
6 minute read
Brake Friction
Pads and discs – beyond the obvious
Keeping up with the latest goings-on behind the parts you fit is never time wasted
The effort that braking manufacturers put into optimising their products may not seem relevant to garages but Rob Marshall reasons that a little behind-the-scenes knowledge is beneficial for everybody
Creativity is a vital part of any business. Thinking differently and promoting your activities will give you a competitive edge. Insider knowledge will help with this, which you can align with your customer base. While some car owners obsess constantly over price, many garages refuse (quite justifiably) to join the race to the bottom. Yet, some consumers have other priorities.
The environment
While upcoming Euro VII emissions legislation is considering brake dust emissions, regulations continue to lead change. Some braking companies go further, however, and emphasise the 'green' credentials of their parts, something that may be a powerful marketing tool for you.
While asbestos formulations bit the dust decades ago, heavy metals have become the main target. While copper performs the seemingly impossible task of being both an abrasive and a lubricant within friction material, it is immensely toxic to
aquatic life. With brake dust washing from the road and into drains, it is thought that automotive brake pads account for half of the copper content in urban water tables.
TMD Friction confirms that its pads are copper-free and meet the BBR (Better Brake Rule), which is becoming mandatory for all brake manufacturers by 2025. Some companies are working ahead of the deadline. Comline highlights that its brake pads are copper-free and are ‘N’ rated under the Automotive Aftermarket Suppliers Association LeafMark classification for hazardous materials. This rating certifies that its brake pads contain less than 0.5% copper. Delphi admits to engineering its

entire friction formula to also reduce copper content to below this limit, without compromising longevity, noise control or heat dissipation qualities. First Line reports that all Borg & Beck branded brake pads are manufactured using semi-metallic, copper-free (organic) formulations, making them not just more environmentally friendly but also less corrosive on the discs, compared to coarser formulations that are used in lower quality pads.
Reducing customer returns
Noise is the main reason behind customer brake-related claims. Therefore, considering how your chosen brake pad reduces the risk of come-backs is relevant not just to cut your warranty work but also to bolster positive customer relations. While TMD Friction's pads are tested for noise characteristics, the manufacturer states that its tests are more stringent than those dictated by the basic ECE R90 regulations. Its anti-noise technologies, for instance, include the Textar Q+ Shim and the Mintex FIT Shim that work with the differing chamfer configurations on the pad friction surface to meet the needs of the specific vehicle.
Comline adds that its clip-on RMR (Rubber-Metal-Rubber) backing shims feature with over 500 popular references to cut noise and eliminate squeal. Borg and Beck's pads also boast multi-layered shims, as part of its BECKTEC technology branding. The company reports that the technology suppresses vibration that is generated during caliper piston and brake back plate contact, which is the main source of noise.
Aside from noise-abating shims, Delphi adds that its brake pads feature the company's OE under layer technology. This is a 3mm thick layer of modified, noise-absorbing friction material that not just promotes less noise but it reduces brake fluid heat transfer by up to 22 percent. This may be a consideration for customers that tow heavy weights, for instance.
Helping with installation
Inspecting the old and new pads together will help guide you. The main consideration is that directional brake pads must be installed in a specific orientation. Most pads will possess an arrow, printed on their reverse sides, pointing in the direction of forward wheel rotation. Devoting a little time, looking for such markings, will pay dividends.
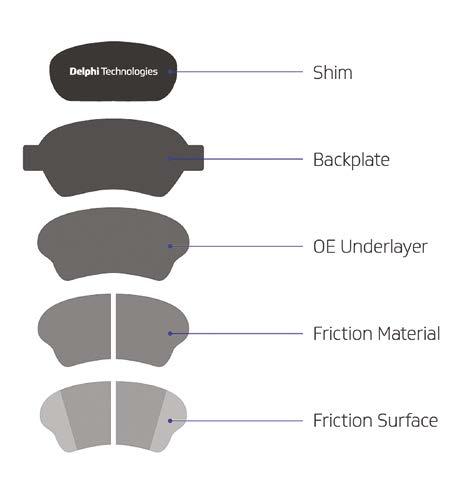
A SNEAK PEEK
Despite spending millions on development, it is not obvious which technologies lie behind the pads you fit. Unsurprisingly, much of this information is confidential but Delphi Technologies provides us with a breakdown of several technical features that are crucial to satisfactory brake pad performance that exceeds the basic ECE R90 requirements.
1: Shims:
These OE-quality, multi-layered shims are essential for noise reduction
2: Backplate:
Powder-coated high-strength pressed steel for increased strength and wear resistance
3: OE under layer:
3mm noise-absorbing friction material for reduced heat transfer and a stronger pad
4: Friction material:
20 unique friction formulations, selected for the required vehicle
5: Friction surface:
OE configured chamfers and slots for improved bedding-in performance.
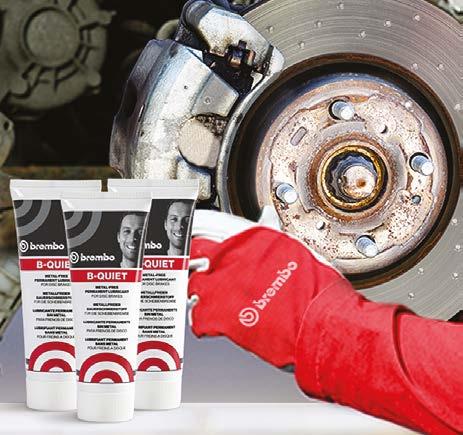
BRAKE SYSTEM MAINTENANCE CHECKLIST
While this feature covers brake friction components, technicians should not limit their checks to pads and discs alone. This advice is emphasised by renowned brake manufacturer, Brembo. A more complete check of the whole braking system should include the following tasks:
1. If changing pads, check for disc wear. 2. If changing discs, do not replace the old pads. 3. Clean rust and dirt from the disc and hub coupling surfaces.
4. Check the oscillation of the brake disc, mounted on the wheel hub. Normally, it should not exceed 0.1mm. If it does, test the oscillation of the wheel hub alone, which should not exceed 0.02mm. 5. If the new pads possess anti-noise shims, ensure that they are fitted correctly. Do not re-use the old shim. 6. Check the pistons, seals, dust boots and sliding elements on the caliper to ensure that they are neither damaged, nor corroded. Use the correct lubricant (i.e. not copper grease) that is suitable for each component. 7. Clean the contact surfaces between the caliper bracket and the pads. Then, apply anti-noise grease. 8. Should the caliper/shoe springs be old and weak, replace them. 9. Check that any return springs are positioned correctly. 10. Assess the brake fluid level and its boiling point. 11. Tighten the wheel screws in the right sequence, to the correct torque. 12. Conduct a brief road test to check the braking system is working well and there are no vibrations or noises.
Check also for any bespoke fitting instructions that are provided with the pad. TMD Friction, for instance, includes a standard of instructions with all brake pads sold. Yet, where a set of brake pads have less conventional fitting needs, these are highlighted within the box, in the company's Brakebook online catalogue, as well as on the pads themselves.
Keeping up to date
Being such a popular consumable product, brake friction products are changing continually and it is worth keeping abreast of developments, especially from well-recognised brands. Delphi highlights its high-carbon brake discs, the increased carbon content within which reduces the risk of thermal cracking and warping. The formulation also permits the discs to operate at reduced temperatures, for more consistent braking performance.
First Line's range of Borg & Beck BECKTEC coated discs utilises a water-based coating. Offering both corrosion and enhanced thermal protection, an obvious advantage for technicians is that they can be fitted from the box and transit oils do not require cleaning off with solvents, before installation. Coated discs are especially appreciated by owners with vehicles with widely-spaced alloy wheel spokes, through which rusty discs let down the car's overall appearance. Again, coated discs are becoming more popular but may be worth you considering as a customer upsell for certain applications.
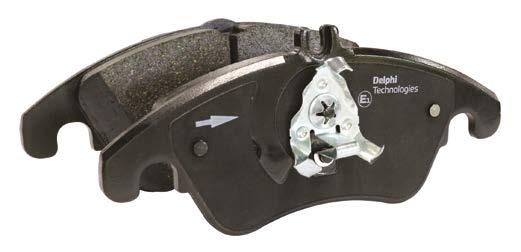