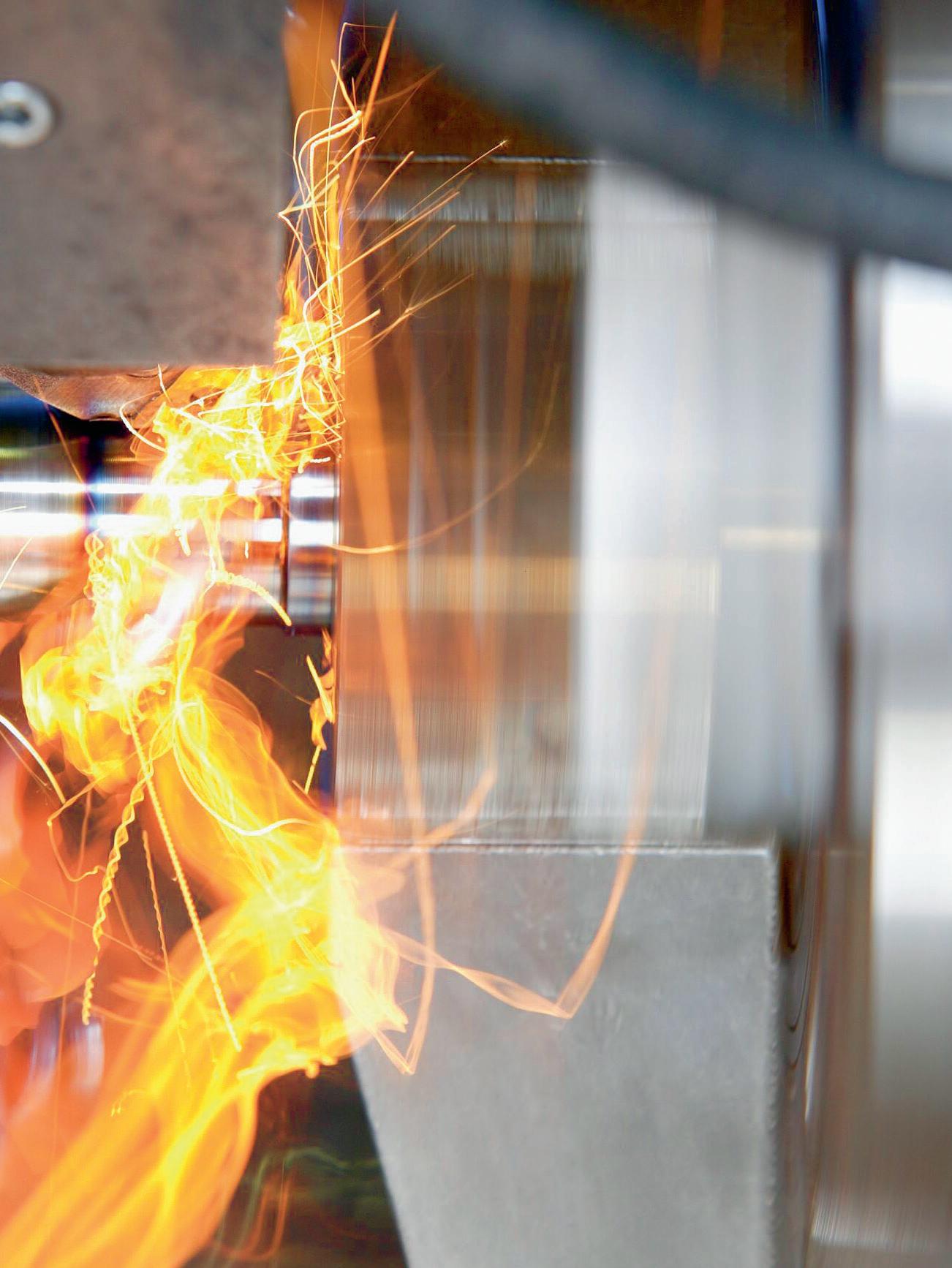
11 minute read
SOLDADURA EN ALUMINIO:
¿CÓMO EVITAR PROBLEMAS
TÉRMICOS EN EL MATERIAL?
Uno de los procesos de soldadura más complejos puede ser dominado evitando los principales efectos térmicos o escogiendo procesos alternativos.
La soldadura de aluminio es un proceso crítico en la fabricación de estructuras y componentes para una amplia variedad de aplicaciones, desde la construcción de aviones hasta la fabricación de piezas para la industria automotriz. Sin embargo, la soldadura de aluminio presenta desafíos únicos debido a las propiedades térmicas del material. En particular, la alta conductividad térmica y el bajo punto de fusión del aluminio pueden llevar a problemas térmicos en la zona afectada por el calor (ZAC, ó HAZ, por su sigla en inglés de Heat Affected Zone) durante el proceso de soldadura.
En este artículo, se explorarán los problemas térmicos comunes en las soldaduras de aluminio y se discutirán las estrategias para minimizar estos efectos y mejorar la calidad de la soldadura, incluyendo una revisión de un proceso de soldadura alternativo y automatizable.
La afectación térmica en aleaciones de aluminio tras procesos térmicos de soldadura como el MIG o TIG puede ser significativa. Durante la soldadura, el calor generado puede provocar la deformación y la oxidación del material, lo que puede afectar a las propiedades mecánicas y a la resistencia a la corrosión de la aleación.
En términos generales, la afectación térmica en aleaciones de aluminio puede ser minimizada mediante la selección adecuada de los parámetros de soldadura, como la velocidad de soldadura, la corriente y el voltaje. Además, es importante precalentar el material antes de la soldadura para reducir el estrés térmico y evitar la deformación. Es recomendable utilizar técnicas de soldadura pulsada para disminuir la cantidad de calor aportado al material. También se pueden utilizar técnicas de post-soldadura, como el recocido, para restaurar las propiedades mecánicas del material afectado por el calor.
Como evitar la deformación en soldadura por fusión Para evitar la deformación tras la soldadura en aleaciones de aluminio, se pueden aplicar diversas técnicas. Una de ellas es el precalentamiento del material antes de la soldadura, lo que puede reducir el estrés térmico y minimizar la deformación. También es importante utilizar técnicas de sujeción adecuadas para fijar el material durante la soldadura y evitar que se deforme. Otra técnica es la soldadura en etapas, donde se realizan pequeñas pasadas de soldadura en diferentes zonas del material para minimizar la acumulación de calor en una sola zona. Además, se pueden utilizar dispositivos de enfriamiento para reducir la temperatura del material después de la soldadura y evitar la deformación. Por último, es importante seleccionar el proceso de soldadura y los parámetros adecuados para minimizar la cantidad de calor aportado al material durante la soldadura.
Evitando Efectos T Rmicos
ADVERSOS CON UN PROCESO SIN FUSIÓN
La soldadura por fricción y agitación (friction stir welding) es un proceso de soldadura sólido que se ha vuelto cada vez más popular en los últimos años.
El proceso de soldadura por fricción y agitación implica la unión de dos piezas de metal mediante la aplicación de calor y presión debido al movimiento relativo y esfuerzos de contacto entre la herramienta y el material a ser unido. A diferencia de otros procesos de soldadura, no se utiliza un material de relleno para unir las piezas. En su lugar, la fricción y la agitación generan calor que ablanda el metal (lo lleva a un punto de deformación plástica) y permite que las piezas se unan. Según Patxi Blanco, Regional Industry Manager AWS EMEA & LATAM en KUKA Robotics, "es un proceso equivalente a la forja, en el cual se logra formar un material sin necesidad de cambiar su estado de sólido a líquido".
Problemas T Cnicos De La Soldadura De Al
La soldadura de aluminio puede presentar varios problemas técnicos, entre los que se incluyen:
1. Distorsión: El aluminio tiene una alta conductividad térmica, lo que significa que se calienta y se enfría rápidamente durante el proceso de soldadura. Esto puede provocar una deformación o distorsión de la pieza soldada.
2. Porosidad: La porosidad es un problema común en las soldaduras de aluminio debido a la alta solubilidad del gas hidrógeno en el material. Si no se controla adecuadamente, el hidrógeno puede quedar atrapado en la soldadura, lo que puede debilitar la unión.
3. Agrietamiento: El agrietamiento es otro problema común en las soldaduras de aluminio, especialmente en aleaciones que son sensibles a la fisuración. El agrietamiento puede ocurrir durante el proceso de enfriamiento o después de la soldadura debido a tensiones residuales.
4. Corrosión: La corrosión es un problema común en las soldaduras de aluminio debido a la formación de óxidos y otros compuestos durante el proceso de soldadura. Si no se eliminan adecuadamente, estos compuestos pueden debilitar la unión y provocar problemas de corrosión.
La soldadura por fricción y agitación (friction stir welding) es un proceso de soldadura sólido que se ha vuelto cada vez más popular en los últimos años.
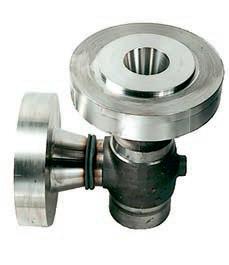
El proceso de soldadura por fricción y agitación implica la unión de dos piezas de metal mediante la aplicación de calor y presión debido al movimiento relativo y esfuerzos de contacto entre la herramienta y el material a ser unido. A diferencia de otros procesos de soldadura, no se utiliza un material de relleno para unir las piezas. En su lugar, la fricción y la agitación generan calor que ablanda el metal (lo lleva a un punto de deformación plástica) y permite que las piezas se unan. Según Patxi Blanco, Regional Industry Manager AWS EMEA & LATAM en KUKA Robotics, "es un proceso equivalente a la forja, en el cual se logra formar un material sin necesidad de cambiar su estado de sólido a líquido".
Este proceso se ha utilizado en una variedad de aplicaciones, desde la fabricación de aviones hasta la construcción de automóviles. También se ha utilizado en la industria naval y en la fabricación de tuberías. Una de las principales ventajas de la soldadura por fricción y agitación es que produce uniones fuertes y de alta calidad sin los problemas asociados con otros procesos de soldadura, como la deformación y el agrietamiento. "La unión generada por el friction stir welding tiene mayor dureza que el material base", dice Blanco. "Incluso, con un debido control de parámetros de proceso, es altamente reproducible", agregó. Además, este proceso es más eficiente energéticamente que otros procesos de soldadura, lo que lo hace más económico. A medida que la tecnología ha mejorado, el costo de la soldadura por fricción y agitación ha disminuido, lo que ha llevado a una mayor adopción en la industria. "Existen clientes que reportan que 1 metro de soldadura por friction stir welding les cuesta lo mismo que 1 metro de hilo de relleno en soldadura por fusión. Si a esto se suman los gastos que tenía la fuente de energía, por boquillas, antorchas, se tiene que el costo del primer proceso es mucho menor. Tan solo el consumo energético puede verse reducido en un 95%", comentó Blanco.
Aplicaci N En La Industria Automotriz
Una aplicación común de la soldadura por fricción y agitación robotizada para aluminio es en la fabricación de paneles de carrocería para la industria automotriz.
Proceso robotizado de soldadura por fricción y agitación (friction stir welding). Cortesía KUKA Robotics.
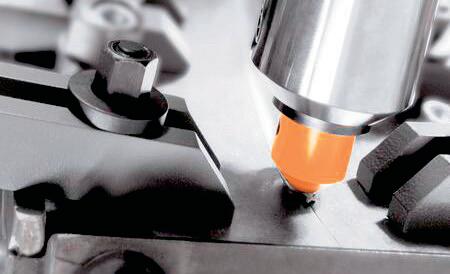
T Cnicas Comunes De Soldadura Para Aluminio
Las técnicas más utilizadas para soldar aluminio son:
Soldadura TIG (GTAW): La soldadura TIG es la técnica más comúnmente utilizada para soldar aluminio. Esta técnica utiliza un electrodo de tungsteno y un gas inerte, como el argón, para crear una soldadura limpia y de alta calidad.
Soldadura MIG (GMAW): La soldadura MIG también se utiliza para soldar aluminio. Esta técnica utiliza un alambre de soldadura alimentado automáticamente y un gas de protección inerte para crear una soldadura rápida y eficiente.
Soldadura por arco sumergido (SAW): La soldadura por arco sumergido se utiliza a menudo en aplicaciones de alta producción y en materiales de mayor espesor. Esta técnica utiliza un arco eléctrico sumergido en un fundente granulado para crear una soldadura fuerte y duradera.
Soldadura por fricción: La soldadura por fricción es una técnica de soldadura sin fusión que se utiliza a menudo en aplica ciones de alta producción. Esta técnica utiliza la fricción entre dos piezas de aluminio para crear una unión sólida y resistente.
Un ejemplo de esto es el proceso utilizado por la empresa KUKA Robotics, que utiliza robots para soldar paneles de aluminio para la carrocería de vehículos, y más recientemente para carcasas de baterías para la electromovilidad. Estos componentes, necesarios en los automóviles eléctricos, requieren materiales ligeros, resistentes y duraderos que puedan soportar las demandas de la aplicación. Por lo tanto, se utilizan aleaciones de aluminio específicas para cumplir con estos requisitos.
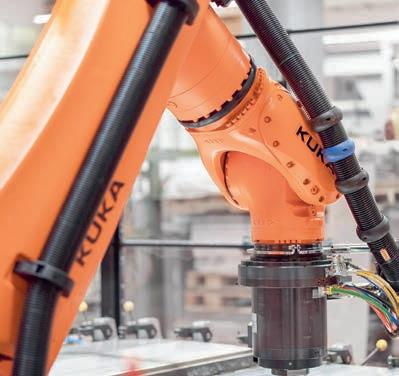
En este proceso, se utiliza un robot para mover una herramienta de soldadura por fricción y agitación a lo largo de la junta de soldadura. Adicionalmente, como lo confirma Patxi Blanco, de KUKA Robotics, "el proceso robotizado permite soldar piezas tridimensionales, en lugar de procesos basados en sistemas gantry que solo lo hacen en chapas en dos dimensiones". Esto aumenta la flexibilidad de aplicación del proceso, si se incluye la capacidad del robot para implementar de manera automatizada diferentes piezas de trabajo y diferentes espacios de trabajo 360° alrededor del robot. MMI
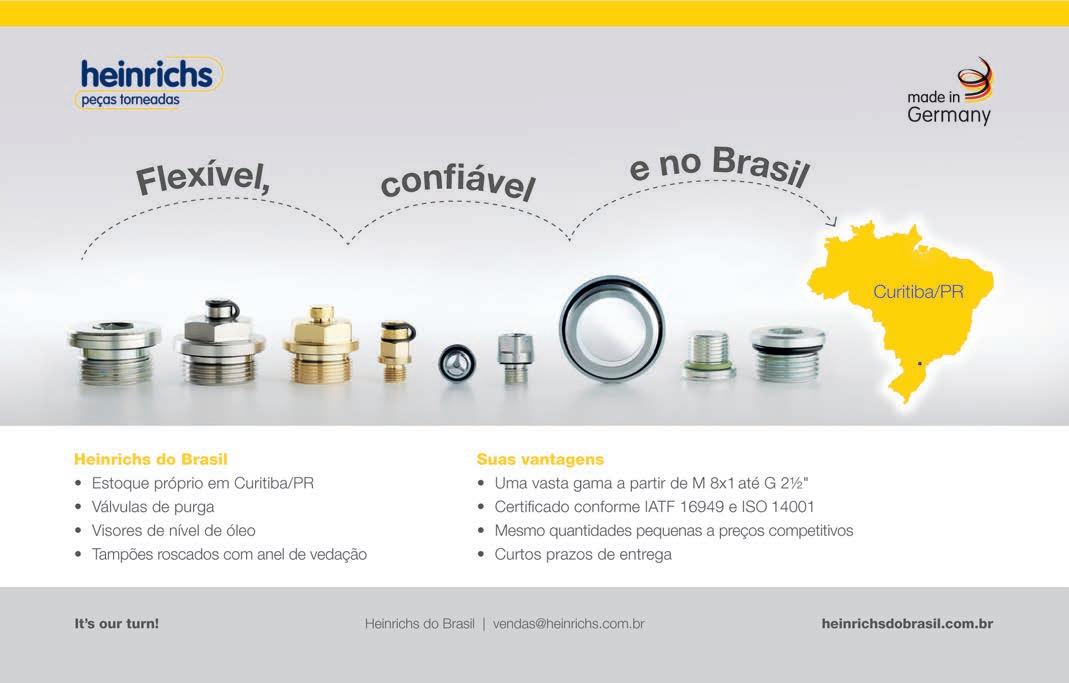
Tecnolog A De Sujeci N De Doble Contacto Asegura Proyectos De Alta Calidad En Taller Mexicano
Conozca una historia de éxito de un taller metalmecánico que ha logrado mejorar su calidad y reducir costos de producción mediante el uso de mejores sistemas de sujeción.
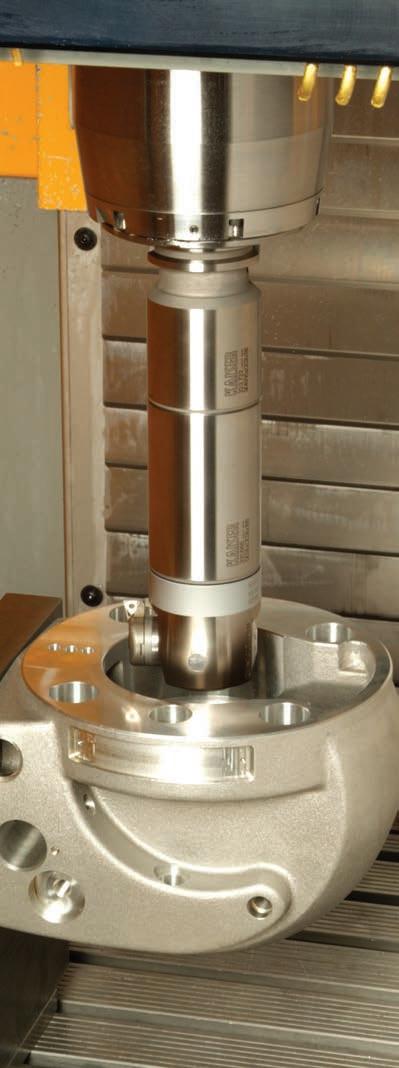
Tal vez fue intuición, pero la ingeniería detrás de una repentina idea generó una solución que permitió conservar un proyecto, y tal vez, un cliente. Más importante aún, la disponibilidad de la herramienta con tecnología BIG-PLUS® de doble contacto, permitió al equipo de Mecanizados Laguna, hacer una prueba que cambió el rumbo de un proyecto que parecía no tener solución en una ecuación donde las variables de dureza, paralelismo, profundidad y circularidad; formaron un acertijo complicado en el área de maquinado.
Dedicada a la fabricación de componentes metálicos, en Mecanizados Laguna consideran que su principal objetivo es brindar un servicio al cliente altamente especializado y con la mayor calidad posible. Entre sus clientes principales destacan las empresas Carterpillar Torreón, Jyson Safety Systems, Precision Coating, Tecnologia Estructural S.A de C.V. y Sumitomo Drive Technologies; con los cuales, han ido ganando terreno de a poco, proyecto por proyecto, incrementando volumen a partir de la confianza adquirida de cada lote entregado.
La empresa, con más de 70 empleados que operan en una nave de aproximadamente 6,500 m2, tiene un área de maquinados con equipos Haas (VF1, Vf2, VF3), Gantry (GR712, VF5) y Torno (ST25 y ST20), máquinas Chevalier y Kafo, con capacidades de 1 m a 4 m con Cat 40 y Cat 50, las cuales están más enfocadas a producción en serie, con proceso de generación de barrenos calibrados con boring, barrenos avellanados y barrenos machueleados. Las máquinas Kafo, por su precisión, se han dedicado a la manufactura de moldes para inyección de plástico.
Joel García, gerente de maquinados CNC hace hincapié en lo importante que es orientar la fabricación hacia una cultura de servicio puesto que los componentes que fabrican, tales como herramentales (fixtures, jigs para ensambles), moldes, maquinados y soldaduras, así como otros componentes metálicos; son destinados a la fabricación de tecnología para la producción en industrias variadas, tales como minería, energía, alimentos y bebidas, muebles, automotriz, maquinaria y plásticos.
De ahí se deriva una extensa gama de materiales utilizados tales como aceros inoxidables (316, 304), aceros estructurales (4140, 1045), aceros de bajo carbón (A36) y todo tipo de aceros, como anti-desgaste Hardox y Toolox; de la misma manera utilizan plásticos de ingeniería como acetal HDF, Nylomate, nylamid, acetal, poligar, celerón y materiales especializados como los empleados para el manejo de materiales en la industria de alimentos.
HEMOS INVERTIDO EN CENTROS DE MECANIZADO VERTICALES DE CONTROL NUMÉRICO TIPO C Y DOBLE COLUMNA, TORNOS CNC Y EQUIPOS DE MEDICIÓN DE ALTA GAMA, INCLUYENDO EQUIPOS PORTÁTILES”, JOEL GARCÍA, GERENTE DE MAQUINADOS CNC, MECANIZADOS LAGUNA, MÉXICO
Como consecuencia de la calidad que suelen entregar, los requerimientos de sus clientes se han diversificado con proyectos de tolerancias cada vez más cerradas, hecho que los ha llevado a invertir de manera constante en la mejor tecnología disponible para procesos de maquinados.
Los componentes periféricos seleccionados son clave, pues sin ellos no podrían realizar las operaciones que requieren, las cuales suelen ser de alta precisión, de entre 10 y 30 micras. El joven y bien instruido gerente de maquinado advierte que los equipos de sujeción deben tener una estabilidad muy alta, de tal suerte que les ayuden a lograr planicidades, paralelismos, perpendiculares, circularidades, y conicidades con una precisión muy alta.
García agrega que en procesos de barrenado o boreado, muchas veces se presentan run-outs que afectan la pieza de trabajo, causando daños irreversibles y obligan a que todo un componente sea enviado a scrap. Peor aún, es común no identificar pronto el problema y atribuirlo a la máquina o a la herramienta, mientras que los conos son los responsables de causar esas variaciones. “Para nosotros, que fabricamos muchas veces piezas únicas o lotes muy pequeños, esto puede hacernos perder mucho dinero, pero sobre todo, podría provocar que nuestro cliente pierda la confianza en nuestro trabajo”.
Un Aprendizaje Crucial Para Mecanizados Laguna
Esto sucedió mientras estaban maquinando una pieza para una housing de un motorreductor de gran tamaño. Dicho componente llevaba varios orificios, los cuales debían cumplir con un paralelismo muy preciso. En las camisas de los motores, la economía espacial para la ubicación de los barrenos no permite mucho margen de error, además del poco espacio, los orificios suelen ser de gran profundidad. Esto sin duda es un reto de ingeniería durante el proceso de fabricación.
Estos motores son utilizados en industrias como agricultura y naval y están fabricadas con placas recortadas con oxicorte y ensambladas con soldadura. “Esto genera mucha tensión en el material, la cual se va acumulando y genera inestabilidad que se convierte en un reto para posteriores operaciones de manufactura, como el maquinado”.
Joel García explica: “estábamos batallando para llegar a las medidas que necesitábamos. Entonces me llegó a la mente la asesoría que los ingenieros de la empresa BIG DAISHOWA y de nuestro proveedor AHNSA, nos han estado brindando, y volteamos a ver nuestros conos BIG-PLUS®”.
Esta es una tecnología de sujeción de doble contacto para Husillos con interfaz ISO 7/24 patentado, la cual se convirtió en un estándar y el cuál está siendo utilizado ya por muchos fabricantes de maquinaria. Al tener estos conos en el taller, García recurrió a ellos para realizar el proceso con el cuál estaban batallando, al grado de que habían considerado renunciar al proyecto.
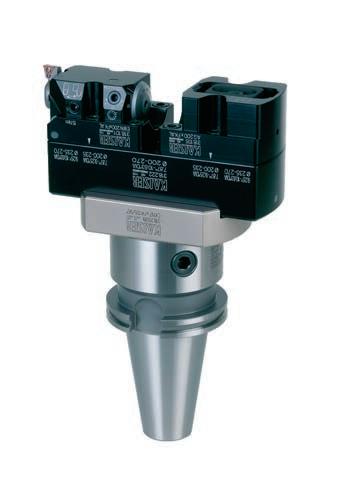
Este no fue el caso y el uso de la tecnología de doble contacto les trajo una muy agradable sorpresa. La rigidez del portaherramientas les permitió cumplir con sus tolerancias de circularidad , concentricidad y paralelismo que estaban contempladas en el dibujo. Y no solo fue eso, la velocidad de fabricación se mejoró. “Hacíamos un barreno de 200 mm de diámetro con una longitud de entre 18 y 24 pulgadas, dijo García.
Un Peque O Cambio En Una
El sistema de doble contacto está generando cambios positivos, pues los maquinados que solían entregar en un mes ahora los entregan en un par de semanas, ahorro de tiempo que ahora están considerando para adelantar sus fechas de entrega.
La mejora en calidad y en costos de producción, permitió a los ingenieros de Mecanizados Laguna llegar a la conclusión de que invertir en tecnología de punta es siempre redituable cuando se tiene el conocimiento adecuado. Pero sobre todo, tener tecnología de alta gama disponible les ayuda a cumplir con su objetivo principal: Satisfacer las necesidades de sus clientes.
En le empresa de Gomez Palacio, Durango, han incorporado tecnología de BIG DAISHOWA casi como un estándar. Además de los sistemas de doble contacto, tienen borings, barras gemelas, herramienta de desbaste, avellanadores y Sistemas Mega Synchro para roscar. También tienen conos adaptadores para fresas de desbaste, mega chucks y milling chucks, entre otros productos. “Una buena selección de herramienta nos da mayor seguridad y nos asegura mayor éxito”.
Mecanizados Laguna trabaja para convertirse en una empresa de clase mundial en función del servicio que son capaces de ofrecer. “Para nosotros no hay cliente mayor o menor”, asegura Joel García. “Todos son importantes. Por tal motivo seguimos creciendo, innovando y adquiriendo nuevas tecnologías que nos permitan trabajar de la mano de los mejores para dar un mejor servicio a los clientes”. MMI
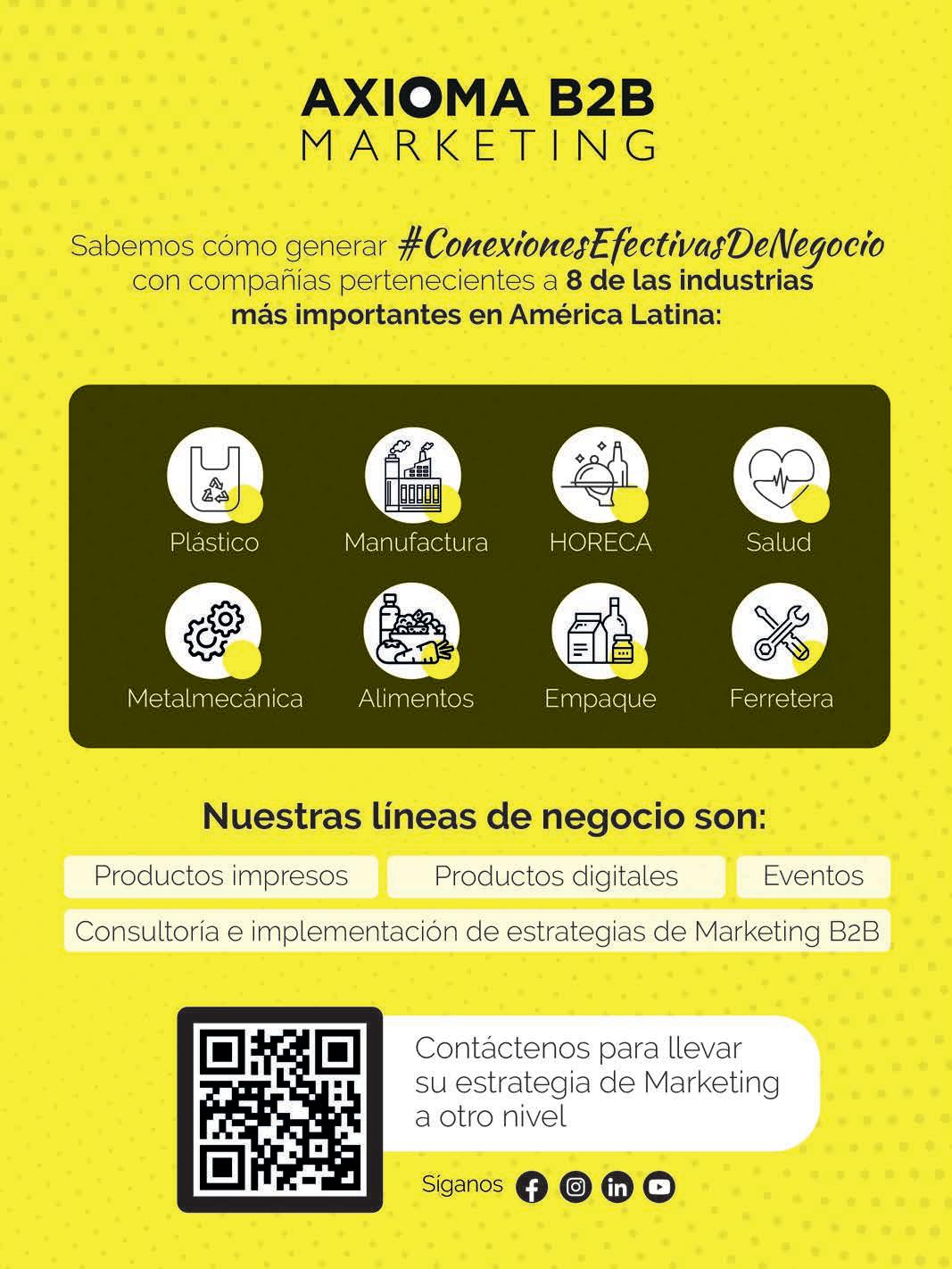
