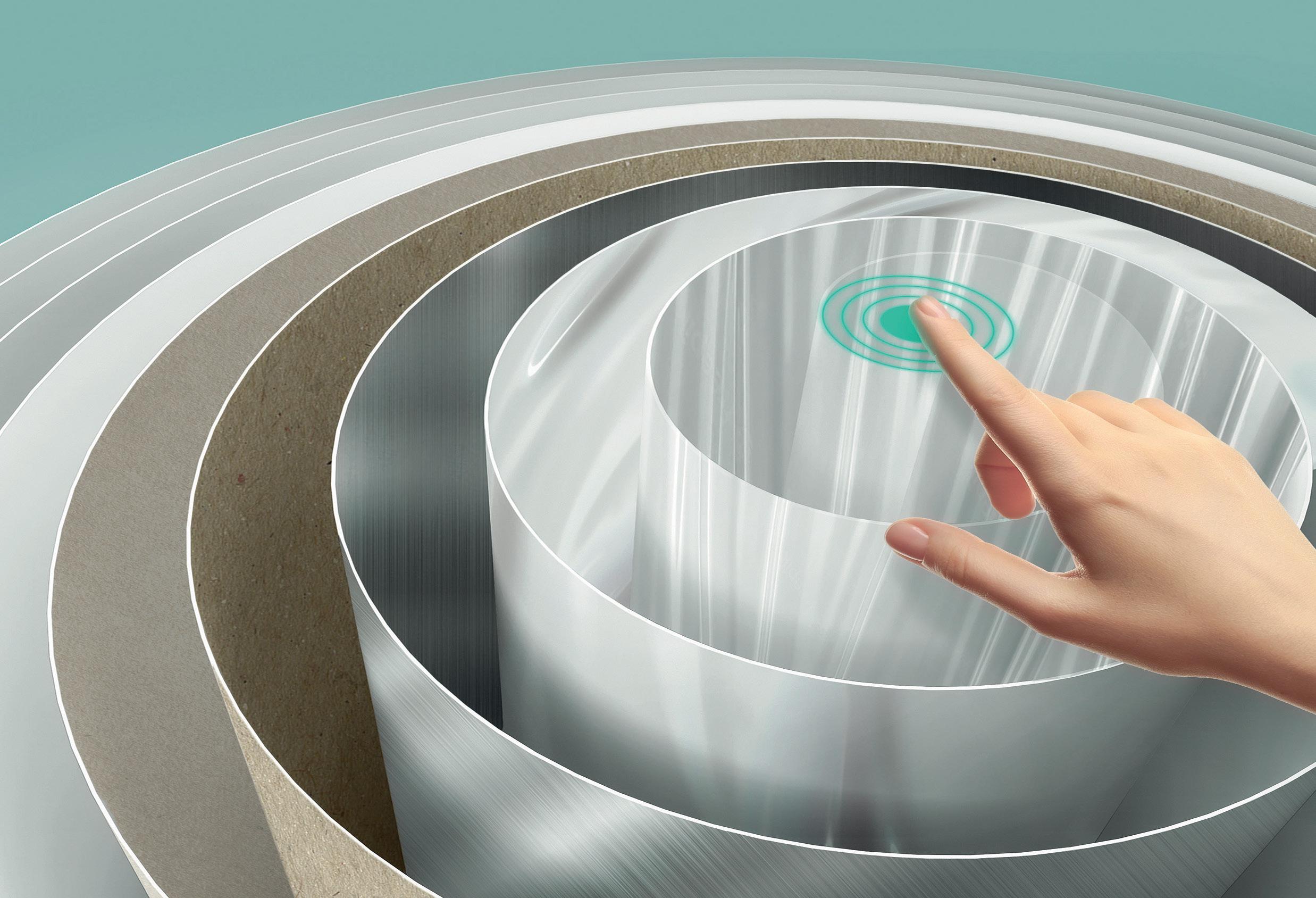
3 minute read
W APPI N G
D L A O -360 X S flex ble s re dy f r m rr ’s llenges
Raw material costs and their availability, national and international regulations - everything changes so fast, making the future increasingly unpredictable.
DELTA OF-360 X is the first future-proof packaging machine, thanks to its variable geometry that can be set with just a touch on the HMI. Limitless flexibility to quickly switch from one material to another, even those which are still to be developed, is the best way to protect your investment. With DELTA OF-360 X, the future is in your hands.
Multi-lane dough divider
Reiser’s Vemag Multi-Lane Dough Divider adds versatility to production lines and works for all types of buns, rolls and English muffins. The Vemag is easily adjusted to consistently produce exact-weight portions of any dough absorption or crumb structure. It can run up to eight lanes of product at up to 300 cuts per minute. www.reiser.com
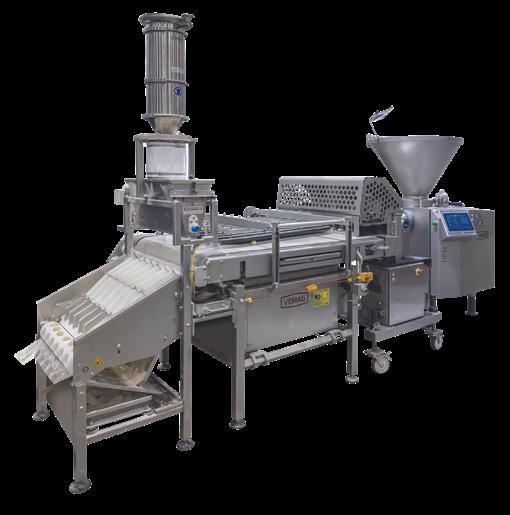
Intelligent portioning for cookies and crackers
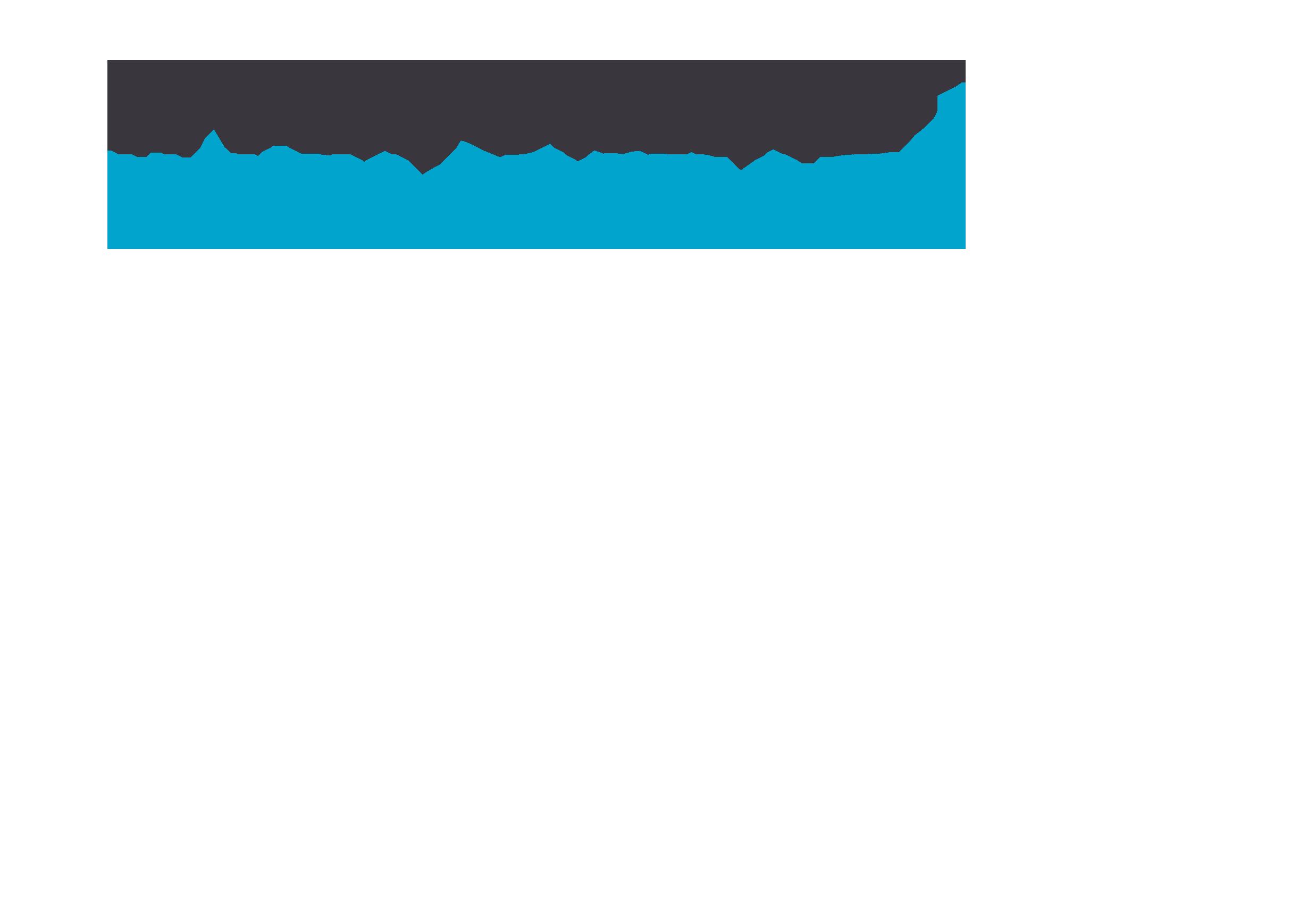
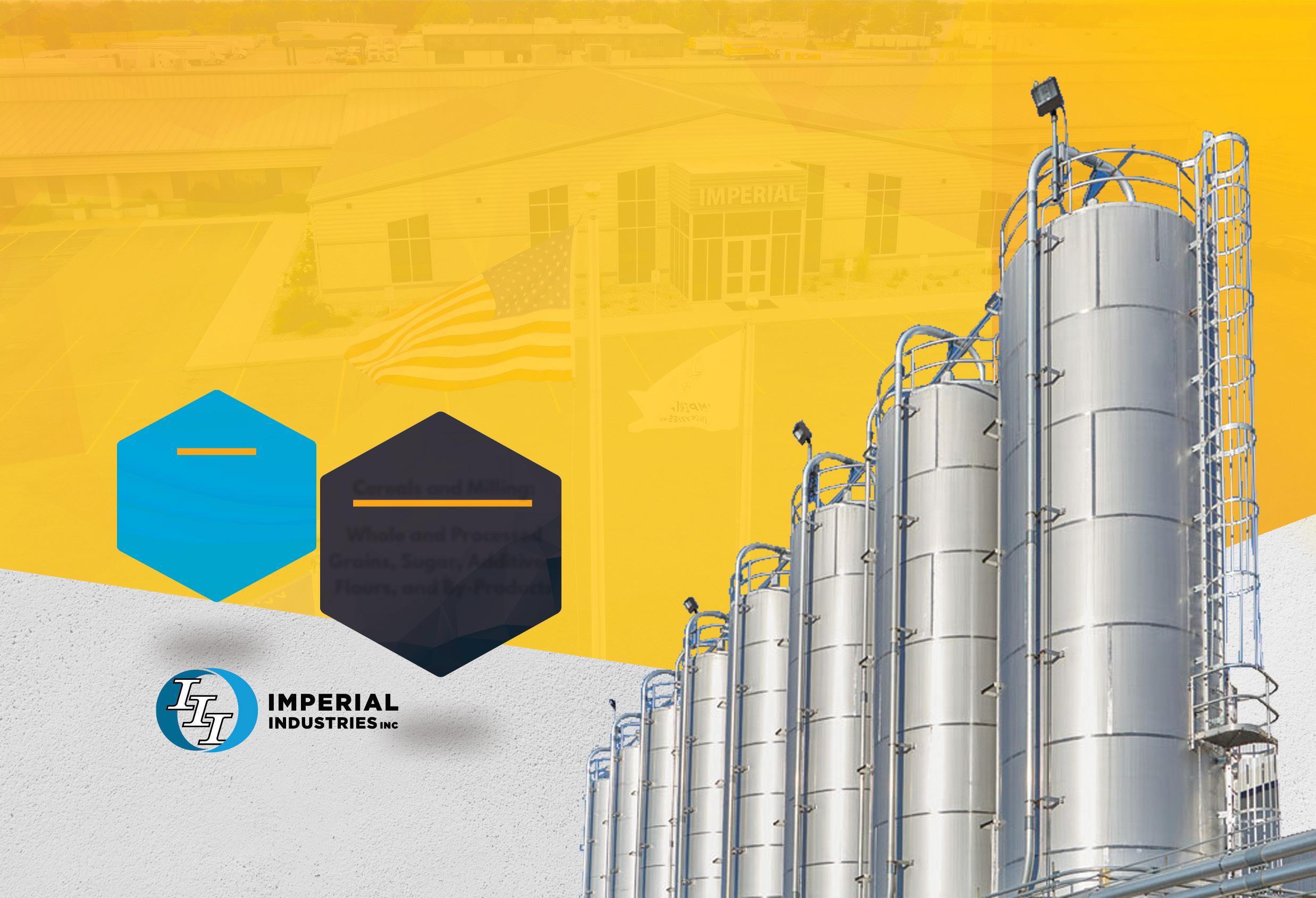
Syntegon has developed a solution for the handling and portioning of cookies and crackers. This innovation features gentle product placement through linear motor technology, managed by user-friendly, format-altering software. It has the ability to perform seamless changeover between a variety of product shapes and pack styles. www.syntegon.com
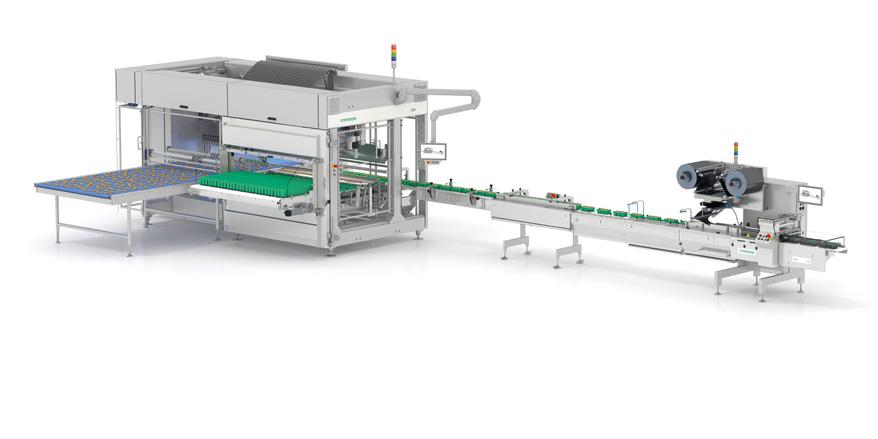
Preventative maintenance scheduling program
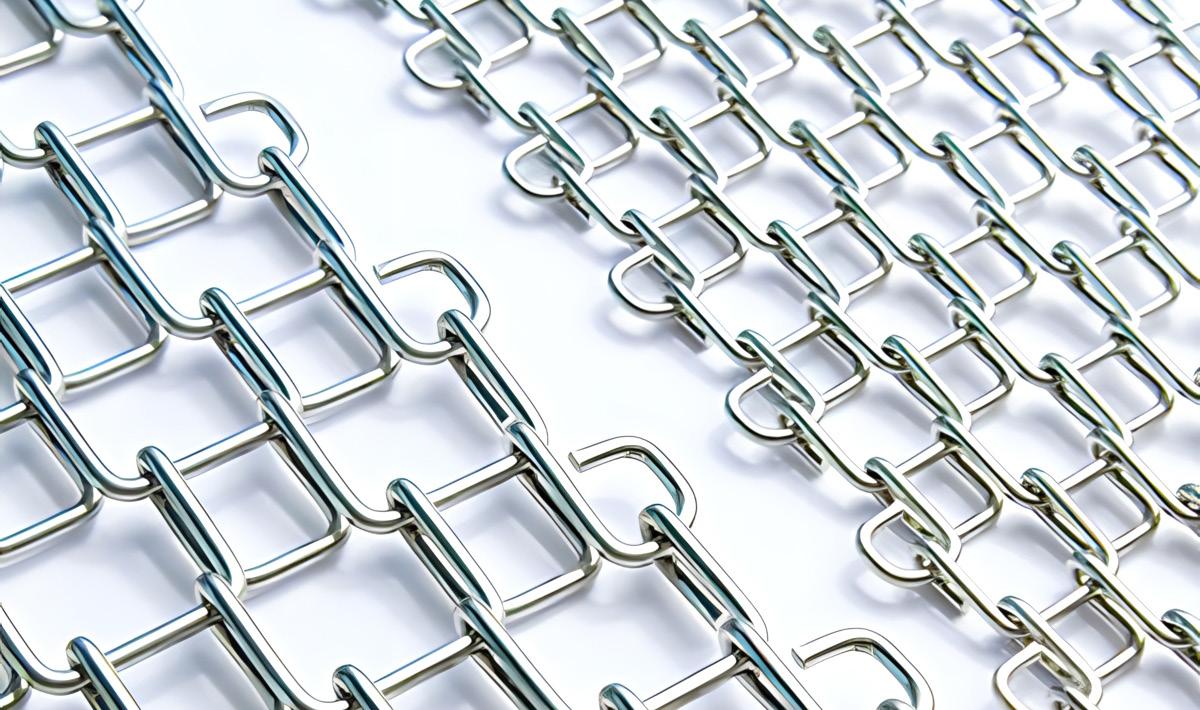
Unifiller’s Preventative Maintenance Program provides priority access to the company’s service technicians and allows appointment scheduling to ensure equipment runs smoothly. The company provides training, guidance and safety advice on how to use its equipment. Experts guide customers through the process in preventing downtime, selecting replacement parts, and cleaning and storing equipment efficiently. www.unifiller.com
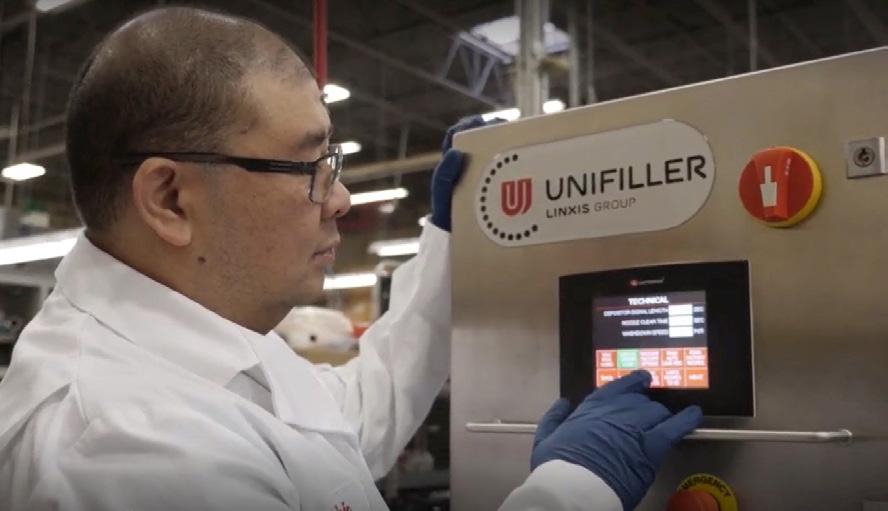
Improved conveyor belt mesh
Wire Belt launched CG15, an addition to the Compact-Grid conveyor belt family. The 15-mm mesh has an increased wire diameter of .082 and boasts an even larger open surface area at 73%. This offers better flow-through properties for heating, cooling and coating operations. Thicker and larger, the mesh can also hold more weight per square foot. www.wirebelt.com
Automate Moisture & Oil Measurement in Food Production
Automate Moisture & Oil Measurement in Food Production
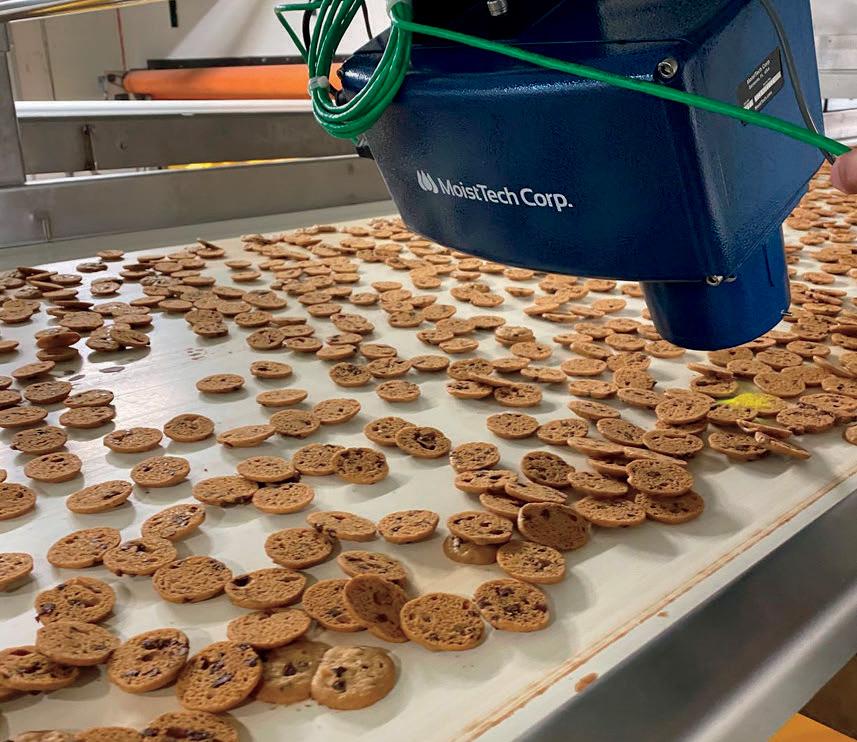
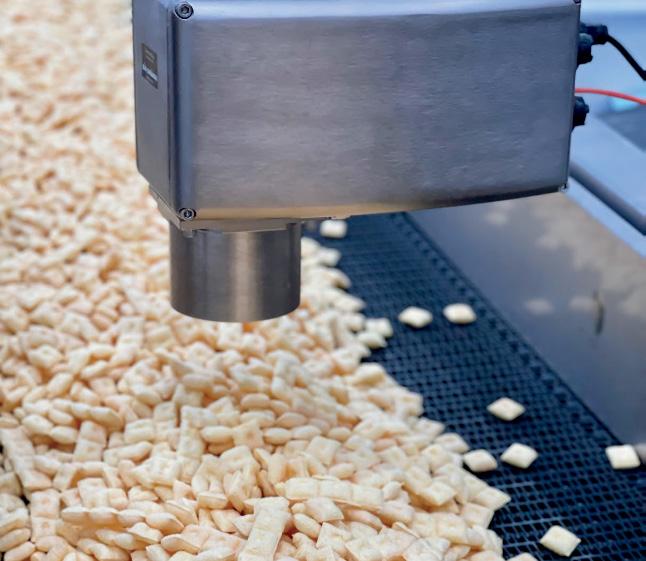
EXPERIENCE THE BENEFITS OF NIR MOISTURE CONTROL DIRECTLY ON THE PRODUCTION LINE!
EXPERIENCE THE BENEFITS OF NIR MOISTURE CONTROL DIRECTLY ON THE PRODUCTION LINE!
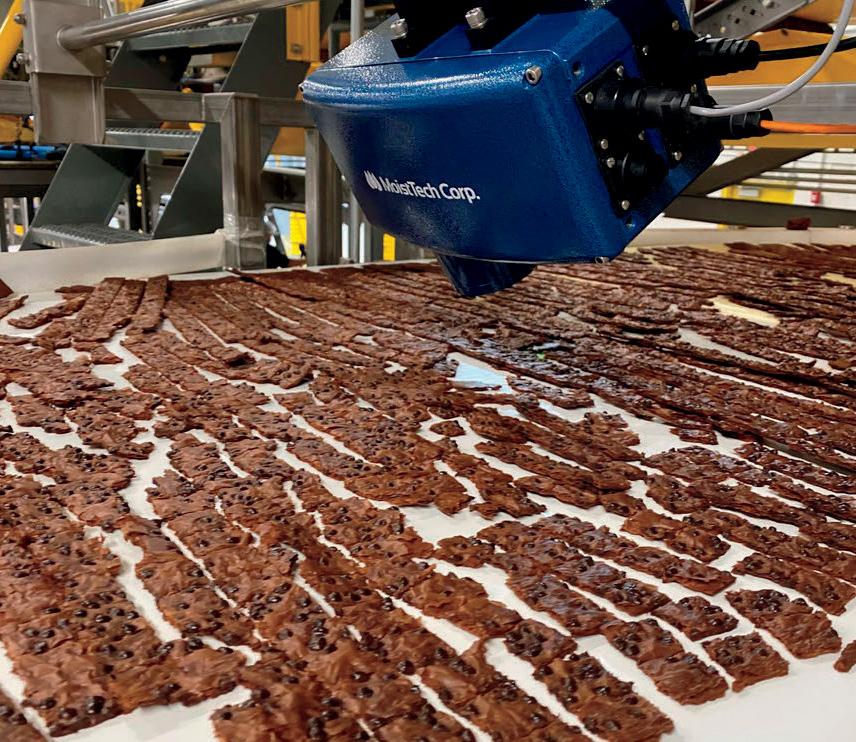
Constant Monitoring Adjustments Made Easy
Constant Monitoring Adjustments Made Easy
Allows for a constant, non-contact solution to moisture and oil measurement directly on the production line in real time
Allows for a constant, non-contact solution to moisture and oil measurement directly on the production line in real time
Operational personnel are able to make crucial, immediate adjustments on the line to avoid waste and downtime
Operational personnel are able to make crucial, immediate adjustments on the line to avoid waste and downtime
Closed Loop
Closed Loop
Measuring moisture directly on the production line produces instant, accurate data that can be easily communicated to a PLC - creating a closed loop process
Measuring moisture directly on the production line produces instant, accurate data that can be easily communicated to a PLC - creating a closed loop process
Immediate Improvements
Immediate Improvements
A MoistTech system provides improved product quality, lower waste and energy costs, process optimization, increased plant efficiency, oven control & reduced downtime
A MoistTech system provides improved product quality, lower waste and energy costs, process optimization, increased plant efficiency, oven control & reduced downtime
The following advertisers appear in this issue. We encourage readers to reach out to these companies through the listed website or email for further information. This index is provided as a service to readers and advertisers, but Commercial Baking does not assume any liability for errors or omissions. Please send any updates or corrections to info@commercialbaking.com

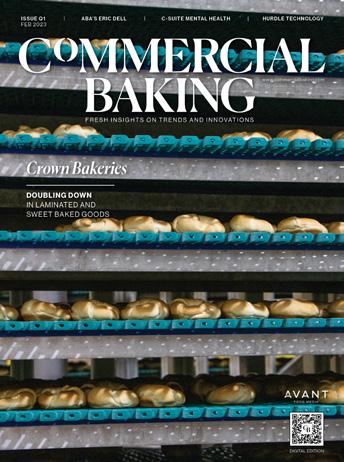
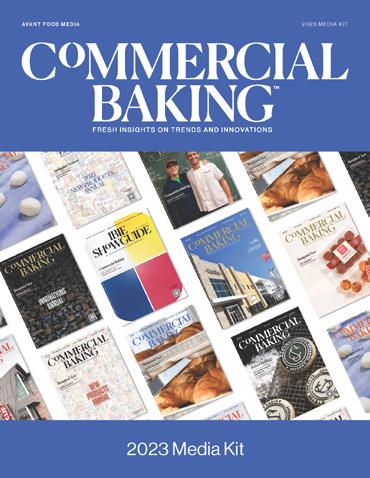
This month, the world celebrates Earth Day, a day of education about environmental issues and a demonstration of support for the protection of the air we breathe, the water we drink and all other natural resources.
Across our industry, companies are exploring ways to reduce use of resources like water, packaging and energy. And while there is work yet to do, we are improving in many areas, and I couldn’t be prouder of our collective efforts.
At Flowers, we recognize that carbon dioxide and other greenhouse gases (GHG) may have an adverse impact on global temperatures, weather patterns, and the frequency and severity of extreme weather and natural disasters. We seek to reduce emissions through a combination of energy awareness and efficiency upgrades. And we know that small steps can yield big results.
Our energy strategy includes three key components — track, integrate and share.
We use an online energy management program to track energy use and emissions at all our facilities: bakeries, distribution centers and warehouses. Any unusual change in energy consumption that may warrant an investigation triggers an alert, notifying the facility’s management.
We improve energy efficiency by looking for ways to incorporate energy-saving measures when upgrading equipment, installing new production lines or designing new projects.