a potential “never-ending” battery, too. Made from recovered and reused nuclear fuel, these batteries could last for more than 28,000
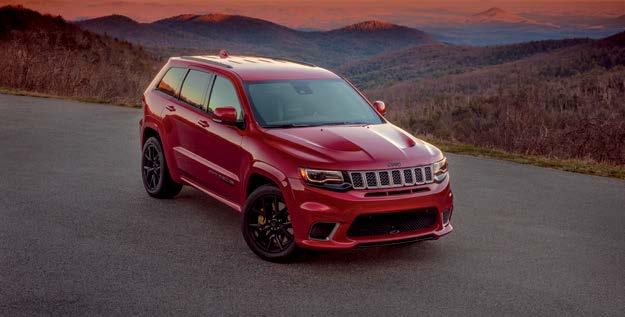
NOTHING BEATS AN O.E. FINISH.
QUALITY MOPAR® COLLISION PARTS READY TO INSTALL.
Only Mopar® tests their parts as a complete vehicle system to provide optimum performance and safety. Mopar® Parts are designed to precisely match the fit and finish of your customers’ vehicles. They protect your customers and your reputation; and because they’re easy to install, they also reduce your cycle time. For hassle-free installation and higher turn rates, use Authentic Mopar Collision Parts.
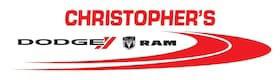
16655 West Colfax Ave. Golden, CO 80401
Toll Free: 1-800-426-6032 Parts Direct: (303) 590-7040 24 Hour Fax: (303) 590-7112 Mon.–Fri. 7:00 a.m.–6:00 p.m. Sat. 8:00 a.m.–4:00 p.m. www.cdodge.com 17 Delivery Vehicles! 4M+ Inventory!
We accept orders via OE Connection, CollisionLink, OPS Trax , PartsTrader, CCC True Parts and RepairLink.