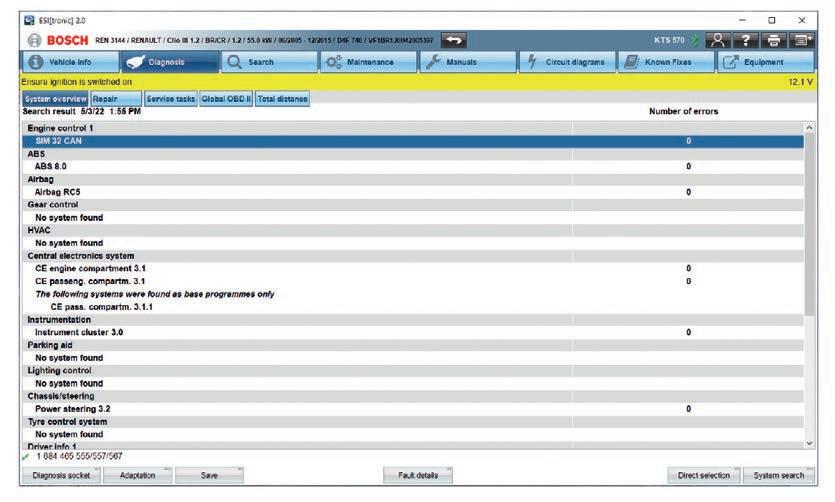
12 minute read
KTS Diagnostics made ESI
LESSON 2: UNDERSTANDING SYSTEM OVERVIEW AND PROTOCOL REPORTS
Welcome to the second in a series of guides from Bosch to help your workshop make the most of its ESI[tronic] 2.0 software, designed to boost your know-how of the key features to maximise pro ts and enhance e ciency. This series of technical articles will break individual topics down and build all the way up from the basics to advanced expert tips.
Remediation And Reporting Made Simple
In our last article, we covered how users of the software can easily and e ciently select the correct vehicle, and the importance of retrieving reliable information on the vehicle being worked on.
In this short guide, we’ll dive into the detail of how the System Overview feature can help you identify potential issues to arrive at the right diagnosis, faster than ever before. As well as how our Protocol Reports option can help you document the remediation action taken by your technician team in a professional report.
Accessing Your System Overview
The ‘System Overview’ feature on the ESI[tronic] 2.0 works as the users ‘complete vehicle diagnostic check’, allowing you to carry out the necessary tasks e ciently for every vehicle that comes through your workshop doors for a service or repair. It helps to quickly and easily identify intermittent issues, pending technical problems and mechanical di culties that the driver or customer may not be aware of.
This feature will also run a systematic check on the vehicle, ensuring it has a clean bill of health for when it is handed back to the owner after a repair or service. Allowing you to know that you are delivering the best service possible to your customers, see Figure 1
How To Perform A System Overview
STEP 1
Open the Diagnosis main tab.
STEP 2
Click on the ‘System search’ F12 soft key in the System Overview sub tab.
STEP 3
The KTS will then perform a full ‘Control unit search’ of all communicating systems.
STEP 4
Double click any of the system names in the categories for direct access to the ECU diagnostic functions for further information and testing. If a fault code is erased here, it will refresh when a user returns to it – enabling you to save and show the before and after status to show the vehicle owner.
STEP 5 to save or erase whichever information you choose to, which can be bene cial when you are justifying a lengthy repair process or operation time, see Figure 3
Store the complete list in the job report with the F3 save button. You can also access a speci c list of Diagnostic Trouble Codes (DTC’s) and any available descriptions via the F5 fault details button. Again, this can be saved to the job protocol with a tap of the F3 save soft key.
When the system overview is complete, you will see a list of all ECU systems that are communicating and an indication if any fault codes are present. This is particularly bene cial when users are analysing a vehicle prior to any in-depth diagnostic testing as some faults, for example ESP problems, can log a DTC in more than one ECU.
Once you have retrieved the overview list, if necessary, any of the system names in the categories can be double-clicked. This will take the user straight to the ECU diagnostic functions for additional investigation and testing. From here, if the fault code no longer shows up, the overview list will refresh itself once you return to it.
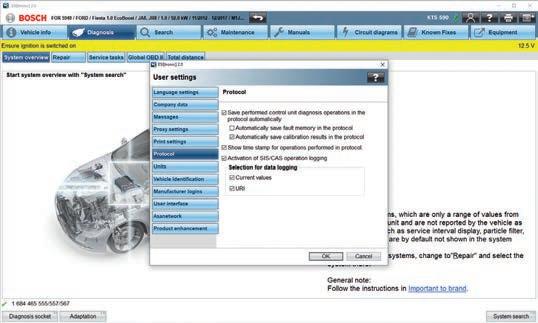
Alternatively, you can also select the ‘Delete All Faults’ button to delete all DTC’s across multiple systems or ECU’s – in a single click. It’s worth noting that many newer vehicles will now support a fast CAN Bus search of all of the ECU’s on the vehicle system communication network. In some instances, a vehicle brand can have up to 60 ECU’S that can all be checked in under a minute, speeding up the technician’s task of assessing the diagnostic state of the vehicle. Yet, for other vehicle brands, this process may take a little longer, due to the KTS checking each ECU individually for presence and fault status of each group. The new generation of KTS (560/590) can communicate simultaneously over two communication channels in parallel to signi cantly speed up the time required for a complete vehicle scan.
Preparing Your Protocol Report
The System Overview function enables you to quickly and easily produce a professional and accurate vehicle report. The perfect tool to help you justify any repairs that you need to carry out on the vehicle to the owner, see Figure 2
Show The Full Journey
Document the end-to-end process followed by your technicians during any diagnostic fault- nding work and share the before and after progress with your customers.
BUILD YOUR REPORT, YOUR WAY
Choose to include a variety of di erent information in your reports – from ECU system names and identi cation details to the number of trouble codes stores and their descriptions.

Save Your Preferences
The amount of information included in your protocol can be stored under ‘User settings’ in the main menu. This allows you
You can also choose to include your garage details that will appear in the report, alongside the option to include the job number, customer’s details, and any advisory comments to be communicated to the customer.
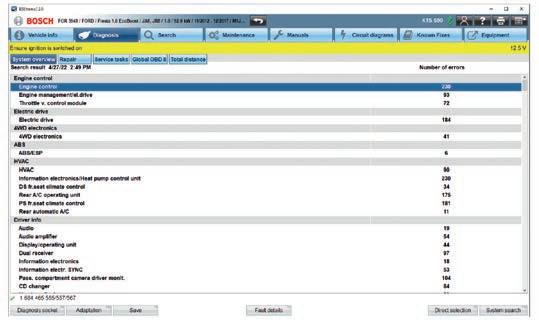
Importantly, the protocol le can be saved in a PDF format, which is useful for technicians to print and attach to an invoice, highlighting to customers what problems were found and repaired.
Each time a technician selects a di erent vehicle with the software and some information is saved, a new protocol report will be created.
A key new feature of the ESI[tronic] 2.0 is that you can continually save data to a previous protocol within the ‘last 30 vehicles’ list if you return to an un nished job, see Figure 4 www.bosch-training-solutions.com/eventcalendar
In the next issue, discover how the Bosch ESI[tronic] software streamlines your everyday service tasks in the workshop.
Overview of the fuel system
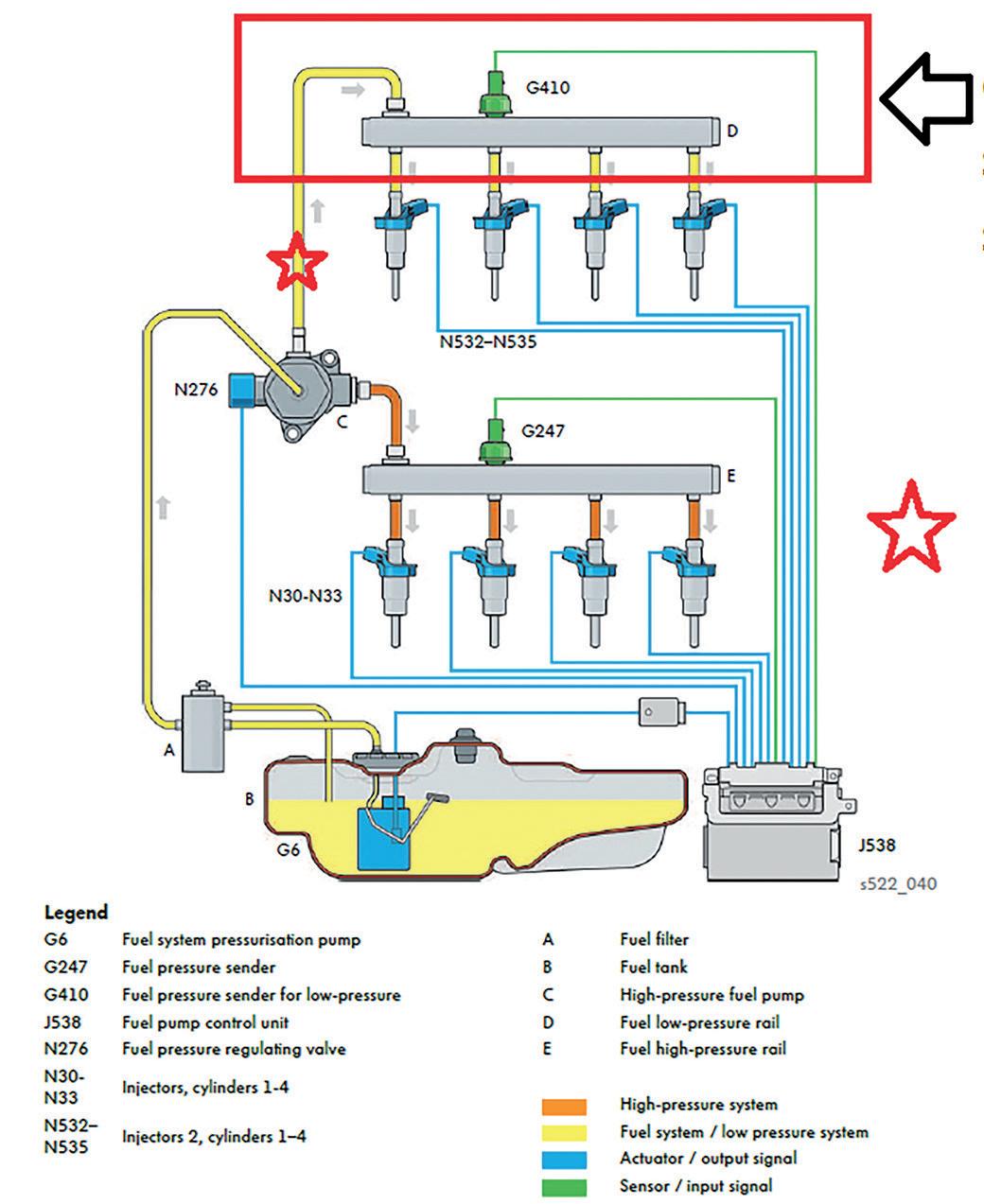
Technician
By Gareth Davies AAE FIMI, Euro Performance
Case study:
016 VW Golf R TSI 45,000 miles
Long Crank no DTC’s
Last year, we were presented with a 2016 VW Golf R TSI, and its issues were well documented by the customer in a ‘love letter’ as we call them in the workshop. It explained the symptoms, a large list of work conducted to date in a previous workshop and what they believed was responsible for the issues starting on a fairly low mileage, well-loved car.
Initially this was not my task to examine; there’s six of us on the workshop oor. Initially it was perceived the issue resided with the High-pressure fuel pump (HPFP) and was duly repaired with a new genuine item, tested under failing condition, and collected by the customer. My assistance was required for a di cult phone call from a disappointed customer two days later who reported that almost the same symptoms were back, and that they weren’t best pleased given the amount of cash invested both with my garage and a previous garage, to be at the same point.

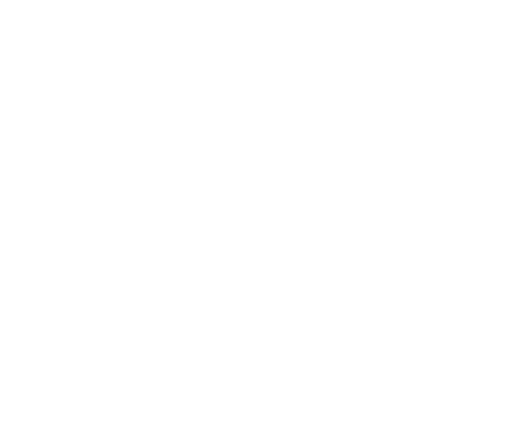
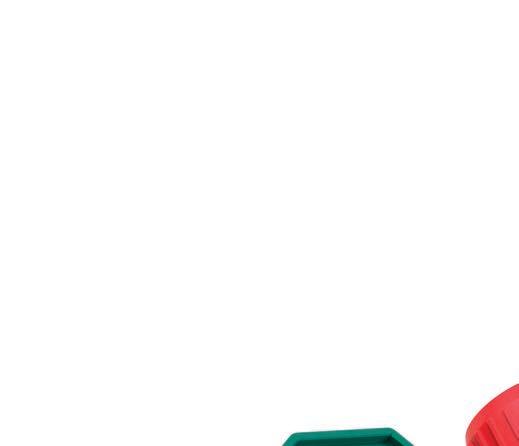
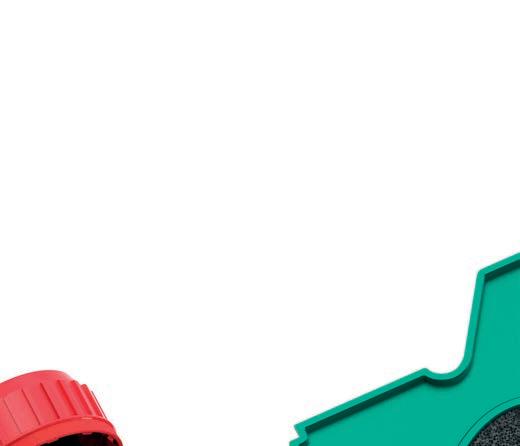
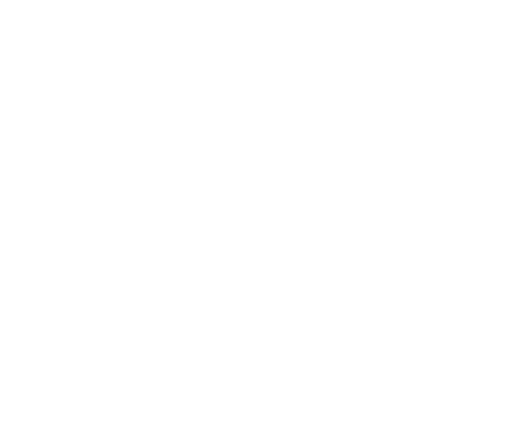

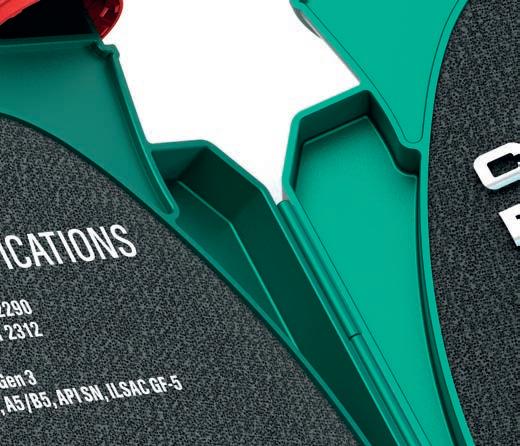
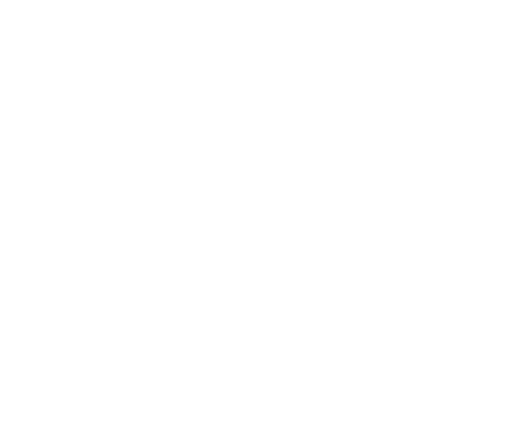
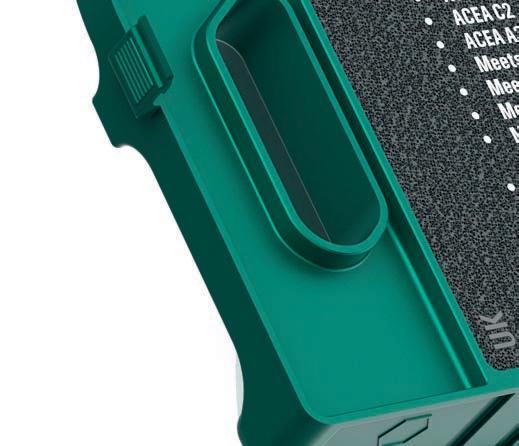
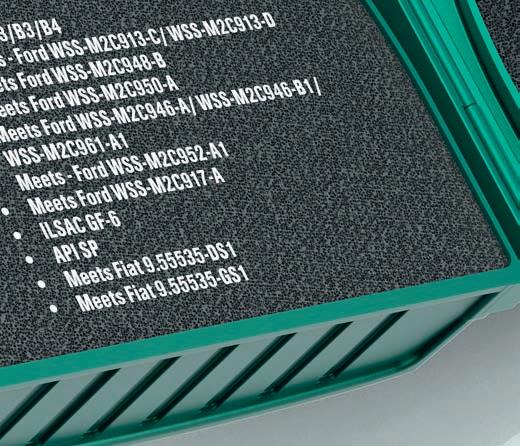
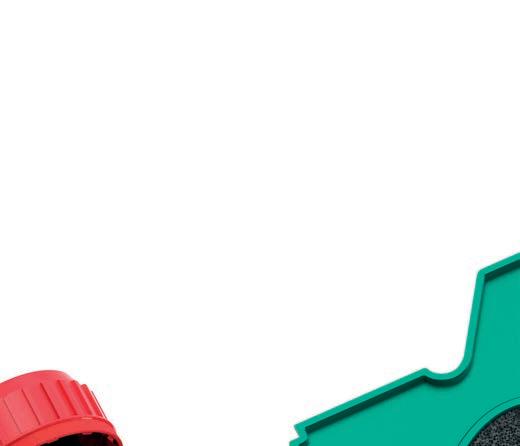
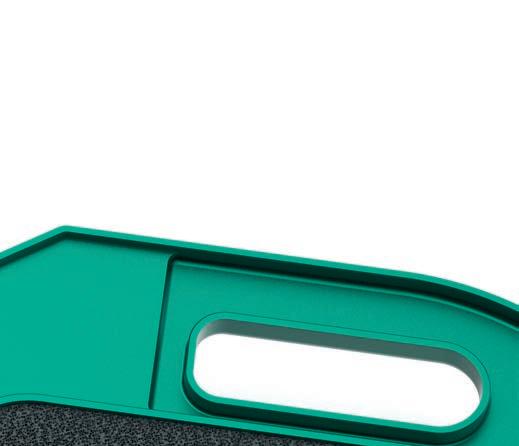
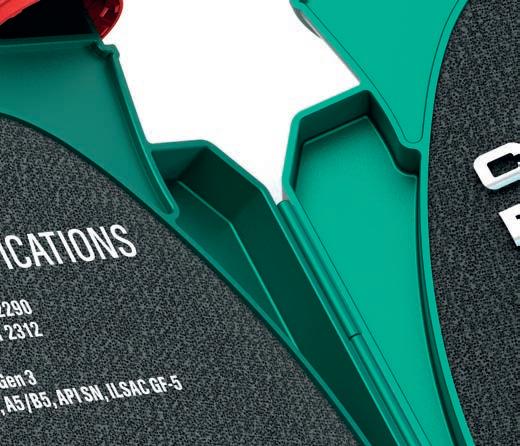
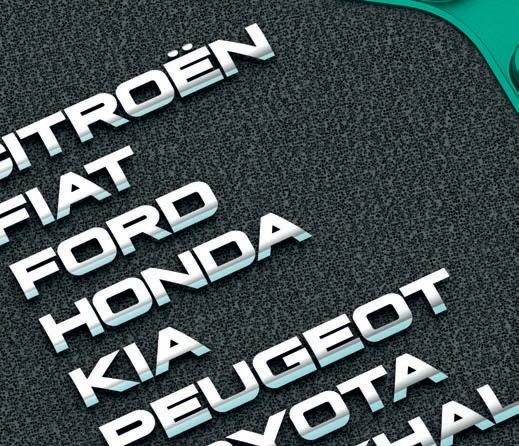
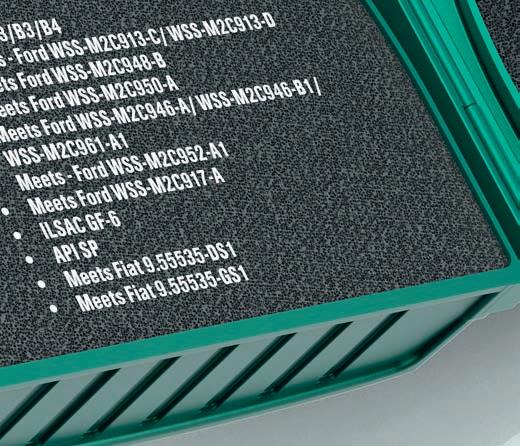
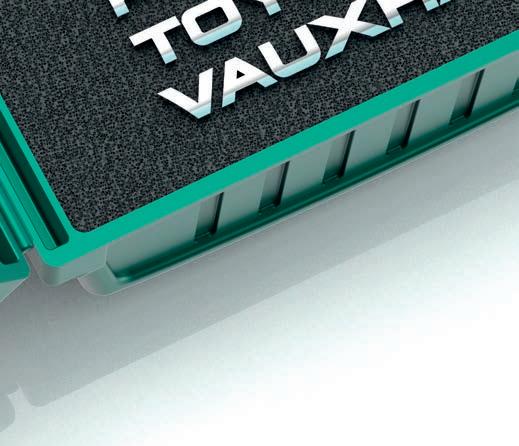
I listened to the customer issues and took the time to discuss how we could reach a mutually amicable position. We agreed to have the vehicle back in and carry out tests to try to understand how the symptoms were the same and provide an answer on what should be done to repair the issue. The customer was very sensible and relaxed about timescales, simply focused on the outcome of accurate diagnosis and recti cation of the issue. Furthermore, I had agreed I would spend as much time as needed, at my expense, to get to the route of the issue in testing charges. No pressure then!
I am sure we’ve all been in this position, xing a clear and present issue and being pleased the car is xed, only to nd, as Andy Crook describes, as peeling another layer from the onion. The heartache experienced by the customer of more problems and more expense magically then becomes your problem because the bit you xed was not it, or all of it. However it is dressed up, this phenomenon of the pressure being dialled up is a mental challenge that makes clear thinking and problem solving that much harder. Thankfully, unlike many customers who need their car back yesterday (I get it, it’s hard without wheels) this customer was magic and said they wouldn’t bother us, they’d hear from us when they hear from us – more of these please!
First port of call was to get the car into the workshop on the Friday afternoon in preparation for Monday morning. I wanted it to be in the workshop, in a position to connect any relevant tools and testing gear at the point at where the symptom occurs. What we were troubleshooting was a long crank, usually rst thing in the morning or when left for extended periods of rest. So, my point of testing to catch the fault is extremely limited and I needed to make any of the tests I did count before having to do something else, for a few hours at least. The tech in question was also on annual leave for a week too, so the job narrative from its previous visit was all I had to go on.
Over the weekend, I read up on what the previous garage had done in terms of repairs and part changes and exactly what had been carried out in our workshop prior to my involvement. According to the customer, the vehicle had been lled up with ‘bad’ fuel that he had acquired ‘on the cheap’. It had caused a mis re and poor running with EPC and engine management light on which took him to his normal garage. They conducted tests and had replaced the spark plugs, ignition coils and four fuel injectors. The bad fuel was drained o , fresh fuel added, and an oil service conducted. The car appeared to work well for a week until the engine management light returned – it went back to said garage for further tests and was booked in with us around this point.
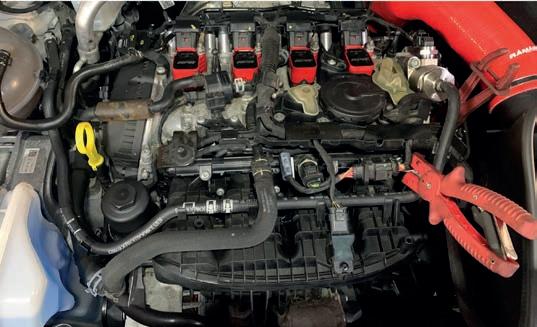
The vehicle was producing a DTC and engine management light but no mis ring at the point at which we rst saw the vehicle. The DTC being generated was P0087 – fuel pressure too low. It would take some time to return from clearing and pressure testing, including data logs, didn’t yield a huge number of clues to the problem area. The only anomaly found was with high fuel pressure being below the 50-bar required at idle, the scan tool reported a uctuating 43-46 bar. The technician removed the HPFP and found the spring and piston not to be quite square. This HPFP is driven o the camshaft on the engine, his theory being this could be a ecting that pressure reading. Before replacement, he straightened and lubricated the piston and re tted it. Coincidently, the pressure now resided at 50bar during idle testing and the actual and desired values when road testing under load showed almost identical in the logs. On this basis, and the bad fuel trauma, it was recommended to be replaced with a new genuine item. Not that it should matter as we try not to change parts because of whether they are common or not, but these pumps are fairly common on our brand base, noting that normal failure does display as a di erent failing symptom but similar DTC’s.
The repairs were actioned, and the same testing conducted after an overnight rest revealed no long crank and perfect performance, all appeared well.

Monday came, as it always does, and I had to begin my testing. Prior to leaving the car I had left the driver’s door open but with the catch rolled as a lot of modern cars give a pre-squirt from the low-pressure fuel pump when the car is unlocked or driver’s door is opened. I didn’t want this to skew any tests I was about to carry out or diminish the chance of catching and experiencing the symptom for myself. Symptom experienced with scan tool live data showed that there was virtually nothing to go on. A very small dip in pre supply pressure but the window of opportunity to catch the issue was so small before starting and running without issue was minimal, a few seconds or so.
Contemplating what test(s) could be carried out to try and expose or promote the failure was tricky. I found myself standing at the front of the car looking at the engine bay for inspiration. I decided to think about what could be causing the symptom, without a running or performance issue. The fuel delivery unit or low-pressure fuel pump has an integrated lter that is part of the pump assembly. I elected to remove the LPFP for inspection. At the bottom of the pump is a strainer and it was badly blocked. I couldn’t be sure this was from the bad fuel or just normal build up, either way I cleaned it, repressurised the system and opted to try it the next morning. Before trying it I also had my scope set up to evaluate the pump itself during pressure build up and normal operation. All of this checked out and the two tests carried out were checking the command from the controller (pulse width modulated) and the 3-phase pump. All was good, but sure enough, it faulted the next morning.
The next step was to evaluate the low-pressure fuel pump pressure build up and decay. I used an inline pressure gauge adapted to measure the pressure from the pump up to the engine bay, see Figure 1, previous page . What I noticed before attempting to crank it the next morning was that although ‘leak free’ I had no residual pressure on my gauge. I was not sure whether this was correct, but truthfully, I had expected to see some remaining pressure here. Sure enough, the gauge rose quickly to approx. 5 bar when the ignition was turned on and upon cranking, the car faulted again. Getting thin on ideas for this mysterious phenomenon I found myself staring at the engine compartment once again. I had failed to notice this later variant of the EA888 engine has two sets of injectors.
I pulled up one of the very useful VAG self-study programs (SSP’s) and read up on how this type of dual injector system works. I remember dual injection systems from back in the day when you were looking to extract big power from Ford Sierra Cosworth’s and the old Turbo Technics converted MK2 VW Golfs but hadn’t personally seen them to this point on this engine. If I had, I clearly wasn’t paying enough attention! With this in mind, I updated the customer with the relevant test ndings. I also queried which injectors were replaced. The group of injectors that had been replaced for mis res were the High-pressure injectors mounted in the cylinder head.
With pressure decay being at the forefront of my mind, given pressure generation had been proven on low- and highpressure fronts, I elected for a very crude test before going home for the day. I used a set of clamps on the low-pressure feed hose to rail supplying the plenum-based injectors, see Figure 2. All my other test equipment, including low pressure gauge was still in situ and I was keen to see the pressure reading on the gauge on my return the next morning. To my surprise it was still registering around half of the pressure (around 3 bar) on the gauge. Hmm I have a change here. With eyes tightly closed and techs for an audience I cranked the engine. To my amazement it started straight away, no long crank and no running problems. With these so called SRE injectors the last stop on this line I opted to set up a Columbo Test, of sorts.
I removed the clamp and ran the engine for a time. I then removed all xings securing the rail and injectors so I could remove them quickly and easily on my return in the morning. What I was able to prove is that the SRE injectors were working but leaking/decaying due to being faulty. Figure 3 shows wet injectors before the vehicle was even cranked, just ignition on and pre supply pressure built. With them removed, I was also able to see dampness on the piston crowns, which shouldn’t be there after a full 14 or so hours’ rest from combustion. The failure in this instance was only responsible for one perceived complaint and not other running issues and proved very tricky to accurately pin down. Having read the full SSP for this fuel injection system it's explainable and understandable how this fault could be overlooked and not revealed with average symptom-based testing.
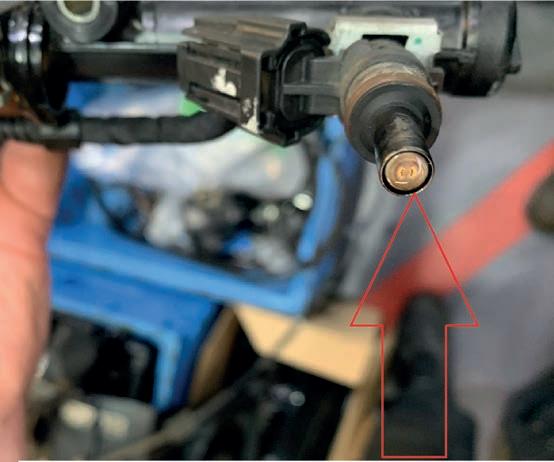
I submitted my ndings to the customer, and a repair was actioned. Follow up testing the next day revealed the symptom was cured and the test equipment still connected showed that full decay in the low-pressure system is not normal and some should be retained.
I was pleased to get to the bottom of the issue, but xing this particular fault raised questions as a technician and business owner. Did the original fault get xed with the HPFP and that’s why there was no return of P0087 DTC? Should I have discounted our diagnostic testing when the vehicle returned, was I obligated to or was I taking ownership for the customers car problems? It’s a di cult quandary and the mindsets of technician vs business owner play o against one another in situations like this.