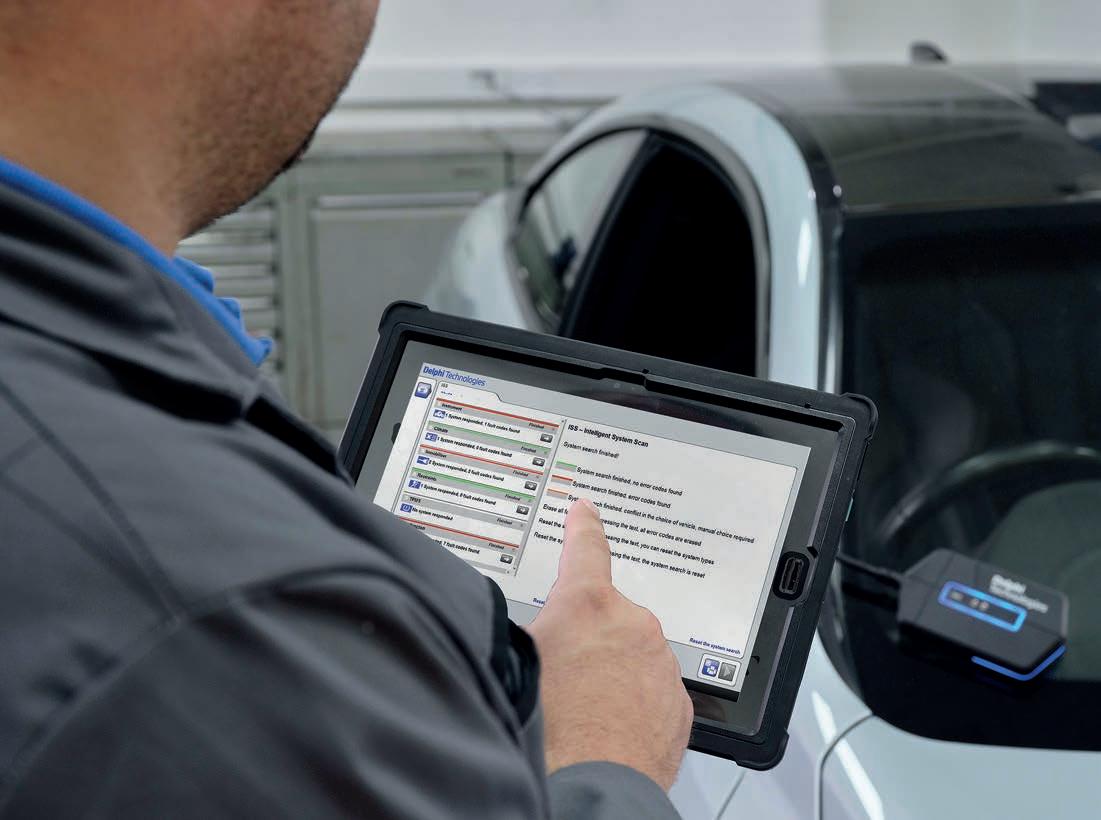
22 minute read
Diagnostic tooling
Delphi’s latest diagnostic tools include access to e-learning
Delphi Technologies, makers of the pioneering Bluetech VCI diagnostic unit, has added extra functionality to its diagnostic tooling to enable ‘on the job’ training using customised, remote e-learning.
Delphi Technologies’ diagnostic tooling is supplied with car and light commercial vehicle diagnostic software, providing access to in-depth, up-to-date diagnostics and advanced technical information for a comprehensive range of makes and models.
The interface is designed to be easy to use and provides fast and accurate diagnostics of key vehicle systems. Key functions include:
• Ability to read and erase fault codes
• Recode/activate components and reset service lights
Build your CPD credits
In addition, it has integrated its e-learning within the diagnostic tool software. This means techs can capture and absorb the key principles of diagnostic operation without leaving the workshop. The e-learning modules contribute to Institute of Motor Industry (IMI) Continuing Professional Development (CPD) accreditation, with the ve sections worth 1.5 CPD credits. The IMI development path encourages techs to accumulate 30 credits over the period of 12 months.
The rst stage of diagnostic tool e-learning is an introductory lesson, detailing the setup requirements for Delphi’s diagnostic equipment, which ensure a stable, reliable operation for fault- nding and calibration activities. Stage 2 details EOBD (European On-Board Diagnostics) principles and operation. EOBD enables emission system tests, ‘freeze-frame’ data and fault code assistance, all of which are critical to tracing all-toocommon faults like faulty diesel particulate lters on modern diesel vehicles.
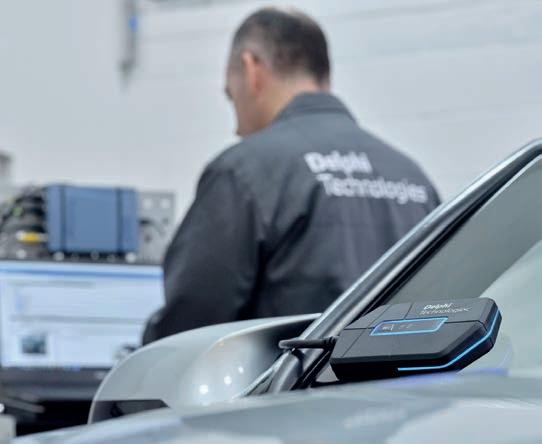
searching to correctly identify engine types and their technical requirements (such as oil type). The nal, fourth section coaches in the fundamentals of diagnostic protocols and Intelligent System Identi cation (ISI). This section also explains the use of a data logger to track sensor outputs and measure system performance, alongside the creation of calibration certi cates.
Delphi Technologies’ diagnostic tool e-learning concludes with an end test, to ensure an appropriate understanding, before awarding the 1.5 CPD credits. Luke Garratt, Technical Services Manager, says: “We recognise the value of technicians’ time, so our latest addition to DS software is an easy-to-use portal to e-learning. There is nothing more frustrating than having the hardware without the requisite knowledge to perform a task, so Delphi Technologies’ diagnostic tooling now incorporates e-learning to support techs wanting to learn on-the- y.”
“The IMI CPD credits earned during these Delphi Technologies e-learning courses help develop technicians’ careers. Ultimately our diagnostic tool range is a one-stop shop for contemporary vehicle diagnostics, covering routine service jobs to advanced fault- nding on newer, sophisticated electronic systems.”
Reader review
We spoke to Andy Marsden, owner of Stonegate Garage in Hunmanby, North Yorkshire, who runs an independent, familyowned village garage that’s been trading for over 26 years. Andy’s team of technicians have always used Delphi tooling so it was a natural progression to the Bluetech VCI diagnostic unit, obtained through York Motor Factors two months ago. “It ticks all the boxes and does everything we need it to do – service lights, regens, resets... code reading being the main one.” Andy is keen to get his team using the eLearning element when they are a little less busy.
www.delphiautoparts.com/gbr/en/product/bluetech-vcidiagnostics
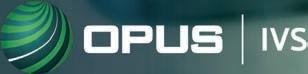
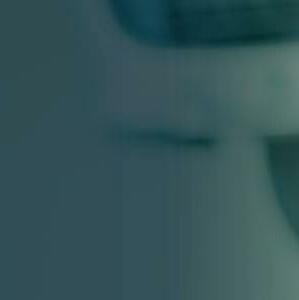
CORRECT CORRECT REPAIRS REPAIRS THE FIRST TIME THEFIRSTTIME
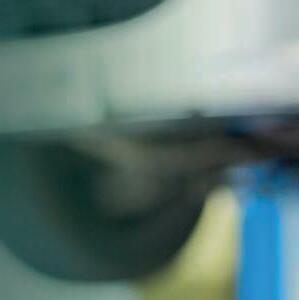
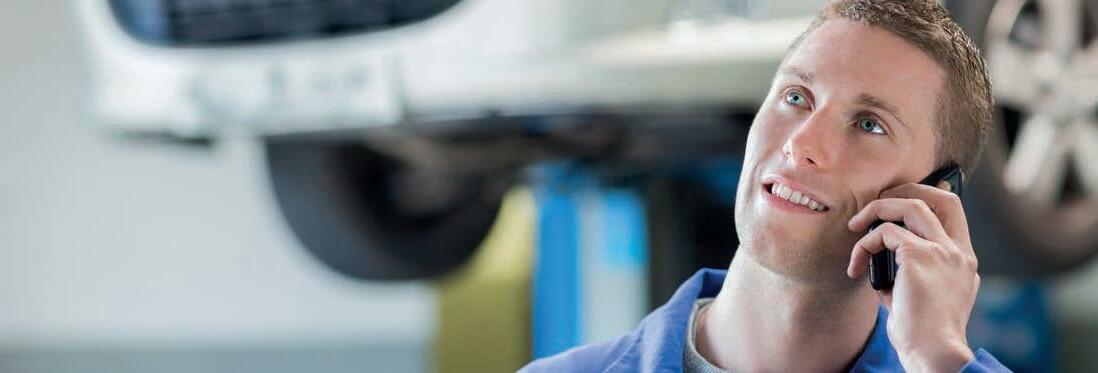


Failuretodiagnosevehiclesquicklyandcorrectlyreduces profitabilityandlosesyourworkshopvaluablecustomers! UsingtheDrivePro EliteDiagnosticKitcoupledwith IVS360 yourtechnicianscantapintoapoolofbehindthe TM scenesexpertisefor quick complexdiagnosisandrepairs,
correctlythefirsttime! AccessIVS360 DirectlyFromDrivePro! TM
TM
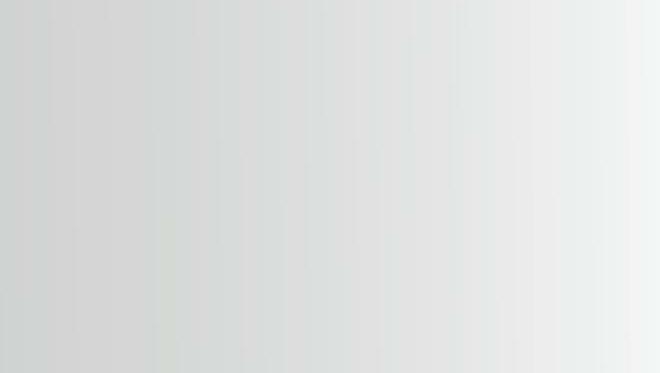
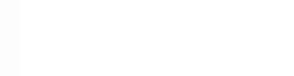
✔ Unlimited –Nosupportrequestlimits,andyourwholeworkshophasunlimitedaccess! ✔ On-demand –RequestsupportfromourOE-certifiedMasterTechnicianswhenyouneedit! ✔ Savetime –Nomoresendingjobstodealers,orwastingtimeGooglingrepairs!
SCHEDULEADEMO

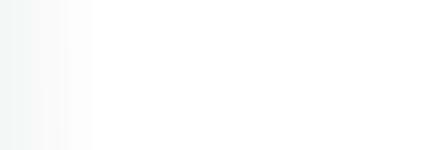
sales-uk@opusivs.com 44(0)1865870060 opusivs-uk.com
Tools that keep tasks in-house
autotechnician discovers the range of diagnostic tools available from TopDon
TopDon’s range of diagnostic tools provide varying levels of functions, ranging from the Phoenix Lite 2 entry tool, which is useful when servicing and frees up the main diagnostic tool, the Phoenix Elite, which includes ADAS capabilities and enables online coding and programming for six manufacturers for an investment of £1,695, up to the top of the range Phoenix Smart and Phoenix Max – its two most popular tools. The Phoenix Max includes a 4-channel oscilloscope, ADAS compatibility, and Topology Mapping. It provides the ability to reprogramme ECUs and replacement modules on 14 vehicle brands. TopDon also supplies an ADAS solution in the form of the Phoenix Mobile ADAS, a foldable calibration frame. TopDon states these tools unlock huge potential for independent workshops, keeping tasks in-house rather than lining the pockets of local dealerships and stalling the job.
Its latest tool, Phoenix Remote, is a new take on all-make vehicle diagnostic tools and is now available to pre-order. It has a vehicle database of over 200 vehicle brands for local diagnostics and also o ers a Remote diagnostics Pay-bysession platform – allowing workshops to reduce vehicle key-to-key repair times and the amount of work that is subcontracted to local specialists or dealerships.
It is mounted within a powerful Android 10 rugged tablet, boasting a 12000mah Battery and 128GB HDD, alongside a Quad-core 2Ghz processor. Unlike other all-make diagnostic tools, the Phoenix Remote does not come with a wireless VCI, eliminating any possible disconnection issues and allowing the tool to charge the battery directly from the vehicle's OBD port.
The Local diagnostics within the TOPDON Phoenix Remote includes Cloud Based Programming and online coding for 14 Vehicle brands. These include VW, Seat, Skoda, Audi, Porsche, Mercedes, BMW, Nissan, Renault, In niti, Jaguar Land Rover, Hyundai and Subaru. All the latest vehicle protocols are also covered, including CAN-FD, RP1210 & DoIP.
The Remote service is provided by Auto Diagnostic Support, based in Poole – a team of experienced technicians alongside a vast level of Genuine Manufacturer and all-makes diagnostic equipment. Create a Remote session booking using your Phoenix Remote tool and once the booking is picked up by an ADS technician, a communication window is opened, allowing you to chat directly and give as much detail as they require to complete the job successfully.
Once connected to the vehicle, the ADS technician can use any OBD diagnostics equipment remotely to access the vehicle in your workshop – whether you need a control module programmed, software updates, VAG component protection removal or just help to diagnose a problem you are struggling
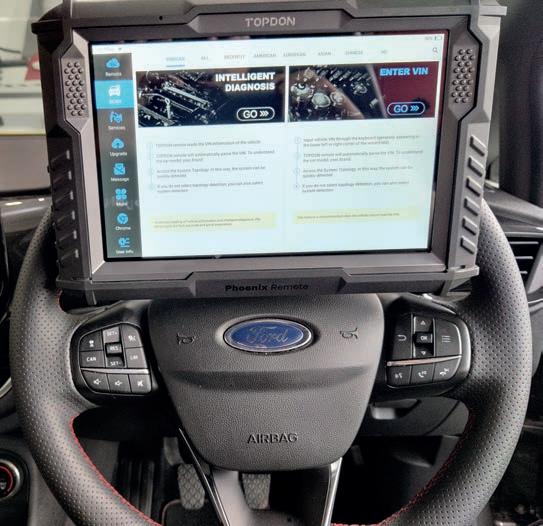
The Phoenix Remote tool is now available to pre-order, providing workshops with remote functions, such as dealer tool coding
with. Continuous communication is essential whilst any diagnostic functions are being carried out as this will more than likely include physical actions to be performed during the process, such as switching the ignition of the vehicle on and o .
Pricing per remote function varies per job, depending on the steps, process and tooling required to complete the job successfully.
In addition to Remote diagnostics, users are able to utilise ADS knowledge and equipment to check for fault guidance, suggested solutions and technical service bulletins provided by vehicle manufacturers.
www.topdondiagnostics.co.uk/phoenix-remote
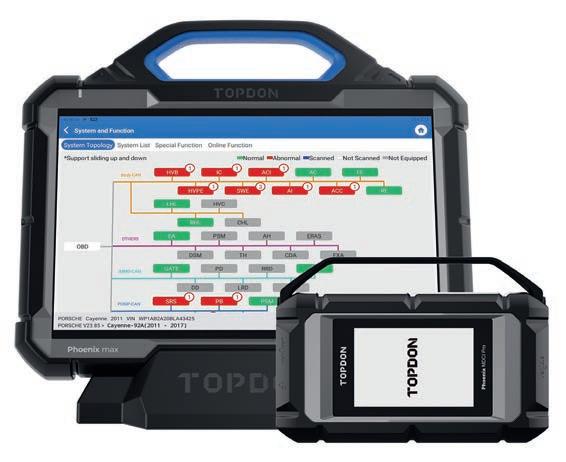

Access to secured vehicle data
A number of vehicles now require a manufacturer-speci c access authorisation in order to perform active diagnostic tasks, such as the calibration of driver assistance systems or resetting of service noti cations. This can present most independent workshops with some serious problems. To overcome this, Bosch has developed Bosch Secure Diagnostic Access (SDA) which provides access to securityprotected diagnostic contents using ESI[tronic] diagnostic software.
Since August 2021, workshops using ESI[tronic] 2.0 Online, combined with a license for Control Unit Diagnosis, are able to access protected electronic systems of several vehicles produced by the Volkswagen group via SDA. Bosch SDA meets the requirements of the current security level for tasks on vehicles produced by the VW group. Ever since the ESI[tronic] 2.0 Online and KTS 250 software updates released earlier this year, users can now also use SDA to access protected vehicle data of Fiat, Alfa Romeo, Lancia, Abarth, Chrysler, Jeep and Dodge/RAM vehicles, plus Mercedes-Benz vehicles. The company is working closely with the development departments of additional vehicle manufacturers in order to expand the access possibilities via SDA.
Personal Bosch ID
subscription. To use Secure Diagnostic Access, members of workshop sta need to create a personal free-of-charge Bosch ID consisting of an e-mail address and a self-chosen password. Once registered, they will be granted access to all protected diagnostic data.
To access protected data of Mercedes-Benz vehicles, an additional process step called User Identi cation for two factor authentication (2FA) is required, besides creating a Bosch ID.
Explanations and hints
There are two ways of accessing SDA via ESI[tronic] workshop software. Users can activate the SDA access within ESI[tronic] right at the beginning of their diagnosis using their Bosch ID. ESI[tronic] also informs users: Once the vehicle is connected for diagnostic purposes, ESI[tronic] opens a pop-up window pointing out that the respective vehicle is equipped with a protected electronic system. By means of a link, users can also access the SDA Help Center providing additional support. It contains important information concerning topics related to Secure Diagnostic Access, such as frequently asked questions as well as explanatory images and videos.
A prerequisite for the use of Bosch Secure Diagnostic Access is ESI[tronic] 2.0 Online diagnostic software and a valid license for Control Unit Diagnosis, as well as a stable internet connection. A diagnostic tester of the current Bosch KTS generation – such as KTS 590, KTS 560, KTS 350 or KTS 250 – is also required.
RELIABLE DIAGNOSTIC SOLUTIONS
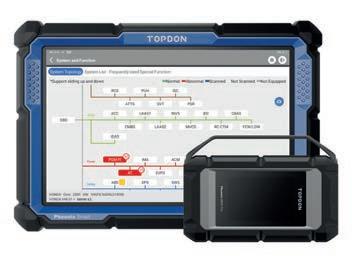
Phoenix Lite 2 £850+VAT
Your workshops go-to for fast service functionality
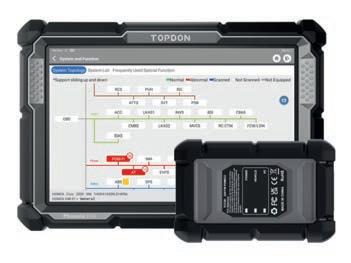
Phoenix Elite £1695+VAT
Featuring Cloud based Programming for 6 Brands & vast vehicle diagnostic coverage
Phoenix Smart £2250+VAT
Cloud based Programming for 14 Brands & Latest Protocol functionality
Phoenix MAX £3495+VAT
Same Smart capabilities, but a huge hardware upgrade including 4 channel oscilloscope
Phoenix Remote £44.95+VAT
Per week or £2700+vat outright Diagnostics Without Boundaries – 14 Brands of in house, cloud based Programming with the addition of Remote Diagnostics Specialists for those ‘dealer only diagnostics’ jobs.
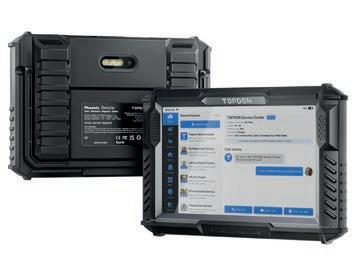
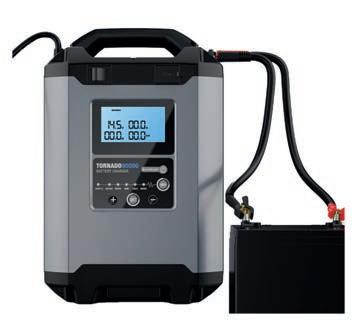
Tornado 90000 £595+VAT
Reliable, Smart and Affordable Battery support for all your diagnostic needs

Pushing the envelope
autotechnician talks to Andy Brooke, Managing Director of Wrexham-based Maverick Diagnostics, to nd out how they are supporting workshops who want to futureproof their diagnostics
“We are the only company in the UK that currently o ers an end-to-end solution for OEM diagnostics for the life of the tool. We not only help workshops register, but we also check out their prerequisites before registering with the OEM. We have a real inside track to this because I work with UK AFCAR and the IAAF in an advisory capacity, providing feedback when we have problems with manufacturers. If you are an independent workshop who wants to work with OE tools, we can advise you on what manufacturers are going to be possible and what ones are going to be possible in the future. We're trying to futureproof your workshop, to ensure that you're going to earn money into the future and we're going to make sure you're fully supported.
“Aftermarket tools are all well and good – I have been developing and designing aftermarket tools for many years and I still do; we have some tools that will come out through Maverick next year. We understand the reverse engineering side of the tools, but here's the problem – you can't currently keep up, by the time you've reversed engineered that tool it is out of date. The manufacturers change the tool protocols and add new chassis numbers to it every single day. So realistically, the very best aftermarket tool will not have security
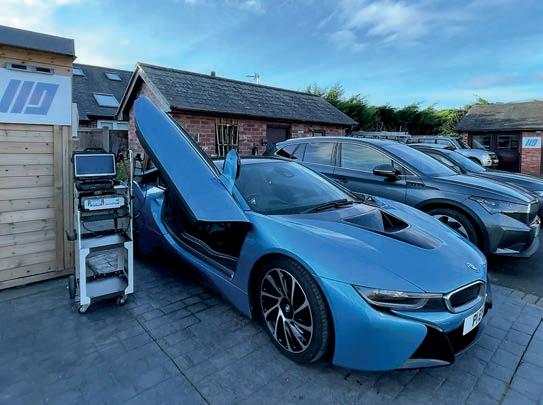
Maverick boasts that it has just introduced the world's rst full OEM level Tesla diagnostic tool, enabling the diagnostics, repair and con guration of Tesla vehicles. A 2-day remote training course is provided with this kit.
LOKI provides Live Data from CAN, will read & clear alerts, self-test & calibrate. It comes with free regular software updates to stay up-to-date with the latest Tesla version. Free technical support and the latest information is supplied via a Telegram support group.
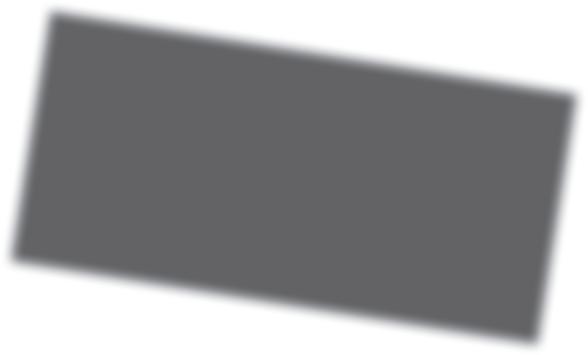
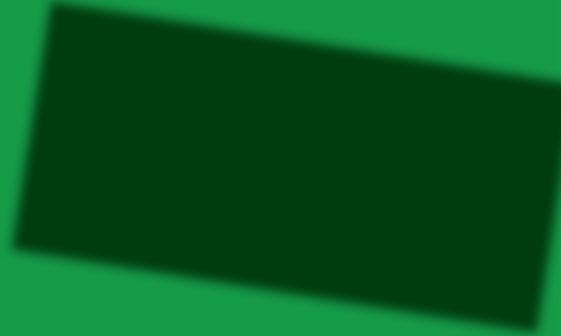
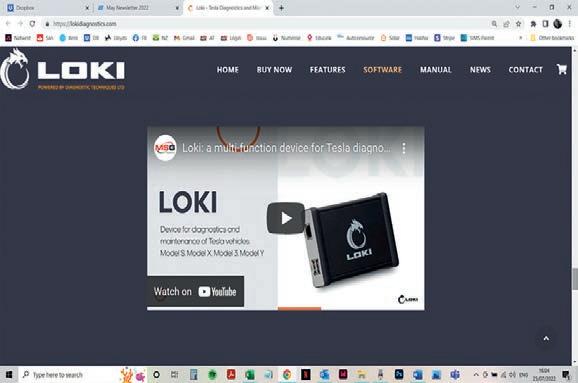
access, particularly after August 1st 2023, because that's when SERMI comes in" [a scheme for accreditation, approval and authorization to access security-related repair and maintenance information].
Could remote diagnostics be the answer?
"If you read the manufacturer's prerequisites, it says that you cannot carry out remote diagnosis. It’s actually illegal because you are, by security terms, not the technician who is working on the vehicle. So realistically, what they want you to do, what they're going to try and force through SERMI, is to have everybody with their own OE tool and they're own OE login. So, unfortunately, it does push the future into OE, which is actually ten times more complex than using an aftermarket tool. This then pushes the market into specialisation. This is something we've realised for a number of years, but we have an end-to-end solution to help those customers that want to move down that route, and Maverick has got a proven track record that's been going for 23 years this year.
What dealer tools do you supply?
“Pretty much all of them, there's really nothing we do not cover. Some of them are really a ordable; the average cost of the majority of them is between three/three and a half thousand pounds and that includes your registration set-up and an OE tablet. Unfortunately, ones like Renault, Nissan, Kia, Hyundai have nailed it down, so you have to pay around seven and a half/eight grand for a kit.
Can you tell us about TechSuite?
"When you have an OE tool, if you're in the dealership, you have somebody there who can support your IT. When it needs an update, a lot of the time, it actually just stops working. Now it may take you four or ve hours to reload and upload that system. It's not a small programme, it could be 100 gig of les on there. We charge a small monthly fee, and we'll do however many is needed a month on that tool, which saves the workshop a lot of time. We also provide dealer tool support as well as technical support. We also have online training, and we recently opened our Automotive Training Academy."
The Maverick Automotive Training Academy in Wrexham delivers a suite of IMI Hybrid & EV courses from levels one to four and will also provide OE training courses in the near future. Visit www.maverickdiagnostics.com/academy for more information.
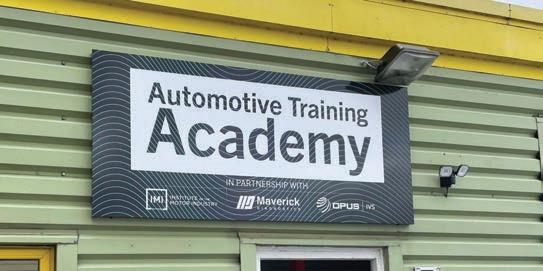
Maverick's new Autotmotive Training Academy in Wrexham provides Hybrid & EV courses Level one to four Technical support & training
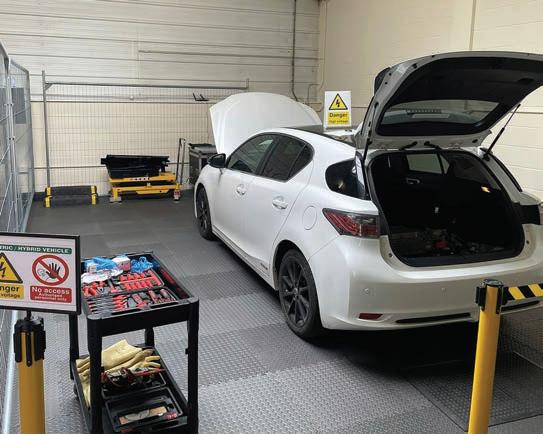
For less than £6.50 a day, TechSuite provides access to tailored support packages – 70 live Master Technicians, training, dealer tool support & IT support.
The Maverick Diagnostics Vehicle Technical Support (VTS) ticketed system includes unlimited use of an online portal detailing known xes; OEM Tool Software Support with Maverick Help Desk and a suite of 26 e-learning courses recognised by the IMI. Within the Maverick Academy Online, you’ll also nd skills tests to motivate and guide student learning.
DIAGNOSTICS
The APOLLO-D9 has landed
The APOLLO-D9 from Snap-on Diagnostics is designed to withstand the rigours of the workshop environment and features a fourway thumb pad for quick navigation, a 9" colour touchscreen display, and 5 GHz wireless compatibility for more productivity in the garage.
Designed to help users get answers faster, experience-based software lters out unnecessary information. ’Intelligent Diagnostics’ on the APOLLO-D9 is said to simplify your work ow, with SureTrack delivering veri ed parts replacement records and ‘Real Fixes’ — along with Smart Data for relevant vehicle and code-speci c PIDs, and access to pre ltered functional tests to verify repairs.
To reduce the amount of time switching back and forth between resources to nd information you need, the tool o ers advanced graphing features and OEM-level data, with up to eight live data parameters onscreen at a time.
Tool features
Quick Access Menu
Ability to switch quickly between functions at any time — without having to go back to the start of the process.
Code Scan and Code Clear
Fast code scans with a complete overview of the vehicle and its history for fast fault diagnosis and work ow organization; “Clear All Codes” lets you quickly nish the repair.
Pre and Post-Scan Capability
Faster approvals, histories, repairs, and payments — with reports (including speci c ADAS calibration reports) that help you build customer con dence.
Product Support
The APOLLO-D9 comes with Snap-on Customer Care, plus 24/7 online training and support, online training, exible nancing, and exclusive access to the Snap-on Cloud, where you can save, sort, and share pre/post scan and ADAS calibration reports.
A subscription programme provides regularly scheduled software upgrades, and the ability to self-download these, and full access to the Intelligent Diagnostics features to ensure that your diagnostic tool continuously provides the most up-to-date data and information, whilst saving up to 30% on the software costs. Online training and support is available at http://diagnostics.snapon.com/trainingsolutions.
Reader reviews

Colin Shea, owner of Wellesley Service Station in Clactonon-Sea, invested in the APOLLO-D9 around two months ago. He told AT: “We’ve always used Snap-on and it just does everything we need, it’s a brilliant bit of kit.” Colin and his team have found it very easy to use, so much so, that they felt they didn’t need to do the product training as they quickly learnt its functions on the job. “We’re quite involved in diagnostics, most days we’ll use it – we use the graphing a lot for the waveforms, resistances and so on. We’ve had to contact the support team a couple of times, but the helpline is fantastic.”
Colin says that the return on investment has been quickly realised, he explains: “We charge customers a diagnostic fee and it makes things so much easier. We normally charge customers £25 plus VAT and if they have the work done, we’ll deduct that from the price of the job.” They print out the fault codes and any initial ndings, which they nd a useful tool when explaining issues with the customer.
Chris Venni upgraded to the APOLLO-D9 from the SOLUS in the past month as he was interested in the guided fault- nding function. Chris told AT: “I’ve used the Intelligent Diagnostics on injector and airbag issues, DPF problems… So, the rst thing I’d look at is the error code and when you go into that, you can see other people who have seen the same one and it provides quick things to check on that error code, such as a blocked injector, fuel pipe issue, a wiring issue, and it helps you quickly work out where the problem actually lies. I would say it has been accurate a good 95% of the time. It will give you a graph of the most common solved problems in that area – it does save a lot of time. I used to take around 45 minutes to do the same thing with the older machine, I’m now down to 15-20 minutes.”
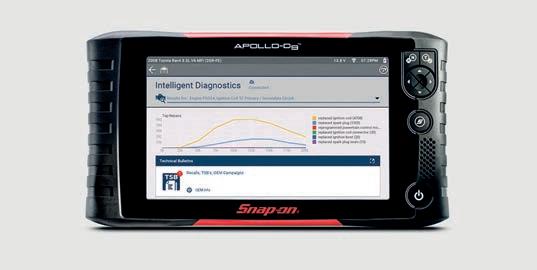
Opus-IVS Case study – KCAN2 failure
By BMW Master Support Technician, Simon Tyrrell CAE AMIMI
Vehicle: BMW F11 520D 2015
Customer complaint: Vehicle electrical systems misbehaving. Various warning message appearing, and instrument cluster had a mind of its own. Plus, the radio could not be turned o .
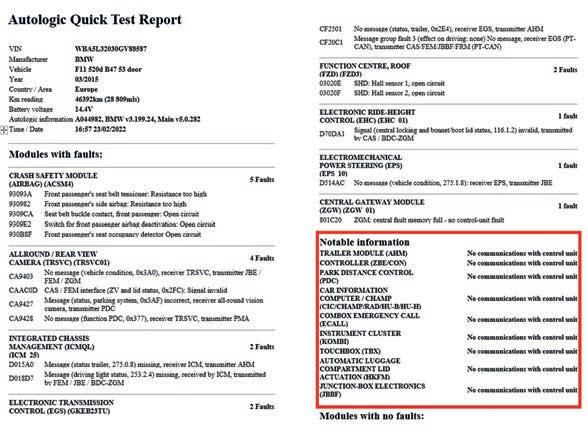
Figure 1.
After receiving the support request, the BMW Master technician opened up the quick test to look for clues as to the cause of the customer complaint. The quick test report, see Figure 1, showed that a large group of control units were not communicating. Before calling the customer to discuss further, the Master Support Technician looked for a link between all of the control units.
Using their years of experience, the Master Support Technician noticed that the AHM (trailer module) was one of the control units not communicating. A quick check on the wiring diagram for the AHM control unit power supply showed that the AHM was connected to the KCAN2 body network. He then proceeded to look up the KCAN2 complete circuit diagram and noticed that all of the other control units that were shown as not communicating were also part of the KCAN2 Circuit. Armed with this information, he called the customer and began the diagnostic process.
The AHM is located in the rear right of the boot, is low down and can su er from water ingress. When guided to the AHM, the mechanic working on the car said the AHM was ne and dry. As we were here already, this was the best place to actually check the K-CAN2 circuit.
What is K-CAN?
The Support Technician then described what K-CAN is and how we can test it.
K-CAN2 is a high-speed body bus/CAN network. It has two wires for data transmission – a high side and a low side. The high side has an approximate signal voltage of 2.6V and the low side approximately 2.4V This is because the base voltage for both signals is 2.5V, the high will switch up to 3.5V and the low down to 1.5V. When testing, we see the average voltage, see Figure 2.
As it is a high-speed circuit with a 500kb/s data transfer rate, there are two terminating resisters tted at either ends of the circuit, these are connected in parallel and are each around 120 Ohms – this gives a total circuit resistance of approx. 60 Ohms.
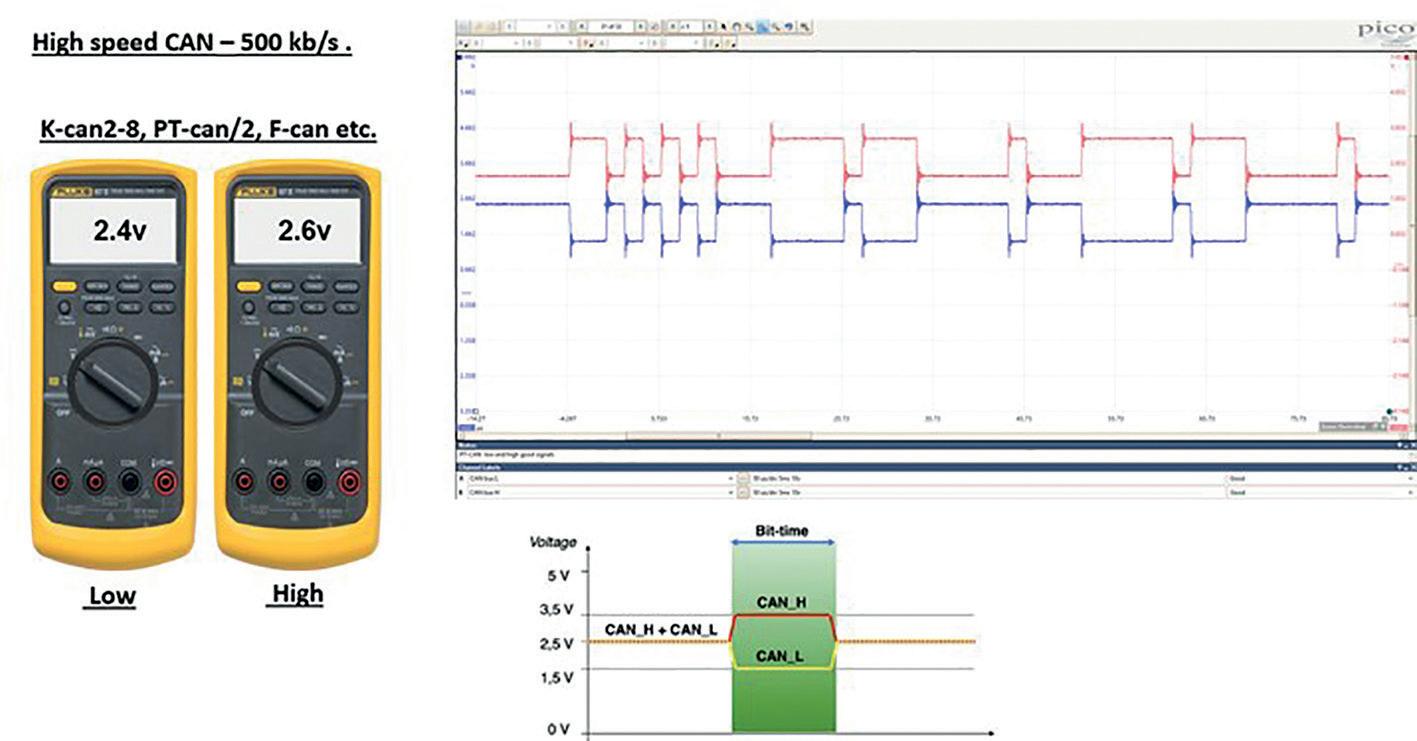

Figure 3.
Voltage checks
When the mechanic working on the car tested the KCAN2 high and low voltages we got something di erent to what is desired. Both the high and low sides were measuring 2.01V, see Figure 3. The Master Technician knew straight away because of his years of experience and knowledge of BMW BUS and CAN systems that the high and low sides were shorted together. To prove this further, after disconnecting the battery, the Master Technician got the mechanic to measure the circuit resistance by placing his meter probes across both pins at the AHM control unit for the KCAN high and low sides. What was measured was approx. 0.6 Ohms, this further proved that the circuit was shorted together somewhere as a good, complete circuit should be 60 Ohms.
The challenging task now awaiting the mechanic was to locate the area where the short was. One method would be to access each control unit connected to the KCAN2 circuit and disconnect them one at a time whilst observing the voltages or signals to see if they become correct after the disconnection. However, the K-CAN2 circuit is quite large and has several control units connected to it – this would be a lengthy process.
Using his experience of diagnosis CAN faults and reading BMW wiring information, the Master technician noticed that there was a connector behind the glove box that, when separated, would separate the KCAN2 network into three sections.
With the plug disconnected, we measured the resistance across pins 24 and 25 – this showed a resistance value of 126 Ohms. This proved that the wiring, control units, and the terminating resister connected after that point were OK.
We then measured the resistance across pins 22 and 23, this showed a resistance of 120 Ohms. This proved that the wiring, control units and the second terminating resister were all OK.
All that was left was the middle section and with the connector reconnected the resistance value shot down to 0.6 Ohms again. A quick check of the vehicle spec provided the information as to what control units were tted to the car. In the middle section, the Master Technician was able to establish that only the radio head unit, iDrive controller and the Combox (telephone) control units were the only control units in the middle section of the KCAN2 circuit.
It was easier to start by checking the Combox as it is located in the rear left of the boot. The Combox and wiring tested OK. This meant the radio head unit and centre console had to be removed. It was at this point that the cause was found.
The wiring for the iDrive controller was not routed correctly and the centre console was crushing it against the vehicle oor/tunnel.
Opus IVS helps independent workshops repair the most complex vehicle fast with diagnostics, programming, and live repair guidance from OE brand-speci c master technicians.
For more information, or to discuss the ideal Opus IVS Solution for your workshop, contact the sales team on +44 (0) 1865 870 060 or email sales-uk@opusivs.com.