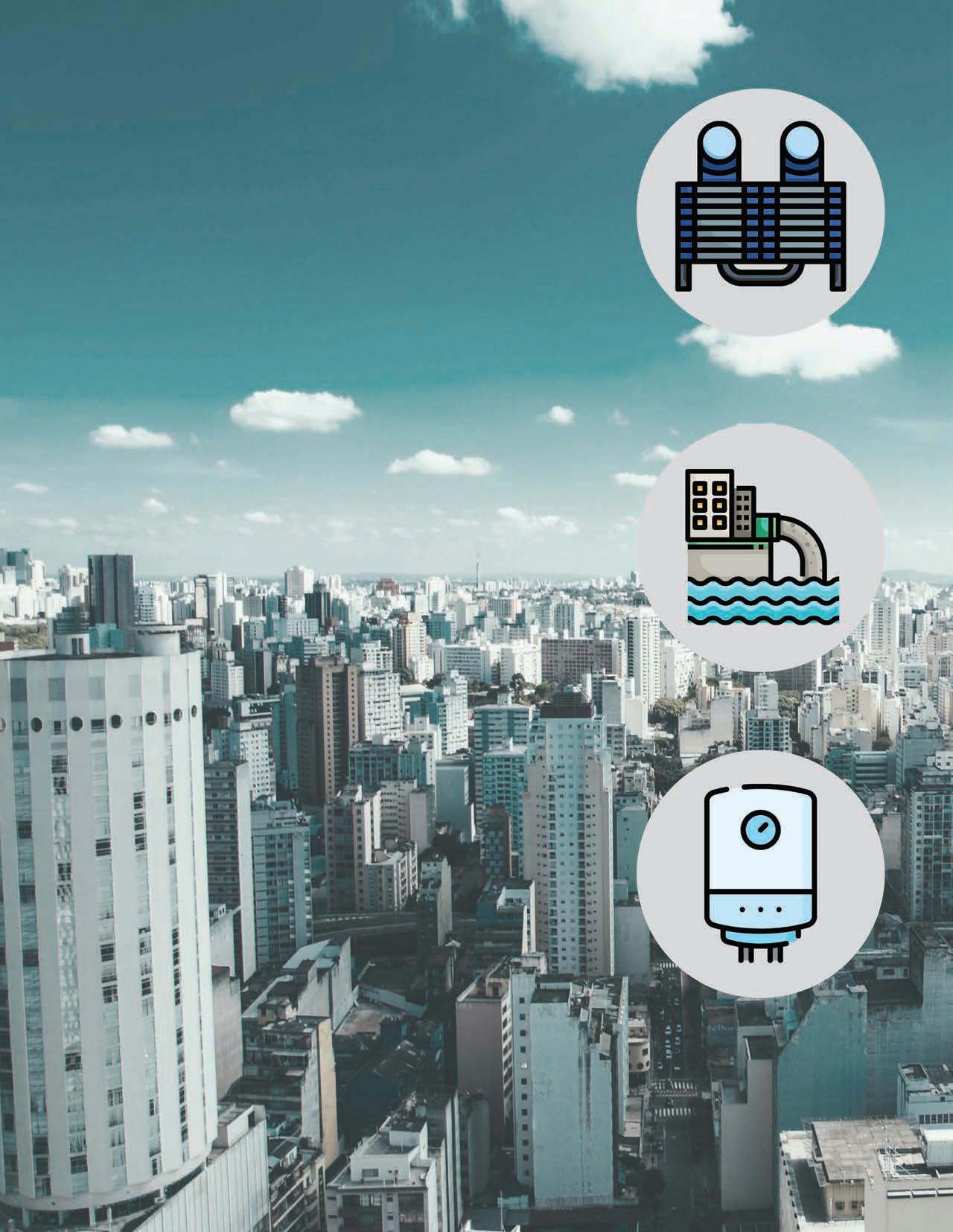
65 minute read
How Can the IoT (Internet of Things) Support Industrial Water Treatment?
Laith Charles, Watermark LLC
A dynamic and evolving landscape of connected technology presents a daunting opportunity to revolutionize the way we manage water treatment. With current technology, it is possible to know immediately when there is a system upset. Most new treatment equipment is either equipped with a connectivity standard or has an optional upgrade.
This wave of connected devices presents a future where online visibility to all your system parameters is at your fingertips. The price point of connected equipment is decreasing, and the number of available connected options is increasing. Meanwhile, the cost of labor is going up, and the supply of labor is scarce. This article will analyze the current state of conventional water treatment methods, highlight some existing Internet of Things (IoT) augmented water treatment methods, and project theoretical use cases and future IoT water treatment models, leveraging connected devices to either optimize workflow or heighten quality control.
Origin of Networked IWT Controllers Interconnected controllers predate to the 1990s. For example, Pulsafeeder’s MCT210 system was established in 1991. It came with the Layer 2 Connection (L2 option) and was capable of interfacing with a networked computer through an analog modem. Also, a software suite called PULSAworks allowed users to access realtime system values by remotely changing operating parameters, viewing historical data, and even receiving a callout in the event of alarm conditions.
The percentage of controllers sold with connectivity in the early 1990s was around 5% due to the large costs associated with getting equipment networked as well as the added cost of modems and need for a clean analog line. The equipment sales were simply pre-purchasing the communications functionality for future connectivity of which was rarely leveraged. Over the years, these previously premium and costly functions became more cost competitive. For example, analog-wired connections became reliable digital connections that could either be wired or wireless. Less reliable one-way protocols were even replaced with complete communication stacks; however, these initial improvements led to lackluster market adoption and diminished the value sell proposition of the platform. First generation networked controllers were also pointto-point communications with limited access to a single controller at a time. Building out multiple processes at a specific location was often time-consuming and extremely cumbersome. These were groundbreaking features in this market, but it was still not enough. The introduction of first-generation interconnected controllers did not exhibit any noticeable market push on water treatment. The reliability, scalability, capability, and overall installed cost all needed to significantly improve to drive adoption rates.
Current State of Networked Devices Most middle market industrial water treatment controllers are still not actively networked. Much of the existing installed infrastructure is simply incapable of managing a network stack and connecting to the internet. Newer middle market controllers in the last 10 years can handle all these protocols and more: Modbus, Building Automation Control Network (BACnet), and the full Transmission Control Protocol/Internet Protocol (TCP/ IP) stack to get on the internet. Depending on the equipment and the manufacturer, systems can either interconnect with an optional communications card or remain standard with the base controller.
Additionally, cellular modems can get process controllers online without relying on the customer’s ethernet connection. The price point of online-capable devices has decreased, and the value proposition of the online capabilities has improved along with the demand for connectivity options. Depending on how you define middle market industrial water treatment, only about 40% of new controllers sold in 2020 are equipped out-the-door with networking functionality, and a much smaller percentage of these devices are ever networked. Approximately 4 to 5% of current state middle market process controllers are networked; however, several market conditions are forcing water treatment to leverage online connectivity. Some of the factors driving connected options include competition, regulation, resource management, and customers.
Current State of IoT Currently, there are several technophilic companies choosing to standardize on remote communications. These companies leverage cloud connectivity and the added value of online tools as part of their business
model. To do this, they either build in the price of connectivity in their service contracts or apply it as a fixed overhead expense as an integral part of their operations. Some companies, either by choice or to stay within regulatory compliance, are forced to lean on connectivity. Largely as a response to heightened visibility to Legionella, some regulations allow for lesser testing intervals when treatment is supported with online controllers. Markets are also pushing to migrate to a connected equipment package due to competitive pressure, upselling services, or compliance reasons. To remain in compliance, the market share of connected devices has been growing steadily, and within the next few years, the majority of sold controllers will have connectivity options standard, with around 25% of new controllers expected to be capable of 24/7 online service.
In the last five years, regulatory entities have increased their supervision of evaporative cooling systems. The presence and risk associated with Legionella has been a driving factor for more legislated oversight. This is leading companies to find creative ways to meet the heightened testing and reporting requirements. New York City is the most stringent area in North America for keeping open-loop cooling systems compliant. For example, New York City Chapter 8, Title 24 requires performing routine manual water-quality monitoring of temperature, pH, conductivity, and biocide concentration.
To remain compliant, monitoring must occur at least three times per week with no more than two days between monitoring. This manual process is required unless it is automated. To replace the need for manual testing, reports from IoT-augmented water treatment equipment can be used to stay in compliance instead. Without online visibility, facilities personnel would need to perform the testing, the number of required service visits would need to skyrocket, and the cost of a service contract would increase to counterbalance labor elements. In this instance, many accounts simply upgraded all the water treatment equipment to online as well as having a dedicated online controller. This option was much easier than tripling your workforce overnight or reducing the capacity of the current staff.
While leveraging online connectivity and reporting is great in theory for automating an otherwise very manual process, reliability of this solution is paramount. In the real world, there are still some hurdles to overcome. If we shift our mentality to require online connectivity as an integral part of our business to manage our evaporative cooling systems, which is common in New York City to maintain regulatory compliance, then reliability becomes vital. We want technology and connectivity to synergize and augment our business as usual and automate what would otherwise be manual processes.
However, R. Baskin (1) reported in a technical paper from the 2018 AWT Annual Convention that this is easier said than done. “Several setup steps have now been added to our standard start-up procedure,” he stated at the conference. Mr. Baskin reported on the need to bring controllers in house for configuration prior to deploying on the field. Additionally, the pain point of establishing a cell modem connection and maintaining it reliably over time is one more thing to manage, as it commonly complicates installs. “Initial connectivity can require changing which cellular carrier the modem connects to or feeding long antenna wires up a few floors where there is a better cell signal,” he said.
Since these installs depend on connectivity, Mr. Baskin has invested in several internal resources to develop failsafes and procedures to detect if a modem or controller were to go offline and stop reporting so that they can quickly troubleshoot and keep their customers compliant with reporting requirements. He is constantly looking for smarter tools that work with his company and solve problems versus creating different problems. When everything is functioning as it should, these tools help remove burden and unnecessary busy work from the working day so that they can focus on other aspects of their organization.
Another real-world application for leveraging IoT devices to augment water treatment is a passivation treatment developed by EVAPCO that allows end-users to put an immediate heat load on a newly installed cooling system. The process involves two steps: 1. A factory applied pretreatment, and 2. A tightly monitored and controlled in-field passivation process. The in-field portion of the passivation requires site-specific chemistry, a local service provider, help from the installing contractor, and the cooling tower maker’s feed and control panels. Remote monitoring of this process through an online
portalA allows for 24/7 visibility to critical system parameters during the infield passivation process to help identify potential issues before they become problems.
The partners work with J. Downie (2), a startup and commissioning specialist at EVAPCO Water Systems, to set up site-specific reports and alarms. In personal communication with the author, Mr. Downie observed that “the response from our partners is that they like getting the daily reports to see how the passivation numbers are trending. The ability to see real time data reduces site visits and improves the passivation outcomes for our customers.” This technology use-case adds a level of quality control to the critical passivation process and ensures, should any system upsets occur, that swift corrective actions can be implemented prior to any system damage.
Theoretical Uses of IoT Continuous innovation of industrial water treatment equipment presents vast possibilities. Today’s largest water treatment issues can be largely solved by some future technology, and some of this technology already exists in either an adjacent market or at a higher price point. With current technology, it is possible to connect a cooling tower controller to the internet and receive routine graphical reports of key system parameters (see Figure 1).
Additionally, an immediate notification can be sent to a smartphone, or as an email, about any system upsets, such as high conductivity. While simple knowledge is powerful, knowing that key parameters stay within desired ranges allows us to validate quality of service for self-verification, company quality control, and a high service level to the customer. How else can we leverage data today? What are some improved workflows using technology in today’s state that allow for efficient use of all our resources? For a little bit of theoretics, if all our control equipment were online and reliably networked, could we fundamentally shift our service model? With complete transparency to all probe measurements, tank levels, water meters, and more, it is simple to mine information from accounts prior to rubber hitting the road.
Figure 1: Example of controller probe and relay data.
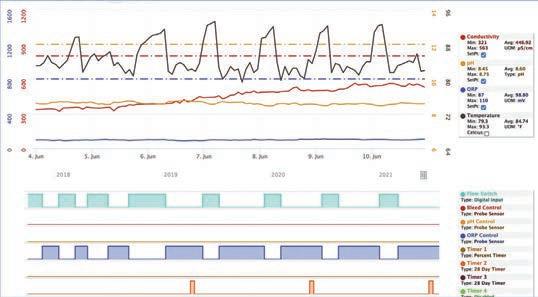
For instance, an online controller goes into a high conductivity alarm. The water system supervisors get notified at 9:23 am of the system upset. There are at least two distinctly different reaction scenarios. First, we confirm the controller status online and check some basic program parameters: the controller programming, presence of flow, and relay HOA (hands-off operation) status. After observing the controller’s information online, we notice the conductivity is indeed high and the controller has entered an alarm state as a result; however, the bleed relay is not currently energized. In a matter of seconds, we can deduce the bleed relay is in a lockout status and we have just fed one of our biocide timers. The controller is fully functional, but seasonal demand has changed, and the tower is cycling up faster than normal.
As a solution, we can remotely make some adjustments to the program to compensate for this seasonal swing by making minor tweaks to the pre-bleed and lockout settings on our biocide timer. One hour after the lockout period has expired, the bleed relay can open again, our conductivity goes back within range, and we get notified that the alarm has cleared. We now have a more refined program and did not need to adjust our schedule to accommodate an emergency visit.
In another reaction scenario, when we check our high-conductivity alarm, we might see that the bleed relay has been energized for hours. Despite the continuously energized bleed valve, the conductivity in the
process continues to rise. When the probe measurements do not match our control measures, we know there is something wrong, and we would like to notify onsite personnel and schedule an impromptu service visit to remedy the issue. Knowing the exact failure mode being troubleshot and seeing the controller online prior to going onsite can ensure that you bring the correct components to fix the issue the first time. With the right spare parts kit, you can pull in the timeline to remedy the issue and reduce burden involved. This accelerated responsiveness will help reduce company attrition rate, improve the percentage of time your chemistry is within desired control ranges, and fix most issues during the initial visit as opposed to making multiple trips. All these measures impact a company’s internal operations, such as account retention and human resource management. Keeping accounts and freeing up time are invaluable for having companies operate at their best. Nevertheless, these benefits still amount to customer hesitation. The upfront burden of modem costs, setup fees, and the recurring data fees frequently seem difficult to justify. Additionally, the learning curve of figuring out a process and training your team to support connectivity can seem intimidating. These factors have stacked up to push a lackluster market adoption. On the other hand, many of the benefits of optimizing the controller programming are based on historical performance, and the cost impact of response time to the end-user is astronomical. Simulation of the operation of a water treatment system is important because it will show an end-user the likely opportunity cost when a process control system is used. To be consistent, let us take the high-conductivity example and run a simulation where we compare efficiency loss in a chiller as a function of response time. Statistically, without customer intervention, we will catch process issues at 50% of our service interval. Conversely, if we are notified of high conductivity online, then we should be able to remedy the system within 24 hours of receiving the alarm. Table A shows the system parameters of a computed simulated failure mode.
Table A: Sample Water Characteristics for Simulated Model
Parameter Value Frequency of service 30 days Cycle of concentration setpoint 3.5 Makeup conductivity 150 S/cm Makeup total alkalinity 120 ppm Makeup calcium hardness 40 ppm System tonnage 500 Drift rate 0.05% Cost of power 15 c/kWh The cost of operating a chiller with these On the other parameters (as featured in Table A) for hand, many of a year at 6,500 hours and a 70% average load during operation is approximately the benefits $220,000 per year. The difference in of optimizing responding in 24 hours to system upsets the controller versus 15 days is exorbitant for scale deposition. Deposited scale will indefprogramming initely add to chiller inefficiency until are based on historical removed, which typically involves some level of system shutdown. Responding within one day leads to less than 1 mil performance, of deposition in our simulated example, and the cost impact of and conversely, responding in 15 days to this upset leads to over 1/64th of an inch of scale deposition (see Figure 2). This response time to would cause a site’s chiller to be 16.2% the end-user is less efficient and likely lead to other issues within the evaporative cooling astronomical. system. Within the 15-day span alone, the end-user would spend ~$1,200 more in energy. Should the scale stay on the chiller tube over the course of a whole year, it would cost an extra $35,640 per year to run that 500-ton chiller. The interesting aspect of this simulation is that scale does not deposit immediately. The Langelier Saturation Index (LSI) needs to be in a scaling state for some time before the point of nucleation begins; then, scale will ramp up the speed of deposition until the flow of the water in the chiller starts breaking off the deposits. The rate of deposition drops off asymptotically. The key difference is response time. A detailed view of the math used to power this tool can be found at: https://ewatermark.net/murphys-law-of-scaling-up/. This is a great example of a value-add service, as online visibility can remove burden from customers and empower them with
visibility to the process to ensure better quality control of the water treatment program.
Figure 2: Graph of simulation example.
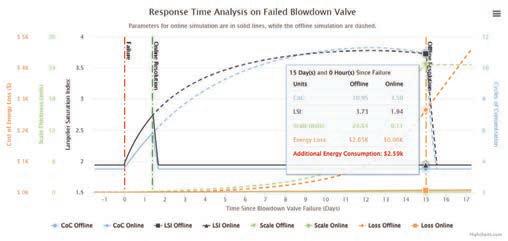
Future Market Needs The current state of water treatment control technology is just the tip of the iceberg. While there is a lot we can do today, several innovations will need to follow suit to improve this platform. The Metro Group on the Eastern Seaboard have been working with online controllers for over six years. For The Metro Group to comply with state and local regulations in New York, online visibility and reporting is convenient and has even become necessary for some clients. Although of course, the equipment is only as good as its ability to measure important species in water.
While some probes like a toroidal conductivity probe are extremely robust where measurements do not drift over time, industry standard pH and oxidation reduction potential (ORP) probes degrade and require eventual replacement. V. O’Reilly (3) of The Metro Group believes sensor electronics still have a way to go to meet the market needs, as current probes are either relatively cheap and require more frequent calibration and replacement or they cost too much for the market to bear. When you need to make water treatment decisions based on your online controllers’ capabilities, you must be able to trust that your probe readings are accurate.
Conclusion The power of future state process data on a large scale specific to water treatment systems is exciting. Today, technology can lead to incremental process improvements and optimizations that will spread over all the accounts we manage. Water and energy are both valuable resources. As water treatment professionals, equipment manufacturers, and chemical blenders, we can make a massive difference to the use of these resources. The amount of energy and water we are responsible for as an industry is astronomical, and it is a moral obligation to police the efficient use of them. Who knows what exactly the future looks like? We might have predictive failure analysis for systems performed on the cloud side, merging of data between a chiller and its efficiencies and the water treatment program, a simplification of connectivity process and more and more smart devices managing processes. These advancements will compound all the time and raise the bar of industrial water treatment and expose opportunities in the marketplace. We are at a critical time in water treatment. Enforced regulations are trending toward becoming more stringent. Our labor pool shortage and rising cost of talent will either force an increase in the cost of services or force innovation to efficiently use what resources we have.
As the technology price continues to drop and connectivity becomes more affordable and streamlined, the opportunity for upselling services and removing complexity from the current status quo will be interesting to watch unfold. Whatever the future looks like or becomes, IoT will play an integral role in the next evolution of water treatment.
References
1. Baskin, R. (September 2018). “Legionella from a Water Treater’s
Perspective,” presentation at AWT Annual Convention & Exposition,
Orlando, Florida. 2. Downie, J. (Spring 2021). Evapco Water Systems, Manchester, Maryland, personal communication with L. Charles, article author. 3. O’Reilly, V. (Spring 2021). The Metro Group, Boston, Massachusetts, personal communication with L. Charles, article author.
Endnote
A The online portal mentioned in the text is through Pulsafeeder’s Pulsalink.
Laith Charles is president of Watermark, a manufacturers’ representative of water treatment equipment, and CTO of Dosinfection, an OEM/distributor of hydronic solutions. He is the first recipient of AWT’s Rising Star Award and a degreed electrical engineer, who is focused on improving sustainable-use and resource management of aquatic systems. Mr. Charles can be contacted at laith@ewatermark.net.
This paper was presented at the 2021 AWT Annual Convention & Exposition, which was conducted September 22–25, 2021, in Providence, Rhode Island.
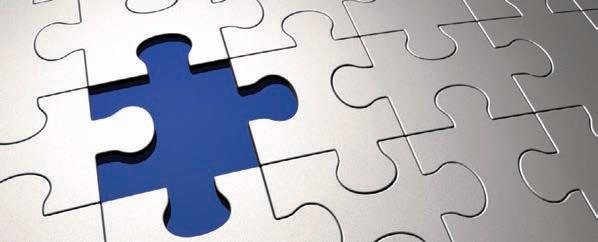
Be Sure You’re Taking Advantage of Your AWT Benefits:
Sign Up to Receive Emails From AWT. Did you know you can manage the notices you receive from AWT? It’s the best way to ensure you learn about all AWT benefits in a timely manner.
Sign in to the AWT website and select your communication choices and complete your profile today. If you have trouble signing in or have any further questions, please contact:
Angela Pike
Senior Member Services Manager (240) 404-6477 apike@awt.org
H2OH2O
AquaPhoenix Launches Aliquot Pro, a Free Mobile Companion App for eSR AquaPhoenix announces the launch of Aliquot Pro, a free mobile companion app for eSR that is included with every company’s subscription. Aliquot Pro is designed to give you and your customers the ability to manage data from any location and device.
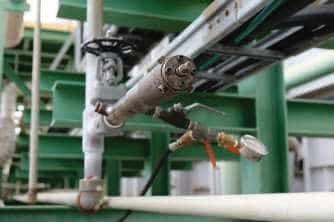
When used together, eSR and Aliquot Pro allow you to create a centralized location for data entry, data storage, and analysis. Key features of the app include:
View Last Three Results – See recent test history when writing reports (online mode) Turnkey Report Entry – Automatically sync data directly to your eSR site Voice-to-Text
Comments – Quickly dictate report comments using voice to text Controller
Connectivity – View recent data history and connect to your compatible controller
Aliquot Pro is available for download on the iOS app store and Google Play. For more information, visit www. esrflexreports.com/ aliquotpro.
For more information about AquaPhoenix Scientific, visit www. aquaphoenixsci.com. Cortec’s VpCI®-641 Hydrotest Corrosion Inhibitor Earns USDA Certified Biobased Product Label Cortec® Corporation is pleased to announce that VpCI®-641 and VpCI®-641 PTSA corrosion inhibitors for hydrotesting and freshwater cooling systems have earned the USDA Certified Biobased Product label. These products represent Cortec’s commitment to developing technologies that use biodegradable and renewable materials where possible, allowing industries to fight corrosion in an environmentally responsible manner. VpCI®-641 offers an economical, “greener” alternative to other hydrotesting products on the market that are not biobased and must be used at a higher dosage.
VpCI®-641 is a water-based blend of contact and vaporphase corrosion inhibitors for protection of ferrous and non-ferrous metals (including copper, aluminum, and brass) in industrial waters. VpCI®-641 contains 69% USDA-certified biobased content and can be used at fairly low concentration levels for greater economy and lower conductivity. VpCI®-641 provides corrosion protection during hydrostatic testing and in some cases can be used in closed-loop cooling systems filled with fresh water. VpCI®-641 PTSA includes a PTSA tracer option that makes it easier to monitor proper concentration for ongoing effectiveness in closed loops and reused hydrotest water. When it comes time for wastewater disposal, VpCI®-641 makes the process easier as a biodegradable water treatment product that does not contain nitrite or phosphate inhibitors.
“We applaud Cortec® Corporation for earning the USDA Certified Biobased Product label,” said Vernell Thompson, USDA BioPreferred® Program. “Products
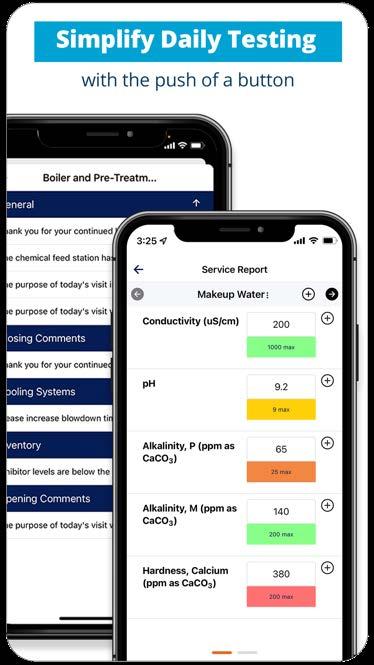
H2SO4H2SO4
from Cortec® Corporation are contributing to an everexpanding marketplace that adds value to renewable agriculture commodities, creates jobs in rural communities, and decreases our reliance on petroleum.”
In addition to creating an opportunity for industries to demonstrate their commitment to sustainability by the voluntary use of biobased products, the USDA BioPreferred® Program also includes a mandatory federal purchasing initiative for federal agencies and their contractors, with special biobased purchasing requirements for products in 139 identified categories. VpCI®-641/VpCI®-641 PTSA surpasses minimum biobased content requirements under the Corrosion Preventatives category (53% minimum biobased content). By using these products, federal agencies and contractors can comply with federal purchasing preferences in their everyday product acquisition. For more information, visit https://www.cortecwatertreatment.com/contact-us/.
FAS-DPD Testing for Sanitizers From Taylor Technologies FAS-DPD is a method for testing sanitizers that uses drop-wise titration instead of color matching.
Why Choose FAS-DPD?
No color matching needed. Even a user with color vision deficiency can see the color change at the endpoint of the titration from pink to colorless. Read chlorine as low as 0.2 ppm and as high as 20 ppm without reagent bleaching. There is no wait time for full color development. This method is accurate and repeatable, no matter what the lighting is in your facility. No electronic meter is needed to read the results.
Testing for chlorine and other sanitizers is essential for protecting food safety. Many facilities rely on colormatching tests to determine chlorine levels, which can result in human error when comparing the pink color created (especially in fluorescent lighting). For a complete listing of our water-testing products, visit www. taylortechnologies.com. French Creek Software Awarded Innovation Award At the end of June, hundreds of industrial process heating and cooling equipment professionals gathered at the Donald E. Stephens Convention Center in Rosemont, Illinois, for the inaugural Process Heating & Cooling Show.
The inaugural Innovation Award was presented to Robert J. Ferguson for French Creek Software, the industry-standard modeling program for cooling water systems. “Rob developed the first easily understood method for interpreting scaling indices that is widely used and accepted. He also has developed and implemented the concept of 3D graphs of operating profiles that indicate scale potential and the associated inhibitor dosage and failure points,” noted Michael Bourgeois of Chemco Products, one of several to nominate Robert for the award. French Creek Software was founded by Robert and his wife, Janet, in 1989. In accepting the award, Ferguson credited his wife, who played integral roles in the company while the couple raised their family. “Rob and Janet’s contributions to those involved in water cooling cannot be overstated,” said Linda Becker. “Their modeling software provides the foundation for numerous programs still in use today to optimize cooling water treatment selection, troubleshooting and evaluation.”
The Innovation Award was created to recognize the innovative application of technical expertise or experience with industrial process heating and cooling equipment and projects or efforts to reduce costs, improve thermal processing efficiency, and increase safety. In Robert’s honor, a $1,000 scholarship was made in his name at the University of Minnesota, College of Biological Sciences, AXE Professional Chemistry Fraternity.
Lakewood Instruments 7838 N. Faulkner Road Milwaukee, WI 53224 Phone: (414) 355-2807 (800) 228-0839 csd@lakewoodinstruments.com Website: www.lakewoodinstruments.com
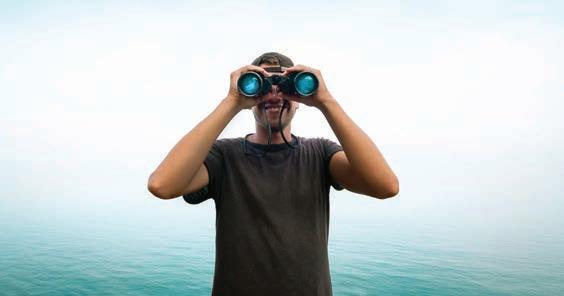
Company History
Founded in 1973 in Compton, California, Lakewood Instruments was among the first companies that manufactured water treatment controllers. When expansion was needed, founder Bob Doenges moved the company to Glendale, California. In 1994, Lakewood was purchased by Osmonics and moved to Glendale, Arizona. In 2000, Osmonics was bought by GE and became part of GE Water. In 2003, GE moved the operations to Glendale, Wisconsin, and then in 2005, Bill Brink purchased Lakewood. Mr. Brink also owns ETI, the manufacturer of the printed circuit board components used in Lakewood products, and he moved the operation to Milwaukee, Wisconsin.
Current Business
Lakewood Instruments designs, manufactures, and sells cooling tower and boiler conductivity and chemical feed controllers for the water treatment industry. Other parameters, such as pH and ORP, can be controlled using numerous user-configurable feed schemes inherent in the company’s controllers. In addition, Lakewood provides drum switches, various transmitters and pre-amplifiers, plumbing accessories, water meters, and process sensors. The company’s goal is to work with water treatment service, and chemical providers, by meeting and exceeding their facility water treatment equipment needs.
Geographic Areas Served by the Company
Lakewood Instruments currently serves all parts of North America from its Wisconsin location.
AWT Membership
Lakewood Instruments has been a member of AWT since the early 1990s.
AWT Awards
Lakewood Instruments was honored with the AWT Supplier of the Year Award in 2011.
Top Executives
Bill Brink, President/Owner; Donald Wiseman, Director of Operations and Marketing; Paul Peacock, Regional Sales Manager.
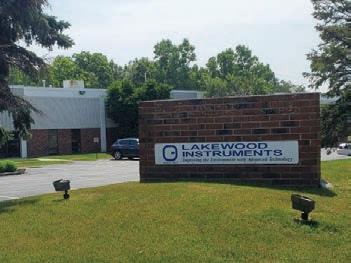
Lakewood Instruments offices in Milwaukee.
Radical Polymers, LLC 4138 South Creek Road Chattanooga, TN 37406 (423) 316 9877 www.radicalpolymers.com
Company History
Radical Polymers was founded by Mike and Leslie Standish in 2014 with the purpose of serving independent water treatment companies with differentiated products backed by extensive comparative technical data. Radical Polymers launched its business at the 2014 AWT convention in Dallas, Texas. In 2016, Radical Polymers purchased its current facility in Chattanooga, Tennessee, where the company has extensive lab and pilot testing facilities. MFG Chemical purchased Radical Polymers on July 1, 2022. MFG, led by Paul Turgeon, is headquartered in Chattanooga and has extensive manufacturing capabilities for polymers and other water additives at its North Georgia manufacturing facilities.
Current Business
Currently, Radical Polymers offers a wide range of polymer technologies for mineral scale and deposit control. The range of applications for the products include cooling towers, boilers, mining, geothermal, and other process water applications. Within the current range, several of the company’s polymers and blends are also NSF 60 registered for use in RO drinking water applications. Radical Polymers dedicates a large portion of its resources to product development and technical service. This has led the company to develop an extensive data package for each of its products and recent granting of a U.S. patent for the use of INITIA® 585 and related maleic technologies.

Skid for testing treatment chemical performance inside company plant.
Geographic Areas Served by the Company
The company serves clients in North America, Europe, the Middle East, and Asia.
AWT Membership/Involvement
Company partner Mike Standish became an AWT member in 1990. Radical Polymers joined AWT in 2014. Radical Polymers has presented papers at AWT conferences, of which two have been published in the Analyst. Mr. Standish has served as a supplier representative on AWT’s Board of Directors.
AWT Awards
Radical Polymers received the 2018 AWT Supplier of the Year Award.
Top Executives
Mike Standish, Vice President–Water Additives; Leslie Standish, Co-Founder; Chelsea Farmer, Product Manager; Paul Turgeon, CEO–MFG Chemical.
Scranton Associates, Inc. 17647 Foltz Parkway Strongsville, OH 44149 (440) 572-2277 www.scrantonassociates.com
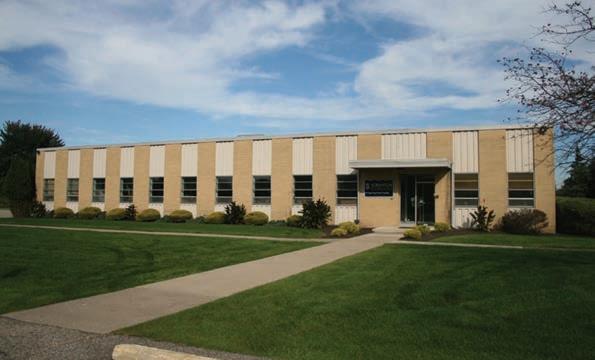
Scranton Associates Company headquarters in Strongsville, Ohio.
Company History
In 1919, Leo A. Lux began to manufacture water treatment chemicals in downtown Cleveland, Ohio. In 2008, Scranton Associates moved to our current facility in Strongsville, Ohio, about 20 minutes south of Cleveland. Scranton Associates is a family-owned business, celebrating 100+ years and four generations.
Current Business
Scranton Associates manufactures (or blends, combines, dilutes, neutralizes, repackages) high-quality water treatment products to your specifications on a privatelabel basis only. Scranton Associates is an EPA-approved establishment; we are able to formulate, repackage, and re-label biocides. predominantly for the industrial water segment. Our formulations include cooling tower products, boiler products, condensate treatment products, closed-loop treatment products, glycol inhibitors, cleaners, and wastewater products, among others. We do not sell to end-users, so as never to compete with our customers. We maintain the confidentiality of customer formulas and lists. Our services include technical and regulatory support, expert assistance in developing and improving customer formulas, and SDS/label services. We offer both liquid and powder blending capabilities.
Geographic Areas Served by the Company
From its Strongsville, Ohio, location, Scranton Associates serves clients in North America and the Caribbean.
AWT Membership
Scranton Associates has been an AWT member from the start. Bob Cavano has written many papers over the years, as well as the Raw Materials Specifications Manuel. Lee Cavano and Jill Cavano have both taken active volunteer roles within AWT. Lee continues to be active on the Legislative and Regulatory Committee; he was a former “Leg/Reg” Committee chair. Jill serves on the Young Professionals Task Force and is currently the chair of the AWT Business Resources Committee.
AWT Awards
Scranton Associates was awarded the Supplier of the Year award in 2015. Robert (Bob) Cavano received the Ray Baum Memorial Award in 1992.
Top Executives
Jill Cavano, President; Lee Cavano, Technical Director.
Chris Turnbull, CWT
Guardian CSC Bedford, PA
What prompted you to obtain your CWT, and when did you begin the process by taking the test?
Guardian CSC has always been focused on technical training for their employees, so very shortly after I entered the water treatment industry, I was told about the CWT. The encouragement and support from the other CWT’s within the company was also a great influence in my pursuit of the CWT.
I was also prompted after going to the AWT technical training seminar for the first time and seeing the amount of knowledge and experience the members had and were willing to share. During these seminars, I could begin to see just how much there is to learn (and how much I did not know). After that, I made it a goal to focus on the technical aspects of the industry and work toward obtaining the CWT certification.
Why do you feel this credential was important to have?
The CWT credential is the gold standard for our industry. It demonstrates that we as water treatment specialists take our profession seriously and are willing to invest the extra time to gain the knowledge and experience needed to acquire this credential. The importance in having a group of well-educated and ethical individuals goes a long way to gaining respect for the entire industry. To be part of this group is a great honor.
There are many advantages to having the CWT designation. The CWT is well known within our industry and has aided me in starting new relationships with others in the water treatment field and provided me with opportunities to build even more. This ability to network is vital to staying up to date and providing the best possible services to our customers.
Also, the CWT designation is a conversation starter. Many times, prospective customers have asked about the designation and it has given me the chance to discuss the advantages of working with a CWT. In turn, our current and prospective customers can see an objective measure to our level of competence and the dedication that we have to our profession.
The CWT designation has improved my professional career by building my confidence in my ability and knowledge of water treatment systems. The continuing education requirements also help me stay up to date on the different technologies, both chemical and equipment, that are out there.
Having my CWT has also improved my career by helping set myself and my company apart. Being able to provide the extra value that comes with the CWT to our customers is very helpful in building and maintaining relationships.
What has been your greatest professional accomplishment?
I would have the say that my greatest professional accomplishment has been building strong, long-term relationships with my customers. It is very rewarding to be thought of as a resource and partner when it comes to troubleshooting complex issues or helping to conserve resources.
Daniel Merritt, CWT
CH2O, Incorporated Olympia, Washington
What prompted you to start volunteering with AWT?
I got started in the water treatment industry in February 2002 in Albuquerque, New Mexico, with Industrial Water Engineering. Two months later I was sent to my first AWT Technical Training seminar in Atlanta—talk about drinking from a fire hose! I had previously been a high school science and math teacher, so at least some of the math made sense! I was impressed by the depth and quality of the presentations, the professionalism of the instructors, and the genuine desire of AWT to provide some of the industry’s best-quality training. I have always had a desire to train and teach, so when the opportunity came up to help as an instructor, I was truly honored. I never imagined back then that someday I would have the opportunity to become part of the same training!
What has been the most rewarding thing about volunteering?
Being able to invest in and hopefully inspire the upcoming generation of water treatment professionals. I joke that I never thought in a million years I would still be in water treatment after 20 years! The water treatment industry has provided more than a job for me—it has become a career and helped develop parts of my professional character and expertise I didn’t know I could achieve.
It has linked me with a family of professionals that I can reach out to and expect to receive honest and industry-leading advice. It has also given a competitive edge when prospecting new business or handling challenges with current customers when they know that you are part of a professional group, such as AWT.
Why would you encourage others to become a volunteer?
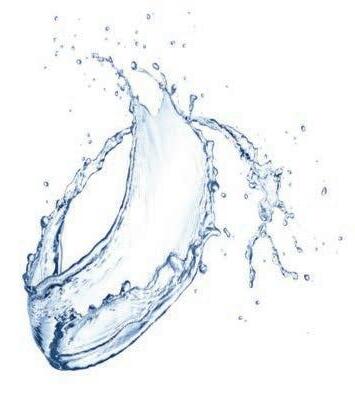
In the world of mentorship, you should always have someone you’re learning from in order to grow. You should also always pour into others to pass on that knowledge. Volunteering with AWT has given me both opportunities at once.
Tell us about a current project you or your committee is working on?
I’ve been honored to take on the role of teaching the chemistry portion of the Water Treatment Training seminar. We are working on creating a module that will help solidify the basic chemistry knowledge needed for professional water treaters and help tie that knowledge to the other aspects of the water treatment industry.
What is a past project that your committee produced that you feel has had the greatest impact on AWT and why?
I also helped in the beginning stages of the online course Introduction to Water Treatment. This course has been a great help to our own company’s initial training for new hires to give them a solid understanding of the basics of water treatment.
How have you been able to utilize the expanded business connections you’ve made while volunteering?
Many of the leading vendors who provide chemistries, testing, and/or equipment also attend many of the AWT events and trainings. Several times, we have met the right people at the right time to help with current needs or projects during AWT events, either at lunch or after a presentation—or right at the bar!
The Midterm Elections— What to Watch For

The 2022 midterm elections are fast approaching and both Democrats and Republicans have a lot on the line, including control of both the House of Representatives and the Senate. Midterm elections are almost always a referendum on the incumbent president, and generally the most closely watched indicator in a midterm election is the president’s approval rating. President Biden’s approval rating average is in the low 40s, pointing to serious losses for the Democrats.
Additionally, in the past three decades, both parties have suffered major midterm losses in the House two years after capturing the White House. Democrats lost 54 House seats under Bill Clinton in 1994 and 63 seats under Barack Obama in 2010. Republicans lost 42 seats under Donald Trump in 2018.
Here is a summary of the most vulnerable Senate and House seats, and governorships this November.
Senate: Currently the Senate is evenly split between the two parties. Therefore, a pick-up of only one seat for either party means they will control the Senate. Of the 35 seats up for reelection this year, 14 are held by Democrats. Republicans will be defending 21 seats. These seats are the ones to watch.
Georgia: An especially competitive race is shaping up in Georgia, where incumbent Sen. Raphael Warnock (D) will face former NFL running back Herschel Walker. The Republican has high name recognition but is untested as a candidate and faces allegations of domestic abuse.
Arizona: The state is in the spotlight as Sen. Mark Kelly (D) hopes to win his first full term in the Senate. With voters giving Democrats low marks on the economy and immigration—two defining issues for Arizonans— Kelly’s challenger is sure to be competitive.
New Hampshire: Sen. Maggie Hassan (D) won by just over 1,000 votes in 2016, and in a year that so far is trending in Republicans’ favor, she will be vulnerable in November.
Nevada: Of all the competitive races with Democratic incumbents, Republicans are most bullish about Nevada. The GOP has been hammering Democrats for prolonging COVID restrictions that hurt Las Vegas’ tourism-based economy.
Wisconsin: The most vulnerable Republican this year is Ron Johnson, whose job approval rating is lower than Biden’s.
Pennsylvania: This state has quickly become a battleground, ever since the Republican incumbent, Patrick Toomey, announced his retirement.
House: Republicans need a net gain of just five seats to retake the House majority. Current thinking is that 26 Democratic-held seats are considered toss-ups or leaning Republican. By contrast, only nine Republican-held seats are toss-ups or leaning Democrat.
In 2020, Republicans flipped 15 Democratic-held seats, and they are hoping to replicate that success this year by focusing on inflation and pointing to the rise in crime across the United States as evidence that Democrats cannot handle law and order. House Democrats are arguing that they are trying to counter inflation by pushing for tax cuts, providing child-care options, lowering prescription drugs costs, and fixing the supply chain.
In total, Republicans are targeting about 70 Democratic seats. They include seats in Arizona, Maine, Ohio, Iowa, and New Jersey.
Governors: There are 30 gubernatorial races this year. Democratic losses in Michigan, Pennsylvania, or Wisconsin would give Republicans full control of the government in those states. The three most competitive races are in Georgia, where Gov. Brian Kemp will be in a rematch with Democrat Stacey Abrams; Wisconsin, where Gov. Tony Evers (D) will have a tough battle for reelection; and Nevada, where Gov. Steve Sisolak (D) is concerned about possible erosion among Latino voters, long a prime constituency for their candidates.
The Issues: Several issues remain at the forefront of voters’ minds this year, including: Inflation and the economy: Inflation is a constant presence on the minds of voters when buying groceries, filling their gas tanks, or paying their home heating bills. Unless there is a considerable easing in the next few months, it will continue as one of the top issues of concern. The most recent polls show that nearly 7 in 10 Americans disapprove of the way President Biden has handled inflation. Fifty percent say they trust Republicans to handle the issue, compared with 31 percent who say they trust Democrats more.
Crime: Crime is another hot issue as many major cities are suffering from rising homicide rates and increases in other types of crime.
The border: The surge of undocumented immigrants along the U.S.-Mexico border continues to be a problem that the Biden administration has yet to bring under control.
Ukraine: The war in Ukraine is a wild-card issue. So far, Ukraine has not become a dominant political issue, in part because of support for Ukraine and advocacy of U.S. assistance by both parties.
Janet Kopenhaver is president of Eye on Washington and serves as the AWT Washington representative. She can be reached at (703) 528-6674 or janetk@eyeonwashington.com.
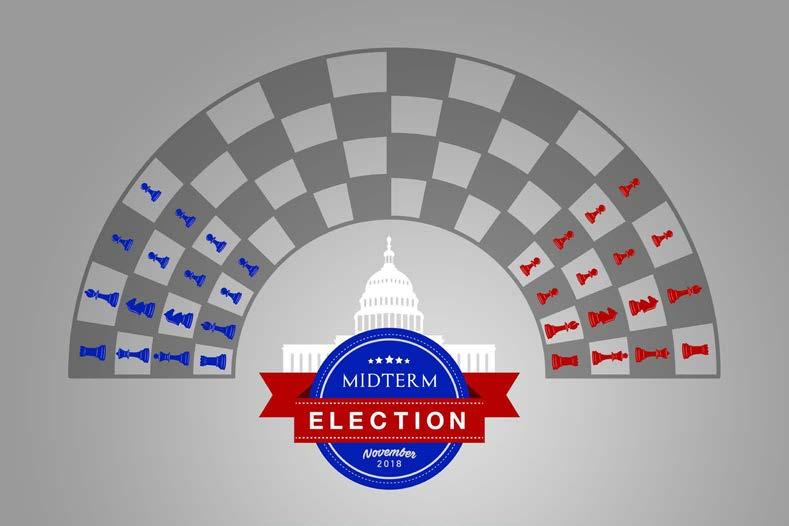
An Innovative Way to Attack Biofilm and Fouling
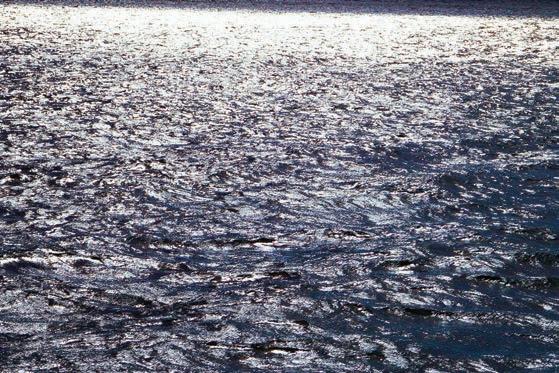
Jerry Angelilli, Consultant
Biofilm, biofouling, and corrosion can be serious problems in water systems. In this article, we will examine a creative solution that worked when we faced this issue at an end-user that made plastic bottles.
The Problem Biofilm and microbiological fouling were found in small-diameter channels of changeable molds in a large Eastern plastic bottle manufacturing facility. The molds are composed of various materials, but mostly proprietary grades of either stainless steel or aluminum alloys. To complicate matters, small fittings or other components like valves can also have copper-bearing alloys.
Situation This problem caused increasing downtime and falling production efficiency by decreasing the service-run length of molds before they had to be changed for cleaning. A variety of microbiocide products were applied under the direction of a water treatment consulting firm with little to no effect on correcting the problem. These molds are supplied by a semi-closed chilled water recirculating system. The system water is chilled by heat exchangers, sent to the process equipment, and then returned to tanks that are open to the atmosphere, which allows airborne contamination to enter the system.
Engineering Audit As part of the problem audit team, I participated as a representative of our engineering department for the existing water treatment chemical supplier. After a complete survey of the equipment, we compiled data on existing corrosion rates and microbiological dip slides, documenting the attempts to correct the situation with traditional chemical agents. This history included corrosion coupon results on carbon steel, a stainless-steel grade, copper, and an aluminum alloy to reflect various metallurgies in the system.
Background Employing different approaches to the traditional methods using chlorine dioxide, I have addressed biofilm and organism growth in a variety of water systems. I had successfully applied this chemistry to a once-through river water cooling system to eliminate biological fouling in a cement production facility with a former employer. In this application, a separate building was erected to house the generator and precursor chemicals. This particular method employed sodium chlorite, sodium hypochlorite, and hydrochloric acid. The customer requested a turnkey operation, so the entire process was kept under lock and key. I alone attended and serviced the generator and changed chemical drums.
My approach was selected over the competitive proposals of applying a typical organic biocide or using chlorine. Both of these methods required that that the chemicals be completely neutralized before discharging the water back into the river. These methods required additional chemicals and testing to prove no residual remained. With the low level of chlorine dioxide of 0.5 parts per million (ppm) applied, no testable levels of chlorine were seen at the discharge point with no neutralization process needed. The result of the application of chlorine dioxide was completely successful in treating the cooling water and remediating all microbiological fouling of cooling water channels.
As part of a team working with a large Southern university hospital system, I assisted in developing a unique process that was tried and proven to reduce water usage. Air-conditioner condensate is relatively pure water and is usually sent to drain. A system was devised and installed to collect this water from three different chiller plants with a connected chilled water loop. The biggest issue was to prevent biological fouling without complex biocide applications. Our recommendation was to feed chlorine dioxide at each recovery tank and pump the free condensate into the chilled water loop to overcome the water losses that were previously replaced with costly city water. By adjusting the treatment chemistry in the chilled water loop, we successfully kept corrosion minimized while saving the customer considerable operational costs.
Additionally, I served on a team to effectively use this technology to disinfect complete building water systems that were infected with Legionella bacteria. The first successful application was in a VA nursing home in the Midwest. After a total evacuation of patients and personnel, our team applied chlorine dioxide in a solution to the entire domestic water system to develop and maintain a 5 to 10 ppm residual for a period of 1 to 2 hours. Every tap in the building was tested to ensure a positive residual was held for the desired holding time. After the disinfection, the entire system was flushed with fresh water and every tap was retested to confirm that all chemical was gone. This similar procedure was applied in various other locations, including a large Gulf of Mexico coastal hospital whose water system was fouled by the storm surge after a hurricane.
As a member of a company task force, I also worked on applying chlorine dioxide in various oil field water system disinfection processes, which resulted in two patents for treatments in that area. This process was first applied to water impoundments in rural Arkansas, where a co-worker and I procured a rental trailer with a chlorine dioxide generator and had precursor chemical delivered to the site along with sections of hoses and a large pump to bring water into the generator trailer. There, the chemical could be applied and then returned by a discharge hose to the opposite side of the pond.
Within hours, we could observe dramatic changes in the clarity of the pond water. Disinfection was verified using serial dilution bottles prepared with specific agar for a variety of organisms, like total heterotrophic bacteria (aerobic) and sulfate-reducing bacteria (anaerobic.) After this simplified concept was validated, the team received approval for purchasing a trailer and generating equipment to control this application for use on a hydraulic fracturing site. This successful trial led to the development of a new subsidiary company; the purchase and erection of a manufacturing facility; the development of an application standard for the chemical residual necessary for these applications, and production of several state-of-the-art portable treatment and control trailers for use on hydraulic fracturing of oil and gas exploration sites in Arkansas, Oklahoma, Texas, Pennsylvania, and West Virginia.
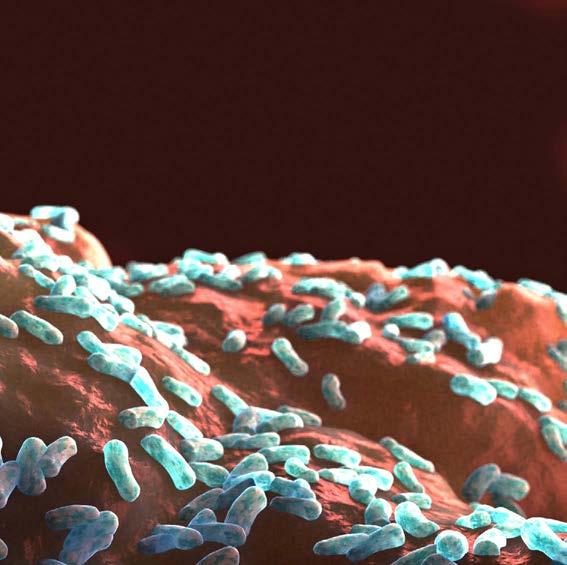
Problem-Solution Approach After completing the audit and data compilation, I suggested a two-fold approach to the problem at the plastic bottle molding plant. The first step would be to disinfect the system and remove existing biofilm by applying chlorine dioxide in a premade solution product of 3,000 ppm strength to prove the concept. Once the concept was validated, we would move to the second step, which would be to propose a permanent chlorine dioxide generator to the plant management for maintaining a low, continuous residual in the
Ways to Make Field Testing for Chlorine Compounds Simpler
Chris Golden, CWT, Taylor Technologies, Inc.
Introduction Regular testing for oxidizing biocides in water is more important than ever in the times of Legionella and diseases like COVID-19. Industrial water systems are frequently targeted as the source of illness, especially Legionella. It is the responsibility of professional water treaters to design, recommend, and implement programs that protect water systems and prevent outbreaks.
Oxidizing biocides have been widely used to maintain control against bacteria in water systems. Chlorine has been fed to municipal drinking water systems for years. In this article, we will focus on cooling tower waters. Chlorine and bromine products are a part of every open cooling water system’s treatment program, especially since the ANSI/ASHRAE Standard 188-2018 was published and the CDC issued the Legionella Control Toolkit. Details about each are noted below:
ANSI-ASHRAE Standard 188 (2018):
3. Water treatment. The legionellosis risk management plan documents shall include:
i. monitoring method and schedule for temperature measurements in the hot water and cold water systems. ii. monitoring method and schedule for measuring the chemical disinfectant residual or physical parameters in the hot water and cold water system. iii. procedures to address water supply interruptions or breaks in water supply piping. iv. procedures and schedule for maintaining water treatment system disinfectants, and v. water treatment products, the procedures for their application, and configuration that the products comply with applicable regulations.
Source: https://blog.ansi.org/2018/09/ansi-ashrae-standard-188-2018-legionnaires/
From the CDC Cooling Towers Toolkit:
Monitor water parameters, like disinfectant residual and pH, on a regular basis. Measurement frequency should be based on performance of the water management program or Legionella performance indicators for control. Adjust frequency according to the stability of performance indicator values. For example, the measurement frequency should be increased if there is a high degree of measurement variability.
Source: https://www.cdc.gov/legionella/downloads/Control-Toolkit-Cooling-Towers.pdf
Testing for the biocide residual should be an integral part of any risk management program. This testing should not be reserved for the water treatment supplier and their periodic visits but should also be part of the system owner’s regular responsibilities.
In this article, we will discuss several testing options and point out their advantages and disadvantages.
Testing Options The following methods are available for testing chlorine and its related compounds:
Test Strips Color Matching Colorimeter/Photometer/Spectrophotometer Titration
Test Strips
Test strips (Figure 1) can measure free chlorine and total chlorine. These can be good for quick chlorine checks, but they are generally not sensitive enough to measure the lower chlorine levels found in cooling tower waters. Test strips can come in various ranges, and the ones we would use for cooling towers would have an upper limit of 10 parts per million (ppm) as chlorine (Cl2).
Figure 1: Example of test strips.
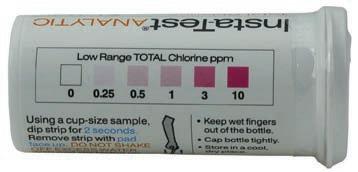
Source: LaMotte Co.
Color Matching
Color matching involves adding an indicator to a properly measured sample and allowing a color to develop. This color is usually in proportion to the amount of analyte in the water. The color is manually measured against color standards. For chlorine, the indicator is usually DPD* (N,N diethyl-p-phenylene diamine), and a pink color develops in proportion to the chlorine level in the sample. Color-matching methods are shown in Figures 2 through 5. *Note: OTO (orthotolidine) is also used as an indicator for chlorine testing, but it only tests total chlorine.
Color Cards
Color cards (Figure 2) are printed with colors corresponding to the various levels of chlorine, both free and total. The proper volume of sample is added to the sample cell, and then the appropriate volume of indicator is added to the sample cell. The tester then looks down through the sample from the top and matches the color in the water to the colors on the printed card. The color intensity of pink increases with the higher levels. Again, as with test strips, they generally do not have the sensitivity we look for in cooling towers.
Figure 2: Color card printed for chlorine test
Color Disks
Color disks (Figure 3) are printed with colors on a circular disk. The procedure is similar to the color card being a liquid-toprint color match, except that a blank with no reagent is used for the color comparison against the prepared sample. The tester then looks across the sample from the side and matches the color in the water to the colors on the wheel. This method is better than the color card because it allows for any color or turbidity in the sample water to be accounted for in the color measurement. This method also allows for better sensitivity in reporting chlorine levels.
Figure 3: Color disk.

Source: Hach Co.
Liquid Color Standards (Midgets and Slides)
The midget and slide comparators use a liquid-to-liquid match where the water sample created matches against a liquid standard. This is preferable to the liquid-toprint, as in the color cards and color disks. Precision is increased with this method, but the comparators are somewhat more fragile and susceptible to freezing.
Figure 4: Midget (top) and slide (bottom) color standards.
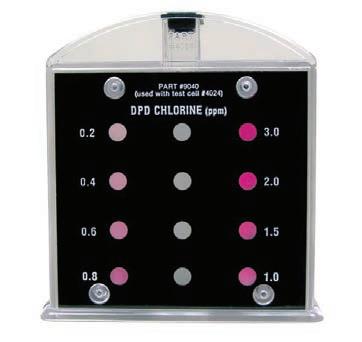
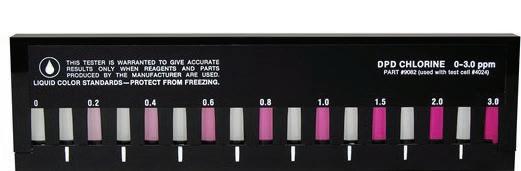
Ampoules
The ampoules (Figure 5) have the reagent predispensed in the test ampoule. This saves the user from measuring reagent and sample size. This method uses a liquid-to-liquid color match, but it could also use a photometer, improving the accuracy over manually read colors. Precision is increased with this method, but the ampoules and comparators are somewhat fragile.
Figure 5: Ampoules.

Source: CHEMetrics.
In the author’s opinion, for manually measuring chlorine, the slides and midgets are preferred. They provide good precision, as they are read in 0.2 parts per million (ppm) increments at the levels that typically concern us for cooling towers. (The ampoules using the photometer will be discussed in the next section.)
These color-matching methods, however, require human eyes to determine the color and the corresponding chlorine concentration. DPD is the preferred option for this method and creates a pink shade of color. This color may be difficult to distinguish at the low levels in cooling water. Want to know your color IQ? Click (https://www. xrite.com/hue-test) to take a quick test to determine your color vision acuity.
Asking a water tech, especially one who may be color-impaired, to do this testing may not be the best choice for determining chlorine levels, particularly for free chlorine at the lower levels prescribed.
Colorimeter/Photometer/Spectrophotometer
These electronic devices are excellent for determining free and combined chlorine in the typical ranges for cooling tower waters. They are accurate and precise, and they increase in accuracy and precision as you move up the scale in cost. Every professional water treater should have a colorimeter/photometer. The reason is for the other critical tests they do, like metals, scale inhibitors, and corrosion inhibitors. The drawbacks to these devices can be initial cost and maintenance They are electronic devices and need to be handled with more care than our other work tools. Be sure to choose a colorimeter with a robust warranty period. Figure 6 shows two examples of a colorimeter/fluorometer.
Figure 6: Examples of colorimeters/fluorometers.

Sources: Taylor Technologies (left) and Hach Co. (right)
But are these the right devices if you are to arm your customers with daily chlorine test kits to meet risk management objectives?
Titration
The industry seems to not know enough about the chlorine titration method FAS DPD. Asking a water tech, especially one who may be color-impaired, to do this test method may be the best choice for determining chlorine levels, particularly for free chlorine at the lower levels prescribed. It is generally inexpensive, and, therefore, excellent for customer contract accounts where profits need to be protected. Figure 7 shows an example of a titration kit.
Figure 7: A titration kit used for water testing.
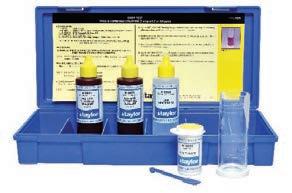
This is the method that the author would like to emphasize for testing chlorine compounds, including bromine. It has the following qualities, which are beneficial for field testers and customers alike:
Accurate Easy to use Low cost Reliable results High upper limit
For those who are interested in learning more, here is a link to a video of this method: https://www.youtube. com/watch?v=4ugRC3bDsaI&t=184s.
The color change at the endpoint is effortless to discern. The drop equivalency for a 25-milliliter (mL) sample is 0.2 ppm as Cl2, so it covers a good portion of the 0.2 ppm to 2.0 ppm as Cl2 range we should want. The procedure is easy to use and repeatable while being relatively low cost. An added benefit is this method will not “bleach out” like other DPD methods when chlorine is above 10 ppm—this method can measure up to 20 ppm as Cl2 and can test bromine as well.
Closing Thought Finally, with chlorine product pricing being high this year (as of 2022), you want to not only protect your low end of the spec range but also the high end. Overfeeding, especially in contract accounts, could prove to be very costly. Maintaining a tighter control on chlorine and bromine levels will improve your bottom-line profits. Asking customers to participate in testing and control is another good idea. Table A provides an overview of chlorine testing options for cooling tower water.
The FAS DPD method fits both the field representatives’ and customers’ test ranges and abilities. Fast, economical, and easy to use, it is the test method that could be at every cooling water application.
Table A: Overview of Chlorine Testing Choices
Chlorine Testing Options Advantages Test Strips Ease of use Disadvantages
Limited sensitivity
Cost Human error
Color-Matching Cards (liquid-toprint) Ease of use
Cost
Color Wheels (liquid-to-print) Ease of use Cost
Midgets, slides, and ampoules Ease of use Cost Limited sensitivity
Human error Comparing a liquid to a printed color is not optimum
Limited sensitivity
Human error Comparing a liquid to a printed color is not optimum
Relatively fragile
Human error
Colorimeters/Photometers/ Spectrophotometer Improved sensitivity with more standards Improved precision comparing a liquid to a liquid
Best sensitivity and precision Cost
Takes human error out of interpreting colors Maintenance Relatively fragile
FAS-DPD Cost
Improved repeatability over color-match Reagent shelf life around 12 months Less sensitivity than colorimeter/ photometer methods
Higher upper limit
Chris Golden has been involved in the water treatment and chemical industries since 1989. For more than 16 years, he worked as a field consultant for industrial facilities’ water systems. These facilities included steel mills, paper mills, power plants, manufacturing, and food processing. Mr. Golden joined Taylor Technologies in 2007 and currently serves as the director of sales. In 2007, he also became involved with the Association of Water Technologies and went on to earn his Certified Water Technologist (CWT) in 2007. Mr. Golden holds a degree in chemical engineering from Lehigh University. He can be contacted at cgolden@taylortechnologies.com.
This paper was presented at the 2021 AWT Annual Convention & Exposition, which was conducted September 22–25, 2021, in Providence, Rhode Island.
What Dangers Are Faced When Treating Water?
Compiled by James McDonald, PE, CWT, Chem-Aqua, Inc.
Editor’s note: This is a new column in the Analyst that contains discussions from the Industrial Water Treatment interest group on LinkedIn about different subjects relevant to water treatment. Each column will contain excerpts from “Questions of the Week” posed by James McDonald on LinkedIn.
Question of the Week To illustrate the importance of safety awareness, what are examples of “100 Ways to Die” in industrial water treatment? What are the dangers we may face every day that pose a risk to life?
Group Discussion James: When I was brand new in industrial water treatment and being trained on boiler inspection, my manager and I were just about to enter the mud drum of a water tube boiler when steam started coming out of the manhole. My manager and the plant manager looked at each other a little white in the face. An operator had blowdown one of the nearby boilers, and steam had backed up into the one we were literally just about to enter.
Neither lockout/tagout nor proper communication had been conducted. Lessons were learned quickly very early in my career.
Matthew: I’ve seen an 8-inch hose explode. It shot right near me and several union plumbers. It sounded like a howitzer going off. This could have been tragic. We’re talking a 200-pound hose traveling hundreds of miles per hour. I hugged my wife and kids later that afternoon. The cause was one of two things: Either a pocket of air that compressed too fast or a bad hydraulic crimp on the hose.
Peter: Some real cases: 1. Operators working around got legionellosis and died; 2. A technician fell into a wastewater anaerobic tank and suffocated; 3. A boiler operator got severely burned by leaked high-pressure steam.
Robert: Driving. This is the most dangerous thing you will do in this career, and there is no way to avoid it, unfortunately.
Daniel: I lost a co-worker several years ago who went into a new vessel to check a header prior to loading media while he was there to commission a UPW system. The vessel was only about 5 feet from the manway to the header. It was full of argon due to a purge line connected to a system a contractor was working on downstream. Had he done a proper confined space entry, he would still be with us.
Dennis: I had an account about 35 years ago, where a truck driver was killed delivering caustic to a bulk storage tank. The tank vent had corroded closed and allowed the tank to pressurize during delivery (or at least, so it appeared). The driver was within the tank containment when the opposite end blew off, projecting the tank onto the driver. Be careful out there!
Question of the Week: What do you LOVE about your job?
Group Discussion Gian: I love that there’s always something new to learn and new people to connect with, all for the benefit of society and the environment.
Mark: Everything!!!!!!!!! ��
Nellie: New technology, new solutions, transfer of knowledge … I just love water, the impact it has on industries, environment, and society, and most of all, our dependence on water, the bloodline for survival.
Miguel: Amazing new challenges with each passing day, allowing for a constant growth of knowledge.
Ghaith: No day is similar to the other one.
Damilola: Meeting people all the time, and of course, solving problems for customers.
Patrick: I love everything about it. Dealing with different systems, working with a team to help problem solve, and not being behind a desk all day, every day. My absolute favorite thing is seeing behind the scenes what others probably will never be able to see.”
Angela: Everything!
Lisa: Every day is different.
Chris: What’s not to love?
Tammy: The people and that it’s different every day.
Phil: I’d say the same: the people I work with, the customers, and always learning something new!
John: The really great people I have met and worked with!
Des: Probably the people in the water business.
Ali: Troubleshooting and customer service.
Adam: The people and places. I’ve met some awesome friends through this industry. And I get to travel around my territory and feel involved with many different communities.
Michael: “Making customers happy, because they are the true purpose of all our collective actions.”
Steven: Taking business off competitors (one in particular).
Allen: “Making a difference and bringing value to my customers. In addition to learning new technologies.”
Muhammad: Continuously thinking about solutions.
Steven: Problem-solving. I truly enjoy being presented with a water treatment problem and finding a solution. Sometimes, the problem isn’t water related, but I can still assist the customer in finding the right solution. Being more than a chemical person and more of a solution provider is what I love about my job.
Francis: I agree. Problem-solving is at the heart of what we do every day! Without such challenges, life would be boring!
Muhammad: Here’s my list: 1. Continuous learning aptitude. 2. Knowledge about multiple industries. 3. Positive efforts to save natural resources and maintaining the integrity of critical equipment. 4. Inspection of critical equipment, troubleshooting/ report writing. 5. Searching of new chemistries. 6. Training engineers. 7. Abstract and case studies writing.
Last but not least: Whenever our company is having any issue, we have brainstorming discussions with the utility and plant operation team.
Craig: Solving problems, working in the lab. Precision chemistry work. Bucket chemistry.
Justin: Building friendships that carry on outside of work. Seeing my customers being successful.
Brian: Making friends and constantly learning new things.
Joshua: I love seeing all the different processes and how
“stuff” is made. I love the smell of cereal, Combos, and soda. Some I could do without.
Question of the Week How do you determine what an acceptable baseline annual water loss is for a closed loop?”
Group Discussion Vinod: It should not be more than 5%—maximum 7%. If it is more, then check your system for a leak. Truly closed cooling systems should have maximum of 1% loss per month.”
Paul: When chemical treatment regarding biological and corrosion rate is ok, a maximum of 10% is acceptable. Everything, such as corrosion rate, temperatures, level of chemical treatment, and biological counts, should be monitored.
Tony: I would say no more than 5 to 10% to cover routine maintenance, strainer cleaning, flushing and replacement of filters, and blowdown of Spirovents. Anything over 10% should really be investigated as a leak. Also, having a water meter on the pressurization unit will help monitor whether the loss is consistent (potential leak) or can be attributed to once off maintenance events.
James McDonald, PE, CWT, is a director of technology & marketing with Chem-Aqua. He holds a master of engineering degree in chemical engineering and is a Ray Baum Memorial Water Technologist of the Year award winner (2013). Mr. McDonald also chairs AWT’s Technical Committee. He can be reached at James.McDonald@chemaqua.com. system to prevent accumulation of future biofilm and bacterial fouling.
Safety Concern Issue Normally, chlorine dioxide generators require at least a solution of sodium chlorite or (chlorate form) and some method of acidifying the component using a strong inorganic acid, like hydrochloric or sulfuric. Some methods actually use chlorine gas or sodium hypochlorite (bleach) in the process. Since this facility has a strong corporate safety department, they ruled out any potentially hazardous materials like these.
Our Solution From my research and experience with a variety of chlorine dioxide generation methods, I had already placed a type of generator that used a mild (less than 6% as sodium chlorite) product described as stabilized chlorine dioxide. The solution is made of chlorine dioxide that is pH-adjusted with caustic. In this form, it can be activated using any acidic material. In this case, we suggested citric acid, which is used safely a food additive.
Conclusion The plant management personnel agreed to our approach, and within a few months, we documented success by improved corrosion rates and minimized microbiological issues. These treatment steps resulted in improved plant efficiency and fewer mold changes.
Jerry Angelilli retired as engineering manager at Chem-Aqua Inc. in 2020. He began his career in water treatment with Betz Entec in 1978 as a sales representative. After serving as a staff engineer with that company, Mr. Angelilli developed technical knowledge and skills that led him to other positions in both sales and technical roles with other industry-related companies. He began his last affiliation with Chem-Aqua in 2007 as a senior engineer and was promoted to manager of oxidative technology in 2010, and eventually to engineering manager until his retirement. Mr. Angelilli has served on the AWT Technical Committee since 2008 and currently chairs the Boiler Subcommittee.
How to Help an Employee Who Struggles With Time Management
Elizabeth Grace Saunders Real Life E-Time Coaching & Speaking
The telltale signs are there: Tasks done at the last minute, completed late, or even forgotten. Tardiness at meetings. No response to emails or replies at weird times, like 2 am. And more explanation of why items aren’t done than action to finish them.
You’ve got a direct report struggling with time management. As a manager, it can be challenging to know how to address the issue. On the one hand, you need them to get things done, and your natural tendency might be to respond in obvious annoyance at the lack of followthrough or even to consider writing them up. On the other hand, you want to develop your team members. You may have truly brilliant individuals whom you know have the potential to be exceptional contributors if they could only figure out how to use their time effectively.
If you’re a manager unsure of how to help, here are some practical steps you can take to improve the situation.
Acknowledge Your Emotions If you’ve been managing this person for a long time, you’ve likely experienced a broad range of emotions, ranging from mild irritation to outright infuriation. Your feelings will vary depending on how severe the issues have been, the stakes involved, your personality, your expectations, and your stress levels.
Before you give feedback to your employee, acknowledge your emotions. Write out anything you might be thinking or feeling in a free-flowing manner. Do not share your raw thoughts (via email or otherwise) with your colleague. This exercise is so you can become aware of your own internal state. Process what you’re feeling on your own or with a trusted person, and honestly assess why you’re so upset. Is it a lack of control? Fear? Embarrassment? Stress?
This process helps you to release pent up negative emotions before you give feedback so that you’re not overly harsh with your direct report and do more harm than good.
Assess Your Part Your direct report may very well have poor time management. But you might want to consider whether you also have poor time-management skills and in which ways, if any, you’re contributing to the problem.
If you send over assignments last minute, don’t give clear direction, refuse to set priorities, have no follow-up system or forget to give feedback, then your actions could be playing a role in the situation. If you also expect your employees to be constantly available through email, chat, or other channels, which prevents them from setting boundaries to complete focused work, you’re also partially at fault for the struggles they face.
By identifying these issues in advance of the feedback conversation, you can go in acknowledging where you could also have done better.
Pinpoint the Stress Earlier this year, I had a situation I found very stressful with an outside contractor. There was a large project that I needed them to complete, and they were very delayed. One day as I was thinking about it, I realized that within the larger project, there were just a couple of distinct

items that mattered most. Once those were done, my stress would dramatically decrease, and the other parts could take more time.
By clarifying my most important needs, I felt less stressed and could communicate what I needed to get back most urgently, even if the whole project wasn’t done.
Take the time to think through exactly what’s causing issues for you with your direct report’s lack of time management: Do you not have what you need for important update meetings or presentations? Are you experiencing stress from them asking you to review things last minute? Are their actions costing you time or money? Do you feel anxious when there isn’t good communication on status? Once you know this, it will help focus your feedback discussions.
Communicate What You Need Once you know exactly what’s bothering you, calmly communicate exactly what you need, when you need it, and why you need it. You can also ask them what they need from you to help them be successful.
Although you may feel tempted to unload all of your frustration on your direct report about the stress they’ve caused you and the issues they’ve had, a harsh approach will typically backfire. They’ll be so overwhelmed by your anger and shut down or become defensive and stonewall. Take deep breaths, and try to remember that they likely mean well but simply struggle in this area.
Help at the Start In some situations, simply giving feedback about what you need or want can improve the situation. But in others, you’ll need to do more to help things move forward.
To get your direct report started, consider taking these actions with them:
Work with them to prioritize the work. Brainstorm the direction to take. Talk through the smaller parts. Set up intermediate milestones. Do some of the work with them in a meeting. Team them up with colleagues. Request daily updates on what they planned to do and what they’ve accomplished. Structuring the situation so that they can get and keep momentum can make a world of difference.
Appreciate Progress When you start noticing movement in the right direction, show appreciation for each step forward. You may feel concerned that giving positive feedback too quickly when they haven’t done everything yet will cause them to slack off. But the opposite is usually true. Positive feedback helps to build their confidence, positivity, and motivation and can propel them toward better and better outcomes.
Your direct report likely knows they have really bad time management and may feel worse about it than you do. Laying into them is counterproductive; increased negative emotions about their work usually causes more delay, not less. Remember that you’re on the same team. Instead of tearing them down, build them up each step of the way.
Get Outside Support Sometimes you’re too close to a situation. No matter how hard you try, you can’t provide objective, calm feedback. Or your direct report may not be able to be honest with you about what’s truly going on, such as wasting hours each day scrolling on their phone or a situation at home that may be distracting them.
In these situations, it can be helpful to connect your employee with outside resources, such as time-management training, an internal coach, or an external coach who can help them to develop these skills. Someone with experience in helping people overcome these challenges and who is more emotionally distant from the situation can often be more effective than someone with a history of frustration.
As a manager, you can’t force anyone to improve their time management. But your communication and actions can make a huge difference in your direct report’s ability to overcome their struggles and increase their productivity.
Elizabeth Grace Saunders is a time management coach and the founder of Real Life E Time Coaching & Speaking.
2022 Harvard Business School Publishing Corp.
53 AMSA, Inc.
49 AquaPhoenix Scientific
59 Bio-Source, Inc.
19 Brenntag North America
82 CHEMetrics
13 EMEC
11 EMSL Analytical Inc.
2 Environmental Safety Technologies
31 IDEXX
25 Lutz-Jesco America Corp.
42 Myron L Company 35 Process Engineered Water Equipment
29 Pulsafeeder, Inc.
36 Pyxis Lab, Inc.
33 QualiChem, Inc.
7 Quantrol, Inc.
37 Radical Polymers
23 Sanipur US LLC
21 Scranton Associates Inc.
84 Special Pathogens Laboratory
17 USABlueBook
83 Walchem, IWAKI America Inc.

WATER TESTING SHOULD BE SIMPLE
That’s why our self-filling ampoules are PREMIXED, PREMEASURED and PRECISE
We provide test kits for Low Range Dissolved Oxygen, Ammonia, Chlorine, DEHA, Filming Amines, Hardness, Hydrazine, Iron, Molybdate, Ozone, PAA, Phenol, Phosphate, Sulfide and more.
