
9 minute read
Advice from the Big Weekend
Big Weekend inspires guests to work smarter not harder
Trainers share the processes they have honed over the years to improve their first-time fix rate, to nurture customer trust and get paid accordingly
When you want to improve – whether it’s upskilling, increasing your financial health or striking a better work/life balance – one of the best ways to start is by surrounding yourself with people who share that desire, are committed to that same journey and who will lift you up. Those who attended the Big Weekend at Delphi Technologies did just that and were inspired by technician trainers who are also striving to improve their process and first-time fix rate, and have also specialised to futureproof and diversify their business. No-one can know everything but it’s those that turn up, evaluate their effectiveness regularly and encourage an open culture in the workshop to learn from mistakes without blame who will see big improvements.
The enthusiasm, humour, and honest presentations from each of the trainers were infectious and all guests – from those in their early twenties to those with decades of experience in the trade – left with a renewed vigour and a head or notebook full of ideas, tweaks and resources to use back at their own workshops. These tried and tested processes would help reduce time spent headscratching when faced with troublesome faults, improve relationships with customers and help workshops charge accordingly for their expertise.
For those of you who couldn’t make this year’s event, here are a few highlights...

Andy Crook uses an optical illusion to demonstrate that everyone has their own perspective and agenda - when managed, this can create better outcomes for both the technician and customer
Framing a problem
Andy Crook of GotBoost opened each day’s training with content taken from his 'Business of Diagnostics' course. We hope you will get to experience his sessions in the future as he delivers an incredible amount of valuable, practical guidance relevant to both technicians and workshop owners. Congratulations to Mr Crook as he received news at the event that he had been accepted to begin a PHD where he will be looking to create an aviation engine that can be powered by Hydrogen! But back down to earth with vehicle faults, he first considered how to frame a problem and asked guests to consider the three perspectives of the customer, the technician and the person front-of-house when faced with an engine light that has switched on. The first feels panic and only cares about how much it will cost to fix and how long it will take. The technician has a mindset of ‘I must fix this’ and wants to be efficient, with front-of-house focussing on securing the booking and being effective. As technicians are under pressure to get an answer, it is tempting to find shortcuts and make assumptions, but Andy says workshops should build a system and follow processes to avoid pitfalls. The following steps should be taken:
1. Primary data capture 2. Communicate our offer 3. Deal or no deal (must be a win-win) 4. Take payment.
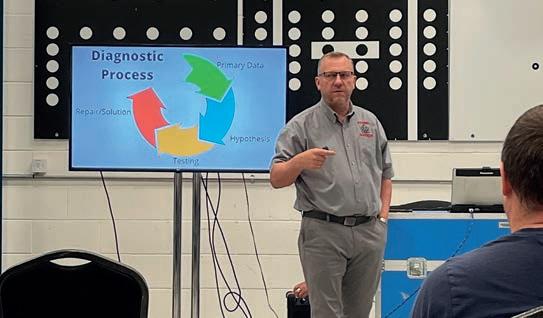
The primary data capture is all important
When communicating your offer to customers, Andy says the four Cs should be followed: The CONTRACT should be clear to both parties; Agree on when and how to COMMUNICATE, COUNT – agree on a budget for repairs; CONSENSUS – deal or no deal? When the contract is agreed, Andy books in the initial diagnostic assessment and takes payment for it there and then (and when he books in re-maps) and says that customers who do not like this are the types of customers he doesn’t want.
One big takeaway from his first talk – when good customers want to get an approximate idea of cost for an MOT and any subsequent repairs, he will explain the average MOT bill is say £200 and ask if they are happy to preauthorise up to this amount. He has also given customers an average repair bill of £500 and average repair time of four days to some good customers, removing the need for pre-approval at every step.
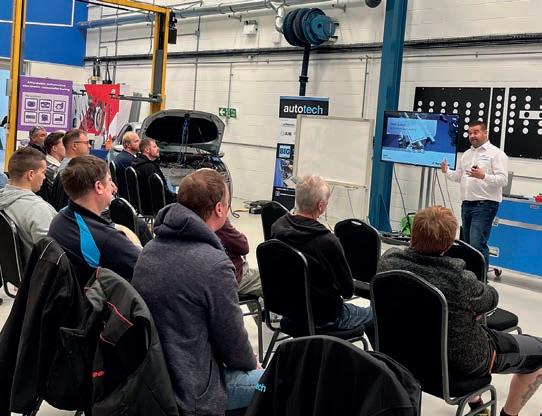
Delphi's Phil Mitchell discussing diesel injectors and coding
The Killer Test
Andy’s second session focussed on closing the loop. He suggested following a script to collect vital initial information and when you think they have offered up everything, asking the customer ‘Is there anything else?’ This has paid dividends time and time again at GotBoost, providing a clue that could have easily been missed out by the customer. Talking of clues, he urged attendees to use the Columbo Test (“Just one more thing”) when you believe you have the faulty part in your sights. Ask yourself if the part you are about to t doesn’t fix the car, what will you do then? You could run a simulation, run the monitors, just one more test… to prevent that engine light coming back on.
Live case study
This was only the second time that autotechnician contributor and VAG specialist Gareth Davies had ever hosted a training session and his comprehensive presentation did not disappoint. He conducted 5V reference troubleshooting in his first session, to help build a robust process when faced with these often-intermittent faults that provide weird and wonderful symptoms. Fault code PO641 Sensor reference A open circuit was present on a 2010 VW Polo 1.2 TDi and with the help of the crowd, he gathered initial data using Autodata and Alldata. He advised to take guided fault- finding with a pinch of salt as they would commit you to go down certain paths depending on the validity of the answers you input into them.
Gareth’s second session focussed on interpreting live data and signals, again presenting evidence from case studies within his workshop. He guided the technicians through a ‘dreaded diagnostic job’ where there was no DTC present, but the vehicle was performing too many regenerations.
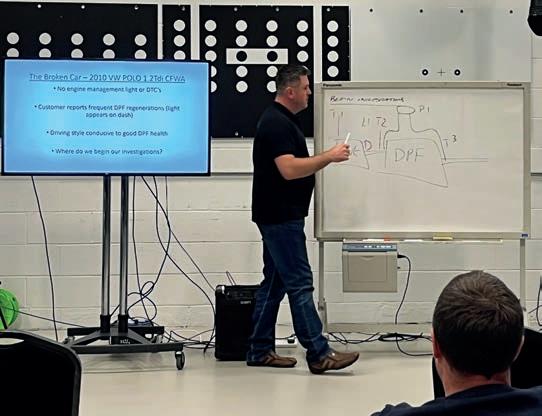
VAG specialist Gareth Davies presents a real case study of a vehicle that has too many regenerations but there's no DTC present
Top tip – Use Control F when trying to find a search term on reference sources rather than scanning through reams of data!
Gareth will provide another meaty case study for readers in the next issue of autotechnician.
TECHNICAL TIPS
In addition to the main presentations, sponsors provided a few technical tips and a heads up on new technology within the workshop and during the networking lunch. febi’s Technical Manager Charles Figgins considered the science of NVH and the need for quality parts to ensure NVH countermeasures are not impaired. When diagnosing problems, Charles stressed the importance of getting as much detail from the customer on what happens and when, ideally heading out on a road test with them to analyse the issue. Delphi’s Phil Mitchell provided an insight into coding and how injectors are controlled. He also gave guests a sneak peek into the development of Hydrogen ICE – injection systems redeveloped to be powered by hydrogen. Darren Lloyd, ZF’s Technical Training Manager, gave advice on automatic transmissions, suggesting oil changes should take place no later than 96,000 miles or as it enters your workshop if its past is unknown or has had high load or use. There are still some places left on ZF's transmission course running on 23rd November, email protech.zf-aftermarket@zf.com.
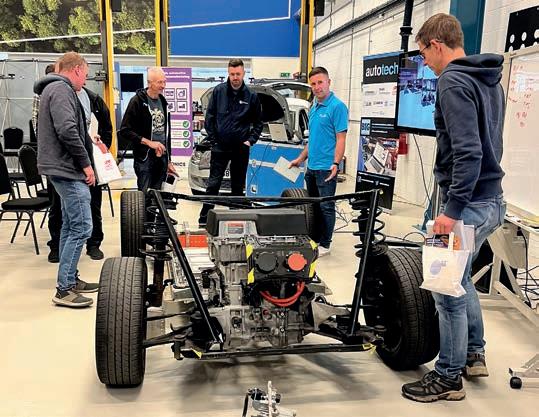
Matt Cleevely presents his FrankenLeaf!
The electric trailblazers pave the way for newcomers
Having not been able to join us in person last year due to coming down with Covid, (he managed to film a fevered video message) Matt Cleevely was ring on all cylinders (or should we say fully charged) at the Big Weekend accompanied by his FrankenLeaf – which shows all the HV components of a Nissan Leaf. Matt has been repairing cars for 26 years and moved into EV repair after buying a Leaf. Cleevely EV is a specialist sister company of Cleevely Motors that sees customers travel far and wide for their expertise. He came to the Big Weekend to dispel some myths, highlight ways of diversifying (becoming a battery specialist, EV sales, parts supply) and to show how a move into this growing sector can put you a step ahead of your competitors and keep your passion in vehicle technology alive! He stated that 95% of the work they undertake on EVs is not related to the high voltage components, it is still just a car that needs steering & suspension, brakes, tyres and mechanical fixes. “There’s a huge opportunity to get this jump on the main dealers who aren’t prepared to take a risk and give it a go.”
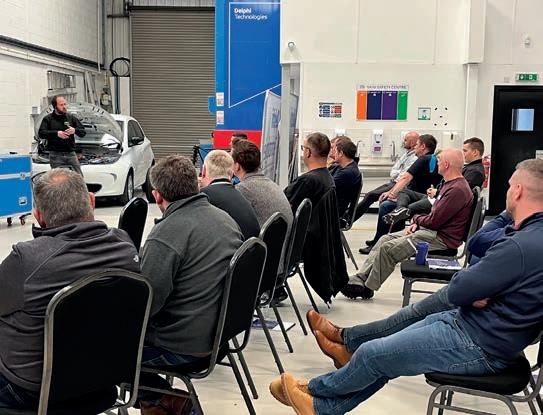
Pete Melville of HEVRA guides technicians through diagnosing a Renault Zoe fault
Matt explained how HEVRA’s technical support is an invaluable resource for his workshop and founder Pete Melville got the technicians at the event to suggest tests and the plan of action when faced with a fault code on a Renault Zoe. Pete guided them through the diagnostic process, explaining the HV components and systems along the way.
autotechnician visits Cleevely EV and talks to HEVRA within in a special Hybrid & EV feature in the November issue.
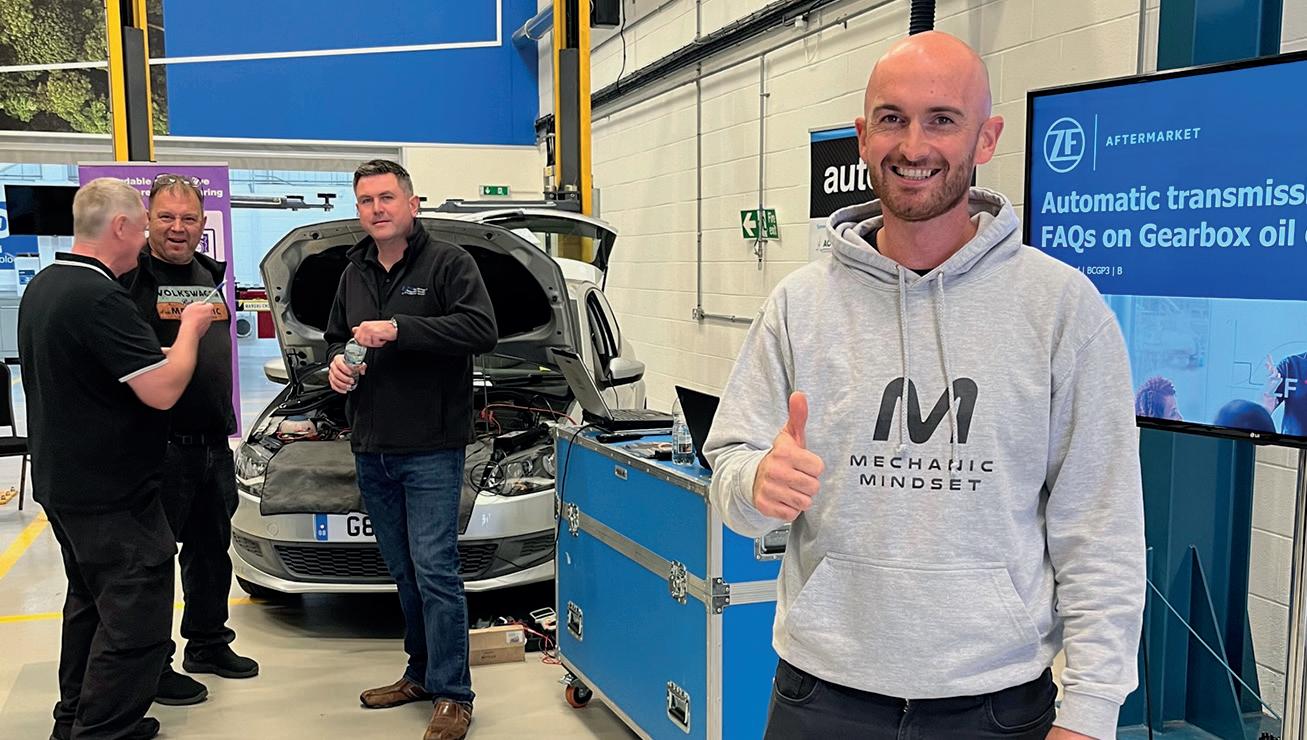
Darren of Mechanic Mindset gives the presentations a big thumbs up!
Last, but not least…
When you are in the fortunate position of working with such a supportive, friendly team, it doesn’t feel much like work. Thank you to all our trainers who put so much effort into delivering thought-provoking sessions and to our wonderful hosts at Delphi Technologies. autotechnician would also like to thank each of the sponsors who took the time to network with guests over the Big Weekend, to our amazing caterer Gemma (www.foodtasticcatering.co.uk) who made sure we were all well fed and to the great bunch of technicians who took time out of their busy workshops to invest in their livelihoods. It was a pleasure, until next time…
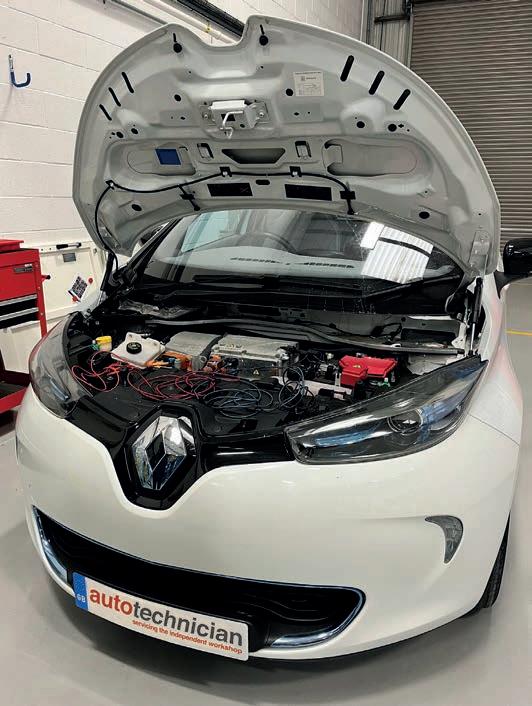