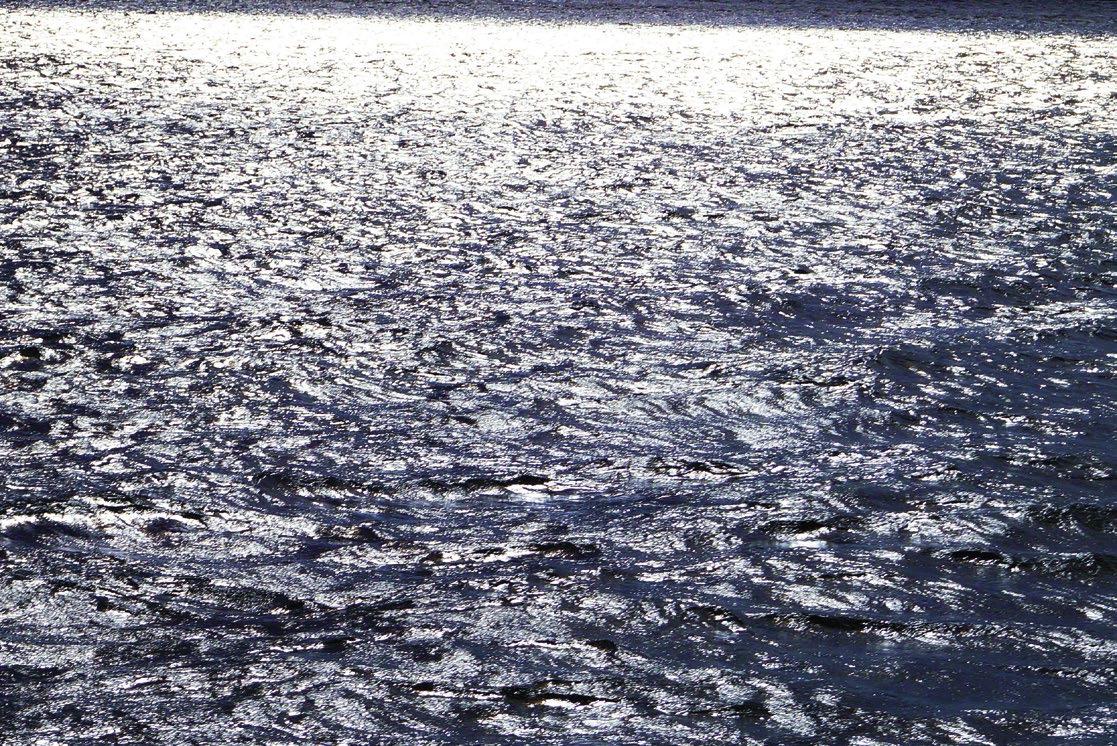
11 minute read
Tales From the Waterside
Some Untold Water Treatment Yarns
By Dave Christophersen, Dave Christophersen Consulting LLC
Traveling back from working in Australia on water treatment issues for the mining industry, I had a not-so-preferred seat in the middle of a wide body jet. Getting prepared for what I anticipated would be a very long 14-hour flight, I met my passenger to the left. He was an American traveling around Australia to play concerts with his rock band, but his greater success was writing and performing 62 songs used in television show episodes or as commercial jingles. To my right was a college-aged Irish women who was six months into backpacking around the world on her own.
As soon as we leveled out, the stories began passing through me from the left and right from two really fun people. The American talked about song lyrics he had written and TV show personalities he had met; the young Irish woman talked about sites she had seen and strangers she had befriended. In all, there were enough experiences had for a lifetime. After they had told some of their stories, I suggested, “Hey, I am an experienced, well-traveled water treater. Would you like to hear some good water treatment stories?” From my left I heard, “No.” From my right I heard, “No, not really.”
So, this episode of “Tales from the Waterside” is my chance to tell some of the stories that were omitted one day at 30,000 feet. The most fun ones, though, will be spoken, not written.
For me, as my years of water treatment experience start to add up, I realize that what I have seen, done, and heard—basically “been there, done that”— has had a much more lasting impact than reading the AWT Technical Reference and Training Manual (TR&TM) or the old Betz Handbook of Industrial Water Conditioning. I tend to look at water treatment now as not repeating the mistakes that I have made in the past, comparing how water treatment systems are to how they should be, and evaluating all risks involved for successful outcomes based upon water quality and variability, operation and control, and equipment and design. I look to design for the 95% “most-of-the-time” scenario but anticipate and prepare for the 5% “out-of-control-time” when things have changed, are upset, or have basically gone south.
So, some of these are stories and memories that resulted due to failures on my part, immaturity, laziness, eagerness, or because I just had not yet been there or done that. They are in no particular order of value or importance, humor or concern, or interest.
Water Tales Worth Sharing Here are some stories I might have shared if my fellow passengers had expressed interest.
Early in my career, I had read about boiler inspections but had never participated in one to experience the confinement, heat, dirt, and knee-knocking movements.
I was told to make sure the entry is safe, all blowdown lines blocked out, and that people were around. (The confined entry requirements now are much better than when I tried to kill myself on several occasions.) My boss and I entered a large field-erected coal-fired boiler for inspection. The other two boilers were still online.
When someone performed a manual blowdown on one of the operating boilers and hot steam and water entered our mud drum, it was a race to see how fast we could crawl and escape through a very small hole.
Not learning as quickly as I should have, I once got stuck trying to get out of a large steam drum of a competitor’s
account when no one was in the boiler room. I eventually lost enough weight and was able to maneuver my way out. Never told anyone. Never got the account.
Hot process softeners were common in my early career, and they were often followed by hot zeolite softeners. I was young and thin, so there was no problem going into one to inspect the internals, even though it was still hot and steamy. But it was hard to climb out with the rope ladder laying against the side and you are exhausted from the heat.
Helping hands dragged me out from that poor decision.
A customer’s facility manager once told me of a Lassie
TV episode where Timmy was stuck in a drainage culvert with a big thunderstorm approaching, and
Timmy yelled to Lassie to go get help. My customer was extremely claustrophobic and even had a hard time watching me inside a boiler. When I got stuck in a very tight steam drum, he screamed, “Run, Lassie, run!”
At the request of a client, I made a visit to a large chemical plant operating a new demineralizer system for its high-pressure boilers. The purpose was to determine why its new $1.5-million demineralizers were not producing water to the designed total dissolved solids (TDS). My boss was busy working on it, but all of this was quite new to me, being freshly out of college. While they were out in the water plant troubleshooting, I was reading the manual. I noticed that the specs called for water quality to be expressed in parts per million (ppm) TDS as sodium chloride (NaCl). Turns out, the company had won the bid because it (yes, I remember who it was) pulled a fast one by expressing TDS as sodium (Na) instead of NaCl. There was no problem in performance when we converted the water TDS of the effluent to NaCl. Lesson learned? Know your chemistry, conversions, conventions, and sneaks in the industry.
I was cleaning a slimed-up cooling tower containing lots of sludge at 5:00 am with a new client of mine. (Don’t ask what personal protective equipment [PPE] we used.) As we cleaned, he turned off his high-pressure hose and said to me, I have four years of college.
I replied, I have seven. “Just wondering out loud,” he said. Then we got back at it.
Feeding sulfuric acid into cooling towers for pH control is not uncommon, but it used to be much more common than it is today. A colleague of mine working at a client site was working on the acid metering pump and the client asked me if he knew what he was doing. I said, “oh yeah, he does this all the time.” Just then, while still pressurized, the discharge tubing popped. His face showed the acid pot marks pretty much immediately, and his nice wind breaker jacket began showing the insulation inside.
My worst acid experience was when the acid line above me had come loose and was spilling down right onto me. I saw my smoking wet shoes not knowing why they were wet, and then looked up to catch acid in my face. I made it to the eyewash stand and washed for about 15 minutes, but then my clothes and shoes were pretty worthless, except my belt apparently, which someone stole while I was changing into some overalls.
I had business at some rendering plants or meat packers that also rendered. That smell is not so pleasant and tends to adhere quite well to a person. When I would come home to my apartment, my wife would “suggest”
I change outside before coming indoors. For basketball league, one time I had to go directly there. It was my best scoring night ever. No one wanted to guard a sweaty man who smelled like dead pig.
How fast does corrosion occur? A prospect was operating his boiler room with a hot water tank instead of a having a properly operating deaerator. This almost never works well, at least without a passivator or filming treatment chemistry. I put a coupon into the bottom of the tank using a retractable coupon holder, but then needed to pull it out to make sure I had it positioned correctly. Even with sulfite and a residual in the tank, the coupon showed significant corrosion after only 30 minutes.
A new client called me at home late one night. He could not keep his boilers from tripping off whenever they went onto high fire, and of course he blamed the chemicals.
This time, the customer was right. Late at night, I learned that if you overdose polymer (in this case in the 300 ppm range), it becomes very surface active, causing the boiler water to prime with the site glass, filling and then emptying as the water line inverted. This is not the only place I have seen that happen.
On another bad night for me, a client called around midnight for a similar reason. All of the process and
heating boilers were foaming and carrying over. They had retubed a low-pressure heating boiler, and I provided boil-out chemical and procedures. Unfortunately, they did not close the steam isolation valve of the low-pressure boiler; it got cold that night; and it went into high fire and sent foaming boiler water out into the entire plant, contaminating all the steam and condensate system. I spent all night with boiler contractors draining and refilling. At 6:30 am, I had a very special meeting with the VP where I took some very large lumps. Luckily, later that day, my main contact at the plant stood up for me and said that I had told them that they needed to isolate the boiler when they did the boil-out. For all future boilouts anywhere, I made sure procedures and consequences were very clearly understood and agreed to.
Always know your water sources and chemical feed points. Do not rely on anyone without confirming on your own. Things can change. For a very large opportunity but very difficult water, lots of clarification jar studying was required to come up with a workable program. After three long days, I had a program that worked well. Then, I learned that my buckets of water samples contained a certain competitor’s coagulant.
Can you say, wasted time?
I have always been a little suspicious that water company big brother is watching and has his spy network out there. When working for a water treatment company, I was sent a Sean Connery lookalike young water treater to work with me and gain some experience. I had a sales call set up one morning for 11:00 am, when I learned an emergency had come up and the prospect needed to change the meeting to after lunch. I asked “Sean” if he had any ideas for what we could do until the meeting.
He responded, “Bowling?” So, I took him for lunch at a bowling alley. After our first round, when I looked over at him tucked away from me, he was talking into his pen, and said, “Open Channel D please, … you won’t believe what we’re doing now.” By the way, he left water treatment shortly after that, but years later, I am still at it.
When a new client does not yet trust you or is just plain ornery, some people try to make them their friend, but some try to push them over the edge. With a very large
RO install to use reclaimed water for boiler makeup, I experienced for the first time that aluminum in the water can cause very rapid loss of flux without much affecting the differential pressures of any stage. As we were trying to determine the problem, aggressive and frequent RO clean-in-place (CIP) was required by us while the plant manager hovered with some unloving verbose. I knew that angrily and quickly dumping that entire bag of metabisulfite by my colleague into the hot water of the CIP tank would clear the room, and soon the plant manager’s flight and choking cough had landed the intent.
Cooling towers and their sumps can be quite large and intriguing to effectively treat and monitor, often alluring some rather perilous perches. One day, when a board broke above a large sump at a client’s site, with one of my colleagues making a splash, a sign the next day had been strategically hung: “No Swimming
Allowed.” Safe practices are kept front and center much more nowadays, as they should be.
I had a customer who was a really good basketball player, so we would play at lunchtime at a nearby college on my service days. He then suggested tennis, where I had the edge. The first time back after soundly beating him at two sets, he called me into his office, sat me down, and passed me a cartoon. It was two golfers walking off a course with the client saying to the supplier, “Well, that’s the hole, the match, and the account.” He was joking, but years later, I found out a big boss of mine was not so accepting after I beat him 6-0, 6-0, and my immediate boss asked me how stupid I was. Should the customer or boss always be right and always win?
These are some of my stories, but the best are still reserved for non-water treaters and airplane flights.
Dave Christophersen is owner of Dave Christophersen Consulting LLC and a senior consultant to AP TECH, based out of West Chester, Ohio. He has 45 years of experience in the water treatment industry, including managing water treatment programs for industrial sites for boilers, cooling systems, wastewater systems, and membranes. Having worked at Olin, Betz, Crown Solutions, and Veolia, Mr. Christophersen’s water treatment experience includes technologies for wastewater treatment, boiler water treatment and pretreatment, cooling water, and membrane technologies. He provides training, business, marketing, and technical support to the water treatment industry. Mr. Christophersen may be reached at christophersendave@gmail.com.