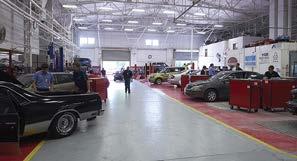
8 minute read
Cox Hires VP of Inclusion and Diversity
dent who completes the Ranken program is not going to immediately be a journeyman A-tech. But Ranken graduates will be really strong B-techs. At many programs, students learn just a little about a lot. At Ranken, they come away with the specific training and hands-on experience to be productive at the basic skills needed in a shop right away to continue to progress in their career. They also start that career with a basic set of tools, and a bunch of I-CAR training credits.
The facility for Ranken Technical College’s Collision Engineering program rivals that of the best shops in the industry
Advertisement
As I said, I’m not easy to impress. But the quality of the welds I saw students at Ranken doing was phenomenal. One of the times I visited, an instructor was working with students on a quarter panel replacement. Everything was being done exactly how the OEM procedures— which the students had access to— call for it to be done. For more information about the Ranken program, contact Shelly Jones at sajones@ranken.edu. Now you might be thinking: That’s great, Mike, but my shop is nowhere near St. Louis. So here are a few more things you should know. I have been so impressed with the Ranken facility, I moved the hands-on ADAS training we do for Nissan/Infiniti from Florida to Ranken. So come take that training and see Ranken for yourself. The school has a dorm and cafeteria for students who don’t live in the area. I know a shop owner in Colorado who, like me, was so impressed with Ranken, he’s having his own son attend the program there. If I still had my shops and I found good prospective apprentices, I would definitely have them attend the Ranken program. I’d tell them they would need to line up the grants, scholarships or loans needed initially to pay for the program themselves. But I’d also have an agreement with them that as long as they were working for my company and doing a good job, I would make their student loan payments. They’d have some skin in the game up front, but also a strong incentive to stay at my company.
And here’s the really good news for the industry: I want to give a big shout-out to the Enterprise Rent-ACar Foundation, because they have gotten behind the Ranken program. What’s more, the foundation is helping fund a pilot project to bring the Ranken model, including that awesome eight-week rotation system, to other schools around the country, including Contra Costa College in San Pablo, CA; Texas State Technical College in Waco, TX; and College of Lake County in Grayslake, IL. As the pilot project continues, participating schools, shops and students are perfecting an awesome model for what entry-level collision repair training should look like. Get involved if you can. I truly believe it will be a key part of improving the development of the entry-level technicians this industry so badly needs.
Cox Enterprises has hired Erin Mitchell Richeson as the vice president of inclusion and diversity (I&D), effective Oct. 29.
In this role, Richeson will lead the implementation of the company’s inclusion, diversity and equity (ID&E) strategy and will report directly to EVP and Chief People and Operations Officer Jill Campbell. She will consult on and support Cox’s efforts around diversity recruitment, employee engagement, diversity learning, talent development and supplier diversity across our divisions. Prior to joining Cox, Richeson was vice president of global inclusion and diversity at the Kimberly-Clark Corporation. She designed and managed the execution of sustainable I&D workforce plans globally and in key markets. Her work in this area helped improve business results through inclusion-based strategies that enabled workforce diversity growth. Source: Cox Enterprises
Your Trusted Source for All Your Genuine GM Collision Parts
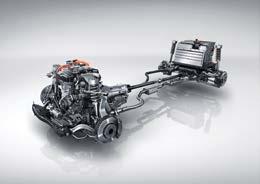
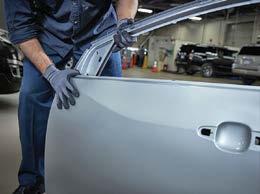

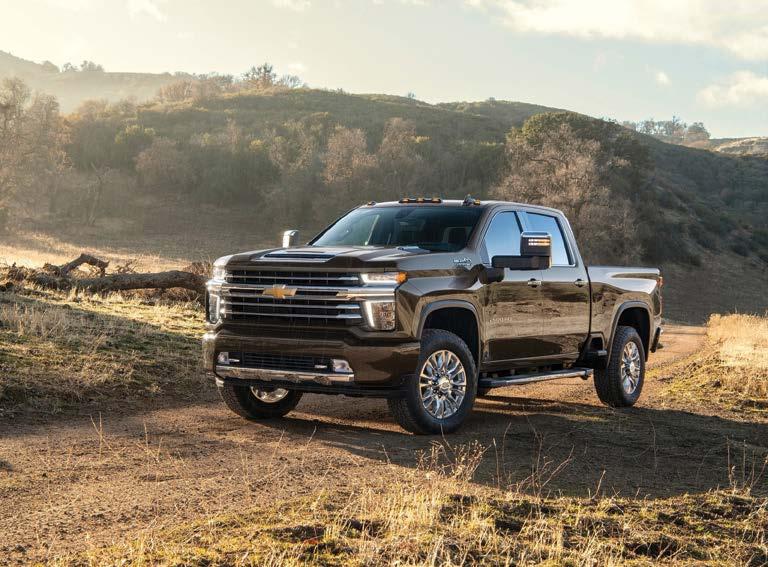

833-691-1440
Direct: 210-341-2217 24 Hr. Fax: 210-308-8683 Hours: Mon-Fri 8am - 6pm Sat 7am-4pm
• Extensive 3 Million+ Inventory of OEM GM Parts • Fleet of 13 Delivery Vehicles Covering the Greater San Antonio Area and South Texas • Certified GM Wholesale Parts Specialists Dedicated Exclusively to WS Clients with 150+years combined experience • We offer Progressive Competitive Pricing and Discounts
hart encourages repairers to act differently. “If we keep doing the same things, we are going to keep getting the same results,” he noted. “We know we have to find ways to attract new talent, but we also have to find ways to reduce staff turnover, which is in a business owner’s control.”
Flockhart cautioned shop owners and managers to not lose sight of the significant cost attached to someone leaving an organization and having to find a replacement. “The cost is approximately one and a quarter times their salary and benefits package,” he said. Flockhart shared five ways to improve a team’s performance in a collision repair facility:
1) Identify the skill gaps 2)Attract people with potential even if they don’t have the skills today 3) Create a career path for them and invest in their development 4) Ensure they have a sense of purpose and recognize their efforts 5) Reward their performance, not necessarily financially
Flockhart recommends moving away fromthestructureofA,BandCtechnicians and focus instead on apprentices, entry-level journeymen and master technicians.
He also encouraged owners and managers to focus on the culture in their shop so it is considered a great place to work. Although it can be challenging at times, he said business owners shouldn’t lose sight of how much of a positive impact that can make.
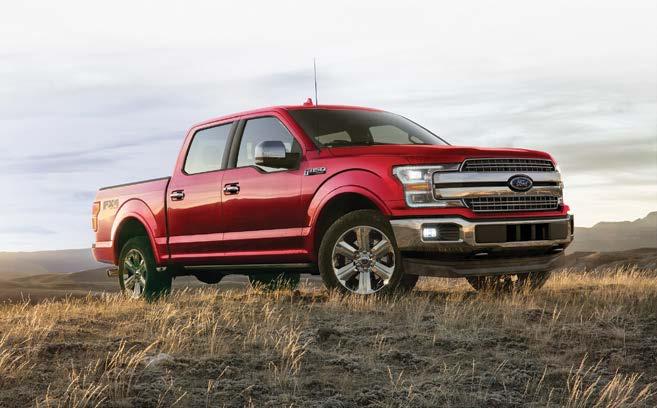
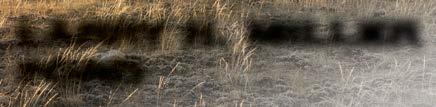
How Work Mix Impacts Performance
The typical work mix in shops today, according to Flockhart, is 6065% outer panel repair, 15-20% structural repair and 20% total loss. “The percentage of outer panel repair is increasing as a portion of the total because ADAS features are reducing impact speeds and by extension, the heaviness of the hit,” explained Flockhart. “However, severity in terms of dollars is increasing because of the cost of repairing/ replacing the same ADAS technology when there is a collision, even if it is at a slower speed.” During COVID, with less traffic on the road, the average impact speed trended upwards but this should be an anomaly when considered over a longer timeframe, he added. Approximately five years ago, total losses were about 13-14% of the work mix, according to statistics from CCC Intelligent Solutions shared by Flockhart. He pointed out for the first time, just over 20% of
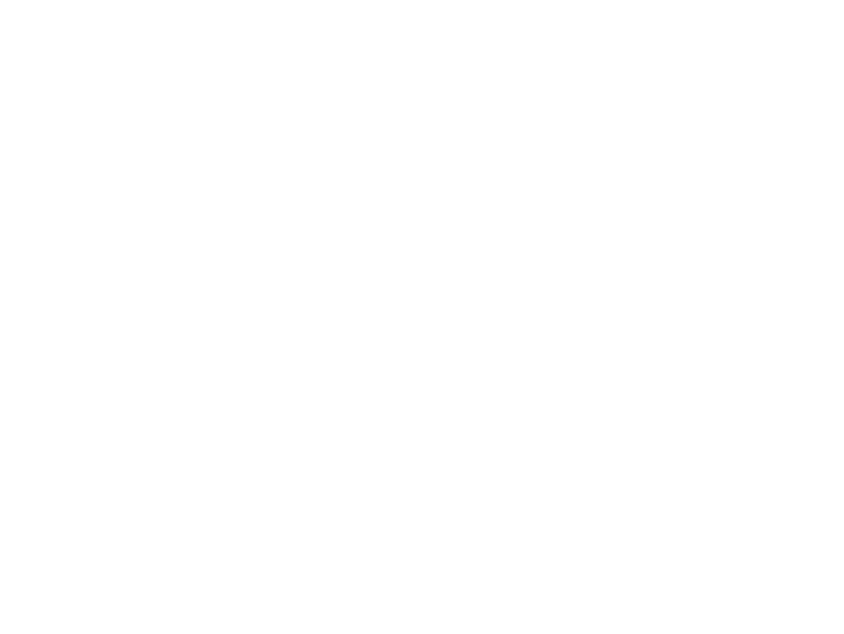

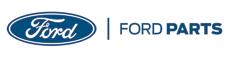
vehicles—one in five coming into the shop—were deemed to be total losses. Not only are these vehicles taking up space, but they also take up estimating time. Although shops must deal with the total loss side of the business, Flockhart said they are ultimately in the business of repairing vehicles. “With some very good reasons, the focus and investment tend to center on structural repairs,” said Flockhart. “If we are going to be in the business of repairing cars, there is no question as repairers we must be able to do that properly.”
However, he pointed out that structural repairs represent the smallest part of the work mix but take up a disproportionate amount of investment dollars, time, training and technicians. In light of this, Flockhart recommends shops put their focus and investmentdollarstowardouterpanel repair to improve performance. Although it has typically been an overlooked area over the years, Flockhart said it represents the majority of work now and continues to grow.
“Materials have evolved but repair methods have not; performance is suffering as a result,” he said. With OEMs incorporating more complex, lighter-weight materials in vehicles, such as aluminum, thinner steels and composites, repair methods have not kept up.
“The challenge is that we have this ever-present pressure to focus on the repair,” he said. “I think this has manifested itself and has become disruptive in the shop. This is where the skill shortage comes in.” By focusing on outer panel repair work, Flockhart said shops have an enormous opportunity to become more proficient in this area and improve performance metrics, increase touch time and reduce cycle time, and lead to higher gross margins and more workflow. “If we can find a way as repairers to become better than we currently are in that section, the opportunities are significant,” said Flockhart. “It enables apprentices and journeyman technicians to become super productive outer panel repair specialists, allowing the master technicians to focus their skills
on the complex repairs that demand experience.” Tohelpfindwaystoattract,train and develop the skills of apprentice and entry-level journeyman techs, BETAG created a technicians’ training and accreditation program for an outer panel repair specialist (OPRS) to help businesses increase productivity and repair quality. Flockhart said the program aims to help equip the technician of tomorrow with the skills they need to have a direct impact on business performance today. For more information about BETAG, email Dave Flockhart: flockhart@betaginnovation.com. For more information about Dave Luehr’s Elite Body Shop Academy and to watch this webinar, visit: https://elitebodyshopsolutions. com/academy. For more information about BETAG’s program to grow skilled technicians and perform better, visit: https://betagnorthamerica.com/tech Part of BETAG’s Outer Panel Repair Specialist (OPRS) nicianAccreditation.php. program includes aluminum panel repair training www.autobodynews.com The Ford Wholesale Parts You Need Now! Hours: M-F 7am - 7pm Saturday 7am - 4pm
LARRY H. MILLER
FORD FORD FORD butch.lemen@lhmauto.combutch.lemen Wholesale Hotline : 480-530-9720 24 Hr. Fax: 480-530-9708 460 East Auto Center Dr., Mesa, AZ 85204
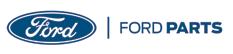