
8 minute read
Fast moving friction
Fast moving friction
Even with EVs, braking system servicing is a worthy and growing revenue stream, leading Rob Marshall to suss out the latest news
While the UK car fleet is getting older, it is reassuring to know that brake friction suppliers are not resting on their laurels. Take Brembo as an example. Within twelve months, it has expanded its aftermarket offerings considerably. With Battery Electric Vehicle brakes vulnerable to corrosioninduced binding, Brembo presents its Beyond EV Kit, which incorporates discs and pads that are not just more corrosion-resistant but also quieter. They also produce less dust and it is this latter issue on which the Greenance Kit Concept is formed, where Brembo focusses on brake friction pollution. The company tells us that it is evaluating whether, or not, it can meet the stringent EURO VII emissions regulation, before considering offering it to the aftermarket.

The bilstein group has also had a very busy year. Notably, its febi brand has introduced a 650-strong range of new (not remanufactured) brake callipers. Like febi, Comline has also expanded its friction offerings for newer vehicles, including those for Vauxhall Corsa/Mokka ranges and Nissan's Qashqai. Delphi too presents pads and discs for the ubiquitous Nissan, as well as expanding its EV range to include pads and discs for the Ford Mustang Mach-E, plus the Hyundai Ioniq 5/6 and its sister car, Kia's EV6.

Other brands are expanding their aftermarket friction portfolios, too. Since being acquired by Fras-le, a Brazilian OE manufacturer in February, Juratek is growing its ability to service the braking needs of both passenger and Light Commercial Vehicles. TMD Friction is also increasing its ranges for both passenger cars and electrified vehicles. Even so, innovations continue for existing offerings. Ferodo reports that it is engineers are exploring new material formulations, pad designs and other innovations constantly, to enhance stopping power, minimise noise and dust emissions, while extending pad and disc life. Its most recent product improvements include chamfered directional brake pads and a directional arrow imprinted on pad back plates to aid correct installation. First Line has also been providing new practical alternatives for the aftermarket. Its states that the expansion of its Borg & Beck BBD7000 brake disc series allows garages to offer aftermarket alternatives to costly two-piece bimetal OE discs. These comprise one-piece discs, made from high-carbon steel, protected from corrosion by a water-based zinc-aluminium coating. Being a retailer has not stopped LKQ Euro Car Parts from upping its game, either. It says that its Wear & Tear Manufacturing Defects warranty, introduced earlier this year, has been received very warmly by garages.
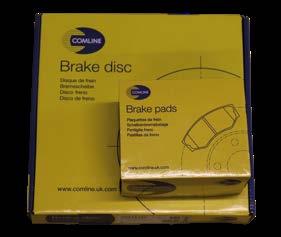
Low Viscosity brake fluid – is it a con?
We are hearing of a different type of brake fluid being introduced for vehicles requiring non-silicone fluid. Speaking under anonymity, a trade contact told us that this is a cynical attempt to make the trade and public pay more for brake fluid that is the same as normal DOT 4. Yet, our contacts disagree.
Ferodo says that such low-viscosity fluids are formulated to maintain correct performance of the ABS/ESP hydraulic control unit, which possesses very narrow piping and nozzles, where a fluid with higher viscosity could cause a delayed reaction.
DRiV argues that garages can upsell an enhanced specification DOT4/5.1 fluid in the case of highvoltage vehicles. It reasons that, due to the potential electrical currents near the braking system, a lower conductivity fluid is advisable. Brembo shares this view. DRiV also reasons that, because noise from the braking system is more noticeable on Battery Electric Vehicles, its Ferodo DOT5.1 EHV contains special lubricity enhancers to help counter the effect. Yet, First Line, LKQ Euro Car Parts and TMD Friction highlight the importance of complying with carmakers' fluid stipulations.
Febi reasons that some manufacturers recommend a low-viscosity variant of DOT 4 brake fluid, especially for colder climates, because of the lower freezing point.
Delphi agrees that using conventional fluid in systems designed for low-viscosity fluid can compromise braking performance, potentially leading to longer stopping distances and decreased system responsiveness.
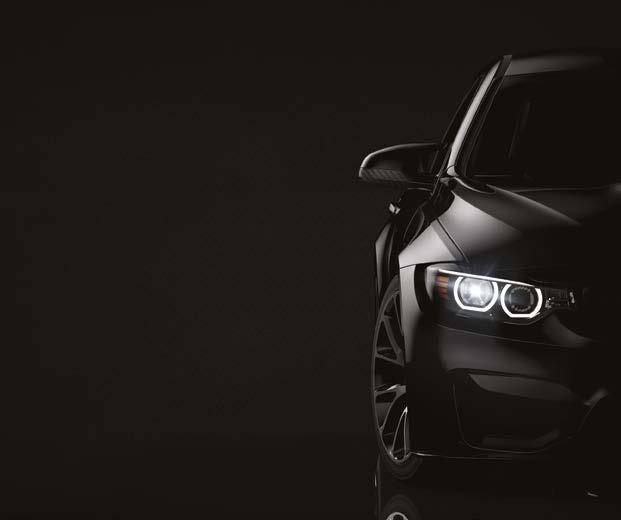
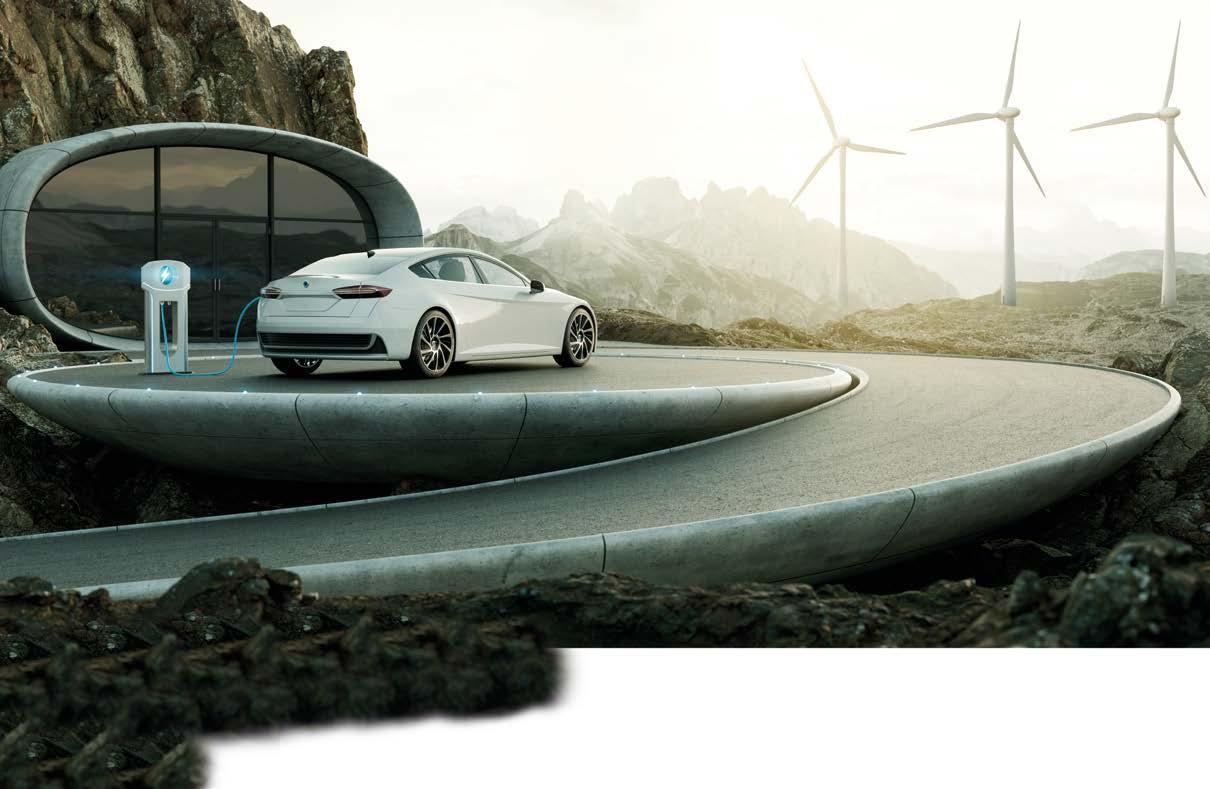
Faced with an almost constant barrage of consumer doom-and -gloom news reports, it is surprising that brake friction suppliers are not experiencing a race to the bottom
Market Trends
Faced with an almost constant barrage of consumer doomand-gloom news reports, it is surprising that brake friction suppliers are not experiencing a race to the bottom. TMD Friction says that this year's sales trends have reflected those of last year. While its trio of brands possess different price sectors to suit market demands, the company has even experienced a spike in demand for its premium Textar brand. First Line states also that it has not noticed any particular shift in brand preference, due to the cost-of-living pressures.
Interestingly, febi reports particularly high sales in ancillary products, such as hoses. Also bucking the trend is Comline. It reports strong growth in its brake friction offerings, which it attributes to workshops repairing increasingly older cars.
LKQ Euro Car Parts agrees, adding that brake friction sales are 'booming'. However, Juratek finds particular interest in its hybrid and electric vehicle offerings, especially as those vehicles are entering aftermarket workshops.
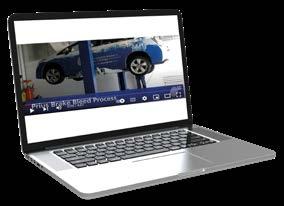
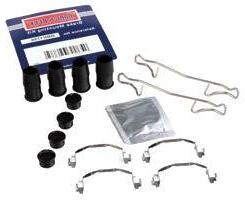
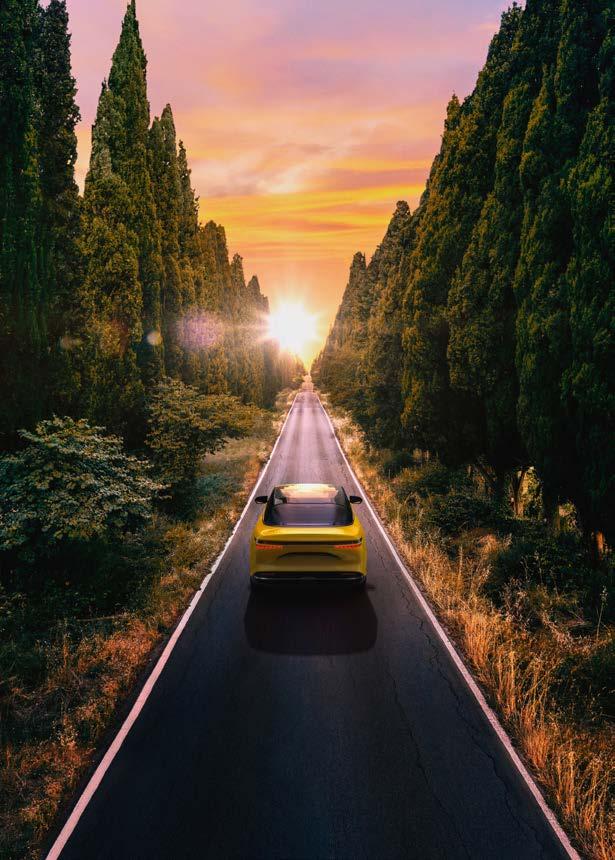
Ten routes to smarter brake repairs
It can be difficult to resist pressure to complete servicing tasks faster. A lack of time may also reduce opportunities for technicians to keep up with training, too. We asked Comline, Delphi, DRiV (Ferodo), First Line, Juratek, LKQ Euro Car Parts and TMD Friction for their top advice for busy technicians on how to avoid the most common errors, which training will correct.
Removing disc coatings
While removing protective oil film on plain unpainted discs is vital; some technicians waste their time, by stripping paint from coated discs. Unless contaminated, coated discs can be installed straight from the box.
Not replacing in pairs
Replacing one side only can be dangerous, because of braking imbalance. Should you find one side exhibits uneven wear, you need to perform extra checks to establish why. Sticking calliper slides and pistons are good places to start.
Not cleaning disc to hub faces
This is a very common omission that causes vibrations and juddering and risks potential braking system failure. This is the main cause of Disc Thickness Variation, which is a condition of 'High Spots' on the discs that cause a pulsating effect on the pedal. Use a wire brush to eradicate rust from the contact surfaces and hub flange, while being careful not to damage the calliper bracket. Rinse the surface with brake cleaner and check the cleaned hub with a DTI gauge, for any possible lateral runout deviations.
Not checking ABS rings
This task includes removing corrosion on the hub. For certain Citroëns and Peugeots, a common error is not verifying the correct air gap between discs fitted with ABS rings and the sensors on the car.
Over-use of impact wrenches
This can over-tighten fixings, risking fracture. Use a torque wrench on all mounting bolts, observing car manufacturer specifications for recommended torque.
Reusing ancillary parts
Workshops tend to skip this step to save themselves time and their customers' money. Yet, brake pad fitting kits increase braking system efficiency and longevity and are especially valuable to prevent imbalance.
Using copper grease
This traditional practice was never advised officially but managed to become adopted throughout the aftermarket for many decades. When used on modern brakes, copper grease causes electrochemical corrosion and may also lead to sticking at high temperatures. It also conducts heat and might cause the vehicle’s ABS/ESP system to malfunction. It also attacks therubber used as calliper piston gaiters.
Lubricating moulded shims
While slide pins and pad-to-calliper contact points should be lubricated with a non-conductive, heatresistant and solids-free ceramic grease, such as Textar Ceratec, the rear of pads that comprise moulded shims must not be greased.
Neglecting brake fluid checks
Most commonly, this refers to postfriction brake repairs. Naturally, most brake fluids should be tested annually and replaced biennially.
Forgetting aftercare
Road-test the vehicle before handing it back to the owner. Clear any coatings from the brake surface, by braking gently and carefully from a maximum speed of 30mph. Afterwards, explain to the customer why bedding-in is essential to prevent future noise issues. The bedding procedure lasts between 200 - 400 miles and enables the pads to deposit a thin, even layer of material onto the disc surface. The driver should avoid harsh braking during this time; otherwise, the pad friction material can glaze, increasing the risk of brake fade. It is worth noting that some companies fit their pads with bedding-in strips, making such careful post-fitting treatment unnecessary.
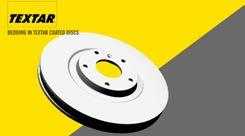
Keep up to date with how braking systems are evolving, by topping up your training
For more information, check out:
Delphi’s Masters of Motion hub: https://mom.delphiautoparts.com
Delphi Academy online learning: https://academyuk. delphiautoparts.com/#/public-dashboard/
DRiV's Garage Gurus knowledge centre: www.garagegurus.tech/en-gb/knowledge-center. html and training: www.garagegurus.tech/en-gb/ garage-gurus-services.html
The LKQ Academy also offers braking courses, too: https://lkqacademy.co.uk/