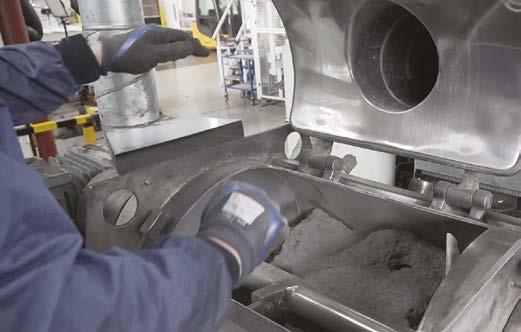
6 minute read
Supplier visit: The home of Ferodo
Behind the Scenes at FERODO
Being a site of immense importance to the motor industry, Rob Marshall fulfilled a longheld ambition, by visiting the home of Ferodo, to establish more about its past, present and future
The motor industry is full of great minds that have benefitted mankind. Karl Benz, Soichiro Honda and André Citroën are such examples but why should the OEMs get all the credit? After all, we also have our share of genius. The aftermarket hall of fame is filled with esteemed people not limited to André/ Édouard Michelin, Robert Bosch, Hans Bilstein, Vincent Bendix, Ercole Marelli – and, in the light of recent events, we should not forget the great gentleman that was Paddy Hopkirk. Yet, what about Herbert Frood? Just because his name is not embalmed obviously in a brand, or company name, does not make his contribution to the automotive arena any less significant.
Mr Frood's place among such esteemed company is well deserved. Like his contemporaries, he was a pioneer and refused to seek traditional answers to well-established problems. When seeking solutions to develop effective friction brakes, Frood did not follow the crowd by looking at raising clamp pressures. Instead, he focussed on the material. After considerable research, he developed a grippy friction matter that was far more effective at dissipating heat than the corkbased substance preferred by Herbert Austin, which had the rather unfortunate and undesirable tendency to catch fire. Yet, Frood was not just an engineer. He was also a businessman, who established the Ferodo brand (an anagram of his name with an extra letter 'e', thought to have originated from Elisabeth, his wife) to manufacture his novel formulation.
All change but no change
Fast-forward 125 years and, understandably, much has altered. The Ferodo brand has passed through four owners, the most recent of which is Tenneco, which acquired Federal-Mogul in 2018 and distributes the brand (and also JURID, another OE braking product) through DRiV. This brings Ferodo and its Chapel-en-le-Frith home into a family that includes 15 global manufacturing plants, many of which serve the aftermarket.
Pictured is a prototype friction formulation mixer. Each recipe contains between 15-20 separate ingredients. The Ferodo brand has been based at the same site in Chapelen-le-Frith, a town in the Peak District, for 125 years. Constructed in 1958, the technical centre incorporates a fullyoperational prototype shop that covers all aspects of disc brake manufacturing. It also houses two dedicated laboratories and a testing centre and provides global engineering support for other Tenneco locations.
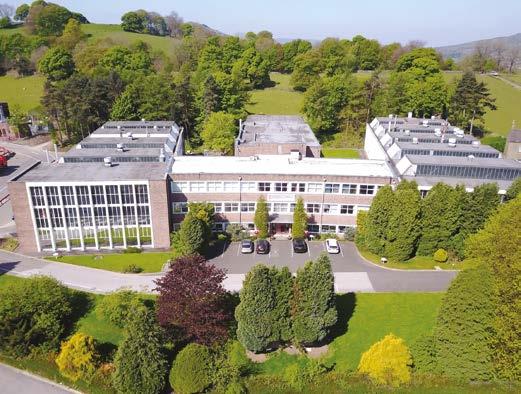
Relationships with car manufacturers have also endured, with Ferodo being the factory fit (and main dealer replacement) for many past and current models, ranging from the Austin 7 to the Jaguar E-Pace. Yet, no barriers exist between Ferodo's aftermarket and OE departments. In situations where Ferodo supplies the vehicle manufacturer, the Ferodo-branded aftermarket offering shares the same development, technology and quality standards.

"Everything good in the world, especially everything good that ever came out of Britain, came out of a shed." - James May. This tribute to its founder is a touching permanent feature on the Chapel-en-le-Frith site.
Mr Frood's passion for innovation has also not diminished. The opening of a dedicated technical centre at the Derbyshire site in the late 1950s was a major commitment to the future of brake pad performance and sustainability. Today, it remains a key part of the business that supports the aftermarket division, primarily. Behind its closed doors, twenty specialists work tirelessly, analysing and formulating new friction materials and even manufacturing prototype pads in-house. Past developments included eradicating copper and developing harder friction materials that do not increase disc wear rates. Even so, innovation must be ongoing and current areas of research include developing friction materials from natural waste. Ferodo is also enhancing its current low-emission formulations to comply with the proposed Euro VII emissions standards that include brake pad dust.

A fully-equipped garage supports a variety of road-legal test vehicles that supports the laboratory-based test centre with realworld data
The test vehicles are modified to allow engineers to replicate tests as accurately as possible. Pictured is the control gear used to control the ABS/ESP hydraulic block.
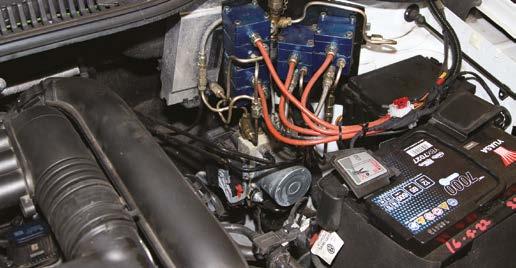
The friction formulations behind Fuse+ are the fruits of the Chapel-en-le-Frith technical centre. Ferodo states that the development is one such example that continues the brand’s heritage of bringing OE braking technologies, quality and performance to the aftermarket. The primary advantages include increased durability but reduced noise and dust emissions with no sacrifices in braking performance.
Naturally, thorough testing underpins the developmental progress, which Ferodo performs in-house. Away from the laboratories and prototype manufacturing areas lie six performance dynameters that run continually to assess performance, durability rates, noise production and dust emissions.
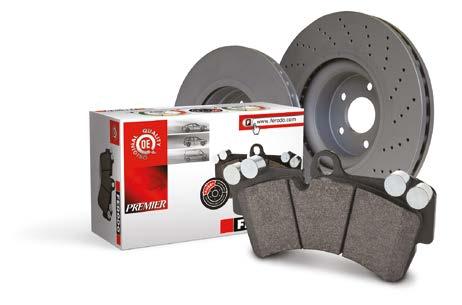
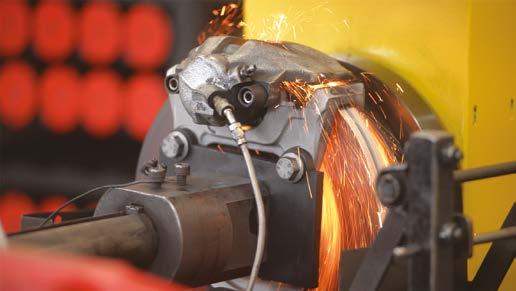
Yet, the company values real-world testing, much of which is conducted at its dedicated facility. Features of Ferodo's private test track include 1-in-4 gradients to test hill-hold capabilities, not just for R90 compliance but also to meet vehicle manufacturer standards. These include noise assessments, such as creaks and groans that can emanate as the park-brake clamp pressure is released. Long straights also evaluate brake pad performance under a variety of pedal pressures, road speeds and temperatures. Interestingly, the wet 'splash' area that assesses performance recovery of soaked linings has been replaced by a more sophisticated mechanism that allows for more constant repeat tests. Fitted within each wheel arch, a dedicated injector sprays water onto the friction brakes, the quantity of which is controlled by the test driver.
Beyond R90
When the DVSA uncovered several brake pad brands that did not meet the minimum legal requirements earlier this year, the topic of ECE R90 regulations hit the headlines. When sourcing replacement pads, it is worth considering whether the brand chosen sees R90 as a target, or a base.
As the test evaluation period lasts between 3-5 hours and includes light brake fade analysis, hill-hold capability, plus pressure and speed sensitivity tests, Ferodo argues that OE specifications are far more demanding. These are the standards that it adopts, instead. Therefore, Ferodo brake pads are developed and tested more rigorously than the minimum standard demands. They must undergo more stringent evaluations that include thermal conductivity, wear rate evaluation (including discs), wet stopping performance, pedal feel and dust analysis. Ferodo also investigates noise – an important consideration for technicians, because these are the most common brake-related customer complaint.
PEOPLE FIRST
Two apprentices at Ferodo's Chapel-en-le-Frith site, Mark Cooper and Ethan Padden, have qualified for the World Skills National Finals. They will compete in the Automation competition as one of the top six national teams. To help in their quest, they will undertake additional specialist training during September. Overall, 500 finalists will compete for gold, silver and bronze at the competitions, which span a range of disciplines and will take place in November.